How Much Does an Overhead Crane Inspection Cost?
The most important factor in determining the cost of an overhead crane inspection is the type of crane, or cranes, that need to be inspected. There are many different kinds of cranes, and each one has its own unique inspection criteria and requirements—requiring varying lengths of time to complete the inspection process.
EDITOR’S NOTE: There is a newer version of this article that reflects 2025 pricing information. Click here to read and understand factors that affect the cost of an overhead crane inspection in 2025.
As a Safety, Maintenance, or Operations Manager, overhead crane inspection should be top of mind for you to stay in compliance with inspection standards laid out by sanctioning bodies like OSHA, ASME/ANSI, and CMAA.
This can seem daunting—especially with all of the other work that you have on your plate—and it can be confusing to understand how often your overhead cranes need to be inspected, and how much that will add to your budget each year.
As a company that employs over 100 certified and experienced crane and hoist inspectors, one of the most frequently asked questions that we get from our customers (often, on a daily basis), is “how much will my crane inspection cost?”
The answer itself can be complex as there are many factors that can affect the cost of an overhead crane and hoist inspection. We’ll dive deeper into these factors below to help you better understand how much an overhead crane inspection will cost you.
What Type of Crane is Being Inspected?
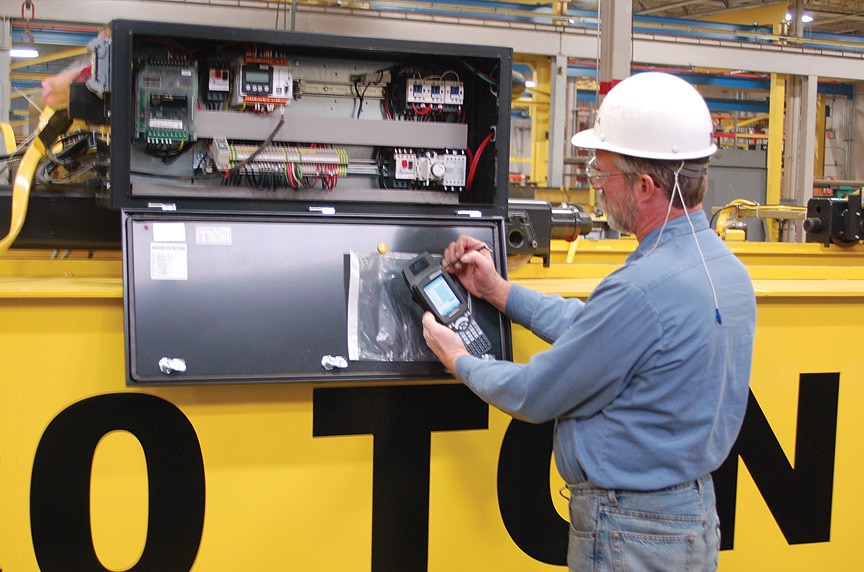
The most important factor in determining the cost of an overhead crane inspection is the type of crane or cranes that need to be inspected. There are many different kinds of cranes, and each one has its own unique inspection criteria and requirements, and can take varying lengths of time to complete the inspection process.
As the duty cycle increases, the cost of the inspection will increase due to the components and the time required to complete a thorough inspection. Think about all of the moving parts required to operate an overhead double girder top running electrified crane. Now, compare that to a basic jib crane or mechanical workstation crane with no electronics, and a basic support structure.
- Number of cranes – The total number of cranes on-site will play a major factor in the cost of the crane inspection. The more cranes there are on site, the longer the inspector(s) will have to remain at your facility to complete the job.
- Capacity – Higher capacity units take longer time to inspect, so it increases cost. A 50-ton crane takes longer than a 5-ton crane, for example.
- Components – A double girder or single girder overhead crane is going to have significantly more parts than a basic jib or workstation crane. Things like electrification systems, braking systems, radio remote controls/pendants, variable speed controls, etc. have their own inspection requirements and are more complex pieces than what you would find on a jib or workstation crane.
- Time – With more components, comes a more thorough inspection, and more time on-site for the inspector to complete the inspection process.
- Environment and accessibility of cranes – What type of environment is the crane in? Hazardous or chemical environments, and accessibility considerations like maneuvering lifts to access the crane equipment, have a direct relationship on the cost of the inspection.
