Overhead Crane Electrification Systems
<p>One of the most important components of an overhead crane system is the electrification system. Admittedly, overhead crane electrification can be one of the more complex subject matters. With different types of electrification systems available, and different varieties that exist for each type of system, it can be difficult to determine which electrification method is best for powering your overhead crane.</p>
One of the most important components of an overhead crane system is the electrification system. Admittedly, overhead crane electrification can be one of the more complex subject matters. With different types of electrification systems available, and different varieties that exist for each type of system, it can be difficult to determine which electrification method is best for powering your overhead crane.
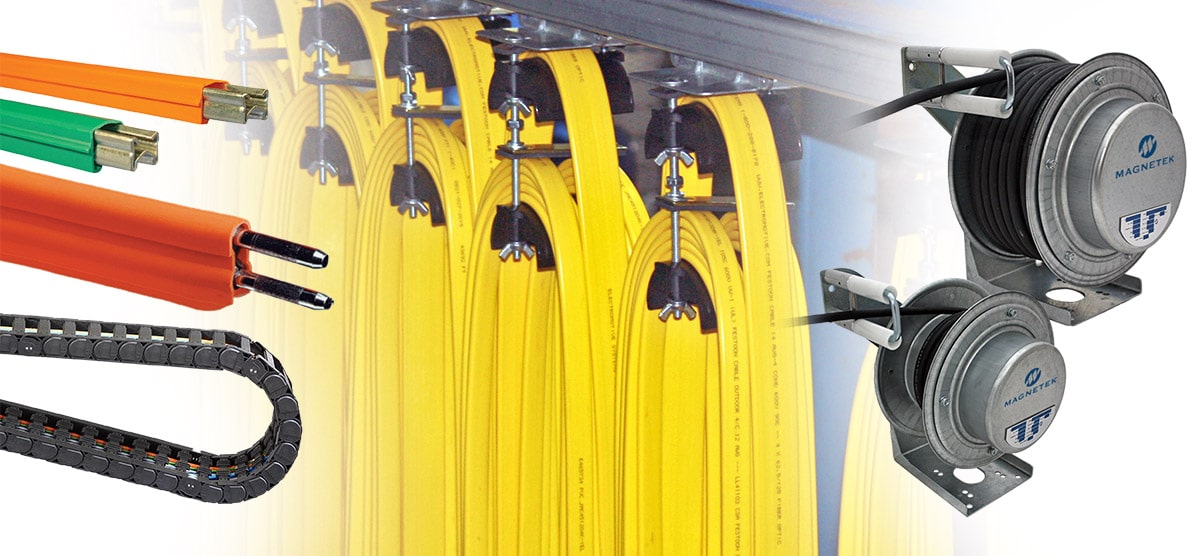
Our goal for this lesson is to:
- Define terms related to overhead crane electrification
- Breakdown and explain the three main types of overhead crane electrification:
- Conductor bars
- Festoon systems
- Cable reels
- Explain how each crane electrification system works and lay out the different options available for each system
- Discuss the advantages and disadvantages of each crane electrification system
- Identify what types of crane applications or environments each electrification system may be best suited for
Definition of Terms
Before we jump into the different types of electrification options for overhead cranes, let’s look at some definitions for terms that may be used throughout this article:
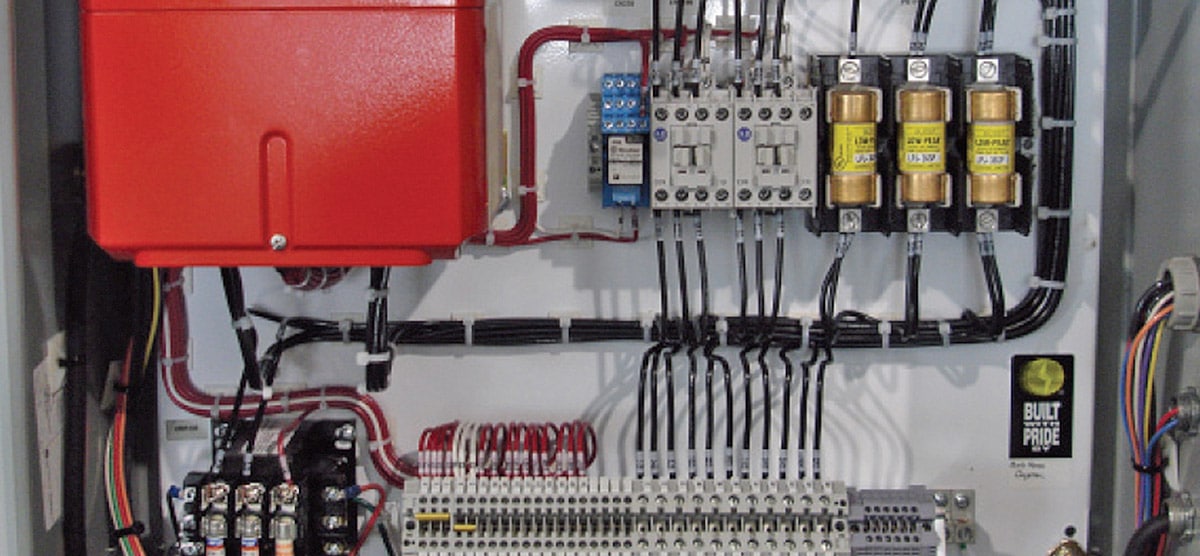
Electric Overhead Traveling Crane
Electrically operated machine for lifting, lowering and transporting loads. It consists of a movable bridge carrying a fixed or movable hoist mechanism and travels on an overhead runway structure.
Power Circuit
Provides energy to lift loads and run the motors that perform work
Control Circuit
Supplies power and includes circuitry to activate the devices that turn the main motors off and on. The crane and hoist are run by a push button type control or radio remote used by the operator. For safety reasons, the control circuit operates at a lower voltage and current to reduce the shock hazard to the operator.
