Crane Inspections and OSHA Compliance
<p>Keeping your overhead crane in service and in peak operating condition, should be a top priority for safety, maintenance, or operations personnel at any job site or industrial facility. Frequent and periodic inspections help to keep crane and hoist equipment operating at top efficiency, help keep the user and other personnel safe, help reduce costly down time, and extend the life of the equipment.</p>
Keeping your overhead crane in service and in peak operating condition, should be a top priority for safety, maintenance, or operations personnel at any job site or industrial facility. Frequent and periodic inspections help to keep crane and hoist equipment operating at top efficiency, help keep the user and other personnel safe, help reduce costly down time, and extend the life of the equipment.
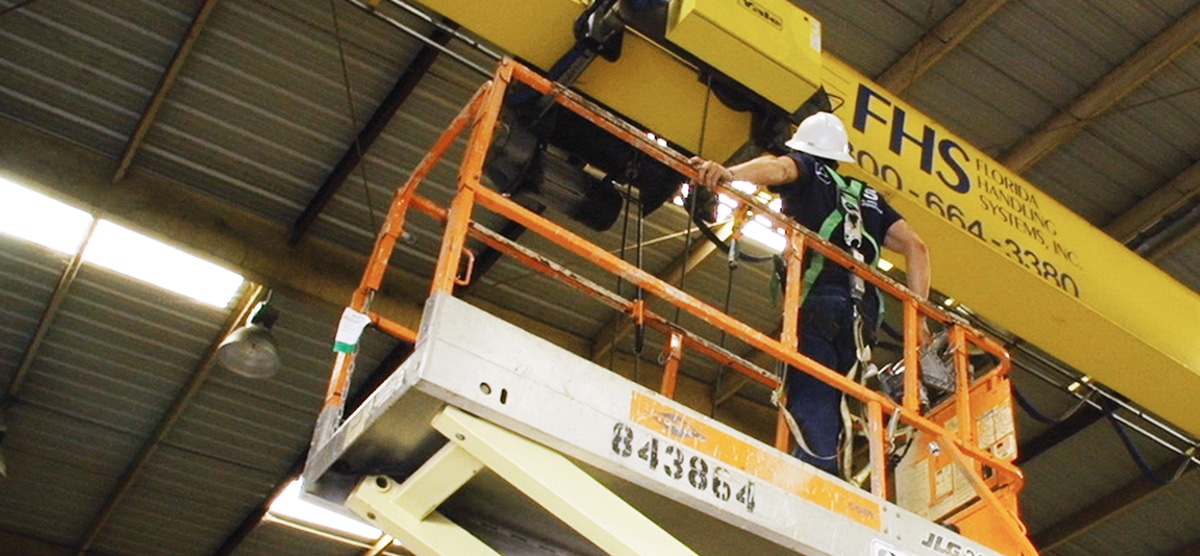
OSHA (Occupational Safety and Health Administration), ASME (The American Society of Mechanical Engineers) and CMAA (Crane Manufacturers Association of America) are the three governing bodies that have developed documented standards and best practices for inspection and preventative maintenance of overhead cranes.
