What Is the Best Kelly Line Rope for a Foundation Drilling Rig?
Swapping out or replacing a Kelly line wire rope is one of the biggest causes of work stoppage and equipment downtime on a drilling rig system. Because of the nature of drilling and the exposure to extreme environmental conditions, a Kelly line wire rope is often subjected to corrosion, degradation, fatigue, and broken wires and birdcaging.
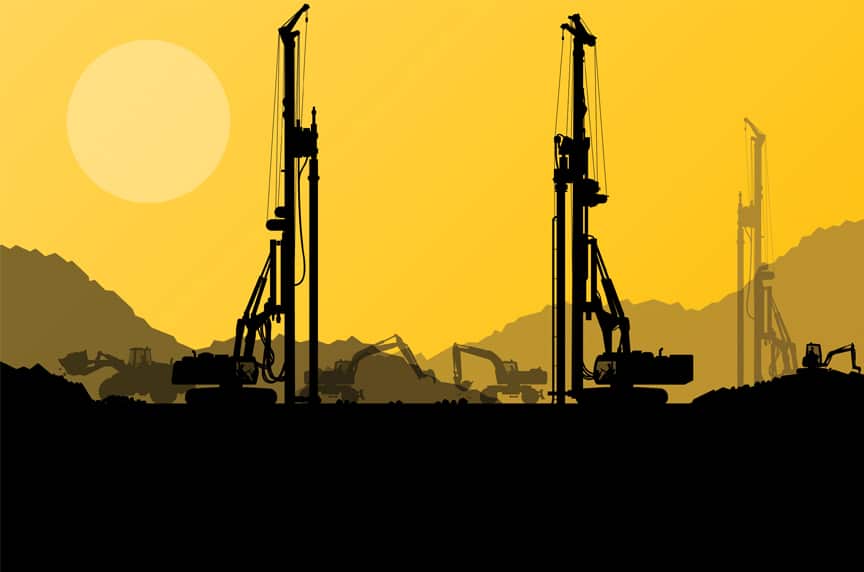
If you work in the marine construction, heavy highway and bridge construction, or foundation and geotechnical drilling industries, you understand how frustrating it can be to stop work on a project because of equipment downtime due to damaged kelly line rope.
Swapping out or replacing a Kelly line wire rope is one of the biggest causes of work stoppage and equipment downtime on a drilling rig system. The wire rope used to lift and lower the Kelly bar, is used to drill large diameter, deep foundation holes that are filled with concrete in preparation of large-scale construction projects.
The Kelly line is one of the most used and abused components of a drill rig system because of the nature of drilling and the exposure to extreme environmental conditions. Because of this, a Kelly line wire rope is often subjected to accelerated corrosion, degradation, fatigue, and broken wires and birdcaging.
At Mazzella, we have a large inventory (and a wealth of knowledge) of high-performance crane rope and wire rope for every major crane manufacturer. Each of our rigging locations stocks wire rope in all sizes, specifications, and constructions that can be used on:
- Overhead cranes
- Mobile cranes
- Tower cranes
- Drill rig systems
We understand that selecting the right type of Kelly line rope is essential for keeping your projects on schedule and within budget. In this article, we’ll explain why the most commonly used Kelly line ropes aren’t necessarily the best for geotechnical and foundation drilling applications.
We’ll also introduce you to our preferred lines of replacement Kelly line rope that may be able to get you up to three times the service life compared to other ropes on the market!