Mainline Conductors
Rigid construction bars, cable festoon system, or cable reel that delivers the mainline power along a runway or monorail track.
Bridge Conductors
Electrical conductors located along the bridge structure of a crane to provide power to the trolley and hoist.
Runway Conductors
Main conductors mounted on, or parallel to, the runway which supplies current to the crane.
Enclosed Conductors
A conductor or group of conductors substantially enclosed to prevent accidental contact.
Collectors
Contacting devices for collecting current from the runway or bridge conductors. Mainline collectors are mounted on the bridge to transmit current from the runway conductors, and the trolley collectors are mounted on the trolley to transmit current from the bridge conductors.
Controller
Device for regulating the power delivered to the motor or other equipment.
Festoon Cables
Looped wires, or more commonly flat cable, that carry power and control across a bridge or along a runway or monorail.
Cable Reels
Also known as electrical cord or power reels, these are one of several alternatives for providing power to electric hoists. Multiple conductor power cable is wrapped around a drum, which rotates to payout or retract the necessary length of cable for the application.
Disconnect
Device where the conductors of a circuit can be disconnected from their power source
Explosion Proof
Electrical specification that includes a variety of components that must be supplied as per the demands of the Group, Class, and Division of the hazardous area in which they are expected to operate
Festoon Stack-Up
When the cables gather together at the end of a rail, it can limit the travel of the components causing the crane or trolley to stop short of it’s full range of travel
How an Electric Overhead Crane Receives Power
Cable festoons, conductor bars, or cable reels are used to transfer power from the building supply to the crane runway and bridge crane control panel. The same components are then used to supply power across the bridge to the hoist trolley.
