Wire Rope Sling Inspection Criteria
As a starting point, the same work practices which apply to all "working" wire rope apply to wire rope which has been fabricated into a sling. Therefore, a good working knowledge of wire rope design and construction will be not only useful, but essential in conducting a wire rope sling inspection.
The goal of a sling inspection is to evaluate remaining strength in a sling which has been used previously to determine if it is suitable for continued use.
Specific inspection intervals and procedures are required by the Occupational Safety and Health Administration (OSHA) and by ASME B30.9 standards, and the responsibility for performance of inspections is placed squarely upon the sling user by Federal Legislation.
As a starting point, the same work practices which apply to all “working” wire rope apply to wire rope which has been fabricated into a sling. Therefore, a good working knowledge of wire rope design and construction will be not only useful, but essential in conducting a wire rope sling inspection.
But because wire rope is a rather complex machine, no precise rules can be given to determine exactly when a wire rope sling should be replaced. There are many variables, and all must be considered.
Removal from Service Criteria
ASME standards specify that a wire rope sling shall be removed from service immediately if any of the following conditions are present:
- Broken wires: For strand-laid grommets and single-part slings, ten randomly distributed broken wires in one rope lay, or five broken wires in one strand in one rope lay. For cable laid, cable laid grommets and multi-part slings, refer to the table below.
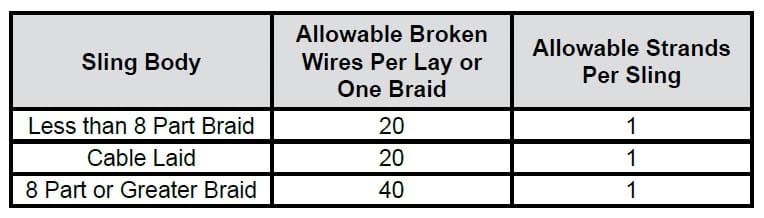
- Distortion: Kinking, crushing, birdcaging or other damage which distorts the rope structure. The main thing to look for is wires or strands that are pushed out of their original positions in the rope.
- Heat damage: Any metallic discoloration, fusing of wires or loss of internal lubricant caused by exposure to heat.
- Damaged end attachments: Cracked, bent or broken end fittings caused by abuse, wear or damage.
- Bent hooks: No more than 5 percent over the normal throat openings, measured at the narrowest point from the plane of the unbent hook (see ASME B30.10 Hooks)
- Corrosion: Severe corrosion of the rope or end attachments which has caused pitting or binding of wires should be cause for replacing the sling. Light surface rust does not substantially affect strength of a sling.
- Pulled eye splices: Any evidence that eye splices have slipped, tucked strands have moved, or pressed sleeves showing serious damage may be sufficient cause to reject a sling.
- Unbalance: A very common cause of damage is the kink which results from pulling through a loop while using a sling, thus causing wires and strands to be deformed and pushed out of their original position. This unbalances the sling, reducing its strength.
- Kinks: Are tightened loops with permanent strand distortion that result from improper handling when a rope is being installed or while in service. A kink happens when a loop is permitted to form and then is pulled down tight, causing permanent distortion of the strands. The damage is irreparable and the sling must be taken out of service.
- Doglegs: Are permanent bends caused by improper use or handling. If the dogleg is severe, the sling must be removed from service. If the dogleg is minor, (exhibiting no strand distortion) and cannot be observed when the sling is under tension, the area of the minor dogleg should be marked for observation and the sling can remain in service.
Disposal of Retired Slings
The best inspection program available is of no value if slings, which are worn out and have been retired, are not disposed of properly. When it is determined by the inspector that a sling is worn out or damaged beyond use, it should be tagged immediately DO NOT USE. This sling should then be destroyed as soon as possible by cutting the eye and fittings from the rope with a torch. This will help assure that an employee will not mistakenly use a sling which has been retired from service.
Federal Work Rules Require Specific Inspection Intervals
Government regulations are specific on when to inspect. Both ASME Standard B30.9 and OSHA require that wire rope slings receive two types of inspections: a daily visual inspection and additional inspections where service conditions warrant.
