Overhead Crane Electrical Grounding: NEC 610.61 Requirements
At Mazzella Companies, our Service Technicians and Engineers commonly come across overhead cranes that are operational, but not in compliance with industry electrical and grounding requirements. There’s still a lot of confusion as to whether an overhead crane using 3-bar conductors, that was designed and installed prior to 2005, is in compliance with the revised NEC standards.
Did you know that cranes using 3-bar conductor electrification are no longer in compliance with electrification standards? Many business owners may not realize that their older electrification systems are outdated, or they mistakenly think they’re in compliance because of a “Grandfather Clause.”
Prior to 2005, overhead cranes using conductor bar electrification only needed three bars—a positive, negative, and neutral to power their overhead crane equipment. The metal wheels on the bridge trolley and hoist trolley provided a ground through contact with the metal track they run on.
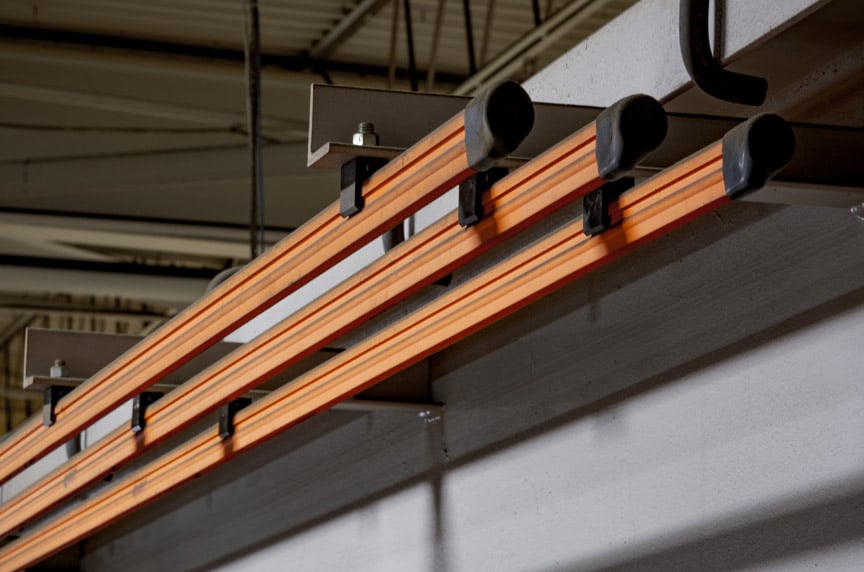
In 2005, that changed. Revisions were made to National Electrical Code (NEC) grounding requirements for overhead cranes and stated that a separate grounding conductor was required in place of the metal-to-metal connection provided by the wheels and track.
At Mazzella, our Crane and Hoist Service Team commonly come across overhead cranes that are operational, but not in compliance with industry electrical and grounding requirements. There’s still a lot of confusion as to whether an overhead crane using 3-bar conductors, that was designed and installed prior to 2005, is in compliance with the revised standards.
Our goal for this article is to help you understand the following:
- The purpose of a ground in an electrical circuit
- Changes to NEC 610.61 Grounding requirements
- OSHA’s interpretation of their electrical and grounding standards
- Your options for upgrading or modifying a 3-bar conductor electrification system for compliance
What is an Electrical Ground and Why is it Important?
In electrical engineering, a ground is the reference point in an electrical circuit in which voltages are measured, a common return path for electric current, or a direct physical connection to the Earth. In a typical A/C electrical line that delivers power to a household or business, equipment that has exposed metal parts are connected to ground so that if, due to any fault conditions, a “Line” supply voltage connection occurs to any such conductive parts, the current flow will then be such that any protective equipment installed for either overload or “leakage” protection will operate and disconnect the “Line” voltage.
This is done to prevent harm resulting to the user from coming in contact with any such dangerous voltage in a situation where the user may, at the same time, also come in contact with an object at ground/earth potential. In electrical power distribution systems, a Protective Earth (PE) conductor is an essential part of the safety provided by the ground system.
If a short to ground exists in an electrical circuit, energy will follow the path of least resistance to complete the circuit—and you don’t want your crane operator or a maintenance technician to become that ground. Essentially, an electrical ground gives a safe clear path for excess energy to travel back on in an electrical circuit and an overhead crane that is properly grounded will help prevent accidental electrocutions or shocks when operating or working on the crane system.