What to Look for in a Replacement Kelly Line Rope
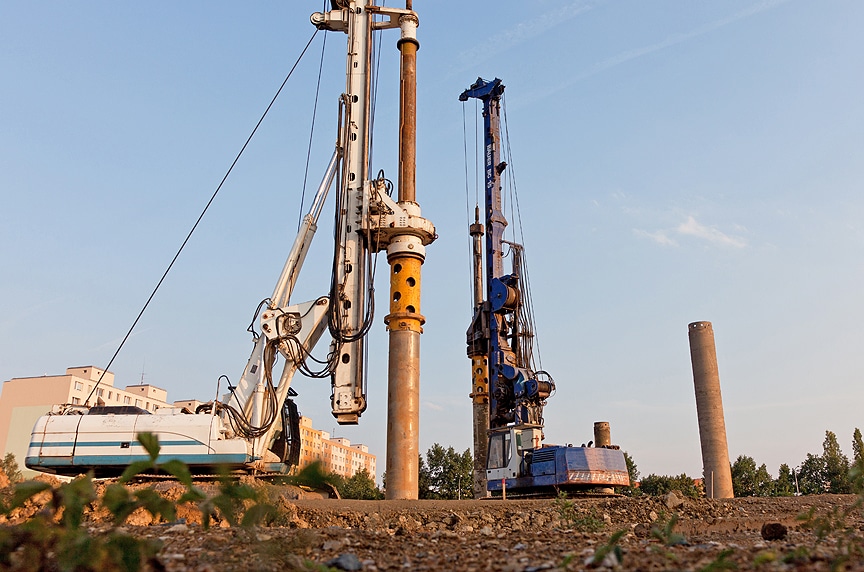
When we’re talking about Kelly lines on geotechnical and foundation drilling systems, we’re talking about large diameter drilling rigs, like:
- Liebherr LB’s
- Bauer BG’s
- Soilmec SR’s
- IMT
- CZM
- Casagrande
In the United States, it’s common for end-users to replace the Kelly line using compacted 6-strand rope, 35×7 rotational-resistant wire rope, or honestly, whatever they can find that is closest in diameter to the rope they pulled off their machine. They’ll typically order a length of rope, add some wire rope clips and a thimble, and call it a Kelly line.
The problem with this mindset is that not all ropes are designed for the rigors and environmental stresses of drilling applications. When you connect a Kelly line to the Kelly bar, most of the impact, vibration, and torque gets transferred to the wire rope that’s lifting and lowering that Kelly bar.
Over time, and often quite quickly, this type of abuse can chew up a wire rope that wasn’t designed to withstand that type of abuse. When that setup fails, you can lose your Kelly bar down hole due to rope failure.
35×7 rotation-resistant wire rope is commonly used on pile drilling rigs. They’re popular in construction applications because they’re considered “soft ropes”—meaning they spool easily and wrap smoothly around the drum on a tower crane or mobile crane.
However, when you’re using these types of ropes for geotechnical applications—specifically for the Kelly line—a “soft” rope is a bad thing. They’re too soft and malleable, which leads to all types of problems, including:
- Corrosion and degradation
- High strands
- Birdcaging
- Broken wires and excessive fatigue
We often see contractors buying based on price and trying to match a rope to the closest diameter of the OEM rope that was supplied with their drilling equipment. This can be problematic because there isn’t any consideration given to the minimum break force, or to the termination efficiency.
The Wire Rope Users Manual defines “efficiency” as the ratio of a wire rope’s actual breaking strength and the aggregate strength of all individual wires tested separately—usually expressed as a percentage.
Some end-users don’t even consider the termination efficiency and just use wire rope clips without a splice or swage to terminate the wire rope! Without proper end termination, a rope gets fatigued quickly and more easily—leading to more frequent birdcaging and broken wires. This is a vicious cycle that will continue to repeat itself and result in costly equipment downtime and delay a construction schedule.
What Are the Best Kelly Line Replacement Ropes for Foundation Drilling?
