How a Waste-to-Energy Facility Replaced Their Old Cranes Over a 30′ Pit
Based in Lorain, Ohio, Skylift is a leading easement equipment manufacturer that specializes in industry-leading solutions for specialty backyard utility products. However, in order to more efficiently build their machines, they needed help from Mazzella to overcome supply chain and cumbersome equipment issues.
What Did McKay Bay Waste-to-Energy Hope to Accomplish on This Project with Mazzella?
- Find a safe way to work over a 30’ deep pit
- Repair and reinforce concrete pillars next to the pit
- Remove outdated overhead cranes
- Install new runway beams and repair concrete walls
- Install new semi-automated overhead cranes with new hoist and grapples
- Update and repair crane cab control area
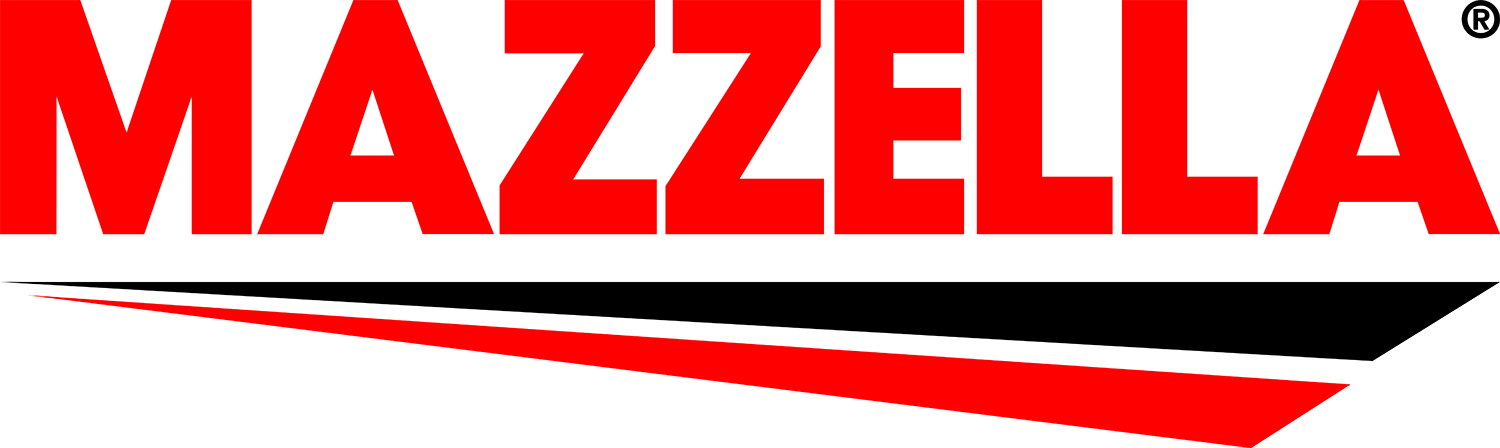
The Waste-to-Energy facility in McKay Bay has powered homes and buildings for the citizens of Tampa since 1984.
They create clean energy by burning trash that would have originally been destined for landfills, which helps sustainability for the city in the long-term. Every month, they generate enough electricity to power about 15,000 homes in Tampa.
On the grounds of McKay Bay, a transfer station ingests solid waste from the city for processing. There, the waste is sorted and anything that can be recycled is sent to an off-site location. The leftover refuse is then sent to the Waste-to-Energy facility to be burned.
At the facility, waste is dumped from trucks and wheel loaders from the tipping floor into a 30’ deep trash pit. Above the pit are two overhead cranes with remote-controlled grapples that pick up the trash from the pit and drop it into hoppers. The waste is then incinerated in a furnace to create steam to power generators, providing electricity to the city of Tampa.
“Nobody’s ever done this before,” said Blake. “So, trying to figure out how to do it was pretty tough.”
