How to Inspect Wire Rope Slings According to ASME B30.9 Standards
Understanding ASME standards will help to ensure the safety of the users, help extend the service life of the slings, and help reduce loss of production due to equipment downtime.
Do you know who is supposed to be inspecting your lifting slings? More importantly, do you know how often they’re inspecting them? OSHA and ASME have different inspection requirements, frequencies, and removal criteria for each type of sling—including alloy chain slings, synthetic slings, metal mesh slings, and wire rope slings.
At Mazzella, we understand the amount of effort and coordination it takes to stay current on industry standards and to develop an inspection program that keeps your business in compliance. Because of this, we have a dedicated business unit made of up highly-trained and qualified inspectors and technicians that focus only on rigging equipment inspections, industry compliance, and sling testing and repair.
In this article, our goal is to help you understand what is required to inspect wire rope slings to meet ASME standards, which in turn, will help to ensure the safety of the users, help extend the service life of the slings, and help reduce unnecessary equipment repair costs and loss of production due to equipment downtime.
Who Performs Wire Rope Sling Inspections and How Often Do They Occur?
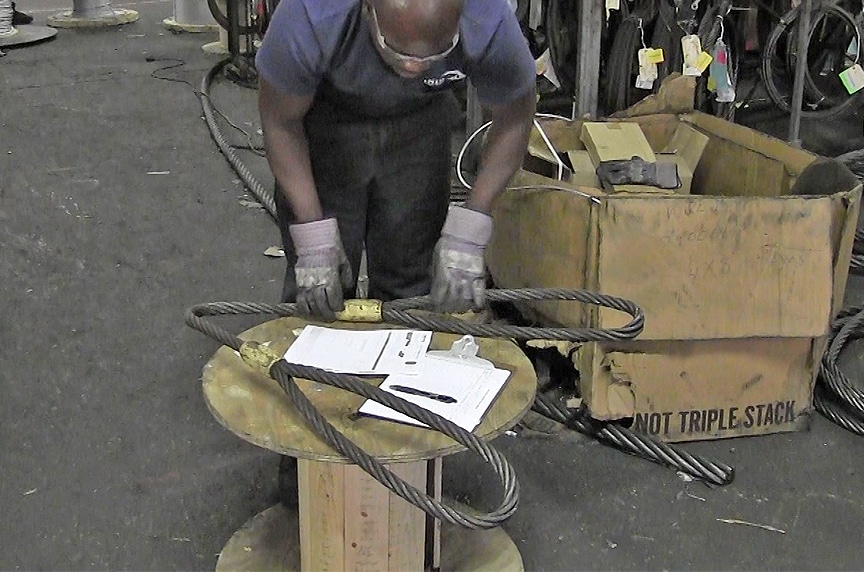
As a starting point, the same work practices which apply to all “working” wire rope apply to wire rope which has been fabricated into a sling. Therefore, a good working knowledge of wire rope design and construction will not only be useful, but essential in conducting a wire rope sling inspection.
There are two industry standards that exist to provide the end-user with guidelines for inspection and criteria that warrants removal from service: OSHA 1910.184 and ASME B30.9.
Initial Inspection (prior to initial use): Best practice is to inspect the wire rope sling upon receiving it from the manufacturer. Double-check the sling tag to make sure it’s what you ordered and that the rated capacity meets all of your project specifications and lifting requirements.
Frequent (daily or prior to use): Designate a Competent Person to perform a daily visual inspection of slings and all fastenings and attachments for damage, defects, or deformities. The inspector should also make sure that the wire rope sling that was selected meets the specific job requirements it’s being used for.
Users can’t rely on a once-a-day inspection if the wire rope sling is used multiple times throughout the day. Damage to wire rope can occur on one lift and best practice is to perform a visual inspection before any shift change or changes in lifting application. Because shock loads, severe angles, sharp edges, and excessive heat can quickly cause damage to a lifting sling, the user should inspect the sling prior to each lift.