Below are some of the best types of wire rope you can use for Kelly line and foundation drilling applications:
Teufelberger TK16 Wire Rope
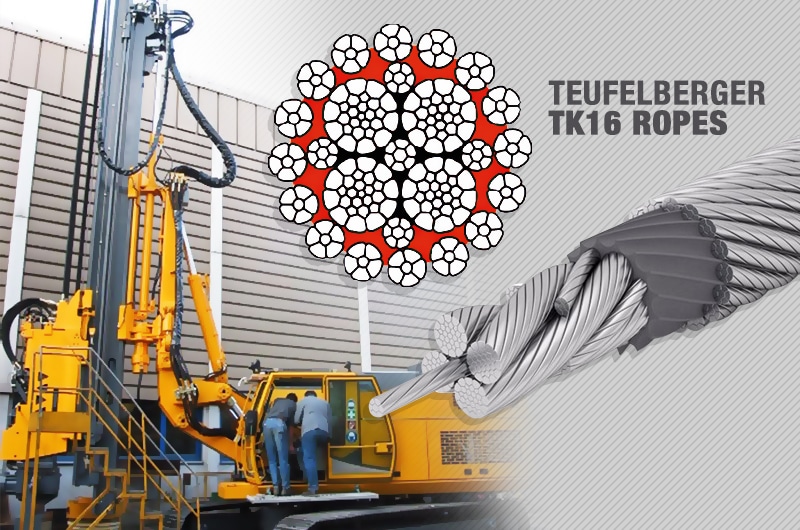
Teufelberger’s TK16 product line offers a high-performance steel wire rope that has an advanced design that excels in geo-foundation and technical drilling applications. It features high flexibility and is extremely durable to withstand the rigors of deep foundation drilling.
The TK16 ropes are a great option for Kelly lines because they’re resistant to environmental influences and the ingress of dirt due to a PLASTFILL® core that acts as a shock absorber and as a lubricant for the inner rope.
Teufelberger’s TK16 wire rope also features excellent spooling characteristics and high dimensional stability under lateral pressure—even when used in multi-layer spooling operations.
The TK16 ropes are engineered to withstand high breaking forces and to be resistant to rotation and torsion. This extra engineering leads to a longer service life—even in the case of shock loads—due to the 4-strand design of the inner rope.
Additional Specifications and Benefits of Teufelberger TK16 High-Performance Wire Rope:
- Galvanized for added resistance to corrosion and degradation
- PLASTFILL® core acts as a shock absorber and a lubricant for inner rope
- Four large inner strands help keep stability in the rope, resulting in less fatigue and reducing high strands, birdcaging, and broken wires
- A flashing die is used to press a swage to European standards. This allows for a higher minimum break force and minimizes fatigue—resulting in longer service life of the rope and full strength from turn back on the rope eyes.
- TK16 ropes utilize thimbles designed to European DIN standards. These offer a larger D/d ratio, which helps provide relief on the eye itself—reducing fatigue and “crown” breaks.
- Annealing machines are used to provide a clean termination of the end of the wire rope. This allows the rope to fit into the dead end of the drums very cleanly and efficiently.
Bridon Dyform 34LR / 34LR PI Wire Rope
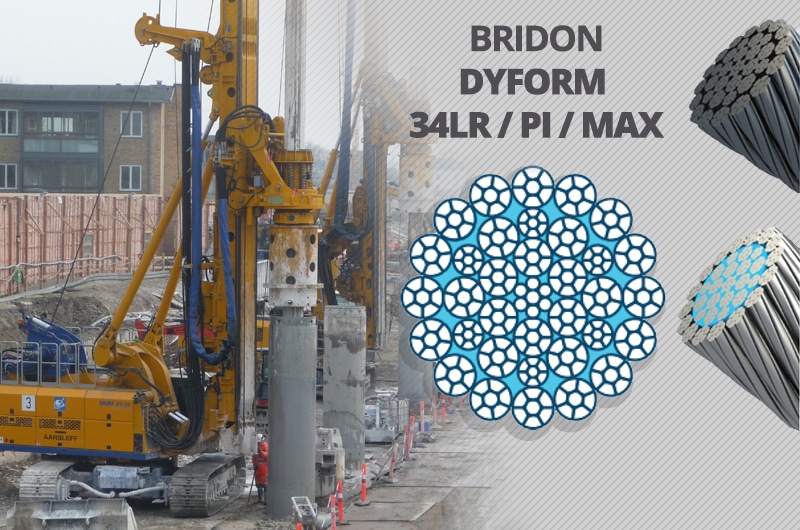
Bridon’s Dyform 34LR is a high-performance compacted low-rotational rope that combines varying multi-strand rope designs to achieve excellent rope rotation resistance in high-lift operations. It also includes the option for a plastic layer (PI) between the inner and outer part of the rope.
