What Are ASME’s Inspection Standards for Lever Hoists?
What are the inspection requirements for Lever Hoists? The American Society of Mechanical Engineers (ASME) sets the standard for all inspections, including types and frequencies.
“The future of the safety movement is not so much dependent upon the invention of safety devices as on the improvement of methods of educating people to the ideal of caution and safety.”
The words of applied psychologist Walter Dill Scott could be applied to the American Society of Mechanical Engineers and why the organization exists in the first place.
It is the responsibility of the ASME to set industry standards for safety through their outlining of manufacturing, inspecting, repairing, and maintaining equipment used in the lifting and rigging business.
In this article, we focus on ASME’s standards for lever hoists, and will be answering the following questions:
- What types of hoists are referenced in the ASME B30.21 Lever Hoists standard?
- Which inspection classifications are applied to lever hoists?
- What inspections are performed on lever hoists?
- Which components need to be inspected?
- What tests do lever hoists need before being put into service?
- How can regular maintenance keep lever hoists operational?
What Types of Lever Hoists Are Referenced in ASME B30.21?
There are three types of lever hoists the ASME B30 Committee has outlined regarding installation, inspection and repair standards for in ASME B30.21 Lever Hoists:
- Chain Type
- Rope
- Web Strap
Regardless of type, a lever hoist is defined in the standard as “a manual lever-operated device used to lift, lower, or pull a load and to apply or release tension.”
Lever hoists feature a:
- Suspension hook
- Load hook
- Lines (chain, rope, or web strap)
- Load block
What Are the Inspection Classifications for Lever Hoists?
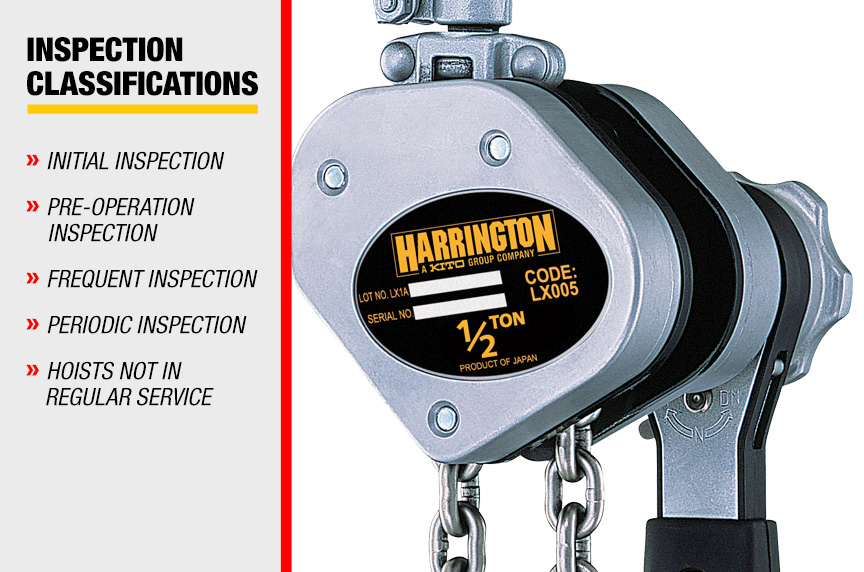
All inspections shall be performed by a designated person in accordance with the manufacturer’s recommendations and with the requirements of this Volume. Any deficiencies identified shall be examined and a determination made by a qualified person as to whether they constitute hazards and whether a more detailed inspection or disassembly is required.
For Inspection Frequency, the intervals shall be determined by a qualified person based on intended operating conditions and their effects on critical hoist components.
Initial Inspection
When being placed in service, all new, altered, or modified hoists shall be inspected per the frequent inspection requirements in para. 21-2.1.4.
Pre-Operation Inspection
Visual inspection performed before the first use of each shift with records not required.
Frequent Inspection
Visual inspection with records not required.