Periodic Inspection: A periodic inspection is performed by either a professional service provider, or by a Qualified Person, every 12 months (at a minimum) and monthly to quarterly in more severe service conditions. The following are all determining factors in scheduling the frequency of a periodic inspection:
- Frequency of use
- Severity of service conditions
- Nature of the lifts being performed
- Experience gained on the service life of wire rope slings used in similar applications
ASME provides these additional periodic inspection guidelines based on the service of the wire rope sling:
- Normal Service – Yearly
- Severe Service – Monthly to Quarterly
- Special Service – As recommended by a Qualified Person
Depending on the severity of the operating environment and frequency of use, your business may decide to inspect wire rope slings more often than the minimum yearly requirement.
Periodic inspections are required to be documented per ASME B30.9 and records of those inspections retained.
The employer is required to maintain a record of the most recent thorough inspection—however, individual records for each sling that was inspected are not required. Failure to maintain and retain inspection records is one of the most common issues we see that can prevent a company from reaching full OSHA compliance.
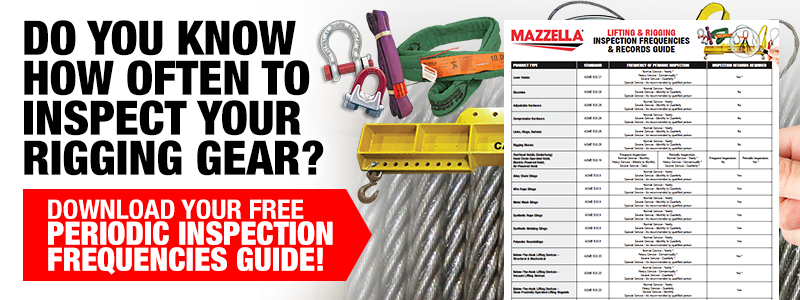
What’s Required on a Wire Rope Sling Identification Tag?
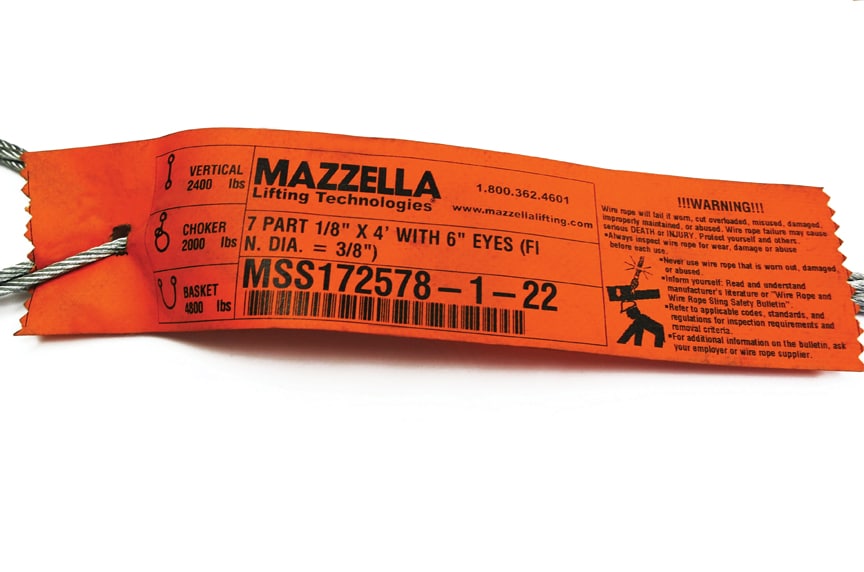
Per ASME B30.9, the wire rope sling tag on all new slings shall be marked by the manufacturer to include:
- Rated load for the types of hitches (single-leg vertical, choker, and basket) and the angle upon which they are based
- The diameter or size
- Name and trademark of the manufacturer
- Number of legs, if more than one
If the tag is missing or illegible, the inspector should remove the sling from service and send it to the manufacturer for current or updated certification, tagging, and testing.
Basic Inspection Criteria for Wire Rope Slings
The goal of a sling inspection is to evaluate remaining strength in a sling which has been used previously to determine if it is suitable for continued use. When inspecting wire rope slings, daily visual inspections are intended to detect serious damage or deterioration which would weaken the sling.
