How to Solve Rigging Equipment Challenges in the Construction Industry
There’s no better feeling than knowing that your employees are equipped with the right tools they need to do the job, they’re properly trained on how to use their gear and make safe lifts, and that all of the gear is well-organized and in compliance with industry inspection requirements.
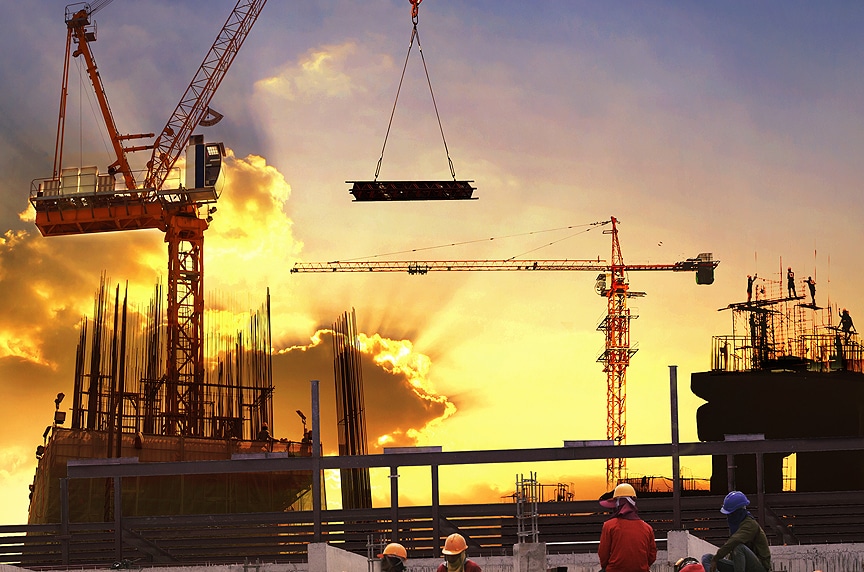
Adam Savage, of MythBusters fame, once said: “Of course, I love tools. I also love arranging them, to the point where I came up with a name for my organizing metric: first-order of retrievability.”
This organization tactic focuses on solving two main problems:
- Not having the right tools for the job. Or worse, knowing that you have them, but not being able to find them when you need them.
- Having a tool kit on hand that has everything you might need—just like Batman’s utility belt.
As you can imagine, construction is one of the biggest industries that can benefit from this type of organizational model. Our salespeople visit a lot of construction sites across the country and encounter frustrated safety and job supervisors struggling with “first-order retrievability.” They struggle to catalog and organize their lifting and rigging equipment and corresponding inspection records.
In this article, we’ll identify and discuss a number of different lifting and rigging challenges we’ve encountered while working with our customers in the construction industry. Our goal is to expose you to some of the solutions that are available for maintaining, storing, inspecting, and organizing your lifting gear as it travels from site to site—all while meeting OSHA and ASME compliance requirements.
Challenge #1: Lifting and Rigging Equipment Never Gets Inspected
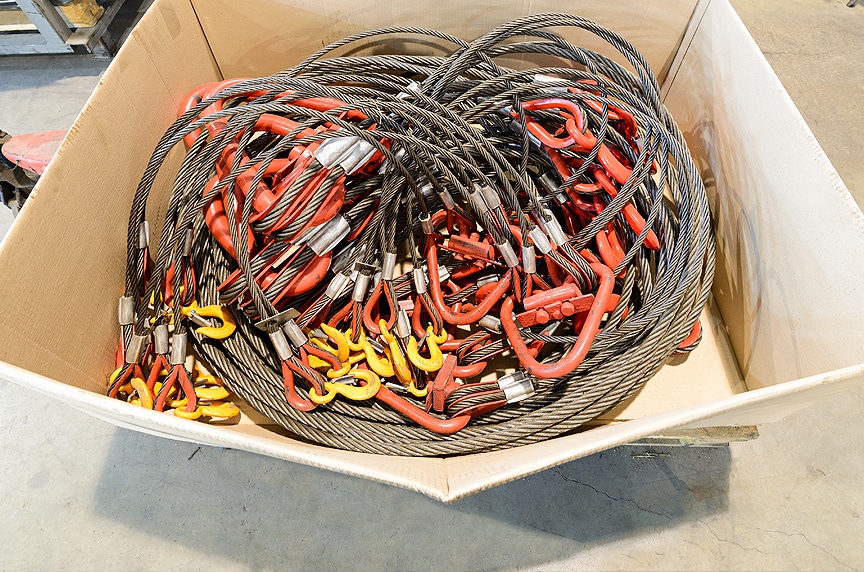
Today, the construction industry is booming. Construction crews work to finish one job on time only to pack up and move right on to the next.
