Warehouse Racking and Pallet Rack Systems: Different Types and Design
Warehouse pallet racking can vary so much in terms of specifications, applications, and configurations. In this article, we’ll discuss the different considerations for selecting the proper pallet rack storage system, and the different designs and components of the most popular pallet rack warehouse systems.
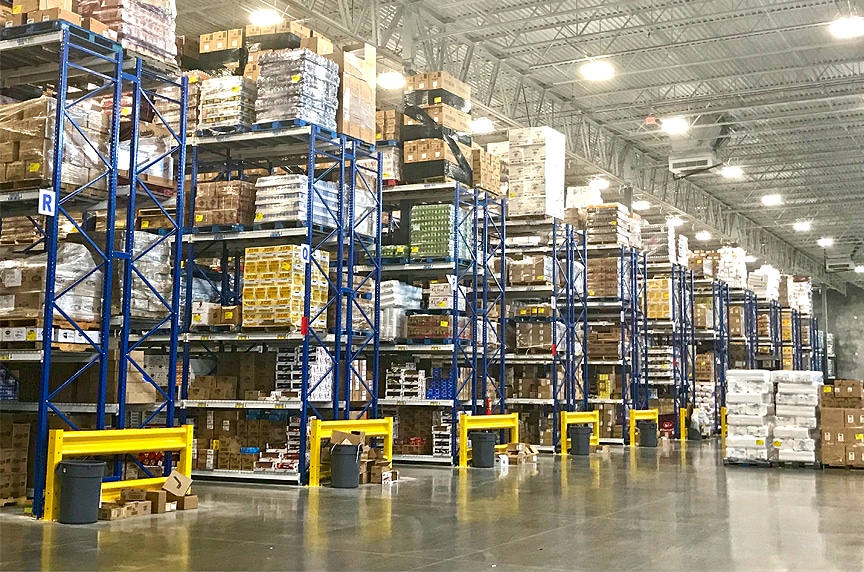
Do you walk out into your warehouse and feel like it’s a chaotic and unorganized nightmare? Are there forklifts buzzing by, pallets scattered on the floor, and workers scrambling to figure out where products and inventory are located?
Or, are you looking for a warehouse management system to maximize the existing storage space in your facility and reduce “honeycombing” in your high-density storage areas?
You can reduce clutter, maximize your warehouse space, and increase worker productivity by investing in a warehouse pallet racking system. Pallet racking systems can solve a number of warehouse storage issues, including:
- Getting pallets organized and up and off of the floor
- Maximizing your existing warehouse space
- Simplifying the loading and picking of pallets or cartons
- Improving worker efficiency and automating some of the labor required to store and retrieve pallets
At Mazzella FHS, we understand how frustrating it can be to feel like your warehouse or distribution center isn’t as organized or working as efficiently as it could be. We offer a variety of warehouse solutions to solve any obstacle you may encounter and we work with our customers to deliver a custom solution that fits within their budget and time frame. We offer everything from simple selective rack and drive-in pallet racking, to more innovative and complex storage technologies and solutions.
In this article, we’ll talk about the different considerations for selecting the proper pallet rack storage system, and the different designs and components of the most popular pallet rack warehouse systems.
Considerations for Selecting a Warehouse Racking System
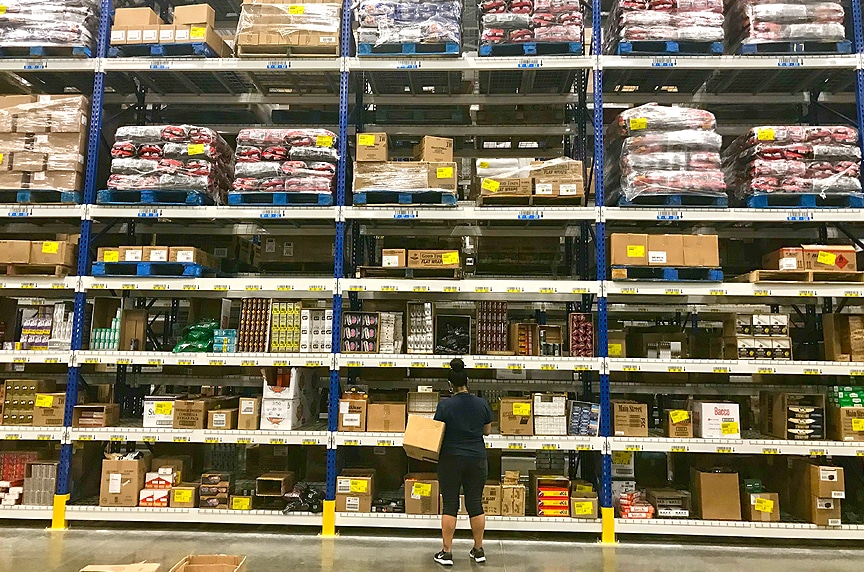
When designing a pallet rack system, some of the factors you need to understand are: total # of SKUs, total # of pallets, weight of material, inventory retrieval method, turnover time, and whether these will be full or split case picks.