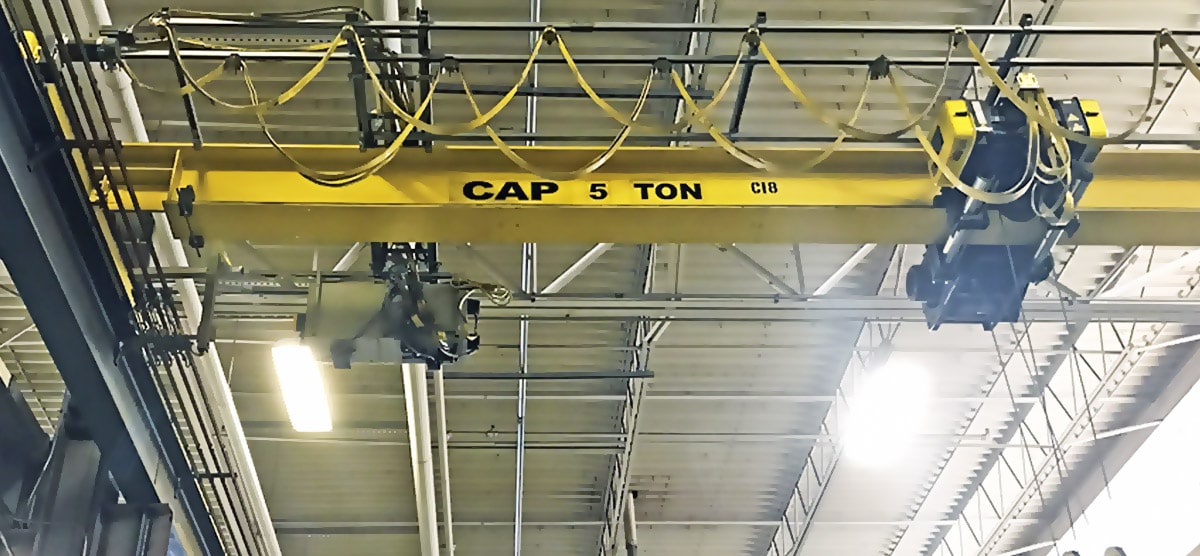
An operator controls the movement of the crane and hoist via push button pendants or radio remote controls. All of these components combined allow the bridge and hoist to move into position over the load. Once the load is lifted, the push button pendant or radio remote control are used to drive the bridge crane to its destination and lower the load.
Crane Electrification via Insulated Conductor Bars
Conductor bars (also referred to as power bars, figure eight bars or hot bars) are one of the most common methods of electrifying and supplying power to a crane and hoist. A conductor bar uses a sliding shoe collector system, which removes most of the exposed conductor safety hazards and can supply higher amperage power compared to other power systems.
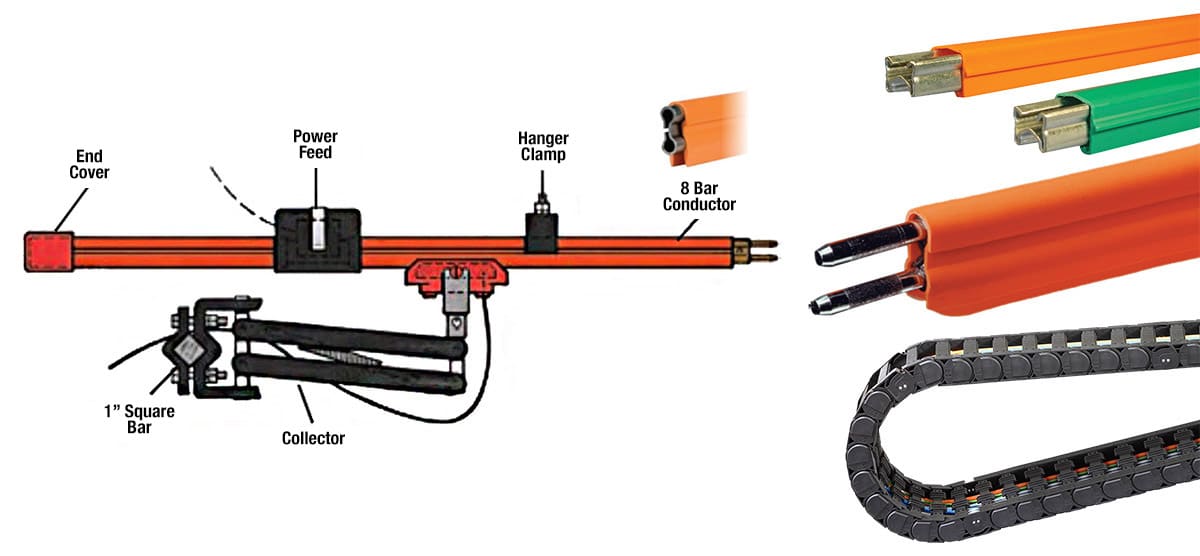
Today, most conductor bar electrification systems are insulated with a cover. There are some applications where the conductor bar may not be insulated, but the most common types have insulated covers.