Packing up all of your rigging gear at the end of a job is kind of like the end of a long road trip. When you’re preparing for your trip, you pack meticulously—planning for all unexpected scenarios, and organizing and optimizing space within your suitcase or baggage.
When you’re ready to return home, you want to get out of dodge and end up jamming stuff wherever you can, knowing that you’ll deal with it at a later time.
Similarly, many of our customers haphazardly pack up their rigging box and send it off to the next construction site for the next crew to deal with. When business is slower, you might have a few weeks in between jobs where you can send it back to a central location to inspect and inventory all of your lifting slings, hooks, shackles, etc.
Today, with new construction projects popping up everywhere, that doesn’t happen too often. If it does make it back to the shop, there often isn’t someone there who is trained to properly inspect and inventory the rigging gear before it goes back out on the road. Essentially, you have two seemingly simple solutions:
Inspect Your Lifting and Rigging Gear Before it’s Sent to the Next Job Site
The first option would be to inspect the gear before it’s sent out to a job site. Starting a job with organized, inventoried, and inspected rigging equipment is always the best-case scenario and helps keep you in compliance with industry standards.
Think back to when you were a kid and it was the first day of school. You knew you had a lot of work ahead of you but you somehow felt better and more prepared because your mom stocked you up with new binders, number two pencils and that cool eraser that erased pencil with one side and the other side that ripped through your paper trying to erase pen.
The point is, having the proper equipment in good working order gives you the proper mental outlook to get the job done.
Inspect Your Lifting and Rigging Gear When it Arrives On Site
The other option is to inspect all of your rigging equipment when it shows up on site. When you get to a job site early, you often hear, “the rigging box will be here in the next few weeks” and “it should have everything we need.”
Invariably, the box comes with expectations of a rigging cornucopia ready to help get the job done. What actually arrives, is a box packed by the last crew who wanted to get the heck out of dodge. Often, the equipment is in poor shape—unfit for use and lacking any documentation.
Fortunately, you can bring a qualified third-party inspector on to the job site to help you sort through your rigging equipment. They can systematically work through all of the gear in the rigging box and inspect each sling, hook, or shackle and also provide the documentation you need to meet OSHA inspection requirements. Third-party inspectors will even come to your shop, yard, or tool room to inspect and document the condition of your gear.
One of the value-added services we can provide is a rigging inspection and repair bin that you keep on site. Any piece of gear that is damaged, or in questionable condition, can be tossed into one of the supplied bins and then we take care of the rest:
- We schedule pick up of your bins of slings, hoists, lever tools, fall protection products and/or any rigging hardware you may have
- We drop off empty bins when we pick up the full ones
- We inspect your rigging gear
- We electronically send you detailed inspection reports to keep you OSHA compliant
- We quote your repairs or replacements to keep your equipment at optimal levels
- We return your inspected, repaired, and new equipment back to you
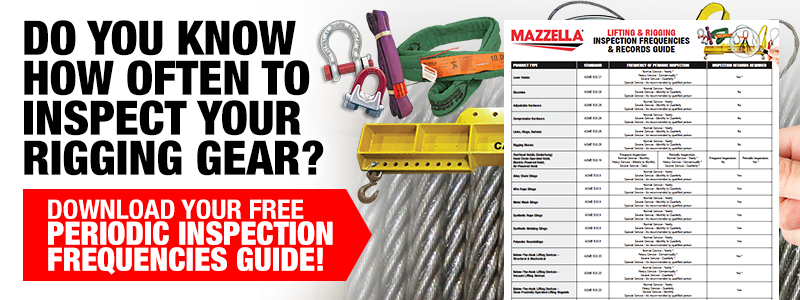
Challenge # 2: Construction Sites Don’t Have the Rigging Gear They Need
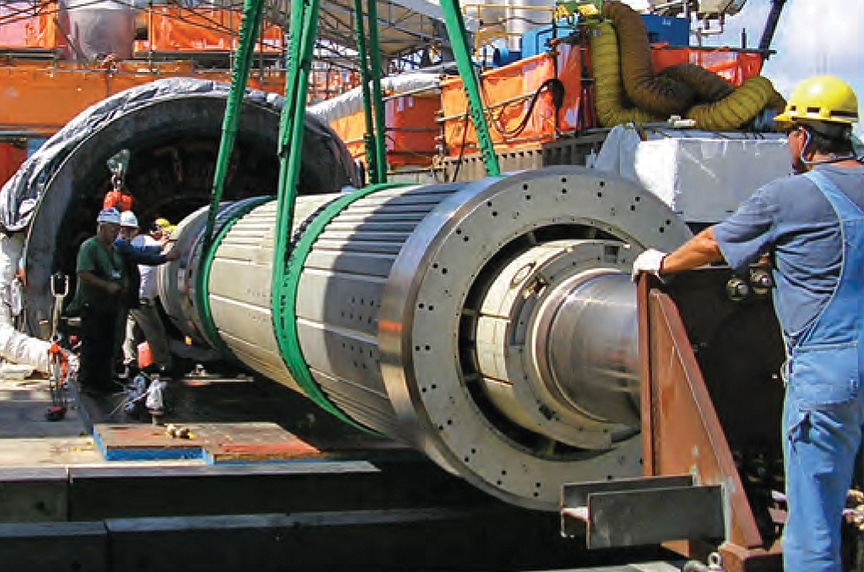
So, the job gets underway and whatever rigging equipment is sent from the last job site is what you have to start with. Inevitably, the rigging box will never contain everything you need for your project. We work with many construction companies at the beginning of a job and continue to work with them throughout the project to fill gaps in their current rigging inventory.
We have mobile teams at the ready who can inspect, document, and re-stock:
- Wire rope slings, chain slings, and synthetic slings
- Lever tools
- Chain hoists
- Shackles, hooks, turnbuckles
- Tie-down straps
- Personal fall protection equipment
- And more!
Equally important are the complex lifts you have to make that may be particular to the job at hand. Chances are you may not have what you would need for critical lifts such as a refinery module, a furnace lid, or a power plant turbine.
Part of the process of supplying a job site with rigging equipment is to understand what special and heavy lifts the contractor has for their job. Often times, the heavy or unusual lifts are later in the contractor’s construction sequence. When a rigging equipment supplier gets contacted about products needed to perform a critical lift, this usually means that a large piece of equipment, or steel fabrication, is in route to the job site.
Preferably, you would have “first-order of retrievability” with equipment needed for those special and heavy lifts. These lifts are usually the most labor and capital intensive lifts of the entire project. For these white-knuckled lifts, it’s preferable for a Lifting Specialist to talk to a Heavy and Special Lifts Engineer if one is available to work with.
Even if the contractor is not ready to make any final decisions, or issue purchase orders for future lifts, a rigging equipment supplier can work in the background to source products based on project specifications and parameters. If the special lifts are being sub-contracted to another company such as a crane rental or erection company, an experienced rigging supplier is often happy to work with them (and probably already has in the past).
Challenge #3: Construction Sites Don’t Have Stocked Rigging Boxes Available
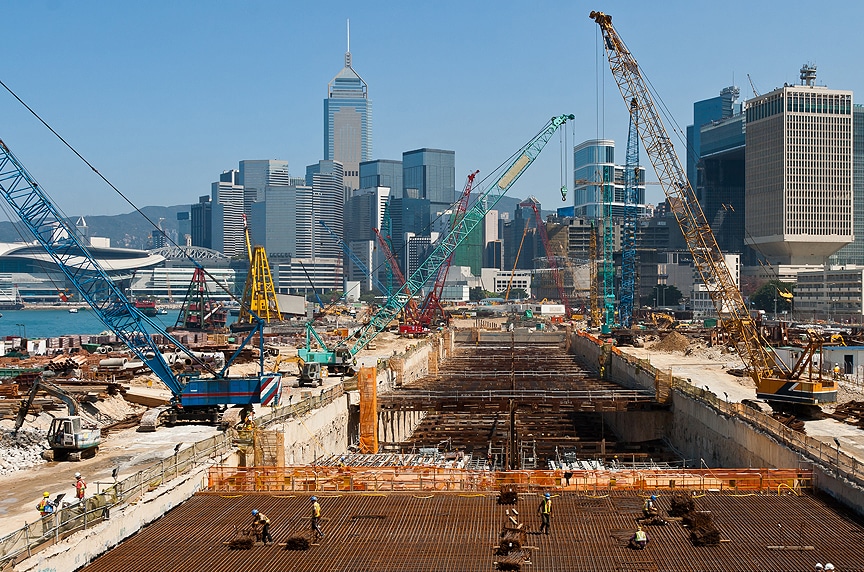
Did you know that you can purchase fully-stocked and furnished rigging boxes built to your specifications? Shelving, lighting, air conditioning, and electrical connections are all options that can be included with a new or refurbished rigging box.
