ASME B30.26 Shackle Inspection Requirements & Best Practices for Use
Are you looking for OSHA and ASME requirements for shackle inspection? Do you need to know how often and what to look for when inspecting your shackles and other rigging hardware? In this article, we help you understand shackle marking requirements, inspection frequencies, removal from service criteria, and best practices when rigging with shackles.
When rigging a load, there are a number of different products and pieces of hardware that allow you to connect the load to the crane or hoist performing the lift. But just like your slings and hooks, all rigging hardware must be inspected on a regular basis.
Fortunately, the American Society of Mechanical Engineers (ASME) created a standard related to the selection, inspection, use, and maintenance of all different types of rigging hardware. ASME B30.26 Rigging Hardware focuses on shackles, adjustable hardware, compression hardware, links, rings, and swivels, and detachable load-indicating devices.
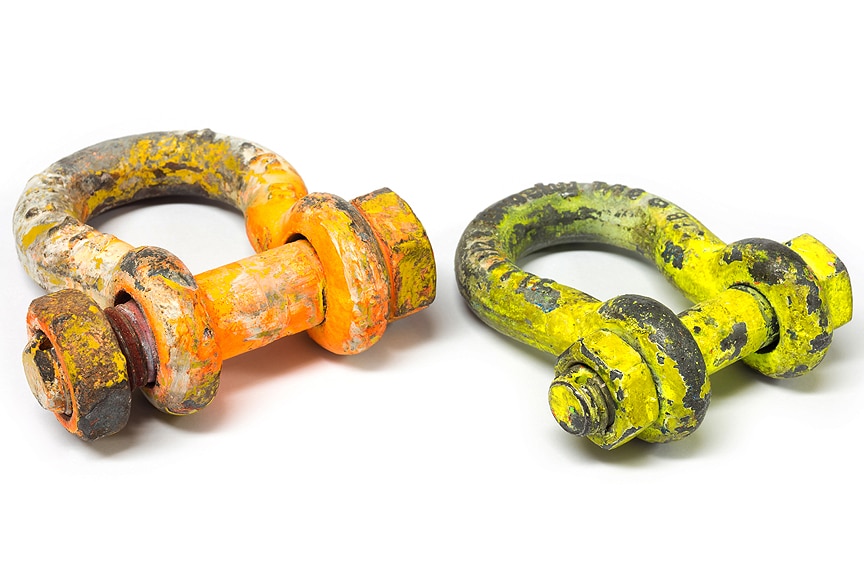
For the purpose of this article, we’ll focus just on shackles and provide you with:
- Shackle identification requirements for the body and the pin
- The types of inspection a shackle shall receive during its service life
- Shackle inspection and removal from service criteria
- Best practices for using and maintaining shackles
ASME Shackle Identification Requirements
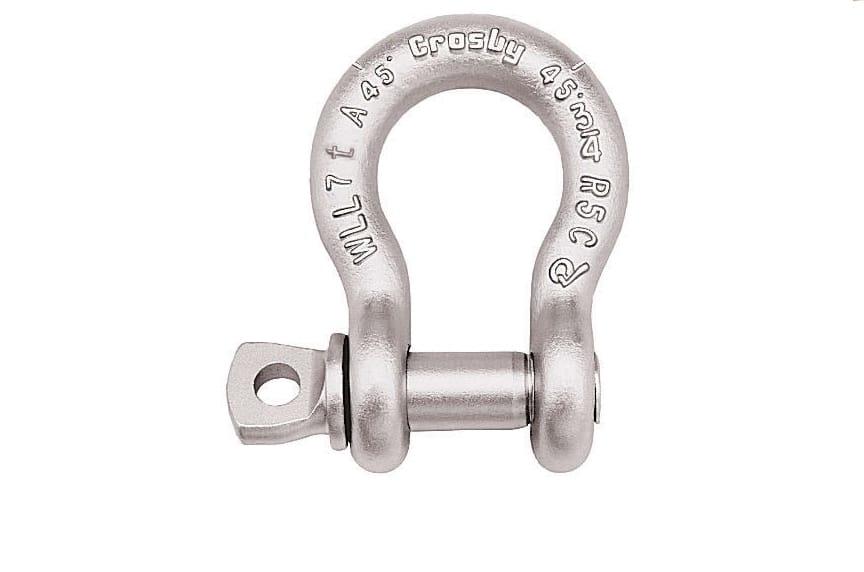
ASME B30.26 Rigging Hardware requires shackle manufacturers to have identification and/or markings on the shackle body as well as the shackle pin. These markings are required to be maintained and legible throughout the service life of the shackle.
