Considerations for Maintaining Load Control When You Rig Your Next Lift
Even if a load is perfectly rigged according to its weight, without proper load control, the lift could fail and cause serious injury and damage. In order to safely and successfully rig and lift a load, it is imperative for the rigger to ensure load control is maintained.
It goes without saying that safety is the most important consideration when it comes to rigging a load for an overhead lift. In order to safely and successfully rig and lift a load, it is imperative for the rigger to ensure load control is maintained.
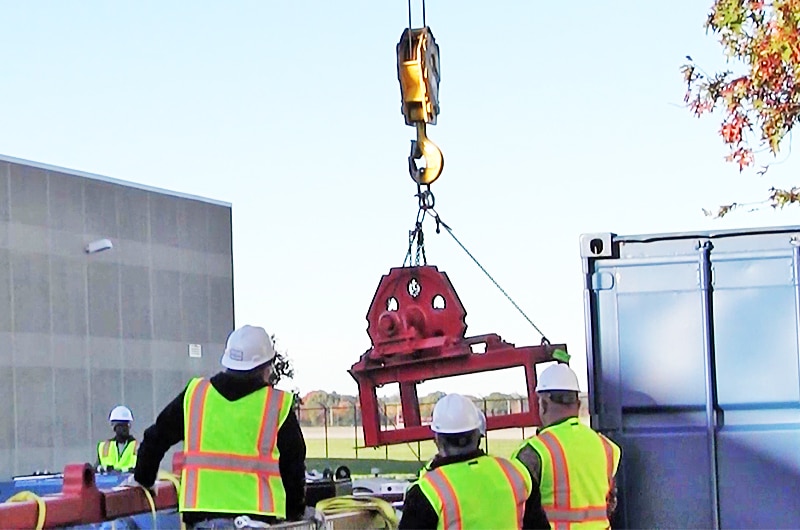
There are many factors for the rigger to consider when it comes to load control. Could the wind cause the lift to go awry? Will the sling and hitch properly support and distribute the weight of the load? Are additional measures needed to ensure the load is lifted and moved along the planned path?
Even if a load is perfectly rigged according to its weight, without proper load control, the lift could fail and cause serious injury and damage.
Rigging and maintaining load control is a complicated process that requires careful and educated planning. In order to maintain load control, a rigger should consider these factors when planning a lift:
- Know the weight of the Load
- Determine the center of gravity
- Select the appropriate lifting and rigging equipment
- Select the appropriate sling hitch
- Be aware of possibility of fouling / clear of personnel
- Determine whether a tag line is needed
- Be aware of environmental conditions
- Understand load stabilization
Know the Weight of the Load
Obviously, one of the most important things in maintaining load control is to ensure that you properly rig and lift the load according to its weight.
Oftentimes, the item being lifted may have the weight marked on it. Or, if it’s a load that you regularly lift and move through your facility, you will already know the weight of the load.
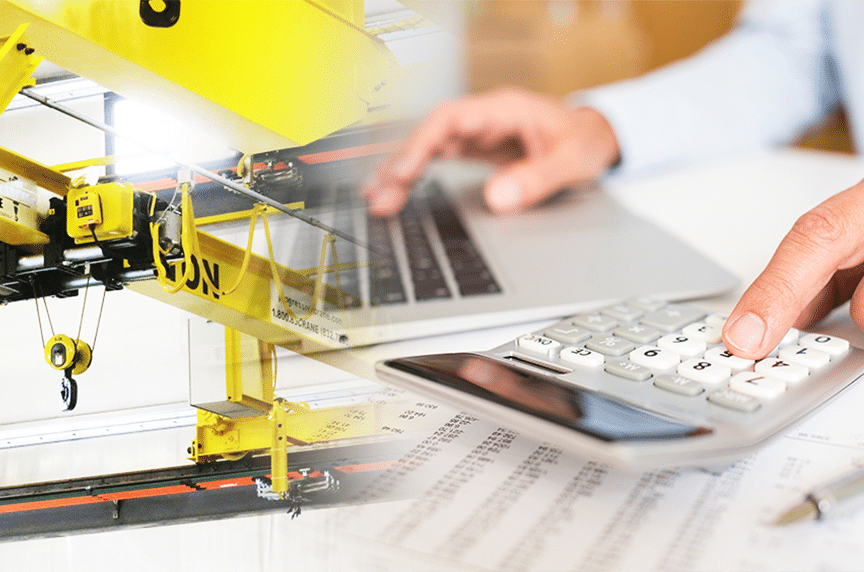
If you don’t already know the load weight or it isn’t marked on the load, there are several ways to determine the weight of the load, including:
- Review bill of lading or shipping documentation
- Refer to engineered prints or design plans
- Use an industrial scale
- Refer to the manufacturer’s specifications or catalog data
- Use load cells or dynamometers
If none of those options are do-able, the only method left is to calculate the weight of the load yourself based on the type of material and its dimensions.
