7 Reasons Why Inspection Tags Aren’t Making Your Lifting Program Safer
In theory, this process seems like a highly-organized and bullet-proof way to make sure your lifting and rigging gear is in compliance with industry standards. However, you may be introducing some ambiguity and unintended consequences into the inspection process to determine if your equipment is in proper working condition
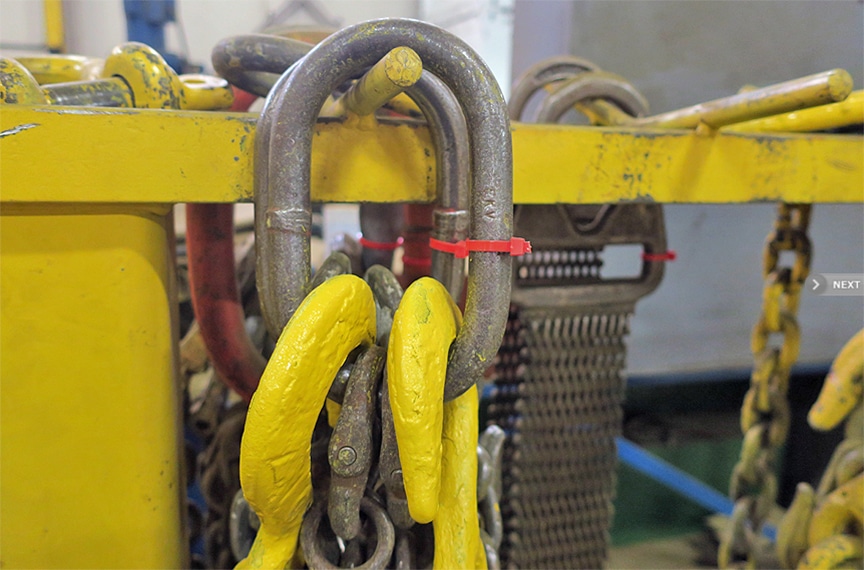
One of the questions that our Rigging Inspectors frequently get asked by customers is, “can you put an identifier tag or a marking on my slings and rigging gear to indicate that they’ve had their periodic inspection?”
We can, and will, add identification tags onto lifting slings, below-the-hook equipment, and any other rigging hardware or gear—if asked to do so by the customer during the course of a periodic inspection. Tags can be barrel tags, colored zip ties, or items that can be painted or marked to indicate that they’ve received a periodic inspection.
In theory, this process seems like a highly-organized and bullet-proof way to make sure your lifting and rigging gear is in compliance with industry standards. It shows initiative that your safety or production personnel are aware of industry requirements and want to implement a program that has safety and compliance top of mind.
However, as you’ll see below, we believe that applying these inspection identifier tags or markings can introduce some ambiguity and unintended consequences into the process of inspecting and determining if the equipment is in proper working condition. In this article, we’ll discuss a number of different reasons that you may want to re-consider starting or continuing an inspection tag program.
7 Reasons Why Inspection Tags Aren’t Making Your Lifting Program Safer
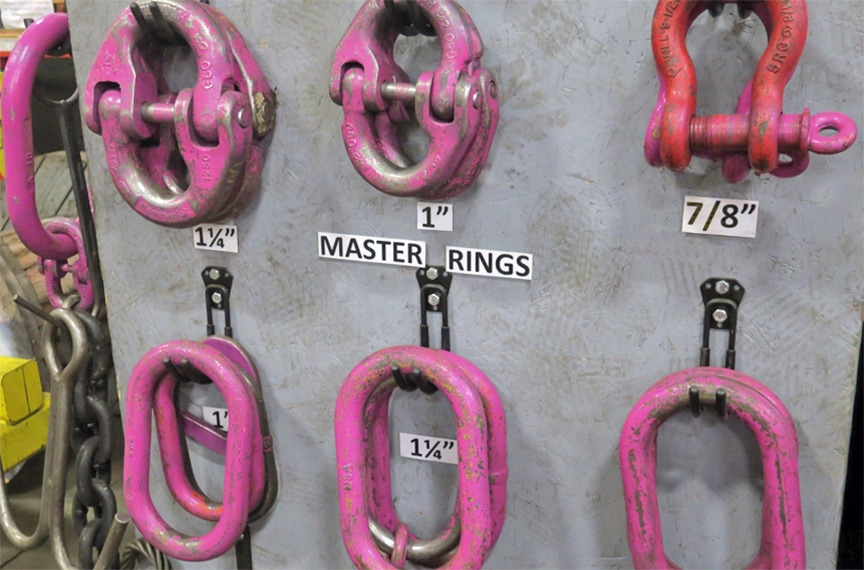
1. OSHA and ASME Do Not Require the Use of Any Type of Visual Tag or Marking to Indicate That a Piece of Rigging Equipment Has Been Inspected
The first thing that you should understand is that a visual indicator, whether it be a tag or marking, on individual pieces of rigging equipment is NOT required by any OSHA or ASME standard. The only requirement is that the owner can provide documentation that they provided training for their employees and that documentation is available to prove a periodic inspection was performed.
