A Wire Rope is a Machine With Many Moving Parts
From childhood, many of us have been conditioned to think of a machine as some device with gears, shafts, belts, cams, and assorted whirring parts. A wire rope is, in reality, a very complicated machine.
From childhood, many of us have been conditioned to think of a machine as some device with gears, shafts, belts, cams, and assorted whirring parts. Yet, by the rules of physics, an ordinary pry bar is a simple machine, even though it has only one part.
A wire rope is, in reality, a very complicated machine. A typical 6 x 25 rope has 150 wires in its strands, all of which move independently and together in a very complicated pattern around the core as the rope bends. Clearances between wires and strands are balanced when a rope is designed so that proper bearing clearances will exist to permit internal movement and adjustment of wires and strands when the rope has to bend. These clearances will vary as bending occurs, but are of the same range as the clearances found in automobile engine bearings.
Understanding and accepting the “machine idea” gives a rope user a greater respect for rope, and enables him to obtain better performance and longer useful life from rope applications. Anyone who uses a rope can use it more efficiently and effectively when he fully understands the machine concept.
How a Wire Rope Machine Works
The extent to which wires move in a rope when it bends is illustrated by the following example—what actually happens when you wrap a 1-inch rope over a 30-inch sheave.
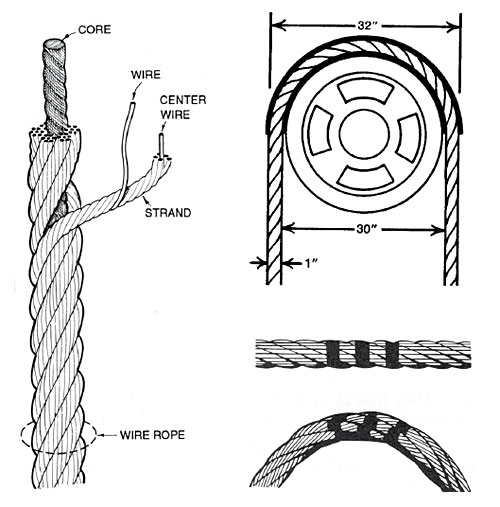
Between the point where the rope first touches the sheave on one side, and where it leaves the sheave on the other side, the length of rope in contact with the sheave would be 3-1/8 inches shorter than the length of the side away from the sheave—if the rope did not move and adjust internally by wires sliding back and forth.
The mathematics is simple: Just subtract half the circumference of a 30″ circle from half the circumference of a 32″ circle.
Circumference = π x Diameter
C= 3.1416 x 32 = 100.5312
C = 3.1416 x 30 = 94.2490
6.2931 / 2 = 3.14
Thus, circumference of a 32-inch circle is slightly more than 6-1/4″ longer than that of a 30-inch circle. Since a rope only touches half of a sheave at any time, the length differential which a rope must accommodate is 3-1/8″.
By this same reasoning, a 1-inch rope wrapped on a 30-inch hoist, the drum must compensate internally for a 6-1/4″ length differential in each wrap.
This change of dimension is achieved by the sliding and adjusting of the strands in relation to one another, and a similar sliding and adjusting of the individual wires within each strand.
By painting stripes around a wire rope as illustrated in the image above, and actually bending the rope, we can see the movement of strands as the rope bends. Anytime a rope flexes, this movement takes place. The sharper the bend, the more the movement.
Quite obviously, the grade of wire will affect such things as strength, resistance to wear, fatigue resistance, corrosion resistance and so on. Today, the greatest portion of all wire rope is made from two grades of wire—Extra Improved, Plow Steel (EIP) and Double Extra Improved Plow Steel (EEIP). Both are tough, strong, wear-resisting carbon steel, with EEIP providing about 10% greater tensile strength. Sometimes wire is plated or galvanized before strands are formed, where special corrosion or wear characteristics are desired. Most wire is “Bright”—that is, without any surface coating or treatment.
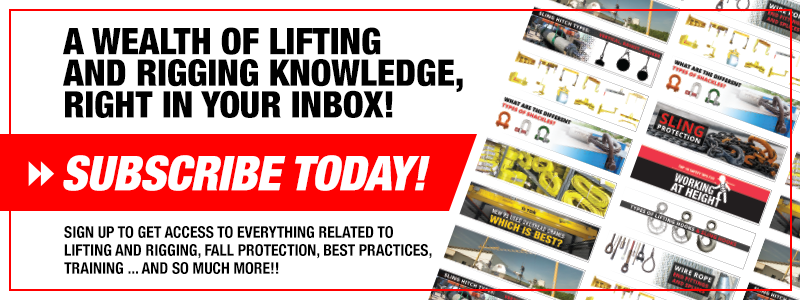