Hoist Types and Design
<p>A hoist could be considered the most important component of an overhead crane system because it’s the device that actually performs the lifting and lowering of a load. </p>
A hoist could be considered the most important component of an overhead crane system because it’s the device that actually performs the lifting and lowering of a load. An overhead crane’s hoist lifts and lowers a load by means of a drum or lift-wheel, in which chain or wire rope wraps around.
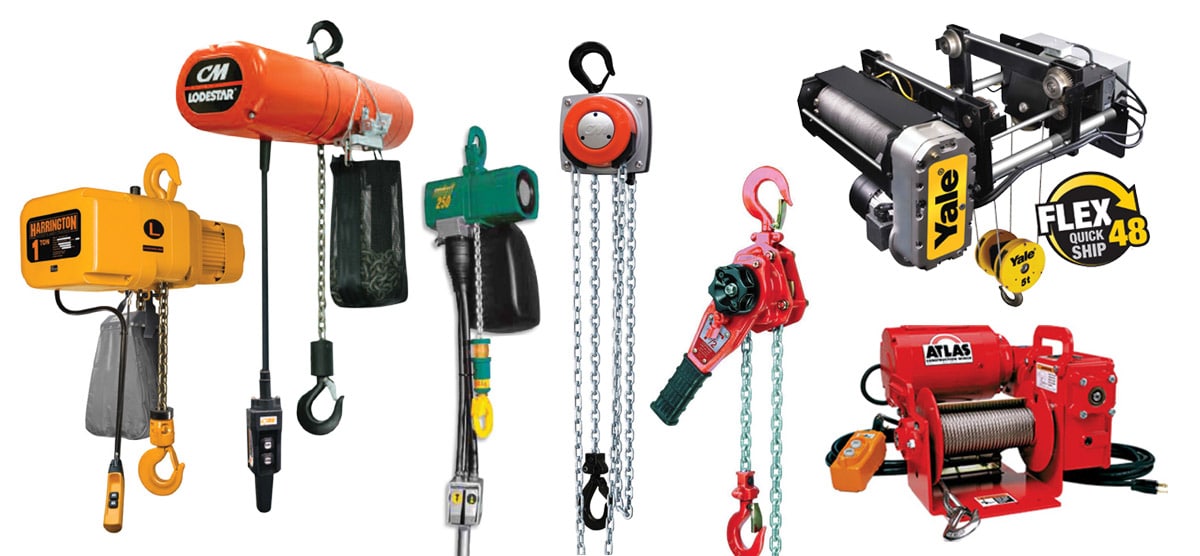
Hoists can be defined by two main characteristics:
- The lifting medium (wire rope or chain) used to support the load
- The power source (manual / hand-powered, electric-powered, or air-powered) used to perform the lift
There are many different configurations of hoists depending on the lifting medium they use, the power sources used to operate the hoist, and the mounting system. It can be difficult to understand what these different terms mean, and which style is best for your overhead crane system.
Chain Hoists
Chain hoists use metal chain as the lifting medium and perform the lift by pulling the chain through sprockets and then deposit it into a container. Chain hoists are a popular choice because they’re relatively low maintenance and can be less expensive than a wire rope hoist system. Chain hoists can be powered manually, electrically, or pneumatically.
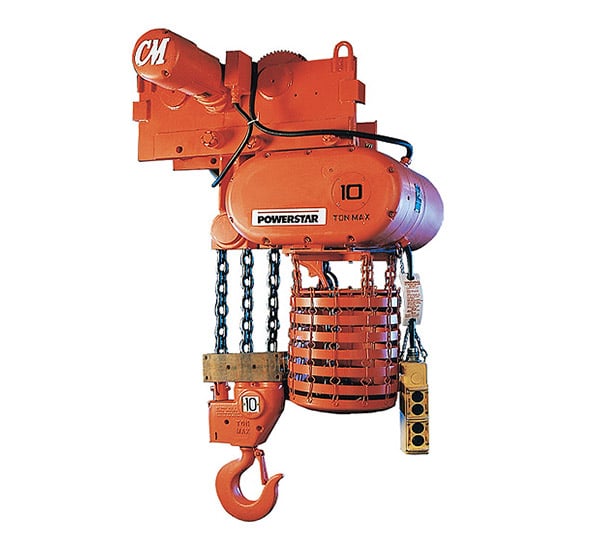
While they’re a reliable and economical option, chain hoists do have a lower capacity and are more commonly found on lighter duty applications under 5-tons.
