Installing a Crane in an Existing Facility
<p>When it comes down to it, installing an overhead crane system into an existing building structure is a completely different process than installing a crane into a new construction facility. </p>
When it comes down to it, installing an overhead crane system into an existing building structure is a completely different process than installing a crane into a new construction facility. With a new construction installation, the building’s support structure, layout, plumbing, electrical/lighting, HVAC and duct work can all be designed so that they don’t interfere with the installation and operation of an overhead crane. The installation window can be more flexible because you don’t have to worry about affecting production.
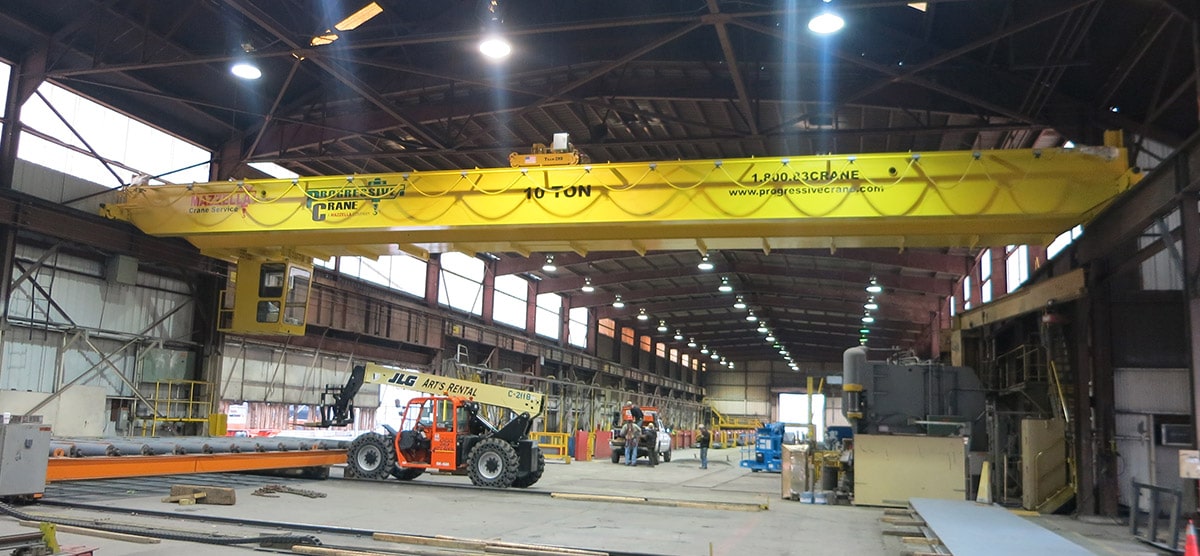
Unfortunately, most crane installations don’t occur in a brand new facility with a flexible installation timeframe and a blank slate to design and build the structure around the crane itself. In most cases, the design and engineering team has to retrofit an overhead crane and its support structure into a space that wasn’t originally designed for a crane system. To further complicate things, production is already up and running with employees moving about and machinery and other equipment in operation—all creating obstacles for getting installation equipment and materials into the building.
Unique Considerations for Designing and Installing an Overhead Crane in an Existing Building Structure
In this section, we’ll discuss how the following factors can affect the timeline and the success of a crane installation:
- Production
- Free and clear access to the building and installation site
- Delivery dates
- Machinery and special equipment required for installation
- Safety programs and requirements
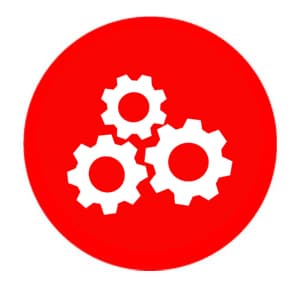
Production
If you ask any overhead crane manufacturer what the most important consideration is for installing an overhead crane in an existing building, they’ll tell you that it all comes down to production. The customer’s Production and Operations teams absolutely need to be on-board with the agreed-upon installation window and time frame.
Because the crane is being installed in a facility where production is already operational, the installation will typically be scheduled during a total or partial production shutdown. It’s ideal for the installers to not have to worry about other machinery or equipment that might be running, or to have to worry about employees being near or in the area where the installers will be working. This increases the efficiency of the installation and also the safety for both the installers and the customer’s employees.