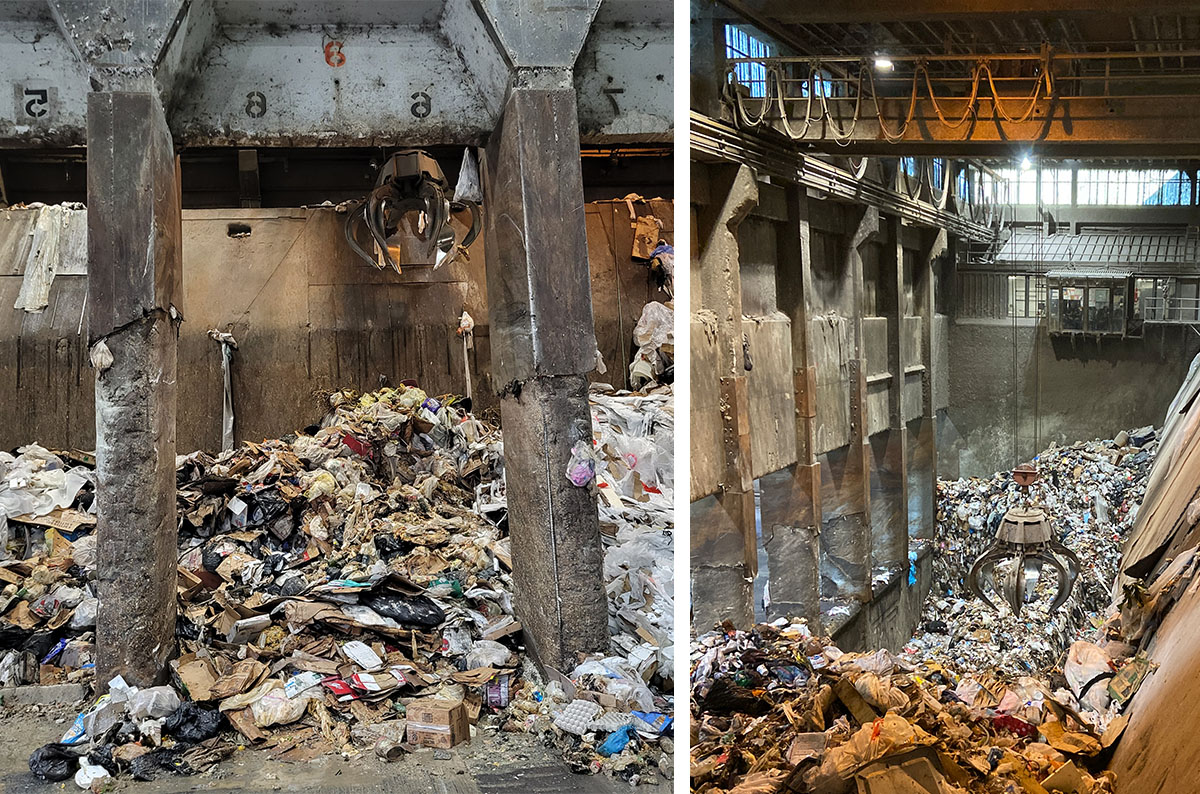
What Problem Was McKay Bay Looking to Solve?
The past few decades had been hard on the facility and the cranes. With the last major update 20 years ago, the cranes were now in disrepair and needed replacing.
“The cranes were way outdated. They were falling apart, they were breaking down,” said Blake Porritt, Estimator at Mazzella.
One of the crane’s brakes would regularly give out and fall to the north side of the building during operation. They also needed new controls to manipulate the crane, hoist, and grapple from the crane cab which overlooks the trash pit.
With their old cranes malfunctioning, it became increasingly difficult to find parts to repair them as they continued to grow more obsolete every year.
“They had numerous breakdowns trying to piecemeal their old cranes together to keep them running,” said Craig Cottingham, Field Project Engineer for Mazzella.
The crane runways mounted in the walls were also out of tolerance and needed concrete repairs to allow the installation of new ones.
Below all of that, the tipping floor next to the pit had load-bearing concrete pillars that had been damaged from years of activity, needing structural repair and protection from future damage.
