ASME B30.10 Hook Inspection Criteria and Best Practices for Use
Do you know how often you should be inspecting your hooks, who should be performing those inspections, and most importantly—what you should be looking for when you inspect a hook? In this article, we'll answer all of those questions, plus provide best practices when using hooks to move or secure a load.
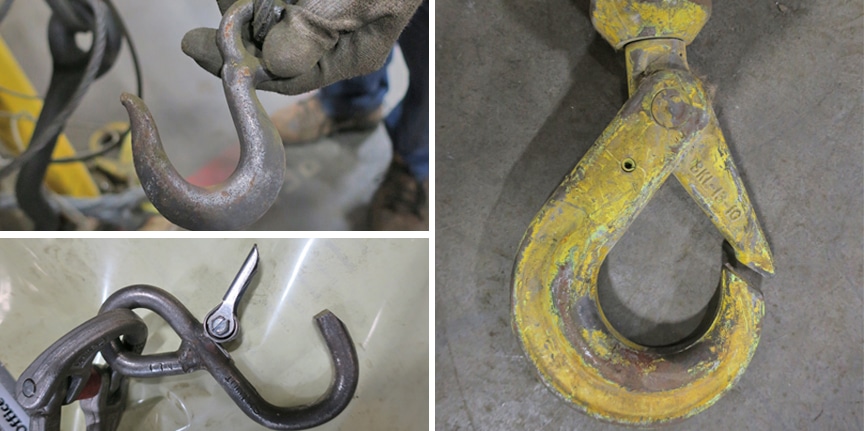
If you use a crane or hoist to lift or move material on a job site, then you know there are a lot of different items you can use to connect a load to the lifting device. Hooks can be attached to a single or multi-leg sling assembly or used for tie-down and load securement purposes. We’ve previously covered ASME B30.9 and the inspection of lifting slings, so for the purpose of this article, we’re going to discuss the ASME B30.10 hook inspection standard and what you need to know about the inspection and use of hooks.
Before we dive in, you should understand that there are two chapters in ASME B30.10 that address the different types of hooks:
ASME B30.10 Chapter 10-1
This chapter specifically refers to all hooks that support the load in the base (bowl, saddle, or pinhole) of the hook. This includes all of the following types of load-bearing hooks:
- Clevis Hook (with or without latch)
- Eye Hook (with or without latch)
- Shank Hook (with or without latch)
- Duplex Hook—also known as a “Sister Hook” (with or without latches)
- Articulated Duplex Hook (with or without latches)
- Quad Hook (with or with latches)
- Single Plate Hooks and Laminated Plate Hooks
ASME B30.10 Chapter 10-2
This chapter specifically refers to all hooks that do not support a load in a direct-pull configuration, such as:
- Grab hooks
- Foundry hooks
- Sorting hooks
- Choker hooks
Chapter 10-1 and Chapter 10-2 may have different information related to the materials and components, proof testing, fabrication and configurations, and repair and modification requirements—depending on if you’re using load-bearing hooks, or hooks that don’t support the load in a direct-pull configuration.
Our recommendation is to obtain a copy of the most recent edition of ASME B30.10 Hooks and review to make sure your hooks are being used, inspected, and maintained in accordance with industry standards.
Hook Identification Requirements
ASME B30.10 requires the manufacturer’s identification and rated load identification be forged, cast, or die stamped on a low-stress and non-wearing area of the hook.
If the hook is used in conjunction with equipment described in other B30 standards, such as on a sling assembly, or as part of a below-the-hook lifting device, the equipment manufacturer’s identification and rated load identification shall be forged, cast, or die stamped on a low-stress and non-wearing area of the hook.