However, it’s understandable that not all customers are willing to totally shut down their production. To prevent any disruption in production, installers can be flexible and schedule installations during weekends, 2nd or 3rd shifts, or during holiday breaks. These types of installations typically come at a higher rate than the standard hourly rate because the installers are working non-traditional hours and may have to run continual shifts to complete the installation during the desired time frame.
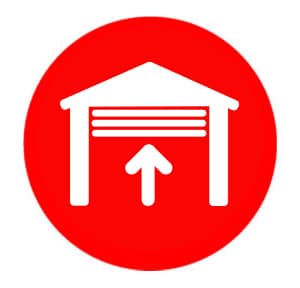
Free and Clear Access to the Building and Installation Site
Prior to the installation, the installers will visit the customer’s facility and perform a Job Site Overview (JSO). During their visit, they may rope off or mark the area where the overhead crane system will be installed and they’ll also get an understanding of the building layout. Most importantly, they need to come away with an understanding of where and how they can bring their trucks and equipment into the facility—including access to doorways and ramps that they can utilize.
Will the equipment and machinery need to travel through areas where production is running? Will production shut down? Is installation occurring in a part of the building that isn’t in use yet? The installers need a clear understanding of what obstacles or machinery they need to maneuver around, and what employees, if any, will be working in those areas, so they can develop an action plan.
During the JSO, they also need to have an understanding of the load requirements for certain parts of the building, including:
- Structural support beams
- Roofing
- Foundation and flooring (concrete, dirt, gravel, etc.)
- Any existing runway structures
These load surveys need to be performed by a third-party civil or structural engineer and are the responsibility of the customer to coordinate and facilitate prior to the installation.
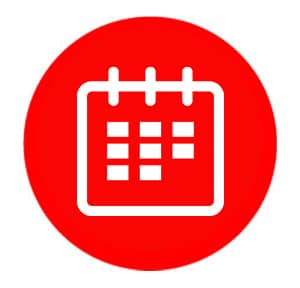
Delivery Dates
During the overhead crane quotation process, the Project Manager or Sales Engineer will work with their team to determine how quickly they can source the components, get them ordered, and have them delivered based on the customer’s specifications.
The biggest contributing factor to whether the crane installation can happen during the customer’s preferred timeline is how quickly the main components—including the hoist, trolley, and end trucks—can get approved and how fast the supplier can ship them. Your crane company can work with their vendors to expedite or rush delivery, but those expedited fees will get passed on to the customer.
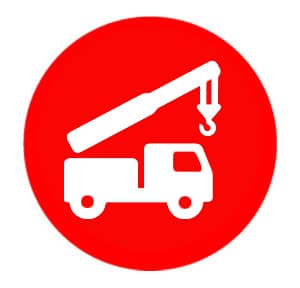
Machinery and Special Equipment Required for Crane Installation
Overhead crane installers typically bring their own equipment, or rental equipment, on-site for an installation, but can use a customer’s generators, welding equipment, man lifts, Lull material lifts, or forklifts if it presents a cost-savings opportunity to the customer. However, if an agreement is reached where the installers will use the customer’s equipment, the installers require exclusive use and the customer will have to agree to forfeit use of the equipment for the duration of the installation.
Each job is unique and requires its own set of equipment and machinery to lift the runway beams, bridge girders, and hoist up into the air and into their final position.
Often times, the materials required for installation need to be lifted up and over existing equipment on the production floor, lowered down into a pit, raised up into a mezzanine. In some extreme cases, we’ve even cut a small hole into the roof to allow the hook block to drop through the opening to achieve greater lifting headroom.
Some of the pieces of equipment that an overhead crane installer may use, include:
- Carry deck cranes
- Mobile cranes with operators
- Existing overhead cranes in the facility
- Man lifts—boom lifts and scissor lifts
- Lull material handlers
- Versa Lifts / Tri-Lifters
- Ladders and scaffolding
Another thing to keep in mind is that you’ll need to reserve an area on your property where the installers can stage their equipment when not in use. They’ll need a place to park flatbeds and trailers, as well as keep their mobile cranes, scissor lifts, and the support structure beams. These can be kept on open land, in a reserved area of the parking lot, or in an empty area of the building if the entry doors and building space allows it.
