How to Inspect Your Metal Mesh Lifting Slings to ASME B30.9 Standards
Metal mesh slings are widely used in demanding environments like metalworking facilities and steel processing facilities where the loads may be abrasive and hot. However, if there is evidence of even one broken wire in the sling, the entire sling needs to be removed from service.
Metal mesh slings, also known as wire mesh slings, can be looked at as the perfect marriage between different types of lifting slings like alloy chain slings and synthetic slings made from polyester or nylon. When using a metal mesh sling, you get strength and durability combined with flexibility and excellent load grip and securement.
Metal mesh slings are widely used in demanding and high-heat environments like metalworking facilities, steel mills, or steel processing facilities where the loads may be abrasive and hot. The steel construction of these slings resists abrasion, cutting, and heat damage that synthetic slings would be more susceptible to.
Often, the wire mesh material is made from galvanized high-carbon steel, alloy, or stainless steel to resist corrosion. The fittings can be plated or made from an alloy material for corrosion resistance and longer service life.
Metal mesh slings are often preferred in rough environments because of their ability to be repaired and re-certified. They also have low stretch and a wide-bearing surface area to firmly grip and secure a load—reducing load damage. They’re extremely resistant to abrasion and cutting, however if there is evidence of even one broken wire in the sling, the entire sling needs to be removed from service.
In this article, we’ll look at:
- How often you need to inspect metal mesh slings
- What information is required for sling identification
- Metal mesh sling construction specifications
- Inspection criteria for metal mesh slings
- Best practices for maintaining metal mesh slings
How Often Do You Need to Inspect Metal Mesh Slings?
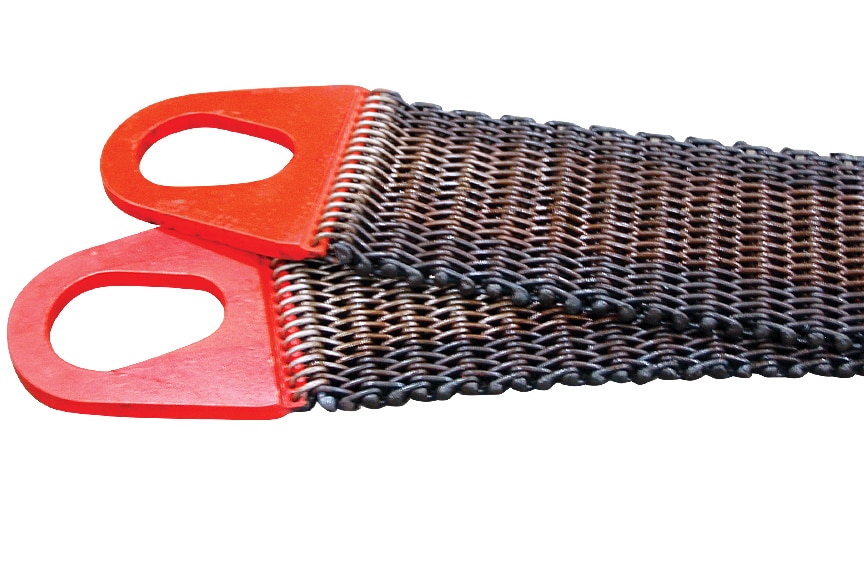
All inspections shall be performed by a designated person with any deficiencies further examined by a qualified person to identify hazards and determine what additional steps need to be taken to address the hazard.
There are two industry standards that exist to provide the end-user with guidelines for inspection and criteria that warrants removal from service: OSHA 1910.184 and ASME B30.9.
Initial Inspection (Prior to Initial Use)
Best practice is to inspect metal mesh slings upon receiving them from the manufacturer. Double-check the sling identification to make sure it’s what you ordered and that the rated capacity meets all of your project specifications and lifting requirements.
Frequent Inspection (Daily or Prior to Use)
Designate a Competent Person to perform a daily visual inspection of slings and all fastenings and attachments for damage, defects, or deformities. The inspector should also make sure that the metal mesh sling that was selected meets the specific job requirements it’s being used for.
