Structural vs. Roll Formed Pallet Racking: Advantages and Disadvantages
When designing a pallet-racking system, a major consideration is whether to go with a structural or roll formed beam and upright construction. It’s important to understand the differences, benefits, and drawbacks of each system to determine which is the best fit for your warehouse.
What’s the difference between structural racking and roll formed racking? Which option should I consider? Which one is most efficient for my operation? These are a few questions we are frequently asked by customers in the beginning stages of designing a pallet racking system.
When designing a pallet-racking system, a major consideration is whether to go with a structural or roll formed beam and upright construction. It’s important to understand the differences, benefits, and drawbacks of each system to determine which is the best fit for your warehouse.
In this article, you can expect to learn:
- What structural racking is and how it’s made
- Advantages and disadvantages of structural racking
- What roll formed racking is and how it’s made
- Advantages and disadvantages of roll formed racking
What is Structural Racking?
Structural racking is made by hot-rolling raw iron into thick, low-gauge steel components that are bolted together. This process creates high-quality, heavy-channel steel that can store heavy pallets and withstand harsh conditions, such as lift truck impact.
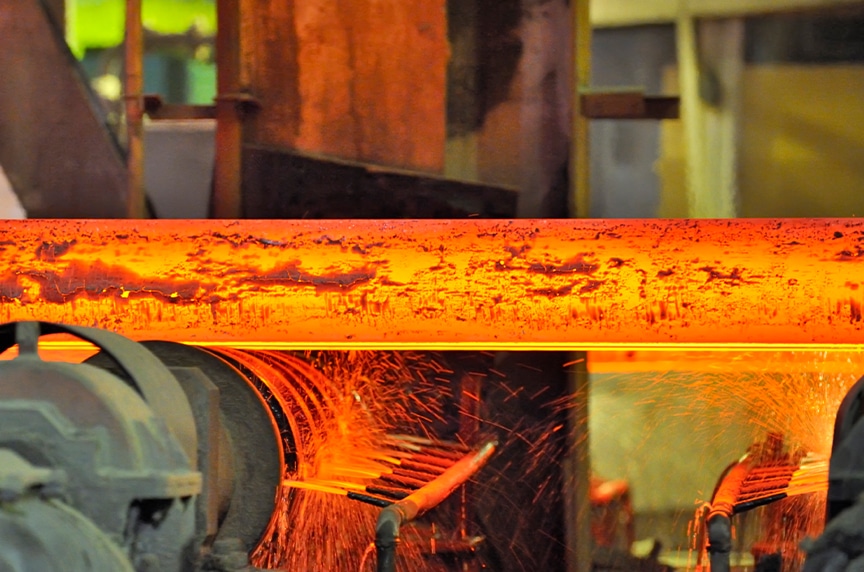
Structural racking systems are best used in warehouses with heavy pallet loads and/or risk of lift truck impact. Companies with fast-paced environments, heavy lift truck traffic, and/or high employee turnover with untrained employees are more likely to experience lift truck damage to their system.
Structural racking can be used to construct all types of pallet racking systems. It is highly recommended for use in drive-in/drive-through pallet racking systems, where employees are repetitively maneuvering lift trucks in and out of narrow bays. Most commonly, structural racking systems can be found in food and beverage distribution facilities, or any cold environment warehouse.
Advantages of Structural Racking
Strength and Durability
Structural racking is made with heavy, low-gauge steel components that are assembled by bolting them together. This creates a system with more structural integrity than roll formed systems where standardized components simply snap into place.
Structural racking systems can support heavier pallet loads and better withstand damage from lift trucks without collapsing or requiring replacement parts.
Accessories
Accessories can be welded to your structural racking system to add customized protection and reinforcement to increase the longevity of the system.
The two most common accessory modifications are:
- Bullnose / Angle Deflector – this component is welded to the front of the racking frame to act as a column protector. This provides additional protection against lift truck damage.
- Reinforced Column – individual upright columns can be reinforced up to 60″. This multiplies the system’s reinforcement and enables the bay to store heavier loads without bending or collapsing.
