Five Common Problems with Overhead Cranes and How to Avoid Them
<p>This section outlines the five most common problems with overhead cranes so that you have a better understanding of what issues or problems you might encounter during the life of your overhead crane. And most importantly, what you can do to help prevent or mitigate them.</p>
Just like with an automobile or any other piece of equipment or machinery, your overhead crane will need regular maintenance to prolong its life and keep it operating efficiently. We understand that purchasing an overhead crane can be a big investment, and an investment that you’ll want to protect.
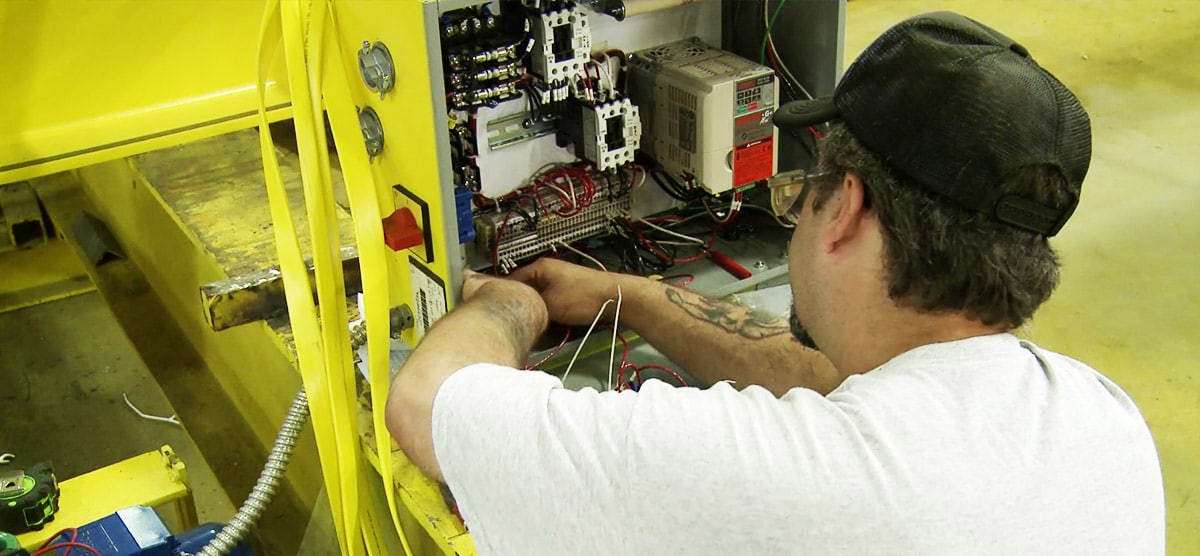
This section outlines the five most common problems with overhead cranes so that you have a better understanding of what issues or problems you might encounter during the life of your overhead crane. And most importantly, what you can do to help prevent or mitigate them.
We recommend that you establish a regular inspection schedule for your overhead crane. You should also follow the manufacturer’s recommendations for service and maintenance intervals, and consider duty cycle and environmental factors when designing your crane to help extend the life of your crane and the crane components.
1. Damage or Degradation to the Wire Rope
Damage or degradation to wire rope is one of the most common issues that you may experience with an overhead crane system.