However, users can’t rely on a once-a-day inspection if the sling is used multiple times throughout the day. Shock loads, severe angles, edges, and excessive heat can quickly cause damage to the material, so best practice is to perform a visual inspection prior to each use.
Periodic Inspection
A periodic inspection is performed by either a professional inspection provider, or by a Qualified Person every 12 months (at a minimum) and monthly to quarterly in more severe service conditions. The following are all determining factors in scheduling the frequency of a periodic inspection:
- Frequency of use
- Severity of service conditions
- Nature of the lifts being performed
- Experience gained on the service life of metal mesh slings used in similar applications
ASME provides these additional periodic inspection guidelines based on the service of the metal mesh sling:
- Normal Service – Yearly
- Severe Service – Monthly to Quarterly
- Special Service – As recommended by a Qualified Person
Depending on the severity of the operating environment and frequency of use, your business may decide to inspect metal mesh slings more often than the minimum yearly requirement.
Periodic inspections are required to be documented per ASME B30.9 and records retained. The employer is required to maintain a record of the most recent thorough inspection. Failure to maintain and retain inspection records is one of the most common issues we see that can prevent a company from reaching full OSHA compliance.
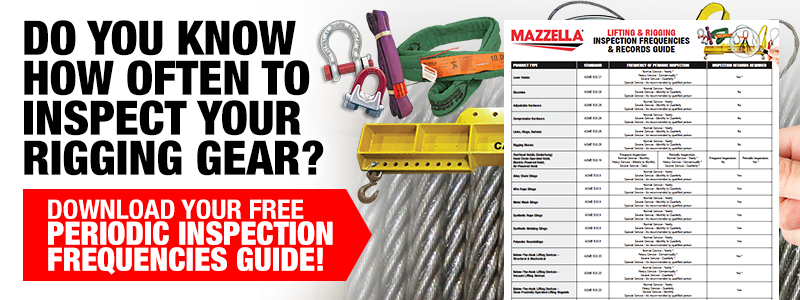
What Is Required for Metal Mesh Sling Identification?
Per ASME B30.9, each metal mesh sling shall be marked by the manufacturer to include:
- Name or trademark of the manufacturer, or if repaired, the entity performing the repair
- Rated load for at least one hitch type and the angle upon which it is based
- Individual sling identification (ex: serial number)
It is the responsibility of the user to maintain the sling identification—ensuring it remains legible during the life of the sling. If the identification is missing or illegible, it should be removed from service.
Metal Mesh Sling Fabric Construction Specifications
The table below can be found in 9-3.2.1 Fabric Construction: Metal Mesh Slings from ASME B30.9-2018.
Specification | Heavy Duty | Medium Duty | Light Duty |
Nominal spiral turns per foot mesh width | 35 | 43 | 59 |
Approx. spiral wire size | 10 gage | 12 gage | 14 gage |
Equivalent decimal size | 0.135 in. | 0.105 in | 0.080 in. |
Nominal cross rods per foot of fabric length | 21 | 30 | 38 |
Approx. size of cross rods | 8 gage | 10 gage | 14 gage |
Equivalent decimal size | 0.162 in. | 0.135 in. | 0.080 in. |
Nominal fabric thickness | 1/2 in. | 3/8 in. | 5/16 in. |
ASME B30.9 Inspection Criteria for Metal Mesh Slings
The goal of a sling inspection is to evaluate remaining strength in a sling which has been used previously to determine if it is suitable for continued use. When inspecting metal mesh slings, daily visual inspections are intended to detect serious damage or deterioration which would weaken the strength and integrity of the sling.
