How Do Twin-Path® Slings Compare to Wire Rope and Alloy Chain Slings?
With standard capacities up to 400 tons, Twin-Path® high-performance roundslings are as strong as steel, but are only about 10% of the weight of a comparable wire rope or alloy chain sling.
Are you tired of wrestling with steel slings that are heavy and unruly to rig onto a load? Are you hesitant to jump into the world of synthetic slings because you’re worried that they aren’t tough enough for your lifting application?
At Mazzella, we often get asked about alternatives to chain or wire rope slings that might save the end-user time, energy, and manpower when it comes to rigging a load. Singmax® Rigging Solutions offers a line of high-performance Twin-Path® roundslings that combine the strength and toughness of a wire rope or chain sling, with the weight-savings and ergonomics of a nylon or polyester sling. Twin-Path slings are a great alternative to steel slings and also hold up to the rigors of repetitive lifts better than most nylon and polyester slings.
For those of you who may be on the fence about converting to a synthetic sling, after reading this article, you’ll have a better understanding of:
- The technologies and extra engineering that separate Twin-Path slings from other synthetic slings on the market
- Common applications that Twin-Path slings are used for
- The benefits of using a Twin-Path sling
- Advantages and disadvantages of Twin-Path products compared to wire rope slings
- Advantages and disadvantages of Twin-Path slings compared to alloy chain slings
Twin-Path® Sling Design, Materials, and Construction
Twin-Path slings are a type of continuous (or endless) high-performance roundsling. They’re constructed from two individual paths of internal load-bearing fibers and two layers of outside covers that all work together as one sling.
K-Spec® Core Yarn
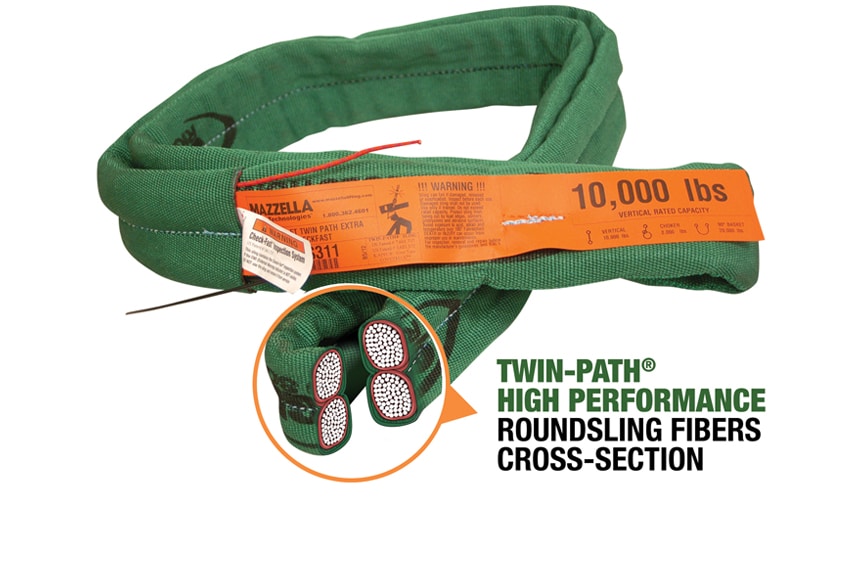
Twin-Path slings have two paths of load-bearing fibers made from a proprietary material called K-Spec® core yarn. K-Spec core yarn is approximately five times stronger than equivalent nylon and polyester fibers.
Besides their strength, K-Spec fibers have low stretch. The stretch is actually more comparable to the stretch that a steel sling might experience under load, than a traditional synthetic web sling or roundsling made of nylon or polyester fibers.
The two paths of K-Spec core yarn also provide redundancy if one path is damaged. If one core yarn is damaged, the second load-bearing path can still support a load to bring it down in a controlled manner. This helps to prevent catastrophic failure of the sling that could damage the load, nearby equipment, and/or injure nearby workers.