There are a number of common wire rope problems, including any of the following:
- The wire rope has jumped out of the reeving system
- Reduction of rope diameter below nominal – loss of core support, internal or external corrosion, wear of outside wires
- Broken or worn outside wires
- Corroded or broken wires at end connections
- Severe kinking, crushing, cutting, or unstranding
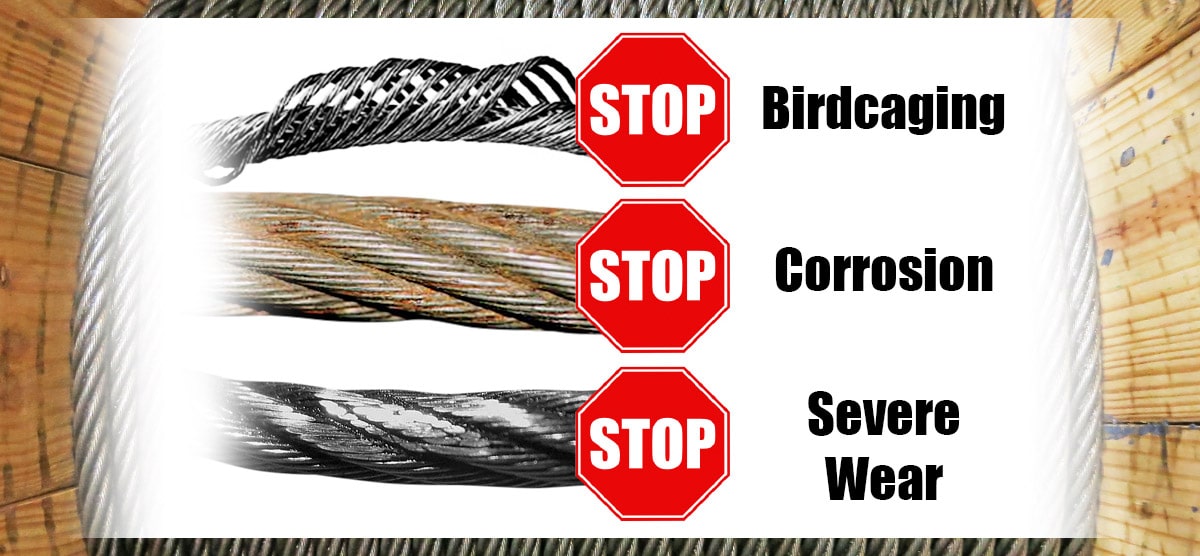
Many operating conditions can affect the life of wire rope. Bending, stresses, loading conditions, speed of load application (shock load), abrasion, corrosion, sling design, materials handled, environmental conditions (heat or chemical exposure), lubrication, and history of usage will all factor into how long wire rope can stay in service.
The best way to prevent damage to, or failure of, a wire rope is to inspect it prior to each shift. If any evidence of damage is observed, the wire rope should be properly disposed of to prevent further usage.
Also, make sure that the wire rope is properly lubricated. Proper lubrication of the wire rope has two primary benefits:
- Reduces friction as the individual wires move over each other
- Provides corrosion protection and lubrication in the core, inside wires, and outside surface
2. Crane Skew and Alignment Issues
An overhead crane that is out of alignment and skewing as it travels down the runway can cause significant stresses and damages to the entire crane system. The problem with a crane that isn’t tracking properly is that over time, forces that weren’t accounted for in the design and installation of the overhead crane cause stresses to the runway beams themselves and also to the tie-backs or building support structures.
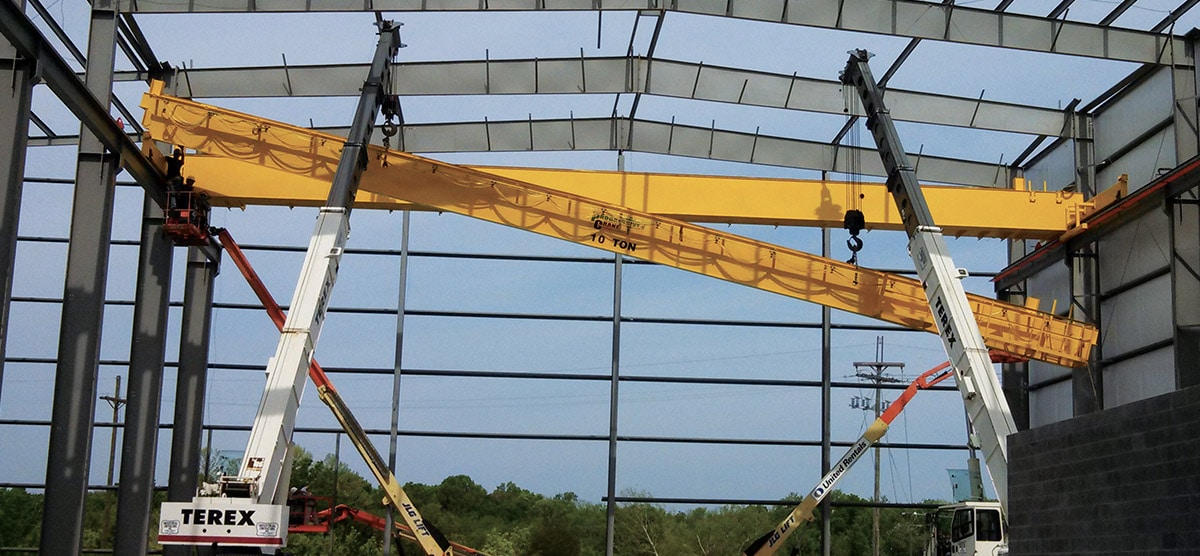
These types of stresses can result in:
- Accidents
- Crane failure or derailment
- Equipment downtime and productivity loss
- Costly repairs and replacement of parts
A crane that isn’t tracking properly also causes extensive wear to the wheels, wheel bearings, and wheel flanges—as well as premature wear to the motor drives and other equipment.
