Five Most Common Problems Found in a Warehouse Rack Inspection
Have you ever wondered what warehouse rack inspectors are looking for? To help you stay informed, we asked our Warehouse Specialists the five most common problems they find during their inspections.
If you’re in the warehouse and distribution sector, you may be thinking about scheduling a rack inspection.
But you may also think an inspection is unnecessary. The racks you inherited seem to be doing great, and there are no glaring deformities.
The truth is, not all warehouse racks are created equal, and the problems that can lead to catastrophic failures can be hidden in plain sight. With warehouse pallet rack inspections, it’s important to be proactive instead of reactive.
At Mazzella, our Warehouse Specialists have decades of experience inspecting warehouses and their pallet racks—ranging from mom-and-pop operations to those owned by the largest corporations in the country.
To help you stay informed about the inspection process, we asked our team members about the five most common problems they see during a warehouse rack inspection.
By the end of this article, you will have answers to the following questions:
How Often Should You Inspect Warehouse Racks?
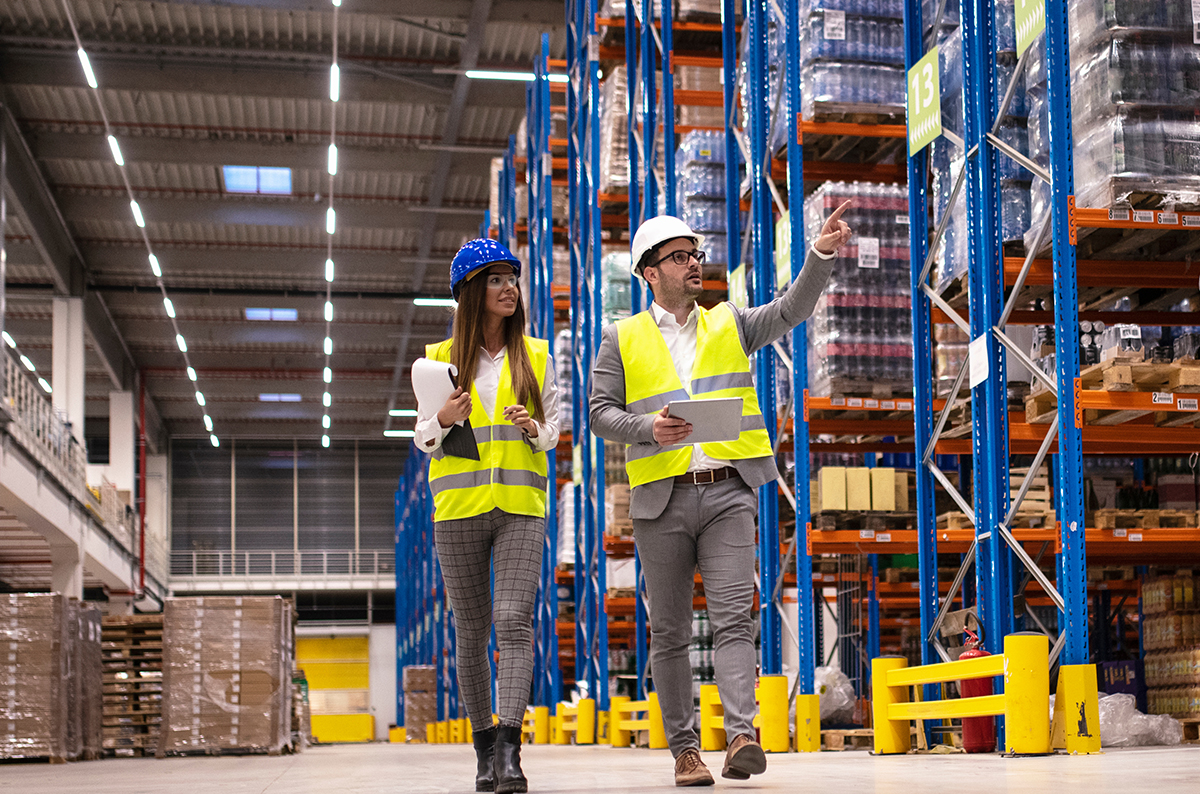
As discussed in our previous article, the biggest factors determining the cadence of your rack inspections are your facility’s size and daily use.
