Bright, Galvanized, or Stainless Steel Wire Rope: What’s the Right Choice?
The most common finishes of specialty wire rope on the market are stainless steel, galvanized, and bright wire ropes. Find out which one best fits your application.
Whether it’s a construction site, a coal mine, an automotive plant, or a shipyard, wire ropes are the backbone of countless industries and sectors.
But not all wire ropes are created equal. Depending on the application and environment, choosing the right type of wire rope can make the difference between a safe, long-lasting installation and a costly failure or a devastating injury. The most common finishes of specialty wire rope on the market are stainless steel, galvanized, and bright wire ropes.
At first glance, they may appear similar, but each type has distinct characteristics that affect performance, durability, and cost.
So, how do these wire ropes stack up against each other, and which one is right for your application or industry? This article breaks it down. Here’s what we’ll cover:
- What Are the Three Main Finishes of Wire Rope?
- How Is Each Type of Wire Rope Made?
- What Are the Key Strengths and Weaknesses of Each Wire Rope Type?
- Where Is Each Wire Rope Type Most Commonly Used?
- How Do Cost Compare Across Wire Rope Types?
- What are the Maintenance Requirements for Wire Ropes?
- Which Wire Rope Should You Choose for Your Project?
- Final Thoughts
What Are the Three Main Finishes of Wire Rope?
Wire rope is made by twisting multiple strands of metal wire together to form a strong, flexible, and durable rope used in lifting, pulling, securing, and structural applications.
While the core construction and function are generally the same, the surface treatment and composition can vary significantly. This leads to three primary types of wire ropes, each with its own unique appearance and characteristics:
Bright Wire Rope
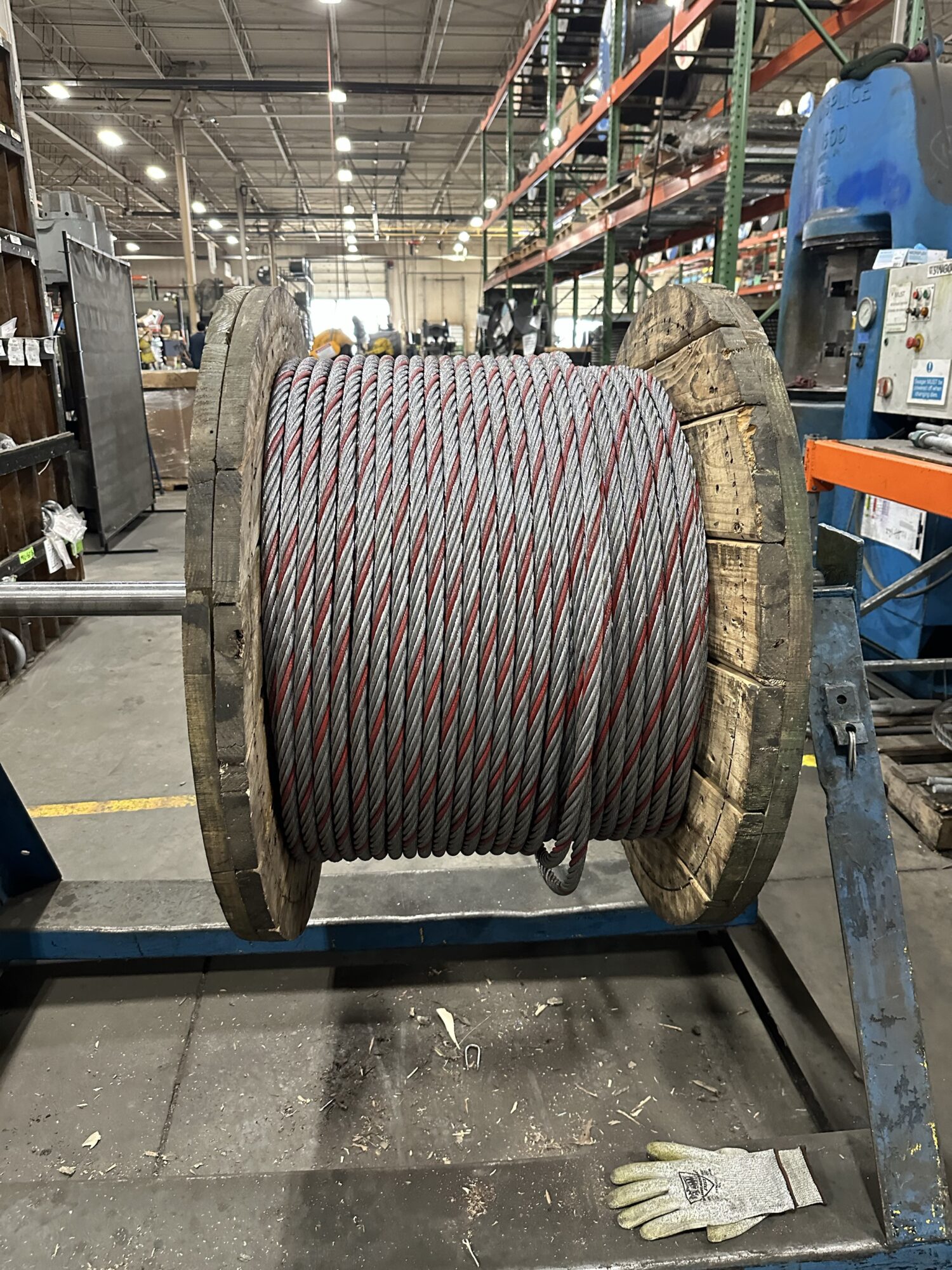
Bright wire rope is untreated and uncoated. It has a clean, shiny appearance, which gives it the name “bright.” Because it lacks any corrosion-resistant coating, it is best suited for indoor applications or environments where moisture and chemicals are not a concern.