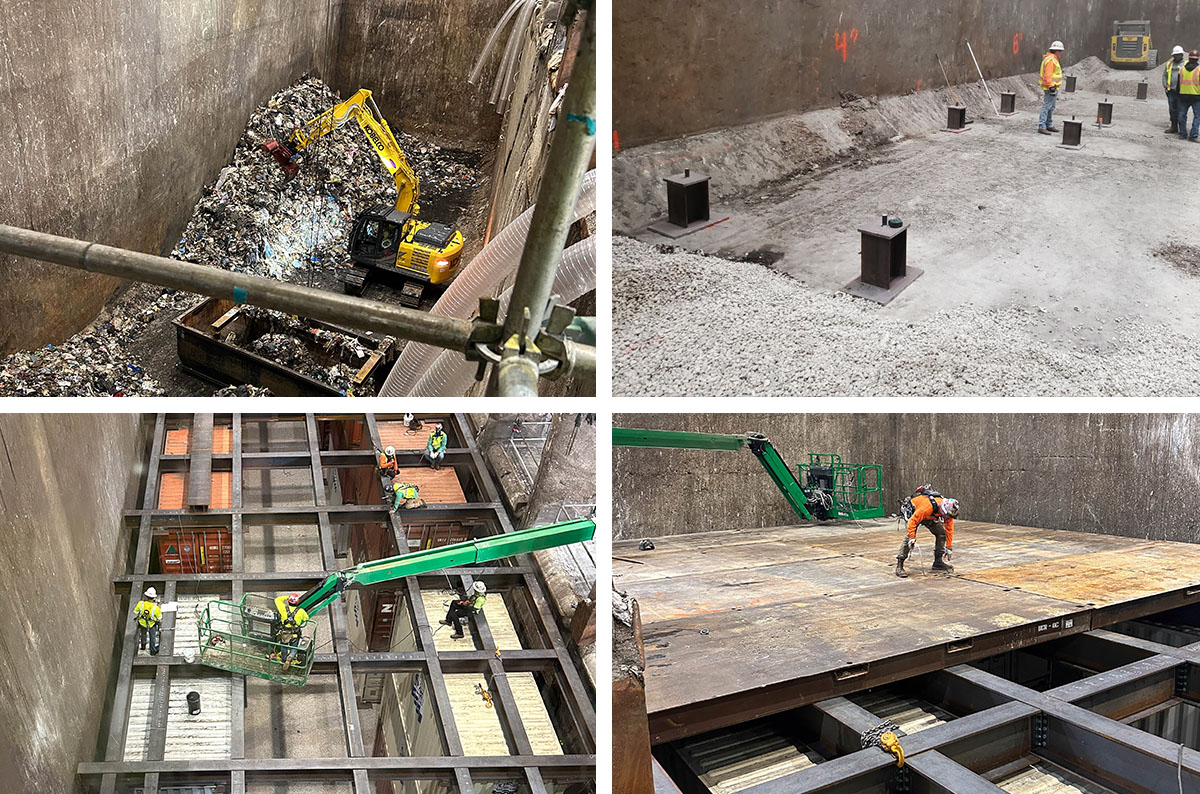
How Did Mazzella Overcome the Space Limitations of the Facility?
Replacing the cranes was going to be tough. There was no easy way to access them as the facility had a concrete roof that couldn’t be taken off and below that was a 30’ deep pit filled with garbage.
Lee Porritt, Field Project Superintendent at Mazzella emphasized, “The biggest challenge was the pit.”
“How do you work over a 30’ pit? We went through a couple of different ideas, using jersey barriers to fill the pit, somehow leaving the trash in and working over that,” Blake said.
The trash pit posed a formidable challenge to the Mazzella team in figuring out how to create a feasible and safe working environment inside the unique space. To do this, Mazzella collaborated with engineering companies to create a custom solution that would allow them access to the cranes.
“Nobody’s ever done this before,” said Blake. “So, trying to figure out how to do it was pretty tough.”
“We came up with pulling all the trash out of the pit and stacking overseas CONEX boxes on top of each other—30 in total. We built a steel structure over top of the boxes, placed steel matting on top of that, creating what we call a dance floor,” Lee explained.
To do this, the entire facility had to be shut down for several months. This would give Mazzella’s team and other contractors the time to empty the pit and lay down the necessary infrastructure to carry on the project.
“We had to logistically figure out how we were going to level the pit,” said Cottingham. “Ultimately, we ended up using stone to get the pit level.”
