Hidden Costs of Overhead Crane Ownership
<p>In this section, we’ll help you identify some of the pitfalls and hidden costs associated with overhead crane ownership. Our goal is to help you better understand how to properly budget for and design an overhead crane so the installation and future maintenance is as painless as possible.</p>
It’s easy to overlook some of the hidden costs of buying an overhead crane and maintaining an overhead crane over the course of its service life.
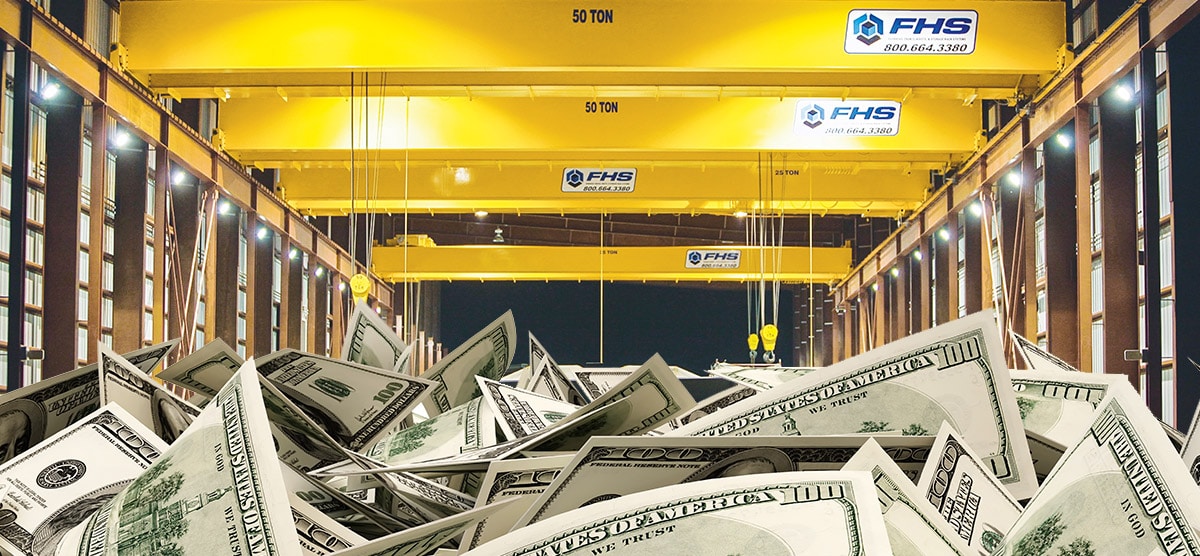
In this section, we’ll help you identify some of the pitfalls and hidden costs associated with overhead crane ownership. Our goal is to help you better understand how to properly budget for and design an overhead crane so the installation and future maintenance is as painless as possible.
The Overhead Crane Design and Quotation Process
The most important thing you can do when purchasing an overhead crane is to partner with a reliable overhead crane manufacturer. You want a partner who understands your unique lifting and material handling challenges and will help design and build a crane system specific for your application.

By having multiple manufacturers bid on your project, you’ll get a better sense of the true cost of buying an overhead crane. Also, if a company knows that they aren’t the only ones bidding on the project, they will tend to provide a more comprehensive and competitive estimate and may be more willing to negotiate on the final purchase price to get your business.
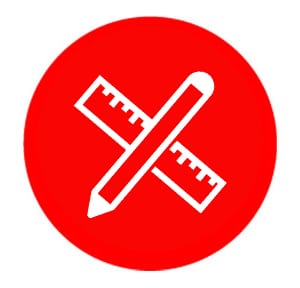
Duty Cycle and Design
Duty cycle and CMAA crane service classifications allow you to select and build an overhead crane that is the most economical and safest design for your lifting application. Selecting the right duty cycle or service classification of an overhead crane helps ensure that the components of the overhead crane are durable enough to withstand the load and usage requirements.