Changes to NEC Article 610.61 – Grounding Requirements for Overhead Cranes
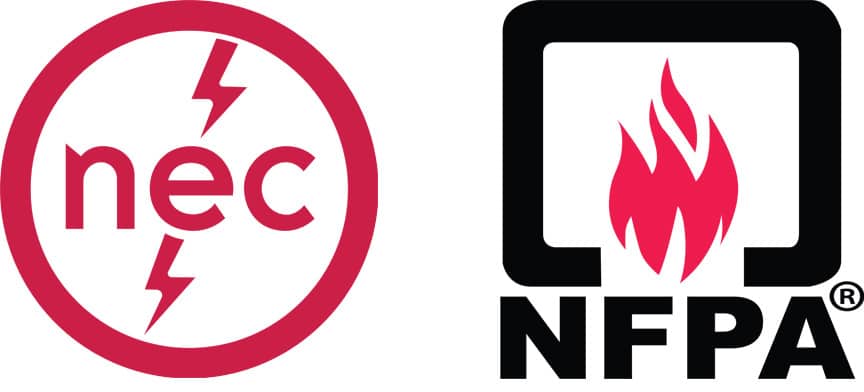
In January 2005, revisions were made to NEC Article 610.61, published by the National Fire Protection Association, with new requirements for how an overhead crane’s electrification system should be sufficiently grounded.
First and foremost, this was a safety amendment. A ground conductor bar gives a clean return path for excess power in an electrical circuit, which helps helps to prevent:
- The build-up of static electricity
- Electrical shock
- Electrical system overload
A change to the standard was proposed by the Crane Manufacturers Association of America, Inc. (CMAA) in 2002 and was implemented in 2005. The CMAA was already recommending the use of a fourth conductor bar for grounding in its overhead crane specifications:
- CMAA Specification # 70 – Specifications for Top Running Bridge & Gantry Type Multiple Girder Cranes
- CMAA Specification #74 – Specifications for Top Running & Under Running Single Girder Cranes
The previous version of the NEC article stated that metal wheels running on a metal track would be sufficient to complete a grounding circuit of exposed metal parts of cranes that are not intended to carry current. However, in the updated version, NEC clarified that this would no longer be considered a sufficient means of grounding.
This amendment provided guidelines for establishing a more reliable metal-to-metal grounding and bonding connection for the trolley frame and bridge frame. The language in the article states that a separate bonding conductor should be provided because over time, dirt or other debris could build up on the wheels or track and impede the effectiveness of the contact connection.
In addition, the CMAA also believed that a fourth rail would help improve the performance of variable frequency drives, as well as help reduce drive faults by draining away excess current. Most importantly, the fourth rail would help to protect those operating or servicing the crane from accidental electrocution.
After the revision, NEC Section 610.61 read:
“All exposed non-current carrying metal parts of cranes, monorail hoists, hoists, and accessories, including pendant controls, shall be bonded either by mechanical connections or bonding jumpers, where applicable, so that the entire crane or hoist is a ground-fault current path as required or permitted by Article 250, Parts V and VII.
Moving parts, other than removable accessories, or attachments that have metal-to-metal bearing surfaces, shall be considered to be electrically connected to each other through bearing surfaces for grounding purposes. The trolley frame and bridge frame shall not be considered as electrically grounded through the bridge and trolley wheels and its respective tracks. A separate bonding conductor shall be provided.
These requirements are not intended to allow the trolley frame or bridge frame to serve as the EGC for electrical equipment on a crane. The EGCs that are run with the circuit conductors are required to be one of the types described in 250.118. Metal-to-metal bearing surfaces of moving parts are considered to be a suitable grounding and bonding connection. However, the bridge and trolley wheel contact with their tracks is not permitted to be used as a reliable grounding and bonding connection. Because dirt or other foreign surfaces could impede the effectiveness of the wheel-to-track contact as a reliable grounding and bonding connection, the bridge and trolley frames of an electric crane are required to be bonded through the use of a separate conductor.”