Additional Specifications and Benefits of Bridon Dyform 34LR Wire Rope:
- Excellent rotation resistance
- Highly efficient due to its flexibility
- Stable rope construction
- Higher bending fatigue performance
- Suitable for single part and multi-part reeving
- Suitable for single part reeving of an unguided load
Bridon Dyform 34LR MAX Wire Rope
Bridon’s 34 LR MAX wire rope is a high-performance compacted low rational rope that consists of varying multi-strand rope designs which have undergone a final rope compacting process.
Additional Specifications and Benefits of Bridon Dyform 34LR MAX Wire Rope:
- Highest breaking strength
- Excellent rotation resistance
- Improved crush resistance
- Accurate diameter and tight diameter tolerance
Bridon Dyform 28 MAX Wire Rope
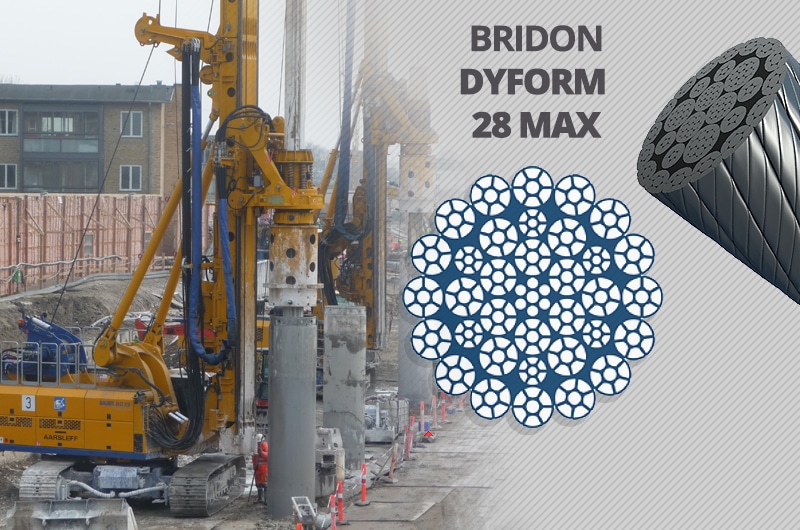
Bridon’s Dyform 28 MAX is a high performance compacted rotational resistant rope specifically designed for demanding applications such as deep foundation works, including piling and drilling rigs, as well as diaphragm walling. It also includes the option for a plastic layer (PI) between the inner and outer part of the rope.
Additional Specifications and Benefits of Bridon Dyform 28 MAX Wire Rope:
- Superior crushing resistance
- Excellent wear resistance
- Robust and stable rope construction
- Tightly controlled diameter tolerance
Bridon 50 DB Series Wire Rope
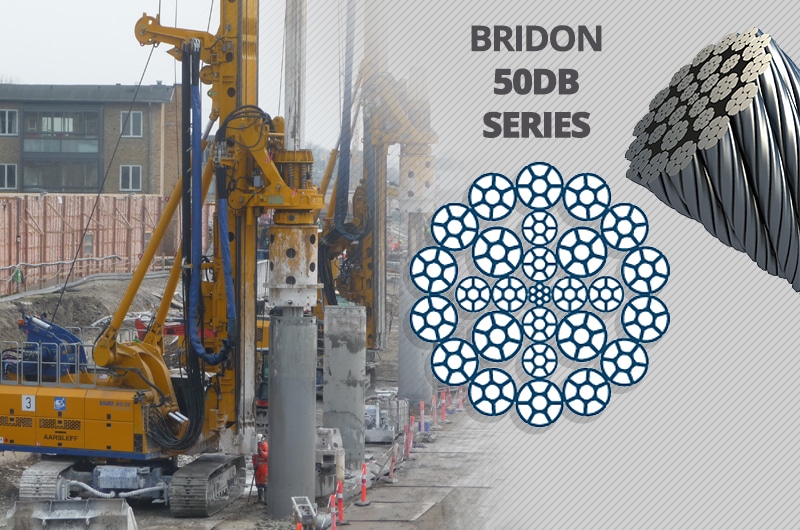
Bridon’s 50 DB Series wire rope has a rotation resistant rope construction consisting of an inner art with an outer layer of strands spun in the opposite direction.