Warehouse pallet racking can vary so much in terms of specifications, applications, and configurations. No two racking systems are exactly alike, and one system that has been designed for a similar building structure, or a similar product type, may not be the best design for your facility.
When considering the best type of warehouse racking system for your business, you should consider the factors below to maximize efficiency, streamline your processes, and get the best bang for your buck:
Number of Palletized SKUs
A stock keeping unit (SKU) is a unique number assigned by a retailer to items in their inventory. To understand the design and layout of a pallet rack storage system, you need to know how many SKUs will be stored in the rack system. For example, you may need to store six different SKUs on pallets, all with their own unique dimensions.
Overall Number of Pallets
The total number of pallets you need to store per rack system.
Dimensions of Pallet
You’ll need to know the dimensions of the pallet (width, depth, and height) in order to design the bays and racks to maximize storage space in your racking system.
Weight of Pallet and Material
How much does each pallet weigh? This will determine the capacity of the steel beams, what kind of decking can be used, and if any additional pallet supports are needed to support the materials.
The type of Product
Is it perishable, is it fragile, does it need to be climate controlled?
Order of Inventory Retrieval
First-in First-out (FIFO) or Last-in First-out (LIFO) retrieval?
Turnover Time
How long will the SKUs stay in your facility? Hours/weeks/months?
Full Case or Split Case Picking
The same facility can utilize one method over another or utilize both methods for different products or processes:
- Split case picking – Individual items are picked from bins or open cartons, typically with lots of SKUs and low pick volume per SKU. This method is commonly used in e-commerce or other order fulfillment centers.
- Full case picking – This method involves the gathering of full cartons or boxes of product for distribution. This method is commonly used for retail distribution of goods, truck or train loads of products, supply chain, logistics, etc.
Seismic Activity Where the Rack is Located
Seismic activity can affect the size of footplates, beam sizes, and additional material required for rigidity and support of the system.
Warehouse Pallet Rack Design, Components, and Construction
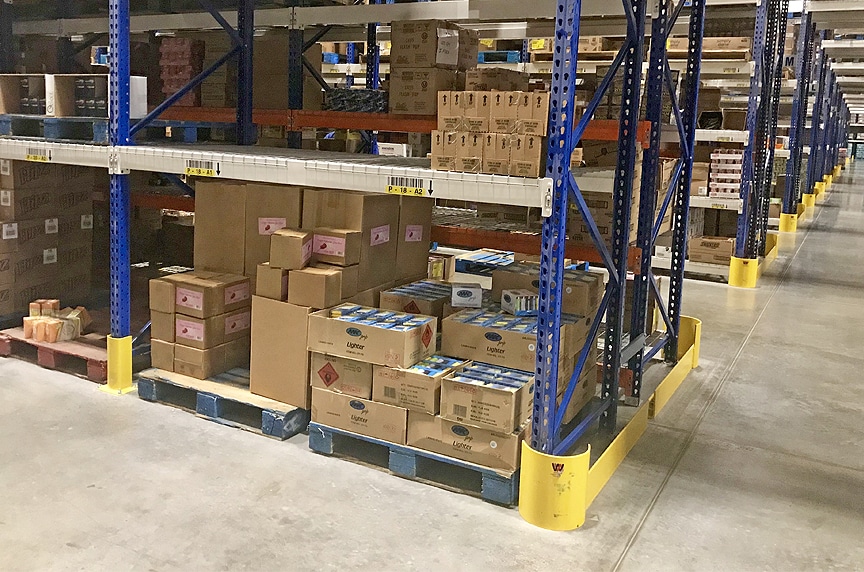
Protective plates (shown here) can be integrated into a racking system to protect impact areas from forklift or truck damage.