Shackle Body Identification / Markings
Each new shackle body shall have forged, cast, or diestamped markings by the manufacturer to show:
- Name or trademark of the manufacturer
- Rated load
- Size
Shackle Pin Identification / Markings
Each new shackle pin shall have forged, cast, or diestamped markings by the manufacturer to show:
- Name or trademark of the manufacturer
- Grade, material type, or load rating
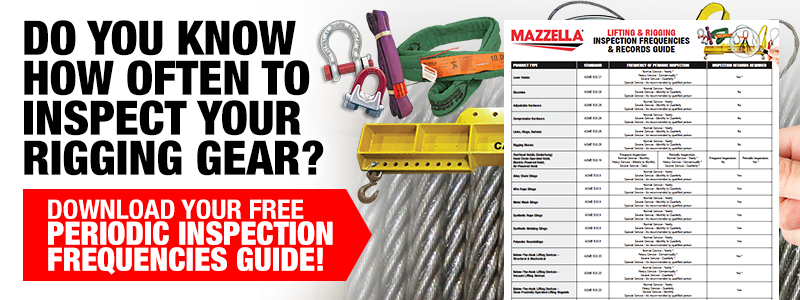
How Often Do You Need to Inspect Your Shackles?
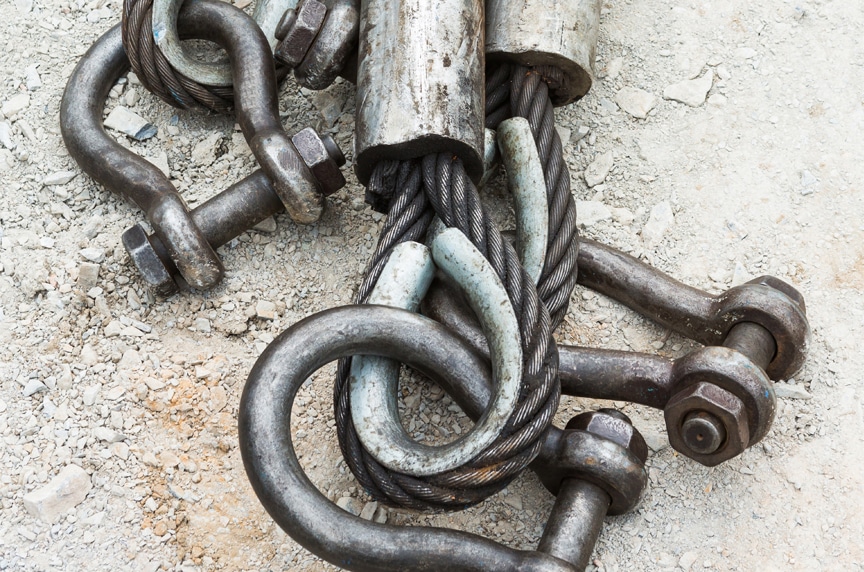
Similar to the inspection of slings, or to the inspection of hooks, all shackles need to be inspected on a regular basis. Below, we will address the three types of ASME shackle inspections that will occur throughout the service life of a shackle:
Initial Inspection
Prior to use, all new, altered, modified, or repaired shackles shall be inspected by a Designated Person to verify compliance with the applicable provisions of ASME B30.26 Rigging Hardware. Written records of an initial inspection are NOT required.
