3-1 | Who Performs Inspections and How Often?
<p>OSHA states that the employer has the responsibility to inspect and document alloy chain slings at a minimum of 12-month intervals. The employer is also required to maintain a record of the most recent thorough inspection.</p>
OSHA states that the employer has the responsibility to inspect and document alloy chain slings at a minimum of 12-month intervals. The employer is also required to maintain a record of the most recent thorough inspection. Failure to maintain and retain inspection records is one of the most common issues we see that can prevent a company from reaching full OSHA compliance.
All inspections shall be performed by a Designated Person with any deficiencies further examined by a Qualified Person to identify hazards and determine what additional steps need to be taken to address the hazard.
There are two industry standards that exist to provide the end-user with guidelines for inspection and criteria that warrants removal from service: OSHA 1910.184 and ASME B30.9.
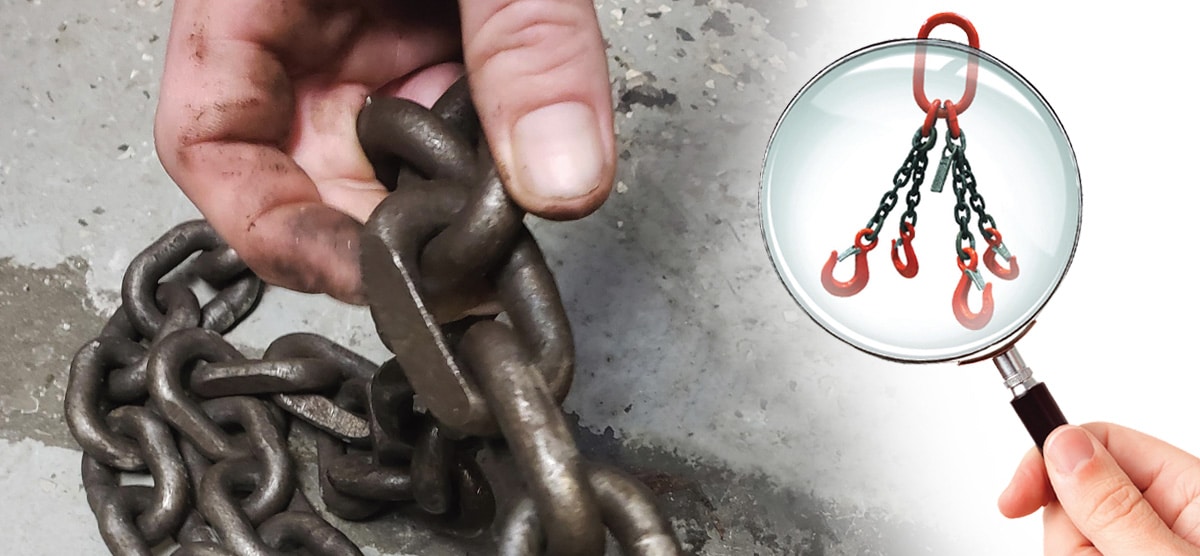
Initial Inspection (Prior to Initial Use):
Best practice is to inspect the alloy chain sling upon receiving it from the manufacturer. Double-check the sling tag to make sure it’s what you ordered and that the rated capacity meets all of your project specifications and lifting requirements.
Frequent (Daily or Prior to Use):
Designate a Competent Person to perform a daily visual inspection of slings and all fastenings and attachments for damage, defects, or deformities. The inspector should also make sure that the alloy chain sling that was selected meets the specific job requirements it’s being used for.
However, users can’t rely on a once-a-day inspection if the sling is used multiple times throughout the day. Shock loads, severe angles, edges, and excessive heat can quickly cause damage to a lifting sling, so best practice is to perform a visual inspection before any shift change or changes in lifting application.
Periodic Inspection:
A documented periodic inspection is performed by either a professional service provider, or by a Qualified person every 12 months (at a minimum) and monthly to quarterly in more severe service conditions. The following are all determining factors in scheduling the frequency of a periodic inspection:
- Frequency of use
- Severity of service conditions
- Nature of the lifts being performed
- Experience gained on the service life of wire rope slings used in similar applications
ASME provides these additional periodic inspection guidelines based on the service of the wire rope sling:
- Normal Service – Yearly
- Severe Service – Monthly to Quarterly
- Special Service – As recommended by a Qualified person
Depending on the severity of the operating environment and frequency of use, your business may decide that a more thorough inspection should occur more often than the minimum yearly requirement.
Periodic inspections are required to be documented per ASME B30.9 and records retained.
The employer is required to maintain a record of the most recent thorough sling inspection—per OSHA 1910.184, individual records are required for each sling that was inspected. Failure to maintain and retain inspection records is one of the most common issues we see that can prevent a company from reaching full OSHA compliance.