“We had great engineers on board that were able to help us with figuring out our loads on the CONEXs and if it could be done safely, which is most important.”
After clearing the trash out, the crew dumped tons of stone at the bottom to level the empty pit. Stacking empty CONEX boxes on top of each other got them the height they needed to build a working surface flush with the tipping floor. The safe and level surface made of steel matting known as “the dance floor” was undergirded with custom steel supports situated between the CONEXs for added structure.
The creativity and problem-solving from the engineering teams allowed Mazzella to overcome the initial hurdle of the job. With a sturdy platform to work on, the contractors were able to begin the work of actually replacing the cranes. They now had the space and stability to position themselves under the old cranes and remove them using a Barnhart Pushup Unit (BPU).
The next phase of the project would involve repairing the building in key areas and installing the new equipment.
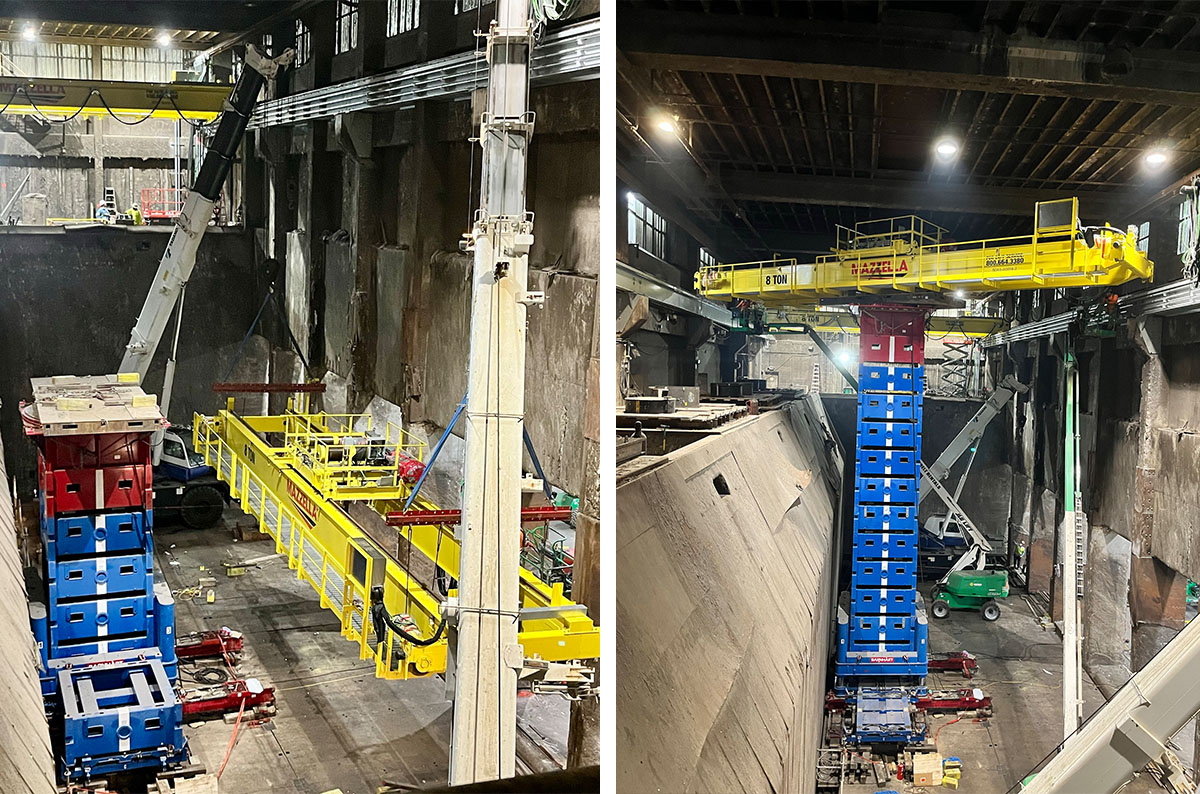
What Products and Services Did Mazzella Provide for McKay Bay?
With the previous cranes taken down, the old runways and rails that the crane used to travel on were also removed. Mazzella repaired the concrete they were originally mounted to and installed new crane rails in their place. Installing a new and more efficient overhead crane system would come next.