Galvanized Wire Rope
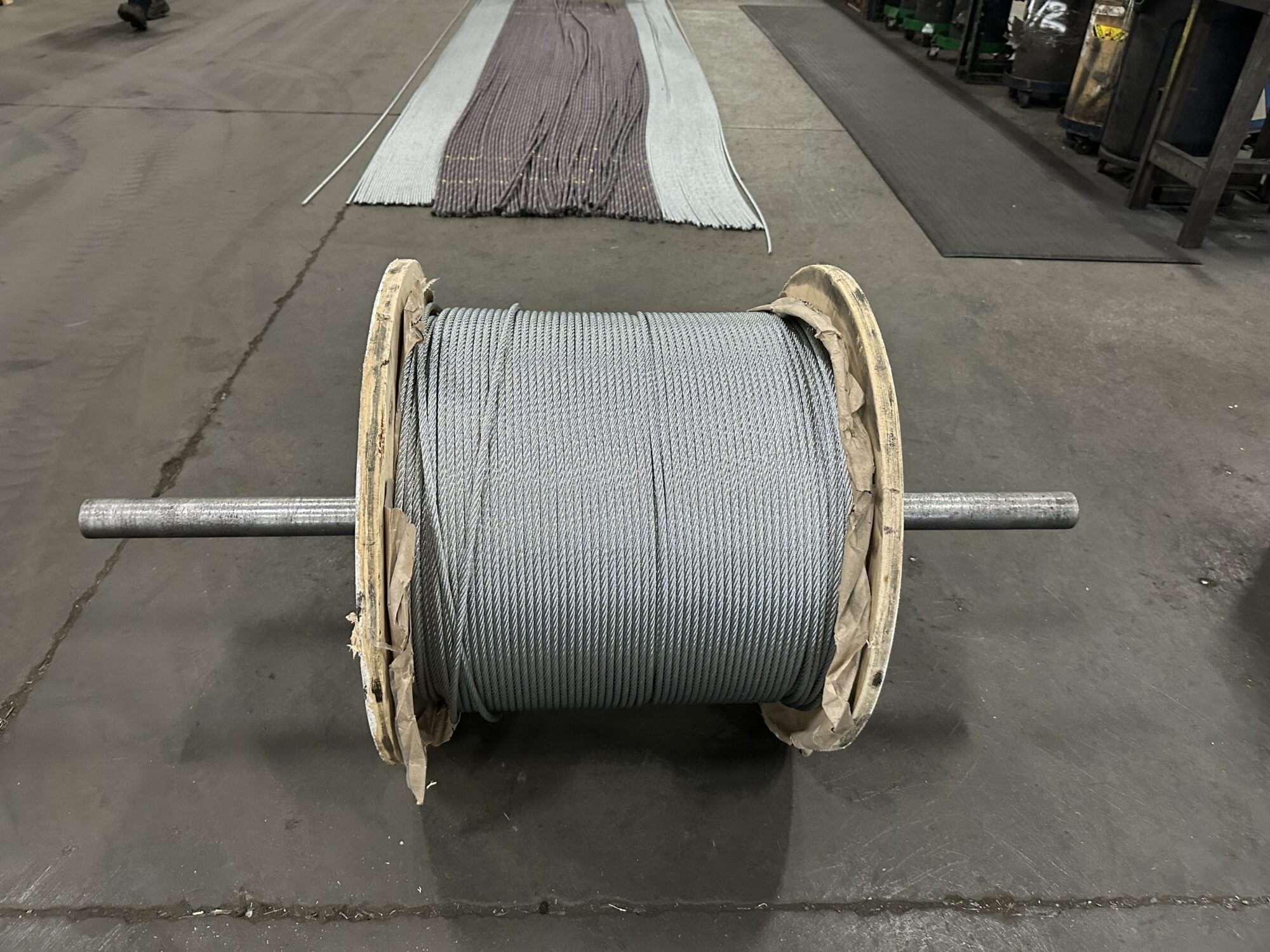
Galvanized wire ropes are coated with a layer of zinc through hot-dip galvanization or electro-galvanization. This coating offers a moderate level of corrosion resistance, making galvanized wire rope a popular choice for outdoor use where occasional moisture is present but extreme corrosion is not expected.