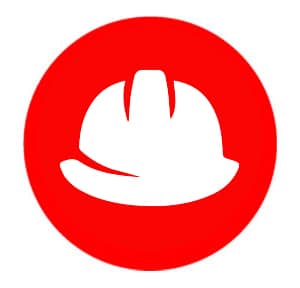
Safety Programs and Compliance
Some facilities require contractors and vendors to have site-specific safety training, perform a background check, take drug tests, or have certified operator cards to use forklifts or man lifts. If your job site has these requirements, make sure the installers are aware so any unplanned delays don’t affect the timing and cost of the installation. In some cases, like where a background check is required, this process needs to be started several weeks in advance to ensure completion before the installation begins.
What Structural Considerations Affect the Design of the Crane?
A bridge crane can be supported by the roof/ceiling, a freestanding support system, or can be tied back to the existing building supports. In an existing building structure, you have to have a clear understanding of the load ratings for the roof, concrete and foundation, and existing building supports.
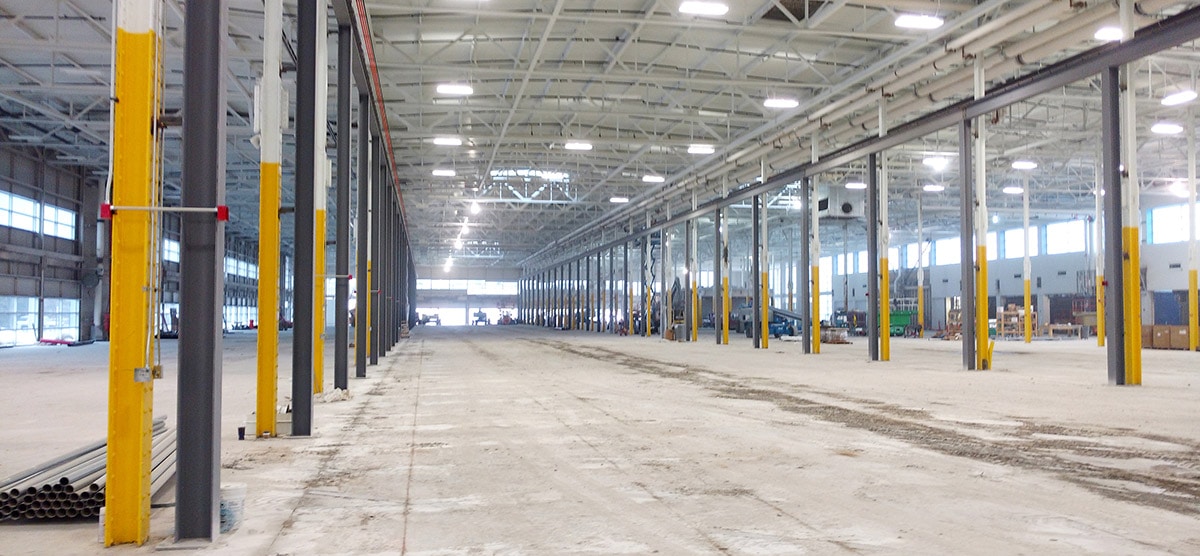
A third-party should come in to provide a structural survey—you may need independent surveys of the:
- Concrete or flooring to determine load ratings
- Roof load ratings
- Existing structural support load ratings
To make sure the building is structurally sound to support an overhead crane system, it’s the customer’s responsibility to have their building surveyed by a third-party, or by their own building engineers, prior to the installation.
A crane installer may be able to help coordinate the effort, but they will not perform the surveys or load ratings themselves. The results of these ratings can determine if the crane is supported from the roof, is a free-standing design, or can be tied back to existing supports.
The deadweight of the crane, or the loads on the structure which remain fixed even when the crane is not performing a lift, need to be considered. Ceiling beams, flooring, and support beams can be reinforced with internal bracing, or can be totally redesigned to spread the load between multiple points versus a single point.
Clearance space around the area that the crane will be installed in will also affect the design and specifications of the crane. If there’s low headroom in the facility, then the crane may have to be designed to be under running vs a top running design. If the crane needs to lift material high into the air, then a top running double girder design would be ideal. If hook approach on either end of the bridge is a factor, then a single girder bridge design will allow your trolley the most travel across the bridge to take advantage of the full span of the crane system.