There are certain signs that your crane may not be aligned properly and is skewing as it moves down the runway.
When your crane is in operation, be aware of the following:
- Loud scraping sounds
- Broken or cracked wheel flanges
- Abnormal wear on the wheels, wheel bearings, and rails
- Extra power required to move the crane through certain areas of the runway
- Wheels that float or climb over the rail and then crash down
The best way to prevent overhead crane skew and alignment issues is to have your crane regularly inspected by a reputable third-party service provider. A crane service provider can survey your crane rails and runway systems to identify and correct any issues before they become bigger problems.
A crane service provider can make sure that your overhead crane system is in compliance with the allowable tolerances specified by the Crane Manufacturers Association of America (CMAA) for the design of the runway system.
CMAA Specification #70 – 1.4.2
“Rails shall be straight, parallel, level, at the same elevation and at the specified center to center distance, within the tolerances given…”
- Crane Span Tolerance:
- Less than 50 feet: ± 3/16”
- 51-100 feet: ± 1/4″
- Greater than 100 feet: ± 3/8”
- Straightness Tolerance: ± 3/8”
- Elevation Tolerance: ± 3/8”
- Rail-to-Rail Elevation Tolerance:
- Less than 50 feet: ± 3/16”
- 50-100 feet: ± 1/4″
- Greater than 100 feet: ± 3/8”
CMAA Specification #70 – 1.4.5
“Rail joint misalignment can be a significant factor in wheel, axle, and bearing failures. It is recommended that horizontal rail separation at joints not exceed 1/16”. Vertical and horizontal alignment at joints should be maintained as closely as possible. Rail joints should be ground flush as necessary to provide a smooth transition from each rail segment to the next.”
3. Excessive Wear to End Truck Wheels
End truck wheels are components of overhead cranes that can require frequent maintenance, replacement, or adjustment. Throughout the course of a crane’s life, the wheels will naturally wear down due to normal use of the crane and will need to be replaced.
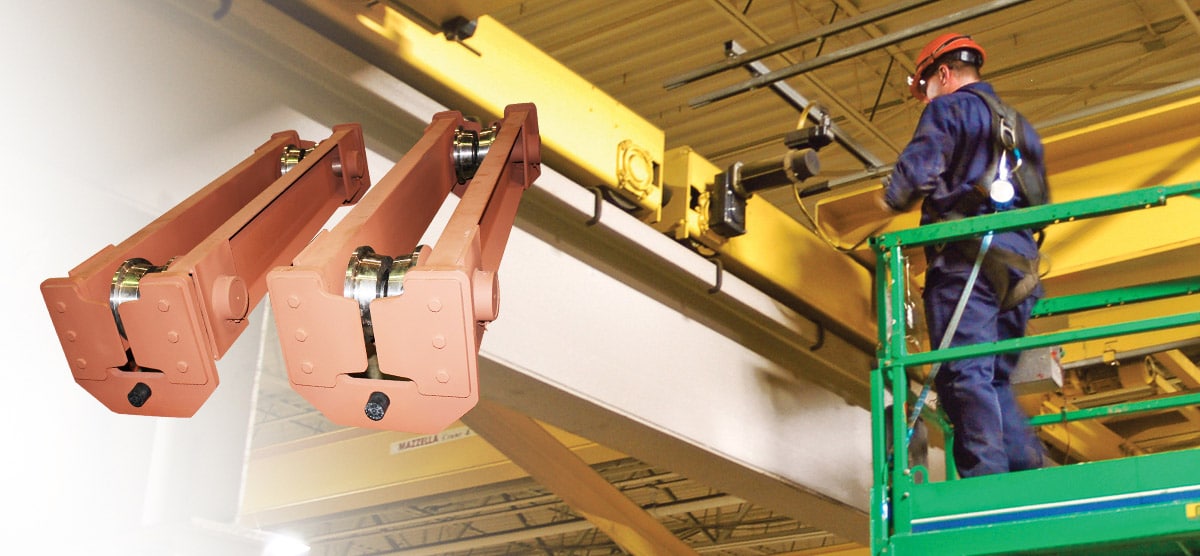
Wheels can be made of a variety of materials, including polyurethane for gantry cranes, alloys, low-carbon steel, or medium-carbon steel. The more carbon in the steel, the harder the wheel will be. There are also methods of heat-treating that can be used to increase the hardness of a wheel—increasing the service life and load capacity of the wheels.