NOTE: When calculating the total weight of the load, all rigging equipment used to rig the load should be included. This means that the weight of the slings, rigging hardware, below-the-hook lifting devices, etc. used in the lift must be calculated into the total weight lifted.
Determine the Center of Gravity
In order to safely lift the load, the rigger must first locate the center of gravity (COG). One, easy way to do this is to rig the load and slowly lift it just a few inches from the ground and observe where the load’s weight shifts.
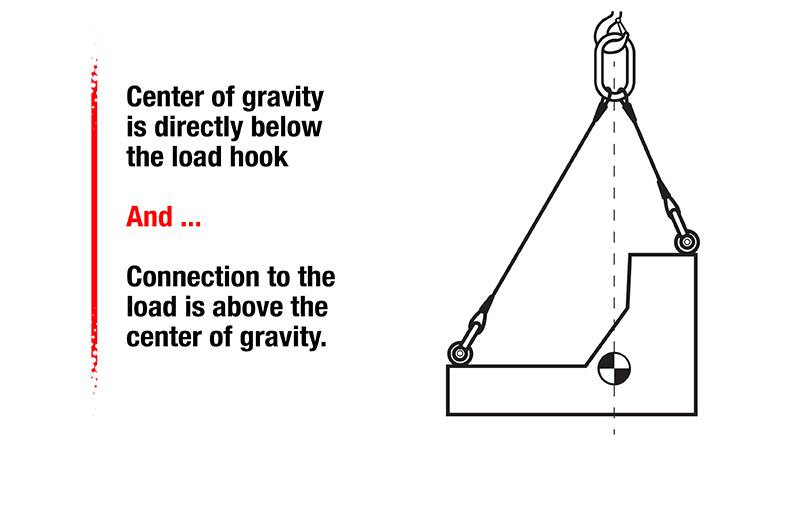
Once you have located the COG, you should rig the load to ensure that:
- The COG is directly below the load hook
- The connection points to the load are above the COG
If the connection to the load is below the COG, this can cause the load to flip upside down which could result in shock loading and a failed lift.
If the load hook is not directly above the COG, when the load is lifted it will shift / swing toward the load’s COG. An aggressive shift toward the COG can cause the load to topple.
Improperly rigging the load in accordance with the COG can lead to the rigger losing control of the load and causing damage to the load, nearby structures, or employees on the job site.
Select the Appropriate Lifting and Rigging Equipment
There are different types of rigging equipment and hardware that can be used to control a lift, including:
- No touch hand tools
- Rigging hardware such as shackles, eye bolts, hoist rings, etc.