Frequency and Type of Crane Inspection
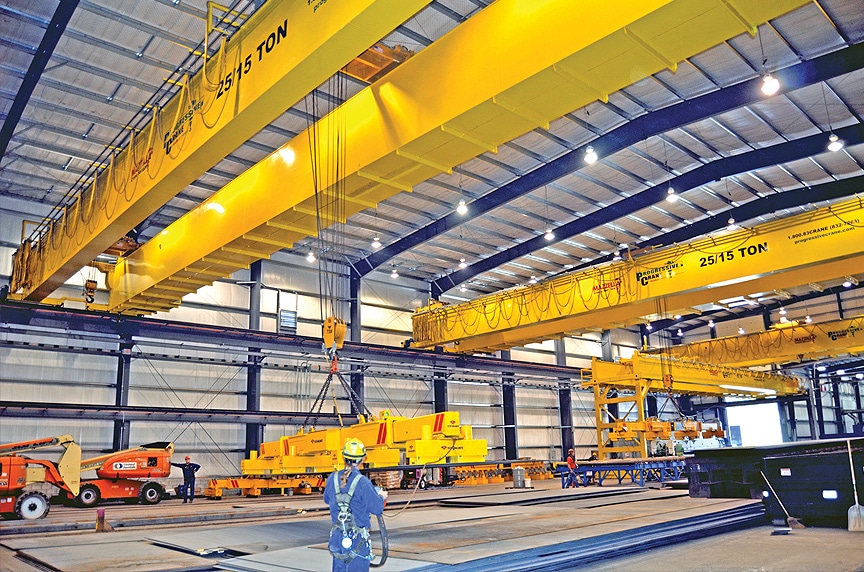
A major factor in determining the cost of an overhead crane inspection is the frequency, or type of crane inspection, that is being performed. Knowing how often your overhead cranes need to be inspected is one of the first steps in determining the criteria for inspection and how often it will be performed. Developing an inspection program that will meet compliance requirements for OSHA, ASME, and CMAA standards will help to keep you compliant for overhead crane inspection—scheduling only one annual inspection will not.
Inspection frequency is based on crane service, environmental factors, and application factors according to OSHA 1910.179:
“Inspection procedure for cranes in regular service is divided into two general classifications based upon the intervals at which inspection should be performed. The intervals, in turn, are dependent upon the nature of the critical components of the crane and the degree of their exposure to wear, deterioration, or malfunction. The two general classifications are herein designated as ‘frequent’ and ‘periodic’ with respective intervals between inspections…”
The section highlighted in bold above is the most critical piece of this statement. Specifically, “the degree of their exposure to wear, deterioration, or malfunction.” The degree of exposure of the crane’s critical components is determined by the duty cycle of the crane, or crane service classification, as determined by CMAA:
- Class A (Standby or Infrequent Service) – This equipment, including installation and maintenance cranes, usually operates at slow speeds for precise handling with long idle periods between lifts. Maximum capacity lifts are sometimes required.
- Class B (Light Service) – This class of equipment includes cranes in repair shops, light assembly operations, service buildings, light warehousing, etc. and service requirements are light and the speed is slow. Loads vary from no load to occasional full-rated loads with 2-5 lifts per hour, averaging 10 feet per lift.
- Class C (Moderate Service) – In terms of numbers, most cranes are built to meet Class C service requirements, including cranes used in machine shops or paper mill machine rooms. These types of cranes will handle loads that average 50% of the rated capacity with 5-10 lifts per hour, averaging 15 feet per lift.
- Class D (Heavy Service) – Typical examples of these types of crane include ones used in heavy machine shops, foundries, fabricating plants, steel warehouses, container yards, lumber mills, etc. These types of cranes constantly handle loads approaching 50% of the rated capacity. High speeds are desirable for this type of service with 10-20 lifts per hour, averaging 15 feet, with not 65% of the lifts at rated capacity.
- Class E (Severe Service) – This equipment is a top riding bridge or gantry type multiple girder electric overhead crane. Applications include magnet, bucket, or magnet/bucket combination and are most commonly found at scrap yards, cement mills, lumber mills, fertilizer plants, container yards, etc. This service class requires a crane capable of handling loads approaching the rated capacity throughout its life with 20 or more lifts per hour at or near rated capacity.
