When Do ASME Standards Require Proof Tests for Rigging Gear?
Regular proof testing of lifting slings is not required by ASME standards, but when are proof tests required for rigging gear? According to ASME standards, proof testing is required by the manufacturer prior to initial use.
“Is it time for proof tests, or is periodic inspections more in line with my company’s needs?”
Lifting and rigging specialists hear that question all the time, and understand there’s some confusion between the two.
A proof test is defined by the American Society of Mechanical Engineers (ASME) as a load test demonstrating the fitness of a load-bearing structure. However, not all pieces of lifting and rigging gear need this kind of testing.
While there’s not regularly mandated testing, there are situations where it’s warranted.
In this article, we’ll answer the following questions:
- Is a proof test necessary?
- What causes this confusion?
- When is a test required?
- Where would you need to do an on-site test?
- Why don’t most companies need mobile proof tests?
- What makes a mobile proof test cost prohibitive?
- How important is employee education?
Is a Proof Test Necessary?
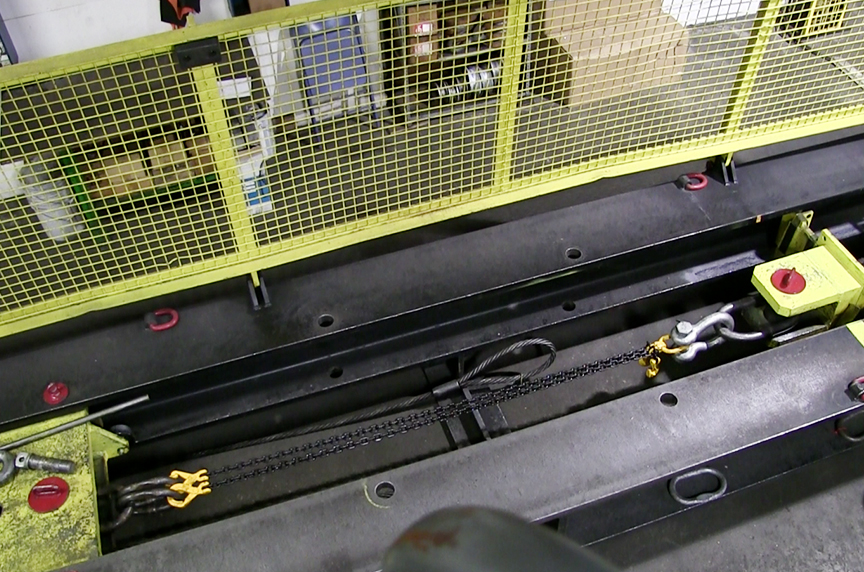
While our inspection technicians have found some scenarios where mobile proof testing is necessary, it’s extremely rare. If you’re dealing with off-shore businesses, a mobile proof test may be the best solution based on:
- Downtime
- Limited replacements on hand
- Difficulty in getting repairs done
However, most businesses only need a periodic inspection of their rigging gear. Our specialists have seen customers confuse inspections and proof tests. When service providers start asking questions, they discover most of the time, customers are substituting the words “proof test” for “visual inspection.”
If you’re inspecting to the ASME B30.9 Slings standard, there’s no requirement for any proof testing across any product whatsoever.
What Causes This Confusion?
It could be as simple as someone new taking over the inspection program, or internal standards requiring more stringent testing. Also, it may be how your company always has done their business, and have budgeted money to cover the costs.
During the initial meeting, it’s the job of the third-party inspection company to understand your situation. They should inform you on what process is needed, instead of conducting unnecessary proof testing.
Mazzella’s rigging inspectors will ask you many questions, including:
- Do you have any internal standards that define this process for you?
- Can we review those internal standards with you?
- Are you open to recommendations for changing your internal standards?
We’re trying to find out exactly what you need. Our process is comprehensive because we don’t believe in providing something you don’t actually need.
