What Are ASME Inspection Standards for Close Proximity Magnet Lifters?
What are the inspection requirements for close proximity magnet lifting below-the-hook devices? The American Society of Mechanical Engineers (ASME) sets the standard for all inspections, including types and frequencies.
“Don’t learn safety rules by accident.”
Having below-the-hook lifting equipment that is in proper working order is one of the best ways to ensure you and your coworkers are making safe overhead lifts. To keep BTH devices functional and within industry standards set forth by the American Society of Mechanical Engineers (ASME), several types of inspections are required.
There are six types of below-the-hook lifting devices:
- Structural and Mechanical Lifting Devices
- Vacuum Lifting Devices
- Close Proximity Operated Lifting Magnets
- Remotely Operated Lifting Magnets
- Scrap and Material-Handling Grapples
- Clamps
Each device is used for different purposes, and as such, has its own inspection, testing and maintenance requirements. In this piece, we will look at close proximity magnet lifting devices and provide the following information as listed in the ASME B30.20 Below-the-Hook Lifting Devices standard:
- Inspection classification for close proximity magnet lifting devices
- Removal from service criteria
- Testing of repaired close proximity magnet lifting devices
- Maintenance for close proximity magnet lifting devices
What Types of Magnets Are Referenced in ASME B30.20?
There are two types of magnets that the ASME B30 Committee has outlined regarding installation, inspection and repair standards for in ASME B30.20:
- Close proximity operated lifting magnets
- Remotely operated lifting magnets
A close proximity operated lifting magnet is defined as: “a lifting magnet used in such a fashion that the operator manually positions the lifting magnet on the load, and manually guides the lifting magnet and load during a lift.”
A remotely operated lifting magnet is defined as: “a lifting magnet that does not require the operator or other personnel to be in close proximity to the lifting magnet or its load while the lifting magnet is in use.”
Inspection Classification of Close Proximity Operated Lifting Magnets
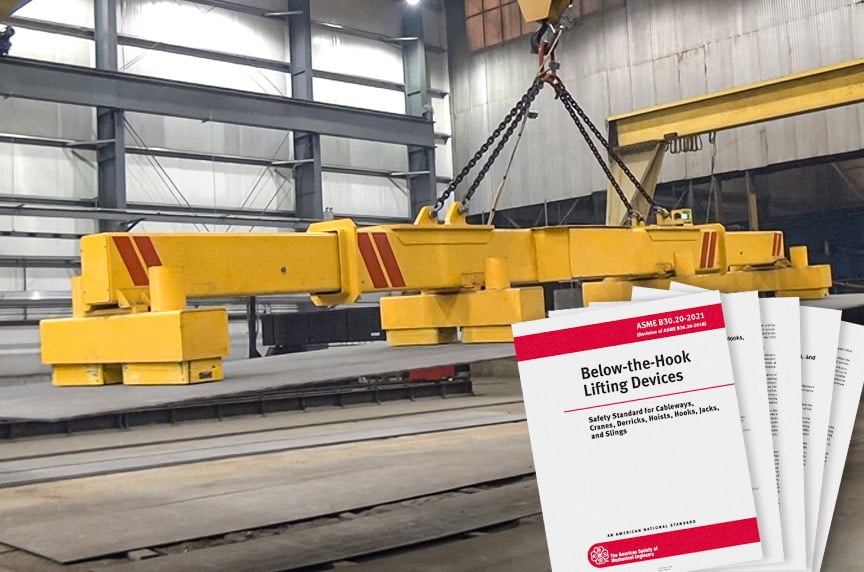
In Chapter 3 of the ASME B30.20 Below-the-Hook Lifting Devices standard, the B30 Committee outlines the following for close proximity operated lifting magnets:
- Inspection
- Testing
- Maintenance
General Inspection Requirements
All inspections shall be performed by a designated person. Any deficiencies identified shall be examined and a determination made by a qualified person as to whether they constitute a hazard, and if so, what additional steps need to be taken to address the hazard.