Daily visual inspections are intended to detect serious damage or deterioration which would weaken the sling. This inspection is usually performed by the person using the sling in a day-to-day job. The user should look for obvious things, such as broken wires, kinks, crushing, broken attachments, severe corrosion, etc.
Additional inspections should be performed at regular intervals based on:
- Frequency of sling use
- Severity of service conditions
- Nature of lifts
- Prior experience based on service life of slings used in similar circumstances
It is required that these additional inspections be carried out by a designated person who must have good knowledge of wire rope. An accurately written and dated record of all conditions observed shall be maintained. Any deterioration of the sling which could result in appreciable loss of original strength should be carefully noted and determination made on whether further use would constitute a safety hazard.
The Wire Rope Technical Board Bulletin: Guidelines on Strand Clearance in the Eyes of Wire Rope Slings
When an eye is formed in a sling, the rope is formed into a relatively sharp bend to form the eye. This bend increases the clearance between the strands on the outside of the eye and, in some cases, this clearance accumulates between two strands. This is not a reason for concern in a new sling, and the sling is acceptable for use.
During the initial and subsequent loadings, this clearance between strands, and position of the strands in the eye of the sling, may change. The condition of all slings must be evaluated in accordance with ASME B30.9, or other applicable standards or regulations, in order to determine the suitability for continued use.
How to Inspect Wire Rope Slings
Precisely how to make proper, adequate inspections is not detailed by OSHA—yet it is in the knowledge of the inspector that the big difference between a good inspection and something less becomes apparent.
Inspection should follow a systematic procedure:
- First, it is necessary that all parts of the sling are readily visible. The sling should be laid out so every part is accessible
- Next, the sling should be sufficiently cleaned of dirt and grease so wires and fittings are easily seen. This can usually be accomplished with a wire brush or rags
- The sling should then be given a thorough, systematic examination throughout its entire length, paying particular attention to sections showing the most wear
- Special attention should also be paid to fittings and end attachments, and areas of the sling adjacent to these fittings
- When the worst section of a sling has been located, this area should then be carefully checked against the OSHA and ASME criteria
- Label or identify slings that are inspected
- Keep records of inspections that include dates and corresponding conditions of slings
- Dispose immediately of slings that are rejected
A knowledgeable inspector will also insist on proper storage for out-of-use sling to make his job easier, if not for the good of the slings. Inspections are much easier—and probably more thorough—when slings are available for inspection in an orderly arrangement, out of the weather and away from heat and dirt.
Lubrication
Like any other machine, wire rope is thoroughly lubricated at time of manufacture. Normally, for sling use under ordinary conditions, no additional lubrication is required. However, if a sling is stored outside or in an environment which would cause corrosion, lubrication should be applied during the service life to prevent rusting or corroding.
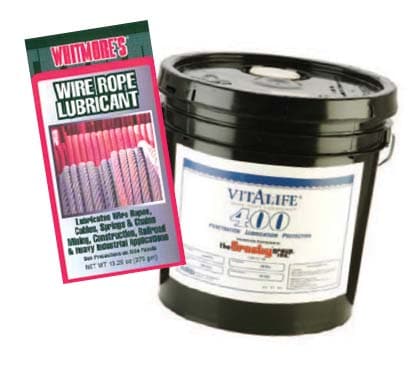
If lubrication is indicated, the same type lubrication applied during manufacturing should be used. Your sling manufacturer can provide information on the type of lubricant to be used and best method of application.
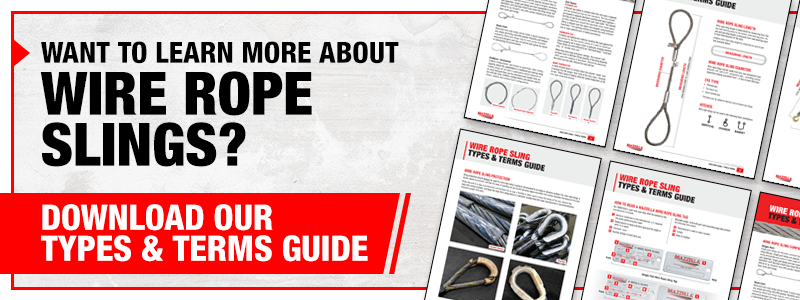