The major benefits of using a chain hoist include:
- Ability to change the height of the lift by changing out the chain
- Compact, space-saving design with no drum
- Portable and can tolerate greater levels of abuse
- Capacity up to 25-tons (as standard design)
- Chain can last longer than wire rope
The main disadvantages of using a chain hoist include:
- Limited lifting speed
- Noisier operation
- May be problematic at lift heights above 20 feet
Wire Rope Hoists
Wire rope hoists use wire rope as the lifting medium and perform the lift by wrapping the wire rope cable around a grooved drum. Wire rope hoists can be powered manually, electrically, or pneumatically.
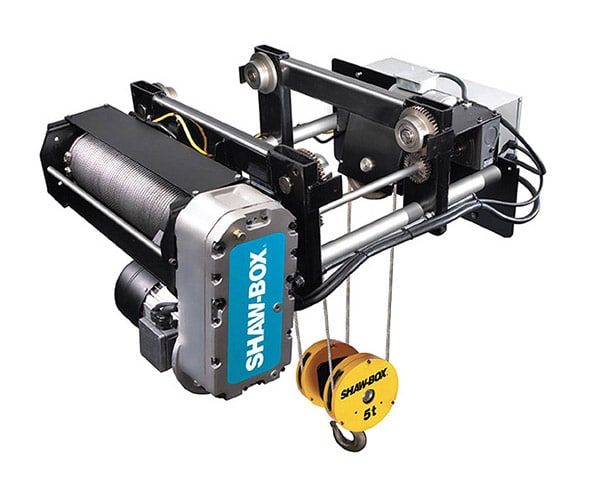
Wire rope is a popular choice in production environments because it can perform lifts at a faster speed, higher heights, and can also be rated for severe duty classifications—Class D, E, and F cranes.
The main advantages of using a wire rope hoist include:
- Offers very fast lifting speeds
- Can be rated to severe duty classifications
- Dominates the market at 10-tons and above
- Quieter and smoother lifting operation
The main disadvantages of using a wire rope hoist include:
- Wire rope may not be as durable as chain in certain instances
- Wire rope drum occupies more space than a chain hoist
- More expensive than chain hoists
Manual Hoists
Manual hoists can be designed in either a chain or wire rope configuration, and are mainly used for occasional lifts where speed of the lift is not a factor. One chain is used to lift and lower the load and the other chain is used to support the load. The chain is pulled using a hand-over-hand motion, or a handheld lever or ratchet, to turn the gears located inside the hoist and deposit the chain in a chain basket.
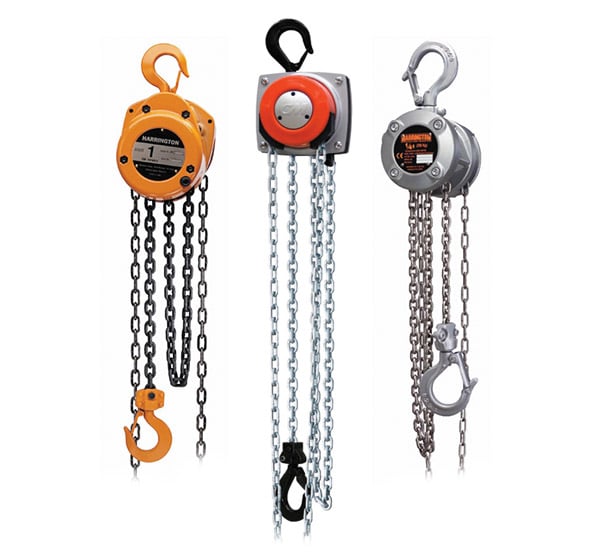
Manual hoists have a simple design that allows for easy inspection, maintenance, and cleaning. Their compact design allows them to be used in tight quarters, and in applications where electricity is impractical or is not available.
Manual hoists are most often used in rigging, maintenance, construction, automotive, general manufacturing, mining, and oil applications. There are three main types of manual hoists, including:
Hand Chain Hoists
- Ideal for construction, maintenance, automotive, and industrial applications
- Typical capacities can range anywhere from 1/4-ton to 50-ton
- Can be attached to a beam or trolley and utilize a vertical pull to produce a vertical lift
- Spark-resistant design can be accomplished using stainless or bronze hooks, wheels, and chains
Lever Hoists or Ratchet Hoists
- Ideal for construction sites, plant maintenance, and industrial applications
- Design allows the user to pull, lift, and position materials either horizontally or vertically
- Typical capacities can range anywhere from 1/2-ton to 9-ton
- 360° rotation of the lever and top swivel hook for easy rigging
- Compact, portable, and durable design allows it be used in tight quarters
Lineman’s Hoist
- Web straps instead of metal rope or chain material allow linemen to work on energized power lines
- Lightweight and one-hand operation
- Designed for precise pulling in tight spots
Electric Hoists
Electric hoists can be designed to use chain or wire rope, and use an electric motor to turn gears located inside the hoist that lift or lower the load. Electric hoists are controlled by push button pendant or radio controls.