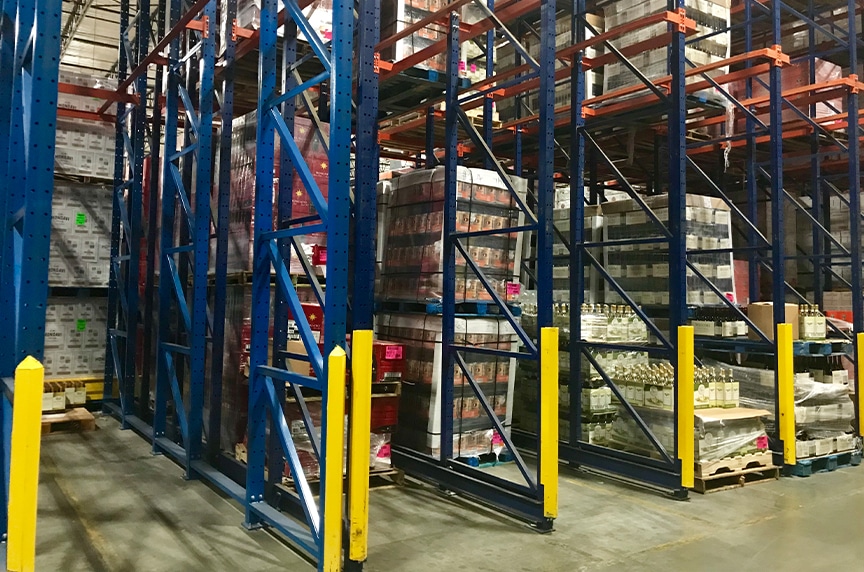
Customized to Precise Specifications
Roll formed racking systems can be engineered to a degree but are typically more modular or standardized type solutions.
Structural racking is a more sophisticated system that is custom engineered to fit the diverse needs of a warehouse configuration.
Long-term ROI
Structural racking is strong, durable, and diverse, so it can withstand more damage and use over a longer period of time. A structural racking system will typically last 5-10 years longer than a comparable roll formed system.
Disadvantages of Structural Racking
Longer Lead Time and Installation
Since structural racking is precisely engineered, it requires a much longer lead time—typically about 5-10 weeks—in order to specify the system.
Structural racking systems are highly customized and assembled by physically bolting each beam and beam level together. Consequently, installation of a structural racking system is also more difficult, time consuming, and requires skilled labor.
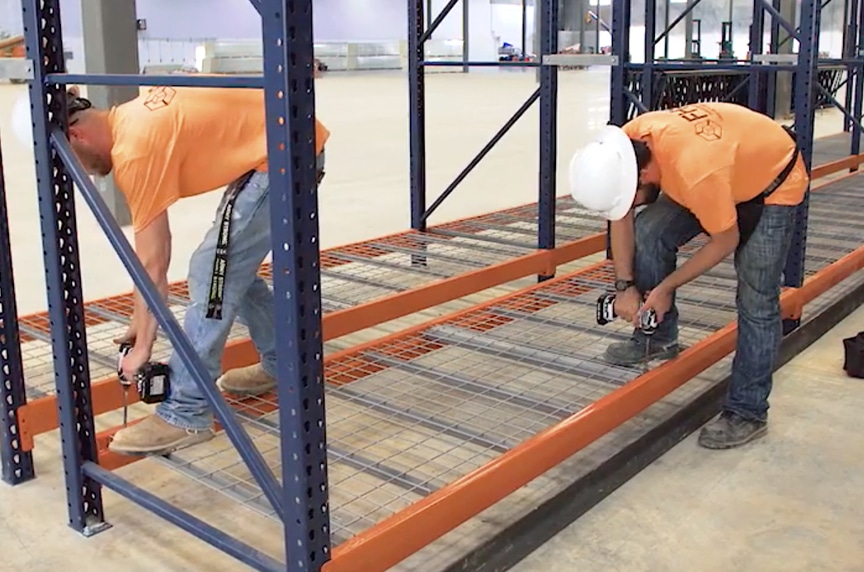
Higher Price
Because of the longer lead time, skilled labor, higher-quality material, and precise engineering associated with structural racking systems, they will come at a higher premium than a comparable roll formed racking system.