Stainless Steel Wire Rope
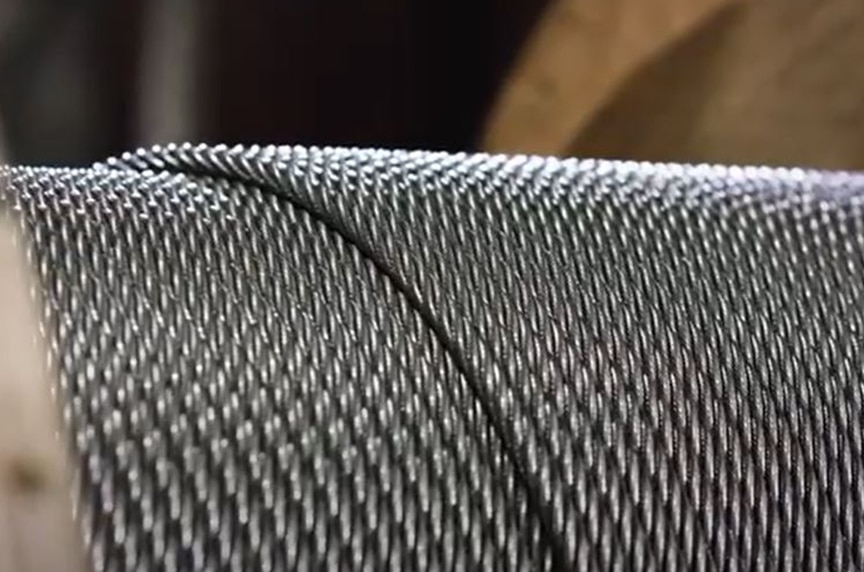
Stainless steel wire rope is made from corrosion-resistant alloys such as 304 or 316 stainless steel. It provides the highest resistance to rust and corrosion, especially in marine, chemical, or high-moisture environments. It’s more expensive than other types, but ideal when durability and longevity in harsh conditions are priorities.
How Is Each Type of Wire Rope Made?
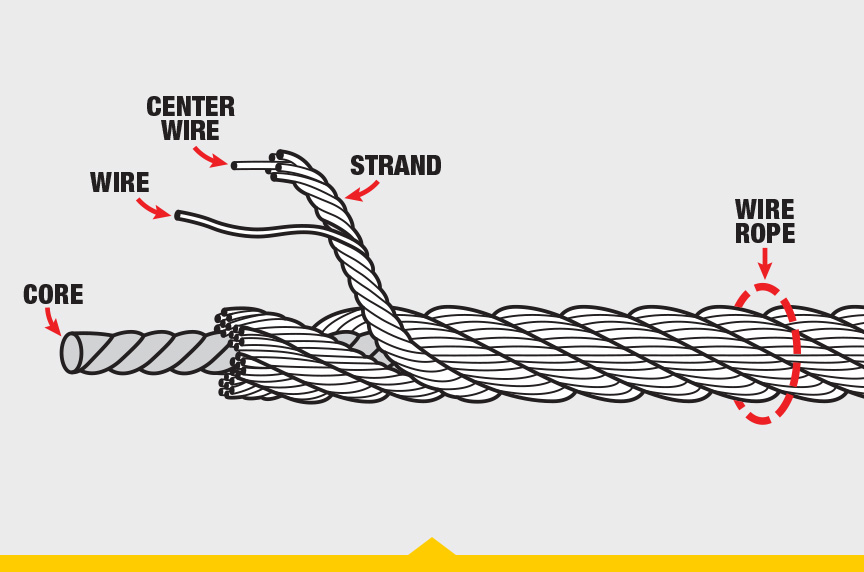
While all wire ropes share a similar basic construction—multiple strands of metal wire twisted around a central core—the materials and finishing processes vary significantly between bright, galvanized, and stainless steel types. These differences directly affect the rope’s durability, corrosion resistance, and performance in various conditions.
How Is Bright Wire Rope Made?
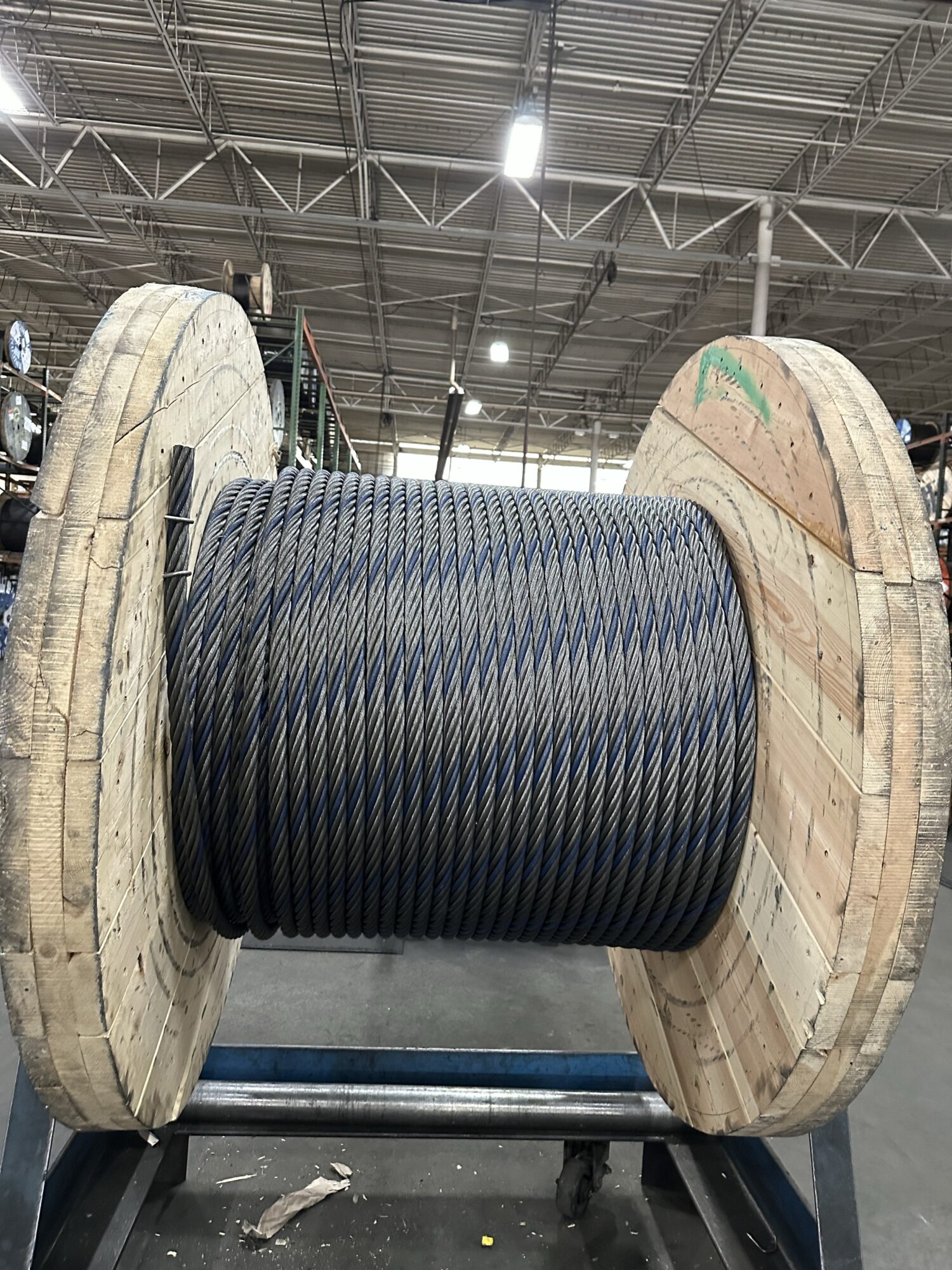
Bright wire rope is manufactured using carbon steel wires that are drawn, shaped, and twisted without any additional surface treatment.
The lack of coating means the manufacturing process is relatively straightforward and cost-effective. However, this also means bright wire rope is more susceptible to rust and corrosion, especially when exposed to moisture or chemicals.