2. Inspection Tags or Markings on Rigging Gear Can Unintentionally Result in a Reduction of Pre-Shift and Frequent Inspections
No matter how good the company’s organizational policy and safety culture is, these types of tags result in more confusion as to the condition of the equipment and the last time they were inspected. Inevitably, someone will interpret a tag or a marking on a sling as a certification that the piece of equipment has been inspected and certified for a certain period of time—and may cause that user to disregard the requirements for pre-shift or pre-use inspection.
The inspection identifier or marking on a piece of rigging equipment really means nothing in regards to the condition of the rigging—it only indicates that it was inspected at some moment in time.
What matters is that you have training in place for your operators and work instructions in place for them to inspect their rigging equipment prior to each use and according to the periodic inspection schedule as determined by a qualified person.
3. Inspection Tagging Can Interfere with Production and Cause Work Stoppages
Inspection tags used in abusive environments can be damaged or can fall off. If your facility has a policy that a piece of rigging equipment can’t be used unless it’s marked with an inspection tag, then you may have to halt production until the sling or hardware is inspected and the tag is replaced. Or, until a replacement item with proper inspection tags or markings can be located and put into service.
This becomes a bigger issue when it comes to the management of your inspection tag program and properly training your employees on:
- Where to place the tags on the sling
- What type of tag or marking can be used on different types of slings
- How to properly trim excess material when installing
- How to cut or remove an old tag to prevent damage to the sling when replacing with a new tag
4. Inspection Tags Can Interfere with the Effectiveness of the Rigging Hardware or Slings
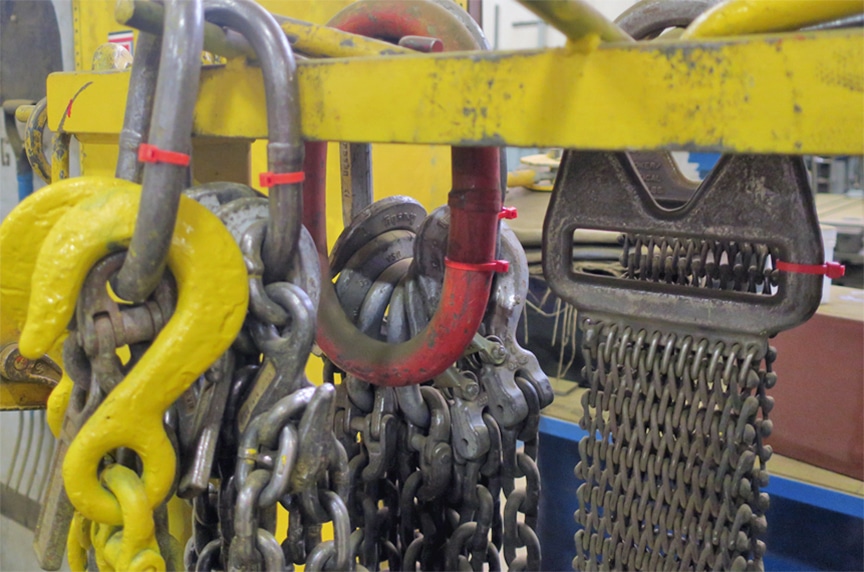
Applying tags to a piece of rigging hardware or to a sling can interfere with the effectiveness and design of the product. An added tag may catch or snag on other materials when being used. An example may be, if a tag is applied to a piece of hardware, it may not allow a load to seat properly on a sling hook, or for a sling to seat properly in a master link.
If applied too tightly, a zip tie or other type of tag, can reduce flexibility on a sling and cause it to kink or bunch on slings made from synthetic materials.
Some items can be small and there’s no effective way to apply a tag. Hardware pieces can be marked with paint, but over time, the paint can chip off or wear away and potentially cause confusion if the inspection markings have worn away.
5. Inspection Tags Can Actually Cause Damage to Rigging Gear
There isn’t one type of tag that’s safe to use on all types of slings. Barrel tags, or other tags that utilize any type of braided wire, can’t be used on synthetic web slings or roundslings. If the wire were to break, or the wire got pinched or applied too tightly around the sling, it could rip, cut, or tear the sling.