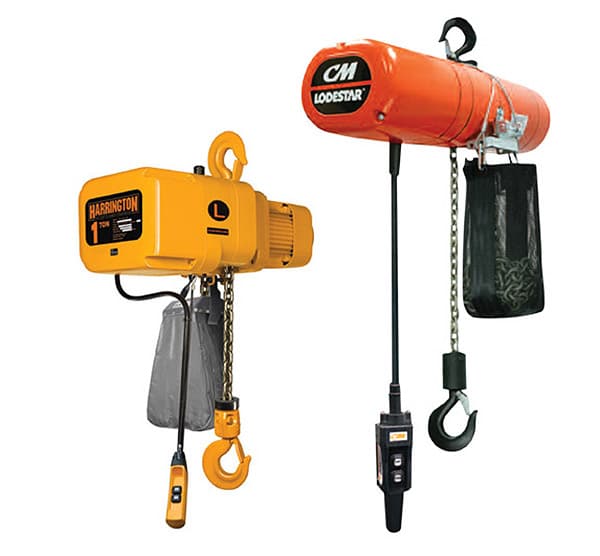
Electric hoists are typically hard-wired into the crane’s electrification system and utilize 220v/440v or 230v/460v. Light duty electric hoists can utilize 110v and plug directly into a standard outlet.
Electric hoists can be used in a variety of applications and come in numerous types and configurations, but are limited by duty cycle and can’t run continuously. The electric motor in the hoist requires a cooling-off period in between uses to ensure that the motor doesn’t overheat.
HMI/ASME Hoist Duty Classifications
There are five main duty classifications for electric hoists outlined by HMI/ASME. Each duty cycle classification takes a number of factors into consideration, including the following:
- Average operating time per day
- Load spectrum
- Starts per hour
- Operating periods
- Equipment life
See the chart below for guidelines on hoist duty cycle classifications based on lifting application, max run time, and max number of starts for uniformly distributed and infrequent work periods.
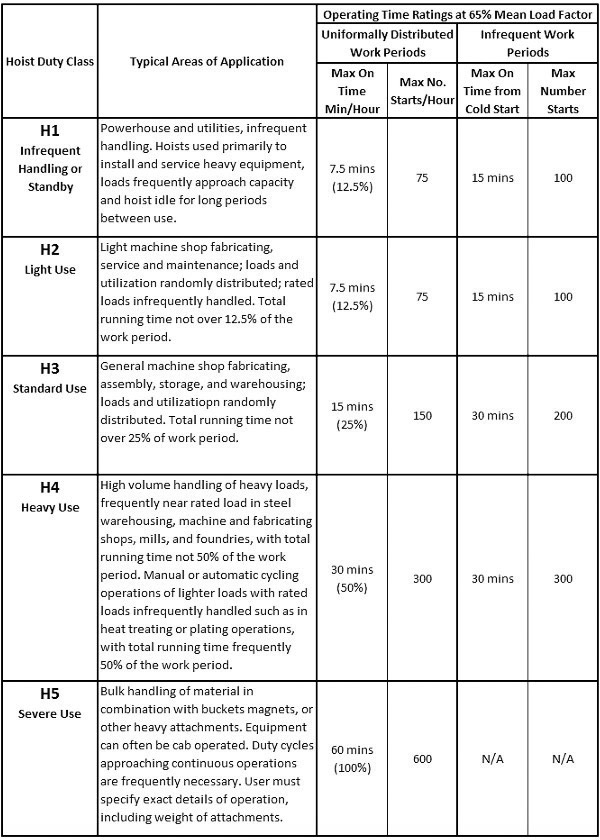
Electric Chain Hoists
- Ideal for manufacturing, power generation, and industrial facilities
- Come in a number of different configurations with different options
- Consider the following when determining the hoist duty cycle, number of lifting speeds, and environment in which it will be used:
- Lifts per hour
- Capacity at which you are lifting
- Amount of time the hoist is in operation
Electric Wire Rope Hoists
- Ideal for industrial, hazardous, spark-resistant, and many other applications
- Light and heavy duty models are available
- Preferred for strength and performance and variety of capacities and lifts
Pneumatic (Air) Hoists
Pneumatic hoists, often referred to as air hoists, utilize a rotary or piston-driven motor powered by compressed air. Air passes through the system and cools the hoist as it operates, so air hoists can run continuously without rest or risk of overheating—unlike an electric hoist system.