Components:
- Conductor bar – the supply of incoming power and/or control along the runway or bridge
- Power feed – attachment of incoming power to the conductor bar
- Collector – a contacting device to collect the electrical current from the conductor bar and forward it to a machine
- Brackets – supporting device for attachment of multiple hangers to the runway or bridge
- Hangers – attach the conductor bar to the brackets
- End cover – safety protection at the end of conductor system
- Anchor clamp – supporting device for directing movement of conductors during thermal expansion and contraction
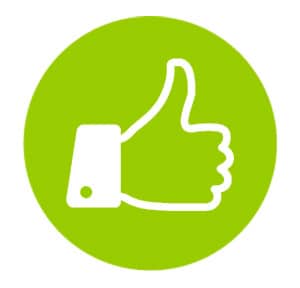
Advantages:
Conductor bar systems for overhead cranes can be used on both indoor and outdoor cranes and are most typically installed on the crane’s runway systems or on monorail cranes. One of the main advantages of using a conductor bar system is that they can be used on runways with more than one bridge operating on them.
They’re also very cost-effective and easy to install with many different types of brackets and hanger clamps. In addition, they are ideal for low headroom applications where cables cannot hang down, and for systems that utilize a curve or track switch.
One final advantage is that conductor bars are excellent for crane setups where future upgrades or expansions may be a consideration. Runway systems can be extended easier and with less cost because conductor bars are so easy to connect together for installation. Conductor bars are also the perfect solution for continuation of power in interlocking crane systems.
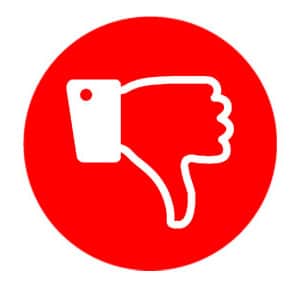
Disadvantages:
On a conductor bar system, one of the main disadvantages is that the collector shoes can wear out quickly and need to be serviced or replaced often depending on the severity of use.
Another disadvantage is that a conductor bar system can never be utilized in an environment that requires an explosion proof crane, and they should not be used to power transfer carts.
Crane Electrification via Festoon Systems
A festoon electrification system utilizes flat or round cable on a trolley traveling on a C track, square rail, or an I-beam. This method of overhead crane electrification provides direct contact, which provides greater resistance to wear on the system’s components.