This inspection is usually performed by the person using the sling in a day-to-day job. The user should look for obvious things, such as broken wires, kinks, crushing, broken attachments, severe corrosion, etc. Any deterioration of the sling which could result in appreciable loss of original strength should be carefully noted and determination made on whether further use would constitute a safety hazard.
ASME B30.9 Standards Specify That a Wire Rope Sling Shall Be Removed from Service Immediately if Any of the Following Conditions Are Present:
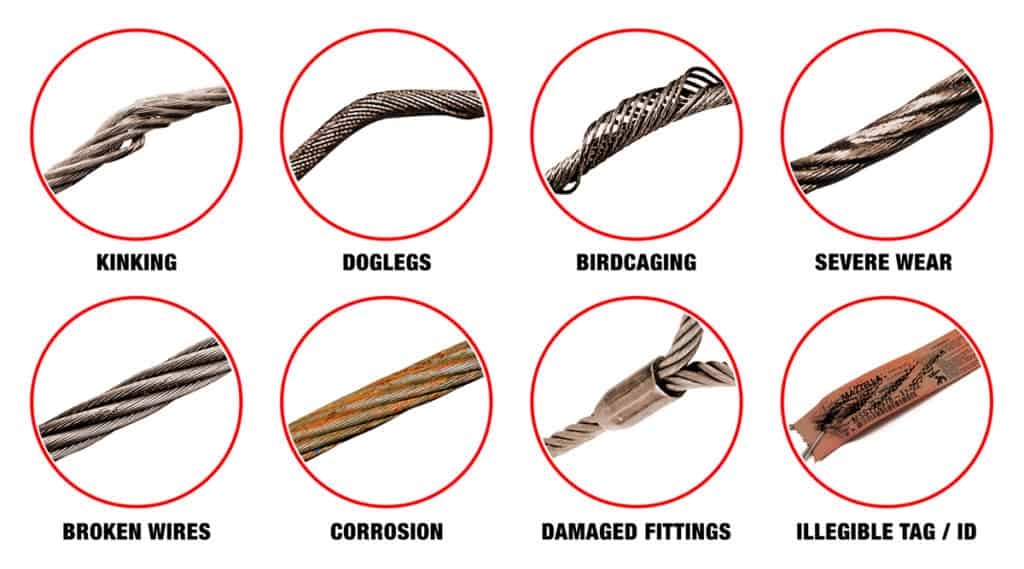
1. Missing or illegible sling identification. If the tag is missing or illegible, the inspector should remove the sling from service and send it to the manufacturer for current or updated certification, tagging, and testing.
2. Broken Wires: For strand-laid grommets and single-part slings, ten randomly distributed broken wires in one rope lay, or five broken wires in one strand in one rope lay. For cable laid, cable laid grommets and multi-part slings, use the following:
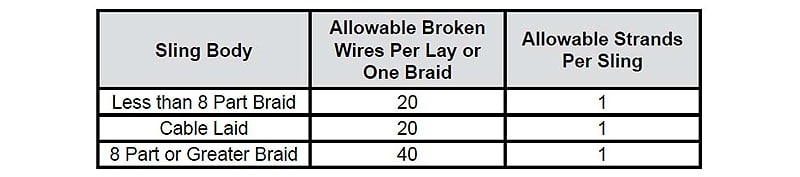
3. Distortion: Kinking, crushing, birdcaging or other damage which distorts the rope structure. The main thing to look for is wires or strands that are pushed out of their original positions in the rope.
4. Heat Damage: Any metallic discoloration, fusing of wires or loss of internal lubricant caused by exposure to heat.
5. Damaged End Attachments: Cracked, bent or broken end fittings caused by abuse, wear or damage.
6. Bent Hooks: No more than 5 percent over the normal throat openings, measured at the narrowest point from the plane of the unbent hook (see ASME B30.10 Hooks).
7. Corrosion: Severe corrosion of the rope or end attachments which has caused pitting or binding of wires should be cause for replacing the sling. Light surface rust does not substantially affect strength of a sling.
8. Pulled Eye Splices: Any evidence that eye splices have slipped, tucked strands have moved or pressed sleeves show serious damage may be sufficient cause to reject a sling.