When partnering with a manufacturer, be open and honest with them about the following:
- How often you will be using an overhead crane
- How hard your overhead crane will have to work
- The type of environment that your crane will be operating in
This information will give the manufacturer a good sense of what type of crane class will be best for your business or facility and what type of crane will be the most economical design for your application.
When designing an overhead crane, you’ll also want to give special consideration to any future usage requirements. If you think that your production may expand down the road (which may result in higher capacity lifts or an increase in the number of lifts per day) then you may want to spec out the crane and components so it can accommodate future growth.
If you over-specify a crane, it will result in a higher initial cost for the crane and runway system, but will have less maintenance and down time in the long run.
However, if you under-specify an overhead crane system, it will result in a lower initial investment, but will cost you more in maintenance and downtime in the long run.
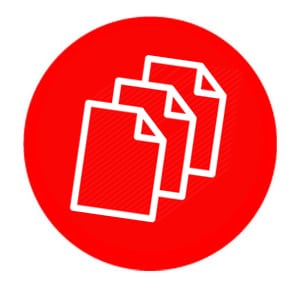
Comparing Quotes
When reviewing and comparing overhead crane quotes, it’s essential to make sure you fully understand the specifications and full details of the quote. Every project is different and not all cranes of equal capacity are the same. Sit down with each manufacturer and review the specifications of the crane system that they’re proposing. This gives each manufacturer a chance to explain their design, why they chose the materials they did, and why they’re specifying the individual components. This will give you a more comprehensive understanding of the cost and capabilities of the crane system, as a whole.
Also, understand that you should never select a manufacturer based solely on price. An overhead crane is a complicated piece of equipment and no two cranes are built exactly alike. Unfortunately, some in the industry view a crane system as nothing more than a commodity and will base their purchase on the lowest-priced option. This mindset can lead to a crane that isn’t properly specified for the application and may be comprised of low quality components that will break down frequently and not hold up to the rigors of the lifts being performed.
Remember, if you purchase solely on the lowest cost option, it’s likely going to cost you more in maintenance and downtime in the long run.
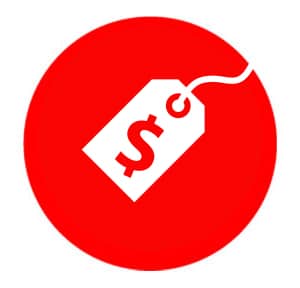
Material Costs
Right now, the U.S. steel market is volatile and unstable. Steel prices have been rising steadily due to the recently announced tariffs on imported steel. Be aware, there may be a disclaimer in your quote stating that the estimated material costs are only valid for a certain time frame or can change at any time.
From initial consultation to installation, the process of buying an overhead crane can take a long time. By the time you’re ready to purchase, it’s possible that the original estimated cost of the steel may have gone up 3-5% or even more! Fortunately, the price of steel is published and publicly available, so you can check to make sure what you’re being quoted is accurate and up-to-date.
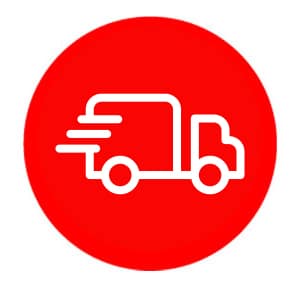
Freight Costs, Permits, and Inspections
When you look at your quotes, are the manufacturers providing you with one single price for a turnkey project—including equipment, freight, and installation? Or, are they providing itemized prices for each of those services? You’ll want to make sure you’re clear on the total costs for the project—including FOB shipping, and at what point you, as the buyer, are responsible for freight and additional installation expenses.
Do you know who is responsible for obtaining and paying for permits? You’ll need to know whether the manufacturer or installer will handle the paperwork to obtain permits, and who is responsible for paying any associated fees and arranging for surveys prior to the work, and inspections once the work is complete.
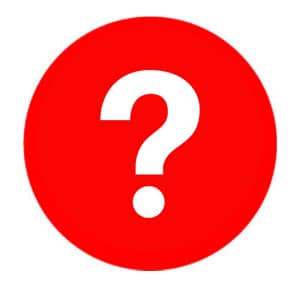
Other Common Misunderstandings
Other common misunderstandings between a customer and an overhead crane installer may include in-house electrical work prior to the installation and load testing of the overhead crane equipment once it’s been installed.