- Class F (Continuous Severe Service) – This equipment is a top riding bridge or gantry type multiple girder electric overhead crane. Applications include custom-designed specialty cranes essential to performing critical work task affecting the total production facility. These cranes must be capable of handling loads approaching rated capacity continuously under severe service conditions throughout its life.
So, now that we’ve identified the different types of overhead crane service classifications, we can lay out guidelines for inspection frequency. A crane will go through two types of inspections during the course of a year: Frequent and Periodic. Let’s identify what these types of inspections are, and how often they need to occur:
Frequent inspection – A frequent inspection is a visual and operational inspection performed monthly or as often as daily. Inspection frequency is based on service, environmental, and application factors, as designated by a qualified person.
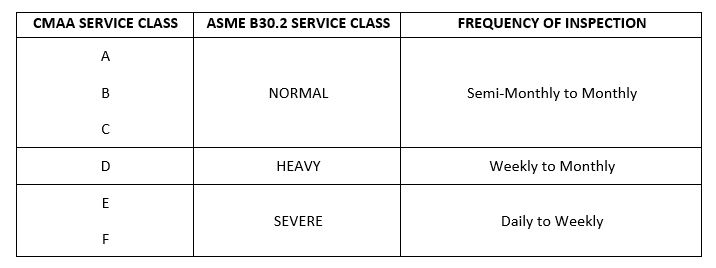
Periodic inspection – A periodic inspection is a detailed visual and operational inspection where individual components are examined to determine their condition. Inspection frequency can be quarterly to annually and is based on service, environmental, and application factors, as designated by a qualified person.
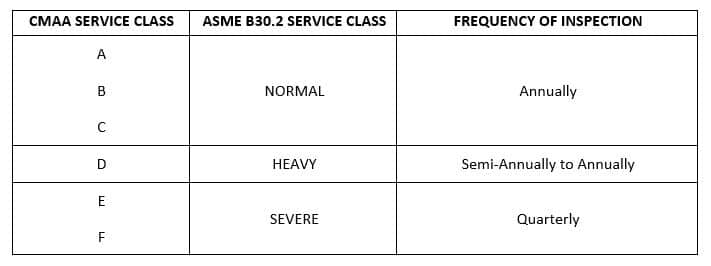
As you can see, a crane that is in a normal service class may only need a Periodic Inspection once a year and Frequent Inspections semi-annually. Cranes in heavy or severe service classes should have a Frequent Inspection performed weekly and need a Periodic Inspection 2-4 times a year. Determining how often you need to have your cranes inspected will affect the cost of developing an overhead crane inspection program.
Other Factors That Can Affect the Cost of Crane Inspection
There are a few other factors that can affect the cost of a crane inspection. Things like equipment, downtime or wait time, training, and environment can all affect the overall cost of a crane inspection.
Equipment – Will the inspector need to provide their own lift or is there equipment on-site that will allow the inspector to access the cranes? If a technician needs to bring their own lift, it can add up to an hour onto the service time to complete the unloading and loading of the lift.
Are there provisions in place (anchors, guardrails, etc.) for fall protection? Is the equipment easy to reach? Accessibility of the crane or unit can affect the time it takes to complete the inspection.
Drive time – Drive time will be calculated based on the distance and time that it takes the technician to drive from their shop to the customer’s location.
Down / wait time – Any additional time that the inspector has to wait for a shift or production run to end, before they can access the equipment, will be charged at published hourly rates and fees.
Training – Is additional safety training required for an inspector to come on your job site or access your facility? Additional training will add on to the number of hours required for the inspection and increase costs. It’s best to let your crane service provider know about this upfront so they can build it into their quote.
Environment – Abnormal or hazardous environments (chemical baths, hot metal, extreme heights, etc.) will require additional equipment and/or additional protection for an inspector to come on-site. It may even require an inspector with specialized training who is familiar with and qualified to work in an environment with potential hazards.
How Much You Can Expect to Pay for an Overhead Crane Inspection
Every crane service provider has their own set prices for overhead crane inspection, but you should expect to ask for their hourly rate, plus an estimate of the total number of hours required to complete the crane inspection process at your facility.
We’ve seen ranges starting around $65 per hour all the way up to $125 an hour for crane inspection services. However, many companies quote between the ranges of $75-$100 per hour on average.