How Is Galvanized Wire Rope Made?
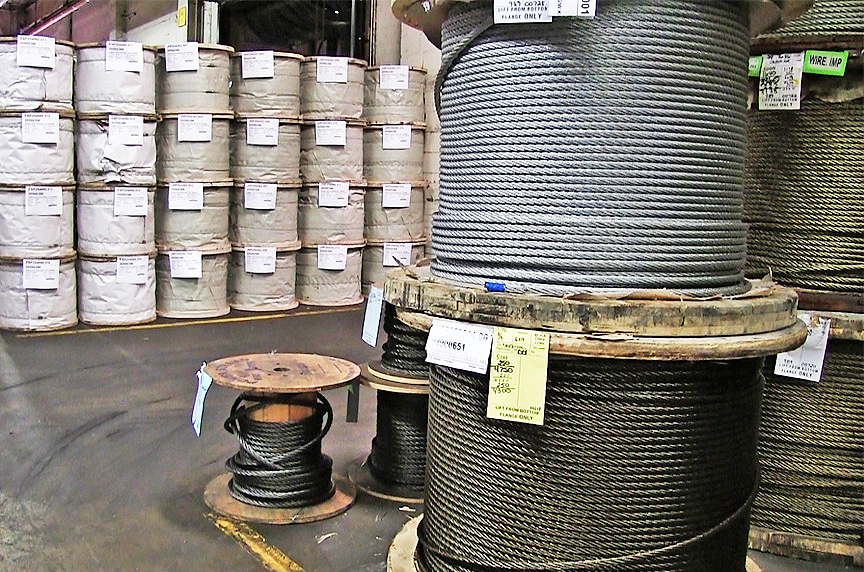
Galvanized wire rope undergoes an extra step after forming: the steel wires are coated in zinc to protect against corrosion. There are two main galvanization methods:
Hot-dip galvanizing: Wires are submerged in molten zinc, creating a thick, durable coating.
Electro-galvanizing: Zinc is applied through an electrochemical process, resulting in a thinner, smoother finish.
After galvanization, the wires are twisted into strands and then into the final rope. The zinc coating offers a balance between corrosion protection and affordability.
How Is Stainless Steel Wire Rope Made?
Stainless steel wire rope is made from high-alloy steel that includes chromium, nickel, and other elements that enhance its resistance to oxidation and chemical damage. Common grades include:
304 stainless steel: General-purpose, good corrosion resistance.
316 stainless steel: Superior corrosion resistance, especially in saltwater or acidic environments.
The strands are cold-drawn and twisted with precision to maintain the rope’s strength and integrity, especially under high-load or corrosive conditions. Because the corrosion resistance is built into the metal itself, no external coating is needed.