For this project, Mazzella built two 8-ton semi-automated overhead cranes, complete with new hoists and grapples for lifting waste from the pit to the hoppers. Stuart Vining, Mazzella’s Director of Panel Manufacturing built the electrical panels used for the new cranes, collaborating with Brunswick Industrial Services to pull off the PLC programming integration for the project.
Commenting on the previous cranes, Vining explained, “From a 20-year-old perspective, the drives, the PLC for the semi-automation positioning, stuff like that was not nearly as up-to-date and as good as what we provided.”
By installing semi-automated cranes, Mazzella was able to bring the facility into the 21st century with much needed efficiency. The new buttons and controls allow the worker controlling the overhead cranes to move the crane automatically to pre-programmed areas.
With the new cranes also came an updated and improved crane cab for the operators. In the facility, the crane cab sits above the pit against a wall and allows the operators to see and easily manipulate the cranes, hoists, and grapples. Mazzella repaired the crumbling concrete around the old cab and installed new glass windows for the operators to look out of. Inside the cab, new chairs for the operators were installed as well as new controls for the semi-automated crane.
“Right at their fingertips, the crane operators have a whole section of pre-programmed buttons that are pit areas and hopper areas that they can select, put the crane in semi-automation, and they will run to that particular setup spot.” Vining added.
Next to the pit area, the concrete pillars supporting the ceiling above the tipping floor needed repair. Years of wear-and-tear from wheel loaders dumping garbage into the pit had compromised parts of the pillars, exposing the rebar underneath. Mazzella repaired the concrete and installed protective steel guards around the pillars to prevent future damage.
“What we’ve done here, we’ve prolonged the life of this plant with our equipment, and they’ll get another 60 years out of it.”
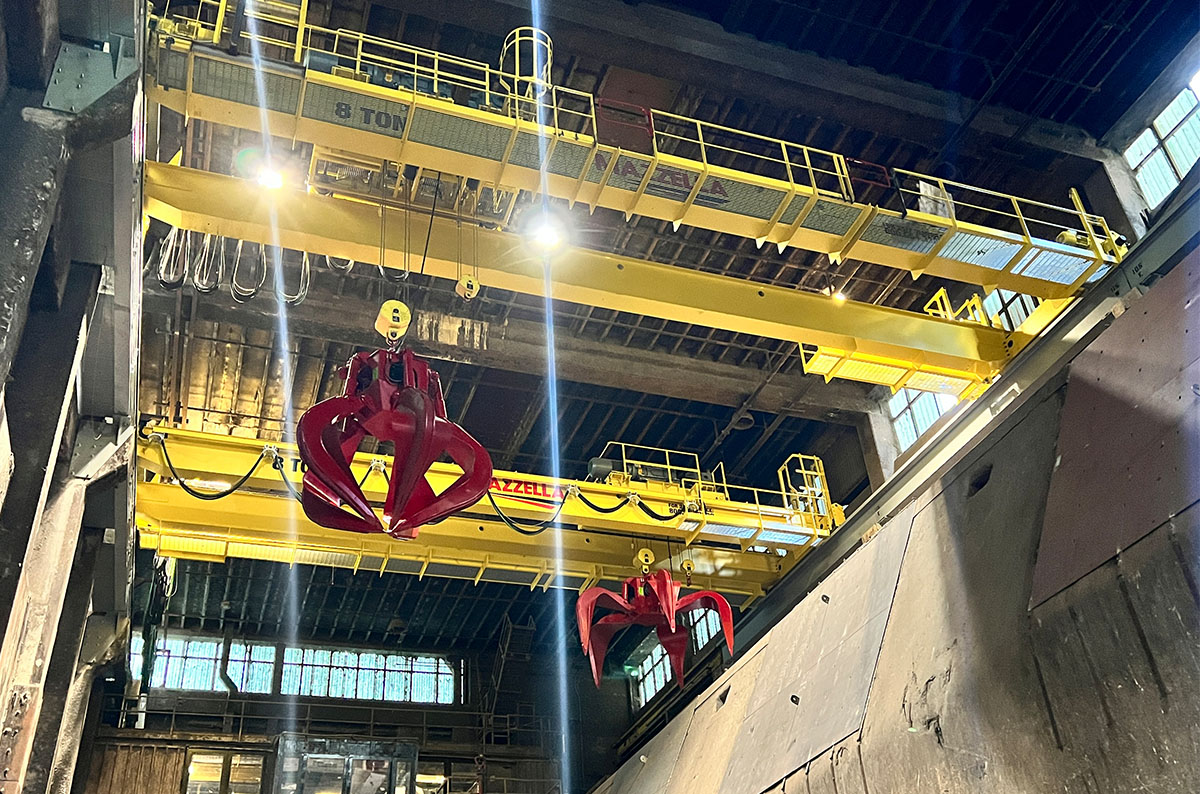
How Will These Improvements Help McKay Bay?