- Normal service — monthly
- Heavy service — weekly to monthly
- Severe service — daily to weekly
Periodic Inspection
Documented visual inspection to provide the basis for a continuing evaluation. An external coded mark on the hoist is an acceptable identification in lieu of records. (A metal stamp mark shall not be made in a highly stressed area.)
- Normal service — yearly
- Heavy service — semiannually
- Severe service — quarterly
Hoists Not in Regular Service
A hoist that has been idle for a period of one month or more but less than one year shall be inspected in accordance with para. 21-2.1.4 before it is placed in service.
A hoist that has been idle for a period of one year or more shall be inspected in accordance with para. 21-2.1.5 before it is placed in service.
***The paragraphs referenced in this section (21-2.1.4 and 21-2.1.5) outline requirements for items needed to be examined in frequent and periodic inspections.
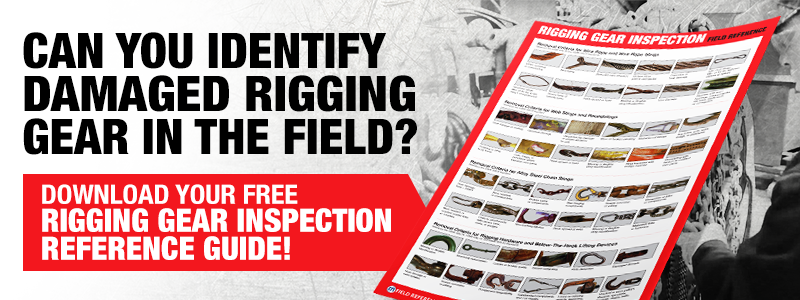
What Inspections Are Performed on Lever Hoists?
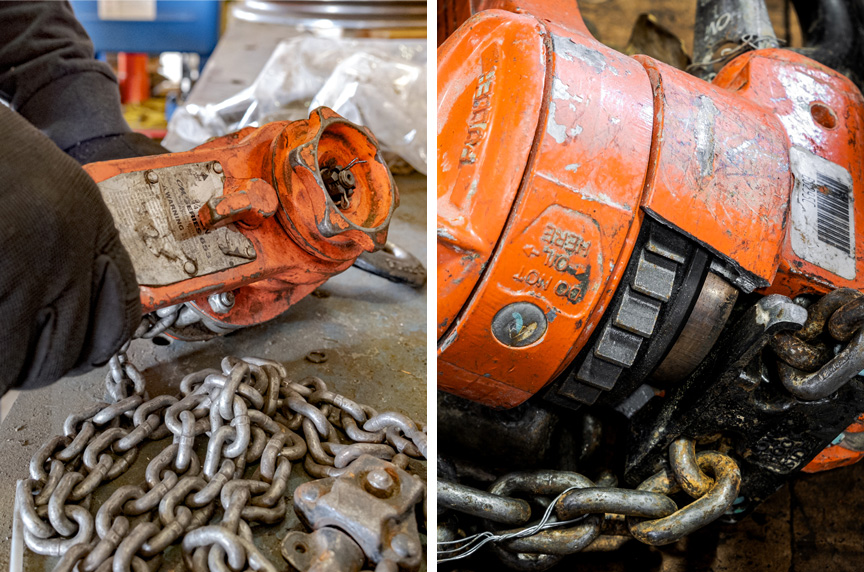
Like shackles, and other rigging hardware, including hooks, lever hoists have detailed inspection standards. There are three main classifications of inspections:
- Pre-Operation Inspections
- Frequent Inspections
- Periodic Inspections
Pre-Operation Inspection
At a minimum, the following items shall be inspected:
- Operating mechanisms for proper operation, proper adjustment, and unusual sounds
- Hooks, including latches when provided, in accordance with ASME B30.10, Frequent Inspection (paras. 10-1.10.3 and 10-2.10.3)
- Load chain, rope, or web strap for gross damage
- Load chain, rope, or web strap reeving
- Overtravel restraint for proper attachment
- Hoist body and lever for deformation, cracks, and / or other damage
- Supporting structure or trolley, if used, for evidence of damage
Frequent Inspection
At a minimum, the following items shall be inspected:
- Operating mechanisms for proper operation, proper adjustment, and for unusual sounds
- Hooks, including latches when provided, in accordance with ASME B30.10, Frequent Inspection (paras. 10-1.10.3 and 10-2.10.3)
- Load chain in accordance with para. 21-2.2.1 or 21-2.2.2
- Rope in accordance with para. 21-2.2.3
- Web straps in accordance with para. 21-2.2.4
- Load chain, rope, or web strap reeving
- Overtravel restraint for proper attachment
- Hoist body and lever for deformation, cracks, and / or other damage
- Supporting structure or trolley, if used, for evidence of damage
Periodic Inspection
Periodic inspections may be performed with the hoist at its location and do not require the hoist to be disassembled.