9. Unbalance: A very common cause of damage is the kink which results from pulling through a loop while using a sling, thus causing wires and strands to be deformed and pushed out of their original position. This unbalances the sling, reducing its strength.
10. Kinks: Are tightened loops with permanent strand distortion that result from improper handling when a rope is being installed or while in service. A kink happens when a loop is permitted to form and then is pulled down tight, causing permanent distortion of the strands. The damage is irreparable and the sling must be taken out of service.
11. Doglegs: Are permanent bends caused by improper use or handling. If the dogleg is severe, the sling must be removed from service. If the dogleg is minor, (exhibiting no strand distortion) and cannot be observed when the sling is under tension, the area of the minor dogleg should be marked for observation and the sling can remain in service.
Disposal of Damaged or Failed Wire Rope Slings
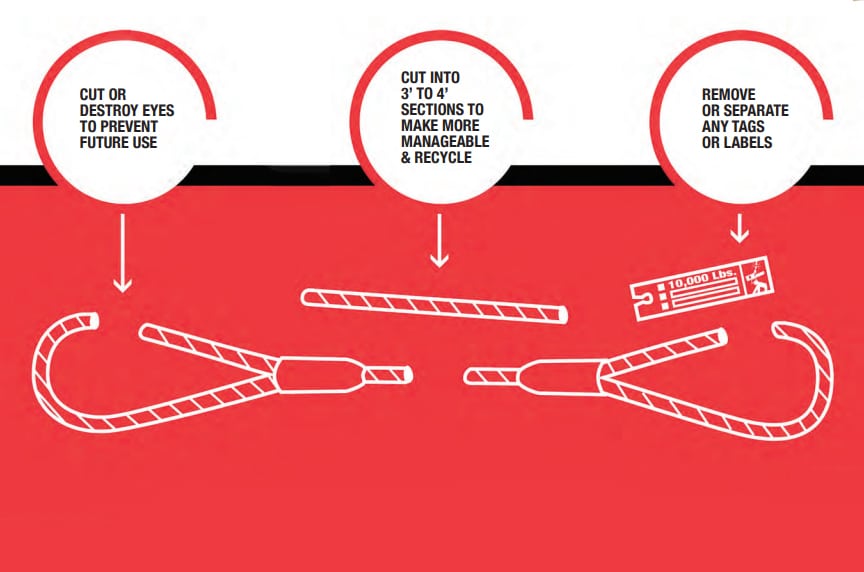
The best lifting and rigging inspection program is of no value if slings, which are worn out and have been retired, are not properly disposed of. When it is determined by the inspector that a sling is worn out or damaged beyond use, it should be tagged immediately DO NOT USE.
If it’s determined that the wire rope will be removed from service, we suggest cutting it down into more manageable sizes before discarding. This extra effort will help to accommodate the needs of most recycling facilities that will accept the damaged wire rope and also help to make sure that it cannot be used any further. Keep the following in mind when disposing of wire rope slings and wire rope cable:
- Cut into approximately 3’ to 4’ sections
- Use a chop saw or torch to cut, or destroy, the eyes of the wire rope sling to prevent any further use of the sling
- If the sling body is long enough to allow for an eye to be reformed by other means, the wire should be cut down to shorter lengths
- Use proper PPE when handling the pieces of cut wire—cut or frayed ends of the wire rope will be sharp
- Remove, or separate, any tags and labels from the sling
- Place scrap into your facility’s metal recycling bins and coordinate pickup or delivery
How to Inspect Wire Rope Slings
OSHA does not provide clear guidelines on how to properly and adequately inspect wire rope slings. It is up to the designated inspection personnel to know the requirements of the sling inspection standards, and to develop a comprehensive inspection protocol. Wire rope inspection should follow a systematic procedure:
- First, it is necessary that all parts of the sling are readily visible. The sling should be laid out so every part is accessible.
- Next, the sling should be sufficiently cleaned of dirt and grease so wires and fittings are easily seen. This can usually be accomplished with a wire brush or rags.
- The sling should then be given a thorough, systematic examination throughout its entire length, paying particular attention to sections showing the most wear.
- Special attention should also be paid to fittings and end attachments, and areas of the sling adjacent to these fittings.