If the wheels, wheel bearings, or wheel flanges begin to wear or break down prematurely, it can be an indication that the crane is skewing and not properly tracking down the runway system. Skewing of the crane can cause excessive wear and stress on the wheels, but also on the runway beams and support structures as well.
Wheels tend to wear out faster on a crane that was installed using an existing rail system as opposed to a new installation. Unless the runway has been properly surveyed prior to installation, the runways may be misaligned or the rails may be out of tolerance.
To avoid premature wear on the wheels and end trucks, your overhead crane runway system should be designed, tested, and regularly inspected by a reputable overhead crane manufacturer. Any signs of premature wear will indicate the possibility of a larger problem that should be addressed and corrected before the problem compounds itself. Make sure wheels were made specifically for the rail they’re running on. Hardness must match hardness of rail.
4. Issues with the Electrification System
There are a number of different issues related to an overhead crane’s electrification system that may require service or future maintenance.
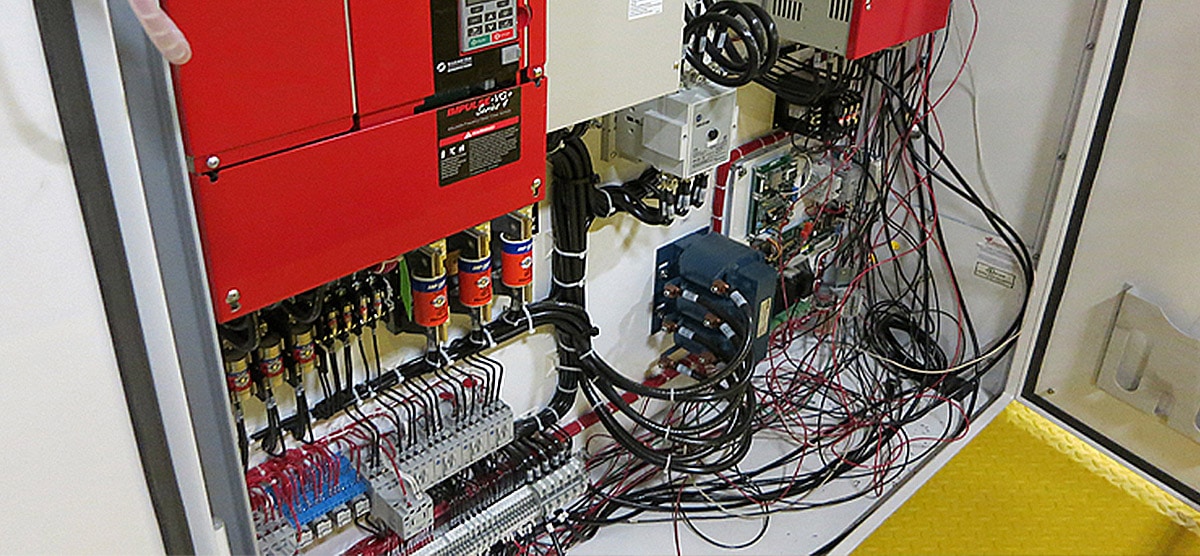
Problems with Contact Interruptions
One of the most frustrating problems that a crane operator can experience is when there are contact interruptions between the conductor bars and the collector. These contact interruptions can cause intermittent control problems with the overhead crane system.
On the collector, a brush made from carbon graphite can wear down, which can cause carbon graphite to build up. Because carbon graphite dust is a conductive material, this build up can cause shorts in the electrical connection.
On older crane systems, the copper rails on the conductor bars can also become corroded or oxidized due to the operating environment or due to long periods where the crane is not being used. To prevent this from happening, the conductor bars and collectors should be inspected and cleaned regularly to make sure that the contact between the collector and conductor bar is uninterrupted.