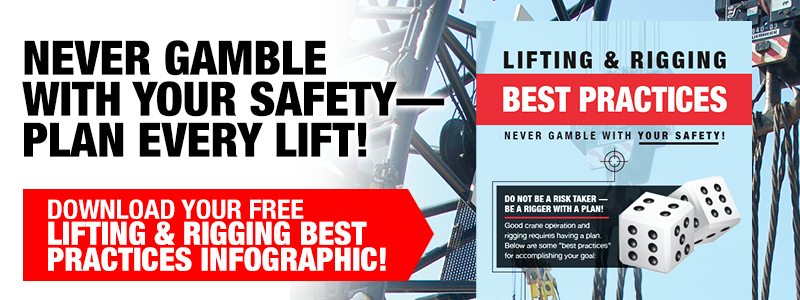
What Are the Key Strengths and Weaknesses of Each Wire Rope Type?
Choosing the right wire rope means weighing performance characteristics like strength, flexibility, corrosion resistance, and cost. Each type of wire rope has its own advantages and limitations.
Strengths of Bright Wire Rope
Bright wire rope offers users the strongest rope finish per cost, making them ideal for heavy-duty applications, especially in indoor settings. They also tend to be the most affordable option.
Weaknesses of Bright Wire Rope
With no coating or protective finish, bright ropes have poor corrosion resistance, making them not suitable for outdoor or wet environments. Bright wire ropes will also require more frequent inspection and maintenance in less controlled settings
Strengths of Galvanized Wire Rope
Galvanized wire ropes offer users a versatile option with moderate corrosion resistance that makes it suitable for light-to-moderate outdoor exposure. They also tend to be more affordable and slightly stronger than stainless steel ropes.
Weaknesses of Galvanized Wire Rope
The coating on galvanize ropes will wear off over time, especially with consistent abrasion and exposure to the elements. Consequently, galvanized ropes are not ideal for harsh marine or chemical environments. Furthermore, the zinc layer makes the rope slightly less flexible than other rope types.
Strengths of Stainless Steel Wire Rope
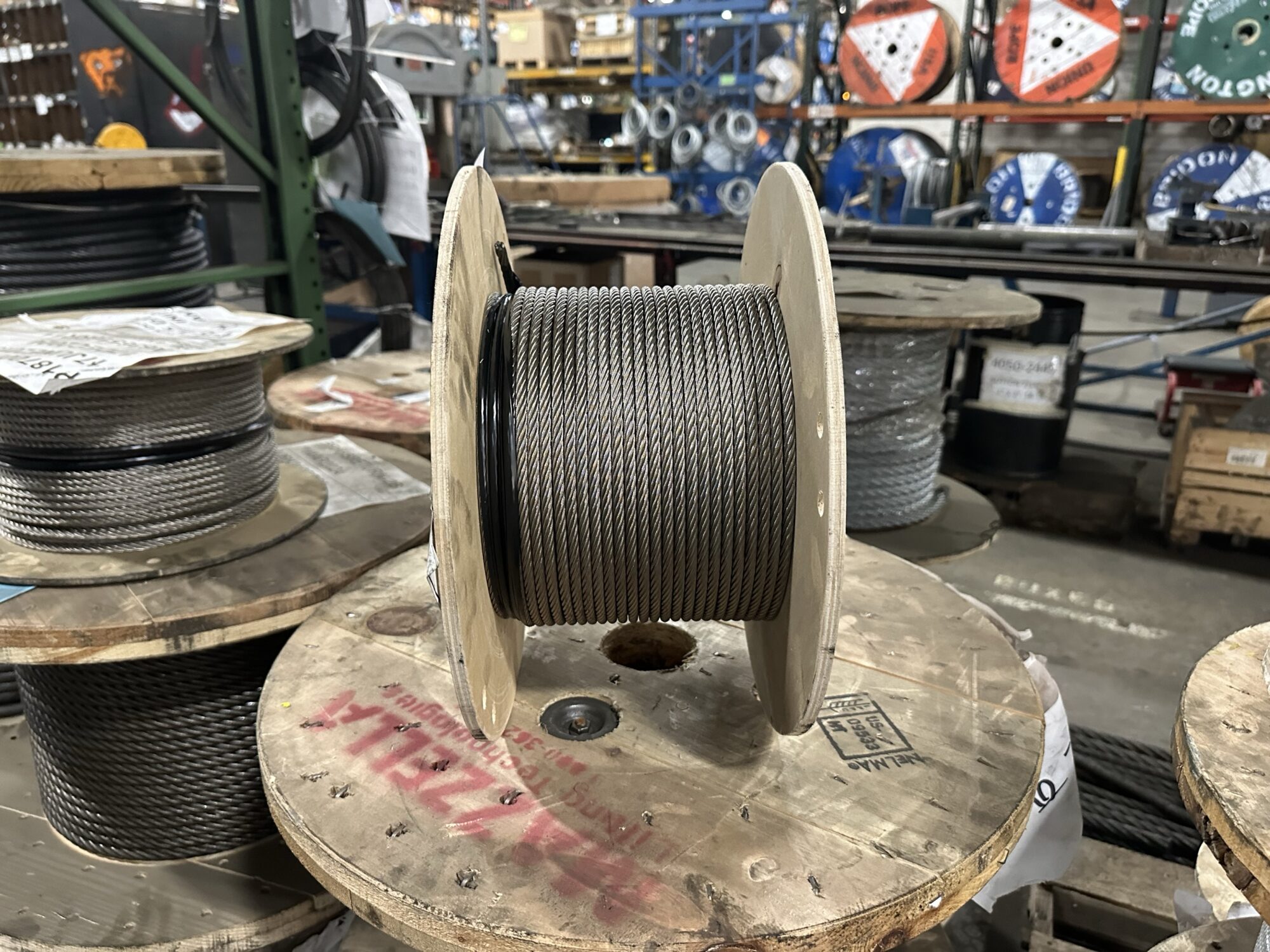
While stainless steel ropes don’t have the same tensile strength as bright ropes, they still offer end users high strength rates. Stainless steel ropes also have excellent corrosion resistance that makes them ideal for marine, chemical, and high-moisture environments. Their high corrosion resistance leads to longer service lives with minimal maintenance requirements.