- Below-the-hook lifting devices
- Lifting hooks with latches
No Touch Hand Tools
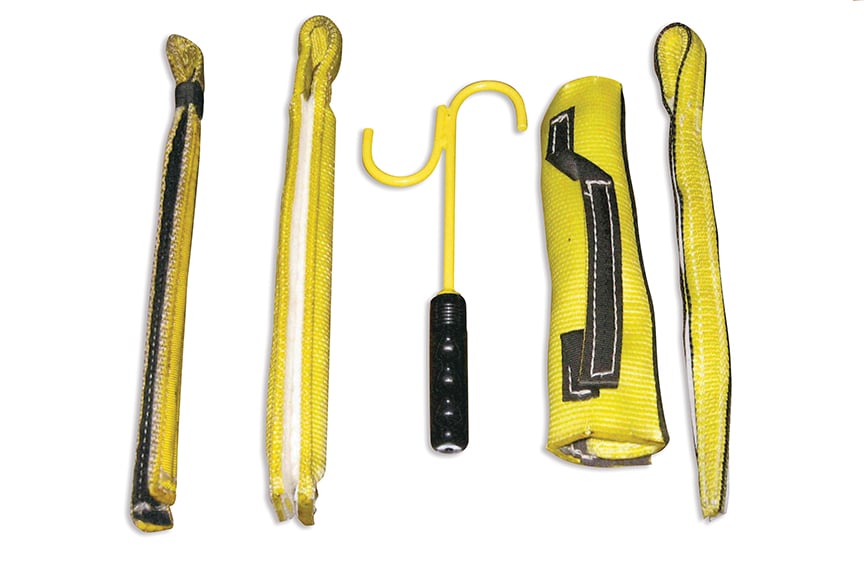
No touch hand tools are used when a load contains pinch points and it is not safe to touch or manipulate with your hands. These tools are used to handle and manipulate the load without physically touching it.
Rigging Hardware
Rigging hardware—hoist rings, swivels, shackles, etc.—is often used in conjunction with lifting slings. The hardware can be used as an intermediate hookup to connect slings to the load or crane hook or even to other slings. Rigging hardware can also be used as a hookup point directly from the load to the hoist or crane hook.
Below-the-Hook Lifting Devices
When a load is extremely wide, large, or uniquely shaped, a below-the-hook lifting device can come in handy. Because these devices are customized, they offer more load control and support than traditional rigging. Below-the-hook lifting devices can be customized to lift metal coils, furnaces, pallets, and much more.
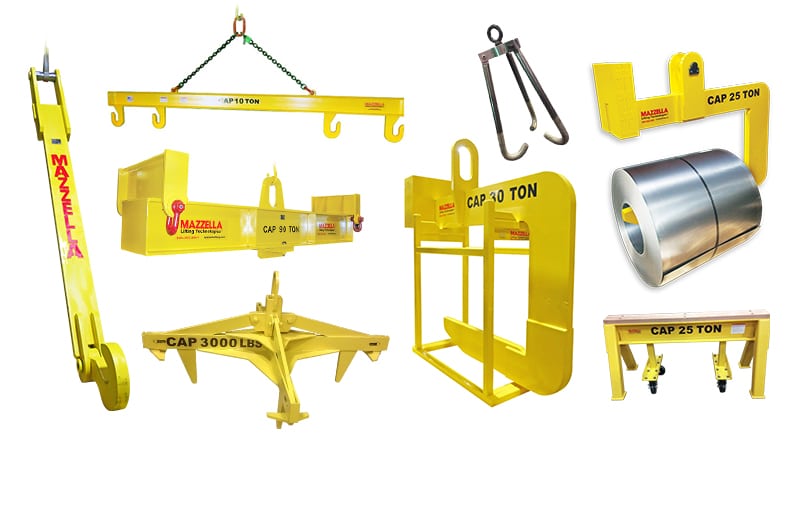
Spreader beams and lifting beams—two specific types of below-the-hook lifting devices—can be used to create lifting points on a wide surface or heavy-duty load so as to more evenly distribute the weight of the load.
Lifting Hooks With Latches
When deciding on whether or not to use a hook latch, careful consideration must be given to the specific lifting application.