If you are a Plant Manager or Operations Manager in charge of inspecting and maintaining your company’s overhead crane equipment, you will want to familiarize yourself with the following standards:
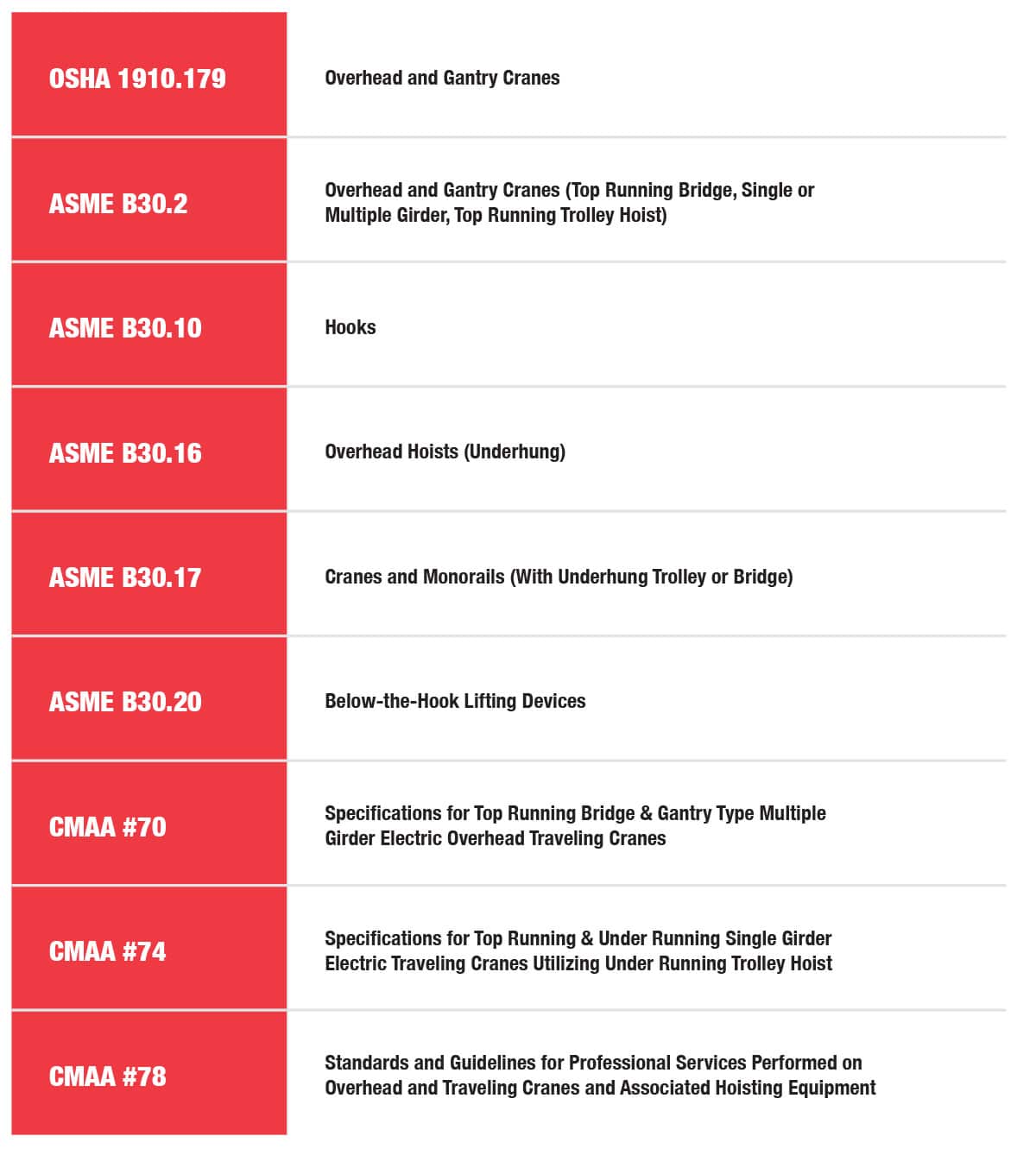
Our goal for this article is to break down and summarize these inspection standards and help you understand how you can become OSHA compliant in regards to overhead crane inspection, preventative maintenance, crane repair, and user training.
