What Are the Seven Primary Characteristics of Wire Rope?
Each rope construction has been established to produce a desired combination of operating characteristics which will best meet the performance requirements of the work, or application, for which that design is intend and each rope construction is, therefore, a design compromise.
Every wire rope has its own “personality” which is a reflection of its engineered design. Each rope construction has been established to produce a desired combination of operating characteristics which will best meet the performance requirements of the work, or application, for which that design is intend and each rope construction is, therefore, a design compromise.
The best illustration of a design compromise—or best combination of desired characteristics—is the interrelationship between resistance to abrasion and fatigue resistance.
Fatigue resistance (a rope’s capability to bend repeatedly under stress) is accomplished by using many wires in the strands. Resistance to metal loss through abrasion is achieved primarily with a rope design which uses fewer and, therefore, larger wires in the outer layer to reduce the effects of surface wear.
Therefore, from a design standpoint, when anything is done to alter either abrasion resistance or fatigue resistance, both of these features will be affected.
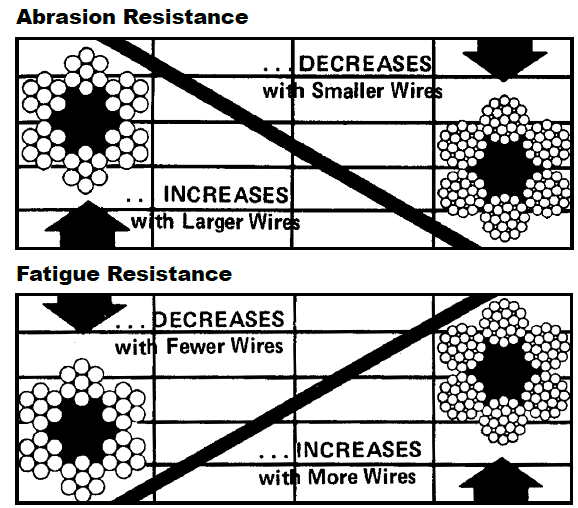
1. Strength
Wire rope strength is usually measured in tons. In published material, wire rope strength is shown as minimum breaking force. Minimum breaking force refers to calculated strength figures that have been accepted by the wire rope industry.
When placed under tension on a test device, a new rope should break at a figure equal to, or higher than, the minimum breaking force shown for that rope.
To account for variables which might exist when such tests are made to determine the breaking strength of a new wire rope an “acceptance” strength may be used. The acceptance strength is 2-1/2% lower than the minimum breaking force and ropes must meet or exceed this strength.
The minimum breaking force applies to new, unused rope. A rope should never operate at, or near, the minimum breaking force. During its useful life, a rope loses strength gradually due to natural causes, such as surface wear and metal fatigue.
2. Reserve Strength
The reserve strength of a standard rope is a relationship between the strength represented by all the wires in the outer strands and the wires remaining in the outer strands with the outer layer of wires removed. Reserve strength is calculated using actual metallic areas of the individual wires. Since there is a direct relationship between metallic area and strength, reserve strength is usually expressed as a percentage of the rope’s minimum breaking force. Reserve strength is used as a relative comparison between the internal wire load bearing capabilities of different rope constructions.
Reserve strength is an important consideration in selection, inspection and evaluation of a rope for applications where the consequences of a rope failure are great. The use of reserve strength is premised on the theory that the outer wires of the strands are the first to be subjected to damage or wear. Therefore, the reserve strength figures are less significant when the rope is subjected to internal wear, damage, abuse, corrosion or distortion.
The more wires there are in the outer layer of a strand construction, the greater will be the rope’s reserve strength. Geometrically, as more wires are required in the outer layer of a strand, they must be smaller in diameter. This results in greater metallic area remaining to be filled by the inner wires. Separate columns are shown for standard fiber core and independent wire rope core (IWRC) ropes. For fiber core ropes, the reserve strength is the approximate percentage of the rope’s metallic area made up by the inner wires of the outer strands.
An IWRC in a rope is considered to contribute 7-1/2% to the rope’s total strength. By definition, the core is not included in the reserve strength calculation so a 7-1/2% reduction has been made for ropes with an IWRC.
Rotation resistant ropes, due to their construction, can experience different modes of wear and failure than standard ropes. Therefore, their reserve strength is calculated differently. For rotation resistant ropes, the reserve strength is based on the percentage of the metallic area represented by the core strand plus the inner wires of the strands of both the outer and inner layers.
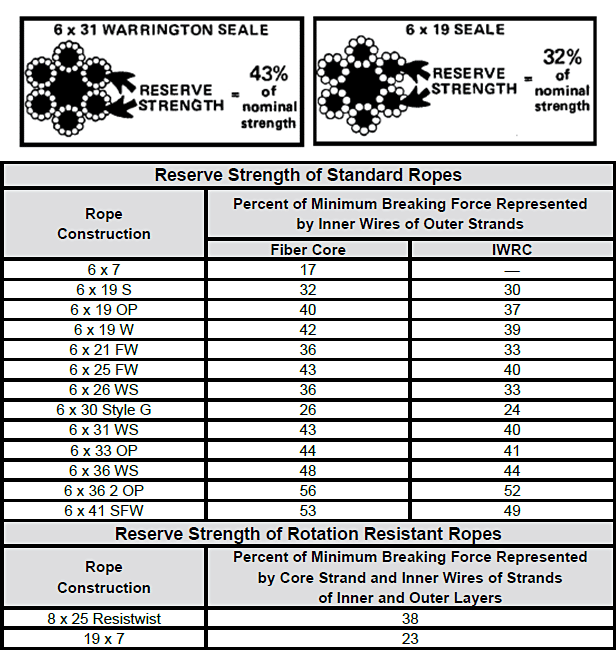
3. Resistance to Metal Loss and Deformation
Metal loss refers to the actual wearing away of metal from the outer wires of a rope, and metal deformation is the changing of the shape of outer wires of a rope.