Inspection of slings (ASME B30.9), hooks (ASME B30.10), rigging hardware (ASME B30.26), or other special devices shall comply with the inspection requirements in the applicable volume.
Initial Inspection
New and reinstalled lifting magnets shall be inspected prior to initial use to verify compliance with applicable provisions of this Volume.
Altered or repaired lifting magnets shall be inspected. The inspection may be limited to the components affected by the alteration or repair, as determined by a qualified person.
Inspection procedures for close proximity operated lifting magnets in regular service are divided into three general classifications, based upon the intervals at which the inspections shall be performed. The intervals, in turn, are dependent upon the nature of the critical components of the lifting magnet and the degree of their exposure to wear, deterioration, or malfunction.
The three general classifications are designated as every lift, frequent, and periodic, with respective intervals between inspections as defined below.
Every Lift Inspection. Visual examination by the operator before and during each lift made by the lifting magnet.
Frequent Inspection. Visual examination by the operator or other designated persons with records not required.
- Normal service — monthly
- Heavy service — weekly to monthly
- Severe service — daily to weekly
- Special or infrequent service — as recommended by a qualified person before and after each lift
Periodic Inspection. Documented visual inspection of apparent external conditions to provide the basis for a continuing evaluation.
- Normal service for equipment in place — yearly
- Heavy service for equipment in place — quarterly
- Severe service — monthly
- Special or infrequent service — as recommended by a qualified person before the first lift and as directed by the qualified person for any subsequent lifts
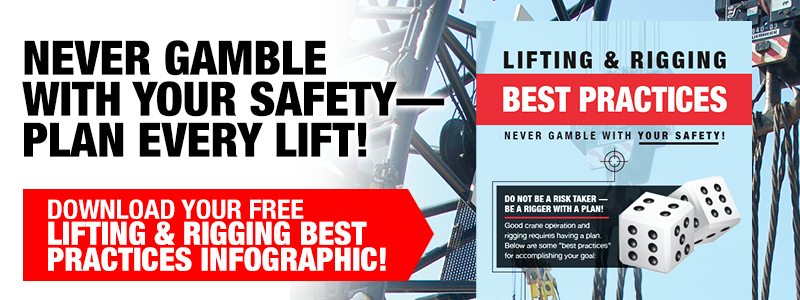
What Inspections Are Performed on Close Proximity Magnet Lifters?
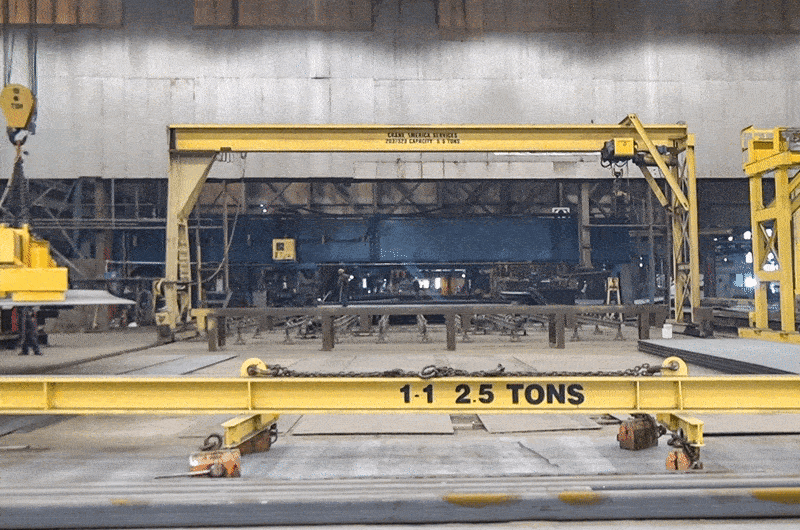
Along with the initial inspection, ASME B30.20 lists several other types of inspections for close proximity lifting devices to make sure they are in working order and safe for employees to use.