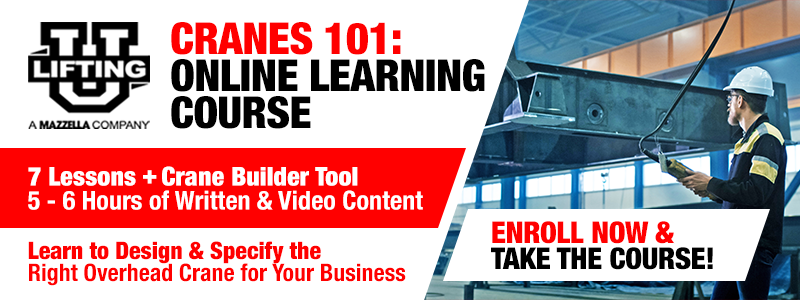
How Does OSHA Address the 4-Bar Grounding Requirements? Is there a Grandfather Clause?
In 2011, OSHA provided an interpretation of their standards to address questions that were asked regarding general industry requirements for grounding overhead cranes and hoists.
Question 1: With respect to electrically operated overhead cranes and hoists, does OSHA require the equipment to have a connection to ground via separate equipment grounding conductor and prohibit the path to ground from going through the wheel bearings lubrication, and the wheel-to-rail contact surface?
OSHA’s Response: OSHA’s standard does not specify this requirement. However, the crane equipment you discuss in your request travels on wheels in contact with supporting rails. Where a separate conductor rail is not provided as the low-impedance path for ground-fault current, the grounding path for the crane equipment, whether through the wheel bearings and lubrication and through the wheel-to-rail contact surface or otherwise, must meet the requirements of OSHA’s standards. OSHA requires the frames and tracks of electrically operated cranes and hoists to be grounded such that “[t]he path to ground from circuits, equipment, and enclosures shall be permanent, continuous, and effective.” 29 CFR 1910.304(g)(5) and (g)(7).[1]
Therefore, to the extent that the employer ensures that the path to ground through the wheel will be “permanent, continuous, and effective,” the employer may ground the crane through the wheels. However, OSHA notes that there are a number of substances that could be initially present, or develop through usage, that could be potentially prevent the ground path through the wheels from being “permanent, continuous, and effective.” These insulating materials include, but are limited to, paint, rust, dirt accumulation, and even animal nests and carcasses. OSHA further cautions employers that the most recent editions of the National Electrical Code (NEC) (2005, 2008, and 2011) include a general prohibition on equipment through the bridge and trolley wheels.[2]
Question 2: Does OSHA have any grandfather-type exceptions regarding the grounding requirements for overhead cranes and hoists?
OSHA’s Response: No. Although there is a grandfather provision in 29 CFR 1910.179(b)(2),[3] it applies to the design of overhead and gantry crane equipment and not to how that equipment is installed and connected at a facility. According to 29 CFR 1910.179(g)(l)(i), all crane installations must comply with 29 CFR Part 1910 Subpart S, which contains grounding requirements in §§1910.304(g)(5) and (g)(7). Existing crane equipment is not grandfathered (excepted) from these requirements based on the date the equipment was designed or installed. See § 1910.302(b)(1) (“The following requirements apply to all electrical installations and utilization equipment, regardless of when they were designed or installed:*** §1910.304(g)(5)-Grounding-Grounding path … § 191 0.3 04(g)(7)- Grounding-Non Electrical equipment.”).
What if Your Crane is Still Equipped With a 3-Bar Conductor System?
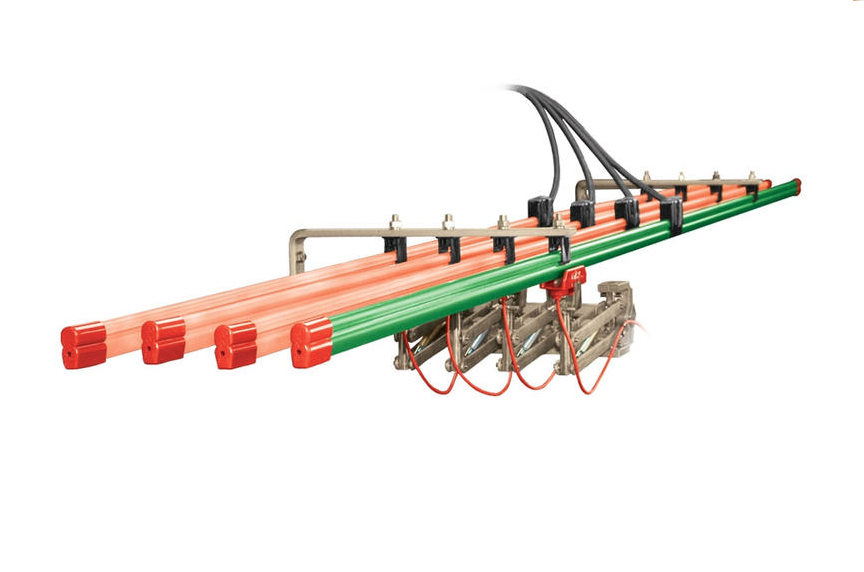
At Mazzella, we believe the ideal method for getting your overhead crane equipment in compliance with NEC 610.61 is to install a 4th ground bar and make sure that the bar is properly grounded to the building grid. If the existing brackets are long enough and can be re-used, this can be a fairly simple and inexpensive solution that can be performed by a reputable crane service company.