We love putting together new rigging boxes; it gives our customers and fabricators the opportunity to be creative. It’s also a good sign for the construction industry when all available assets are out in the field and there is still demand!
Challenge #4: New Construction Employees Need Rigging Training
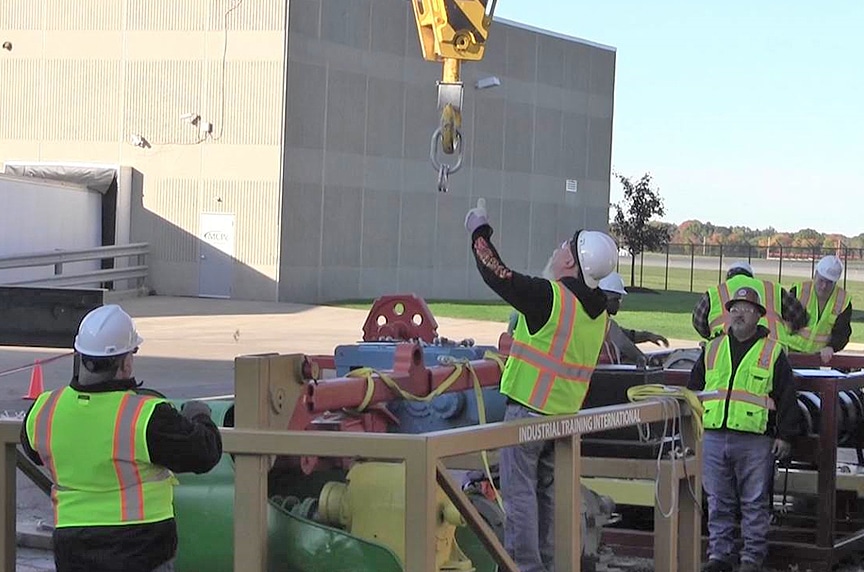
In the construction industry, the labor market is tight—with top contractors always in search of talented and hard-working people to build this country’s buildings, roads, and infrastructure. While there is a need for skilled labor, there is a greater need for employees joining the construction workforce that need to be trained on how to properly and safely perform overhead lifts.
In recent years, we’ve seen construction companies make huge strides in developing internal safety training programs for their employees. It’s great to be at a job site early in the morning and see a supervisor leading the daily safety meeting and tool box talks. Not so long ago, this was a rarity.
New construction workers need to be trained to work in the safest possible environment. Of course, the “seasoned” workers shouldn’t be left out of training either. Why? Because even the most seasoned lifting and rigging veterans can be misinformed or misguided in how to rig a load or perform a safe overhead lift.
As hard-working and knowledgeable as they are, they too often draw a line between the way you are supposed to do it safely and the real way you need to do it to get the job done.
Fortunately, we offer turnkey lifting and rigging training modules that address a number of topics that suit new employees as well as seasoned construction professionals. These training modules cover topics, including:
- Identifying and Managing Risk
- Planning Every Lift
- Rigging Techniques and Best Practices
- Rigging Hardware: Care, Use, and Inspection
- Wire Rope: Care, Use, and Inspection
- Lifting Slings: Care, Use, and Inspection
- Load Control
- Design and Use of Custom Below-the-Hook Lifting Devices
We know your training time is limited and you have a building schedule to meet—which is why we break up our training modules into smaller sessions. These training modules can be picked from a menu of “à la carte” options that suit your training requirements.
Most often, our training programs are used to supplement a contractor’s current safety training. Sometimes, the contractor wants to add focus or more detail to their lifting or fall protection training. Other times, it breaks up the normal training routine by bringing in a fresh voice and different perspective. And of course, other times it’s just to give an often overburdened safety supervisor a break.
Safety and training are paramount to a job site, but finding the time and material to do it can be a struggle for contractors. There is not a day that goes by when our trainers aren’t out working with contractors and safety professionals, teaching safe lifting and rigging principals and habits.