Frequent Inspection
A visual inspection shall be performed by the user or other Designated Person each day and before each use. Rigging hardware in semi-permanent and inaccessible locations where frequent inspections are not feasible shall have periodic inspections performed.
Conditions listed under Removal Criteria, or any other condition that may result in a hazard shall cause the shackle to be removed from service. Shackles shall not be returned to service until approved by a Qualified Person. Written records of frequent inspections are not required.
Periodic Inspection
A complete inspection of the shackle shall be performed by a Designated Person. During an ASME shackle inspection, the shackle shall be examined for conditions listed under Removal Criteria and a determination made as to whether they constitute a hazard.
Periodic inspection intervals shall not exceed 1 year and periodic inspection frequency should be based on:
- Frequency of shackle use
- Severity of service conditions
- Nature of lifting or load-handling activities
- Experience gained on the service life of shackles used in similar circumstances
Guidelines for periodic inspection intervals:
- Normal Service – Yearly
- Severe Service – Monthly to Quarterly
- Special Service – As recommended by a Qualified Person
Written records of periodic inspections are NOT required.
ASME B30.26 Shackle Inspection Criteria
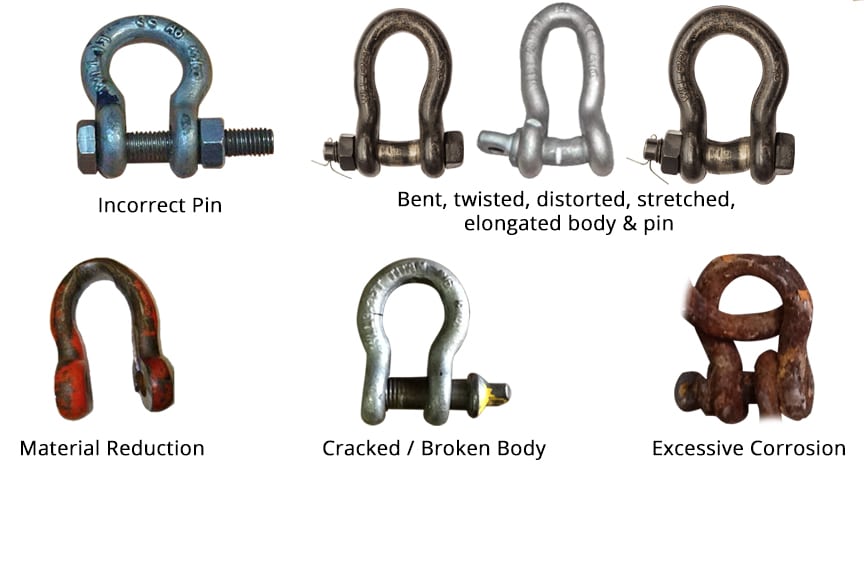
The goal of a rigging inspection is to systematically observe the condition of your lifting and rigging equipment. After a rigging inspection, you’ll better understand if your shackles are properly marked and if the general overall condition of the equipment meets the ASME B30.26 Rigging Hardware requirements.