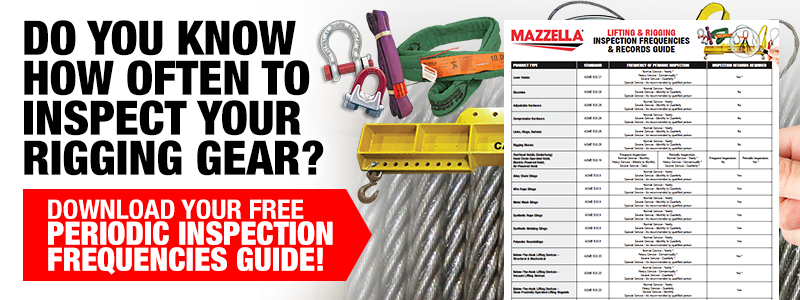
When is a Proof Test Required?
While regular proof tests are not required by any written standard from ASME or the Occupational Safety and Health Administration (OSHA), there are times when proof tests are required by ASME B30.9 Slings.
Before we do an inspection or proof test, we’re going to educate you on the differences between the two. During that process, we’ll help you identify which option is best for your business.
According to ASME Standards, these are situations where proof tests are required to be performed, by the sling manufacturer, before the sling is sold and put into service:
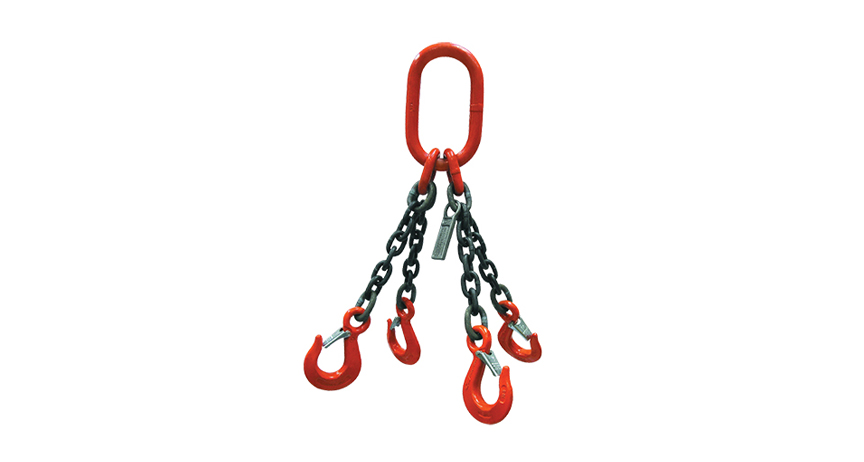
Alloy Steel Chain Slings
“Prior to initial use for all new and repaired chain and fittings of an alloy steel chain sling shall be proof tested either individually or as an assembly by the sling manufacturer or a qualified person.”
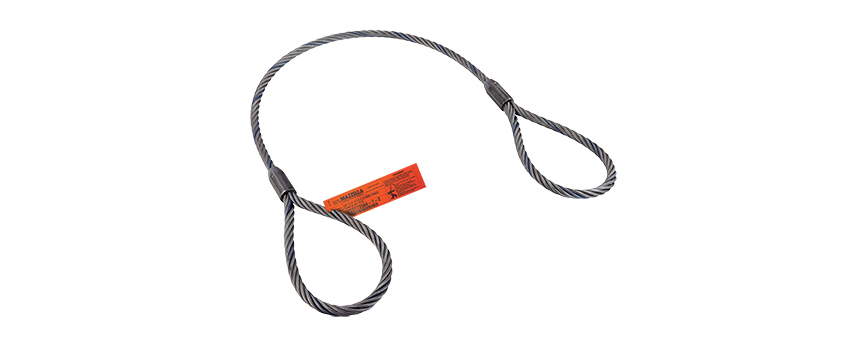
Wire Rope Slings
“Prior to initial use, all new swaged socket, poured socket or turnback swaged eye type slings, and mechanical joint endless wire rope slings shall be proof tested by the sling manufacturer or a qualified person.
“Prior to initial use, all wire rope slings incorporating previously used or welded fittings and all repaired slings shall be proof tested by the sling manufacturer or a qualified person.
“All other new wire rope slings are not required to be proof tested unless specified by the purchaser.”