Covermax® Covers
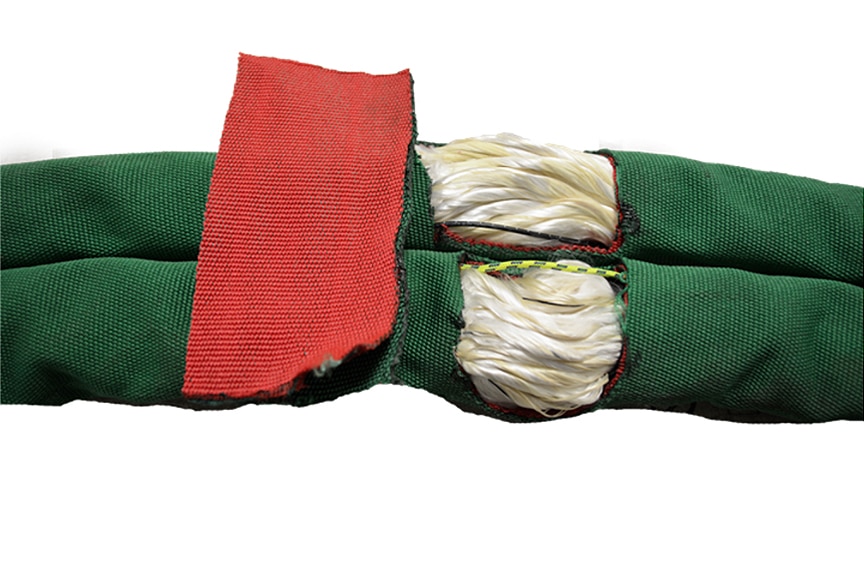
The outside of the sling has two layers of Covermax® bulk nylon covers designed to protect the internal core yarns. The top green layer provides abrasion resistance and the second layer provides another level of protection to the core yarns, but also is a visual indicator that the top cover has been damaged.
The heavy-duty, double-layer industrial nylon jackets have been tested to provide the best ultraviolet (UV) protection and the best abrasion protection of any synthetic slings.
When you perform a visual inspection of the sling prior to any lift, take the Twin-Path out of service immediately if you see any of the red cover. During the inspection, you should ensure that the internal core yarns have not been damaged.
A major benefit to the Covermax jackets is that they can be repaired by any authorized Slingmax manufacturer.
Check-Fast® Inspection System
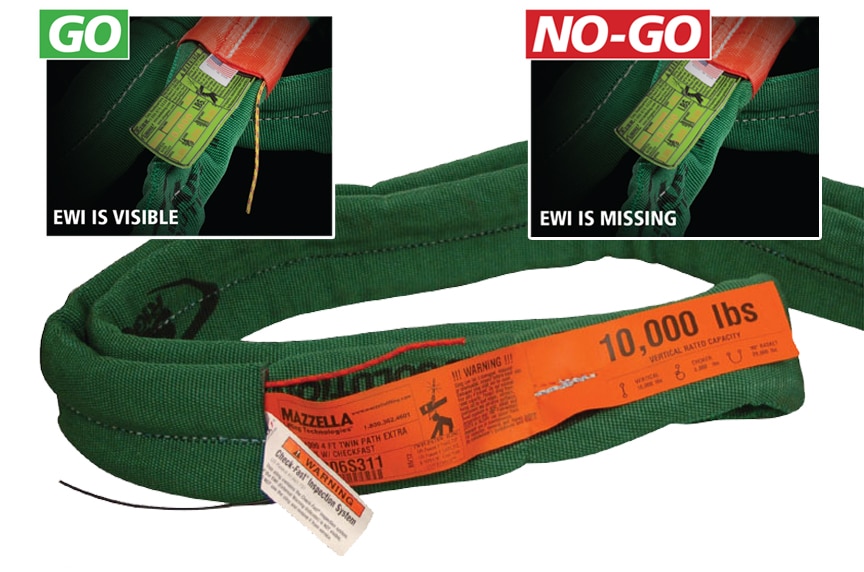
The Check-Fast® system is unique to Slingmax’s Twin-Path roundslings and acts as an external warning indicator (EWI) that sticks out from the cover and is an easy pass/fail inspection tool. If the sling is overloaded, the indicator is pulled into the sling and disappears before the sling fails. If during inspection, you don’t see it, the sling has been overloaded and needs to be removed from service.
