Different Types of Overhead Cranes
Overhead cranes can vary so much in terms of specifications and configurations. No two crane builds are exactly alike! A crane that worked in a similar building structure, or similar lifting application, may not be the best crane for your facility or your application. So, selecting the right type of crane for your business is critical to maximizing efficiency, streamlining workflow, and getting the best bang for your buck.
Bridge Cranes
An overhead bridge crane can be configured in a single girder or double girder design. In simple terms, a bridge girder, or beam, is the support structure that allows the trolley and hoist to move from side-to-side along the bridge. The trolley is used to precisely position the hoist prior to raising or lowering a load.
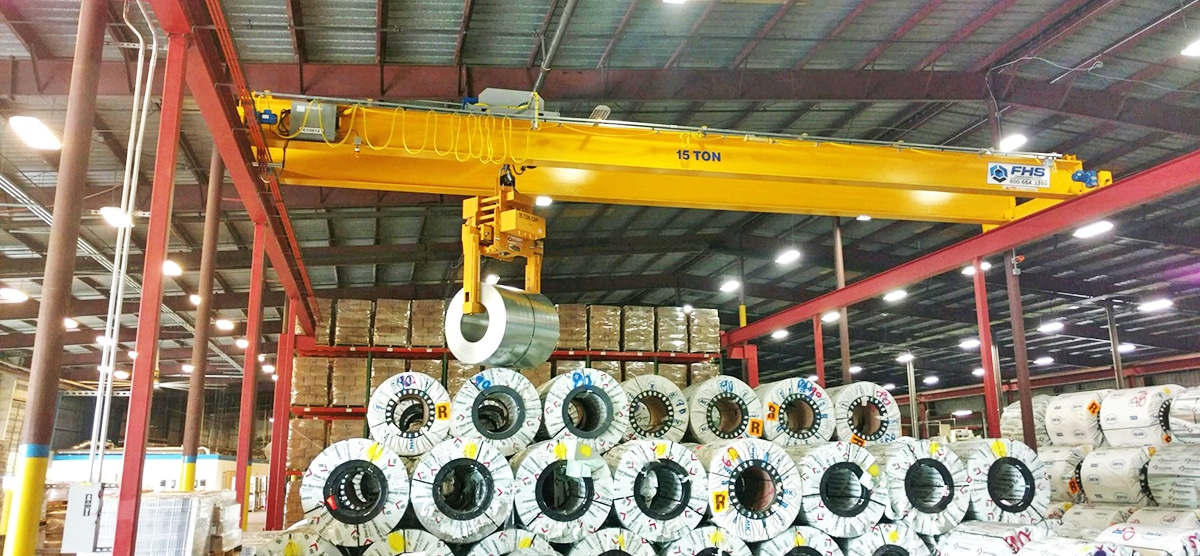
Single Girder and Double Girder Bridge Cranes
To a degree, both single and double girder cranes are equal in strength and durability. The main difference between the two comes down to hook height, or how high above the ground your hoist can lift. A double girder crane can provide more hook height because the hoist is placed on top of the girders, instead of below them.
There are some instances where a double girder or single girder configuration may be the better option. We’ll discuss some of these instances below:
Single Girder — The bridge consists of one girder beam supported on each side by an end truck. The trolley and hoist are most commonly underhung—meaning they run on the bottom flange of the bridge. They also tend to be less expensive due to:
- Only one girder is required to move the trolley
- Reduction in freight expenses
- Faster installation
- Simpler hoist and trolley design
However, in the instance that a crane needs to handle more than 15 tons, or the span is more than 65 feet, a double girder configuration may be the better option.
Double Girder — There are two girder beams that make up the bridge, and they are supported by an end truck on each side. The trolley and hoist run on a rail installed on top of the bridge girders. Double girder cranes are recommended for heavier-duty applications where the crane has to handle more than 15 tons, or the span is more than 65 feet.
Double girder cranes are the best option when the crane needs to be customized with things like walkways, cabs, magnet cable reels, or other specialized equipment. And on a top running design, they can provide more lifting height since the hoist isn’t hanging underneath the beam.
Top Running Vs. Under Running Cranes
When it comes to defining clear differences between bridge cranes, you will want to consider if you require a top running or under running crane.
On a top running crane, the bridge runs on rails along the top of the runway beams.
On an under running, or underhung crane, the bridges are supported by the bottom of the runway beams and the wheels run along the bottom of the lower beam flange.