If you’re a mom-and-pop shop with a few dozen pallets and two forklifts, an annual inspection is your best option. Conversely, a major distribution facility with hundreds of bays, workers, and forklifts would benefit from a quarterly or monthly inspection.
Regardless of your operation’s size, you should never go a full calendar year without a rack inspection. You will also want to answer these questions:
- How many seasonal / temporary employees do you hire, who may not be properly trained?
- Do you have any deformed structural members?
- Are your forklifts running well, and do you use any forklift attachments?
- Has there been a major accident in recent weeks or months?
- When was the last time you got your racks inspected?
What are the Different Types of Warehouse Racks?
Warehouse racks can be split into two factions: structural and roll formed racks.
Structural racks are made from welded steel c-channels, and they have a reputation for being robust and strong. They are great for:
- Storing heavy pallets
- Preventing forklift damage
- Withstanding harsh work environments
If you are company with a fast-paced, repetitive, and hectic warehouse environment, structural racks are a great option. They are especially common in food and beverage distribution facilities
A roll formed rack is made by cold-rolling steel into thin, standardized components through a roll forming machine. Their thinner, lighter material makes them great for storing lighter pallets and constantly changing inventory. You can find roll formed racks in retail and third-party logistics centers.
Because of their ease of assembly, roll formed racks are exceptionally adjustable and flexible, allowing you to make customizations for storing seasonal / temporary products. While they are more affordable and easier to install than a structural rack system, their light material makes them more susceptible to forklift damage.
What are the Five Most Common Problems Found in a Warehouse Rack Inspection?
1. Damage to Uprights and Beams
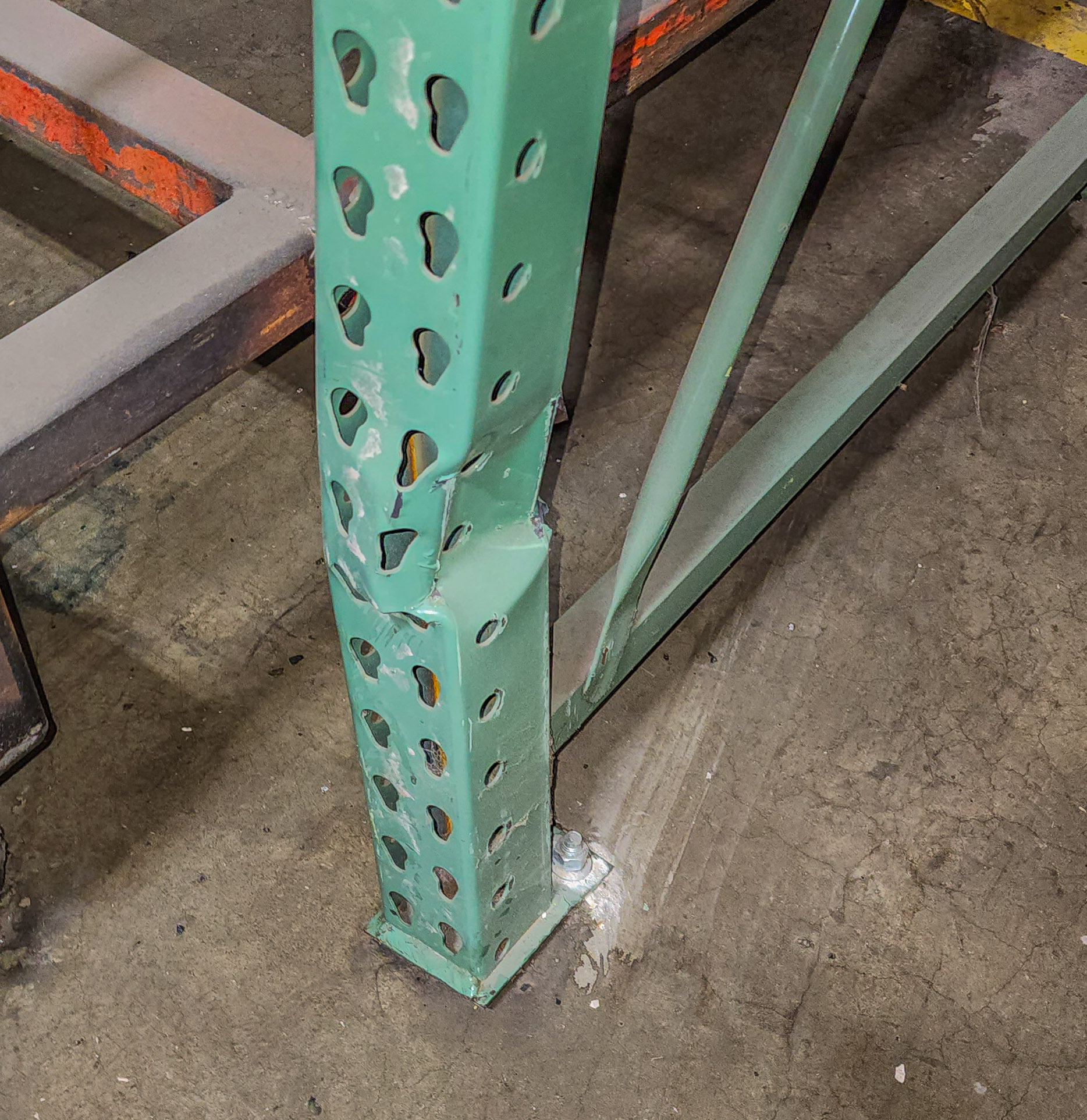
Damage to uprights and beams is the most common problem our warehouse experts encounter. The biggest culprit for beam damage is forklifts, which to our estimates, is responsible for about 90-95% of rack damage. (Corrosion is a distant second.)
Damaged uprights or beams directly affects the structural integrity of your rack, compromising their load-carrying capacity. Other signs of structural integrity issues include:
- Broken welds
- Sheared anchors
- Damage to locking pieces
2. Missing Safety Clips on Beams
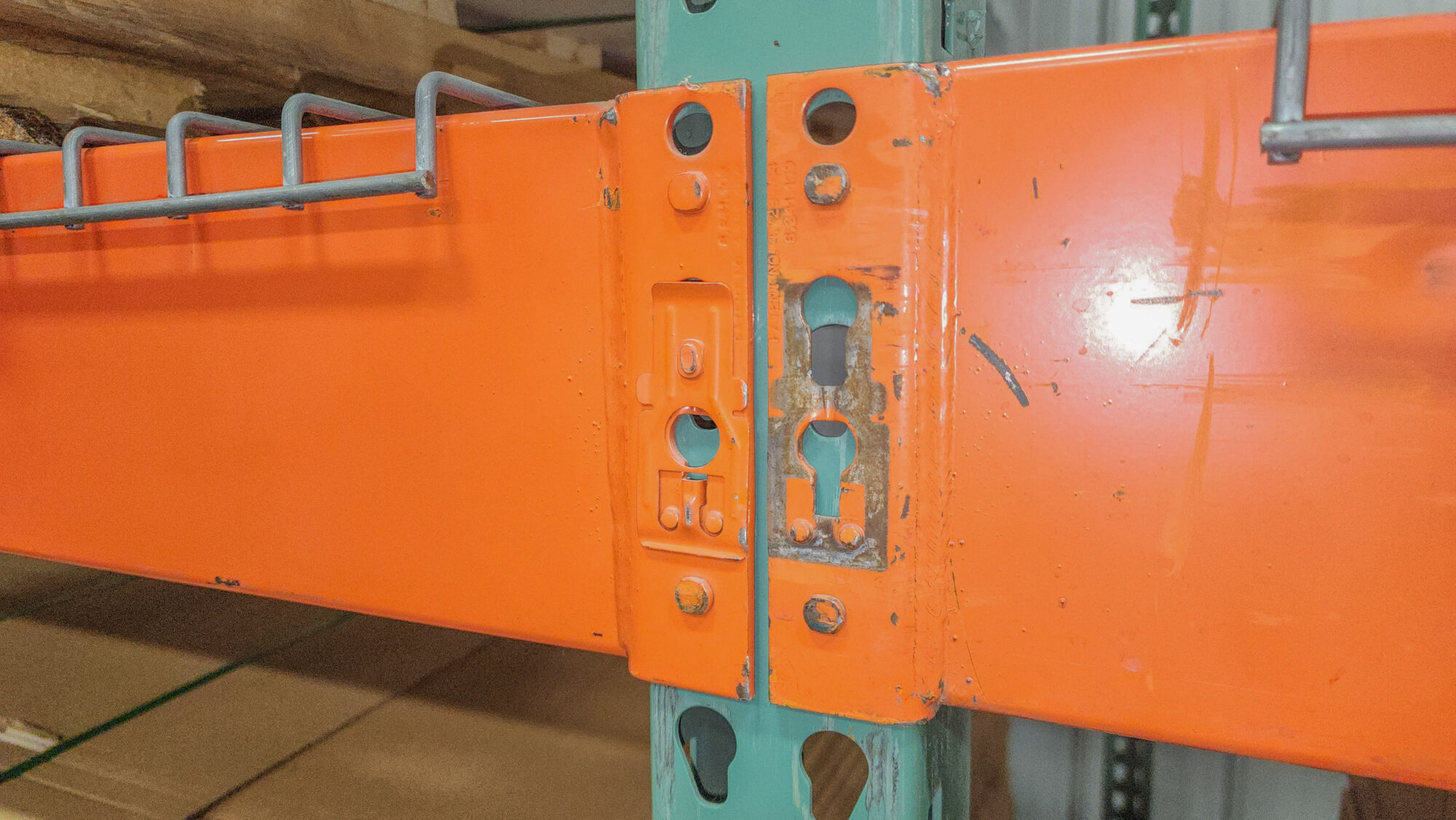
Sent from the manufacturer, safety clips attach to the rack’s pallet to reduce disconnection. The safety clip has a peg on it that pops into place, and it’s there so if a forklift carries a load too high, and those beams are bumped from the bottom, they stay in place.
Without a safety clip, the forklift could dislodge the beam above, and that level could come down.
The issues start when, years later, people decide to change the beam’s elevations levels. They get up there, take a flat screwdriver, and pry the safety pin out because it’s in the way. From here, it breaks off or is bent outwards, they readjust the rack, and a safety clip never goes back on.