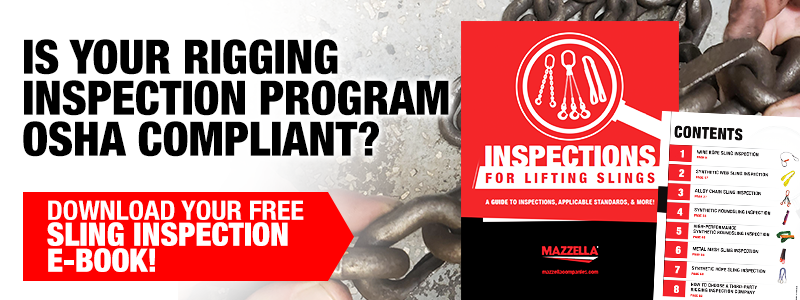
What Type of Applications Are Twin-Path® Slings Commonly Used In?
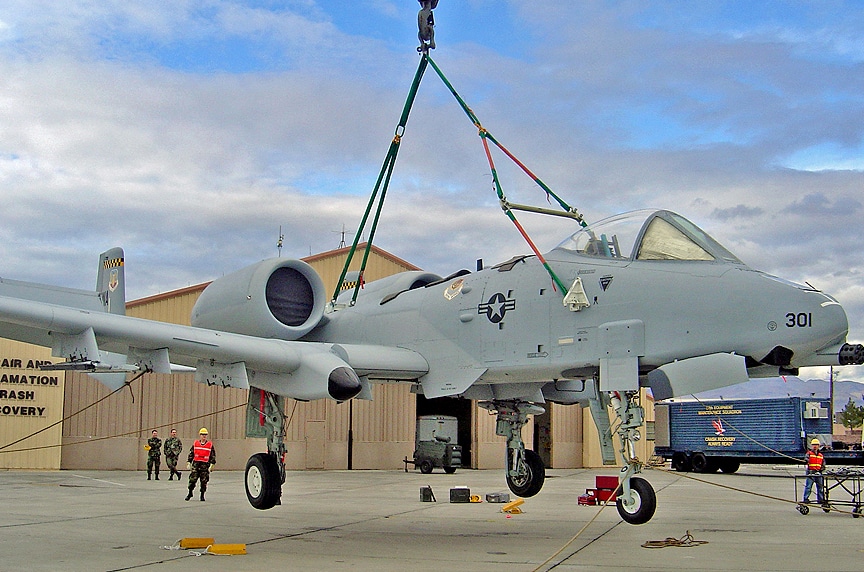
Due to their endless configuration, there may be some confusion about how roundslings are used in rigging. It’s easy enough to figure out a vertical hitch in a straight-line pull, but can it be used in other hitches like basket and choker?
Twin-Path slings can be used in vertical, basket, choker, double-wrap hitches, and used as part of multi-leg assemblies. Twin-Path slings are also commonly used in conjunction with below-the-hook lifting devices on specialized lifts.
Common applications of Twin-Path slings include:
- Construction
- Power industry (power generation and power distribution)
- Wind industry
- Offshore oil and gas
- Manufacturing and general industry (die lifts and other lifts that are repetitive by nature)
At Mazzella, we’ve even helped customers solve unique problems with Twin-Path products. One oil and gas customer used Twin-Paths as blowout preventers in the oilfield. One steel customer used Sparkeater® Twin-Path slings as a lightweight replacement for combination chain and large diameter wire rope slings they were using in an electric arc furnace.
What Are the Benefits of Using a Twin-Path® Sling?