Also, when the tags are applied, excess material has to be cut off and any excess metal or plastic from a zip tie could get caught or snag on a sling—or even cut or injure the operator after being trimmed.
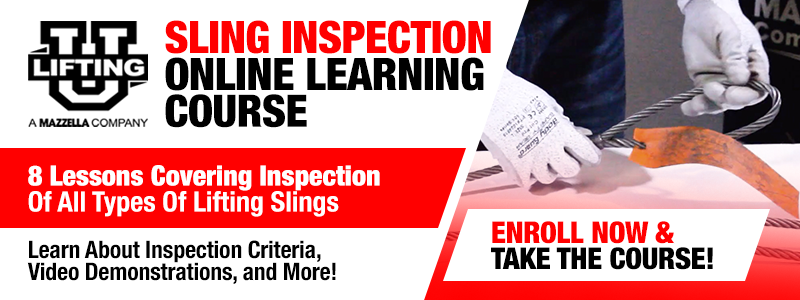
6. Inspection Tags are Not a Cost-Effective Solution
Depending on the style and design, sling inspection tags can range from a few cents a piece to a couple of dollars per piece. If you have a couple hundred slings in your facility, that cost can add up quickly.
Plus, when you factor in the time it takes to remove old tags and apply new tags, you’re either keeping an inspector onsite who may be working on an hourly rate, or taking up additional time from your in-house inspection resources.
7. It’s Difficult to Account for New or Repaired Lifting Slings or Hardware
What happens if you purchase 30 additional slings two months after your periodic inspection has been performed? It’s possible that you may not have another periodic inspection for close to 300 days. Any newly purchased or repaired slings or rigging hardware will not have the proper inspection tagging if they’re purchased or brought into service after a periodic inspection has been performed.
If you have an internal policy that prohibits the use of a sling that hasn’t been properly marked or tagged, then you may have to call a service company back out and pay them to inspect and tag all of that gear, or have an internal resource inspect all of the items and tag them.
Again, if you have proper training and work procedures in place, you can perform an initial inspection when you receive the equipment from the manufacturer, and train your operators to inspect their gear prior to each shift or use—eliminating any need to have new equipment tagged or marked.
What Programs or Solutions Can You Use Instead of Inspection Tags?
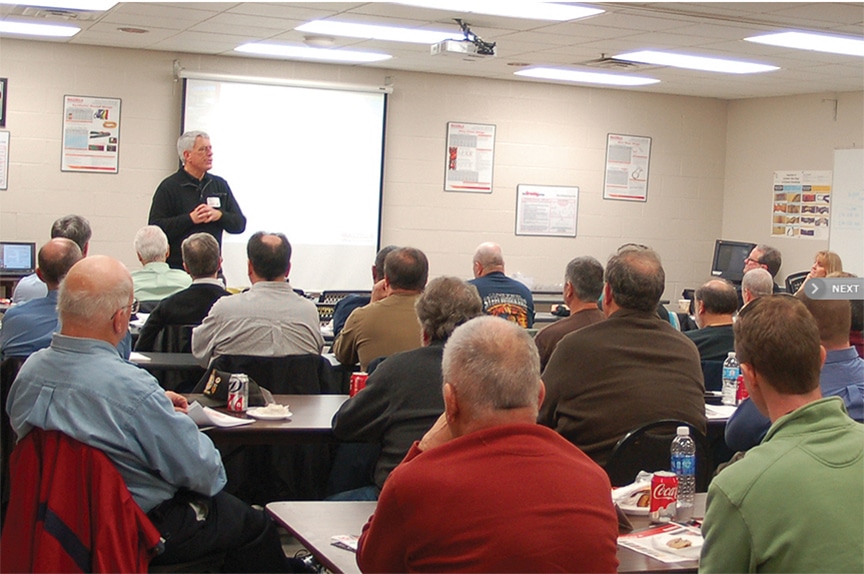
Spending money to purchase inspection tags and/or paying someone for their time to apply inspection tags to lifting gear may not be a cost-effective way to make sure your gear is safe to use and that your facility is in compliance with OSHA and ASME requirements.
Your money could be better spent on providing more thorough training for your operators, or by having inspections of your gear performed on a more frequent basis.
In theory, if your operators are properly trained to inspect their rigging gear prior to each shift, or prior to each lift, then any damage or irregularities to the equipment would be discovered and the item in question would be removed from service before it would ever be put into use. Then, when a third-party inspector comes in to fulfill the periodic inspection requirements, they’re really just validating that your company’s training program and internal workflows are working as intended.