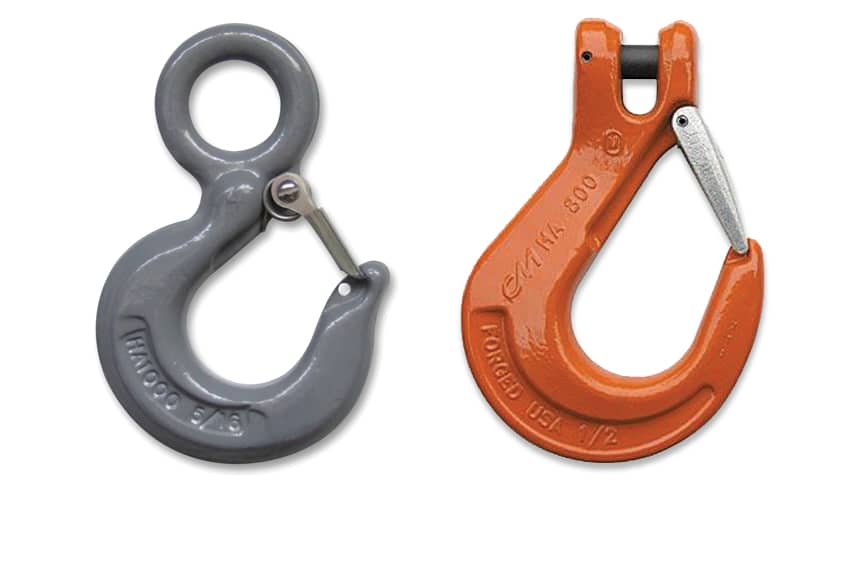
The use of latches on hooks is a topic that is constantly up for debate in the lifting and rigging industries. While some people argue that hook latches are always required and should always be utilized, others argue that latches are not required.
OSHA requires that “slings shall be securely attached to their loads.” They recognize that the use of a hook with a latch is one way of securely attaching a sling to its load. As an organization, Mazzella Companies recommends that hook latches should be used.
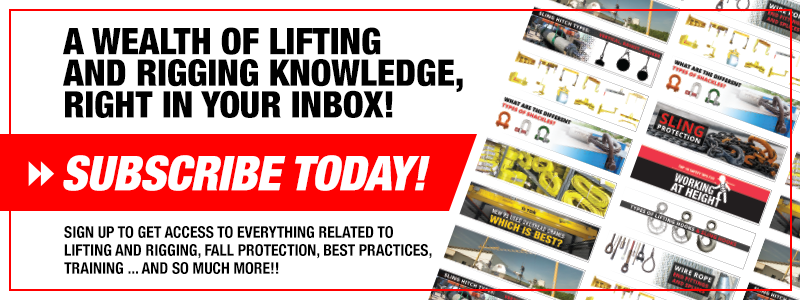
Select the Appropriate Sling Hitch
Depending on the type of load you are lifting, you will probably use one of these three basic types of slings hitches:
- Vertical
- Choker
- Basket
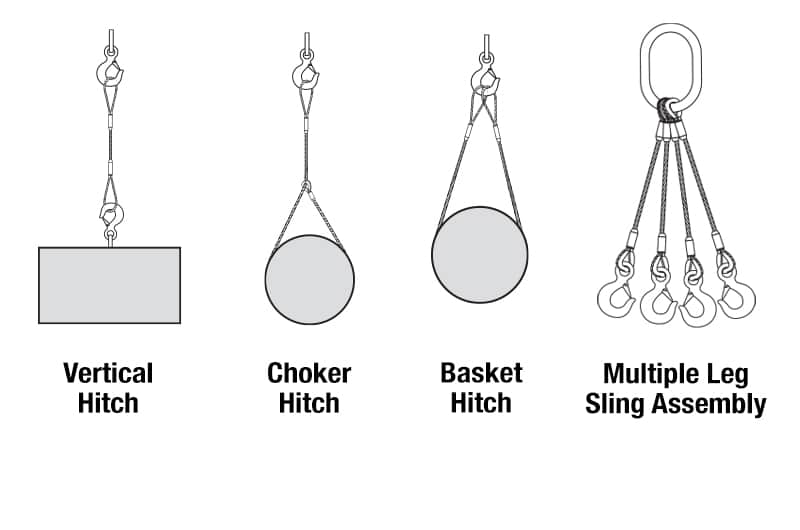
A vertical hitch is the most susceptible to load twisting and swaying, and may require the use of tag lines to ensure that the load does not swing into a nearby structure. Vertical hitches should not be used for lifting loose, long materials that may tip when lifted—for example, a bundle of pipes.