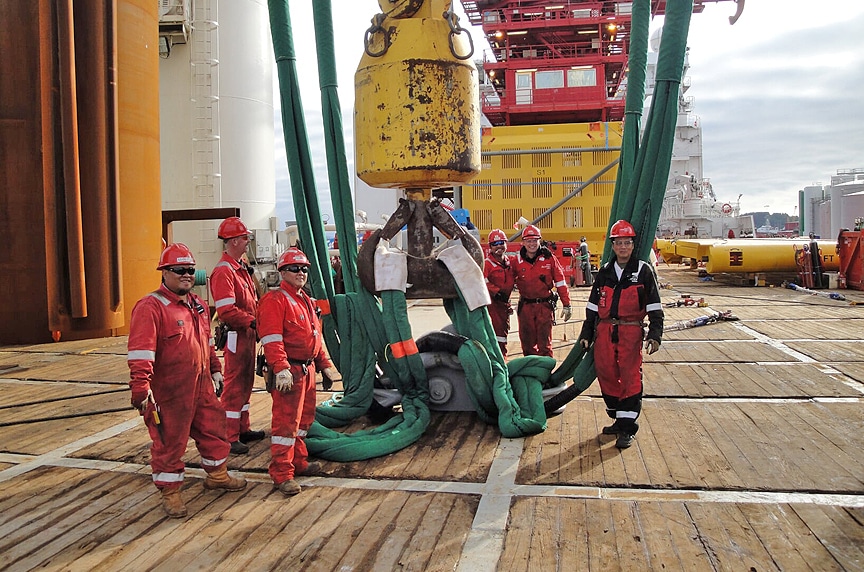
In this section, we’ll introduce some of the benefits to using Twin-Path slings and then cover those in more detail as we do a direct comparison to wire rope slings and alloy chain slings.
Twin-Path® Strength and Capacity
Slingmax offers their Twin-Path roundslings in standard capacities up to 400 tons with a 5:1 Design Factor. Higher capacities and custom design factors can be fabricated upon request.
Twin-Path® Weight Savings
Twin-Path slings are as strong as steel, but at about 90% of the total weight to a comparable wire rope or alloy chain sling. Twin-Path slings reduce the overall weight of your rigging equipment, which means your crane can lift closer to its full capacity by not having to account for heavy chain or wire rope slings.
Twin-Path® Ergonomics / Ease of Rigging
Twin-Path slings can be carried through a facility or job site and attached to a load by one person. In comparison, a high-capacity steel sling may require two to three workers and/or additional equipment like trucks or tow motors to move and set it in place. Companies who utilize Twin-Path products may also see a decrease in injuries to riggers who must lift heavy and unruly slings and wrestle them onto a load.
Twin-Path® Durability
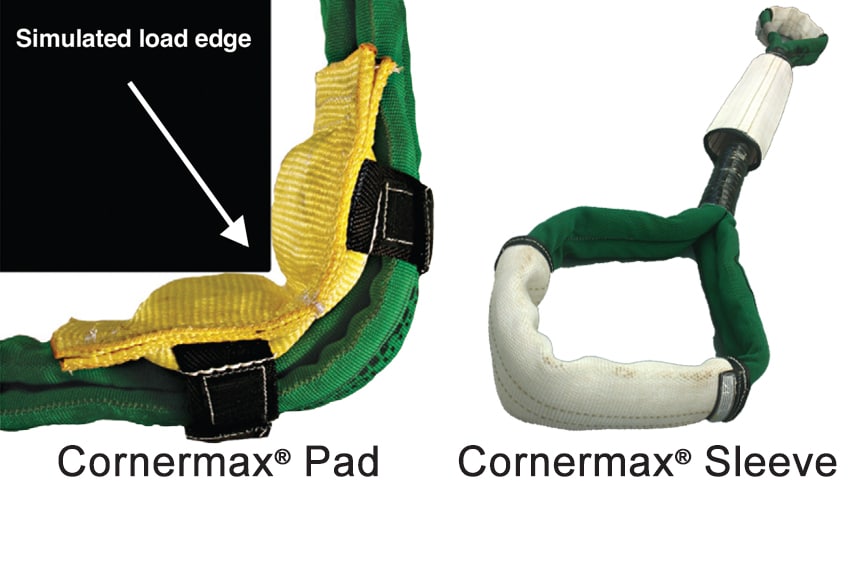
Slingmax offers three types of engineered edge and cut protection made from high-performance synthetic materials. You should always protect your Twin-Path slings from abrasion and cuts that could occur when the slings make contact with any edge of a load.
Slingmax’s engineered Cornermax products provide 25,000 lbs. of cut protection per inch of sling width. Sling protection should always be used when lifting steel beams, concrete, and any other objects with an edge that could cause abrasion or cut an unprotected sling.