Lastly, the installers will need to have a clear understanding of the building’s voltage supply. The customer will need to confirm whether the building is equipped with a 230V or 460V electrical supply. This voltage needs to be determined prior to ordering any components such as hoists or end trucks.
Testing the New Overhead Crane System
Once the overhead crane installation is complete, the installers will test the functionality of the new overhead crane system and also perform a rated load test.
OSHA 1910.179 Overhead & Gantry Cranes Regulations states that:
- Prior to initial use all new and altered cranes shall be tested to insure compliance with this section including the following functions:
- Hoisting and lowering
- Trolley travel
- Bridge travel
- Limit switches, locking and safety devices
- The trip setting of hoist limit switches shall be determined by tests with an empty hook traveling in increasing speeds up to the maximum speed. The actuating mechanism of the limit switch shall be located so that it will trip the switch, under all conditions, in sufficient time to prevent contact of the hook or hook block with any part of the trolley.
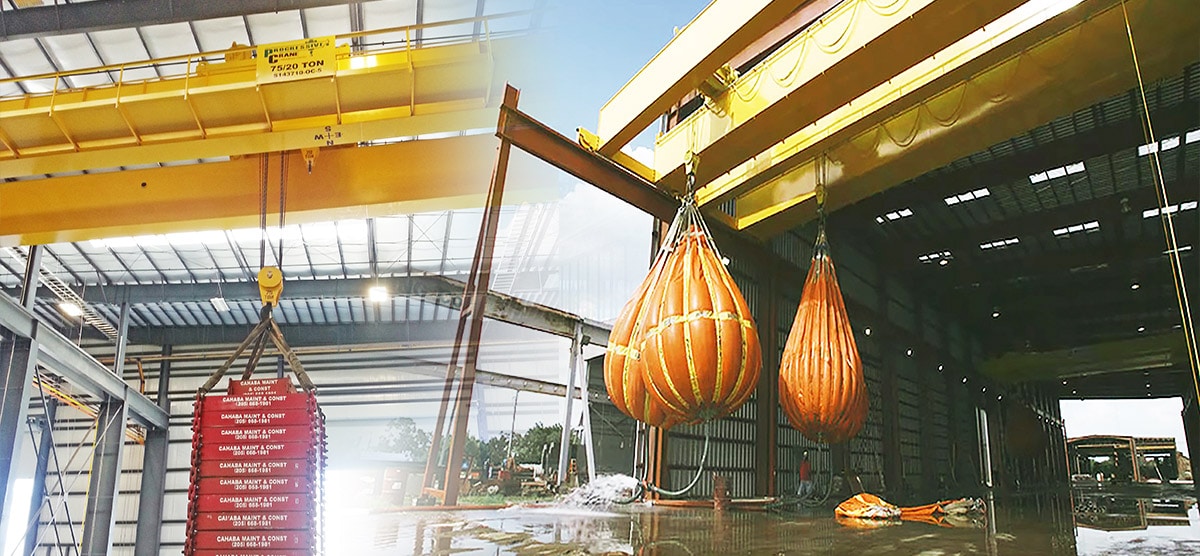
Test loads shall not be less than 100 percent, or more than 125 percent, of the rated load unless otherwise recommended by the manufacturer. These test reports shall be placed on file where readily available to appointed personnel. Overhead cranes can be tested using water weights or by using loads on-site. Load testing is included with any installation or crane upgrade or modernization.
Lastly, once the overhead crane equipment has been tested for proper functionality, the installers will provide training to the operators and end-users on their new equipment. Training can range from a couple of hours to a couple of days—it all depends on the customer’s requirements. Most of the time, the training requirements will be written into the project specifications, so the length and thoroughness of training will be agreed-upon prior to installation.
Training can be as simple as walking one operator through the basic motion controls of the crane, or it could be more in-depth focusing on troubleshooting maintenance issues for individual components and understanding and identifying diagnostics and fault codes.
Wrapping it up
As you can see, successfully installing an overhead crane into an existing building structure requires active involvement from the customer’s production and operations departments, third-party engineers and surveyors, project managers, equipment suppliers, and installation technicians. With all of these moving pieces and parts, you’ll want to select a reputable and experienced overhead crane manufacturer to partner with for your overhead crane design and installation.