Top Running vs. Under Running Cranes
<p>One of the most common questions that we receive from customers during the consultation, design, and quotation process is whether they need a top running or under running overhead crane system. Learn more about the different factors that can help determine whether a top running or under running system will be best for your business.</p>
One of the most common questions that we receive from customers during the consultation, design, and quotation process is whether they need a top running or under running overhead crane system.
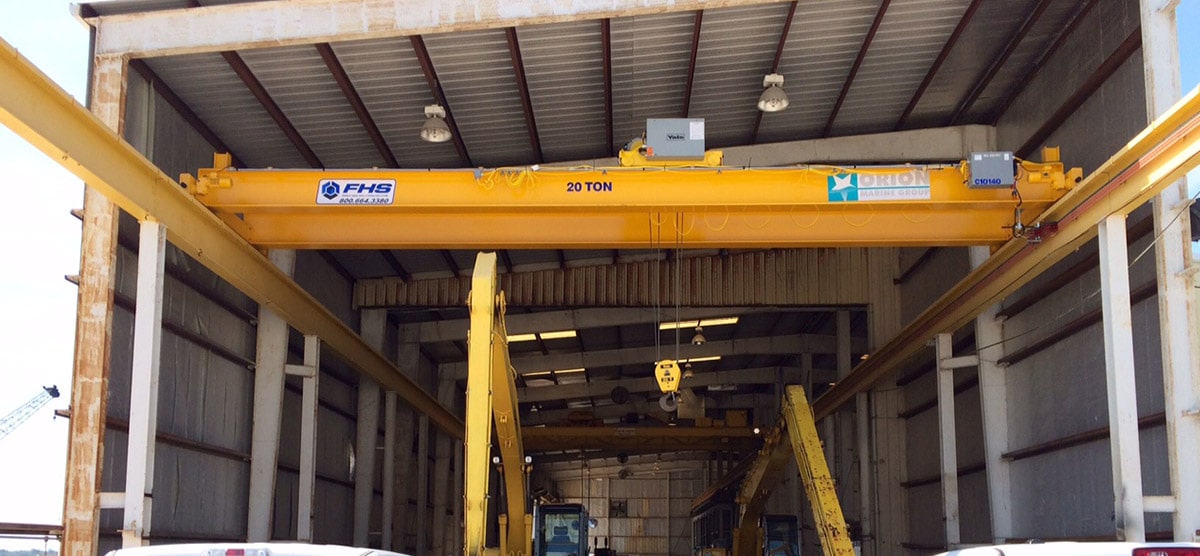
The following factors can help you determine whether a top running or under running system will be best for your facility and business needs:
- Can the existing support structure be utilized or will a new support structure need to be built?
- Are there existing runways in the facility that the crane can be installed on?
- What is the capacity of the loads that you’ll be lifting?
- What type of overhead room is available? High, unobstructed ceilings, or limited headroom due to existing cranes, duct work, light fixtures, etc.?
- How high will your lifts need to be?
- Hook approach – how much of the crane’s bridge will the hoist trolley need to utilize? Do you need to make picks or lifts near the edges or sides of the building?
- How important is free and clear floor space?
Top Running Overhead Cranes
A top running overhead crane has a fixed rail or track system installed on the top of each runway beam—allowing the end trucks to carry the bridge and hoist along the top of the runway system. Top running cranes can be configured in a single girder or double girder bridge design. A single girder bridge utilizes an underhung trolley and hoist, while a double girder design most often utilizes a top running trolley and hoist.