Wrapping it Up
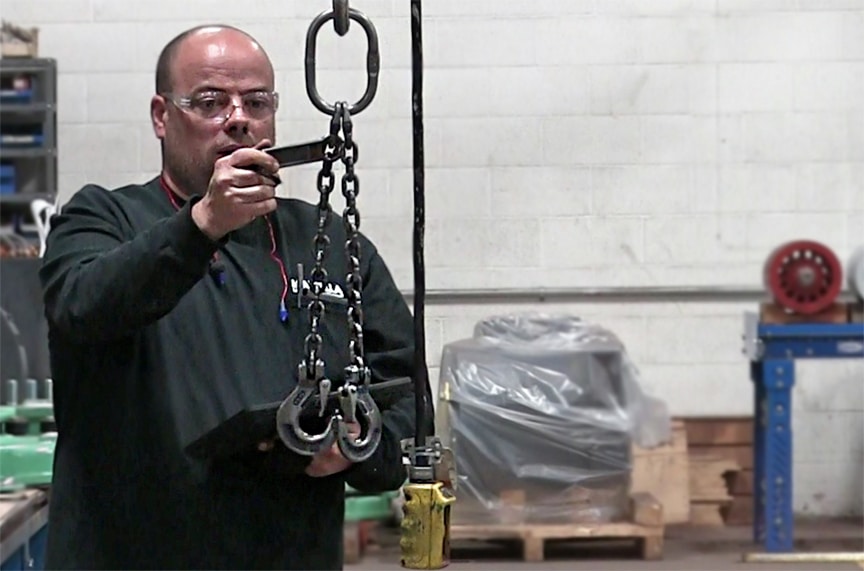
At Mazzella, we truly believe that proper training for riggers and operators is the best way to make sure that your lifting and rigging program is in compliance, and to protect your employees against potentially dangerous lifts.
If you require a specific training course for OSHA compliance for slings, hoists, and/or rigging hardware, we can assist you in creating a safe and reliable workplace. All Mazzella trainers have been accredited through Industrial Training International, Inc. We train to OSHA and ASME standards and can issue certificates of attendance following program completion.
We also perform rigging and below-the-hook inspection services that satisfy all OSHA and ASME requirements. If your company requires all inspected items to be tagged or marked, we will remove the old tags or markings, inspect the equipment, and apply any new tag or identifier to your equipment during the course of the