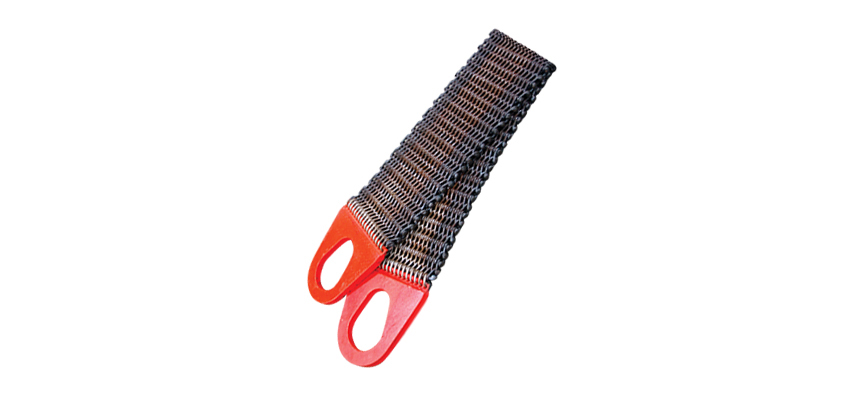
Metal Mesh Slings
“Prior to initial use, all new and repaired metal mesh slings shall be proof tested by the sling manufacturer or a qualified person.
“Coated slings should be proof tested prior to coating.”
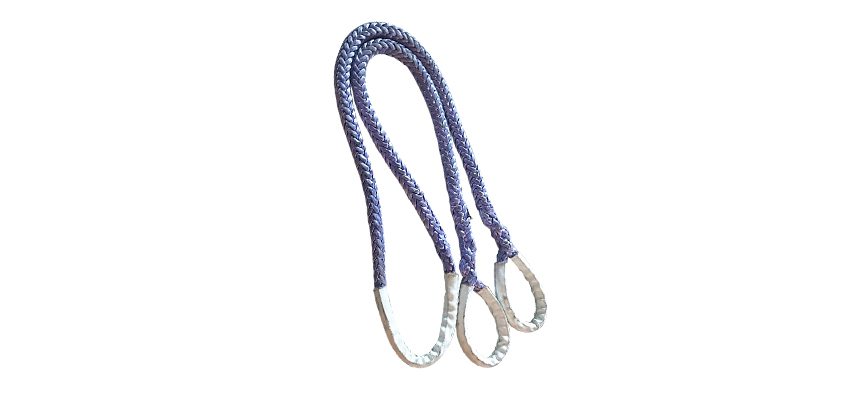
Synthetic Rope Slings
“Prior to initial use, all synthetic fiber rope slings incorporating previously used or welded fittings and all repaired slings shall be proof tested by the sling manufacturer or a qualified person.
“All other new synthetic fiber rope slings and fittings are not required to be proof tested unless specified by the purchaser.”
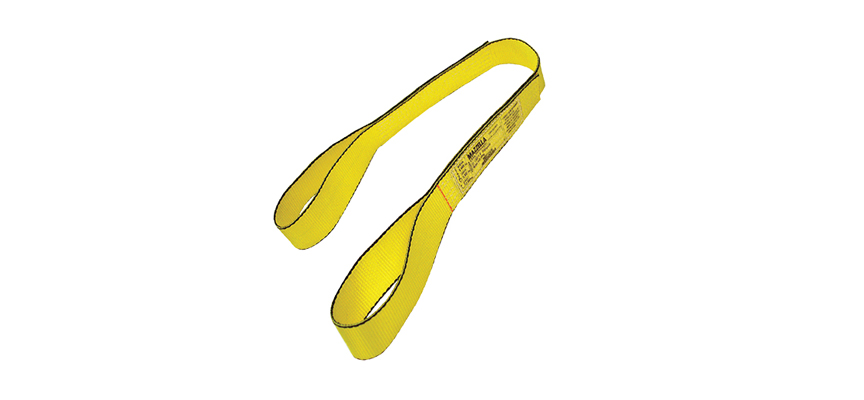
Synthetic Webbing Slings
“Prior to initial use, all synthetic webbing slings incorporating previously used or welded fittings and all repaired slings shall be proof tested by the sling manufacturer or a qualified person.