However, we know that maintenance and production personnel get anxious when tasked with taking their equipment offline, disrupting production for any period of time, and potentially affecting their company’s bottom line.
There is also an alternative solution that can be used that complies with the requirements of NEC Article 610.61 and OSHA’s interpretations of their standards. This calls for installing a positive collector shoe onto the runway rail and this method provides the following benefits:
- You are not relying solely on the bridge and trolley wheels to ground the crane
- You can prove and ensure a direct path to the ground grid
- This is not a “band-aid” or rigged solution
If you choose to use this method, there are some additional considerations:
- The runway systems must be tied into the ground grid of the plant or building through proper grounding methods
- The runway rail cannot have a pad between the rail and runway girders
- The runway rail must be connected (welded or bolted) at the runway rail joints
- Test the ground path to ensure it is working
Also, any additions or repairs to an overhead crane (including major structural or mechanical upgrades), are cause for a 3-bar conductor system to be upgraded to a 4-bar conductor design prior to powering up and testing the modified or repaired crane and hoist equipment. This includes changes or upgrades to any of the following:
- Drives
- Electrical system or controls
- Bridge or hoist
- Extending runways
- Contact controls to VFDs
Wrapping it Up
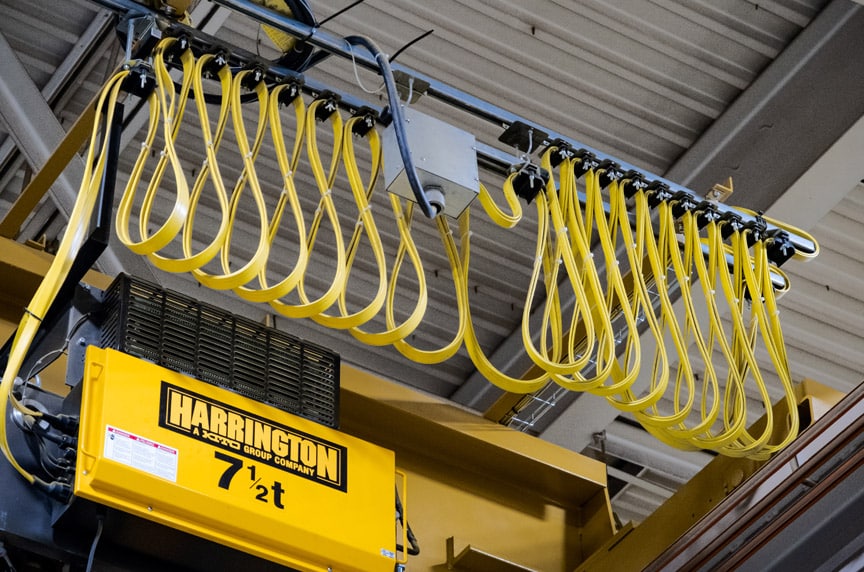
There are three very important things that you should understand regarding NEC Article 610.61 and OSHA language regarding grounding requirements for overhead cranes:
- There is no “Grandfather Clause.”
- It is clearly specified in NEC 610.61 that the bridge and trolley wheel contact with the tracks is NOT permitted to be used as a reliable grounding and bonding connection and that a separate bonding conductor shall be provided.
- OSHA does not directly address the requirement of grounding. They refer to NEC 610.61 and other regulatory agencies.
If you have any questions about whether your overhead crane’s conductor bar electrification system is in compliance with OSHA or NEC 610.61 electrical grounding requirements, or have questions about how you can upgrade your 3-bar conductor system to a to a 4-bar setup, please do not hesitate to reach out.
We have an extensive team of Engineers, Estimators, and Service Technicians who can come on-site and help develop a plan to upgrade your overhead crane for electrical code compliance. Contact us today to schedule a consultation.
Copyright 2018. Mazzella Companies.