Every Lift Inspection
Close proximity lifting magnets shall be inspected by the operator before and / or during every lift for any deficiencies as specifically indicated, including:
- Lifting magnet face and surface of the load for foreign materials and smoothness
- Condition and operation of the control handle of a manually controlled permanent magnet
- Condition and operation of indicators and meters when installed
Frequent Inspection
Close proximity lifting magnets shall be inspected at intervals as defined in para. 20-3.3.1(b)(2). Conditions such as those listed in para. 20-3.3.7 or any other condition that may constitute a hazard, shall cause the magnet lifter to be removed from service. A qualified person shall determine whether any deficiency constitutes a hazard, requires repair, requires disassembly for inspection, or will require more frequent inspection. The lifter shall not be returned to service until approved by a qualified person.
Periodic Inspection
Complete inspections of lifting magnets shall be performed and recorded at intervals as defined in para. 20-3.3.1(b)(3). Conditions such as those listed in para. 20-3.3.7, or any other condition that may constitute a hazard, shall cause the magnet lifter to be removed from service. A qualified person shall determine whether any deficiency constitutes a hazard, requires repair, requires disassembly for further inspection, or will require more frequent inspection. The magnet lifter shall not be returned to service until approved by a qualified person. The inspection shall be based on the manufacturer’s instructions, para. 20-3.3.7, or the recommendations of a qualified person.
Lifting Magnets Not in Regular Use
You may not use your close proximity lifting magnets on a regular basis, but still, there are inspection requirements for it.
A lifting magnet that has been idle for a period of one month to one year shall be inspected in accordance with para. 20-3.3.3 before being placed in service. A lifting magnet that has been idle for a period of one year or more shall be inspected in accordance with para. 20-3.3.4 before being returned to service.
***The paragraphs referenced in the section of the standard that covers “special or infrequent service” states inspections should be conducted on a qualified person.
What Inspection Records Need to be Kept?
Once an inspection is complete, how long do the records need to be kept on file by the end-user?
Dated inspection reports shall be made on critical items, such as those listed in para. 20-3.3.4. Records should be available for each periodic inspection and when the lifting magnet is either altered or repaired.
What Is the Removal Criteria for Close Proximity Magnet Lifters?
A close proximity lifting magnet shall be removed from service if any conditions (if applicable) such as the following are present (limits established by the manufacturer or qualified person) and would result in unsafe performance. A structural and mechanical lifting device shall only be returned to service when approved by a qualified person:
- Deformation, cracks, or wear
- Loose or missing guards, fasteners, covers, stops, or nameplates
- Excessive pitting or corrosion
- Excessive nicks or gouges
- Indications of heat damage
- Unauthorized welds or modifications
- Unauthorized replacement components
- Improper assembly or function
- Lifting surfaces:
- Excessive surface wear
- Nicks, gouges, or any parts impeding the lifting surface from full contact with the load
- Foreign material
- Damaged or distorted pins
- On/Off handle operation
- Impeded movement/rotation of the handle
- Damaged, distorted, or worn threads including foreign material on the threads
- Impaired, seized, or bound bail movement
- Deformed, broken, or missing spring(s)
- Missing or illegible operating control markings or product safety labels
- Loose connections, loss of continuity, corrosion, or damage to insulation of electrical conductors
- Improper level of battery electrolyte or corrosion of either the battery posts or connectors
- Other conditions, including visible damage, which cause doubt as to continued safe use
What Are the Repair Requirements for Close Proximity Magnet Lifters?
Deficiencies disclosed by the inspection requirements of Section 20-3.3 shall be corrected according to the procedures outlined in para. 20-3.3.10 before operation of the lifting magnet is resumed, unless a qualified person determines the deficiency does not constitute a hazard.
Repairs of slings (ASME B30.9), hooks (ASME B30.10), rigging hardware (ASME B30.26), or other special devices shall comply with repair requirements in the applicable volumes or standards.