Choker hitches should not be used to lift loads that are loose or unbalanced. In some cases, choker hitches can be used on loose or unbalanced items if they are double-wrapped around the load.
Basket hitches should not be used on loads that are difficult to balance—they are most effective on evenly-balanced loads.
In cases where one of the three basic hitch types are not the best option for rigging the load, a rigger might resort to using a multiple-leg sling assembly. These assemblies allow the rigger to make multiple connection points to the load, thus increasing stability and control.
Be Aware of Possibility of Fouling / Clear of Personnel
The term “fouling” refers to an instance where the load comes into contact with an unexpected object in its path. Fouling your lift could cause any number of dangerous situations, including:
- The load spinning out of control
- Knocking down a nearby structure
- Dropping the load
It’s also important, for obvious safety reasons, to ensure that the path your load will travel during the lift is clear of personnel.
Personnel should always be a safe distance from the lifted load and should never be present underneath a lifted load. The “fall” zone—where the load would fall if the rigging should fail—should always be avoided during a lift.
Before every lift, it is imperative to scan your surroundings for any possibility of fouling and ensure that all personnel are out of the “fall” zone.
Determine Whether a Tag Line is Needed
OSHA §1926.1401 defines a tag line as a “a rope (usually fiber) attached to a lifted load for purposes of controlling load spinning and pendular motions or used to stabilize a bucket or magnet during material handling operations.”
Tag lines allow workers to control a moving load for the duration of its lift. They are particularly useful in situations where a large or wide load is prone to rotation or swaying. The riggers can attach the tag line to the load and control its movement at a safe distance away from the load.
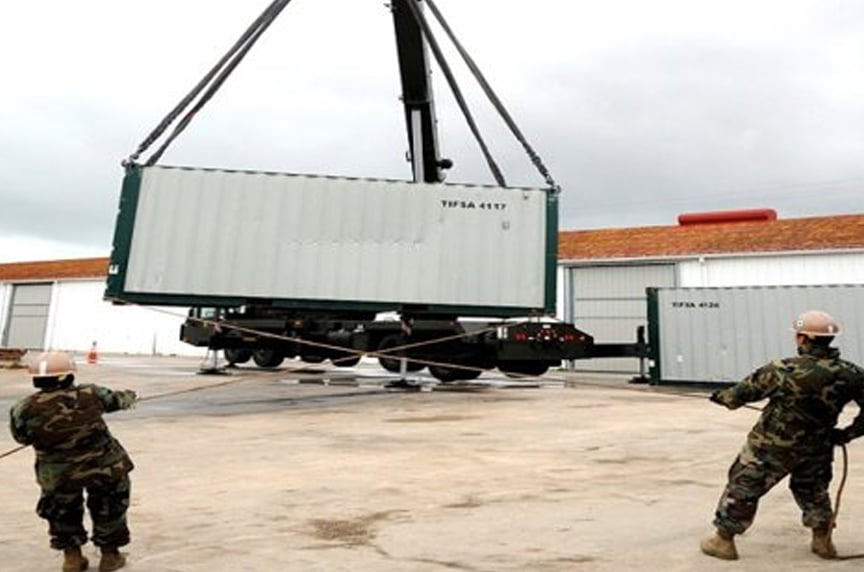
While they can be very useful in controlling a load, tag lines should not be used in instances where they may cause a safety hazard. Such instances include:
- If the rotation of the load is too excessive to be controlled by a tag line
- If there is not enough room or if the tag line is not long enough for the worker to stay a safe distance from the lifted load
- If the worker does not have a clear path to walk along during the duration of the lift where they won’t have risk of tripping or snagging the line and are out of the “fall” zone
Be Aware of Environmental Conditions
In cases where job sites are either outdoors or in facilities that have large bay doors, environmental conditions play a factor. Anytime that wind or other extreme environmental condition—snow, ice, extreme temperature—is present, load control may be affected.