Below are some of the components and design factors for any type of warehouse storage or pallet rack system:
Rack Construction
What material are the beams, uprights, and supports made from?
- Roll formed steel – steel coils or sheets are run through a machine that kinks and rolls the material into the final structural shape. It’s less expensive than structural steel, however it is more susceptible to damage from fork lifts or trucks. Once it’s been damaged, the structural integrity is gone.
- Structural steel – steel made from raw iron that has been processed and formed into its final shape to make it more durable and offer less maintenance throughout its lifetime. It is more expensive to design a pallet rack system using structural steel.
- Hybrid – a mix of structural steel for “impact” areas such as the base, face, or frames of the rack system, and roll formed material for the back end or interior parts of the system.
Rack Decking
How will the pallets be supported? Common materials are steel beams, wire mesh decking, carts, gravity rollers, or solid decking (highly specialized for archiving applications).
Rack Post Protectors
Additional protection can be anchored into the ground and can be designed to take the brunt of a strike from a forklift or truck.
Rack Material Finish
Galvanized material can be used for outdoor applications, as well as an epoxy or powder coat finish to protect against corrosion.
Different Types of Warehouse Racking Systems:
Selective Pallet Racking Systems
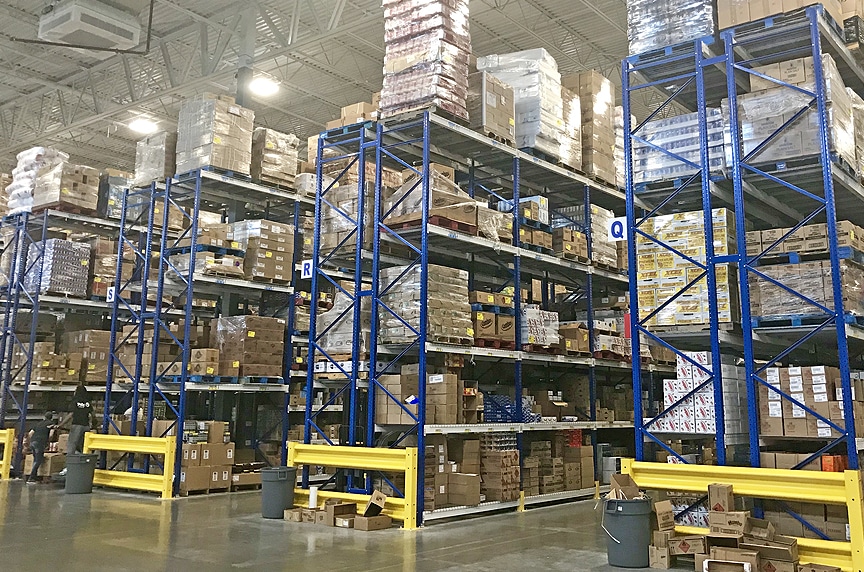
Selective pallet rack systems are inexpensive and designed to organize product and get pallets up and off of the floor.
Selective pallet racks are the most popular type of warehouse storage and pallet rack system on the market. They offer an inexpensive design and the largest selection of sizes and accessories to be custom configured for your warehouse storage application. Designed to get pallets off the warehouse floor and into a racking system, they provide immediate accessibility to store or unload pallets. Using selective pallet rack systems allows you to fully utilize your warehouse floor space as well as efficiently manage worker time.
Picture a really big book shelving system and you’ll understand how selective rack systems work. Selective storage racks are adjustable—allowing you to change the beam levels so you can find the right height for your load, or reconfigure the entire system for new or different sized pallets. This flexibility allows you to customize and maximize storage space within the racking systems.
Selective pallet racks are available in both roll formed and structural steel to accommodate your budget and support requirements.