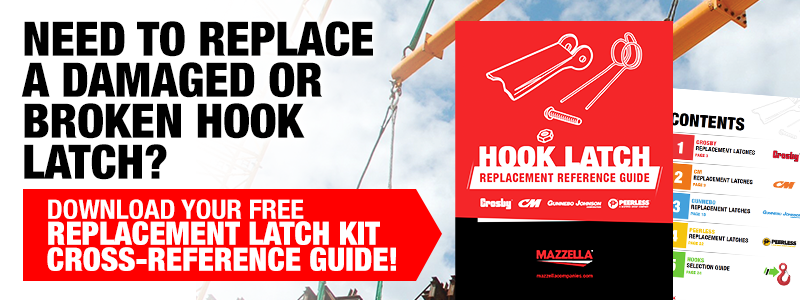
How Often Do You Need to Inspect Your Hooks?
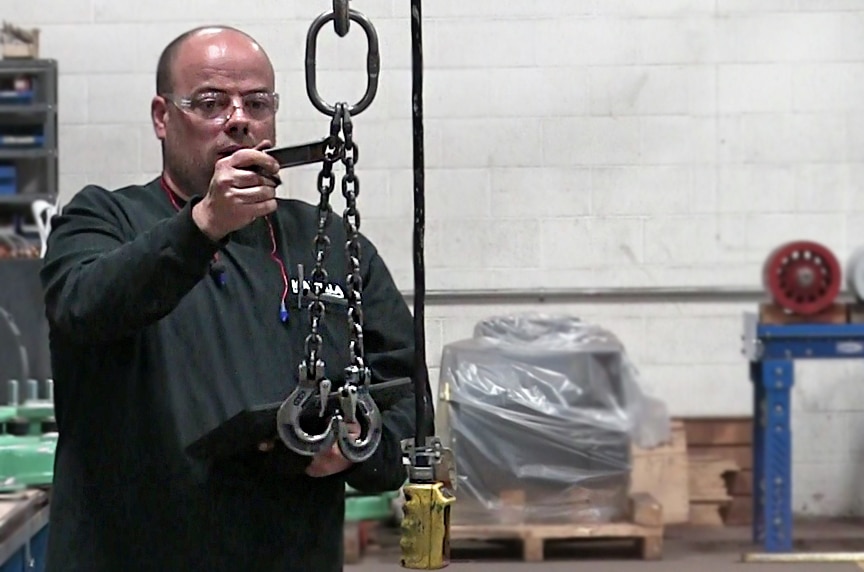
Similar to sling inspections, all ASME hook inspections shall be performed by a Designated Person with any deficiencies further examined and determination made by a Qualified Person as to whether they constitute a hazard.
For hooks in regular service, inspection procedures and record keeping requirements are governed by the kind of equipment in which they are used. If there are more stringent inspection requirements for hooks as stated in standards for specific equipment, those inspection requirements take precedence over the requirements listed below:
Initial Inspection
Prior to use, all new, altered, modified, or repaired hooks shall be inspected to verify compliance with the applicable ASME B30.10 Hooks standard. Written records of initial inspections are NOT required.
Frequent Inspection
Frequent inspections include observations of the hook being used during operation, as well as visual inspections to identify any conditions or removal criteria outlined in ASME B30.10 hook inspection guidelines.
For semi-permanent and inaccessible locations where frequent inspections are not feasible, a Qualified Person will determine the frequency of periodic inspection requirements to satisfy ASME B30.10 hook inspection requirements. Inspection intervals should be based on:
- The frequency of hook use
- Severity of service conditions
- Nature of load-handling activities
- Experience gained on the service life of hooks used in similar circumstances
Guidelines for frequent inspection intervals:
- Normal Service – Monthly
- Heavy Service – Weekly to Monthly
- Severe Service – Daily to Weekly
Conditions listed under Removal Criteria, or any other condition that may result in a hazard, shall cause the hook to be removed from service. Hooks shall not be returned to service until approved by a Qualified Person. Written records of frequent inspections are NOT required.
Periodic Inspection
A complete and thorough inspection of the hook shall be performed. Disassembly of the hook may be required to perform a complete examination and identify conditions based on the removal criteria outlined in ASME B30.10 hook inspection requirements.