In general, resistance to metal loss by abrasion (usually called “abrasion resistance”) refers to a rope’s ability to withstand metal being worn away along its exterior. This reduces strength of a rope.
The most common form of metal deformation is generally called “peening”—since outside wires of a peened rope appear to have been “hammered” along their exposed surface. Peening usually occurs on drums, caused by rope-to-rope contact during take-up of the rope on the drum. It may also occur on sheaves.
Peening causes metal fatigue, which in turn may cause wire failure. The “hammering”, which causes metal of the wire to flow into a new shape, realigns the grain structure of the metal, thereby affecting its fatigue resistance. The out-of-round shape also impairs wire movement when the rope bends.
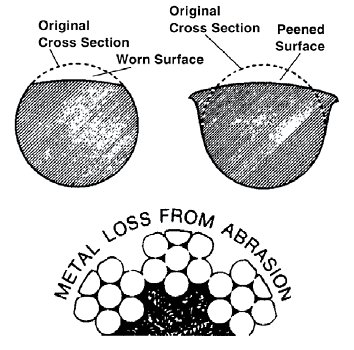
4. Crushing Resistance
Crushing is the effect of external pressure on a rope, which damages it by distorting the cross section shape of the rope, its strands or core—or all three.
Crushing resistance therefore is ability to withstand or resist external forces, and is a term generally used to express comparison between ropes.
When a rope is damaged by crushing, the wires, strands, and core are prevented from moving and adjusting normally in operation. In a general sense, IWRC ropes are more crush resistant than fiber core ropes. Lang lay ropes are less crush resistant than regular lay ropes and 6-strand ropes have greater crush resistance than 8-strand ropes.

5. Fatigue Resistance
Fatigue resistance involves metal fatigue of the wires that make up a rope. To have high fatigue resistance, wires must be capable of bending repeatedly under stress—as when a rope passes over a sheave.
Increased fatigue resistance is achieved in a rope design by using a large number of wires. It involves both the basic metallurgy and the diameters of wires.
In general, a rope made of many wires will have greater fatigue resistance than a same-size rope made of fewer larger wires, because smaller wires have greater ability to bend as the rope passes over sheaves or around drums. To overcome the effects of fatigue, ropes must never bend over sheaves or drums with diameter so small as to kink wires or bend them excessively. There are precise recommendations for sheave and drum sizes to properly accommodate all sizes and types of ropes.
Every rope is subject to metal fatigue from bending stress while in operation, and therefore, the rope’s strength gradually diminishes as the rope is used.
6. Bend-ability
Bend-ability relates to the ability of a rope to bend easily if an arc. Four primary factors affect this capability:
- Diameter of wires that make the rope
- Rope and strand construction
- Metal composition of wires and finish, such as galvanizing
- Type of rope core—fiber or IWRC
Some rope constructions are by nature more bend-able than others. Small ropes are more bend-able than big ones. Fiber core ropes bend more easily than comparable IWRC ropes. As a general rule, ropes made of many wires are more bend-able than same-size ropes made with fewer larger wires.
7. Stability
The word “stability” is most often used to describe handling and working characteristics of a rope. It is not a precise term, since the idea expressed is to some degree a matter of opinion, and is more nearly a “personality” trait than any other rope feature.
For example, a rope is called stable when it spools smoothly on and off a drum or doesn’t tend to tangle when a multi-part reeving system is relaxed.
Strand and rope construction contribute most to stability. Preformed rope is usually more stable than nonpreformed, and lang lay rope tends to be less stable than regular lay. A rope made of simple 7-wire strands will usually be more stable than a more complicated construction with many wires per strand.
There is no specific measurement of rope stability.
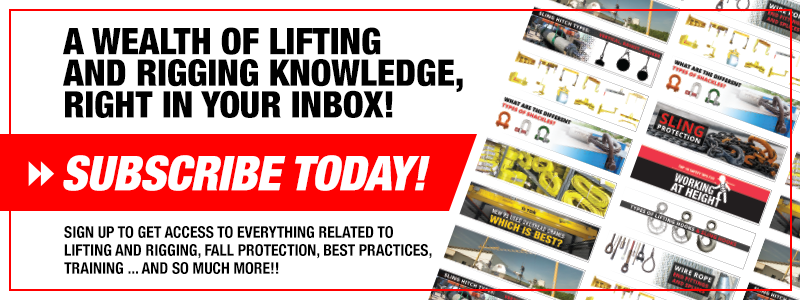