As you probably guessed, wind can cause a load to sway and spin out of control. Tag lines, swivels, and other load control equipment listed above can be used to mitigate the effects of wind on load control.
Other extreme conditions—snow, ice, extremely low or high temperatures—can have an effect on load control.
Understand Load Stabilization
A rigger must account for any contents of a load that may shift during a lift and stabilize it before the lift takes place. This is especially important in situations where a lifted container is filled with something that may easily shift—like fluid or sand.
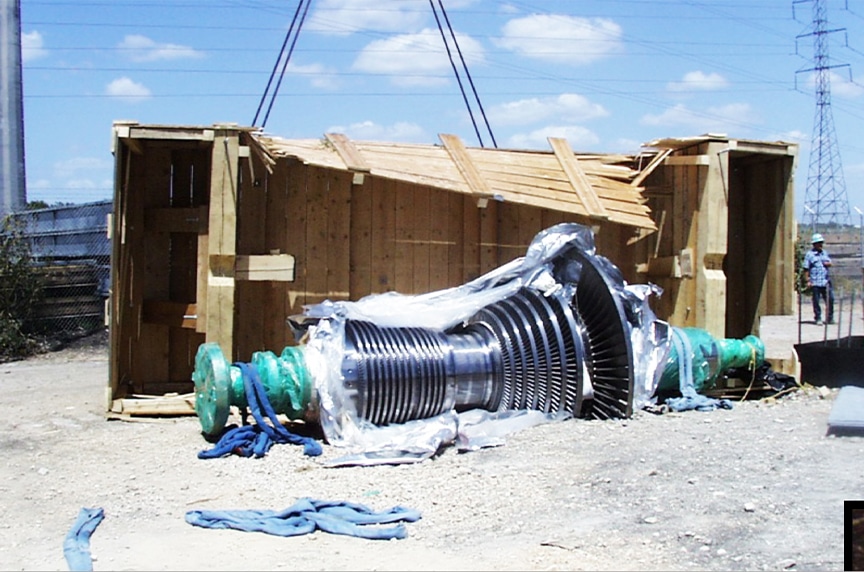
Containers that are only partially full are the most problematic to lift, as the contents inside may rapidly shift to one side of the container and cause the rigger to lose control of the load. When possible, containers should either be lifted completely empty or completely full.
A container that is being lifted must also be structurally sound. If it is not structurally sound—has a leak, parts are rotting, etc.—the container itself could cause the load to fail.
Wrapping It Up
Rigging is a complex process requiring extensive knowledge to do so successfully and safely. In order to do their job, riggers must understand the many factors that can cause a load to become unruly or unbalanced.
Even if a load is perfectly rigged according to its weight and equipment working load limits, the entire lift could fail because basic load control considerations were neglected. There are several considerations to be aware of when it comes to maintaining control of a load, including:
- Know the weight of the load
- Determine the center of gravity
- Select the appropriate lifting and rigging equipment
- Select the appropriate sling hitch
- Be aware of possibility of fouling / clear of personnel
- Determine whether a tag line is needed
- Be aware of environmental conditions
- Understand load stabilization
All of these considerations can have an effect on load control. It’s extremely important to be aware of all situations that could cause you to lose control of a lift and take steps to plan, prepare for, and prevent them.
We hope that this article helped you to become aware of the important considerations for maintaining load control during your next lift. If you need assistance in putting a lift plan together or want to schedule a site assessment of your rigging equipment and practices, contact us today to speak with a Lifting Specialist.