Limited Adjustability
Because the components of a structural racking system are bolted together, adjusting beam levels or replacing parts is much more difficult, time consuming, and often requires the assistance of a professional. Therefore, structural racking systems are not recommended for facilities with frequently changing SKUs or product sizes.
What is Roll Formed Racking?
Roll formed racking is made by cold-rolling steel into thin, standardized components that are easily snapped into place to construct a system. This light higher-gauge steel stores lighter load capacities and is more susceptible to lift truck damage.
Roll formed racking systems are best applied to facilities that store seasonal or changing products of varying sizes in a slower-paced environment. Because these systems are easier to assemble and disassemble, they allow for quicker and easier adjustability.
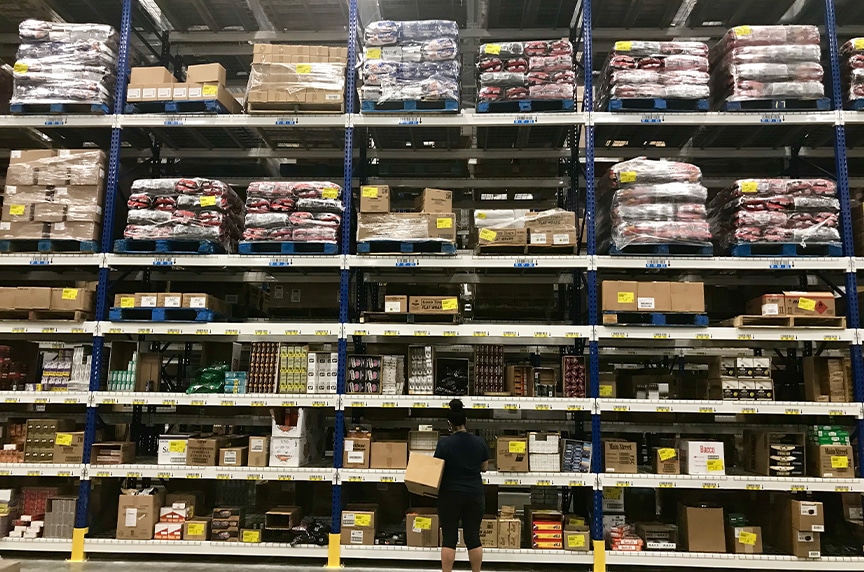
Retail and 3PL warehouses—warehouses used for third-party storage services—are common places to find roll formed racking systems.
Roll formed racking can be used to construct any type of pallet racking system. However, it is most frequently used in selective pallet racking systems.
Advantages of Roll Formed Racking
Adjustability
Roll formed racking components are more standardized and easily assembled by snapping modular components into place. They are easily adjusted, disassembled, and reassembled for situations where you might need to change beam elevations, replace parts, or reconfigure the layout.
Because of their adjustability, these systems are especially useful in situations with frequently changing and limited SKUs where selective pallet racking is often implemented.