Overhead Crane Inspection Frequencies
Many maintenance supervisors and plant managers mistakenly think that they are in compliance with inspection standards if they have their crane equipment inspected once a year. This misconception can be costly and lead to fines and downtime if OSHA were to come on-site and issue citations after performing an audit. OSHA’s overhead crane inspection standards, as well as the ASME and CMAA standards, require three different types of inspections throughout the lifetime of the crane equipment:
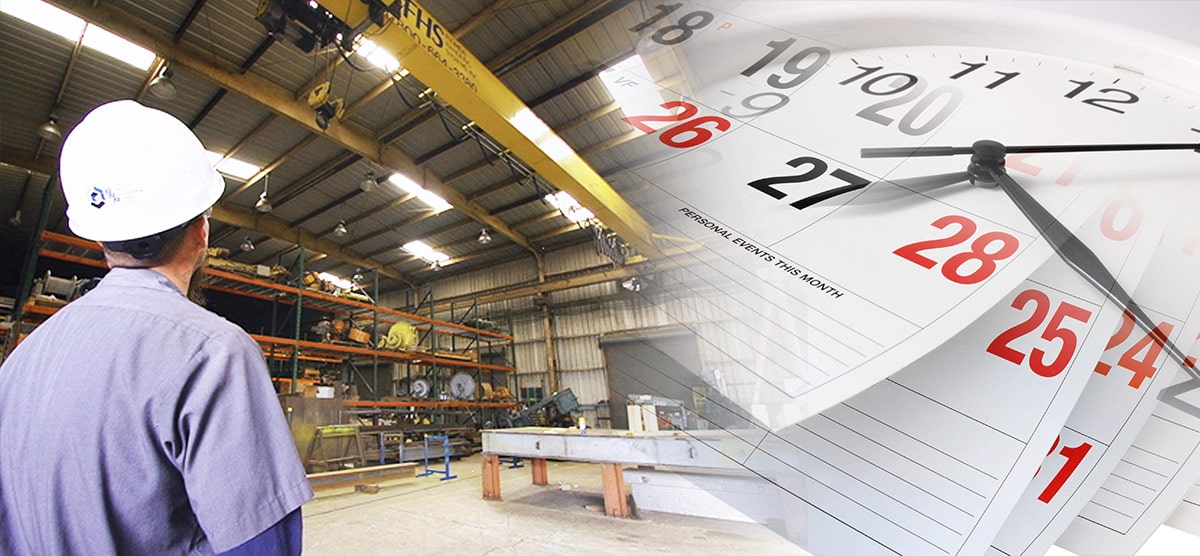
Initial Inspection
Any new, reinstalled, altered, repaired, and modified crane shall be inspected prior to initial use.
- A new crane’s initial inspection shall be performed by a qualified OEM representative in accordance with OEM recommendations
- An altered, repaired, modified or reinstalled crane’s initial inspection shall be performed by a qualified person to assure that the modified component(s) have been properly installed and functionally tested
Frequent Inspection
A frequent inspection is a visual and operational inspection performed monthly or as often as daily. Inspection frequency is based on service, environmental, and application factors, as designated by a qualified person.
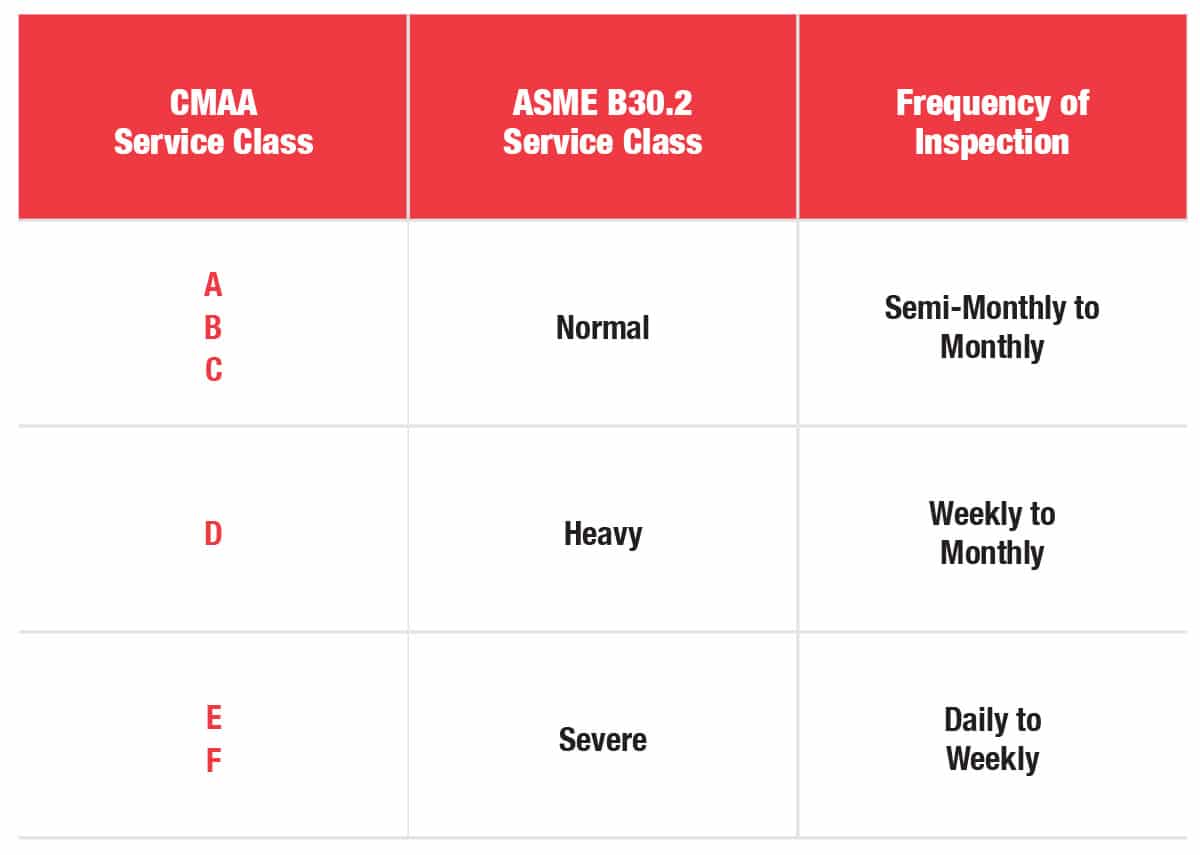
Periodic Inspection
A periodic inspection is a detailed visual and operational inspection where individual components are examined to determine their condition. Inspection frequency can be quarterly to annually and is based on service, environmental, and application factors, as designated by a qualified person.