Covers and other items that allow inspection of components should be opened or removed for the inspection, and then, closed or replaced before restoring the hoist to normal operation.
At a minimum, the following items shall be inspected:
- The items listed in para. 21-2.1.4
- Hooks, including latches when provided, in accordance with ASME B30.10, Periodic Inspection (paras. 10-1.10.4 and 10-2.10.4)
- Fasteners such as rivets and bolts for evidence of loosening
- Components such as load blocks, suspension housings, levers, attachments, clevises, yokes, suspension bolts, shafts, gears, bearings, pins, rollers, and locking and clamping devices for evidence of wear, corrosion, cracks, and distortion
- Load sprockets, idler sprockets, drums, and sheaves for evidence of damage and wear
- Brake mechanisms on friction brake hoists for evidence of worn, glazed, or oil-contaminated friction disks; worn pawls, cams, or ratchets; corroded, stretched, or broken pawl springs
- Supporting structure or trolley, if used, for evidence of damage
- Label or labels, required by para. 21-1.1.4 for legibility and replacement
- End connections of load chains, rope, or web strap for evidence of deterioration, corrosion, cracks, damage, and distortion including overtravel restraints
- The hoist and hoist mounting for evidence of missing items
***The paragraph referenced in this section (21-2.1.4) outlines requirements for items needed to be examined in frequent and periodic inspections.
What Other Components Need to be Inspected on Lever Hoists?
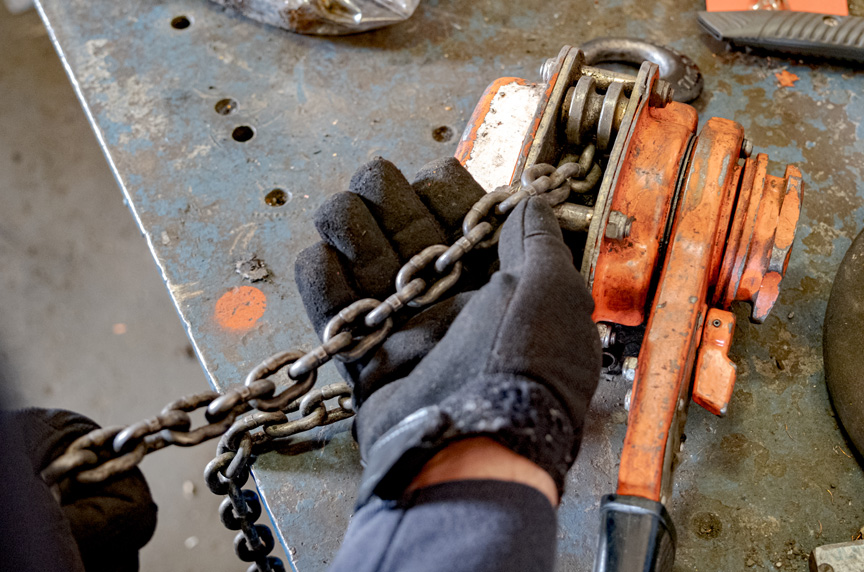
Welded Link Chain
- Welded link chain should first be inspected while it is in the hoist with the hoist suspended in vertical position and a load of approximately 50 lb. (23 kg) applied.