Selective pallet racks are great for: Standard storage of all needs that require immediate access to products or pallets.
Inventory management: First-In First-Out (FIFO) retrieval
Advantages of selective pallet racking:
- Available in numerous capacities, sizes, and configurations for custom fit
- Immediate access to all storage
- Can be made from roll formed, structural steel, or a combination of both materials
- Easy to adjust shelf heights
- Inexpensive – lowest cost option per square foot
Disadvantages of selective pallet racking:
- Lots of aisles – not efficient on floor space
- You need a large amount of warehouse space to accommodate a high volume of inventory
- Lowest pallet storage capacity of all of the systems
- Increased time spent loading and unloading product or stock lines
- Not cost-effective for high-volume storage
- Limited storage height
Drive-in Pallet Racking Systems
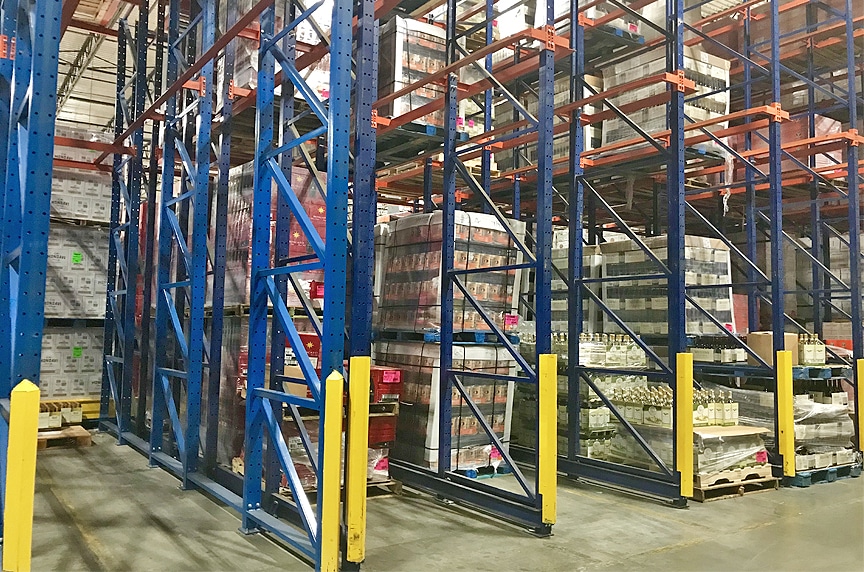
Drive-in pallet rack systems maximize warehouse space and allow for high-density storage of similar products or SKUs.
Drive-in rack systems offer maximum-density storage of similar products and pallets in your warehouse. Drive-in rack systems eliminate aisles in a warehouse facility because the drive-in system is made for storing high quantities of similar product which use the same entry and exit point for each bay or rack. Since drive-in rack systems are fork-lift accessible, they offer maximum-density storage and product or pallets may be stored in lanes up to six or more positions deep on the rack.
A forklift enters the racking from one side to load a pallet on to the back of the rack. From there, the pallets are loaded in working from front to back—giving more depth and up to 3X the amount of storage as selective pallet racking. This results in lower storage cost per pallet, per square foot.
Drive in racking can be single entry where forklifts have access to one side only, or double entry where the forklifts can access both sides of the racking structure.
The drive-in system can be designed specifically to best fit your needs with different heights and depths, as well as a wide variety of different components. This system can be ordered in roll formed or structural steel for more support. If you are looking for a space saving solution that can increase warehouse area, consider the drive-in system.
Drive-in pallet rack systems are great for:
- Manufacturers with limited SKUs
- Large amounts of similar products and limited warehouse space
- Fragile products that can’t be stacked
- Cold storage applications – store a lot of pallets in a small freezer space
Inventory management: Last-In First-Out (LIFO) retrieval
Advantages of drive-in pallet racking systems:
- Most cost-effective high-density system available
- Can be constructed from roll formed or structural rack material
- Reduces square footage imprint up to 35% compared to selective pallet racks
Disadvantages of drive-in pallet racking systems:
- Not a good fit for a facility with a lot of different products
- LIFO inventory management – older products will not be used before new products are added. It can be challenging to rotate time-sensitive products.