Weaknesses of Stainless Steel Wire Rope
For many organizations, especially those working on tight budgets, the high cost of stainless steel ropes is the biggest downside. In some cases, stainless steel wire ropes have lower tensile strength than high-carbon bright wire ropes.
Where Is Each Type of Wire Rope Most Commonly Used?
Wire ropes can be found in almost any working environment. However, the type of wire rope found will vary based on many factors.
Stainless Steel Wire Rope
The corrosion resistance provided by stainless steel wire ropes make them ideal for any marine application and environment with high levels of chemical exposure. You can best use them in:
- Shipbuilding and work on boats
- Docks and shipyards
- Coastal architecture
- Oil and gas
- Mining
Due to their sterile properties, stainless steel ropes can also be found in food processing and medical facilities. Stainless steel ropes are also valued for their aesthetic and sleek design, which makes them popular for decorative and architectural applications.
Galvanized Wire Rope
The zinc coating on galvanized wire ropes gives them an extra level of corrosion resistance, making them great for outdoor applications—fencing, construction, rigging. However, as mentioned earlier, the zinc coating will wear off over time, so be prepared to re-galvanize the rope later on.
Bright Wire Rope
The high strength levels of bright wire rope make them best suited for heavy-duty applications where there is minimal exposure to moisture. You will see bright wire ropes on mobile cranes, overhead cranes, and the majority of lifting slings made throughout the country.
You will also see bright wire ropes at:
- Oil and gas sites to move machinery
- Automotive plants to move components
- Aerospace facilities
- Elevators
- Various industrial manufacturing environments
How Do Cost Compare Across Wire Rope Types?
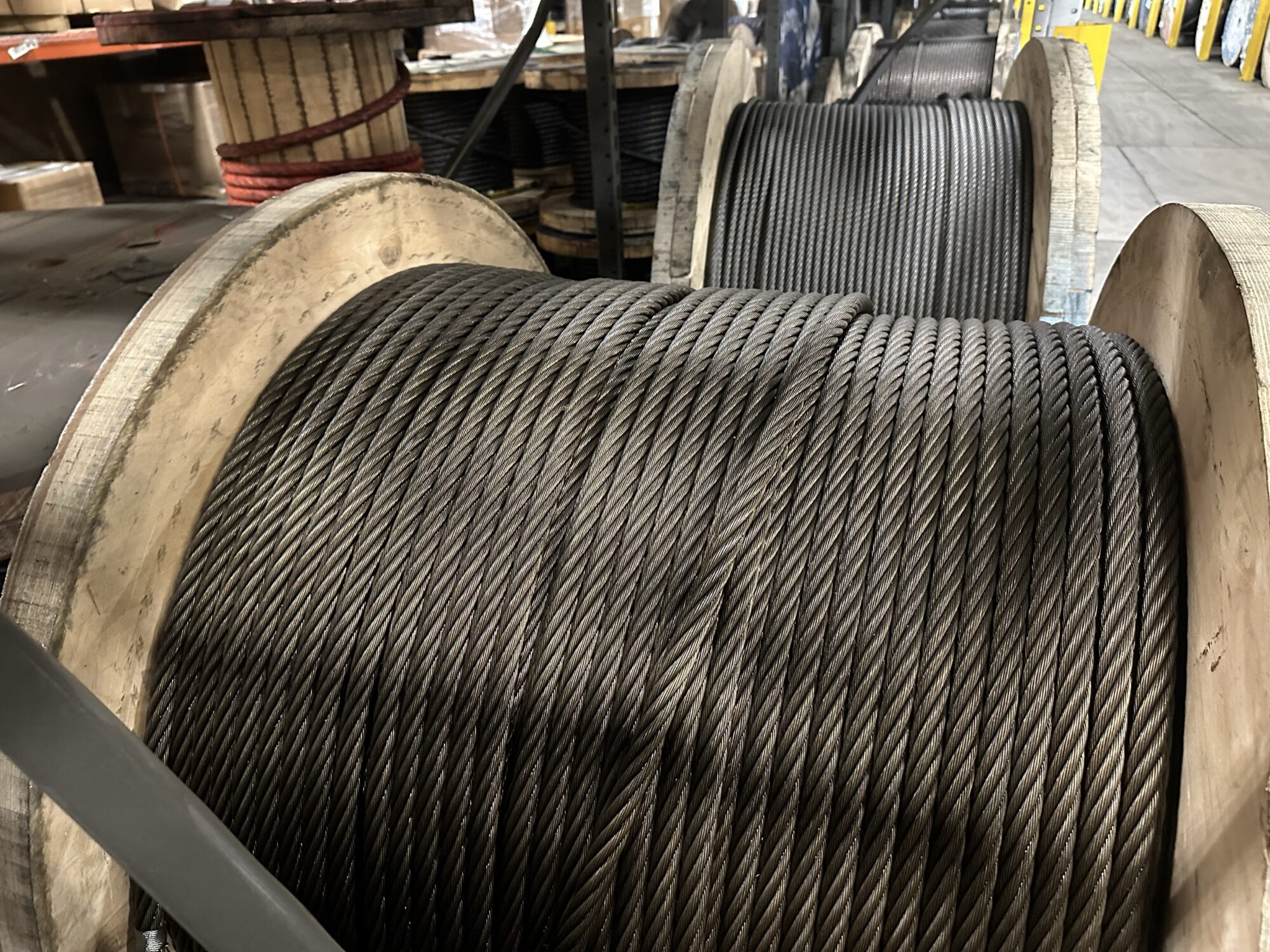
As mentioned earlier, stainless steel ropes are the most expensive wire rope finish. This is due to the extra material and added corrosion resistance. However, that reliability is worth the high price tag for many people, especially those working in marine applications.