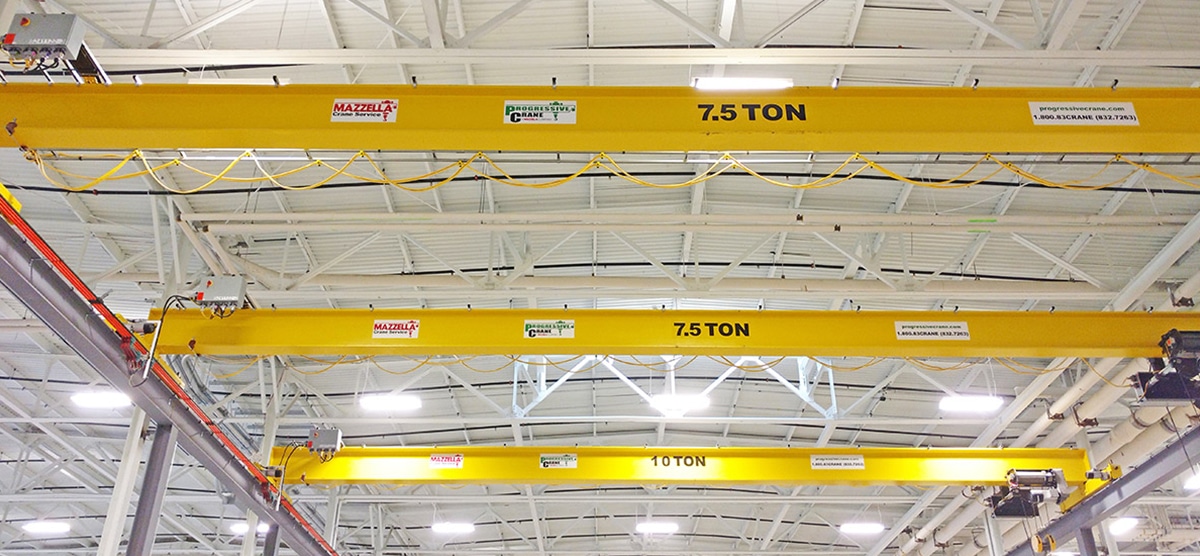
Top running overhead cranes have no limiting capacity—meaning that they can be built to handle small capacity loads or very large capacity loads. Top running cranes can be built to capacities of anywhere from 1/4-ton to excesses of 100-tons. These types of overhead cranes are supported by the building structure or runway support columns and are ideal for moving extremely heavy loads.
Top running cranes provide added lift height for buildings with limited headroom because they ride on rails on top of the runway beam. A top running double girder bridge design allows the greatest lifting height because the hoist and trolley run on top of the two bridges or girders—adding anywhere from an extra 3 to 6 feet of hook height.
Top running overhead cranes are typically larger than under running cranes, as they can be built to higher capacities and can accommodate wider spans.
Because the crane is supported on rails on top of the runway beams, there is no suspended load factor, so installation and future service or maintenance is easier and less time-consuming than an under running crane.
Over the course of its life, the track or rail system that the bridge moves on may need to be checked for alignment or tracking problems more frequently than an under running crane. Fortunately, the service and alignment inspections are fairly easy to perform and require less downtime than an under running crane.
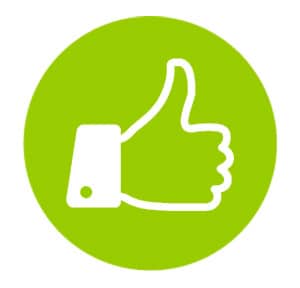
Benefits of a Top Running Crane Single Girder Crane:
- Typical Load Capacity: 1/4-ton to 20 tons
- Typical Span: Under 65 feet
- Typical Service: Light to medium duty
- Common Applications: Light manufacturing, fabrication and machine shops, light assembly line, warehousing facilities, maintenance and repair centers
- Low deadweight
- More overhead space
- Faster hoist and trolley speed
- Lower production cost / lower overall price with less material required
Benefits of a Top Running Double Girder Crane:
- Typical Load Capacity: 20-400 tons
- Typical Span: Over 65 feet
- Typical Service: Medium to heavy duty
- Common Applications: Steel and metal mills, coil handling, foundries, large fabrication and stamping facilities, paper mills, casting plants, large-scale tool and die facilities
- Allows for best hook and lifting height because hoist and trolley can run on top of the two bridge girders
- Provides the most overhead floor space
- High speed
Under Running / Underhung Overhead Cranes
An under running crane, or commonly referred to as an “underhung” crane, uses wheels that are supported by the bottom flange of the runway beam to move the bridge up and down the runway. Under running cranes are most commonly configured in a single girder design for lighter service and lower-capacity applications. They can also be built in a double girder design for higher capacities but it can become impractical and expensive to design and engineer.