3. Missing Wire Deck Over Walkways
Wire decks basically act as a heavy-duty safety net underneath your product. If you were to get under the rack and look up, you should not see just the bottom of a palette with no support underneath it.
If the operator didn’t set a pallet on properly, and a rack system is hit by a forklift with no wire deck underneath, that palette becomes dislodged and collapses, putting employees walking underneath at serious risk injury or death.
Thankfully, wire decks are very affordable, ranging from $40-$100 a bay. They also range in capacity, so assess your current pallet weight before purchasing one.
4. Missing or Damaged Anchors

Missing or damaged anchors are a common cause of catastrophic failure, where the rack’s structure completely collapses. Some companies want to adjust the height of a rack or move it somewhere else. They will move it without anchoring it to the floor, so they can change it if they don’t like the location.
If a forklift operator bumps into a rack with a missing anchor, it could create a domino effect with nearby racks. Additionally, in older facilities, anchors can be damaged from years of wear and tear. A competent warehouse rack inspector should be able to tell you which anchors need to be replaced.
5. Improperly Sized Rack Members or System Configurations
When organizations purchase a warehouse with existing racks, they’re ecstatic.
“Instead of spending thousands of dollars on new racks, we will just use these instead.” And while it’s an understandable mindset, it’s important that your organization drops the idea that racks are a one-size-fits-all solution.