One thing to make note of when reviewing bids from crane service providers: If any bid stands out as abnormally low compared to a comparable bid that you received from another vendor, that company may be discounting their inspection quote to get you to sign up for a contract or service agreement. Once you’re on-board as a customer under contract, they may make up for their low bid by marking up their rates for any service and repairs/replacement parts needed down the road.
Wrapping it Up
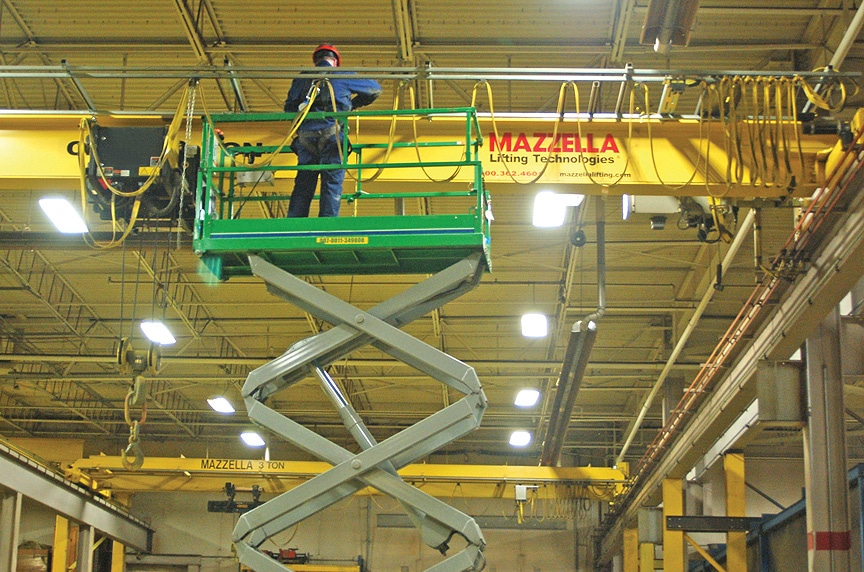
Remember, when a crane service provider is estimating the total number of hours they expect to complete a crane inspection, they will need the following information to put a well-informed estimate together:
- Type of crane and capacity of the crane that is being inspected
- The total number of cranes being inspected
- Crane service class / duty cycle
- Travel time from their facility to your facility
- Unloading and loading time of any special equipment required to complete the inspection
- Other factors, including special training required to come on site, any special equipment needed, operating environment, and accessibility to the crane or equipment
At Mazzella FHS, our field personnel are experienced and certified to help you with in-plant crane inspection needs, field inspections, lifting and rigging inspections, and hoist inspections. We’ll work hand-in-hand with your company to help develop an overhead crane inspection program that meets your company’s unique needs and complies with OSHA and CMAA requirements.
When one of our inspectors comes on site, a typical crane inspection will include:
- A review of existing inspection records
- A detailed inspection of your lifting equipment including cranes and hoist equipment
- A copy of the detailed inspection reports to show documented compliance
- Consultation on inspection reports and actionable items regarding any hazards, mechanical issues, or opportunities for improvement to help keep your employees safe, reduce downtime, and extend the life of your equipment.
- Retention of all inspection records for a period of 7 years
If you’d like to receive a quote, or schedule a consultation to develop a crane inspection program for your facility, contact a Crane Service Specialist today.
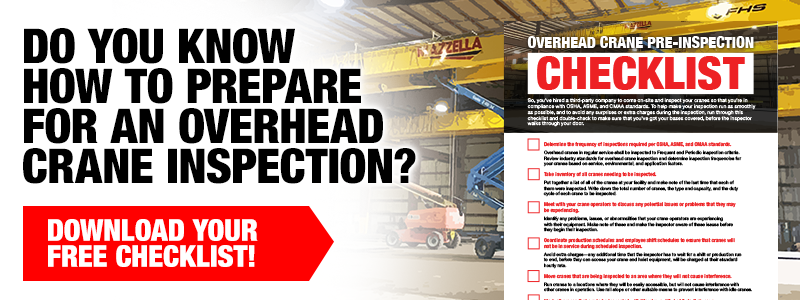
Copyright 2017. Mazzella Companies.