- When the worst section of a sling has been located, this area should then be carefully checked against the OSHA and ASME criteria.
- Keep records of inspections that include dates and corresponding conditions of slings.
- Immediately dispose of slings that are rejected.
Best Practices for Maintaining Wire Rope Slings
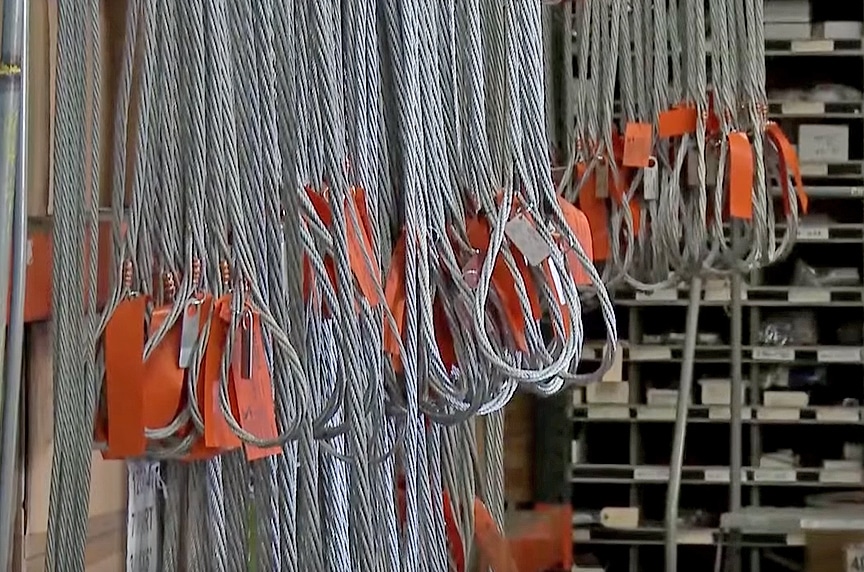
The best way to help extend the life of a wire rope sling, and help to ensure that it stays in service, is to properly maintain it during and in-between each use. Inspections are easier to perform—and probably more thorough—when slings are easily accessible and organized, kept off of the ground, and stored in a cool and dry environment.
- Hang slings in a designated area where they are off of the ground and will not be subjected to mechanical damage, corrosive action, moisture, extreme temperatures, or to kinking.
- When slings are exposed to extreme temperatures, follow the guidance provided by the sling manufacturer or a qualified person.
- Do not subject fiber-core wire rope slings to de-greasing or to a solvent because of possible damage to the core.
- Follow the manufacturer’s lubrication requirements.
Wire Rope Lubrication
Like any other machine, wire rope is thoroughly lubricated at time of manufacture. Normally, for sling use under ordinary conditions, no additional lubrication is required. However, if a sling is stored outside or in an environment which would cause corrosion, lubrication should be applied during the service life to prevent rusting or corroding.
If lubrication is indicated, the same type of lubrication applied during the manufacturing process should be used. Your sling manufacturer can provide information on the type of lubricant to be used and provide the best method of application. We recommend a wire rope lubricant that is designed to penetrate and adhere to the wire rope core.