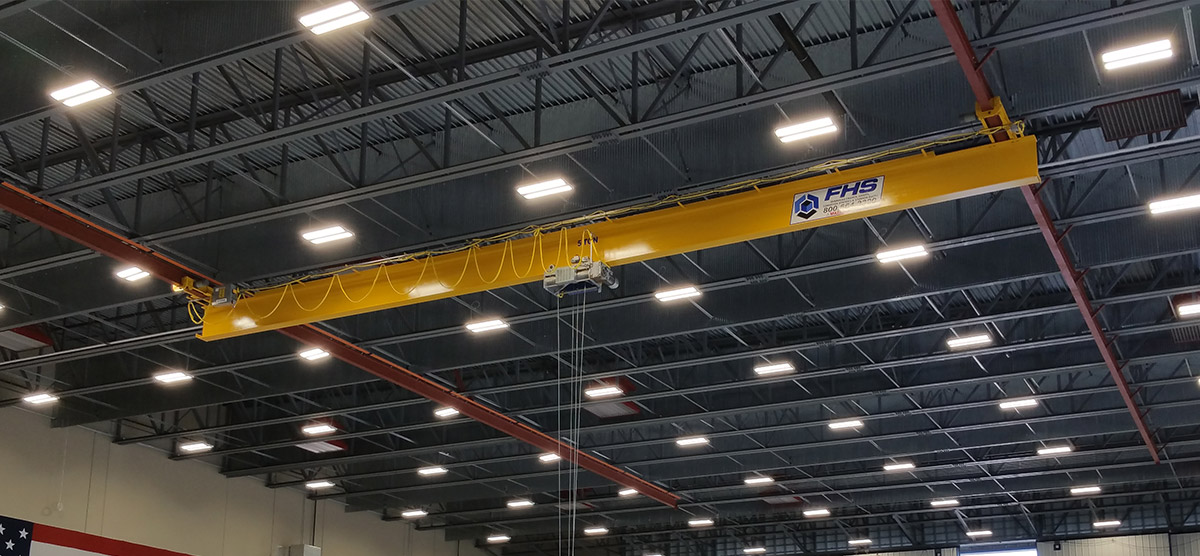
An under running single girder crane will utilize an under running hoist and trolley which moves across the bottom flange of the bridge beam. A double girder under running crane can run its hoist and trolley along the top or the bottom of the bridge beams.
These underhung types of cranes can allow you to maximize your facility’s floor space for production and storage of material because they are most commonly supported from the existing ceiling trusses or the roof structure. Underhung cranes also offer excellent side approach and maximize utilization of the building’s width and height when supported by roof or ceiling structures. They’re ideal for facilities that lack vertical clearance to install a top-running overhead crane system.
Under running cranes can be designed in a free-standing configuration if the building’s existing support structure can’t be utilized, but this setup does require the use of support or mounting columns.
Hook height and lift height is less than top running cranes because the bridge and hoist hang underneath the runways.
When it comes to the installation and service of an under running crane system, it can be more of a complex procedure leading to longer downtime. Because the crane is suspended from the runways, it can take longer to check the alignment or service the wheels of the crane, but it is easier to dial in and maintain the alignment and there are fewer tracking problems because it runs on an I-beam which is secured to building structure—limiting movement.
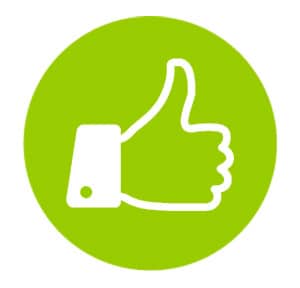
Benefits of an Under Running Overhead Crane:
- Typical Load Capacity: 1/4-ton to 15-tons
- Typical Span: Under 65 feet
- Typical Service: Light to medium duty
- Common Applications: Assembly, fabrication shops, maintenance buildings, and manufacturing facilities
- Maximizes floor space if supported by existing ceiling trusses or roof structure
- Reduces material costs if no runway support columns are needed
- Increased end hook approach and bridge beam and hoist are underneath runway beams