What Tests Do Close Proximity Magnet Lifters Need Before Being Used in a Lift?
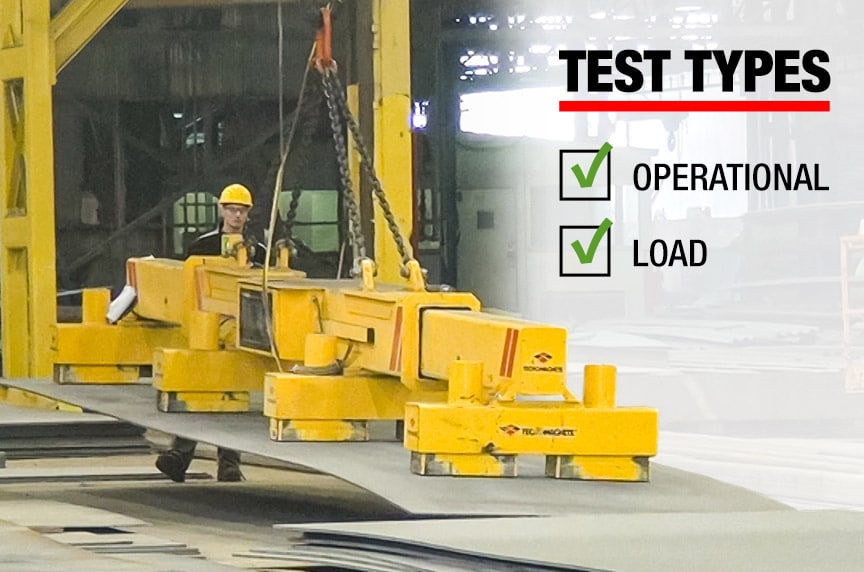
Whether your close proximity magnet lifter is new or has been repaired, there are multiple tests that have to be performed on the device to ensure it is in compliance with the standard and ready to be put into service.
Close proximity magnet lifters must undergo the following types of tests:
- Operational tests
- Load tests
Operational Tests
New and reinstalled lifting magnets shall be tested by a qualified person, or a designated person under the direction of the manufacturer or a qualified person, prior to initial use to verify compliance with applicable provisions of this Volume, including, but not limited to, the following:
- Moving parts
- Latches
- Stops
- Switches
- Any control devices
- Alarms
Altered or repaired lifting magnets shall be tested by a qualified person, or a designated person under the direction of the manufacturer or a qualified person. The test may be limited to the components affected by the alteration or repair, as determined by a qualified person with guidance from the manufacturer.
All indicator lights, gauges, horns, bells, alarms, pointers, and other warning devices shall be tested. Dated reports of all operational tests shall be filed.
Load Tests
Prior to initial use, all new, altered, or repaired lifting magnets shall be tested by, or under the direction of the manufacturer or a qualified person. The rated load of all lifting components associated with the magnet shall exceed the maximum breakaway force of the magnet to avoid overload, or the components shall not be included in the test. The test results shall be recorded confirming the load rating of the lifting magnet.
Breakaway Force Test
General application lifting magnets shall be required to satisfy the rated breakaway force test.
The rated load for permanent magnet lifters shall be less than 33% of the breakaway force measured in this test. For electromagnetic lifters, the rated load shall be less than 50% of the breakaway force measured in this test.
Specified application lifting magnets shall be required to satisfy the specified application lifting magnet breakaway force test.
The rated load for permanent magnet lifters shall be less than 33% of the breakaway force measured in this test. For electromagnetic lifters, the rated load shall be less than 50% of the breakaway force measured in this test.
Design Factor Test
Close proximity operated lifting magnets should have an annual magnetic design factor test to verify the magnet meets (1)(-a) or (1)(-b). This test should be performed to the actual breakaway point of the magnet or may be performed at the calculated minimum breakaway force. The rated load of all components associated with the (magnetic) design factor test shall exceed the maximum breakaway load of the magnet to avoid overload or the lifting hardware shall be removed. Caution should be exercised during the test. The test shall be performed under the direction of a qualified person.