Another problem that can cause contact interruptions is if there are alignment issues with the conductor bars themselves, causing the collector shoes to jump out of the track and lose contact.
Problems with Push Button Pendants or Radio Controls
Although not very common, there are environments that create their own radio waves that may interfere with the operation of an overhead crane. An example might be a facility that performs induction heating or induction welding procedures. Radio waves created during these processes may disrupt the communication between the radio’s transmitter and receiver.
On pendant controls and radio controls, the push buttons or levers may stick or become unresponsive over time. The control may need to be replaced or repaired to correct any issues with the operation of the buttons.
You may also find that pendant controls can become disconnected or pulled out of the hoist. The reason that this can occur is because the operator pulls on the pendant to maneuver or position the crane—especially on jib cranes or workstation cranes. If your controls become unresponsive, you may need to check to see if the pendant became disconnected from the hoist, or have the system serviced and re-wired if any wires become loose.
Blown Fuses
If you find that your overhead crane is blowing fuses, then it’s an indication that you have a faulty circuit in the crane’s electrification system. Contact a crane service provider immediately to come out and inspect the crane’s electrification system and identify the fault.
5. Bent or Damaged Hooks
A hook is designed to hold a load in a particular and precise direction. When the weight isn’t supported as intended by the hook, it compromises the internal integrity of the hook and can increase the chance of it bending, stretching, or cracking. The load can also slip off of the hook if it stretches out the throat opening.
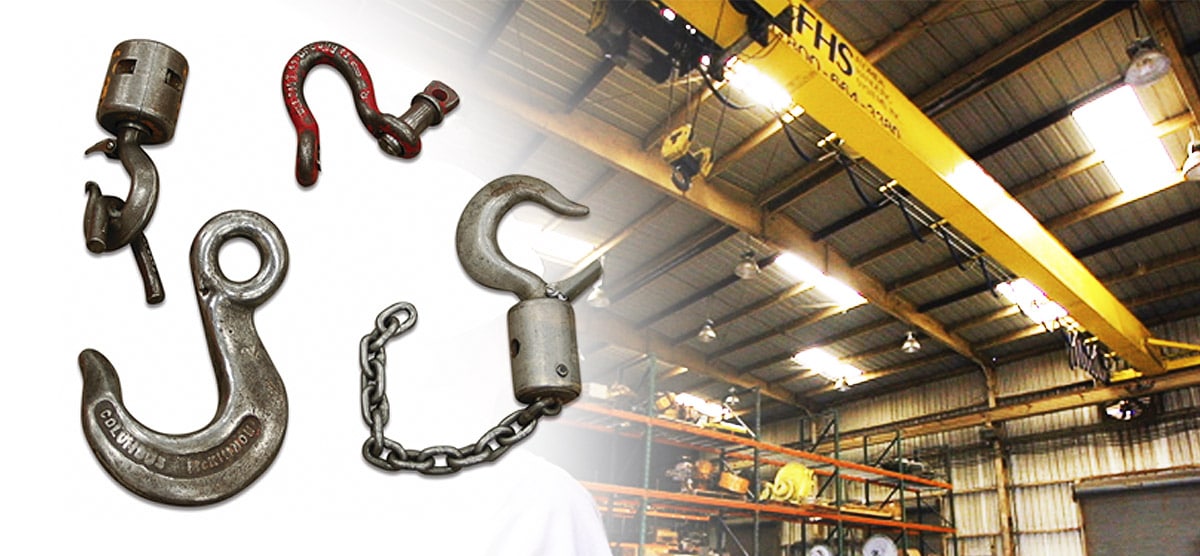
Regular inspection of hooks and other pieces of rigging hardware should be performed at the beginning of each shift to check for deformities or damage.
While there are no clear-cut guidelines on the use of hook latches, we train our employees and inspectors that if a hook is designed to have a latch, it should have the latch installed to help move a load safely and securely. We advise that the end user must evaluate the work activity with regards to the safety of their employees. If the activity makes the use of the latch impractical, unnecessary, or more dangerous, then the end user may choose to eliminate the latch. It is also recommended that each lifting activity is considered independently as far as the use of a hook latch is concerned.