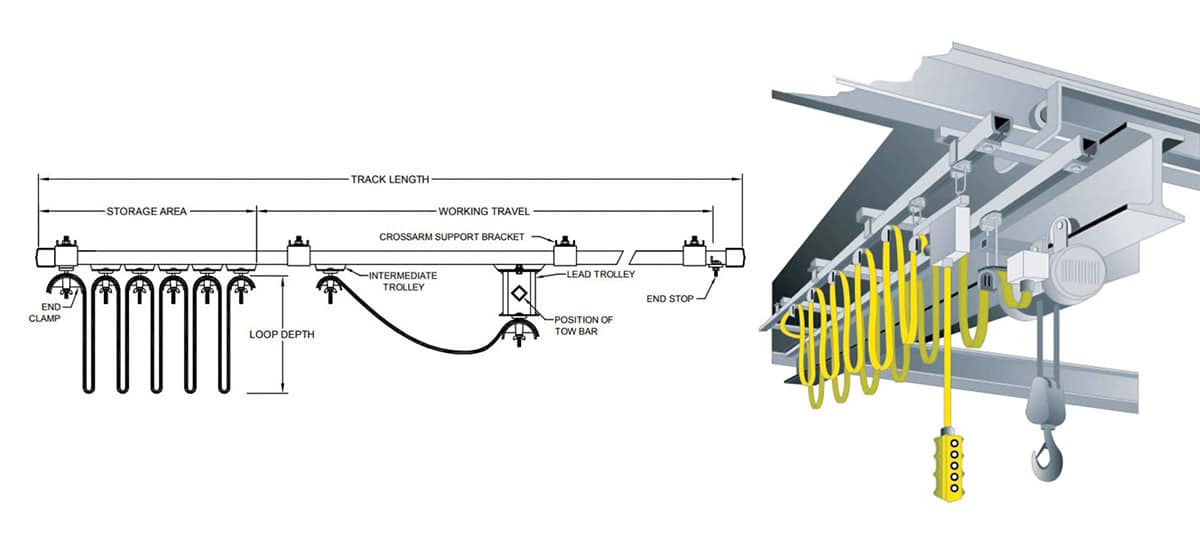
Festoon systems are extremely reliable and can be used in all kinds of applications from indoor to outdoor applications, high heat environments, and in other demanding environments like in mills and at port facilities. They can also be used to safely provide power and control for explosion proof cranes.
Festoon electrification systems are most commonly found on bridge cranes, but can also be used on other types of overhead cranes like gantry cranes, some forms of monorail cranes, and jib cranes. However, some types of festoon track may not be recommended for monorail setups where there may be curves in the rail.
Types of Festoon Systems:
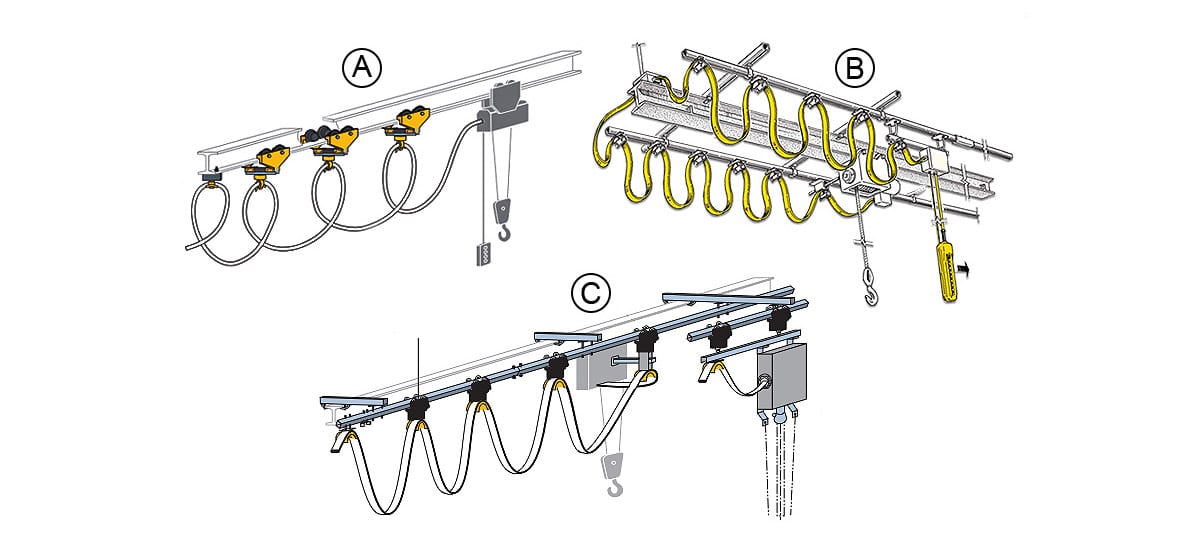
Track-Mounted Cable Festoon Systems – effective cable management in light to medium-duty applications. Track-mounted systems allow you to organize and move cables and/or hoses for power and control circuits. These systems are reliable, efficient, easy to install, and have low maintenance requirements.