- Test the hoist under load in lifting and lowering directions, and observe the operation of the chain and sprockets. The chain should feed smoothly into and away from the sprockets.
- If the chain binds, jumps, or is noisy, verify that it is clean and properly lubricated. If trouble persists, inspect the chain and mating parts for wear, distortion, or other damage.
- Chains should be inspected over their entire length for gross damage that may be an immediate hazard, such as the following:
- Examine visually for gouges, nicks, weld spatter, corrosion, and distorted links (see para. 21-4.3.1 for replacement criteria).
- Verify the chain feeds smoothly into and away from the sprockets in lifting and lowering operations with a load.
- Slacken the chain and move the adjacent links to one side to inspect for wear at the contact points. If wear is observed or if stretching is suspected, the chain should be measured according to the hoist manufacturer’s instructions. If instructions are not available, proceed as follows:
- Select an unworn, unstretched length of the chain (e.g., at the slack end).
- Suspend the chain vertically under tension and, using a caliper-type gage, measure the outside length of any convenient number of links, approximately 12” to 24” (305mm to 610mm) overall.
- Measure the same number of links in the used sections and calculate the percentage increase in length.
Roller and Rollerless Chain
- Roller and rollerless chain should first be inspected while it is in the hoist with the hoist suspended in vertical position and a load of approximately 50 lb. (23 kg) applied.
- Test the hoist under load in lifting and lowering directions and observe the operation of the chain and sprockets. The chain should feed smoothly into and away from the sprockets.
- If the chain binds, jumps, or is noisy, first see that it is clean and properly lubricated. If trouble persists, inspect the chain in accordance with para. 21 2.2.2(c), and inspect mating parts for wear distortion or other damage.
- Chains should be inspected over their entire length for gross damage that may be an immediate hazard, such as the following:
- Examine visually for gouges, nicks, weld spatter, corrosion, and distorted links (see para. 21-4.4.1 for replacement criteria).
- Verify the chain feeds smoothly into and away from the sprockets in lifting and lowering operations with a load.
- Check chain for elongation following the hoist manufacturer’s instructions. In absence of specific instructions, the chain can be checked by determining the normal pitch and measuring a 12” (305mm) section of chain that normally travels over the load sprocket. Using a caliper-type gage, check the dimension from the edge of one chain pin to the corresponding edge of another pin for the number of pitches per foot.
- Check chain for twist.
- Check for side bow in plane perpendicular to plane of rollers.
Additional Inspection of the Chain
This should be made by removing chain from the hoist and cleaning it thoroughly in an acid-free solvent. Then, a check should be made for any of the following deficiencies:
- Pins turned from their original position
- Rollers that do not run freely with light finger pressure
- Joints that cannot be flexed by easy hand pressure
- Side plates that are spread open (a visual check of the pinhead extension at the damaged area, as compared to the pin extension at the free end of the chain, can determine the amount of spread and the condition of the chain)
- Corrosion, pitting, or discoloration of chain (generally indicative of serious impairment)
- Gouges, nicks, or weld spatter
Rope
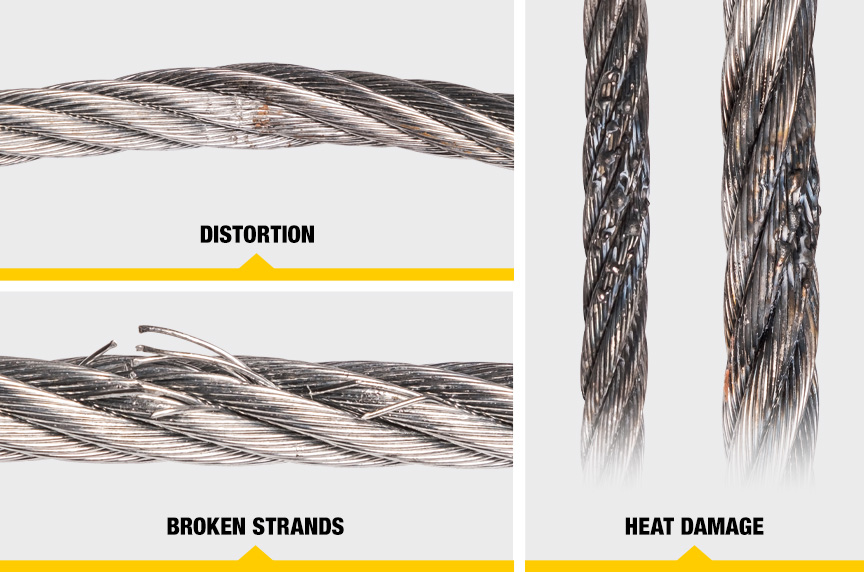
Ropes should be inspected over their entire length for gross damage that may be an immediate hazard, such as the following:
- Distortion of the rope such as kinking, crushing, unstranding, bird-caging, main strand displacement, or core protrusion
- General corrosion
- Broken or cut strands
- In running ropes, six randomly distributed broken wires in six rope diameters or three broken wires in one strand in six rope diameters
- One outer wire broken at the contact point with the core of the rope that has worked its way out of the rope structure and protrudes or loops out from the rope structure
- Evidence of heat damage from any cause
- Reduction of rope diameter due to loss of core support, internal or external corrosion
- Reductions from nominal diameter greater than 5%
- Severely corroded or broken wires at end connections
- Severely corroded, cracked, bent, worn, or improperly applied end connections
Special care should be taken when inspecting sections of rapid deterioration, such as the following:
- Sections in contact with saddles, equalizer sheaves, or other sheaves where rope travel is limited
- Sections of the rope at or near terminal ends where corroded or broken wires may protrude
- Sections subject to reverse bends
- Sections of rope that are normally hidden during visual inspection, such as parts passing over sheaves
Web Strap
Web straps should be visually inspected over their entire length for gross damage that may be an immediate hazard, such as the following:
- Melting or charring
- Acid or caustic burns
- Weld spatter
- Broken stitching
- Cuts or tears
- Damaged eyes or fittings
- Abrasive wear
- Knots
- Discoloration, brittle fibers, and hard or stiff areas that may indicate ultraviolet damage
Special care should be taken when inspecting sections for rapid deterioration, such as the following:
- Sections in contact with saddles, equalizer sheaves, or other sheaves where web strap travel is limited
- Sections of the web strap at or near terminal ends where broken threads or cuts may be evident
- Sections subject to reverse bends
- Sections of web strap that are normally hidden during visual inspection, such as parts passing over sheaves
What Tests Do Lever Hoists Need Before Being Used in a Lift?
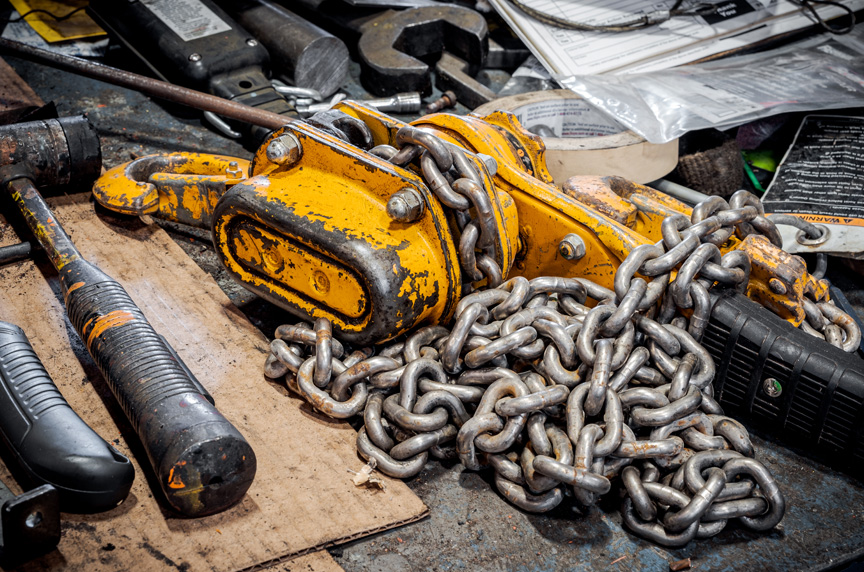
Whether your lever hoist is new or has been repaired, there are two types of tests that have to be performed to ensure the device is in compliance with the standard and ready to be put into service.