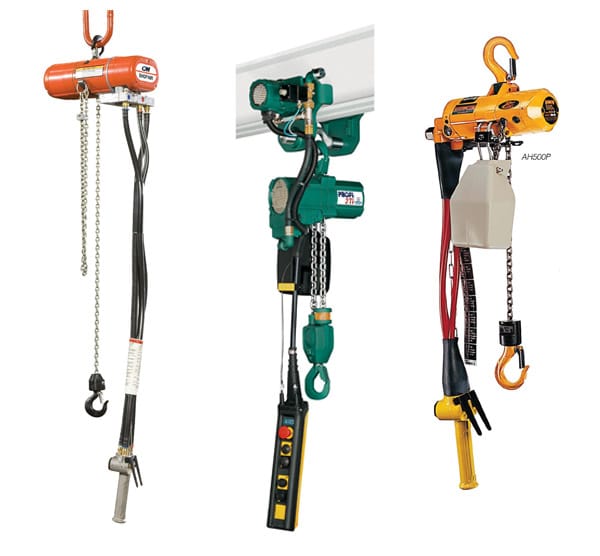
Air hoists are ideal for industrial and heavy-duty production environments and perform exceptionally well in high-speed and heavy-usage environments with constant start and stop. They have a high lifting capacity (up to 100 tons) and are unaffected by high-heat environments. Air hoists are frequently used in explosion proof environments and can be configured to be spark-resistant using brass or stainless components.
A pneumatic air hoist is only as good as the quality of the air, air flow, and pressure that it receives for it to work at its rated capacity and performance.
Air Chain Hoists
- Offer rugged construction, minimum headroom, low maintenance, and are impervious to dust and humidity—making them ideal for manufacturing, power, and industrial facilities
- Excel in places where safety is paramount because compressed air does not generate sparks, making it the preferred choice in hazardous areas
- Allows for variable speed controls and precise load spotting where heavy items are lifted and positioned as part of production or warehousing
Air Wire Rope Hoists
- Strength and productivity for lifting and position virtually any load
- Available in a wide range of capacities and lifts to suit any industrial, spark-resistant, or hazardous application
Built Up Hoists
Built up hoists are highly-engineered and completely integrated systems that are used primarily on Class D, E, and F cranes. These hoist systems operate on process cranes and are built to withstand high-output production and demanding industrial environments. No two built up hoist systems are alike as they’re completely customized for the job at hand.
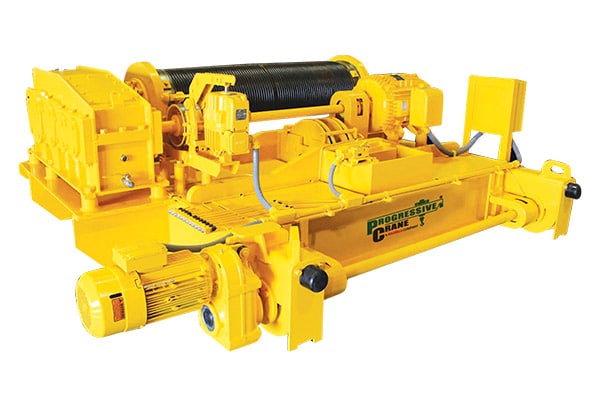
Some of the applications where a built up hoist might be utilized include:
- Automation
- Bucket hoists
- Ladle and charging hoists
- Explosion proof hoists
- Magnet service
- Wet and dry end paper-mill service
- Turbine handling
- Critical lifts
- Die flipping and metal coil handling
A built up hoist consists of robust and specially-designed components that are designed to work together to accomplish a very specific and precise lift. Some of these components include:
- Drums
- Motor
- Gear box
- Couplings
- Sheaves
- Encoder
- Brakes
- Limit switches
- Drives and control systems
- Festooning
Many of these components are precision-machined to very specific tolerances and designed to last so they can perform a complex or critical lift over and over again. The materials used on a built up hoist are often high alloy, heat-treated/hardened, and precision welded to reduce stress, fatigue, and distortion within the system.