- Track material can be made out of galvanized, stainless, or sometimes PVC materials for corrosive environments
- Can be run indoors or outdoors in dusty, dirty, or corrosive environments, in high-temperature environments, and can be used for applications that require an explosion proof design
Square Rail Festoon Systems – Runs on a square or diamond-shaped track. This type of track is especially useful in dirty or dusty environments, can be used indoors or outdoors, and will work for applications that require an explosion proof design.
- Perfect for monorail cranes as it can be configured to work in a straight, curved, or circular track design
- I-Beam Cable Festoon Systems – ideal for medium to high-duty applications and environments. Different carriers available from basic economic versions to custom-design. Ease of maintenance and high-reliability in any operating environment. Pre-assembled systems are available for easier installation.
- Can be configured in a basic economical design or totally customized for specialized systems
- Built for demanding environments like steel mills, plants, and ship to shore cranes. They are simple to install and low-maintenance.
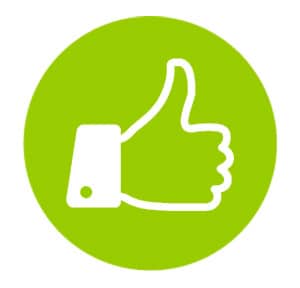
Advantages:
A festoon system organizes and allows cable to stack up without twisting and the trolleys can accommodate multiple layers of cable.
Festoon systems are easy to maintain and have a pretty straight forward design and operation. They are hard-wired to operate in harsh or extreme temperatures and environments and can be configured in basic economic designs to accommodate a few light cables or can be totally customized with more complex cable packages for heavier-duty applications.
Encoder cables (and other types of cables) can also be run to the hoist motor from a control panel on the bridge crane for special and unique applications. Festoon systems may also utilize “plug and play” electrical connections made of male and female pin connector sets that make installation simple and easy.
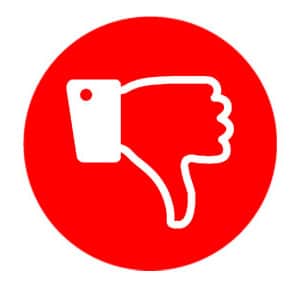
Disadvantages:
A festoon system is not ideal for use on runways that have multiple bridges. Each bridge must be wired separately which can cause complexities and isn’t a very cost-effective design. In addition, monorail systems that utilize a complex curve or track switch cannot use a standard C track or I-beam rail for power delivery.
Additionally, if the crane has a long runway system or wide span, you can experience festoon cable stack-up which limits the crane or hoist travel near the end stops.
If the environmental factors are not taken into consideration, stressors such as UV, oil, radiation, abrasion, temperature, and friction can cause the cable to degrade over time. Environmental factors must be considered so that the proper materials for the cable and cable jackets are selected during the design and manufacturing processes.
Crane Electrification via Cable Reels
Another type of crane electrification method involves the use of a cable reel—either spring-loaded or motor-driven—to release, retrieve, and store conductor cable for crane equipment. A reel with conductor cable wrapped around it is most often used for mainline power delivery along a runway or monorail. When mounted to a trolley, a cable reel can be used to deliver power and control to a below-the-hook lifting device or other equipment attached to the crane hook.
