Cordage Product Warnings / Cautions / Guidelines
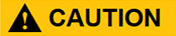
Phillystran Cautions:
Break Strength: The breaking strength of a rope is the load at which a new rope will break when tested under laboratory conditions. Break strength should not be mistaken for safe working load.
Safe Working Load: Because of the wide range of rope use, rope condition and the degree of risk of life or property, it is not possible to make a blanket recommendation for safe working load. It is ultimately dependent on the rope user to determine what percentage of break strength is their own safe working load.
Wear: Ropes wear out with use; the more severe the usage, the greater the wear. It is often not possible to detect wear on a rope by visible signs alone. Therefore, it is recommended that the rope user determine a retirement criteria for ropes in their application.
For assistance in developing safe working load and retirement criteria for each application please call or write Phillystran.
All printed statements, data and recommendations are based on reliable information and tests, and are presented without any guarantee or warranty. Statements regarding the use of Phillystran’s products and processes are not to be construed as recommendations for use in violation of any applicable laws, regulations or patent rights. © All rights reserved.
For complete warning and application information, see Phillystran, Inc. at www.phillystran.com.
Cordage Institute International Warnings & Guidelines:
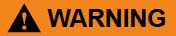
The use of rope and cordage products has inherent safety risks which are subject to highly variable conditions and which may change over time. Compliance with standards and guidelines of the Cordage Institute does not guarantee safe use under all circumstances, and the Institute disclaims any responsibility for accidents which may occur. If the user has any questions or uncertainties about the proper use of rope or cordage or about safe practices, consult a professional engineer or qualified individual.
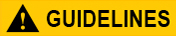
CI 1401-06 Safer Use of Fiber Rope
Purpose
- This Guideline is provided to help in the selection and safer use of cordage products. Compliance with Cordage Institute Standards and Guidelines does not guarantee safe use under all circumstances, and the Institute disclaims any responsibility for any accidents that may occur.
1. Overview
- There are inherent risks in the use of rope and cordage because such products are subject to highly variable conditions that change over time. Therefore, Design Factor selections and Working Load Limits must be calculated with consideration of exposure to risk and actual conditions of use for each application. If in doubt, consult an experienced engineer or other qualified individual regarding the design, application and selection of a rope product.
2. Minimum Breaking Strength
- The Minimum Breaking Strength (MBS) is the force that a given rope is required to meet or exceed in a laboratory test when it is new and unused. MBS values are given in Cordage Institute Standards and individual manufacturers’ specifications.
3. Working Load / Working Load Limit
- The Working Load (WL) is the weight or force applied to rope or cordage in a given application.
- The Working Load Limit (WLL) is a guideline for the maximum allowable capacity of a rope product and should not be exceeded.
- Applied loads higher than a specified WLL can overstress and damage fibers, resulting in premature rope failure.
The Working Load of an application should not exceed the WLL of the rope for optimal product performance and the safety of personnel and property.
4. Design Factors
- The Design Factor (DF) is the ratio between the MBS and WL. This value is the margin of safety for an application. For a particular application, the factors affecting rope behavior and the degrees of risk to life, personnel and property must be considered when setting a DF.
- Commercial and industrial users must determine a DF based on actual service conditions and establish operating procedures for a specific application. A “general use” consumer must also assess his application and determine conditions of use and hazards that may apply.
- As a rule, the more severe the application, the higher the DF needs to be. Selection of a DF in the general range between 5:1 and 12:1 is recommended. A design factor at the low end of this range should only be selected with expert knowledge of conditions and professional estimate of risk. DF at or above the high end of the range should be used for more severe conditions of use. When in doubt, always select the highest practical DF, or contact the manufacturer for additional guidance. Engineering assistance may be necessary to determine the service loads and risks and to set the appropriate DF.
Considerations in the Selection of a Design Factor
- Experience is the best guide for determining a DF. Select a DF value used in a similar application that proved successful.
- Consider increasing the Design Factor if:
– Problems have previously been observed in similar applications
– Injury, death or loss of property may result if rope fails
– Loads are not accurately known
– High or continuous dynamic loads are anticipated (See Section 6)
– Shock loads are anticipated
– Extensive cyclic loads are likely to occur
– Tension is on the rope for long periods
– Knots are used, as knots can reduce strength by as much as 50%
– Operators are not well trained – Operation/use procedures are not well defined and/or controlled.
– Severe abrasion is likely to occur from exposure to rough surfaces or cutting edges, or by contamination from dirt and grit.
Expert Guidance is Strongly Suggested for the Following Situations:
- Rope is used constantly over pulleys or around a small bend.
- Rope is used at elevated temperature that may glaze, weaken or melt the fibers.
- Rope is used in the presence of hazardous chemicals.
- Rope is not new and is of unknown properties and/or prior use.
- Rope is not inspected frequently or adequately.
- Rope will be in service for long periods that may lose strength due to fatigue.
CI Guideline 2003 Fibers for Cable, Cordage, Rope and Twine explains some of the effects of elevated temperature and chemicals on synthetic fibers.
5. Calculation of Values
- After the WL has been estimated and the DF for an application has been determined, a rope can be selected by calculating the necessary new rope Minimum Breaking Strength. The required MBS is determined by multiplying the Working Load by Design Factor. WL x DF = MBS. For example, an application with a Working Load of 3 tons and a Design Factor of 10 would require an rope with MBS = 3 x 10 = 30 tons.
- Similarly, the Working Load Limit of a new rope is determined by dividing the Minimum Breaking Strength by the Design Factor for a given application. MBS ÷ DF = WLL. Examples of WLL, based on a DF of 5:1 and 12:1, are given in individual Cordage Institute Standards. The WLL in CI standards are for new ropes with standard terminations.
6. Dynamic Loading
- Nearly all rope in use is subject to Dynamic Loading to some degree. Whenever a load is picked up, stopped, moved or swung there is an increased force due to the acceleration or dynamics of the movement. The more rapidly or suddenly such actions occur, the greater the forces. In extreme cases, the force sustained by the rope may be two, three, or even more times the static load. (e.g., when picking up a tow on a slack line or using a rope to stop a falling object) Therefore, in applications such as towing lines, lifelines, safety lines, climbing ropes, etc., the DF must reflect the added risk involved. If significant dynamic load is foreseen, a DF at or above the high end of the range should be considered. Loads should be handled slowly and smoothly to minimize dynamic effects.
- Users should also be aware that dynamic effects are greater on a low elongation rope, such as manila, than a high-elongation rope, such as nylon. Also note that dynamic effects are more significant on short segments of rope as opposed to longer ones.
- Excessive dynamic loading will shorten the life of a line and/or cause premature failure.
7. Recoil / Snapback Safety Warning
When a tensioned rope breaks, an attachment fails, or either are suddenly released, the energy in the rope will cause it or the attachment to recoil back in unpredictable directions with great force, resulting in possible injury or death to persons in its path. Persons should never stand in line with or in the general path of rope under tension to avoid snapback injuries.
8. Special Applications
- The DF ranges can be lower or higher than recommended in applications where actual field experience has proven successful, where a recognized standard or specification exists, where qualified professionals have made a thorough engineering analysis of all conditions of use and/or a regulatory agency has granted specific permission. In such controlled cases, breaking strength, elongation, energy absorption, and other factors, including operating procedures, must be evaluated during the selection of the Design Factor.
- In addition to the above, more specific guidelines should be considered for applications such as life safety and marine use.
For complete warning and application information, see Cordage Institute International at www.ropecord.com.