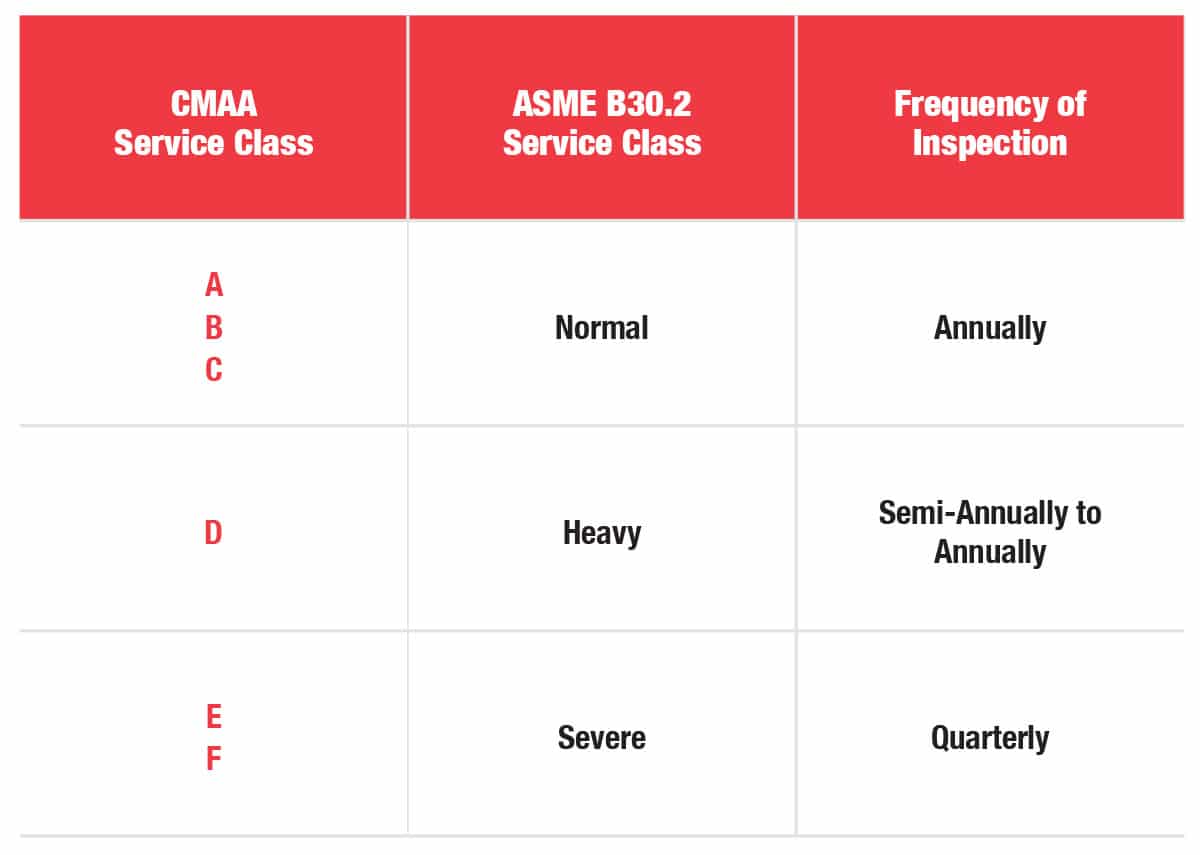
Manufacturers’ Recommendations
In addition to the types of inspections listed above, any inspection provisions found in the manuals supplied by the manufacturer(s) of the crane and the crane components shall also be followed.