In regards to electrical work, make sure that you and the installers are clear on who will run the electrification from the disconnect to the runway to tie into the crane’s electrification. Often times, this is done by a third-party or by an in-house electrification. As long as everyone is clear on who will be doing it, it shouldn’t be an issue.
Per OSHA 1910.179 Overhead & Gantry Cranes Regulations, your new crane system will need to have two operational tests, plus a rated load test performed prior to initial use:
- Testing of the hoist operation up and down; trolley travel; bridge travel; limit switches and locking and safety devices
- Testing of the trip setting of the hoist limit switches to make sure the actuating mechanism of the limit switch is functioning properly
- Load test the crane at no more than 125% of the rated load and keep test reports on file where readily accessible
The load testing of the crane can be performed with a variety of materials including concrete, steel, or water weight bags. Again, make sure that the installers have a clear understanding of who is responsible for providing the testing materials so that they can have material on-hand and begin load testing the crane as soon as installation is complete.
The Overhead Crane Installation Process
Any special considerations for an overhead crane installation actually begin during the quotation process. During that process, the overhead crane installer will review generic drawings of the crane equipment and review blueprints or building floor plans to give their best estimate of what it will take to install an overhead crane in the customer’s facility.
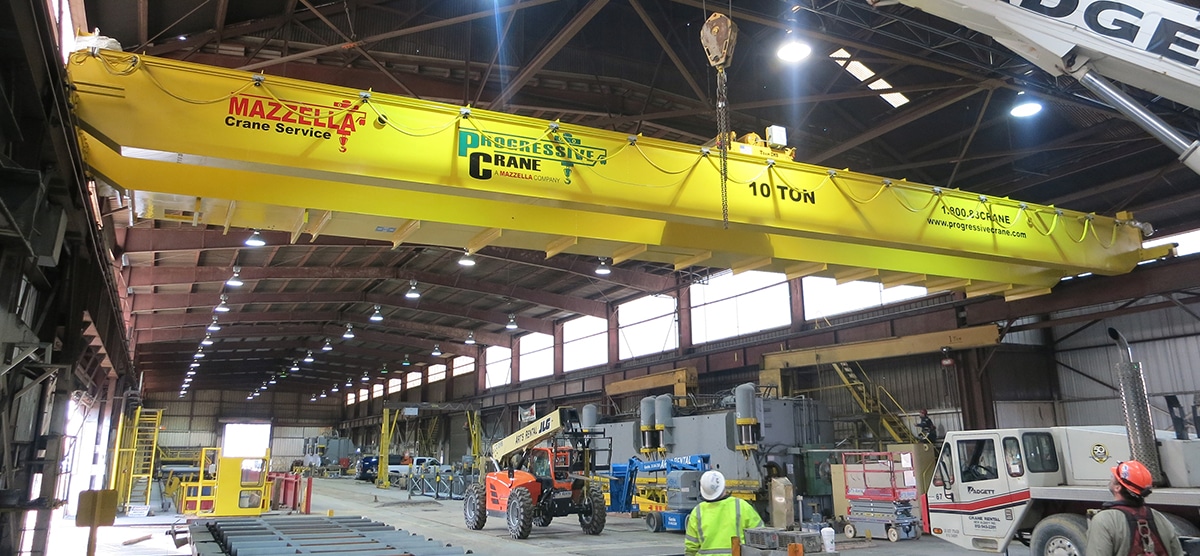
In the quote, the crane installer will provide a window or time frame that they think they’ll need to complete the crane installation. This can range anywhere from 2-10 business days, to a longer time period for more extensive or complex crane installations.
This estimated installation window will be consecutive working days—once they’ve brought the cranes, trucks, materials, and all installation equipment on-site, they can’t break up their time, or stop and re-start the installation, without significant increases to cost of the crane installation.