Wrapping it Up
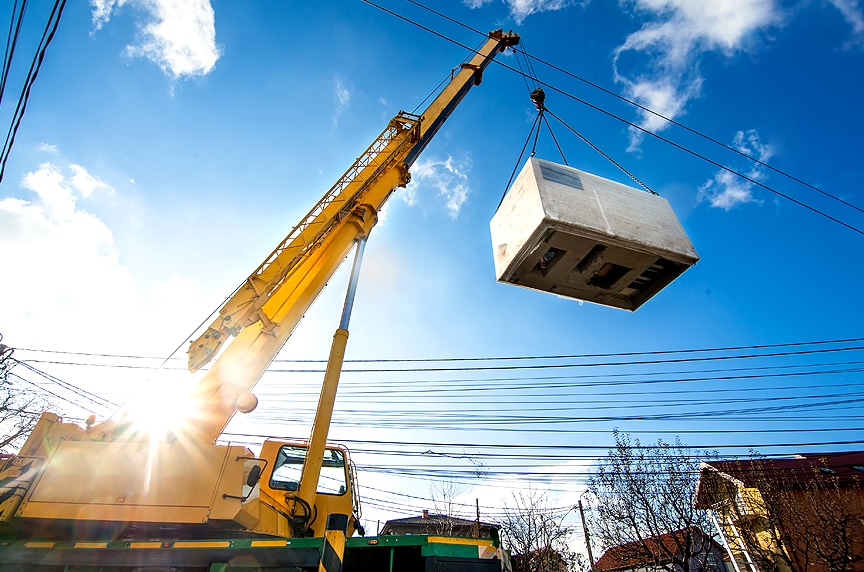
Winston Churchill said, “Give us the tools and we will finish the job.”
We understand there are many challenges that contractors face on every job site and we certainly can’t help with all of them. But, we can help with supplying the lifting, rigging, inspection, and training tools that you may need to finish the job safely and efficiently.
If you’re struggling to keep your rigging equipment organized, need advice on the right gear to use, or want to invest in further training, then feel free to contact one of our Lifting Specialists. They’d be happy to come on site and put an action plan together to help solve any or all of the following challenges you face, including:
- Keeping your rigging equipment supplied and organized
- Providing application-specific advice on the right tools to use for the job
- Providing periodic rigging equipment inspection and documentation
- Providing training on best practices, care, usage, and inspection for lifting and rigging gear