If during any point of the inspection the following is observed, the metal mesh sling should be removed from service, according to ASME B30.9 standards:
- Missing or illegible sling identification
- Broken weld or a broken brazed joint along the sling edge
- Broken wire in any part of the mesh
- Reduction in wire diameter of 25% due to abrasion or 15% due to corrosion
- Lack of flexibility due to distortion of the mesh
- Distortion of the choker fitting so the depth of the slot is increased by more than 10%
- Distortion of either end fitting so the width of the eye opening is decreased by more than 10%
- 15% reduction of the original cross-sectional area of any point around the hook opening of the end fitting
- Visible distortion of either end fitting out if its plane
- Cracked end fitting
- Slings in which the spirals are locked or without free articulation shall not be used
- Fittings that are pitted, corroded, cracked, bent, twisted, gouged, or broken
- Other conditions, including visible damage, that cause doubt as to the continued use of the sling
Best Practices for Maintaining Metal Mesh Slings
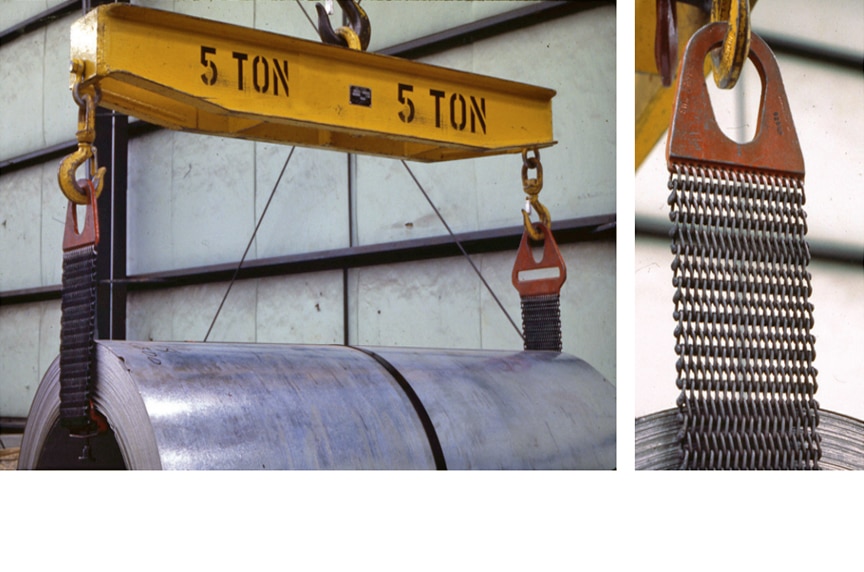
Maintaining a metal mesh sling during and in between uses is the best way to help extend the life of it and help to ensure that it stays in service. Inspections are easier to perform—and probably more thorough—when slings are easily accessible and organized, kept off of the ground, and stored in a cool and dry environment.
Hang up your slings or keep them in a designated locker or rigging box where they are off of the ground and will not be subjected to mechanical damage, corrosive action, moisture, or kinking.
Temperature
When slings are used at temperatures above 550°F / 228°C or below –20°F / –29°C, the sling manufacturer should be consulted.
If the sling contains any coatings that change the temperature range of the sling, the manufacturer shall provide a revised temperature range.
Chemically Active Environments
The strength of metal mesh slings may be degraded by chemically active environments. This includes exposure to chemicals in the form of solids, liquids, gases, vapors, or fumes. The sling manufacturer or a qualified person should be consulted before slings are used in chemically active environments.
Edge and Cut Protection
Slings in contact with edges, corners, or protrusions, should be protected with a material of sufficient strength, thickness, and construction to prevent damage.
Edge protection and cut protection should be used on all edges and corners—even the ones that aren’t load-bearing surfaces.
Keep Your Slings Clean
Continual exposure to dust, dirt, and moisture can degrade the materials and cause corrosion—shortening the life expectancy of the product. Wipe grease or oil off of your slings and try to keep them clean of dirt, chemicals, or other particulates which can break down the material over time.