Lever hoists must undergo the following types of tests:
- Operational tests
- Load tests
Operational Tests
All new hoists shall be tested by the hoist manufacturer. All altered or repaired hoists, or hoists that have been placed in service that have not been used within the preceding 12 months shall be tested by, or under the direction of, a designated person to ensure compliance with the requirements of this Volume, including the following:
- All functions of the hoist shall be checked with the hoist suspended in the unloaded state. (Some hoists may require a nominal load or pull on the load hook to test the lowering motion).
- After testing in the unloaded state, a load of at least 100 lb. (46 kg) times the number of load-supporting parts of chain, rope, or web strap shall be applied to the hoist in order to check proper load control.
Load Tests
- New hoists shall be tested by the manufacturer with a test load of at least 125% of the rated load.
- A hoist in which load-suspension parts have been altered, replaced, or repaired should be statically or dynamically load tested.
- A qualified person shall determine the need to load test the hoist.
- A written report of the test should be prepared and placed on file.
- The test load shall not be less than 100% of the rated load of the hoist or more than 125% of the rated load of the hoist unless otherwise recommended by the hoist manufacturer or a qualified person.
- The replacement of chain, rope, or web strap is specifically excluded from this load test; however, an operational test of the hoist should be made in accordance with para. 21-2.3.1 prior to placing the hoist back in service.
- Test anchorages or suspensions shall be approved by a qualified person.
What Maintenance Programs Are Required for Lever Hoists?
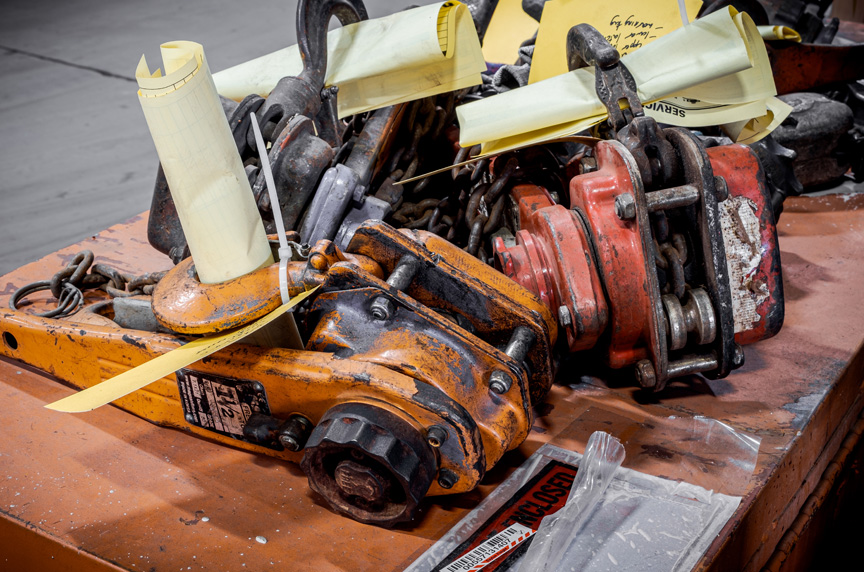
No matter how much care one takes with their equipment, eventually parts do wear out and need to be repaired or replaced. A good way to avoid undo wear and tear on your lever hoists and their components is by following regular maintenance steps that can extend service life.
Preventative Maintenance
A preventive maintenance program shall be established and should be:
- Based on the recommendations outlined in the hoist manufacturer’s manual
- Reviewed by a qualified person for the application of the hoist, when required
- Replacement parts shall be at least equal to the original manufacturer’s specifications
Adjustments, Repairs, and Replacements
Conditions disclosed by the inspections performed in accordance with the requirements of
Section 21-1.3 that are determined to be a hazard during continued operation shall be corrected by adjustment, repair, or replacement before continuing the use of the hoist.