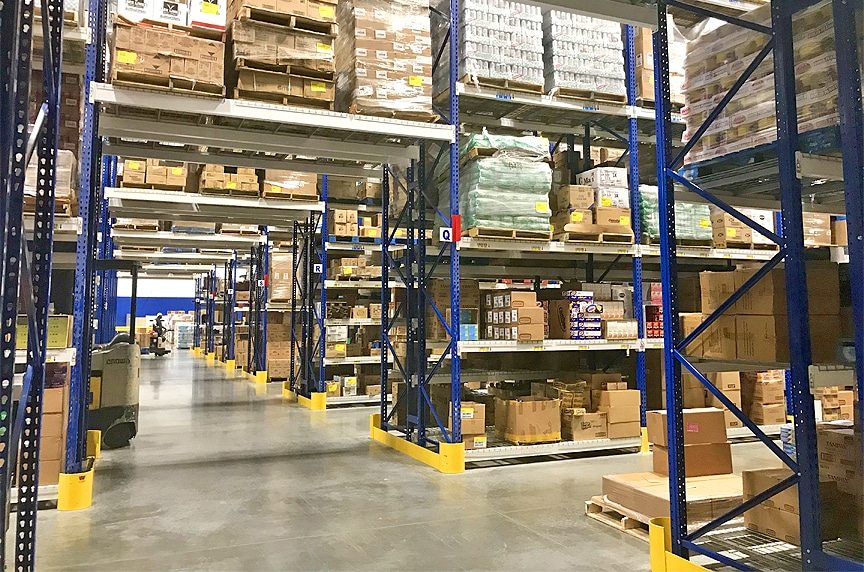
Adaptability
Since these systems are easily adjustable, parts are also easily replaced. Most roll formed components are a universal size and shape, so parts can usually be used together even if they are from different manufacturers.
Lower Price and Quicker Lead Time
Because the parts in a roll formed racking system are less customized, they are quickly shipped, easily assembled, and priced at a lower premium. In many cases, you can receive a roll formed racking system within 48 hours.
Disadvantages of Roll Formed Racking
Susceptible to Damage
The thinner higher-gauge steel used to make the racking system’s beams and uprights has less structural integrity than a structural racking system and is therefore more susceptible to damage from lift trucks.
The components of a roll formed racking system rely on shape for strength, similar to the structure of an aluminum can. In the event of an overload or side impact, the racks will not provide any additional support and will likely collapse.
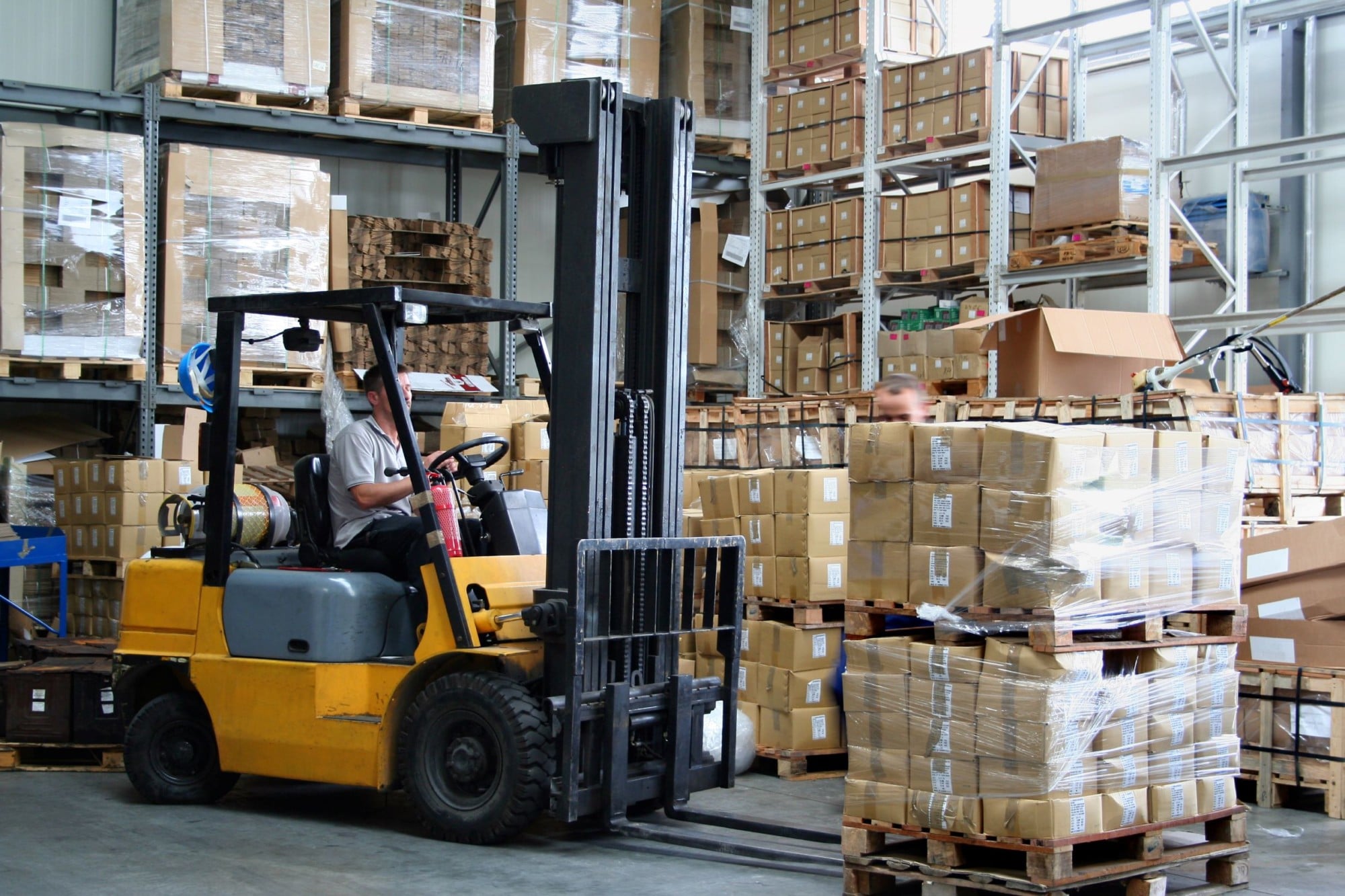
Lower Capacity Limit
Structural racking systems can support exponentially more weight than a roll formed racking system. A typical pallet load on a roll formed racking system is approximately 2,000-2,500 lbs. When the pallet loads begin to approach 3,000 lbs. or above, roll formed racking may become compromised.
Less Longevity
These systems are more susceptible to damage and have less structural integrity. They often require replacement parts due to damage and are not as durable as a structural racking system.