Help Protect Against Excessive Wear and Costly Downtime
To help prolong the life of an overhead crane system, there are a number of things that should be taken into consideration before you even buy an overhead crane:
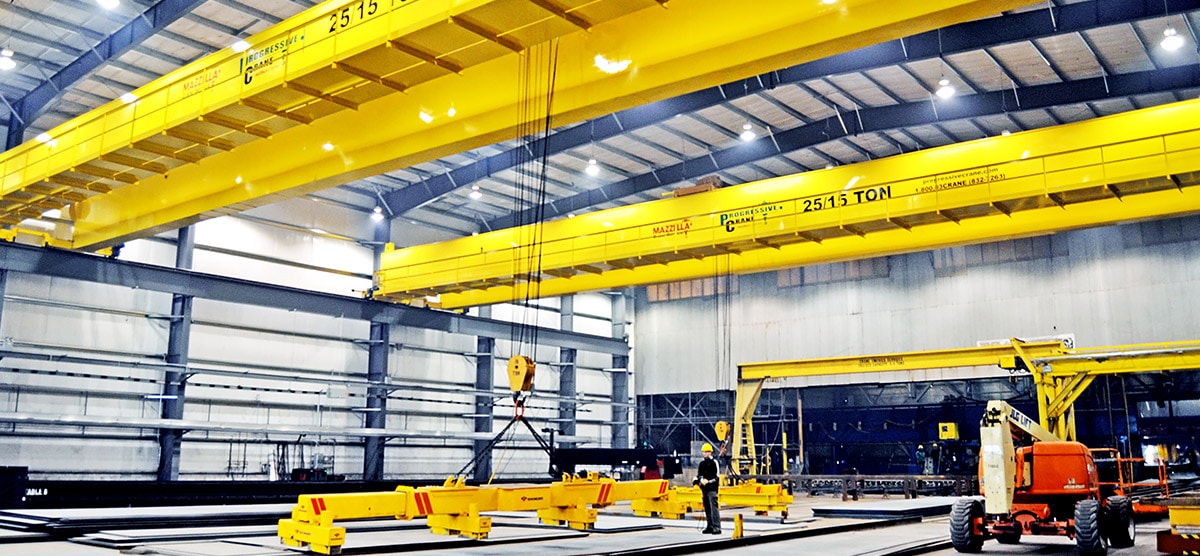
Make Sure Your Crane is Rated for the Actual Duty Cycle and Usage Required
Be honest with yourself and the manufacturer who is designing and building your overhead crane. Don’t try to design or build a crane that won’t meet the actual usage and duty cycle requirements of your business.
Every component on the crane is rated for a specific load capacity—if your crane isn’t built to handle your actual lifting needs, it can lead to premature wear or failure. If you’re straining the crane by lifting loads or using it in matters that it wasn’t designed or rated for—just because you wanted to save a few bucks—you’ll ultimately end up spending more in the long-run in repairs and costs associated with upgrading and modernizing crane components.
Consider Your Operating Environment When Designing and Building Your Crane
The environment where the crane is used can play a major role in the life of your overhead crane and the crane’s components. Environmental factors such as high heat, the presence of chemicals or fumes, steam, dust, or excess moisture can require special metal coatings to protect and enhance the operating life of the crane.
If these factors aren’t accounted for during the design and quotation process, then the components of the overhead crane can be affected by corrosion, oxidization, and parts can get gummed up with dirt and grime.
Have Your Crane Inspected Regularly
Regular inspection is one of the best forms of preventative maintenance. Staying on top of regular maintenance identifies problems earlier and allows you to replace or repair worn-out parts before they cause a major disruption to production or an equipment failure.
Not only will regular crane inspections keep you in compliance with sanctioning bodies like OSHA, ASME, and CMAA but it will help keep the crane and hoist equipment operating at top efficiency, help to keep your employees safe, help reduce costly down time, and extend the life of the equipment.
Follow the Manufacturer’s Recommendations for Regular Service and Maintenance
You should receive some type of owner’s manual or maintenance interval book from your crane manufacturer. The manufacturer’s service recommendations are provided based on the duty cycle and capacity of your specific crane, so follow the manufacturer’s recommendations for crane and hoist maintenance, as well as lubrication and inspection intervals.
Installing an overhead crane in your facility is a big monetary investment. However, it’s also an investment in your employees’ safety, as well as an investment in improving the efficiency of your production and workflow processes.
Hopefully, you have a better understanding of what types of issues or problems you might encounter with an overhead crane system and what you can do to mitigate them.