inspection. However, the customer needs to understand that we do not manage the tagging program and are not responsible for any costs or liability associated with the tagging program.
If you’re interested in learning more about one of our lifting or rigging training programs, or want more information on our rigging inspection services, please don’t hesitate to contact us to speak with a Lifting Specialist.
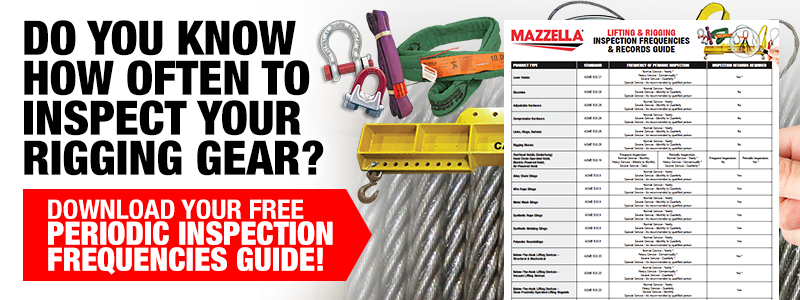
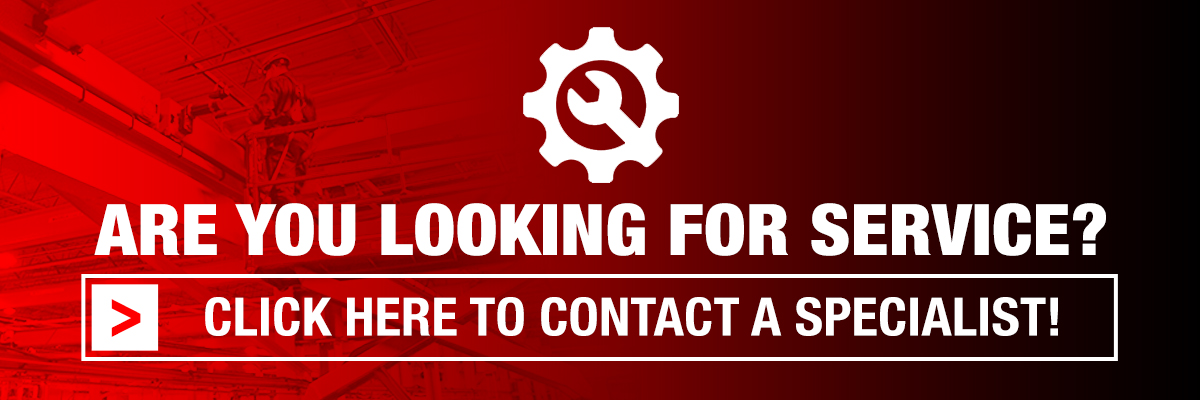
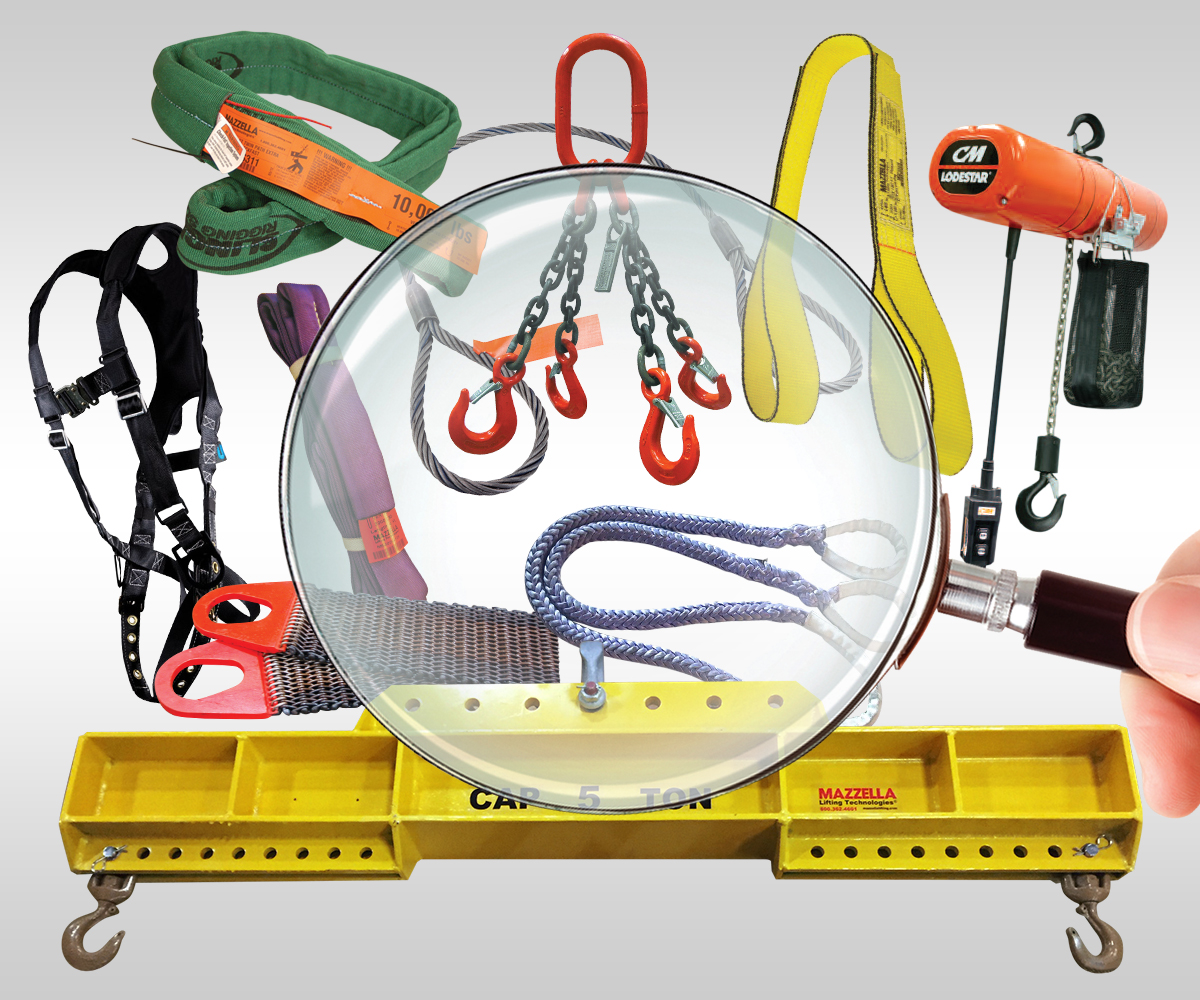
Rigging Inspection Services
OSHA 1910.184, ASME B30.9, B30.20, B30.26, & ANSI Z359 require periodic, documented inspections on slings, rigging hardware, lifting devices, and fall protection every 12 months, at minimum, and monthly to quarterly in more severe service conditions.
Call us at 800.362.4601 or click here if you need inspections for slings, rigging hardware, lifting devices, or fall protection!
Copyright 2018. Mazzella Companies.