Cornermax® Pad – this pad is designed to be used on 90° angles and creates a “tunnel” of cut protection, known as the “No Touch Zone” so that the corner of the load does not come in direct contact with the pad or the sling.
Cornermax® Sleeve – this sleeve is made from tough high-performance fiber and can be permanently or temporarily attached to the sling with Velcro. The sleeve wraps around the sling itself and is then put in position to protect it from any type of edge.
Synthetic Armor™ Pad – this pad protects slings from abrasion damage caused by contact with rough surfaces such as concrete beams and structures. They can also be used to protect delicate finished or painted surfaces from scratches and marring during the course of lifting and handling a load.
Twin-Path® Repairability
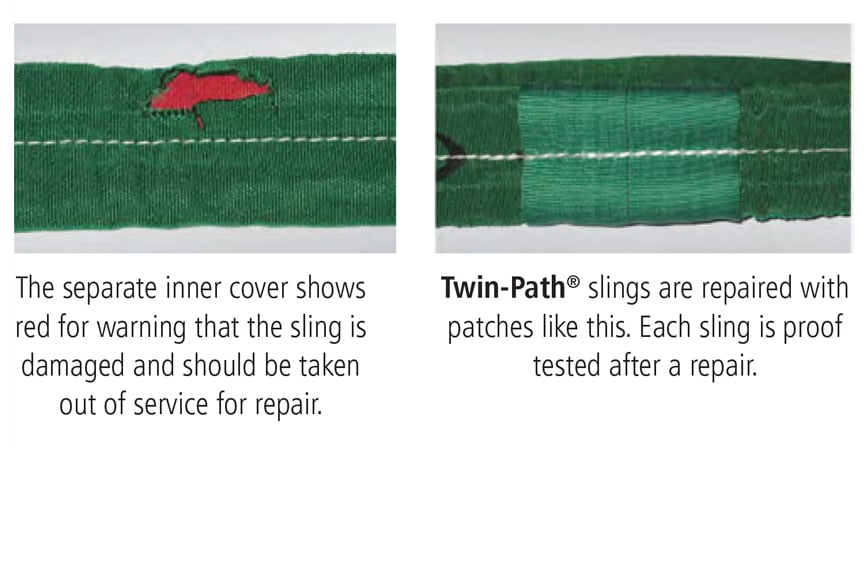
The Covermax covers protect the core yarns from abrasion, cutting, and ultraviolet (UV) exposure. Unlike wire rope and chain slings, the Twin-Path’s load-bearing fibers aren’t directly exposed to the load or environmental elements. This helps protect against abrasion, wear, and the synthetic materials aren’t susceptible to corrosion.
However, if damage on the outer green jacket does allow the red jacket to show through, the sling can be returned to a factory authorized dealer for inspection and repair.
Any holes, burns, punctures, cuts, wear, or abrasion can be cut out and patched on the outer jacket. If the internal core yarns have not been damaged, a Twin-Path sling can be inspected, repaired, and returned into service by a Qualified person.
Twin-Path® Slings vs. Wire Rope Slings
In this section, we’ll compare Twin-Path slings to standard wire rope slings.
Strength
Wire ropes slings and Twin-Path slings can go toe-to-toe when it comes to strength and lifting capacity. Slingmax catalogs their slings at capacities up to 400 tons, but can fabricate slings with an even higher capacity if requested.
Another similar feature is stretch under load. Both wire rope slings and Twin-Path slings have virtually no stretch while under load (less than 1%), so they’re both great solutions for low headroom applications and won’t cause the load to bounce due to stretch.