Avoid Misuse and Abuse
Use rigging best practices when lifting a load with metal mesh slings. Avoid the following before, during, and after an overhead lift to prevent damage to the sling:
- Loads should not be rested on the sling
- Slings should not be pulled from under a load if a load is resting on a sling
- Be aware of possible snagging during load-handling activities
- Slings should not be dragged on the floor or over an abrasive surface
- Slings should not be constricted, bunched, or pinched by the load, hook, or any fittings
- Avoid twisting and kinking of the sling
Wrapping it Up
A well thought-out sling inspection program can help prevent industry compliance issues, keep your workers safe, and extend the life of your lifting equipment.
At Mazzella, we understand the amount of effort and coordination it can take to stay in compliance with OSHA and ASME’s industry standards. We offer a variety of services including site assessments, rigging and crane operator training, rigging inspection services, sling repair, overhead crane inspections, and so much more.
Our Rigging Inspection Services group is its own dedicated business unit with a team of inspectors that are certified through Industrial Training International to meet OSHA 1910.184 and ASME B30.9 requirements for sling inspection.
If you want more information on our sling inspection program or want to schedule a consultation to learn how you can assess the compliance of your lifting and rigging program, contact a Lifting Specialist today.
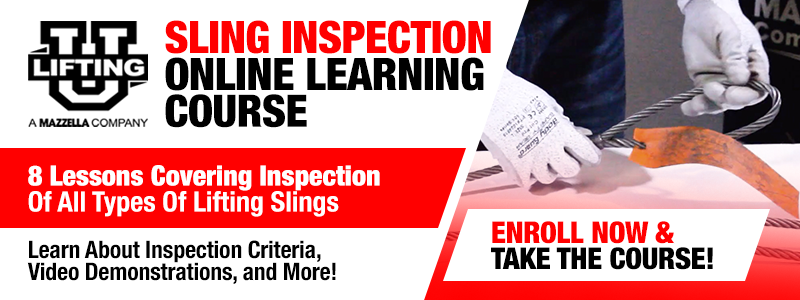
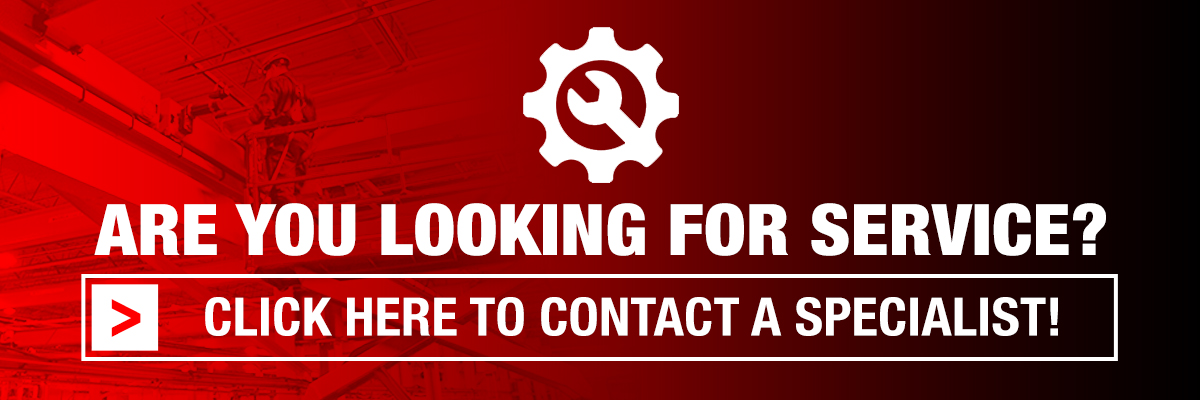
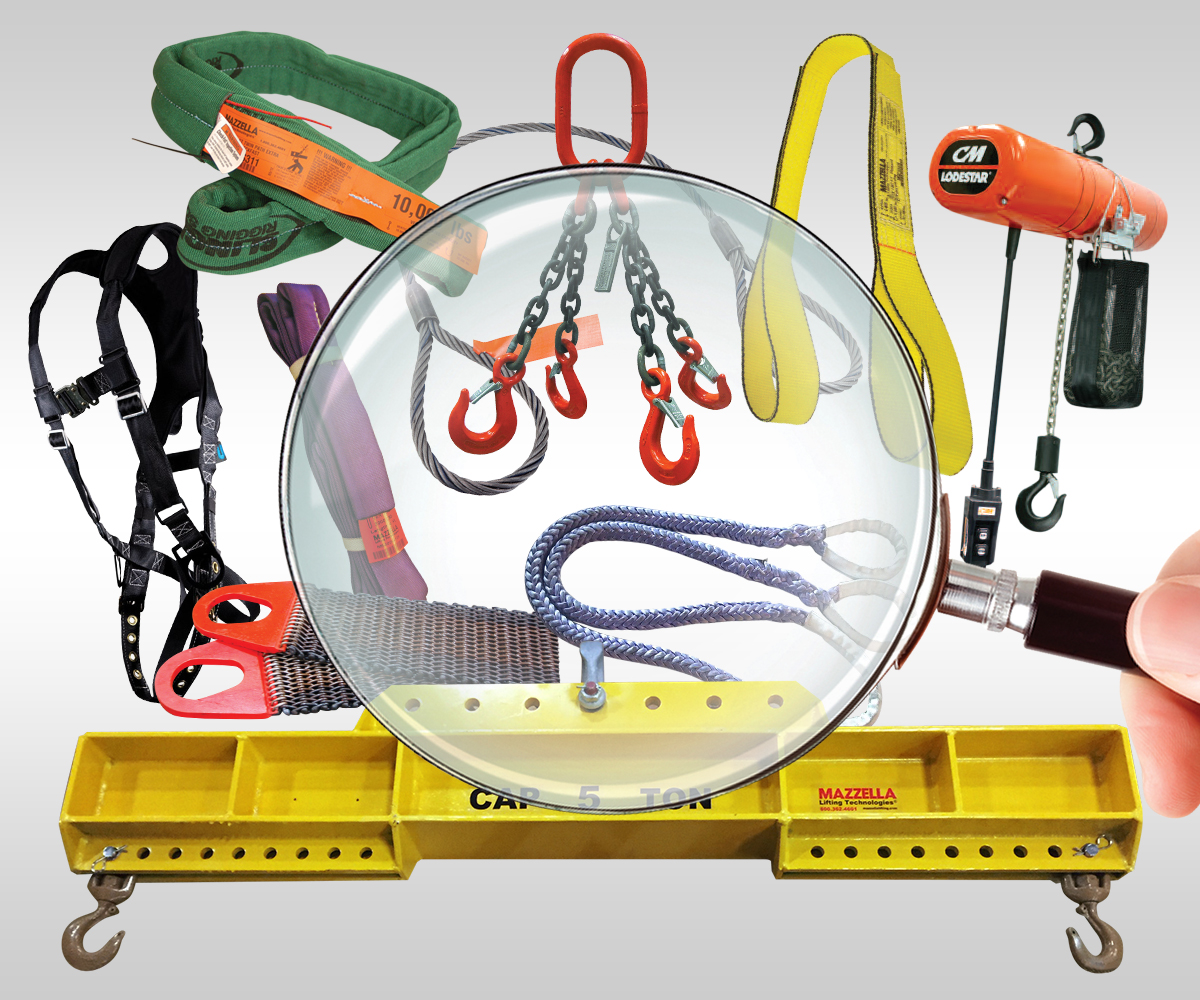
Rigging Inspection Services
OSHA 1910.184, ASME B30.9, B30.20, B30.26, & ANSI Z359 require periodic, documented inspections on slings, rigging hardware, lifting devices, and fall protection every 12 months, at minimum, and monthly to quarterly in more severe service conditions.
Call us at 800.362.4601 or click here if you need inspections for slings, rigging hardware, lifting devices, or fall protection!
Copyright 2018. Mazzella Companies.