- Adjustments, repairs, and replacements shall be performed by a designated person.
- Components shall be adjusted or repaired as needed. The following are examples:
- Operating mechanisms
- Brakes and pawls
- Repairs or replacements shall be made as needed. Examples are as follows:
- Excessively worn components such as friction disks, ratchets, pawls, and pawl springs
- Critical parts including load suspension components that are cracked, broken, bent, or excessively worn
- Bent, cracked, or otherwise damaged levers
- Worn, corroded, or otherwise damaged load chain, rope, or web strap
- Hooks showing conditions described in ASME B30.10. Repairs by welding or reshaping are not permitted
- Missing or illegible warning labels
- Items that are missing
Lubrication
All moving parts of the hoist for which lubrication is specified should be regularly lubricated. Care should be taken to follow manufacturer’s recommendations outlined in the hoist manufacturer’s manual as to points and frequency of lubrication, and quantity and types of lubricant to be used.
How Can Mazzella Help You with Your Hoists?
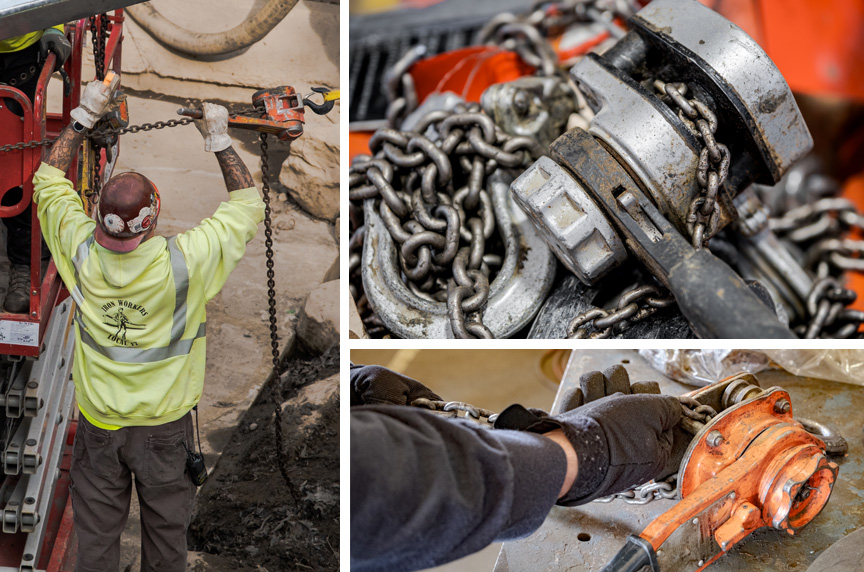
Mazzella is your one source for hoisting products with lifting capacities ranging up to 100 tons. We offer many types of electric, air, and manual hoists for limitless applications.
If you are not looking to replace a hoist, we also have a Hoist Repair Department available to get your hoist back up and running. We provide in-house repair of electric, lever, manual chain, and wire rope hoists.
We offer you the following with our hoist service division:
- Experienced and qualified technicians assigned to perform hoist inspections and repairs
- Repairs and testing that comply with ASME B30.16 Overhead Underhung and Stationary Hoists and ASME B30.17 Cranes And Monorails (With Underhung Trolley or Bridge) specifications
- Static and dynamic testing
- Test certificates that are available electronically or a hard copy on paper
- Repairs and testing performed at our facility
- Load testing of all repaired hoists and pullers
- Repairs and tests to theatrical standards upon request
Call us at 800.362.4601 or click here if you need hoist units, parts, or repairs!