ASME Shackle Inspection: Removal from Service Criteria
ASME states that shackles may be removed from service if damage such as the following is visible after an inspection. Shackles shall only be returned to service when approved by a Qualified Person:
- Missing or illegible manufacturer’s name or trademark and/or rated load identification
- Indications of heat damage, including weld splatter or arc strikes
- Excessive pitting or corrosion
- Bent, twisted, distorted, stretched, elongated, cracked, or broken load-bearing components
- Excessive nicks or gouges
- 10% reduction of the original or catalog dimension at any point around the body or pin
- Incomplete pin engagement
- Excessive thread damage
- Evidence of unauthorized welding
- Other conditions, including visible damage, that cause doubt as to the continued use of the shackle
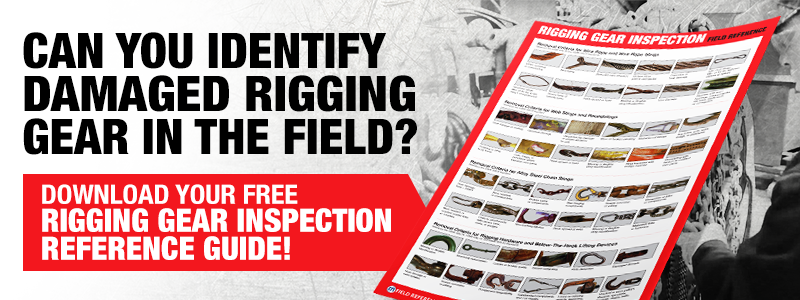
Best Practices for Using Shackles
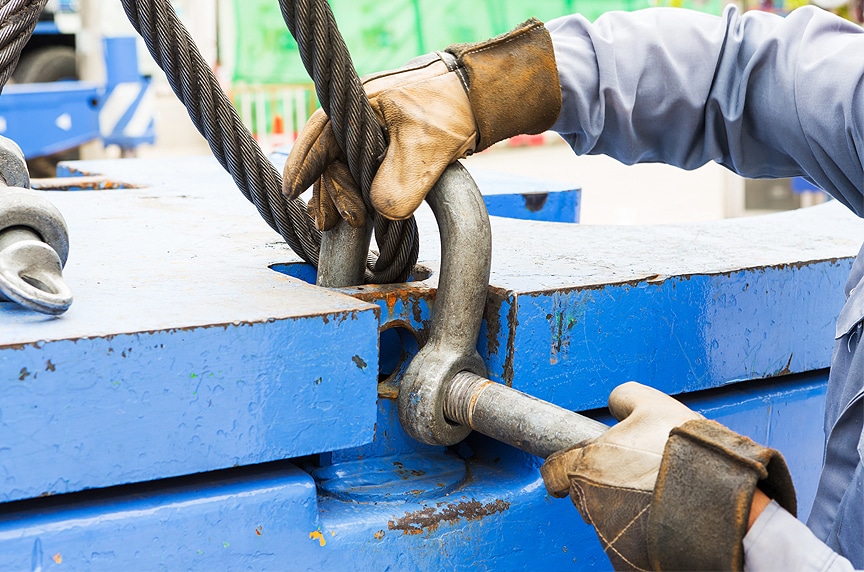
Utilize best practices when using, inspecting, and storing your shackles. Make sure your shackles and all of your rigging equipment:
- Have the proper markings/identification
- Are in acceptable working condition and pass a visual inspection
- Are stored in an area where they’re not susceptible to extreme temperatures, excess moisture, chemical exposure, or mechanical damage
Operators or riggers using shackles shall be aware of the following:
Extreme Temperatures
Avoid using shackles in temperatures in excess of 400°F (204°C) and below –40°F (–40°C). If shackles are to be used in temperatures above or below these ranges, the manufacturer and/or a Qualified Person should be consulted.
Chemically Active Environments
The strength of a shackle can be affected by exposure to caustic or acidic environments. If your shackles have been exposed to or will be used in a chemically-active environment, you should consult the manufacturer or a Qualified Person.
Side Loading Shackles
Some shackles are engineered to handle some form of side loading. For these types of shackles, there will be a reduction to the Working Load Limit as specified by the manufacturer.
Chain shackles are not recommended for side loading, as it could permanently twist or deform the bow of the shackle.