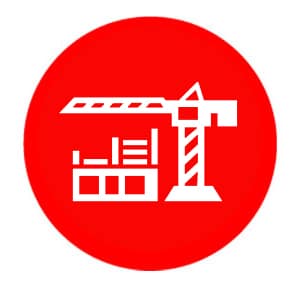
Installing a Crane in a New Construction Facility
Ideally, you’re installing an overhead crane into a new construction facility and the Engineers and Project Managers can work with your building construction contractors right from the start. This gives them more freedom and flexibility to design the building to accommodate an overhead crane system.
The manufacturer can provide a construction contractor with crane loads and also help calculate building support requirements for the crane system. The contractor can provide the crane manufacturer with drawings that allow the manufacturer to incorporate the crane design right into the building design and prints.
In rare cases, you may be able to design and build the facility around the application of the crane. This truly allows you to accommodate all design requirements including hook height, lift, span, and any foundation or structural requirements. This type of upfront planning is the most cost-effective way to help you accommodate the space required to operate an overhead crane, as well as lay out your production areas, design work cells, and maximize storage and floor space.
Heck, if an overhead crane is one of the first items installed in the building, you can even utilize the crane to help with the construction and erection of the building and other equipment in the facility.
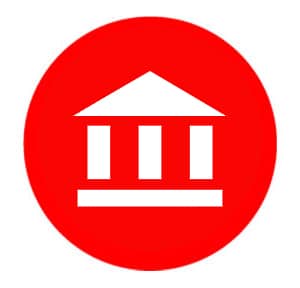
Installing a Crane in an Existing Building Structure
Unfortunately, most crane installations don’t occur in a brand new facility with a flexible installation time frame and a blank slate to design and build the structure around the crane itself. In most cases, the design and engineering team has to retrofit an overhead crane and its support structure into a space that wasn’t originally designed for a crane system.
To further complicate things, production is already up and running with employees moving about and machinery and other equipment in operation—all creating obstacles for getting installation equipment and materials into the building.
Installing an overhead crane in an existing building requires a thorough understanding of the current building’s structural supports. You will most likely have to bring in a third-party to perform structural surveys of the following:
- Support beams or columns
- Roofing
- Foundation and flooring (concrete, dirt, gravel, etc.)
- Any existing runway structures
In most cases, these load surveys need to be performed by a third-party civil or structural engineer and are the responsibility of the customer to coordinate and facilitate prior to the installation. A crane installer may be able to help coordinate the effort, but they will not perform the surveys or load ratings themselves. The results of these ratings can determine if the crane is supported from the roof, is a free-standing design, or can be tied back to existing supports.
The deadweight of the crane, or the loads on the structure which remain fixed even when the crane is not performing a lift, need to be considered. Ceiling beams, flooring, and support beams can be reinforced with internal bracing, or can be totally redesigned to spread the load between multiple points versus a single point.
You should have a clear understanding of any additional costs related to reinforcing your foundation, ceiling beams, or building support columns prior to the installation of any overhead crane.
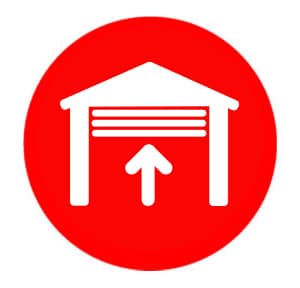
Free and Clear Access to the Facility
The Project Managers and installers should have a clear understanding of how they’re going to get the crane equipment and any other equipment required for installation into and out of the building and yard. This equipment can include any of the following:
- Semi-trucks, trailers, and flatbeds
- Mobile installation cranes to lift the bridge and runway beams
- Generators
- Scissor lifts
For a wide span crane system, it’s a good idea to have the installers come out and do a dry run prior to the installation date. A tape measure can be used to mock up the length of the beams that need to be maneuvered through the facility and a couple of guys can plan a route to safely and efficiently move material to the installation site.
It also helps them determine if any building panels need to come off, if any fencing needs to be temporarily removed from the yard, and identifies potential obstructions within the facility that may affect installation efficiency.