- Must be structurally sound and have good support – more open to abuse from forklift damage and misuse. Front uprights should be braced or protected against rack damage from forklift trucks.
- Requires standardized pallet sizes to fit in lanes – not flexible in design to allow for pallet size changes or SKU increases
Push Back Pallet Racking Systems
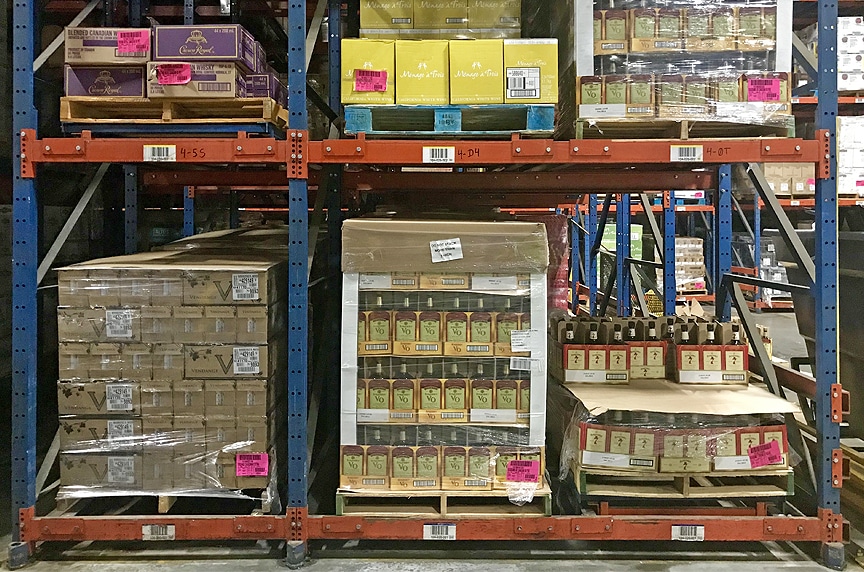
Push back pallet racks are high-density storage solutions that load pallets from the front onto a nested cart system that slides on inclined rails.
Push back rack systems are designed to allow for dense storage of product that doesn’t require First-in First-Out retrieval. Push back pallet racks are stationary rack structures that load pallets from the front onto a nested cart system that slides on inclined rails.
A push back rack system is great for high-density storage of multiple product lines or SKUs. This product uses a design that eliminates maintenance and offers greater selectivity. In a push back system, a pallet is placed on a free rolling cart that is pushed back in to the system each time an additional pallet is loaded on to the system. These systems are available in two, three, four, five, and six-deep cart configurations. Because the pallets slide down to the aisle position, a push back pallet rack is significantly faster to load and unload than a comparable drive-in rack.
In the push back system, everything can be accessed from the aisle while utilizing a Last-In First-Out (LIFO) method of storage. This system provides multiple pick faces while using fewer aisles, therefore opening up more warehouse space.
Push back pallet racking systems are great for: Warehouses that need selectivity of selective racking, but flexibility and high-density storage of drive-in pallet racking.