In cases where there is frequent lift truck damage—often due to high employee turnover, poorly-trained employees, heavy lift truck traffic, or a fast-paced environment—any upfront cost-savings may be wiped out in future maintenance and replacement parts.
Wrapping it up
Structural racking systems are highly durable, long-lasting, and customizable. Consequently, they also come with an exponentially longer lead time, higher price, and limited adjustability.
Structural racking systems are not recommended for warehouses with frequently changing SKUs and are best applied to fast-paced warehouse environments with heavy loads where frequent lift truck impact may be of concern.
Roll formed racking systems are the cheaper option with a quick turnaround and high adjustability. On the flip-side, their limited structural integrity makes them less durable and much more susceptible to damage.
Roll formed racking systems are best applied to environments with frequently changing SKUs, lighter loads, and where frequent lift truck impact is not of concern.
How We Can Help
At Mazzella, we have a division dedicated to providing complete, custom designed warehouse solutions ranging from pallet racking systems—both structural and roll formed—to conveyors, docks, doors, and more.
Our talented and experienced team consists of technicians, system installers, project engineers, project managers, and an extensive sales and support staff. If you are interested in learning more or want to schedule a consultation, contact us to speak with a specialist.
<!–[if lte IE 8]><![endif]–>
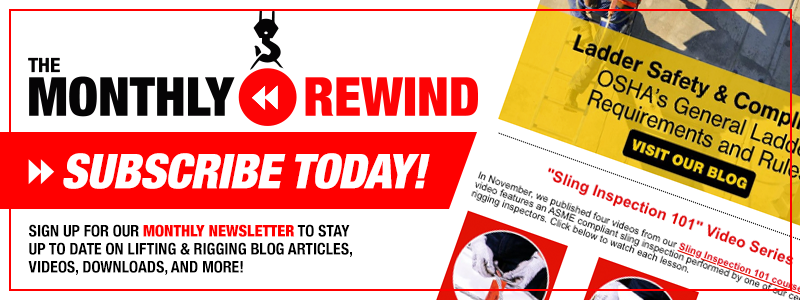
Copyright 2020. Mazzella Companies.