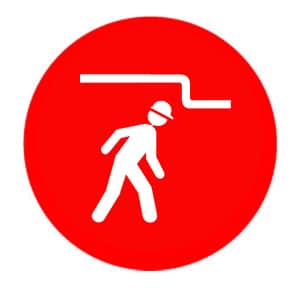
Headroom
Another often overlooked consideration is headroom within the facility. If you’ve designed a crane system that just meets OSHA’s 3” minimum overhead clearance requirement, how do you plan on erecting the crane itself? You may not have enough headroom to use a mobile crane or man lift to pick the beams up to erect the crane’s runway and bridge structures.
You may need to leave off a building panel for a new construction facility, or use a skylight or other means of roof entry on an existing facility. It’s better to plan for that ahead of time, than to realize it’s an issue on the day of the installation—potentially racking up additional charges for a longer than expected installation.
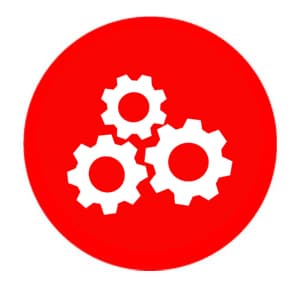
Production Costs
If you’re installing an overhead crane into an existing building, then you have to consider what type of production may be affected by the crane installation. Are there permanent work cells that need to be maneuvered around? What type of other equipment or machinery may cause obstructions for the installers? Do you plan to have production up and running during the installation? If the installers need to work around production or operating machinery in your facility, they need to know that upfront so they can accurately quote and develop a timeline for your installation.
However, sometimes the cost of shutting down production is just too high. Understanding how production downtime can affect your bottom line will help you determine if it’s better to have the installers work while your other equipment is in operation, or if you can schedule an installation to occur during off-hours—including during the evenings, on weekends, or even on holidays.
However, you should know that non-standard installations typically come at a higher rate than the standard hourly rate because the installers are working non-traditional hours and may have to run continual shifts to complete the installation during the desired time frame.
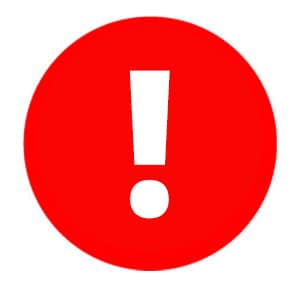
Not Being Ready When the Installers Show Up
Some overhead crane manufacturers require 30 days change notice to the agreed-upon install date, and other manufacturers may only require 7 days prior to make any changes to the scheduled install date. Make sure that you have a clear understanding of the “point of no return” for your overhead crane installation.
Once the process gets rolling, there’s really no way to stop it as the crane and installation equipment is probably en route to your facility. Also, consider all of the different people that will be involved in the installation process and all of the effort involved to coordinate their schedules:
- Truck drivers
- Mechanical installers and mechanical assemblers
- Riggers, who will do the majority of the unloading and setting up of equipment
- Crane operators
- Electrical specialists
- Crane technicians
Your agreement with the installer will specify that if any type of delay occurs within that 7-30 day cancellation window, you will incur significant charges related to paying employee wages, and rental and storage of equipment.
It is so important that you keep in constant communication with the crane installer and notify them immediately of any issues or concerns that could delay their installation time frame.
Overhead Crane Service, Maintenance, and Repairs
Keeping your overhead crane in service and in peak operating condition, should be a top priority for safety, maintenance, or operations personnel at any job site or industrial facility. Frequent and periodic inspections help to keep crane and hoist equipment operating at top efficiency, help keep the user and other personnel safe, help reduce costly down time, and extend the life of the equipment.