Periodic inspections shall be performed at a minimum interval of 12 months, unless approved by a Qualified Person. Periodic rigging inspection intervals should be based on:
- Frequency of hook use
- Severity of service conditions
- Nature of load-handling activities
- Experience gained on the service life of hooks used in similar circumstances
Guidelines for periodic inspection intervals:
- Normal Service – Yearly with equipment in place
- Heavy Service – Semi-annually, with equipment in place unless external conditions indicate that disassembly should be done to permit detailed inspection monthly to quarterly
- Severe Service – Quarterly, as in heavy service, except that the detailed inspection may show the need for a non-destructive type of testing
Hooks shall not be returned to service until approve by a Qualified Person. Written records of periodic inspections ARE required.
ASME B30.10 Hook Inspection Criteria
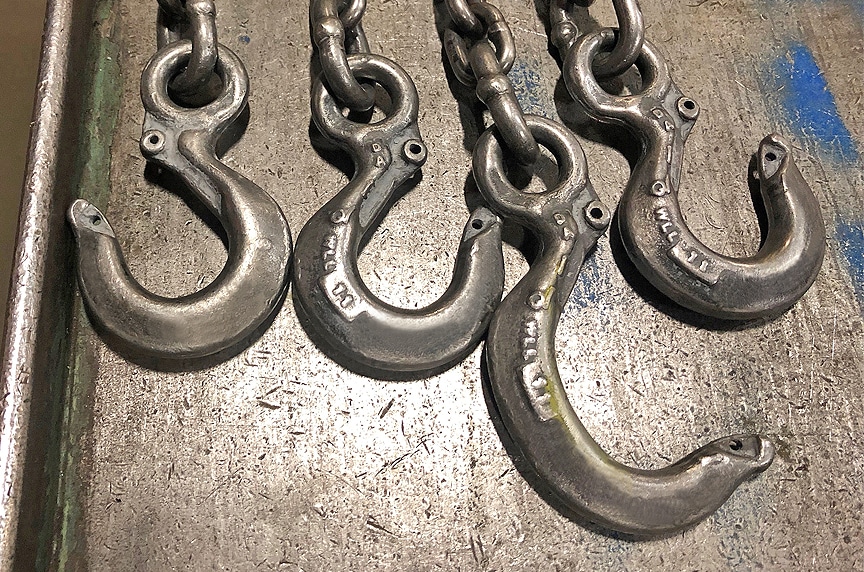
The goal of a rigging inspection is to thoroughly evaluate the condition and remaining strength of all equipment used to perform overhead lifts or used for load-handling activities.
ASME B30.10 requires hook inspection and that hooks shall be removed from service if damage or evidence of any of the following is present. A hook may not be returned to service until it has been approved by a Qualified Person.
Removal Criteria
- Missing or illegible hook manufacturer’s identification or secondary manufacturer’s identification
- Missing or illegible rated load identification
- Excessive pitting or corrosion
- Cracks, nicks, or gouges
- Wear—any wear exceeding 10% (or as recommended by the manufacturer) of the original section dimension of the hook or its load pin
- Deformation—any visible apparent bend or twist from the plane of the unbent hook
- Throat opening—any distortion causing an increase in throat opening of 5% not to exceed 1/4” (6mm), or as recommended by the manufacturer
- Inability to lock—any self-locking hook that does not lock
- Inoperative latch (if provided)—any damaged latch or malfunctioning latch that not close the hook’s throat
- Damaged, missing, or malfunctioning hook attachment and securing means
- Thread wear, damage, or corrosion
- Evidence of heat exposure or unauthorized welding