Inspection Items for Overhead Cranes in Regular Service
The inspection procedure for cranes in regular service (operating at least one time per month) is divided into two general classifications based upon the intervals at which inspection occurs. The intervals are dependent upon the nature of the critical components of the crane and the degree of their exposure to wear, deterioration, or malfunction. The two general classifications we’ll be focusing on are the criteria for Frequent and Periodic inspections.
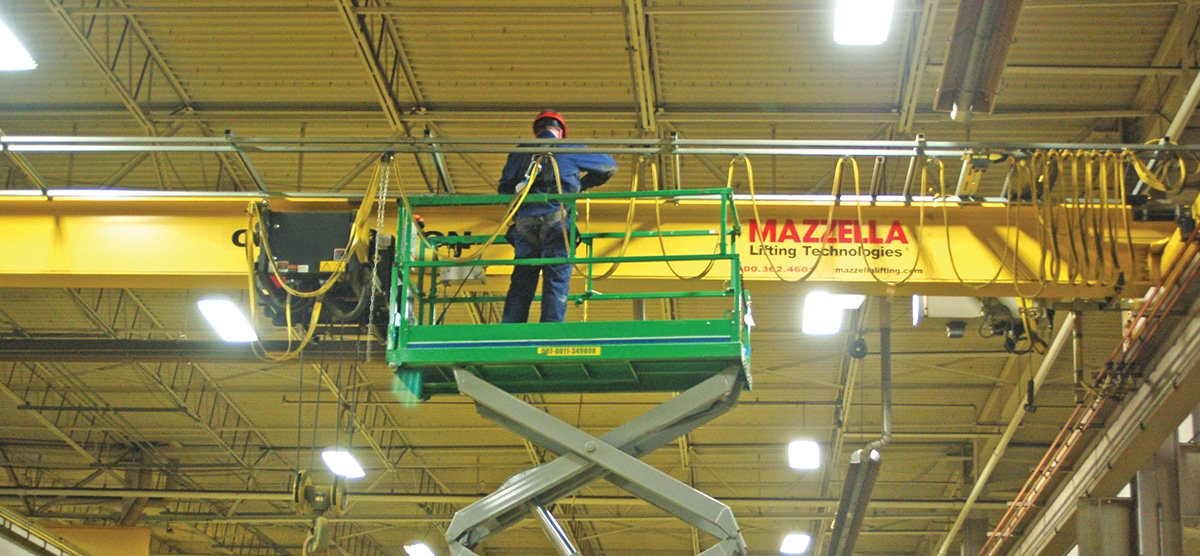
Frequent Inspection Items
Per CMAA Specification #78, when performing a frequent inspection, a qualified person shall include, but not limit themselves to, inspection of the following items:
- Check that the crane or hoist is not tagged with an out-of-service sign
- Check that all motions agree with control device markings
- Check that all braking motions do not have excessive drift and that stopping distance is normal
- *Check hook for damage, cracks, nicks, gouges, deformation of the throat opening, wear on saddle or load bearing point, and twist
- Check that the hook latch, if provided, is not missing and operates properly
- *Check wire rope for broken wires, broken strands, kinks, any deformation or damage to the rope structure, or loss of lubricant
- *Check load chain, including end connections for excessive wear, twist, distorted links or stretch, beyond the manufacturer’s recommendations
- Check that the wire rope or load chain is properly reeved and that rope or load chain parts are not twisted. Make sure wire rope is properly seated in drum grooves
- Check that the hoist upper/lower limit devices stop lifting or lowering motion of the hoist load block before striking any part of the hoist, crane, or floor
- Check bridge and trolley travel limits for proper function
- Check for any sign of oil leakage on the crane and on the floor beneath the crane
- Check for any unusual sounds from the crane or hoist mechanism while operating crane and hoist
- Check that warning and other safety labels are present and legible. Check that audible and visual warning devices are operational
Items marked with (*) shall be documented with a certification record which includes the date of inspection, signature of the person who performed the inspection, and the serial number or identifier of the hook, chain, or wire rope that was inspected.