Top Running Cranes
These cranes have no limiting capacity — meaning they can be built to go from small capacities to very large capacities. They include a rail installed on top of each runway, and the bridge wheels move on the rail instead of the bottom flange of the runway beam. These cranes are supported by the building structure or runway support columns, or sister columns, and are ideal for moving extremely heavy loads.
Top running cranes can be designed in a single-girder or double-girder configuration:
Single Girder Top Running Benefits:
- Typical Load Capacity: .25 – 20 tons
- Typical Span: Under 65 feet
- Typical Service: Light
- Low deadweight
- More overhead space
- High speed
- Lower production cost / lower overall price
Double Girder Top Running Benefits:
- Typical Load Capacity: 20 – 400 tons
- Typical Span — Over 65 feet
- Typical Service — Heavy
- Ideal when extremely high hook height is necessary
- Better hook height
- Most overhead space
- More lift
- High speed
Under Running Cranes
Often called “underhung,” because the crane wheels are supported by the bottom flange of the crane runway beams acting as the crane rail. These types of cranes can allow you to maximize your facility’s floor space for production and storage of material because they are supported from the ceiling trusses or the roof structure. Or, they can be designed to utilize an existing support structure (if adequate), or run on a newly-engineered support structure.
- Typically designed for lighter service / lower capacity applications
- It can become impractical and expensive to engineer an under running crane to make it a high-capacity piece of equipment
- Offers excellent side approaches and maximize utilization of the building’s width and height when supported by roof or ceiling structures
- Hook height is less than top running because bridge and hoist hang underneath runways
Gantry Cranes
A gantry crane is similar to a bridge crane, but instead of moving on suspended runways, the crane uses legs to support the bridge, trolley, and hoist. These legs travel on rails that are embedded in, or on top of the floor or ground structure.
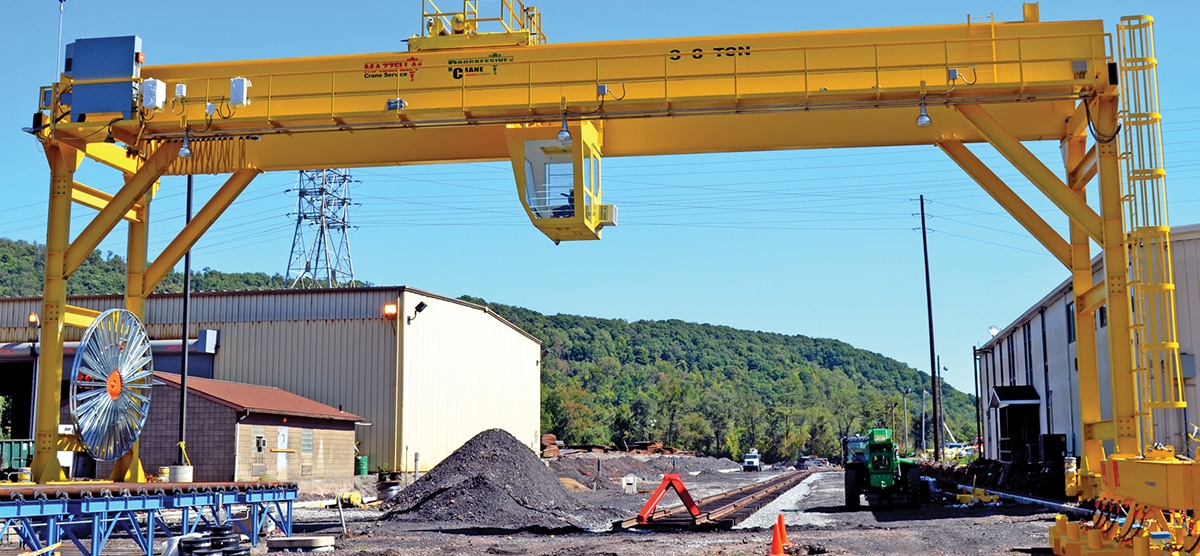
A gantry crane is ideal when you require a lightweight and quick knockdown crane for applications that require portability and corrosion resistance. They are also considered when there is a reason not to incorporate an overhead runway system and are most traditionally used in outdoor applications where full beams and columns can’t be installed, or they can be used below an existing bridge crane system. Gantry cranes are commonly found in shipyards, railyards, special construction sites like where a bridge is being built, or in places like steel mills where overhead room may be an issue.
Gantry cranes come in a wide range of designs, including:
- Adjustable Gantries — used for warehousing applications requiring the movement of materials through aisles, doorways, around obstacles, and over or under obstructions. Welding and fabrication shops can use gantry cranes for lifting parts and equipment into position.