- Evidence of unauthorized alterations such as drilling, machining, grinding, or other modifications
Best Operating Practices When Using Hooks
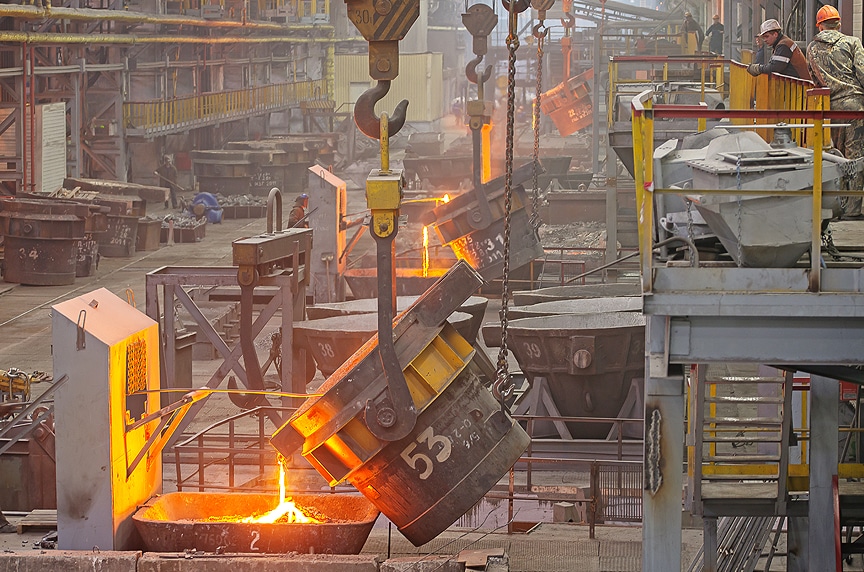
Utilize best practices when using, inspecting, and storing your hooks. Make sure all of your rigging equipment has the proper markings/identification, is in acceptable working condition and passes a visual inspection, and is stored in an area where it’s not susceptible to extreme temperatures, excess moisture, chemical exposure, or mechanical damage.
Operators or riggers using hooks shall be aware of the following:
Extreme Temperatures
Consult with the manufacturer or a Qualified Person if you are planning to use a hook in an environment where temperatures exceed 400°F (204°C) or –40°F (–40°C).
Chemically Active Environments
The strength of hooks can be affected by chemically active environments, such as caustic or acid substances or fumes. The hook manufacturer or a Qualified Person should be consulted before hooks are used in chemically active environments.
Use of Latches on Hooks
We advise that the end user must evaluate the work activity with regards to the safety of their employees. If the activity makes the use of the latch impractical, unnecessary, or more dangerous, then the end user may choose to eliminate the latch. It is also recommended that each lifting activity is considered independently as far as the use of a hook latch is concerned.
While not the official position of ASME, Mazzella Companies as an organization, recommends that hook latches should be used.
When we train our employees and inspectors on the use of hook latches, we take all of the following into consideration:
- Any hook that is designed to have a latch, should have the latch installed
- New slings are sold with the latch installed unless the customer requests no latch
- If customers make an inquiry about the use of a latch on a hook, we may recommend for them to consider several OSHA standard interpretations, among them the following:
Best Practices for Using Single-Point Hooks
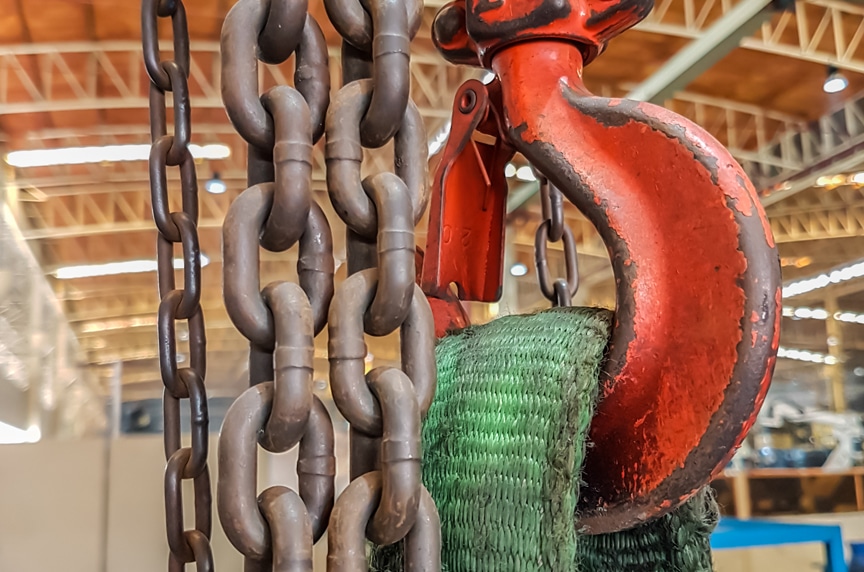
- It shall be determined that the load to be applied does not exceed the lesser of the load rating of the hook or the load rating of the equipment of which the hook is a part.