The repair work and installation of new semi-automated cranes by Mazzella marks a significant turning point for the Waste-to-Energy facility.
“I think it’s going to help them tremendously,” said Cottingham. “With Mazzella, they’ll have parts availability. Obviously, they’re going to be much faster.”
The semi-automation of the cranes increases ease-of-use and lessens cycle times while in use. Less time in the cycle of picking up and dumping garbage means fewer mechanical failures and smoother operation of the cranes. This increased efficiency and longevity will benefit McKay Bay and the city of Tampa for many years to come.
“Their downtime is going to be slim to none now with all brand-new equipment,” Lee explained. “What we’ve done here, we’ve prolonged the life of this plant with our equipment, and they’ll get another 60 years out of it.”
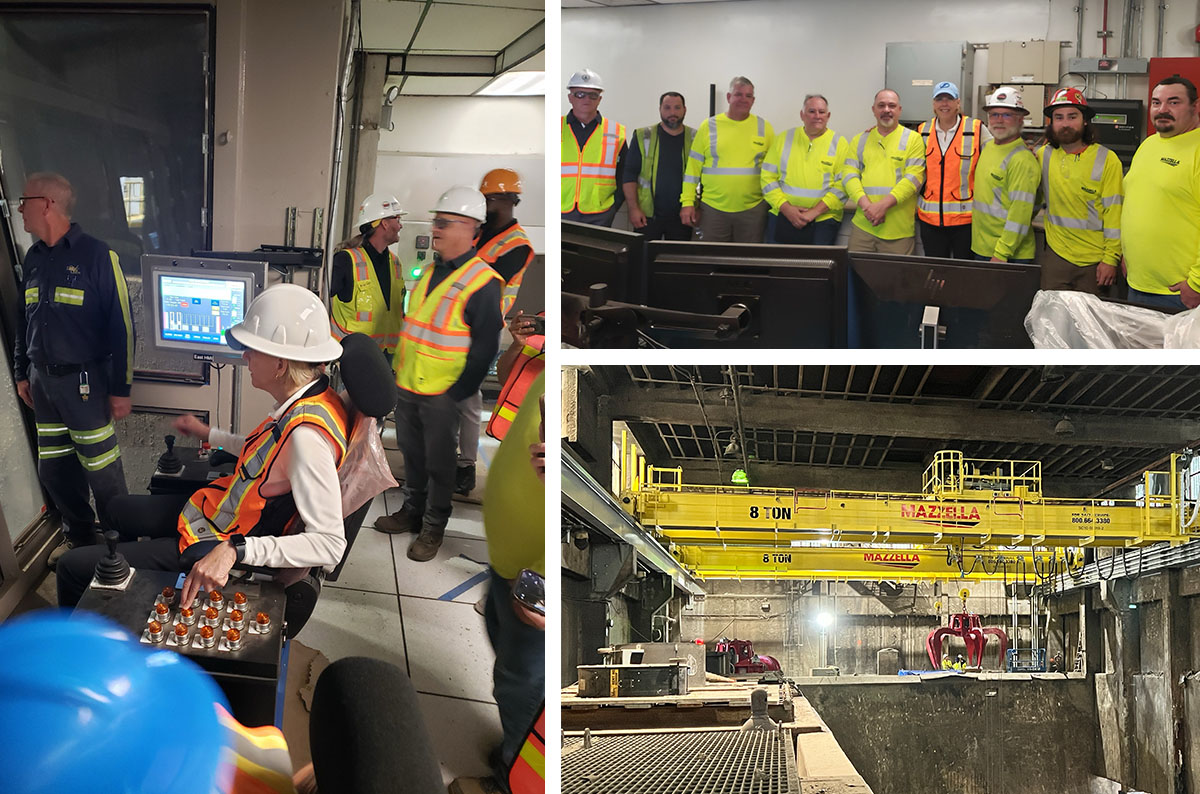
Learn More About How Mazzella Can Help Your Business
No matter how challenging your needs are, Mazzella has tailored solutions for applications across many different industries. We offer products and services for lifting and rigging equipment, below-the-hook devices, sling repair, crane ropes, overhead cranes and material handling, overhead crane and hoist service, crane upgrades and modernizations, hoists, warehouse solutions, fall protection, and training.