Additional Specifications and Benefits of Bridon 50 DB Series Wire Rope:
- Rotation resistant
- Good wear characteristics due to its smooth exterior profile
- High-category breaking strength
- Recommended for limited lifting heights only
Bridon Dyform 18 PI Wire Rope
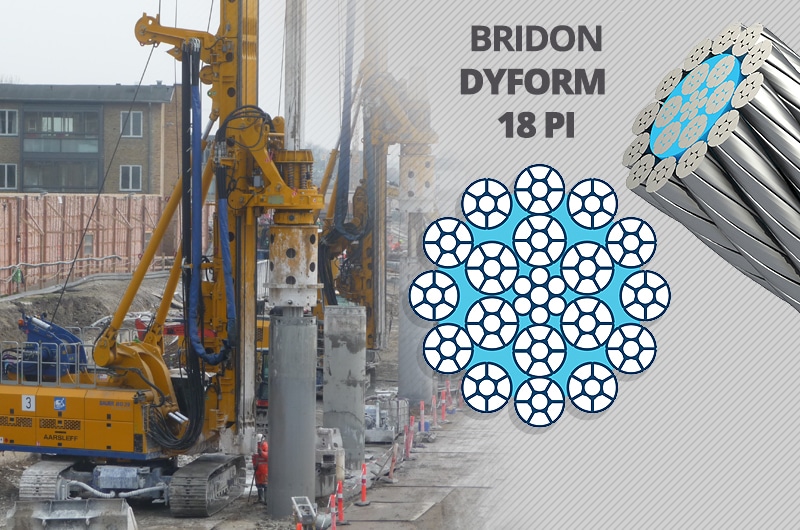
The Bridon Dyform 18 PI series wire rope is a high performance compacted rotation resistant rope which incorporates a plastic layer between the inner and outer part of the rope.
Additional Specifications and Benefits of Bridon Dyform 18 PI Wire Rope:
- Good wear characteristics due to its smooth exterior profile
- Improved bending fatigue performance
- Robust and stable rope construction
- Diameter stability – requirement of multi-layered spooling
Bridon 35LS Wire Rope
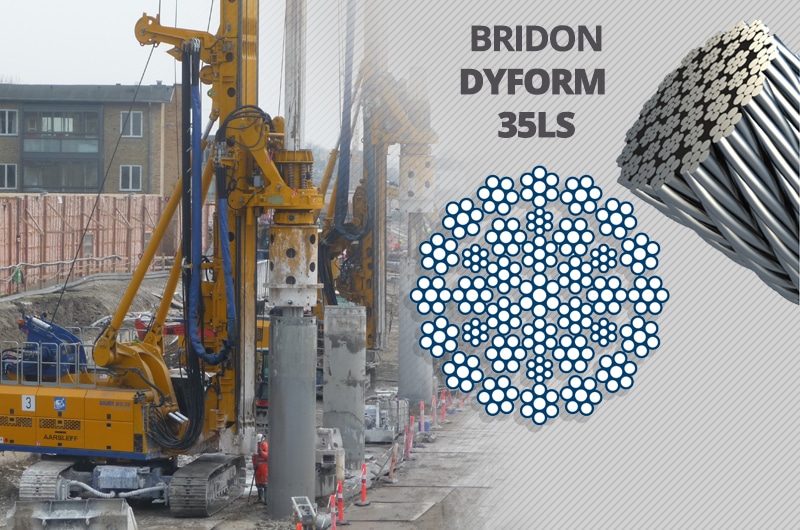
Bridon’s 35 LS wire rope is a conventional low rotation-resistant rope consisting of three layers of strands—the inner two layers spun in the opposite direction to the outer layer of strands. This rope is manufactured in accordance with EN 12385.