- Shock loading should be avoided.
- The load shall be centered in the base (bowl/saddle) of the hook to prevent point loading of the hook.
- When multi-leg slings are placed in the base (bowl/saddle) of the hook, the maximum included angle between sling legs shall be 90° or as determined by the hook manufacturer. The maximum sling leg angle with respect to the hook centerline for any rigging arrangement shall be 45°.
- A collector ring, such as a link or shackle, should be used when more than two legs are placed in a hook or for angles greater than 45° with respect to the hook centerline.
- Hooks shall not be used in such a manner as to place a side load, back load, or tip load on the hook.
- When using a device to close the throat opening of the hook, care shall be taken that the load is not carried by the closing device.
- Hands, fingers, and body shall be kept from between hook and the load. Consider using no-touch hand tools.
- The use of a hook with a latch does not preclude the inadvertent detachment of a slack sling or a load from the hook. Hook latches aid in the retention of loose slings under slack rigging conditions only and are not intended to be anti-fouling devices during load handling or rigging. Visual verification of proper hook engagement is required in all cases.
- Self-locking hooks shall be locked during use.
- When a latch is equipped with a lock open device to facilitate rigging, the latch shall be closed during operation.
- When a hook is equipped with a latch, the load shall not restrict the closure of the latch.
- The need for a latch or mousing on any hook is a function of the application of the hook and shall be determined by a Qualified Person.
Best Practices for Using Duplex and Quad Hooks
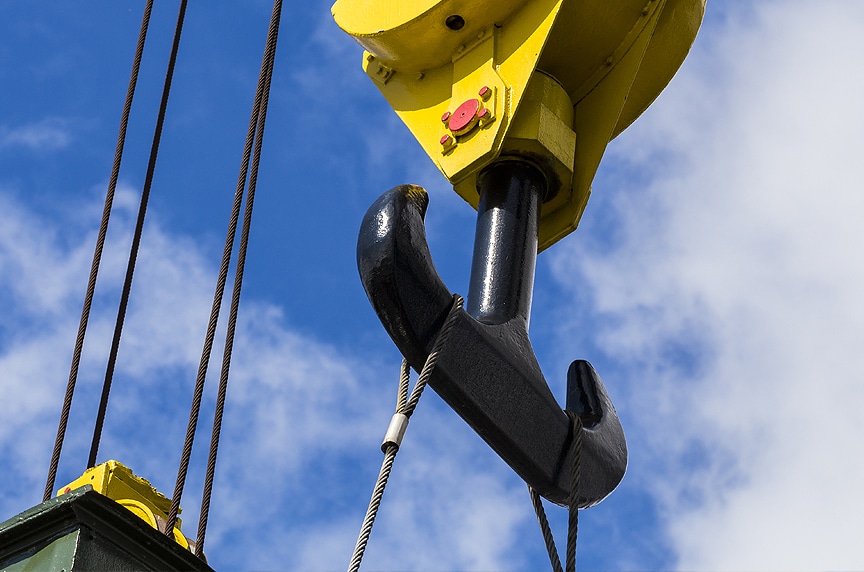
- For determining allowable sing angles for duplex (sister) and quad hooks, consult the manufacturer or a Qualified Person.
- Duplex (sister) hooks shall be loaded equally on both sides unless the hook is specifically designed for single-point loading. When using an articulated duplex (sister) hook, care should be taken because articulation of the hook may cause instability in the slung load.