Weight-Savings
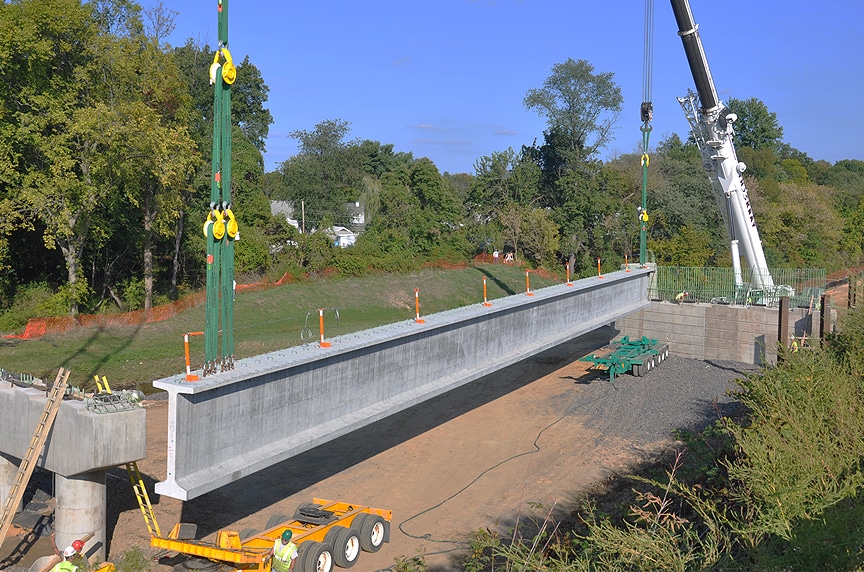
Twin-Path easily wins when it comes to significant weight-savings. Wire rope slings are heavy and cumbersome—especially when you start talking about large diameter wire rope slings used in heavy lifts.
Modular and precast construction is becoming more popular. As pieces used in the construction of buildings and bridges are arriving to job sites in larger finished sections, the lifts become larger, the cranes are bigger, and the slings need to be higher capacity to lift and secure the load. That results in heavier wire rope and steel slings. Or, Twin-Path slings can be used for those same lifts at approximately 10% of the weight of comparable wire rope slings.
Ergonomics
When you talk about high-capacity cranes and rigging with large diameter wire rope slings, you need to start including multiple workers, as well as equipment like trucks and/or forklifts, to move the rigging around the job site.
Wire rope slings can kink easily, which can cause the rigger to have to wrestle them onto a load. Multi-part wire rope slings are more flexible than single-part slings, but can still be heavy and difficult to maneuver in larger sizes.
Twin-Path slings are soft, lightweight, and snug down tight on a load. One person can carry and rig a load using a Twin-Path sling, so you can focus more energy on the job at hand and waste less time and manpower on attaching and removing the rigging.
Durability
One of the biggest misconceptions about Twin-Path slings is that they’re not durable enough to be used in tough industrial environments. When paired with proper edge protection, studies show that Twin-Path slings perform just as well, or better, than wire rope while exposed to an edge under load.
A wire rope’s load-bearing wires and strands are exposed to the load and can be worn down or broken through abrasion. The tough Covermax jackets on a Twin-Path help to protect the load-bearing fibers from direct contact with the load.
Repairability
When inspecting a wire rope sling, ASME B30.9 has certain allowances for broken wires per lay, and per strand, before a sling needs to be removed from service. These wires and strands cannot be repaired, so once a wire rope sling fails an inspection it shall be removed from service. Best practice is to destroy, render useless, and dispose of a failed or damaged sling.
On a Twin-Path sling, if the internal core yarns haven’t been damaged, the outer jacket of the sling can be patched and repaired and put back into service. Nicks, cuts, abrasion, punctures, and other damage to the jacket itself is cause for removal from service, but may not be retirement criteria for a Twin-Path sling if a Qualified person deems it repairable.
Twin-Path® Slings vs. Alloy Chain Slings
In this section, we’ll compare Twin-Path slings to alloy chain slings.