Inventory management: Last-In First-Out (LIFO) retrieval
Advantages of a push back pallet racking system:
- Easy product accessibility – each lane is one SKU
- High-density storage and more flexibility with multiple SKUs
- Can be custom-designed and configured for your storage applications
- Low maintenance pallet storage system
- Rack damage is minimized because the forklifts don’t enter the rack structure
Disadvantages of a push back pallet racking system:
- More expensive than a comparable drive-in pallet rack system
- Higher service costs and maintenance costs – may need to carry extra wheels, carts, or bearings for in-house service, or enter into a service agreement with a rack service provider
Pallet Flow Racking Systems
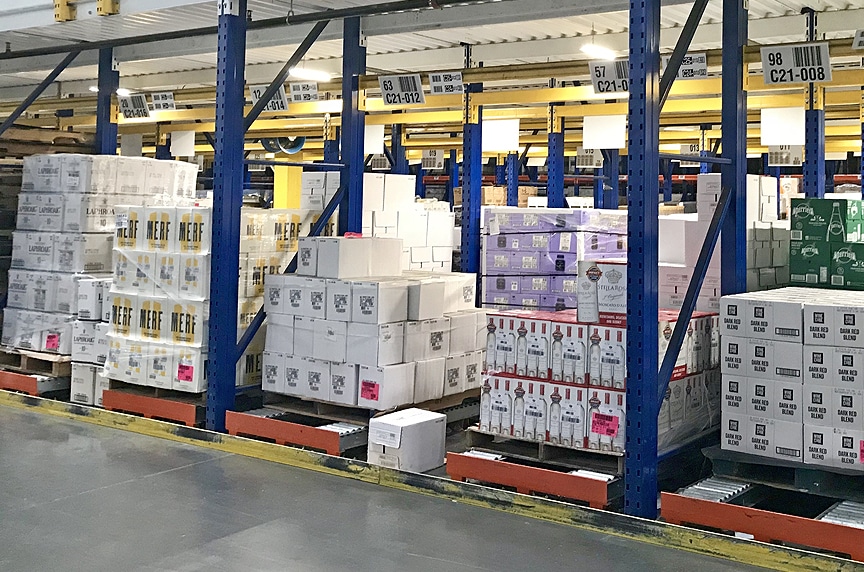
A pallet is placed on the “loading” side, then is moved to the “picking” side using gravity rollers. As each load is removed, the pallet behind it automatically moves one position closer to the picking position.
Pallet flow racks, or “gravity flow” racks are a dynamic storage system that use gravity rollers to automate pallet storage and retrieval and increase storage efficiency. Using a pallet flow storage system can double or even triple the storage capacity in your facility compared to other methods.
A pallet is placed on the “loading” side and is then moved to the “picking” side using gravity rollers. As each load is removed, the pallet behind it automatically moves forward one position closer to the picking position. This makes for an automatic stock rotation, therefore, reducing labor costs.
Thanks to the pallet flow system, companies notice that inventory turnover becomes quick and efficient. Pallet speed can be controlled by the type of rollers and brakes engineered into the system. This system is heavily utilized by companies which have expiration date-sensitive products, which is why they are heavily utilized in freezer warehouse or food distribution centers. Pallet flow systems offer accessories to fit the needs of your product and can be designed to accommodate a depth of up to 20 pallets.
Pallet flow racking systems are great for: Companies who store or distribute dairy, deli, pharmaceuticals, or other date-sensitive or perishable items.
Inventory management: First-In First-Out (FIFO) retrieval
Advantages of pallet flow racking systems:
- Once loaded, product rotation is automatic
- Dedicated lane to one product
- Great for large number of pallets – anywhere from 8-20 pallets
- Quick and efficient inventory turnover (FIFO retrieval)
Disadvantages of pallet flow racking systems:
- High capital investment
- Requires good pallet quality
- High maintenance requirements
- Limited SKU and selectivity
- Requires aisles which can eat up warehouse space
Carton Flow Racking Systems
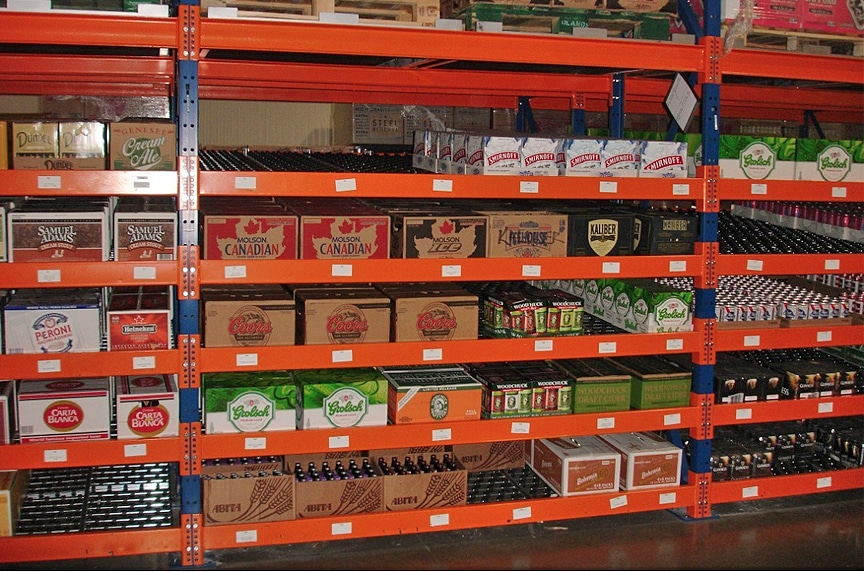
Carton flow systems can be loaded from the back and the product cartons slide down gravity-fed rollers or wheels to the front of the racking for picking and packing orders.