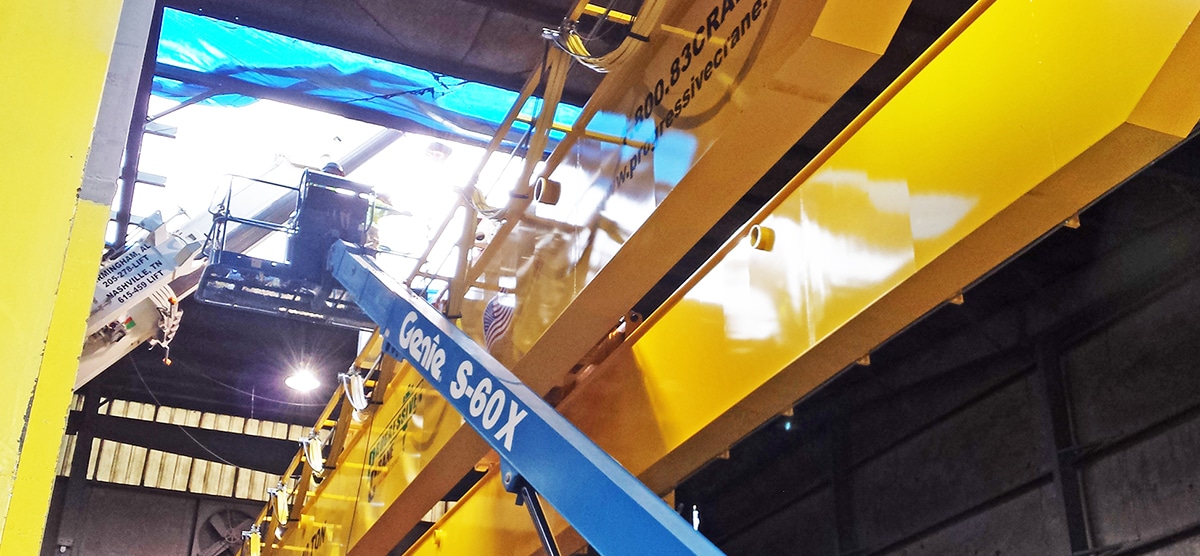
Routine Maintenance
Unfortunately, your overhead crane is going to break down at some point. Just like any other appliance, vehicle, or piece of machinery, an overhead crane requires regular service and maintenance to keep it performing to the best of its abilities. Depending on how often the crane is in use, the operating environment, and how frequently it gets inspected, all contribute to the service life of an overhead crane system.
Just like you need to replace brake pads on your vehicle, or the filters in your furnace, overhead cranes have parts that need to be adjusted, maintained, and replaced at regular intervals. Investing in a reliable overhead crane and hoist service provider, or an in-house maintenance team, can help keep your crane up and running, but you should always budget for unexpected repairs and possible production downtime.
Plant managers and maintenance personnel need to establish a preventative maintenance program for their overhead crane based on the recommendations of the crane manufacturer. Each manufacturer has their own recommended protocol for regular and scheduled maintenance of their equipment, so it’s important to consult with them directly regarding crane operation, application, and maintenance protocols.
Replacement Parts and Repairs
Also, keep in mind that the longer you own your crane system, the more difficult it may become to source replacement parts, or find parts without long lead times. If your overhead crane is critical to your facility’s production and operations, then you or your crane service provider should have an inventory of critical replacement parts, or a backup plan to move that same material through your facility without the use of a crane.
In some mill applications, a broken-down crane can cost tens of thousands of dollars an hour! Know what the cost of production downtime means to your bottom line and plan accordingly.
Overhead Crane Operator Training and Inspection Protocols
Providing training for your overhead crane operators and riggers should not be considered an expense, but you should look at it as an investment to help keep your workers safe and extend the life of your equipment. The same can be said for developing a frequent inspection program for your crane.