Additional Specifications and Benefits of Bridon 35LS Wire Rope:
- Rotation resistant
- Flexible rope construction
- For use on single layer drums only
WireCo / Union XLT4 Wire Rope
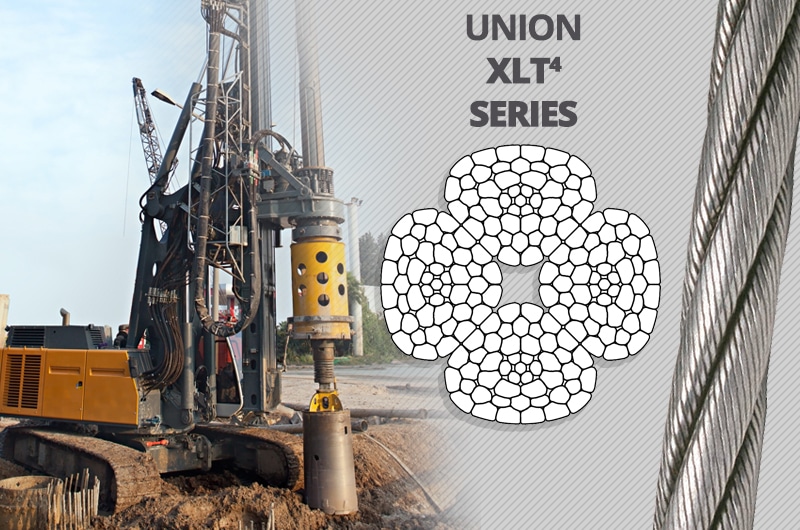
Union’s XLT4 wire rope features a unique design and construction that is different in appearance and feel compared to other wire ropes. It packs more high tensile steel wire into the rope’s diameter—giving the XLT4 wire rope one of the highest strength to diameter ratios ever achieved.
XLT4 wire rope is specially designed to provide very low torque, a high minimum breaking force, and high-resistance to wear in multi-layer spooling.
Additional Specifications and Benefits of Union XLT4 Wire Rope:
- Low torque / high strength
- Can be used with a swivel
- Lower cost than 35×7 construction rope
- Can be used at design factor of 3.5 to 1
WireCo / Union Flex-X 6 Wire Rope
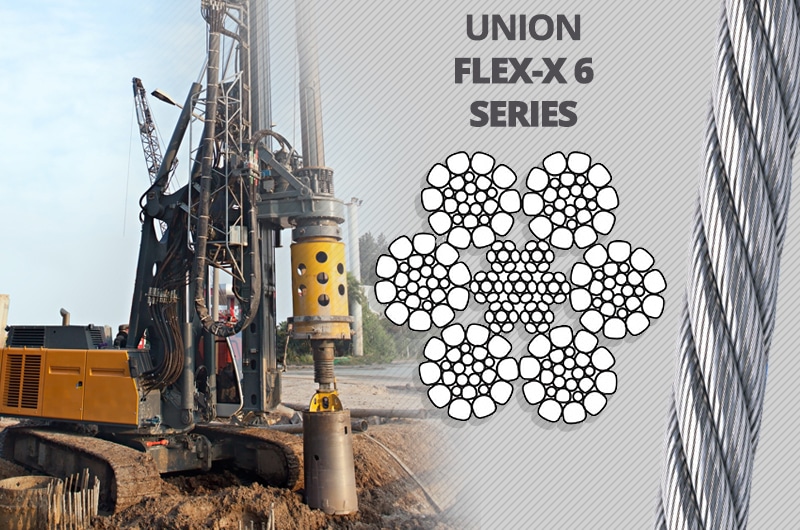
Union’s Flex-X 6 wire rope provides greater surface area and more steel per given diameter than conventional 6 strand ropes.