The general application lifting magnet breakaway force test shall establish the force required to vertically remove the lifting magnet from a low carbon, rolled steel plate of the minimum thickness stated by the lifting magnet manufacturer. The portion of this plate that is in contact with the lifting magnet shall not exceed 125” (3.2 × 10−3 mm) or better and be flat within 0.002 in./ft (0.05 mm/m), without exceeding 0.005” (0.127 mm) total. The full operating face of the lifting magnet shall be in contact with the steel plate, which shall be between 60°F (15°C) and 120°F (50°C). The steel plate, load cell, or other testing device shall be mounted to allow self-alignment so the load is applied to the magnet through the magnet’s center of force.
The specified application lifting magnet breakaway force test shall establish the breakaway forces of the lifting magnet under the variety of loading conditions for which the lifting magnet is specified. The details of this test should be supplied by the manufacturer of the lifting magnet.
Battery-operated electromagnets and externally powered electromagnets shall be operated at the manufacturer’s recommended voltage and current levels.
The test for altered or repaired lifting magnets may be limited to the components affected by the alteration or repair, as determined by a qualified person with guidance from the manufacturer.
What Maintenance Programs Are Required for Close Proximity Magnet Lifters?
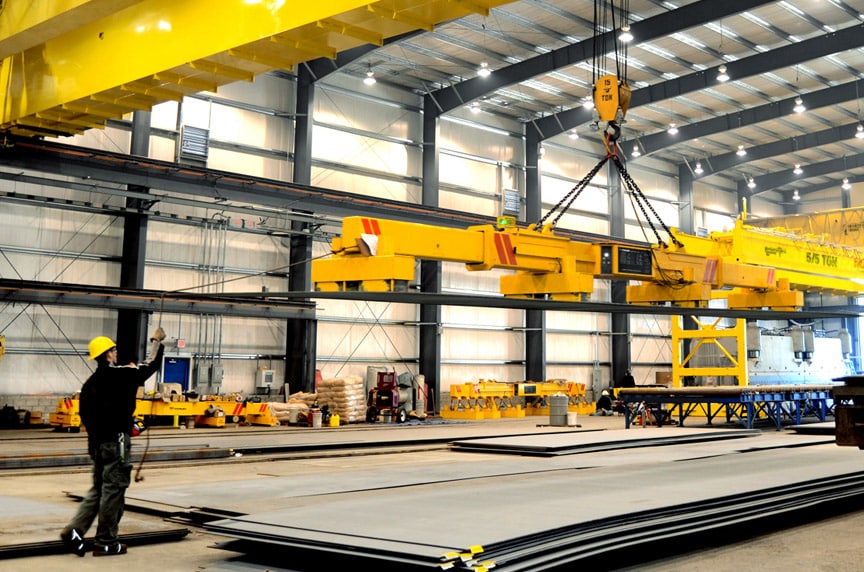
Despite your best efforts to keep your lifting equipment in proper working order, components of your close proximity magnet lifter can and will wear out and need to be replaced. Avoiding unnecessary or preventable repairs can come down to having a proper maintenance program that will help keep your productivity strong and your downtime low.
Maintenance Program
According to ASME B30.20, a maintenance program shall be established and be based on recommendations made by the lifting magnet manufacturer. If a qualified person determines it is appropriate, the program should also include that individual’s additional recommendations based on a review of the lifting magnet application and operations.
Maintenance Procedure
Before adjustment and repairs are started on a lifting magnet or its controls, the following precautions shall be taken:
- All sources of lifting magnet power shall be disconnected, locked out, and tagged “Out of Service.”
- A lifting magnet removed for repair shall be tagged “Out of Service.”
- Relieve fluid pressure from all circuits before loosening or removing fluid power components.
- Only designated personnel shall work on equipment when adjustments, repairs, and tests are required.