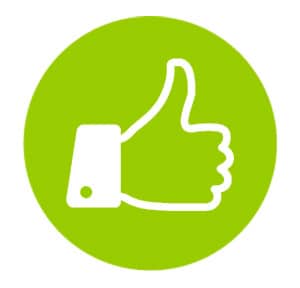
Advantages of a Built Up Hoist
Package hoist systems are primarily designed to be used on lower duty cycle overhead cranes. They fit a specific design criteria and meet the duty cycle requirements of the crane based on their capacity and amount of use they’ll see during the course of their lifetime.
On a built up hoist, all of the components are specifically engineered for a specific purpose and are designed to last a very long time. These are systems that do one thing very well and they thrive in applications where a complex lift is needed. It’s not unreasonable to see built up hoists that can stay in service for 40 years or more when they’re designed properly!
Built up hoists are also designed to be more reliable, easier to inspect, and easier to service and repair than a package hoist system. A catwalk or service platform is commonly found on cranes with built up hoists to allow maintenance and service personnel access to the hoist for inspection or maintenance.
These types of hoists often have individual grease ports for the roller bearings to allow for easy lubrication. The hoist and trolley are also designed to allow easy access to gear boxes, brakes, and couplings for adjustment or repair.
Built up hoists are found on top running double girder crane systems. This design gives them the advantage of:
- No limits to the maximum span or capacity of the crane, hoist, or trolley
- The most overhead room
- The greatest hook height
On a new process crane, the system will come standard with modern features and technologies, which provide better controls, precision movement, and safety when moving a load through a facility. Some of these technologies include:
- Variable frequency drives
- Anti-sway technologies
- Slow down and stop limit switches
- Remote radio controls
- Monitoring and diagnostics
Utilizing diagnostics information, maintenance personnel can monitor the time between recommended maintenance intervals for individual hoist components. This also allows them to schedule preventative maintenance to help reduce equipment downtime.
For example, by monitoring the predictable preventative maintenance schedule, they can help improve the crane’s safety by knowing when the hoist components have reached the end of their useful service life so they can either rebuild the internal components or replace them entirely.
In a steel mill, automotive stamping facility, or mass-production environment, there really is no better option than a built up hoist to handle technical and dangerous overhead lifts.
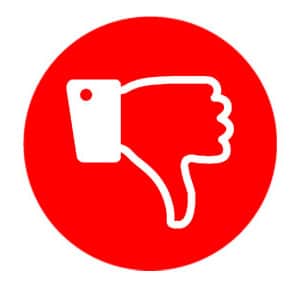
Disadvantages of a Built Up Hoist
Cost would be the biggest disadvantage to specifying a built up hoist into an overhead crane system. The cost factors into the equation in many ways:
- Only compatible with top running double girder crane systems
- Additional engineering and design requirements
- Specialized components and lead times
- Additional transportation and freight costs
- More complicated / longer installation
Lower duty cycle cranes can utilize more standardized and economical hoists—resulting in significant cost savings. However, it can be argued that the initial investment into upgraded built up hoist components and technologies will offset the costs of future maintenance and repairs. By taking the time to engineer the hoist to perform exactly as intended, and to withstand the rigors of the lift it will be performing, the hoist will experience a longer operating life and will be more durable and more reliable for the end-user.
Versatility would be another disadvantage to a built up hoist. These hoists are designed to do one thing and do that one thing extremely well. Lower duty hoist systems have a little more flexibility in terms of how they can be used. They can pick various types of materials and vary the frequency of lifts within their capacity and duty cycle requirements.
Training and inspection would be another factor for the end-user. Even to a seasoned crane operator, there will be an adjustment period to get used to the way the crane handles and performs. If the crane operators were used to operating an older package hoist system, the controls and performance of a new built up hoist can feel very different. The components of the hoist are also more complex and may require more training or a more seasoned inspector to perform frequent and periodic crane inspections.
Most crane manufacturers or service companies will offer training for the operators and in-house maintenance personnel once the crane system has been installed—these trainings can be fully customized based on the preferences of the business owner, operators, and maintenance personnel.
Wrapping it up
We hope that this lesson gave you a better understanding of the different types of overhead crane hoist configurations that are available to you. When designing your overhead crane system, careful consideration should be given to the design and specifications of the hoist—as this will be the device actually performing the lifting and lowering of the loads.
If your hoist will be used in low headroom applications, or will be used on a high-capacity overhead crane system, then you should make sure that you receive and carefully review approval drawings. This will verify that the hoist specifications meet the operating and usage requirements of your lifting needs.
Also, consider whether a chain hoist or wire rope hoist is more applicable for your lifting needs, and whether a manual hoist, electric hoist, or air-powered hoist will meet the demands and usage requirements of your crane system.