Strength
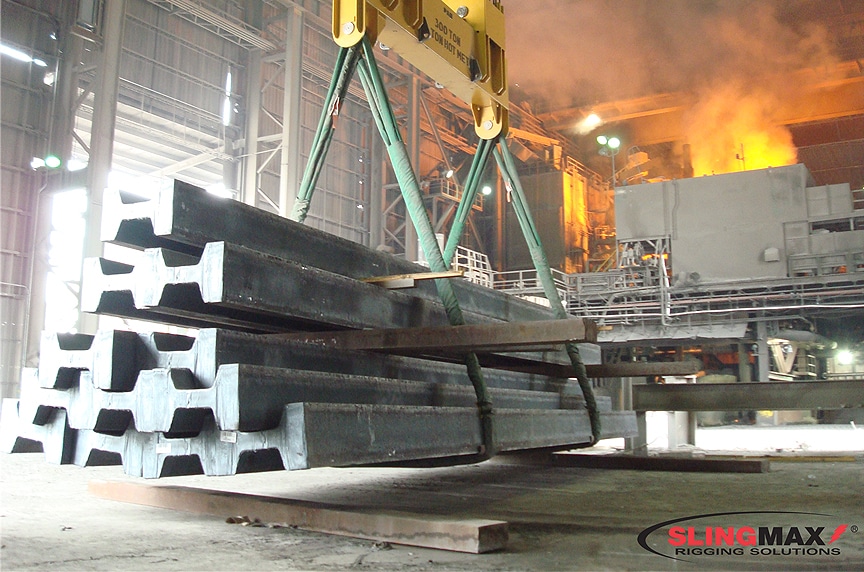
When it comes to toughness and dependability—alloy chain slings are the bulldogs of lifting slings. Chain slings are strong, durable, and can be used to lift very heavy and bulky loads on a regular and repetitive basis.
Slingmax catalogs their Twin-Path slings at capacities up to 400 tons, but can fabricate slings with even higher capacities, if requested.
Weight-Savings / Ergonomics
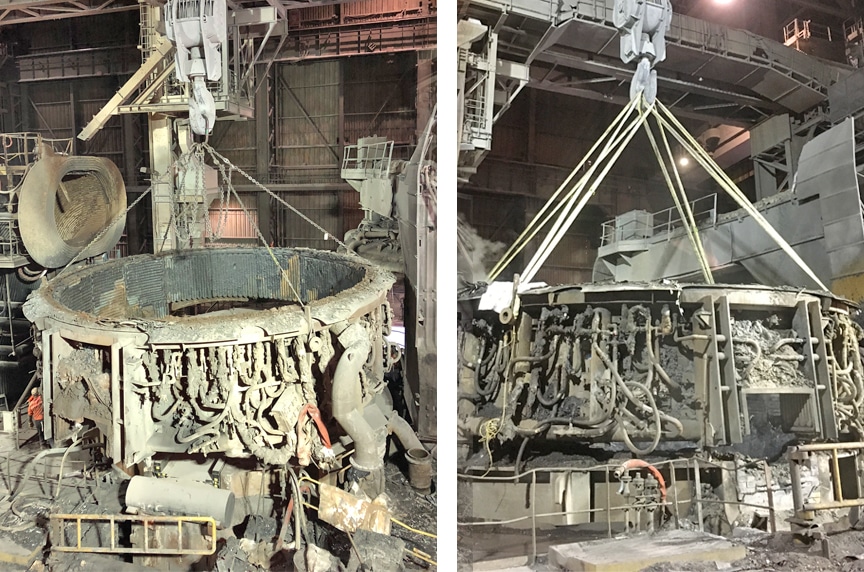
When it comes to alloy chain, we’ll discuss weight savings and ergonomics together, because alloy chain is very heavy. Even low capacity chain slings can weigh a lot—especially when you factor in multiple legs on a double, triple, or quad leg chain sling assembly. The higher the capacity of the sling, the heavier the chain will be. This can add significant weight to the rigging, when you factor in the total weight of the load.
Ask any rigger what their least favorite type of sling to rig with is and they’ll likely tell you it’s chain. Chain slings are heavy, dirty, difficult to run under and around a load, and can cause injuries if hands or limbs get caught in between the links.
At Mazzella, we have a unique example of how we helped a steel mill customer convert to Twin-Path slings used for the maintenance of an electric arc furnace upper shell.
Their existing slings weighed over 2,000 lbs. each and were a combination of alloy chain and large diameter wire rope. When the melt shop had to perform routine maintenance on the upper shell every 3-4 weeks, it required several workers, the use of a man lift, and took two or more hours from start to finish.