Per ASME B30.26 Rigging Hardware, the following rated load reductions will occur when side loading angle deviates from in-line (0°):
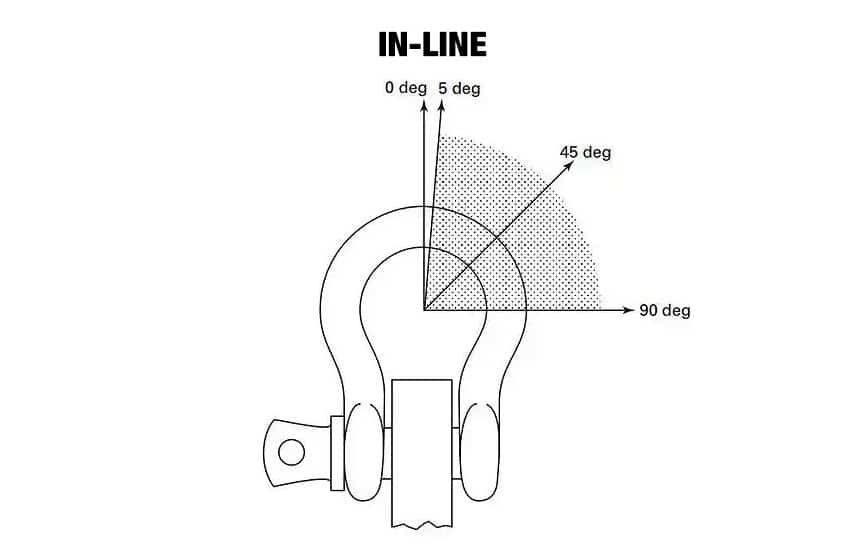
Side Loading Angle (°) | % of Rated Load Reduction |
In-line (0° to 5°) | None |
6° – 45° | 30% |
46° – 90° | 50% |
Over 90° | Not recommended. Consult with manufacturer or Qualified Person. |
When using a shackle with multiple sling legs, the sling legs should rest against the body of the shackle, not the pin. If multiple sling legs are present in the body, they should not exceed 120° in angle. The angle of loading affects the stress in the shackle, so as the horizontal angle decreases, the stress increases in the shackle—see below:
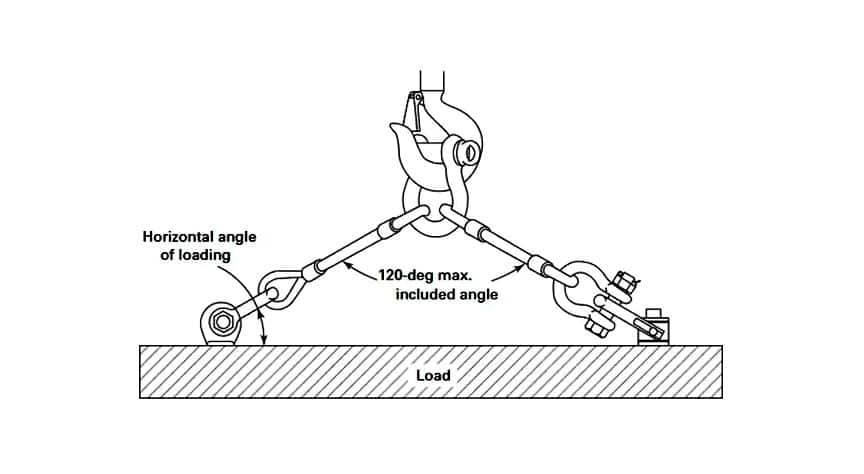
Horizontal Angle (Degrees) | Stress Multiplier |
90° | 1.000 |
60° | 1.155 |
45° | 1.414 |
30° | 2.000 |
Rigging Best Practices
When it comes to using shackles, there are many rigging best practices that must be considered:
- Always ensure the pin threads are fully engaged and the shoulder of the pin is in contact with the shackle body
- Always ensure the cotter pin in is good working condition, and if present, is being used in conjunction with a bolt-type pin or round pin
- Avoid contact with sharp edges that could damage the shackle
- Avoid shock loading
- Center the load in the bow of the shackle to prevent side loading
- Multiple sling legs should be applied to the body of the shackle and not to the shackle pin
- If the shackle is side loaded, the rated load shall be reduced according to the manufacturer or a Qualified Person
- When using a screw pin shackle, do not rig the load in a manner that would cause the pin to unscrew
- Use bolt-type shackles for long-term or semi-permanent installations
- Do not drag shackles across rough or abrasive surfaces
- Multiple slings in the body of a shackle shall not exceed 120° included angle
- When a shackle is used in conjunction with a choker hitch, the pin shall be connected to the choking eye of the sling
Wrapping it Up
Investing in the training of your employees and putting together a lifting and rigging compliance program are two of the best ways you can protect your workers and prolong the service life of your equipment.