- Replacement parts shall be at least equal to the original manufacturer’s specifications.
- After adjustments and repairs have been made, the lifting magnet shall not be returned to service until it has been inspected, according to para. 20-3.3.4.
- Dated records of repairs and replacements should be made.
How Can Mazzella Help You with Close Proximity Magnet Lifters?
We have more than 65 years of experience in designing and developing custom engineered products, below-the-hook lifting devices, and lifting attachments for use with all types of cranes.
On-staff engineering and our commitment to ISO 9001: 2015 guides us to continued success in quality products and processes.
We can design and fabricate all types of below-the-hook lifting solutions for any application—all of our work is done in compliance with ASME B30.20 and ASME BTH-1 standards. Our products range from a common lift beam, to an engineered special 150 lb. engine line lifter, and a 330-ton electric furnace lifter.
Added to our line of engineered below-the-hook lifting products, we also design and fabricate an assortment of specialty engineered solutions for all types of applications. These products are designed to meet your specifications, and we make sure our products are in full compliance with industry standards.
Along with design and fabrication, we provide repairs and / or recertifications of below-the-hook lifting devices.
Call us at 800.362.4601 or click here to specify your next below-the-hook project!
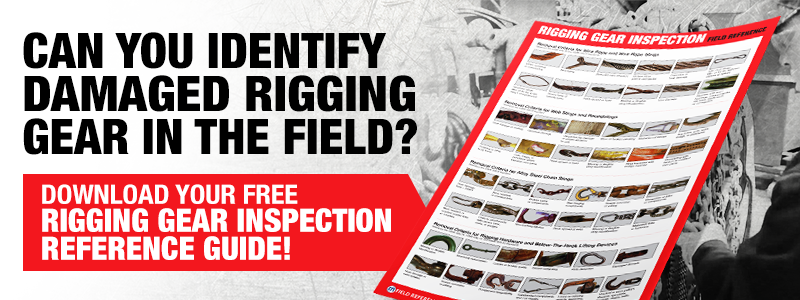
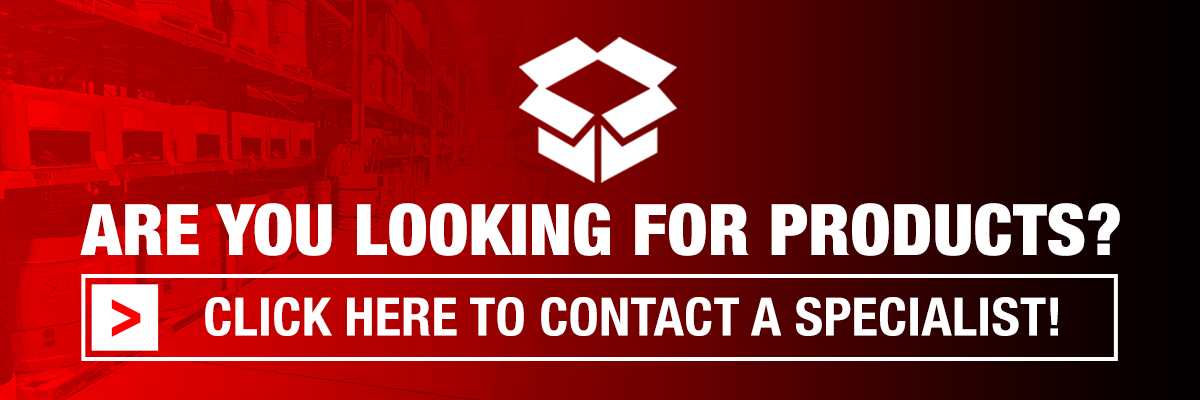
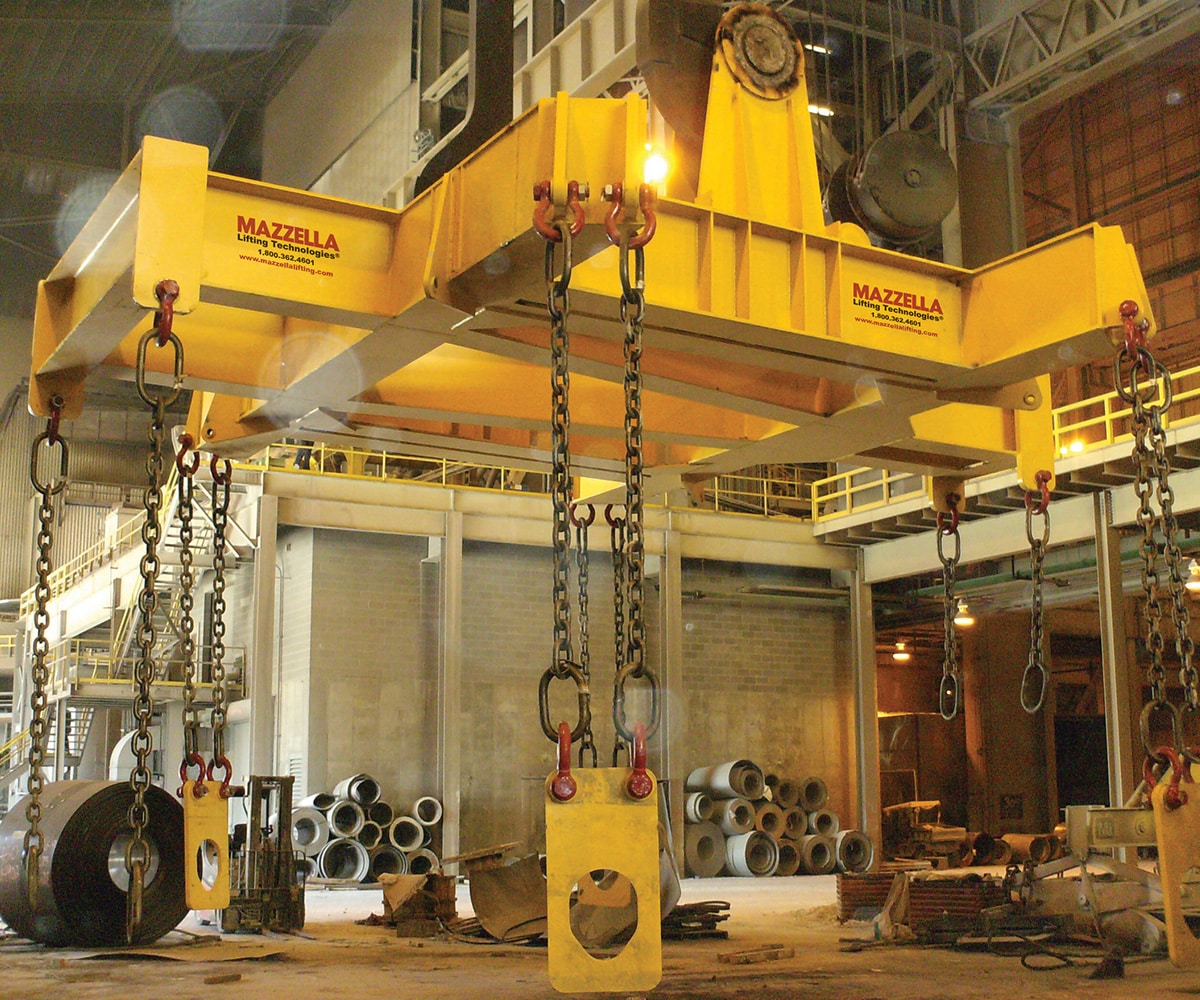
Below-the-Hook Lifting Devices
We have more than 65 years of experience in designing and developing custom engineered products, below-the-hook lifting devices, and lifting attachments for use with all types of cranes.
On-staff engineering and our commitment to ISO 9001: 2015 guides us to continued success in quality products and processes.
Copyright 2022. Mazzella Companies.