You may be a lead molding company using racks originally intended for storing Styrofoam cups and utensils with a 2,000 lbs. capacity, when you need a minimum 6,000 lbs. capacity.
Our warehouse specialists commonly see inherited racks without proper capacity or rating postings, too.
Who Should Perform Your Warehouse Rack Inspection?
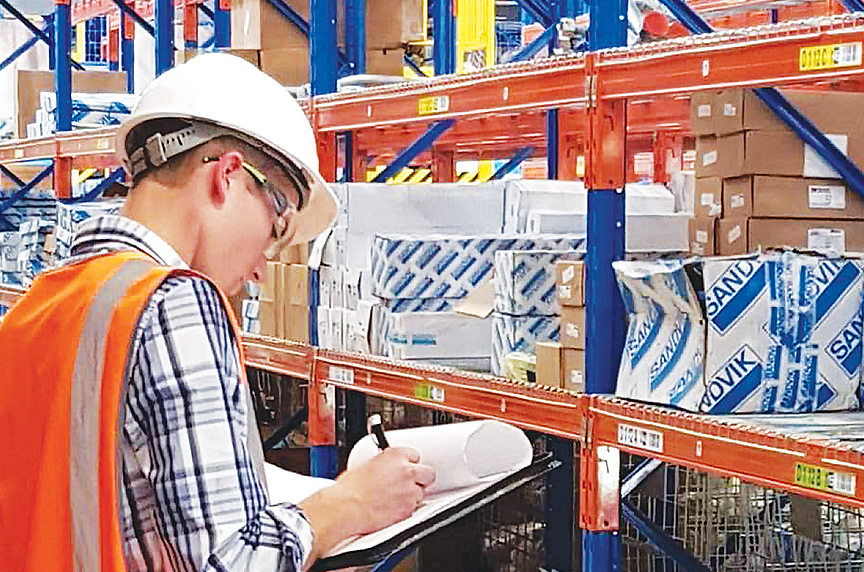
Opting for a third-party rack inspection is a great way to check the integrity of your racks.
It offers you an unbiased and accurate assessment of your warehouse pallet racking system’s condition—removing the potential of implicit biases from your internal safety coordinators.
While current industry standards say any “experienced” professional can perform a rack inspection, there is no set criteria for what makes someone an expert. Technically, someone with less than six months of industry experience could perform an inspection.
Having a qualified third-party inspector come into your facility not only saves you from paying hefty OSHA fines, but it also gives you access to unbiased industry experts with decades of experience.
Who Do I Contact if I Need a Rack Inspection?
It’s inevitable your racks will be damaged, and that’s okay. Warehouses are tough, hectic environments, and it can be difficult to keep up with inspections when the holiday season approaches, there are labor shortages to address, and the warehouses themselves are the size of small towns.
At Mazzella, we understand that our customers are not rack professionals, and we want you to stay focused on keeping your daily operations afloat. Contact one of our Warehouse Solutions Specialists if you want to discuss further. If you want to learn more about Mazzella’s rack inspections process, read our Rack Inspections Brochure.
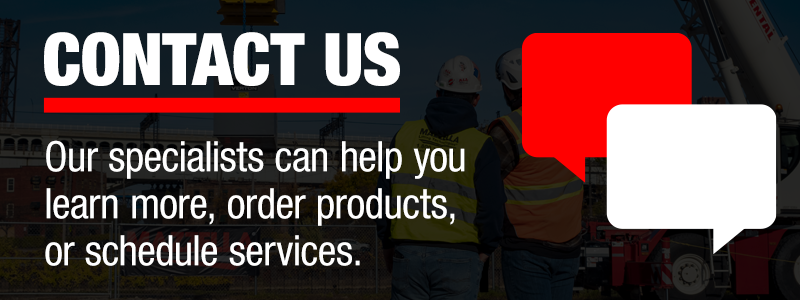
Copyright 2024. Mazzella Companies.