Our years of experience in the industry combined with our commitment to quality and safety allow us to serve you, regardless of how complicated the task. Contact us to find out how we can help your company gain efficiency and compliance!
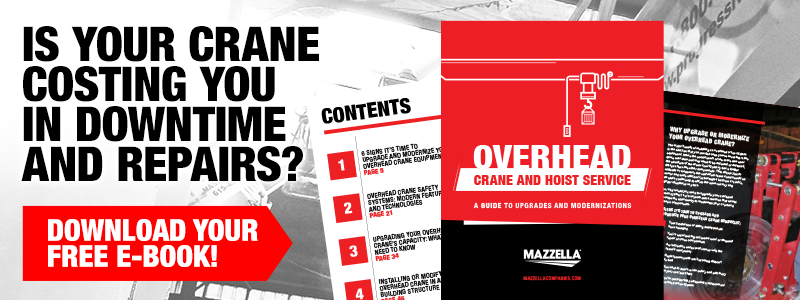
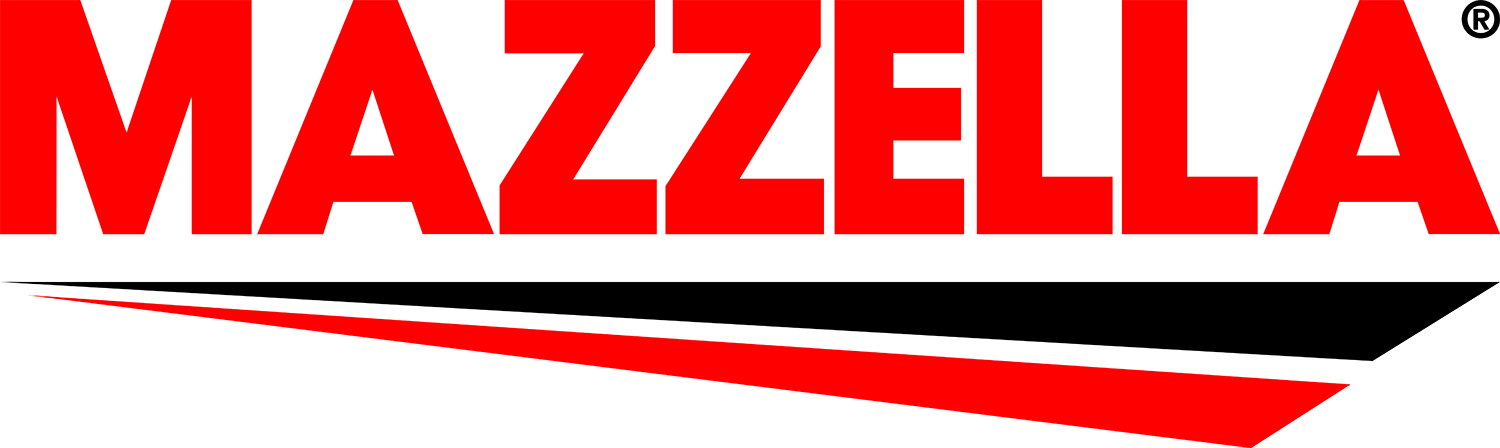