- Portable Gantries — used for plant maintenance applications requiring replacement and relocation of equipment and machinery. Service truck applications requiring quick knockdown for fast, easy movement to and from a work site.
- Track-Mounted Gantries — used for applications requiring lifting and moving heavy loads over a fixed route, either manually or motorized.
Moving and lifting heavy materials doesn’t have to involve installing expensive equipment or permanently changing your facility. Gantry cranes do the job efficiently and economically and are ideal lifting solutions because:
- No permanent installation is required — making gantry cranes ideal if you rent or lease your facility
- Quick and easy assembly and tear-down
- Portable design allows for use in more than one facility or work area
Monorail Cranes
Most commonly found in a production or assembly line, this type of crane uses a trolley to carry the hoist along a single path. Monorail cranes do not utilize a bridge or girder design — instead, the trolley is designed to connect to an I-beam, often already built into the ceiling structure, and runs along the flat surface (flange) on the bottom of the beam. They can also utilize a configured support structure as well.
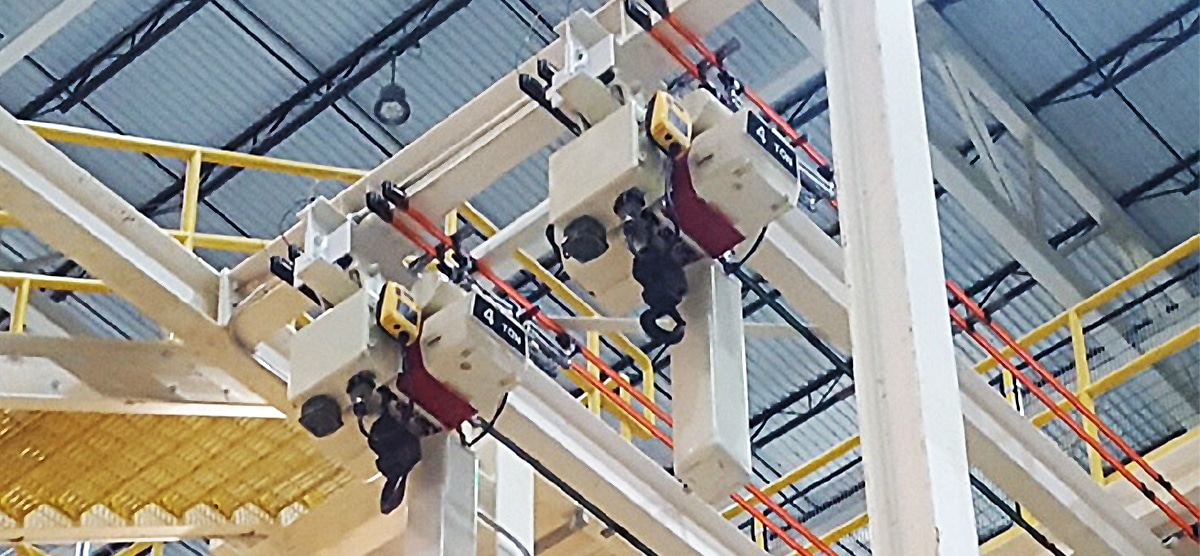
Material can be run back and forth in a straight line, or the rails can be designed with curves, branches, switches, and with changes in elevation. Monorail cranes follow a singular path and are designed for lifts that do not require the side-to-side trolley movement provided by the bridge in an overhead or gantry style crane.
Monorail cranes are perfect for lifting applications where a full-blown crane design is not required. They’re a cost-effective and versatile solution for many assembly line and production applications.
Jib Cranes
Jib cranes come in a number of different styles and types but do not utilize a runway or track system. They can be stand-alone or column / wall-mounted and offer a wide variety of capacities, heights, and spans.