“All other new synthetic webbing slings and fittings are not required to be proof tested unless specified by the purchaser.”
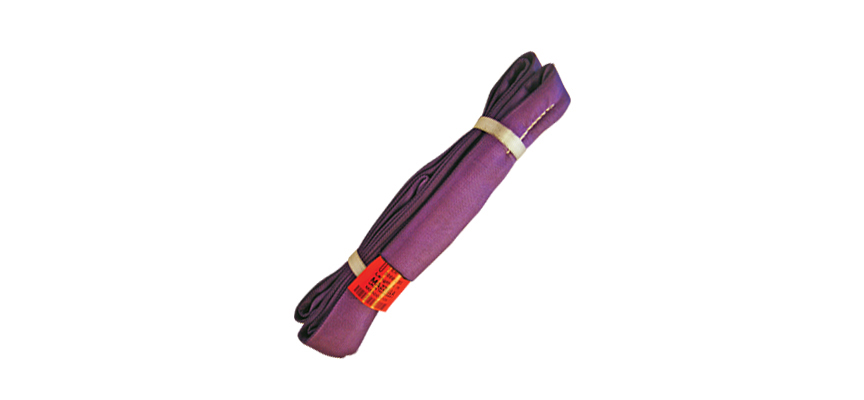
Polyester Roundslings
“Prior to initial use, all polyester roundslings incorporating previously used or welded fittings and all repaired slings shall be proof tested by the sling manufacturer or a qualified person.
“All other polyester roundslings and fittings are not required to be proof tested unless specified by the purchaser.”
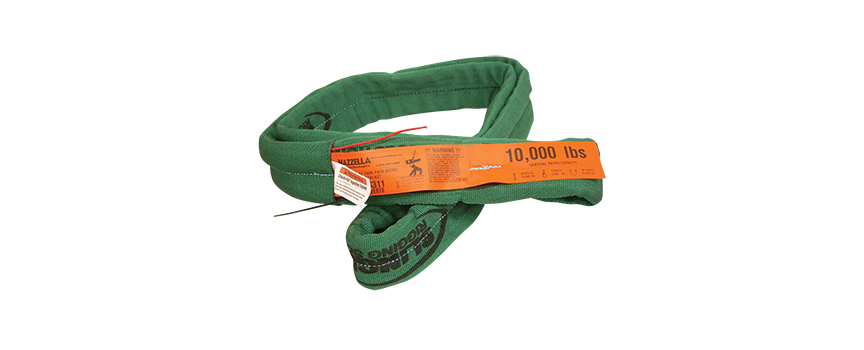
High Performance Roundslings
“Prior to initial use, all HP roundslings incorporating previously used or welded fittings and all repaired slings shall be proof tested by the sling manufacturer or a qualified person.
“All other new HP roundslings and fittings are not required to be proof tested unless specified by the purchaser.”
Why would you need to do an on-site proof test?
Many offshore oil companies have internal standards requiring all cargo to have tags indicating it’s been proof tested in the last year. Employees are instructed not to accept any cargo that doesn’t have the required tagging on wire rope slings.
If it’s not because of your unique circumstances, you may have an internal policy that requires it. We’re going to review that internal standard with you to make sure you don’t just need a periodic inspection.
Why don’t most companies need proof tests in the field?