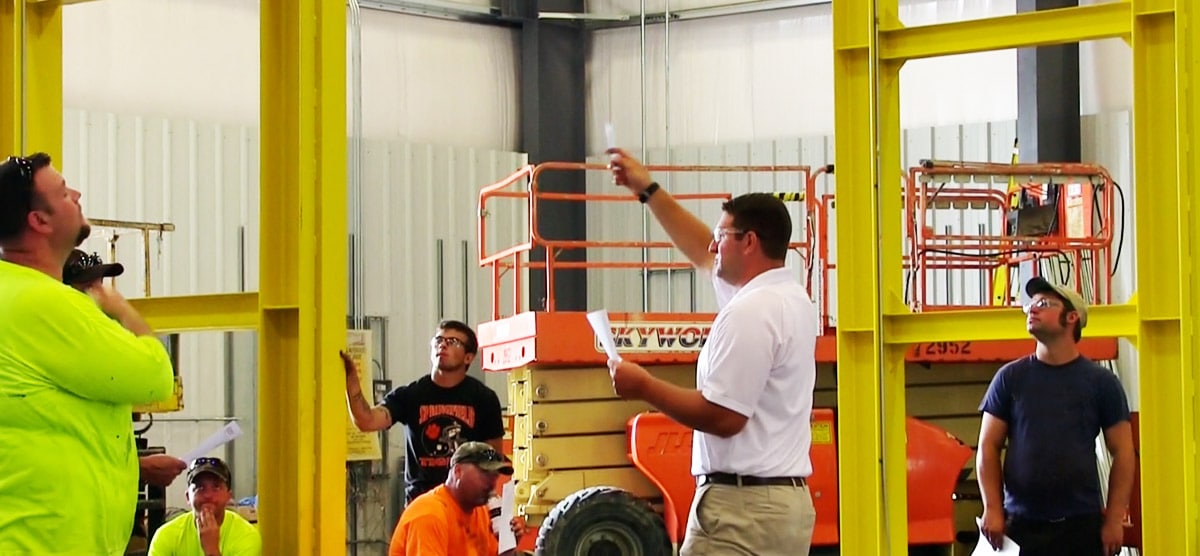
Crane Operator Training
According to ASME B30.2 standards, it is the responsibility of management (owners/users) to provide training to those who will be operating the crane, as well as those who perform maintenance or repairs on a crane.
Operator Training – Crane operator training shall be provided to promote proficient performance of a crane operator in accordance with best practices.
Maintenance Training – Maintenance training shall be provided to promote proficient adjustments, repairs, and replacements to an overhead crane that will allow the crane to perform. Training shall also be provided to persons who maintain the mechanical, structural, and electrical components of an overhead crane system.
They’ll review your equipment, review inspection and training records and watch your personnel rig a load and operate the crane to make sure they’re using the equipment safely and following best practices laid out by ASME, OSHA, and CMAA standards.
Overhead Crane Inspection
Developing an overhead crane inspection protocol and making sure your operators report anything out of the ordinary, will help to identify and address smaller problems before they become much larger and possibly catastrophic problems. Not only is it best practice to regularly inspect your overhead lifting equipment, but it’s also required by OSHA, ASME, and CMAA:
Initial Inspection – Any new, reinstalled, altered, repaired, and modified crane shall be inspected prior to initial use.
- A new crane’s initial inspection shall be performed by a qualified OEM representative in accordance with OEM recommendations.
- An altered, repaired, modified or reinstalled crane’s initial inspection shall be performed by a qualified person to assure that the modified component(s) have been properly installed and functionally tested.
Frequent Inspection – A frequent inspection is a visual and operational inspection performed monthly or as often as daily. Inspection frequency is based on service, environmental, and application factors, as designated by a qualified person.
Periodic Inspection – A periodic inspection is a detailed visual and operational inspection where individual components are examined to determine their condition. Inspection frequency can be quarterly to annually and is based on service, environmental, and application factors, as designated by a qualified person.
You can also bring a third-party on-site to assess your lifting and rigging practices. Their trained and certified personnel will come on-site and observe your lifting practices, review your documentation and training records, and look at the equipment that you use to make lifts.
From there, the results of this assessment can be used to develop programs that solve safety and compliance issues regarding overhead cranes and rigging equipment.
Improved Safety and Production Efficiencies
So, what is the final hidden cost of owning an overhead crane system?
Once that initial overhead crane is installed and up and running, you may find that your employees want you to buy another one!