There’s no better feeling than knowing that your employees are equipped with the right tools they need to do the job, they’re properly trained on how to use their gear and make safe lifts, and that all of the gear is well-organized and in compliance with industry inspection requirements.
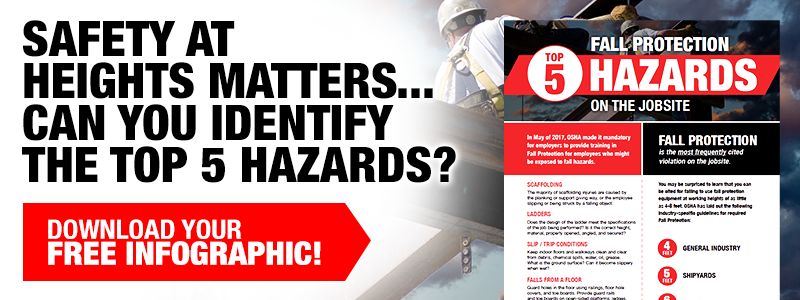
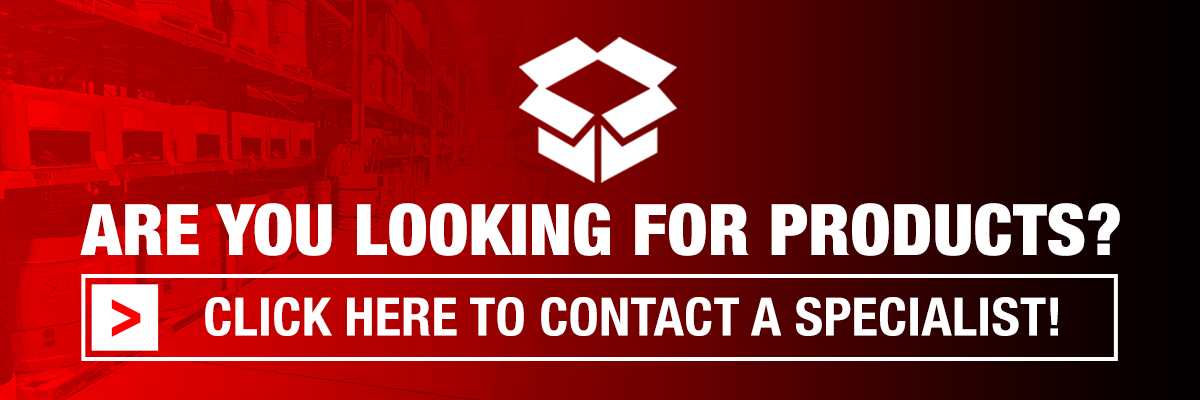
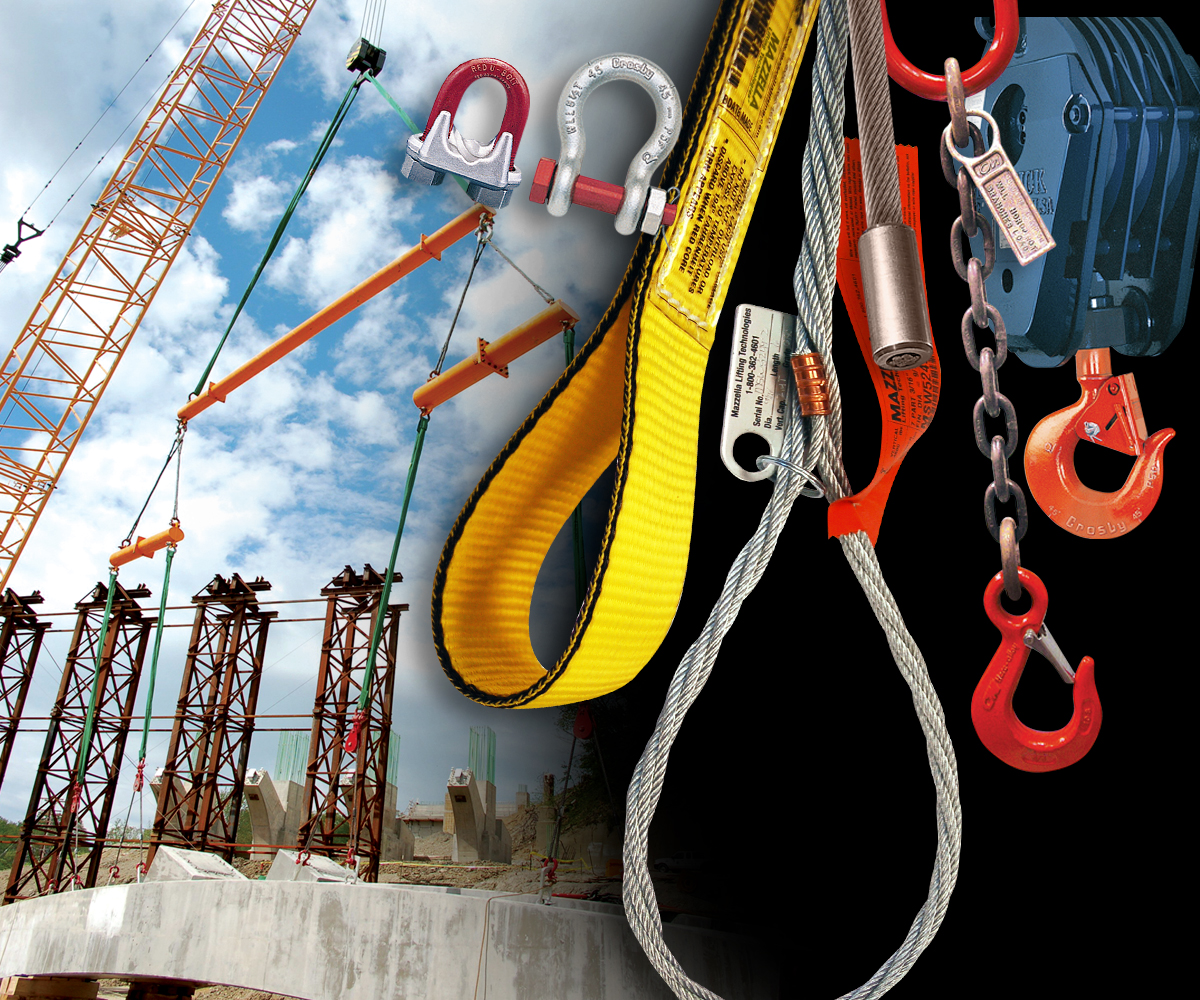
Lifting & Rigging Products
Are you looking for lifting and rigging products that you can trust for your next project? We partner with the largest manufacturers in the world to stock and provide you with the products you need to make your next lift, including all types of lifting slings, rigging hardware products, wire rope, hoists, hoist parts, pullers, and other related distributed products.
Contact us today to get the lifting and rigging products you need!
Learn more about our selection of lifting and rigging products!
Copyright 2018. Mazzella Companies.