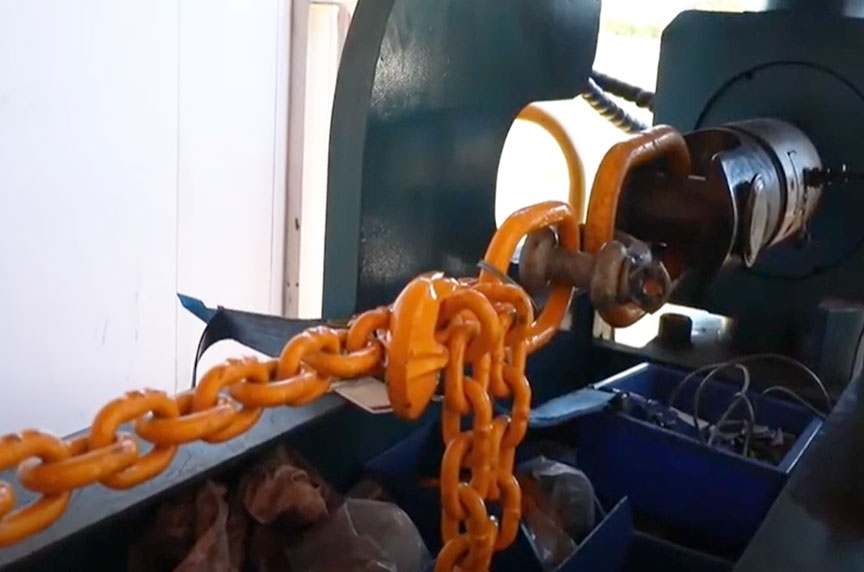
First and foremost, there’s nothing within the ASME standards outlining the need to regularly proof test rigging equipment.
The energy (and expenses) you’d put in for unnecessary tests could be redirected to proper employee training.
If your employees are doing the required visual inspections, and you’re keeping up with the periodic inspections, that’ll give you what you need if your employees are properly rigging your slings.
You want to make sure you’re making the safest lifts, and that’s why pre-shift inspections are important. You don’t want something done on second or third shift that may be incorrect, and then, impact your lifts.
Mobile Proof Tests Are Often Cost Prohibitive
Before hiring a mobile proof testing service, be sure to understand the factors that influence the cost.
Those factors include:
- Transportation to/from your facility
- Setup/tear down of equipment
- Troubleshooting
- Downtime
- Potential need for outside services
- Necessary equipment to help with setup/teardown
Mazzella’s vertical proof testing machine is a 50,000-lbs. unit that stands more than 12’ tall. We must unhook it from the electrical supply (440/3-phase), and unplug from the computer software in our facility. At the customer facility, it needs to be connected to the internet so it can be functional.
You need a tow motor with long enough forks (between 8’ and 10’) to lift the proof tester and its cylinders off the trailer. This is a time-consuming process, and the price needed to set up for, conduct, and then, tear down after conducting the test is paid by the customer.
We’re here to identify the questions you need to ask and understand why doing a mobile test is a challenge. It’s different than you sending in rigging gear for a test. We understand that’s not always possible. However, we want you to consider the following question before making a final decision:
“Are you going to get what you’re paying for?”
How Important Is Employee Education?
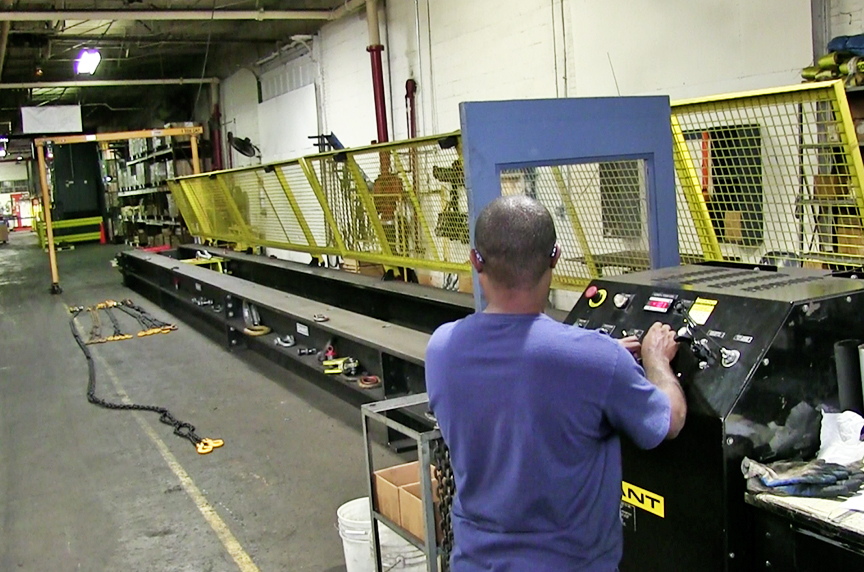
Education is important because there’s much at stake for your company with proof tests.