When we converted them to the higher heat-resistant Sparkeater® Twin-Path slings, their maintenance team immediately saw the following benefits:
- Significant reduction to the weight of their rigging equipment
- A more ergonomic solution that decreased the number of workers needed to perform the job
- Eliminated the use of a man lift to perform the swap
- Decreased the overall downtime of the mill’s equipment from 2+ hours to just minutes
- Cost savings of $2,000 each time this procedure was performed
Durability
Alloy chain slings will always be a popular choice for rigging because their flexible design provides strength and durability so they can withstand impact, extreme temperatures, and exposure to chemicals and UV rays.
Their strength and durability allow them to be used in foundries, steel mills, heavy machine shops, and any other environment where repetitive lifts or harsh conditions would damage or destroy a wire rope sling or synthetic nylon or polyester sling.
Twin-Paths can be used in tough industrial environments and do excel in general manufacturing and machine shops where repetitive lifts can cause fatigue and wear to other types of slings.
Extreme temperatures are a factor that should be considered when using Twin-Paths, as regular Twin-Paths are not recommended for applications above 180°F. For higher-heat applications up to 300°F, Slingmax offers a Sparkeater® Twin-Path sling that can be used. Any environment hotter than 300°F, would benefit from the use of alloy chain slings—with special considerations given to the decrease in W.L.L. rating provided by the manufacturer.
Repairability
Another benefit to chain slings is they can be repaired by replacing individual legs, individual chain links, or link segments. If any damage does occur on a chain sling, they are completely repairable and can be load tested-and re-certified after the repair.
We’ve discusses the repairability of Twin-Path slings as a major benefit to the end-user as well. During the course of an inspection, if the there is evidence of a puncture, tear, cut, or other damage on the outer jacket, the jacket can be patched and the sling can be put back into service.However, the sling must be removed from service and disposed of, if there’s any evidence of damage or overloading to the internal K-Spec core yarns.
Wrapping it Up
As you can see, Twin-Path roundslings match up well against the more traditional steel slings that many industries prefer for their lifting and rigging needs. If you think that Twin-Path products might be right for your lifting application, we have an in-house team of Lifting Specialists that can provide a consultation and make a recommendation on a Twin-Path sling solution for you.
At Mazzella, we’re part of an exclusive network of authorized Slingmax dealers. Our corporate headquarters in Cleveland, OH and our location in Virginia Beach, VA both manufacture, inspect, and perform authorized repairs on Twin-Path slings. We can fabricate slings in standard sizes and can fabricate slings in custom sizes, per customer request.
Contact us today, if you’re interested in starting a discussion about any of the following:
- Reducing the overall weight of your rigging equipment
- Providing your workers with a more ergonomic rigging option
- Replacing other synthetic products with a more durable solution
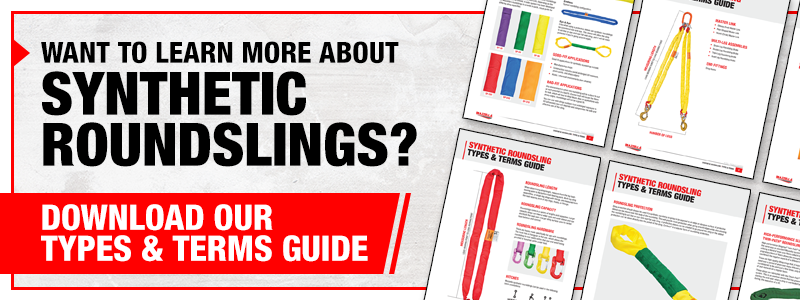
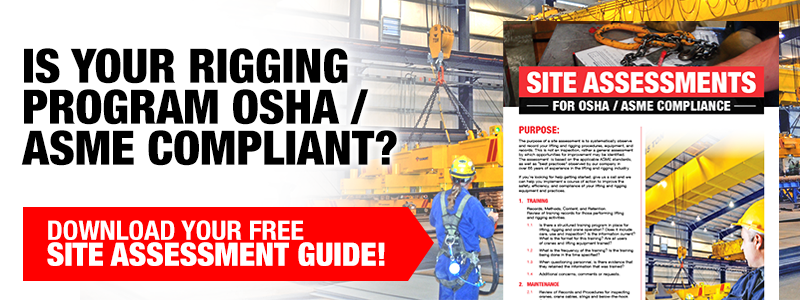
Copyright 2020. Mazzella Companies.