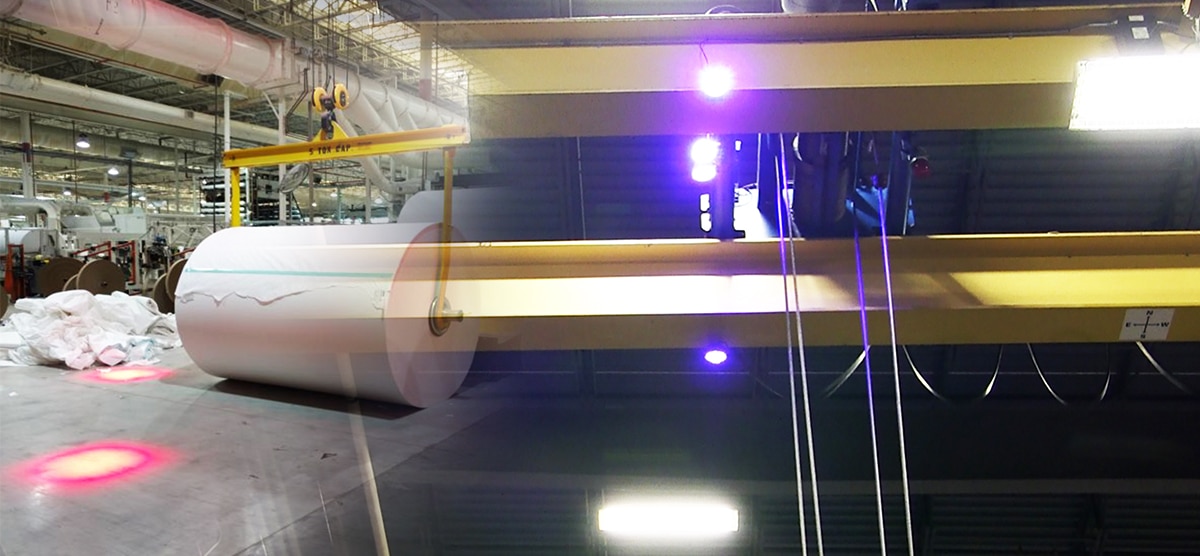
Instead of using a tow motor or manual labor, your crane helps simplify the process of moving heavy materials through your facility in an efficient and safer manner. In fact, those are the two biggest advantages of using an overhead crane.
Overhead cranes are more efficient than using a group of workers or tow motors to lift and move material and can work up to 2-3 times faster. Think about how a manufacturer, mill, or warehouse can streamline their processes and procedures by introducing an overhead crane to automate the lifting, maneuvering, and unloading of materials at their facility.
Another advantage of installing an overhead crane is that cranes can be used to lift and move materials in extreme environments and can handle corrosive or dangerous materials like hot metals, chemicals, and heavy loads. A workstation or jib crane can be put in place to help workers move heavy objects in a controlled manner and help cut down on repetitive motion injuries and muscle strains.
In the industry, they often say that the easiest crane to sell is the 2nd one to a business owner who’s already bought his first. Once you understand how valuable they can be to your production and operations, it’s easy to dream up an endless possibility of future uses for all different types of cranes.
The other major benefits to using an overhead crane system include:
- Reduction in workplace accidents
- Reduction of product or material damage
- Improved workflow
- Lowered operating costs
- Green solution that reduces environmental impact
In order to get the most bang for your buck and understand the future return on your investment, consider the following:
- Understand and discuss with the manufacturer why you’re spending the money you’re spending on their proposed crane design and what you’ll get in return for that investment
- Make sure you fully understand the quote and review it with the manufacturer. Are freight, installation, and miscellaneous fees like permits, surveys, or inspection included?
- Make sure the installers visit the installation site prior to installation to understand your building layout and identify anything that may impact the installation time frame
- Understand how critical this equipment will be to your production process. Is there redundancy built in to move material should the crane go down? How much will production downtime cost you if your crane goes down for service or repair?
- Invest in an in-house training and inspection program. Making sure that your operators know how to use the equipment properly and that the equipment is regularly inspected and serviced will help prolong its service life and reduce future downtime.