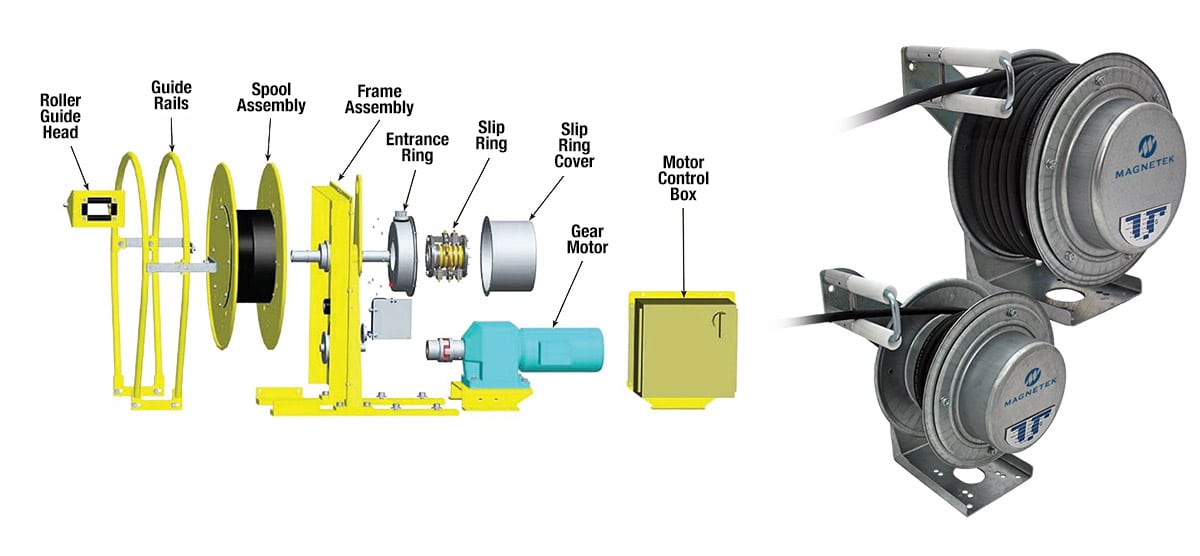
Cable reels utilize a very simple design that automatically winds and stores flexible cables. Cable reel electrification requires little to no maintenance and is easy to install. They can also be mounted stationary, or on a swivel base to allow the cable to payout in multiple angles and directions.
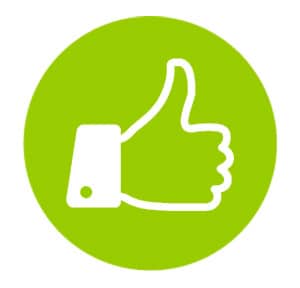
Advantages:
Cable reels may see limited use for standard crane applications but can provide the right electrification method for special applications in tough environments—both indoor and outdoor. Cable reels are often considered for explosion proof applications or for monorails with lighter capacity hoists. They can also be used for below-the-hook devices requiring electrification.
Cable reels can protect cable against corrosive, acidic, or explosive environments with stainless or galvanized steel construction and powder coated components. They’re also great for demanding applications where daily cycles and crane usage are high. These are popular for mobile or heavy-duty gantry cranes and can be used on both electric and pneumatic air systems.
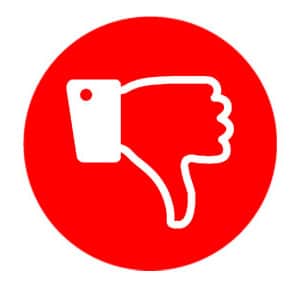
Disadvantages:
You may experience a sag factor which will cause the cable to hang or drop down when the cable is stretched out over a long distance.
As you can see, many different factors can play into selecting the appropriate electrification system for an overhead crane. During the consultation process, an overhead crane manufacturer will work with you to determine which system is best for your needs, by considering the following:
- Type of crane: bridge, gantry, monorail, jib?
- What is being powered: bridge, trolley, runway, below-the-hook device?
- Operating environment: dusty/dirty, temperature, moisture, corrosive?
- Duty cycle and usage of the crane?
- Any special considerations for access/installation, or future maintenance?