Essentially, carton flow racking systems are the same as pallet flow racks, but designed for boxes and small products, or split case picking. While using the First in First out (FIFO) method, carton flow rack brings a dramatic upgrade in cost-savings because it improves warehouse efficiency by organizing product and rotating stock automatically.
Typically found in warehouses with high volume order picking, these systems can be loaded from the back and the product cartons slide down gravity-fed rollers or wheels to the front of the racking system for picking and packing orders.
Since the system uses gravity as a free source of power, carton flow can save anywhere from 25% – 75% in labor costs over your standard storage solution. Carton flow rack systems are versatile and can accommodate fast-moving to slow-moving inventory, and are ideal for odd-shaped cases, cartons, bins, or merchandise.
Carton flow pallet racking systems are great for: Warehouses that utilize split-carton picking and require high-volume order picking. Common applications include order fulfillment centers, food and beverage distribution centers, small parts distributors, etc.
Inventory management: First-In First-Out (FIFO) retrieval
Advantages of using carton flow pallet racking systems:
- Save space and increase efficiency for order fulfillment
- Roller or wheel systems can be configured for dedicated product lanes, or to accommodate cartons of different sizes and configurations
- Can be either front or back loaded
- Uses gravity as free power source
- Utilizes First-In First-Out (FIFO) method
- Dramatic cost savings and increased efficiency for order fulfillment centers
- Visibility of products prevents out of stock dilemma
Disadvantages of carton flow rack systems:
- Carton flow rack systems are more expensive than traditional warehouse shelving
Cantilever Racking Systems
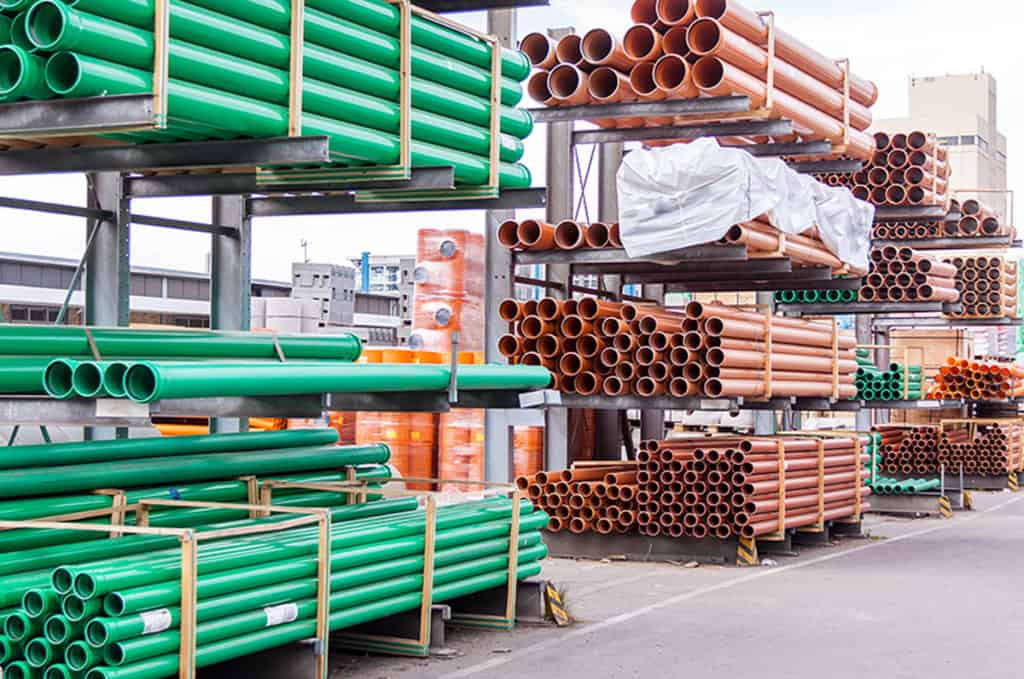
Cantilever racks are comprised of towers, arms, and bases to store long, items like tubing, pipes, bars, and lumber.