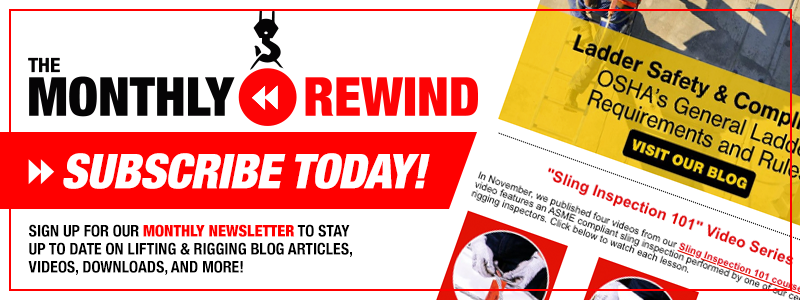
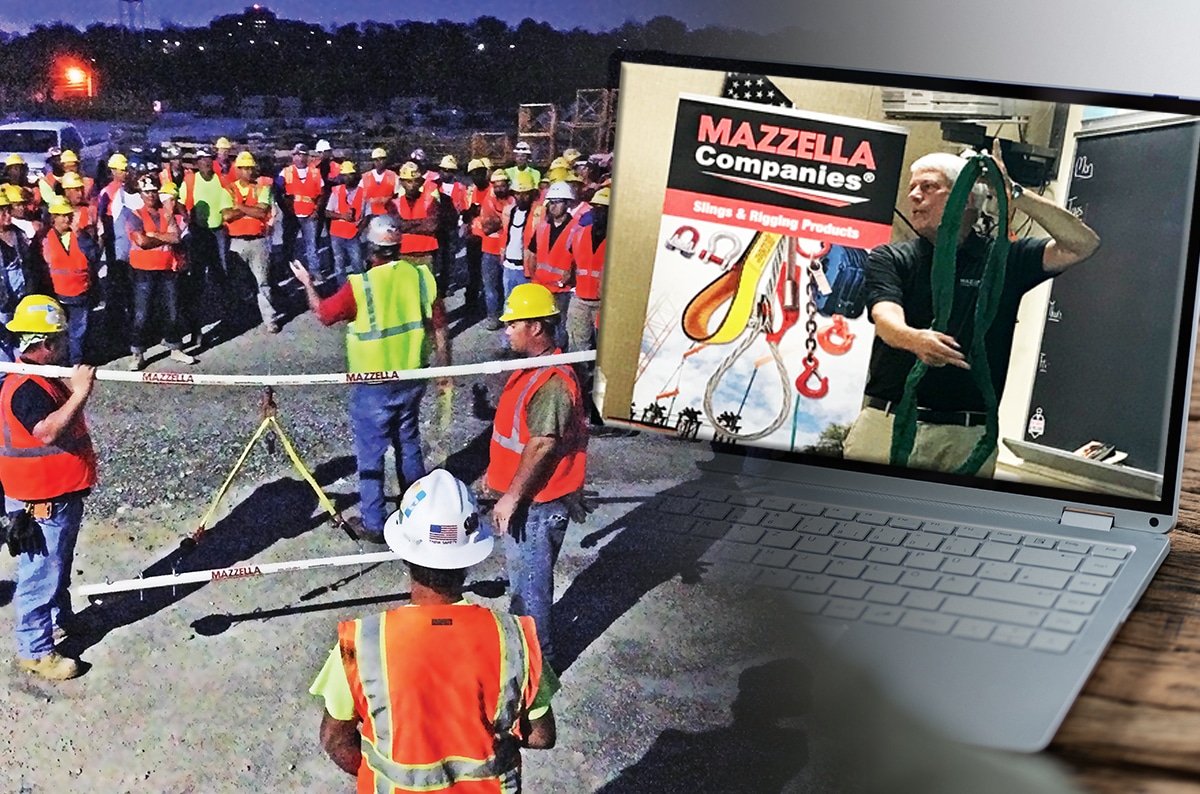
Lifting & Rigging Training
If you require a specific training course for OSHA compliance, Mazzella can assist you in creating a safe and reliable workplace. We qualify our trainers by requiring them to complete an internal train the trainer program (which trains to applicable OSHA and ASME standards and training technique), extensive field experience, and additional training from third-party entities, such as Crosby, CM, Harrington, Gorbel, and Industrial Training International (ITI).
Copyright 2020. Mazzella Companies.