Wrapping it Up
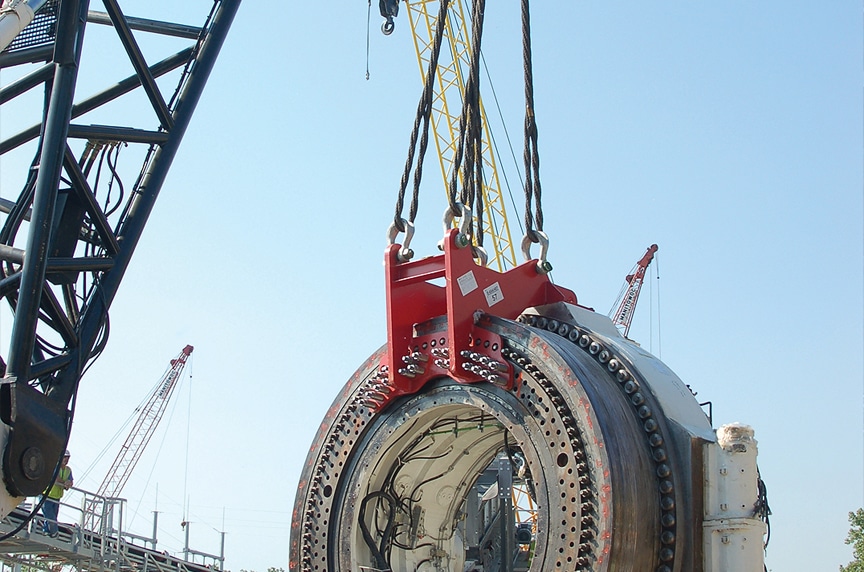
Proper inspection of your wire rope slings for damage or irregularities, prior to each use, is the best way to help keep everybody on the job site safe. Keep in mind that you’re planning to lift valuable and expensive equipment, and if a failure were to occur, it would not only cause unnecessary equipment repair costs and costly downtime, but also potentially jeopardize the lives of workers on site.
At Mazzella, we offer a variety of services including site assessments, rigging and crane operator training, sling inspection and repairs, overhead crane inspections and so much more. Our rigging inspection program is its own dedicated business unit with a team of inspectors that are certified through Industrial Training International to meet OSHA 1910.184 and ASME B30.9 requirements for sling inspection.