Galvanized wire ropes are sometimes viewed as the more affordable alternative to stainless steel ropes, especially for outdoor applications with only occasional moisture exposure.
For bright wire ropes, the lack of coating leads to a cost-effective and straight-forward manufacturing process, making them the most affordable option.
What are the Maintenance Requirements for Wire Ropes?
Regardless of which wire rope you’re using at your job site, proper rope maintenance is crucial for extending the lifespan of the rope and keeping your workers safe:
Lubricate Your Wire Ropes
Lubricating your wire ropes has been proven to enhance the rope’s endurance and longevity, as the lubricant will fight off corrosion that compromises the rope’s integrity. How often you should lubricate the rope will depend on the application, the work environment, how often you’re using the rope, and how many hours are on the crane.
Properly Spool Your Ropes
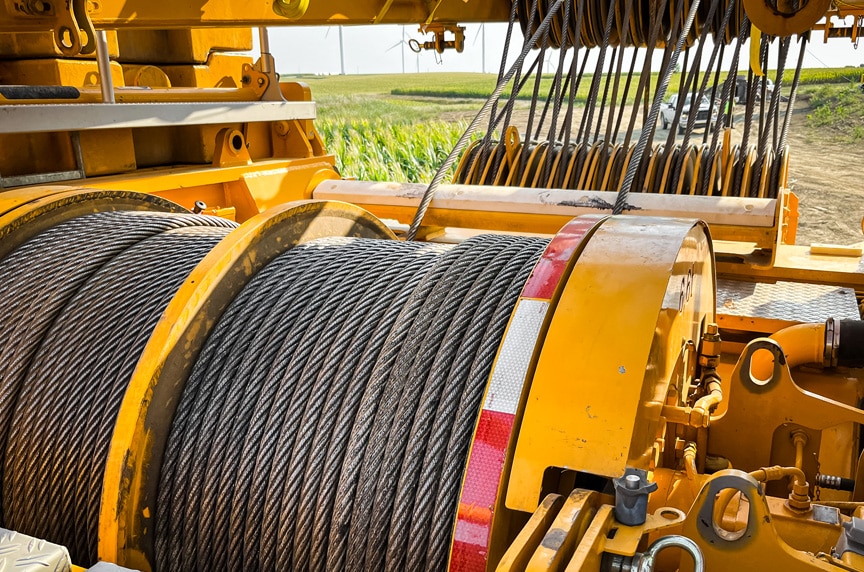
Properly spooling a wire rope will prevent kinks and tangles from damaging the rope’s integrity.
Inspect Your Wire Ropes
Crane operators should conduct a daily inspection of the rope, checking for corrosion, kinking, birdcaging, doglegs, broken wires, and other abnormalities. And while OSHA requires a yearly inspection of wire ropes, you should consider a more consistent inspection cadence—once or month or once a quarter for high use rates.
Hiring a third-party inspector can also help you get an unbiased opinion and a more thorough inspection process.
Which Wire Rope Should You Choose for Your Project?
When it comes to choosing between stainless steel, galvanized, and bright wire rope, there’s no one-size-fits-all answer. It all depends on your specific application and environment.
Bright wire rope offers a budget-friendly option for dry, indoor applications but falls short in wet or corrosive settings.
Galvanized wire rope provides decent corrosion resistance at a moderate cost, making it a go-to for many general outdoor uses.
On the other hand, stainless steel wire rope delivers exceptional durability in harsh conditions, especially where rust and corrosion are constant threats. However, that extra reliability comes with a higher price tag.