Periodic Inspection Items
Per CMAA Specification #78, if any of the following deficiencies are observed, they shall be carefully examined and determined whether they constitute a safety hazard:
- Check that structural members are not deformed, cracked, or corroded. Foot walks are free from debris, grease, etc.
- Check that the operating cab has the proper fire extinguisher in place.
- Check for proper capacity labels, and that they are legible from the floor. Are warning signs in place and legible?
- Check connection points for loose/broken bolts or rivets.
- Check sheaves and drums for worn, cracked, bent, or broken parts. Check for loose or missing hardware.
- Check brake system parts, linings, pawls, and ratchets for excessive wear and proper adjustment. Check to make sure electric control brake functions properly.
- Check indicators, gauges, or other devices for calibration and load, wind, and other indicators over their range.
- Check self-contained electric, hydraulic, or gasoline powered generating units for improper performance or noncompliance with applicable safety requirements.
- Check transmission for excess wear of chain drive sprockets and excessive chain stretch. Check gearbox for gear teeth wear and proper lubrication.
- Check all electrical apparatus for signs of pitting or any deterioration of controller contactors, limit switches, push button stations, motor slip rings, brushes and resistors. Check for loose or damaged wiring, or evidence of overheating.
- Check all bumpers and end stops for damage. Check for proper restraints and obvious under sizing or improper energy absorption capabilities.
- Check trolley and runway rails and fastening devices for looseness, gaps, misalignment, and wear.
- Check runway structure for proper anchors, loose bolted connections, corrosion, and cracked or deformed members.
- Check the conductor system alignment, fastening, splices, power feeds, and conductor shoes for wear.
- Check below-the-hook devices for cracks or structural damage. Check mechanical components for wear, alignment, and missing or loose hardware. Check all motors, pendant or remote radio controls, and wiring. Check that all guards are in place and secure.
NOTE: A qualified person shall determine whether conditions found during the inspection constitute a hazard and whether a more detailed inspection is required. Any unsafe conditions uncovered during inspection shall be corrected before operation of the crane is resumed. Adjustments and repairs shall be done only by designated personnel.
Inspection Of Cranes Not In Regular Use
If you have an overhead crane that has been idle for a length of time due to shutdown or storage, or you have a standby crane with infrequent or irregular usage, the crane needs to be inspected before it is put back into service. OSHA has determined that cranes that have sat idle for the following lengths of time shall be inspected prior to use:
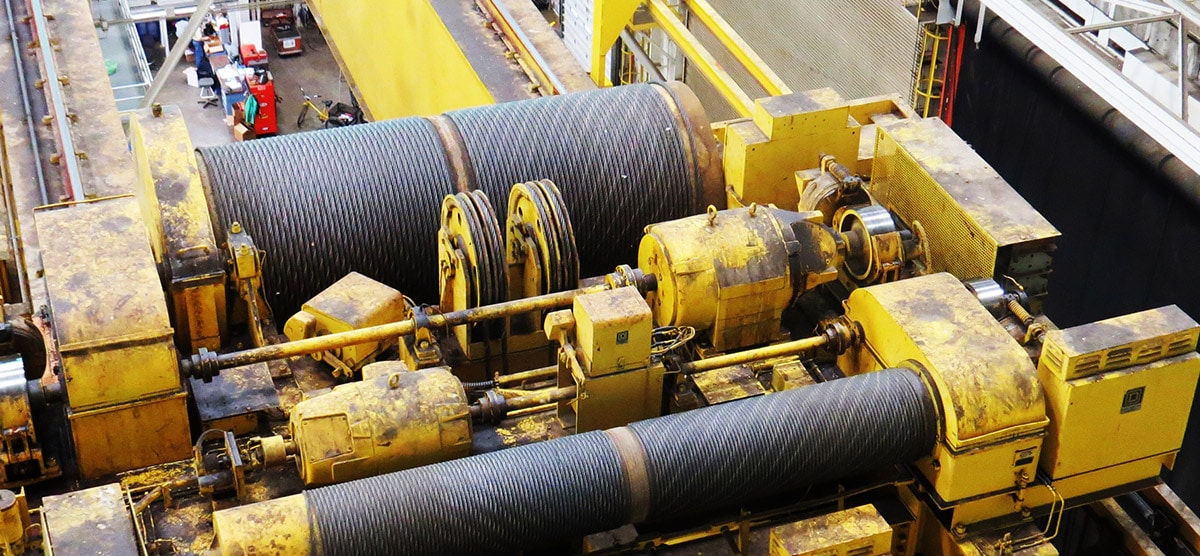
- A crane that has been idle for at least 1 month, but less than 6 months, shall be inspected conforming to the Frequent Inspection requirements.