- If the duplex (sister) hook is loaded at the pinhole of at the two saddles, the load applied shall not exceed the rated load that would normally be shared by the two saddles or the rated load of the supporting equipment.
- Quad hook load handling shall be done with all prongs loaded and rigged to balance prong forces. The hook manufacturer or Qualified Person shall be consulted for two-prong and unbalanced-prong loading.
- Hooks shall not be used in such a manner as to place a side load, back load, or tip load on the hook.
- When using a device to close the throat opening of the hook, care shall be taken that the load is not carried by the closing device.
- Hands, fingers, and body shall be kept from between the hook and load. Consider using no-touch hand tools.
- The use of a hook with a latch does not preclude the inadvertent detachment of a slack sling or a load from the hook. Hook latches aid in the retention of loose slings under slack rigging conditions only and are not intended to be anti-fouling devices during load handling or rigging. Visual verification of proper hook engagement is required in all cases.
- When a latch is equipped with a lock open device to facilitate rigging, the latch shall be closed during operation.
- When a hook is equipped with a latch, the load shall not restrict the closure of the latch.
- The need for a latch or mousing on any hook is a function of the application of the hook and shall be determined by a Qualified Person.
Best Practices for Using Miscellaneous Hooks (Grab Hooks, Foundry Hooks, Sorting Hooks, Choker Hooks)
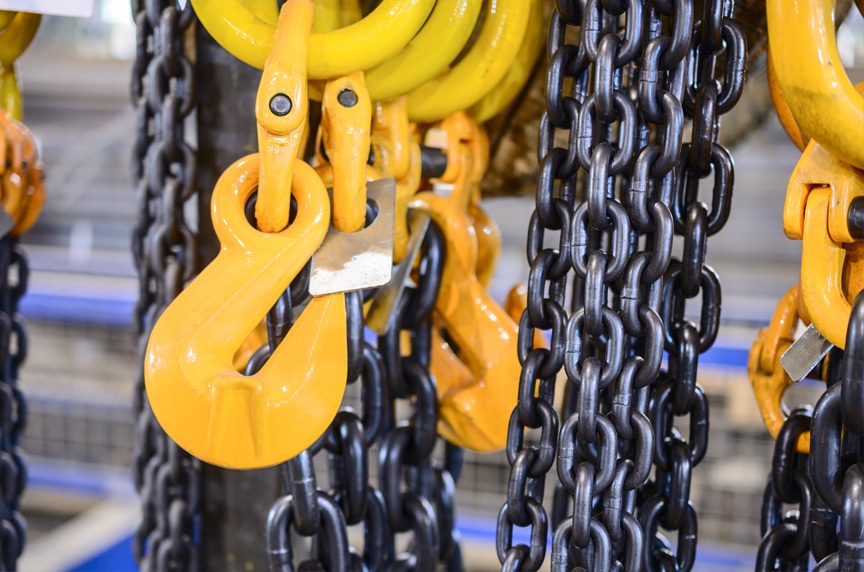
- It shall be determined that the load to be applied does not exceed the rated load of the hook’s assembly, especially when the special conditions, such as choking or grabbing, are considered.
- Shock loading should be avoided.
- A hook shall not be used in a manner other than that for which it is intended.
- Hands, fingers, and body shall be kept away from between the load and the hook. Consider using no-touch hand tools.
- When using a device to close the throat opening of the hook, care shall be taken that the load is not carried by the closing device.
- The use of a hook with a latch does not preclude the inadvertent detachment of a slack sling or a load from the hook. Hook latches aid in the retention of loose slings under slack rigging conditions only and are not intended to be anti-fouling devices during load handling or rigging. Visual verification of proper hook engagement is required in all cases.
- When a latch is equipped with a lock open device, the latch shall be closed during operation.
- When a hook is equipped with a latch, the load shall not restrict the closure of the latch.
- The need for a latch or mousing on any hook is a function of the application of the hook and shall be determined by a Qualified Person.