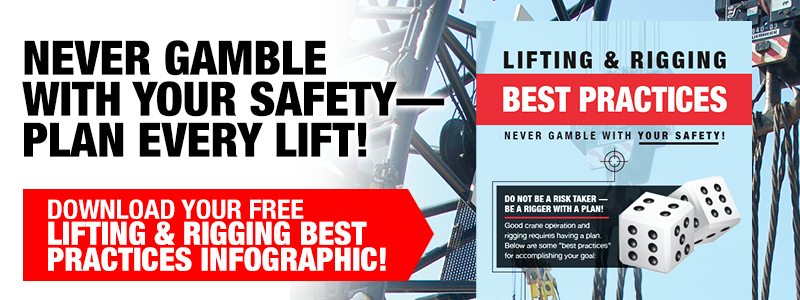
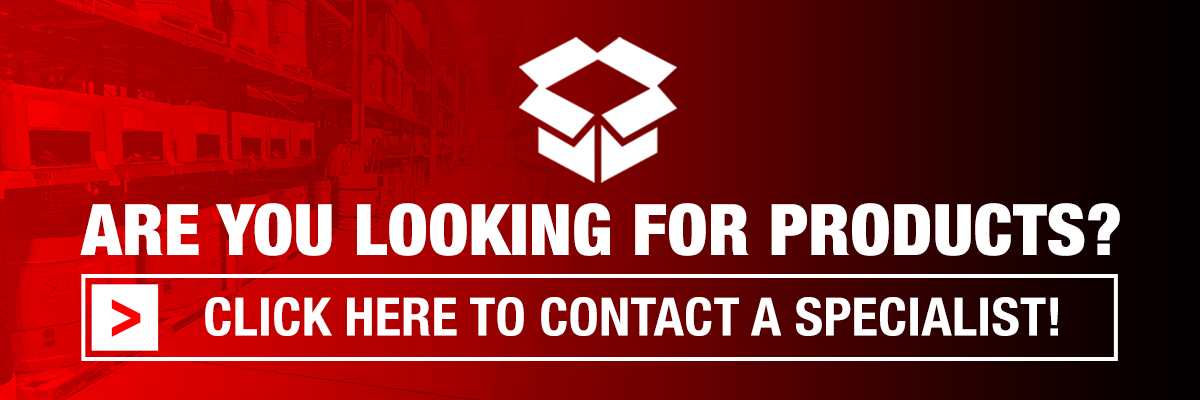
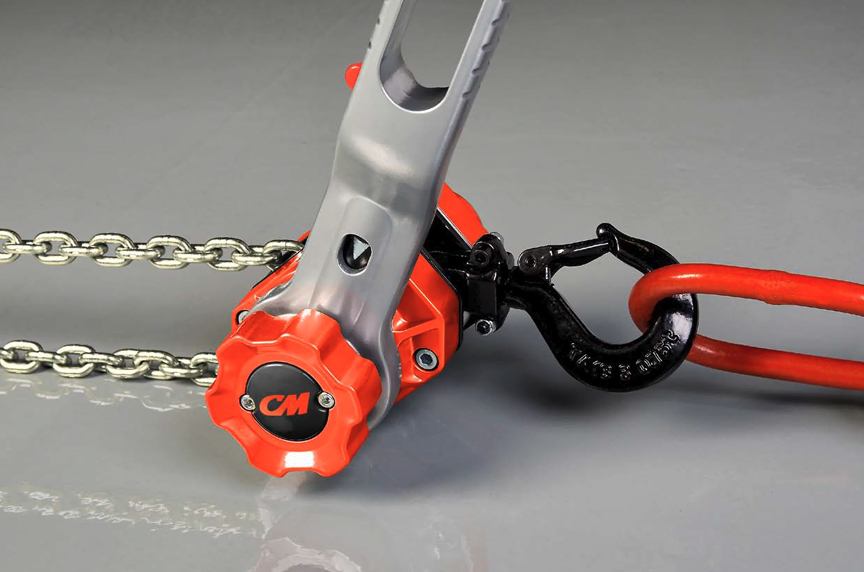
Hoists, Parts, & Repairs
Mazzella are your one source for hoisting products with lifting capacities ranging up to 100 tons. We offer many types of electric, air, and manual hoists for limitless applications.
Copyright 2023. Mazzella Companies.