- A crane that has been idle for 6 months or more, shall be given a complete inspection conforming to the Frequent Inspection and Periodic Inspection requirements.
- A standby crane—meaning a crane which is not in regular service but which is used occasionally or intermittently—shall be inspected at least semi-annually in accordance with the criteria required for Frequent Inspection, as well as the criteria for Idle Wire Rope Inspection (see below).
Idle Wire Rope Inspection
All wire rope which has been idle for a period of 1 month or more due to shutdown or storage of a crane on which it is installed, shall be given a thorough inspection before it is used. A certification record including the date of the inspection, the signature of the person who performed the inspection, and an identifier for the wire ropes which were inspected, shall be kept on file.
When inspecting wire rope that has sat idle for one month or more, look for the following signs of damage or deterioration:
- Reduction of rope diameter below nominal diameter—this could be a result of loss of core support, internal or external corrosion, or wear of outside wires
- A number of broken outside wires and the degree of distribution or concentration of such broken wires
- Worn outside wires
- Corroded or broken wires at end connections
- Severe kinking, crushing, cutting, or unstranding
After the wire rope has been inspected, you will determine if any observed deterioration, defects, or damages to the wire rope will result in a safety hazard with continued use. If the wire rope is deemed a safety hazard, it needs to be removed from service, quarantined, and be replaced.
NOTE: A qualified person shall determine whether conditions found during the inspection constitute a hazard and whether a more detailed inspection is required. Any unsafe conditions uncovered during inspection shall be corrected before operation of the crane is resumed. Adjustments and repairs shall be done only by designated personnel.
Performing Maintenance on an Overhead Crane
Plant managers and maintenance personnel need to establish a preventative maintenance program for their overhead crane based on the recommendations of the crane manufacturer. Each manufacturer has their own recommended protocol for regular and scheduled maintenance of their equipment, so it is important to consult with them directly regarding any questions or issues regarding crane operation, application, and maintenance protocols.