Professional rigging training provides your team with the knowledge needed to inspect their rigging equipment before each shift / each lift and to identify damage and irregularities that may require an item to come out of service.
Fully understanding ASME shackle inspection criteria can seem overwhelming when you pair it with the standards related to:
- Slings
- Hooks
- Below-the-hook devices
- Hoists
- Wire rope
If you’re not confident in your knowledge of the applicable OSHA and ASME standards, or just don’t have the resources to put a lifting and rigging compliance program into place, you should consider a third-party inspection provider.
At Mazzella, we have a dedicated team of Rigging Inspectors that are independently trained and certified and inspect to all applicable OSHA and ASME standards. Their only responsibility is to come on-site and perform a thorough inspection of your rigging gear, address solutions as required, and complete the service in a timely manner.
Our inspectors can help you identify compliance issues and identify opportunities for improvement based on their thorough understanding of all applicable OSHA and ASME standards.
If you have questions about rigging inspections, or want to hire a third-party to satisfy OSHA/ASME periodic inspection requirements, please contact us to schedule a consultation. We can partner with you to ensure the peace of mind that safety compliance brings.
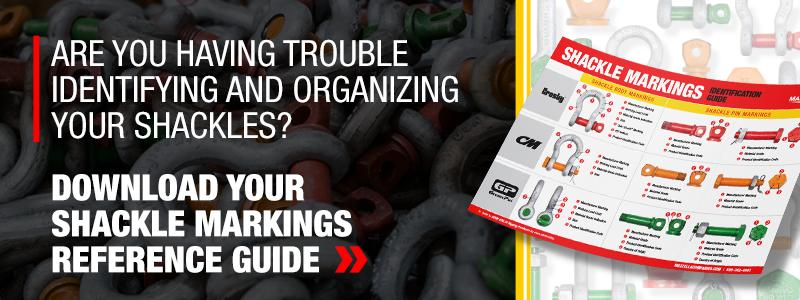
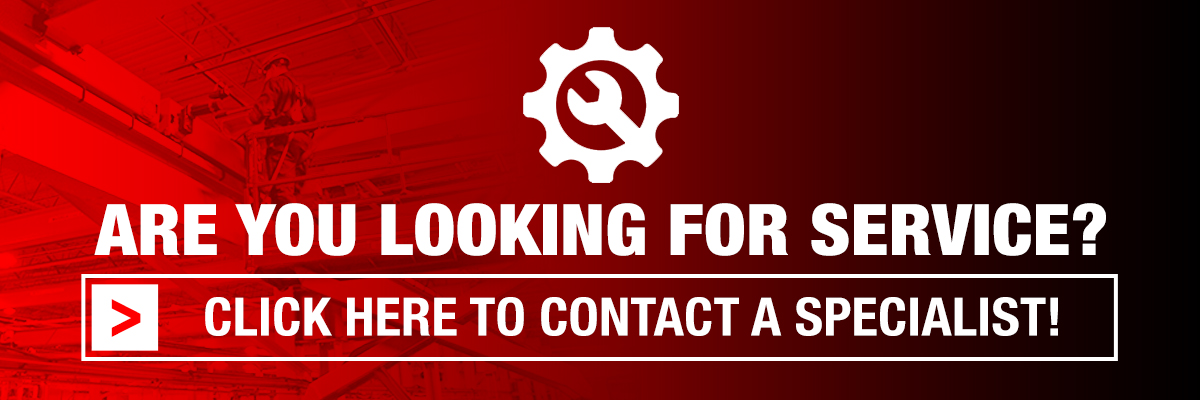
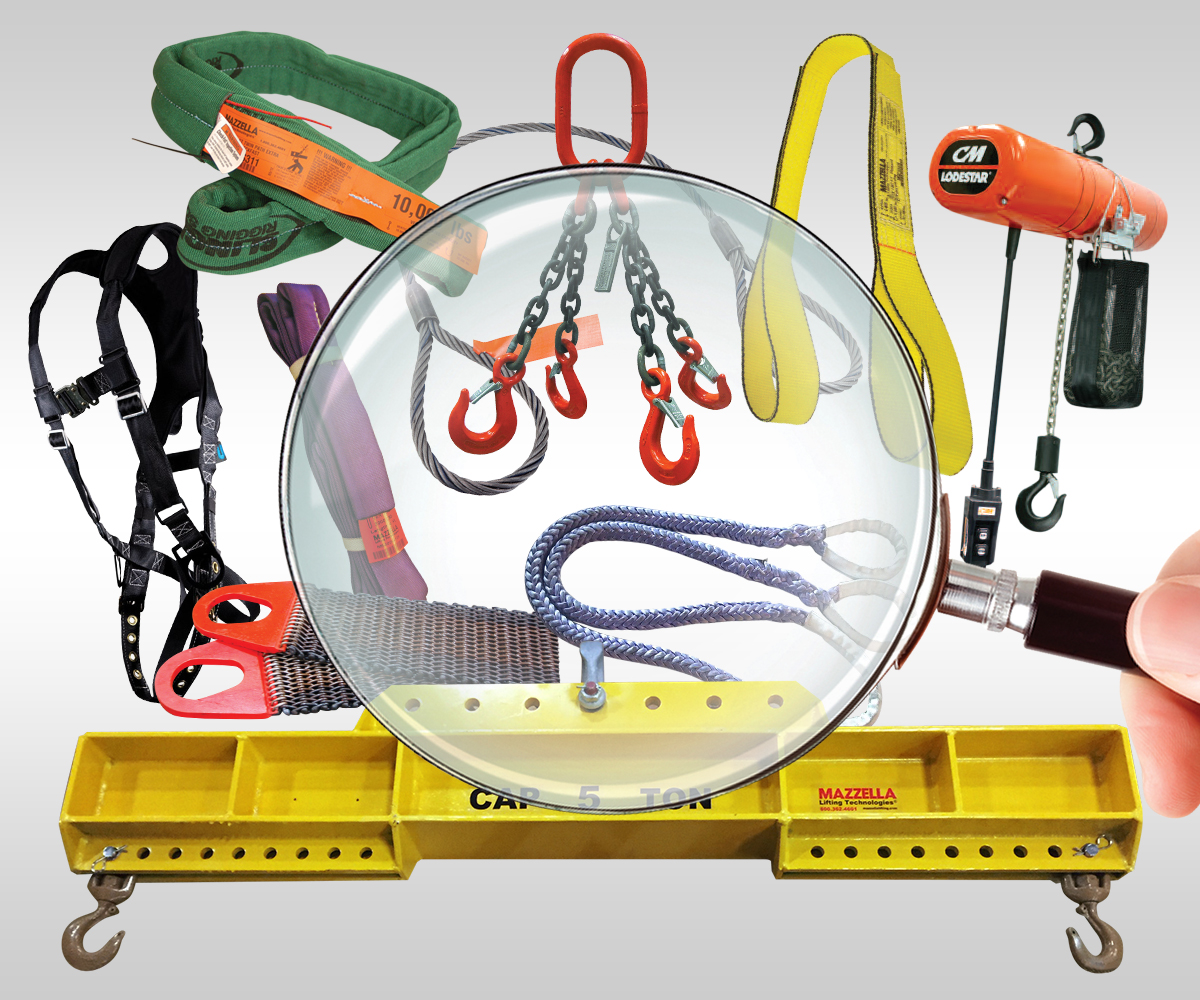
Rigging Inspection Services
OSHA 1910.184, ASME B30.9, B30.20, B30.26, & ANSI Z359 require periodic, documented inspections on slings, rigging hardware, lifting devices, and fall protection every 12 months, at minimum, and monthly to quarterly in more severe service conditions.
Call us at 800.362.4601 or click here if you need inspections for slings, rigging hardware, lifting devices, or fall protection!
Copyright 2019. Mazzella Companies.