Additional Specifications and Benefits of Union Flex-X 6 Wire Rope:
- Superior performance
- Increased service life
- Less sheave and drum wear
WireCo / Union 6×26 WS IWRC
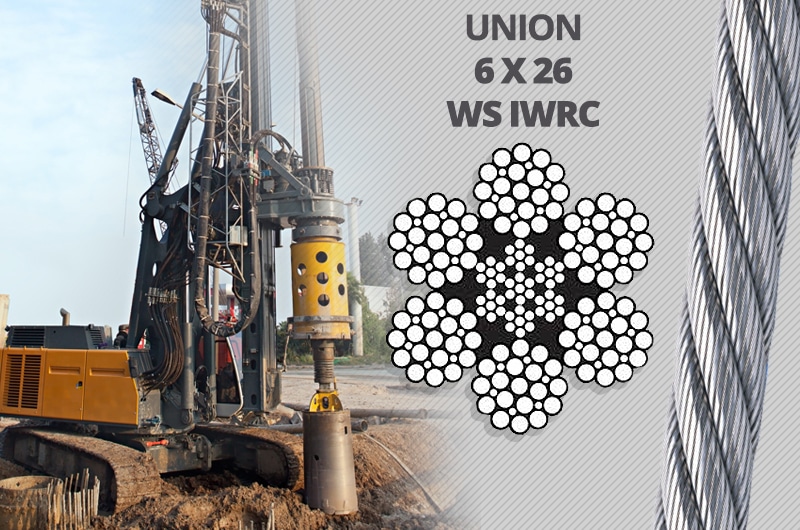
Union’s 6×26 WS IWRC wire rope has better resistance to abrasion than 6×25 FW. It features a compact construction with solid support for the wires; therefore it has a higher resistance to crushing. The number and size of the inner wires provide added stability of the strand for higher fatigue resistance.
Additional Specifications and Benefits of Union 6×26 WS IWRC Wire Rope:
- Higher abrasion and fatigue resistance compared to 6X25 FW construction ropes
- Can be used in any application where 6×25 FW rope is used
Wrapping it Up
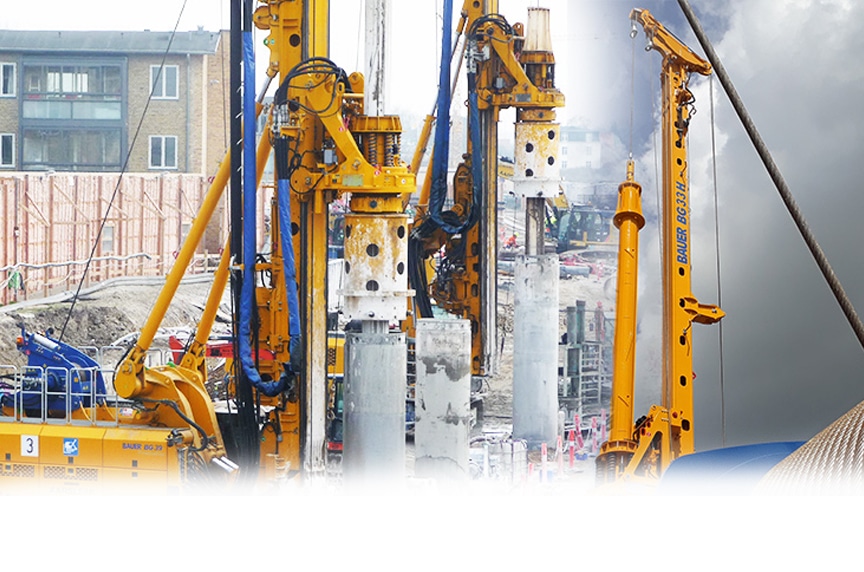
At Mazzella, we take the guesswork out of what wire rope to use on your drilling equipment and machinery. We take a lot of pride in the knowledge our team has of high-performance wire rope and crane rope specifications.
We have a detailed catalog of drilling equipment and machinery specifications and we’ll match the thimble sizes to ensure that your new rope fits the swivel on your specific Kelly bar for a direct replacement solution for your specific drill rig.
We have locations all across the eastern half of the United States and offer next-day delivery for emergency and critical crane rope service. We are one of the few suppliers in the United States with exclusive access to inventory of specialized high-performance wire rope.
We also partner with many other OEM suppliers, including:
- Bridon-Bekaert / Wire Rope Industries
- WireCo / Union / Casar
- Wire Rope Works / Bethlehem Wire Rope
If you’re struggling with keeping your Kelly line in service, or you’re losing Kelly bars down hole due to rope failure, consider changing to a new supplier for your crane rope and wire rope needs. We can help minimize downtime and loss of production and get you set up with wire rope that may last up to three times longer than the rope you’re currently using!
Contact us to receive a quote or schedule a consultation with one of our Lifting Specialists.