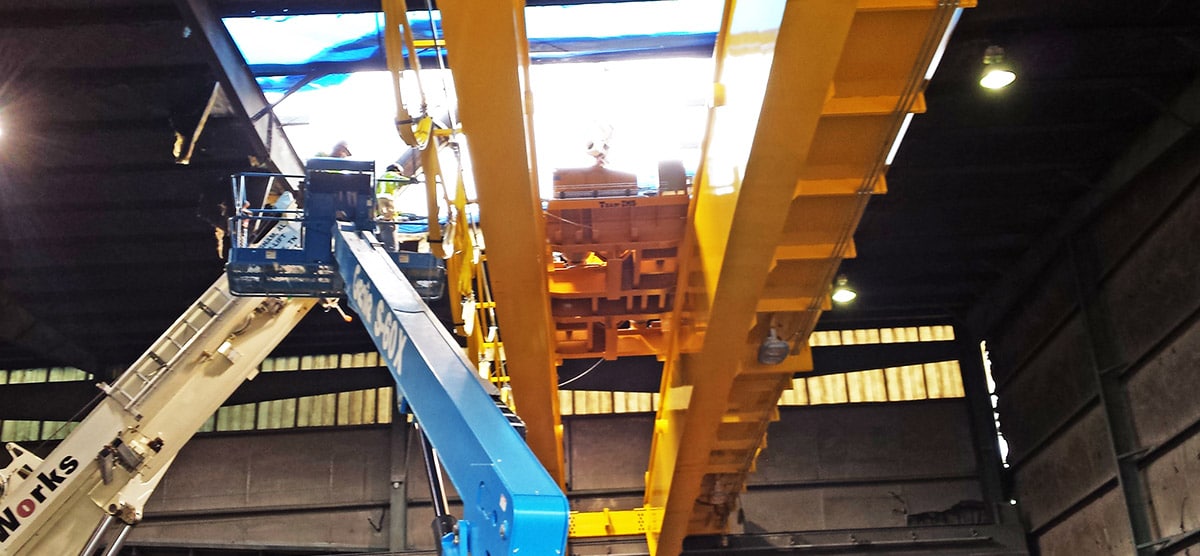
OSHA 1910.179 states that before adjustments and repairs are started on a crane, the following precautions shall occur:
- The crane that is being repaired shall be run to a location where it will cause the least interference with other cranes and operations in the area
- All controllers shall be at the OFF position
- Warning or “Out of Order” signage shall be placed on the crane, and also on the floor beneath the crane, or on the hook where visible from the floor
- Where other cranes are in operation on the same runway, rail stops or other suitable means shall be provided to prevent interference with the idle crane
- After adjustments and repairs have been made, the crane shall not be operated until all guards have been reinstalled, safety devices have been reactivated, and maintenance equipment has been removed
Training for Crane Operators and Maintenance Technicians
According to ASME B30.2 standards, it is the responsibility of management (owners/users) to provide training to those who will be operating the crane, as well as those who perform maintenance or repairs on a crane.
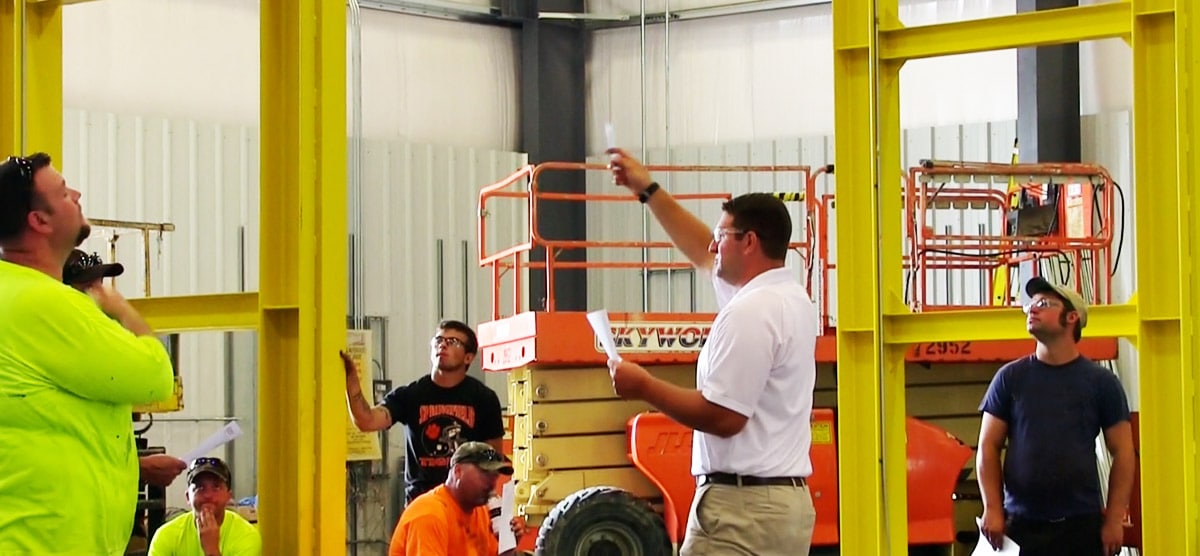
Operator Training — Crane operator training shall be provided to promote proficient performance of a crane operator in accordance with best practices.
Maintenance Training — Maintenance training shall be provided to promote proficient adjustments, repairs, and replacements to an overhead crane that will allow the crane to perform. Training shall also be provided to persons who maintain the mechanical, structural, and electrical components of an overhead crane system.
A certificate or formal record of training will be issued to any person who has been trained and passed the examination requirement.
Following the documented OSHA standards and best practices for overhead crane inspection and preventative maintenance will help keep crane and hoist equipment operating at top efficiency, keep your employees safe, reduce costly down time, and extend the life of the equipment.