Cantilever racks are the best solution for storing longer, bulky items without an aisle upright column to limit horizontal storage space. Their design allows them to be built out of towers, arms, and bases. In most cases, these are stand-alone systems that don’t need to be tied back to the building for support. The components of the system can be roll formed or made from structural steel and can also be galvanized for use in outdoor storage yards or in tough and demanding environments.
With adjustable arms, cantilever rack systems are practical for storing even some of the most difficult items. These types of warehouse rack systems maintain a high load capacity and also offer versatility, durability, and easy installation.
Cantilever rack systems are available in roll formed or structural steel to suit different obligations such as weight, size or space. This rack system offers plenty of accessories to fit the needs of your product.
Cantilever racking systems are great for: Storing long bulky items like piping, lumber, steel sheet, and even boats. Really, anything that is long, flat, oddly-shaped, or low-profile is a great candidate for cantilever rack storage.
Advantages to cantilever racking systems:
- Capacity ranges anywhere from light duty to heavy duty
- Quicker storing and retrieving of heavy, long, or oddly-shaped products—helps reduce handling time and cost
- Strong and safe storage option—both indoors or outdoors
- Fast and easy installation
- Can be designed to meet AISI Requirements
Disadvantages of cantilever racking systems
- Higher capital investment to install and design the racking system
- May require additional flooring or foundation reinforcement prior to installation
- Requires aisle space between racks for forklifts or other material handling equipment
- Inefficient at storing pallets
Wrapping it Up
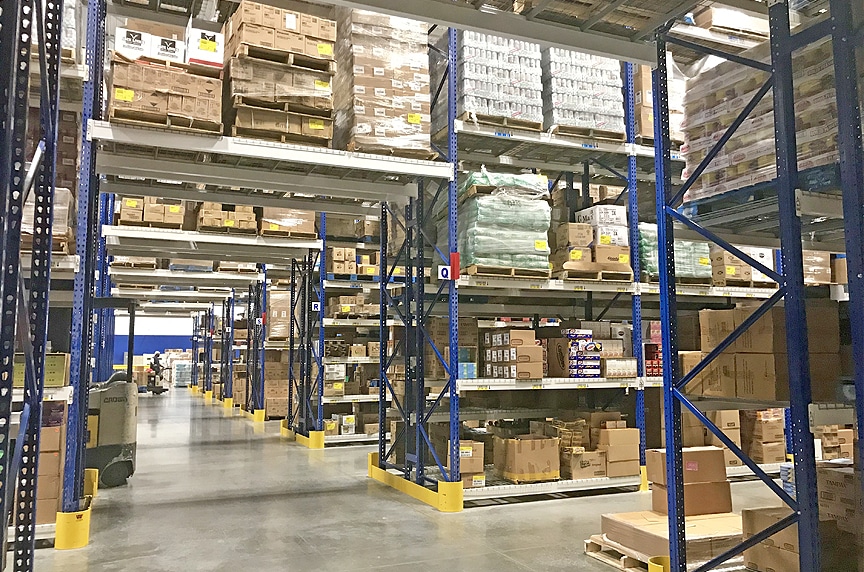
From simple selective racks to more innovative and complex storage technologies and solutions, FHS can work with you to design and install a pallet rack system for any facility or budget.
At Mazzella FHS, our Warehouse Solutions team is dedicated to helping design, plan, and execute our customer’s warehouse needs. Our talented and experienced team consists of technicians, system installers, project engineers, project managers, and a dedicated sales and support staff.
We also have our own fabrication shop where custom components and solutions are modified and, when required, fully fabricated.
If you’re interested in partnering with an innovative warehouse storage designer and manufacturer, please don’t hesitate to contact us. We offer consultation services that will help guide you through the entire warehouse operation, from start to finish.
Copyright 2018. Mazzella Companies.