By understanding the manufacturing process, strengths and weaknesses, and ideal use cases of each type, you can make a confident, informed decision. Whether you’re securing loads, lifting heavy equipment, or building in marine environments, the right wire rope ensures both safety and longevity.
Final Thoughts
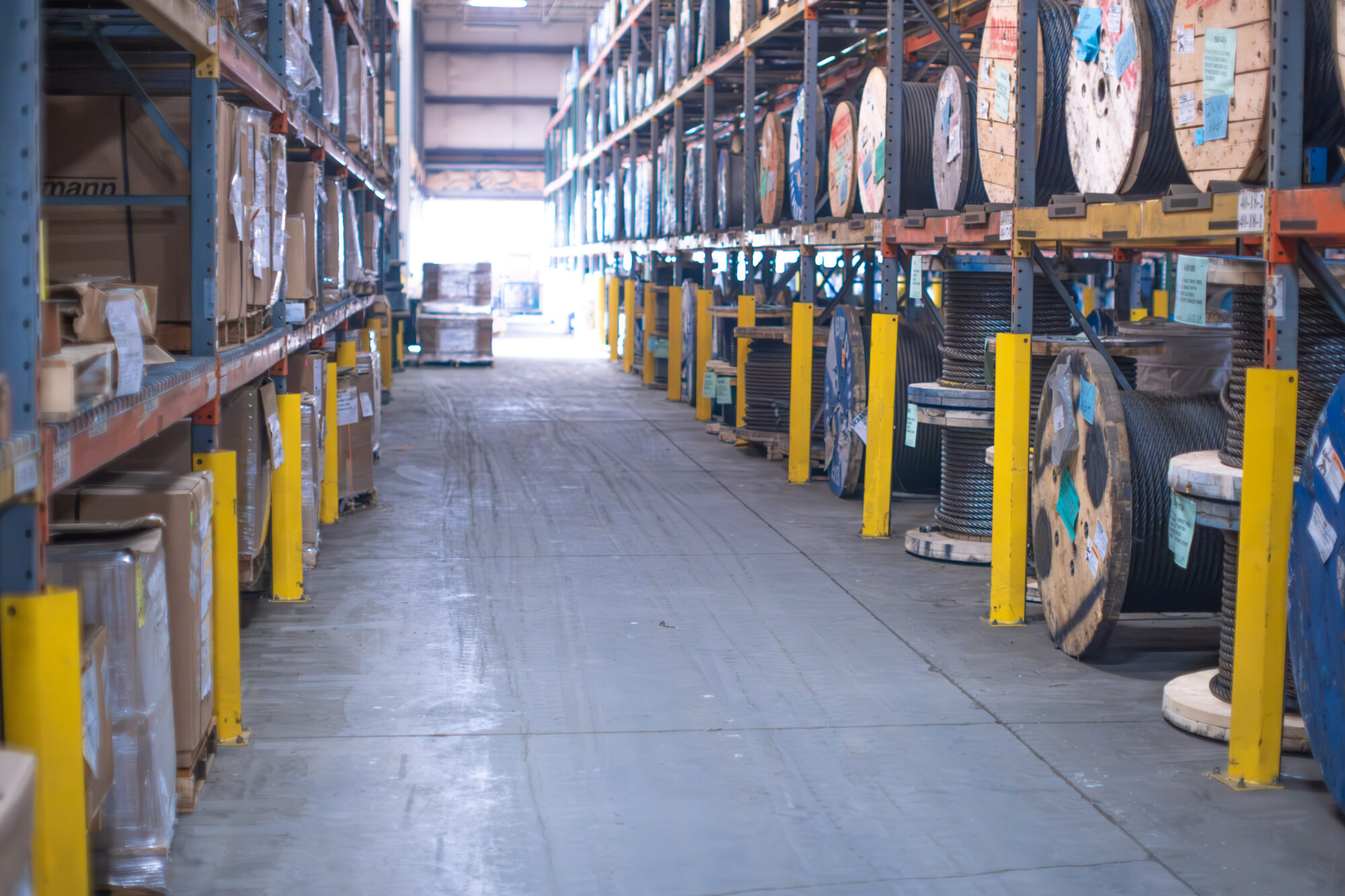
We hope you learned which type of wire rope finish is best for your application. At Mazzella, we are a one-stop-shop for all your wire rope and rigging needs. We have one of the largest wire rope inventories in the United States, along with a world-class inspection and training department with a nationwide footprint. Contact one of our team members if you have any questions.
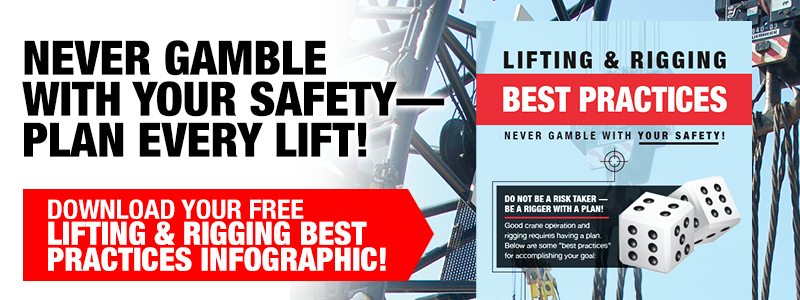
Copyright 2025. Mazzella Companies.