If you’re interested in learning more about our rigging inspection program and how we can help keep you in compliance with OSHA and ASME standards, contact us today to schedule a consultation or site assessment.
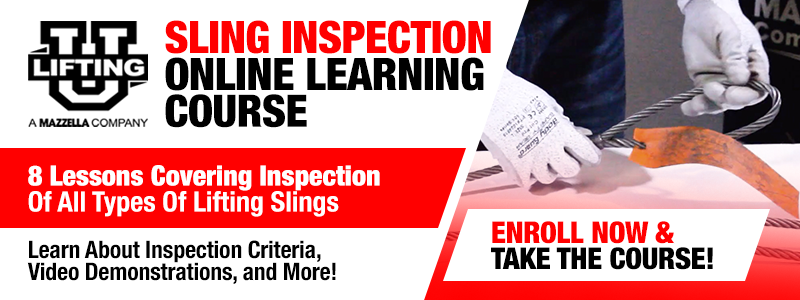
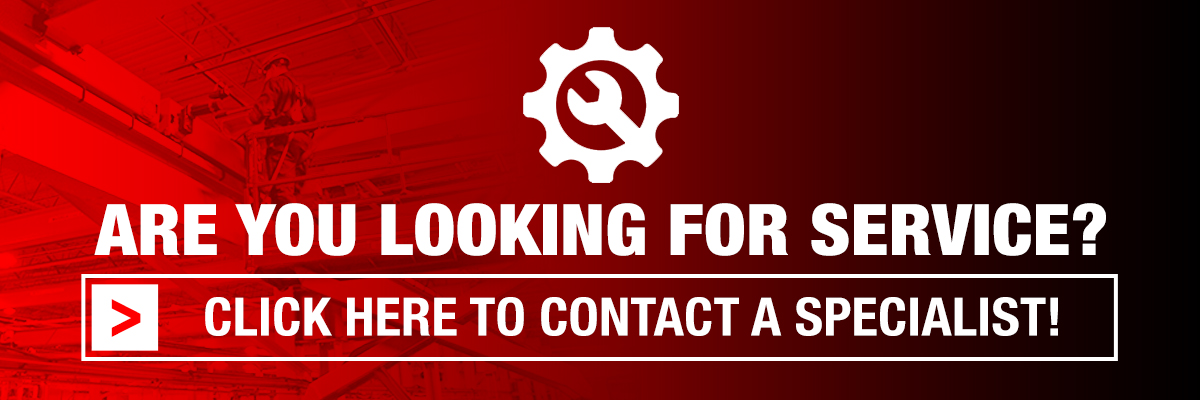
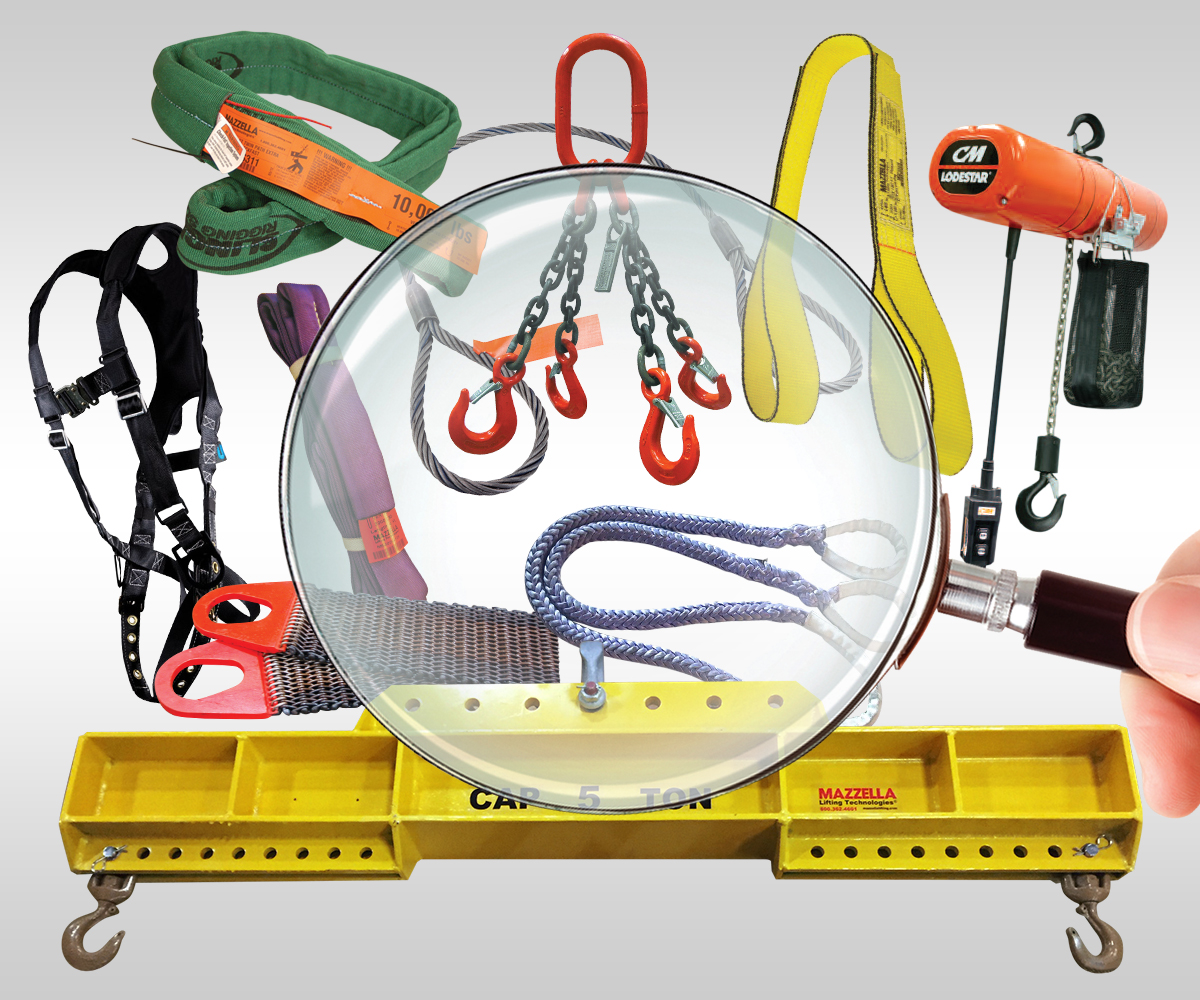
Rigging Inspection Services
OSHA 1910.184, ASME B30.9, B30.20, B30.26, & ANSI Z359 require periodic, documented inspections on slings, rigging hardware, lifting devices, and fall protection every 12 months, at minimum, and monthly to quarterly in more severe service conditions.
Call us at 800.362.4601 or click here if you need inspections for slings, rigging hardware, lifting devices, or fall protection!
Copyright 2018. Mazzella Companies.