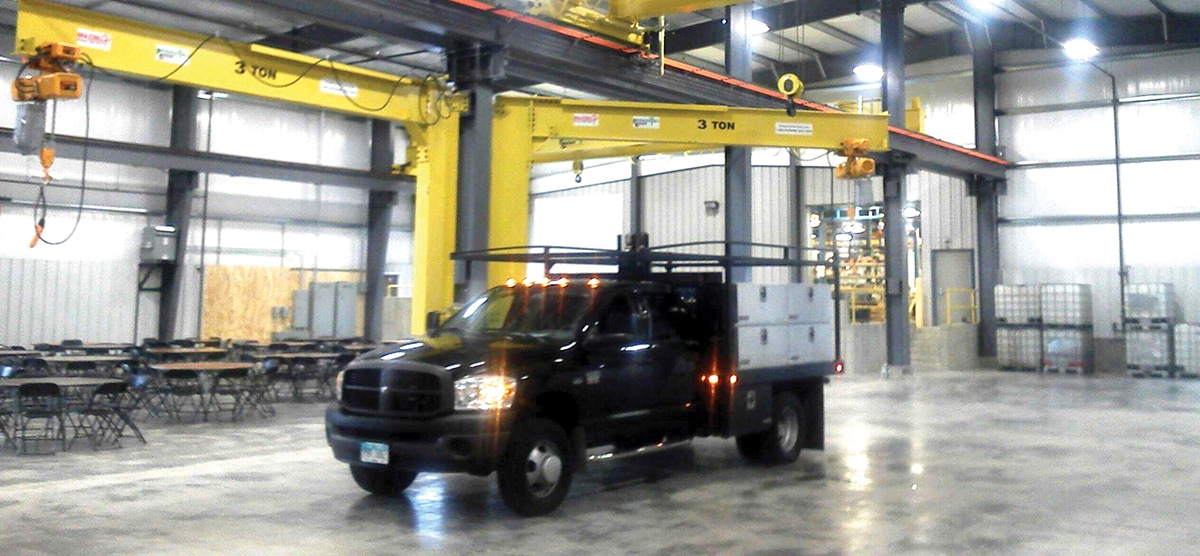
Jib cranes are space-saving, economical, and are ideal for jobs like maneuvering or moving items for assembly within a smaller radius. They can typically offer 180-360° of rotation, and even small ones can hoist several tons of material.
The best way to determine what type of jib crane is best for your application is to consider the following:
- What type of operation or usage will this equipment see?
- What height clearances or spans are required in this work area?
- Is there available support structure available for mounting, or will this be a standalone unit — floor, wall, and ceiling?
- What other special options or considerations are required?
- What is the available budget for the system and installation?
Workstation Cranes
Workstation cranes are designed to allow the operators an ergonomic means of moving or lifting loads with limited effort in a smaller size work area. Workstation cranes are typically lighter-duty systems — lifting materials from 150 lbs. up to 2 tons in capacity. They’re designed for repetitive lifting of loads, positioning of loads, increasing worker productivity and ease of work flow.
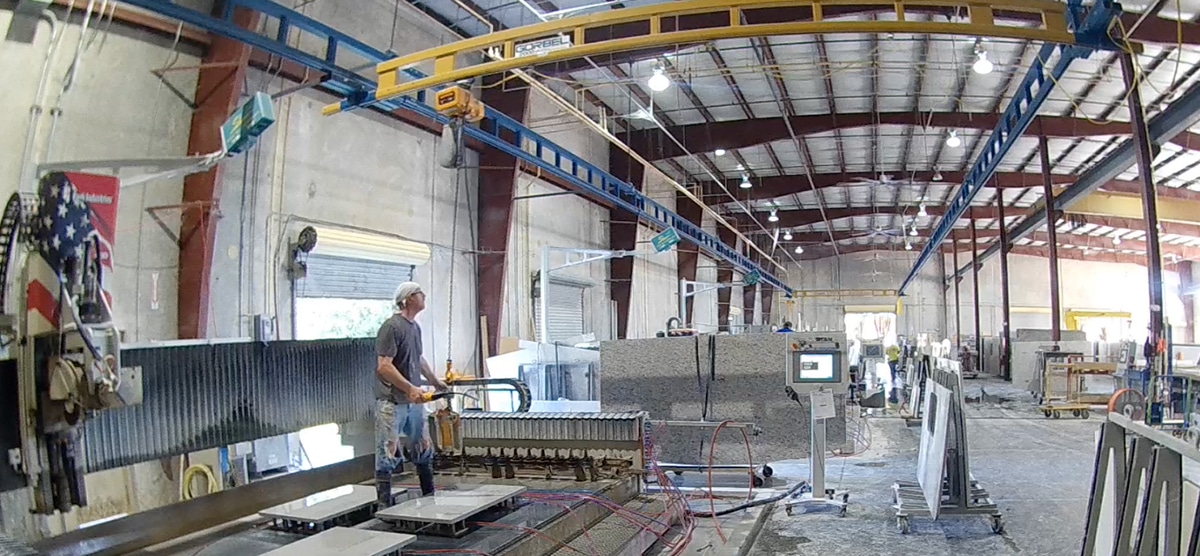
They can be built and installed easily using a modular design for greater flexibility and do not require an existing support structure for installation.