Wrapping it Up
Investing in the training of your employees and putting together a lifting and rigging compliance program are two of the best ways you can protect your workers and prolong the service life of your equipment.
Professional rigging training provides your team with the knowledge needed to inspect their rigging equipment before each shift / each lift and identify damage and irregularities that may require an item to come out of service.
If you’re not confident in your knowledge of the applicable OSHA and ASME standards, or just don’t have the resources to put a lifting and rigging compliance program into place, you should consider a third-party inspection provider.
At Mazzella, we have a dedicated team of Rigging Inspectors that are independently trained and certified and inspect to all applicable OSHA and ASME standards. Their only responsibility is to come on-site and perform a thorough inspection of your rigging gear, address solutions as required, and complete the service in a timely manner.
Our inspectors can help you identify compliance issues and identify opportunities for improvement based on their thorough understanding of all applicable OSHA and ASME standards.
If you have questions about rigging inspections, or want to hire a third-party to satisfy OSHA/ASME periodic inspection requirements, please contact us to schedule a consultation. We can partner with you to ensure the peace of mind that safety compliance brings.
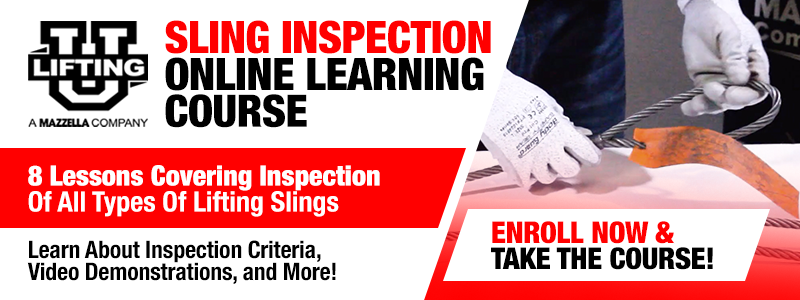
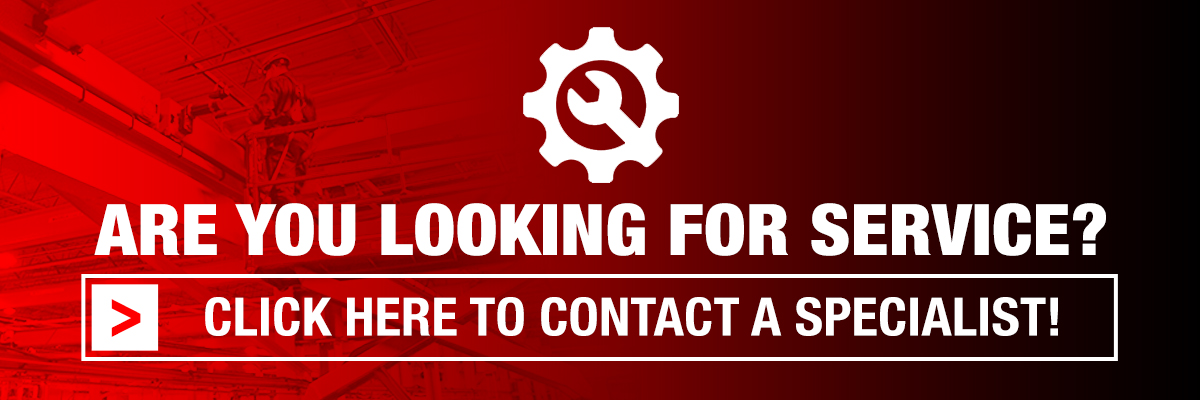
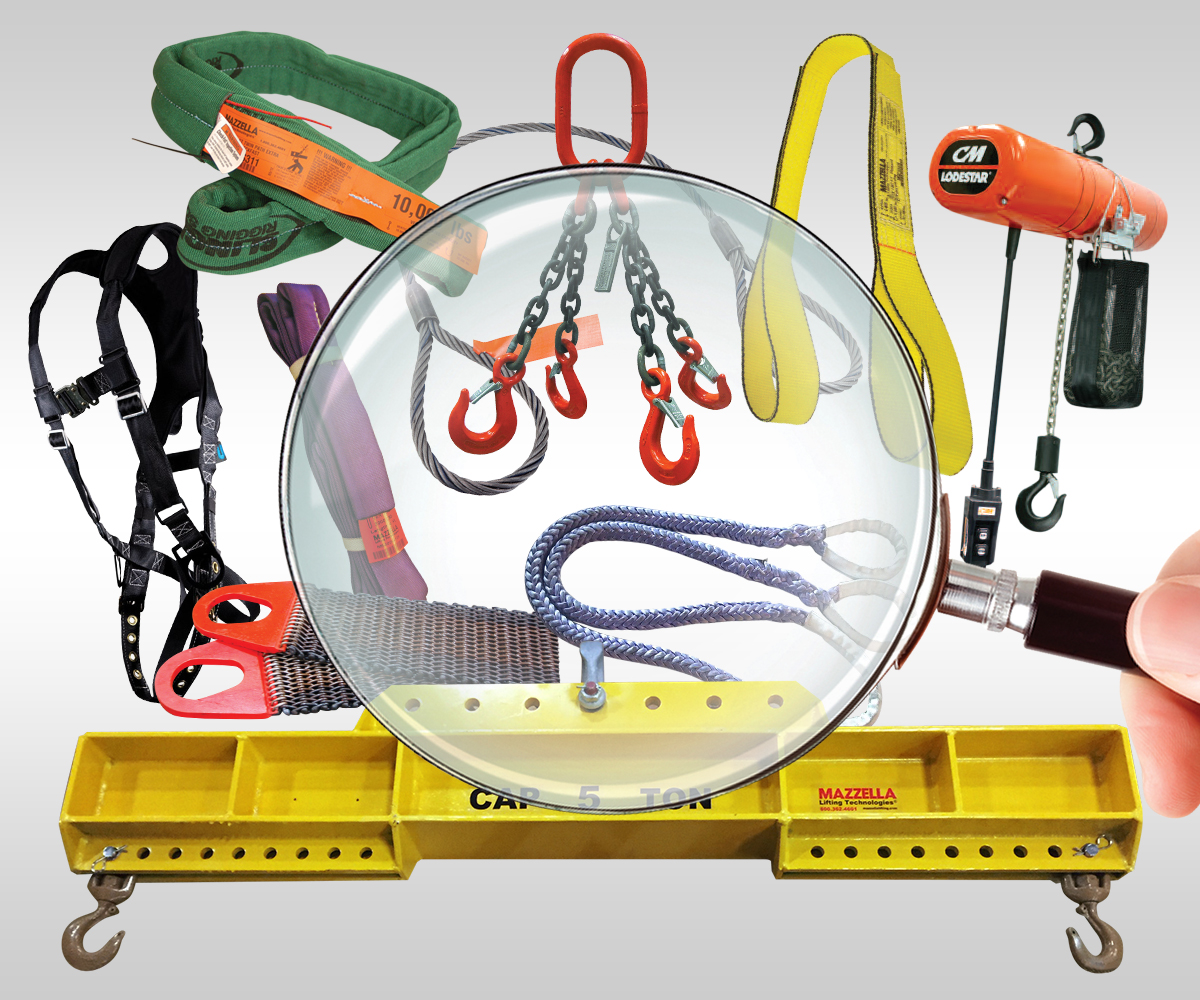
Rigging Inspection Services
OSHA 1910.184, ASME B30.9, B30.20, B30.26, & ANSI Z359 require periodic, documented inspections on slings, rigging hardware, lifting devices, and fall protection every 12 months, at minimum, and monthly to quarterly in more severe service conditions.
Call us at 800.362.4601 or click here if you need inspections for slings, rigging hardware, lifting devices, or fall protection!
Copyright 2019. Mazzella Companies.