Mazzella does due-diligence before conducting these tests because there’s a significant price difference from periodic inspections. Depending on your amount of rigging gear, it may require one or several inspectors coming to your facility for inspections.
If equipment needs to be shipped for a mobile test, you’re looking at a multi-day investment just to get what is necessary on-site. Plus, with expenses for the inspectors doing the tests, the price compounds. That could cost you significantly more money than a required visual inspection.
Educating your employees on the proper maintenance and care for lifting gear will help the rigging equipment last longer. Also, employees may avoid serious injury/death if rigging gear fails during a lift.
What Are My Next Steps?
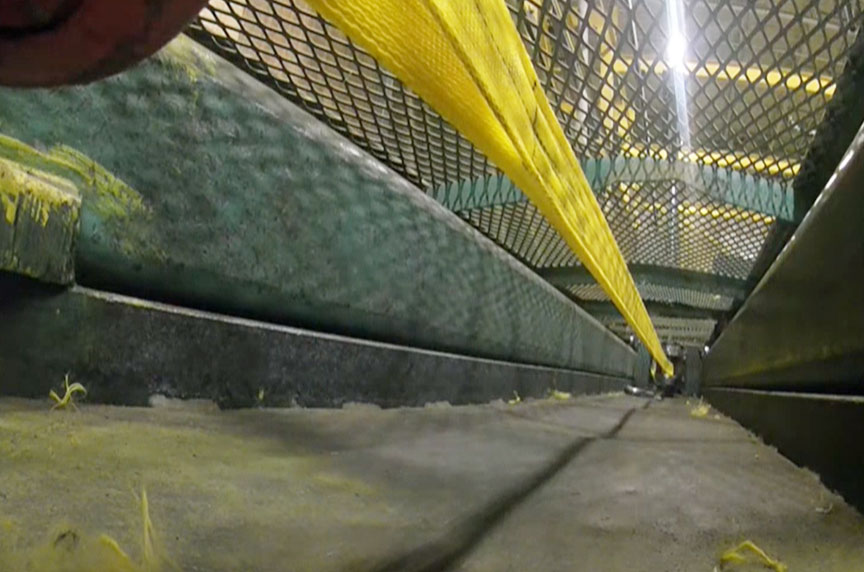
The next step is the first one, and that’s reaching out to a third-party rigging inspection company.
At Mazzella, we’ll take the time to understand your situation and make recommendations on what you need. In addition to performing inspections, we can customize any kind of training needed based on your lifting applications.
One of our trainers can come to your facility, watch what you’re doing, and gain an understanding of your needs. We’ll give you feedback after observing your practices/internal policies, and figure out where training is needed.
Training could be needed in:
- Rigging best practices
- Inspections of rigging gear
- Types of inspections required
It comes down to you being open to that conversation, and then, willing to incorporate it into your culture.
Call us at 800.362.4601 or click here to speak with a rigging specialist about what you need to be in compliance with ASME standards.
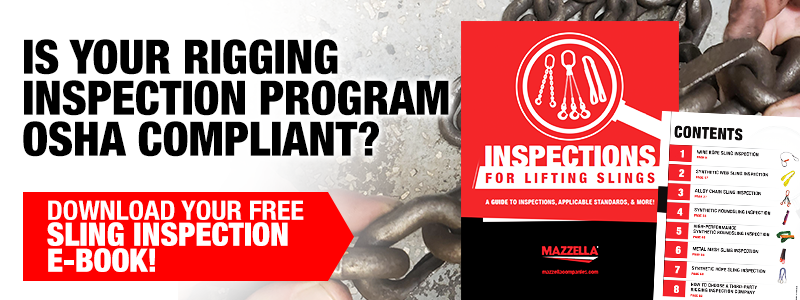
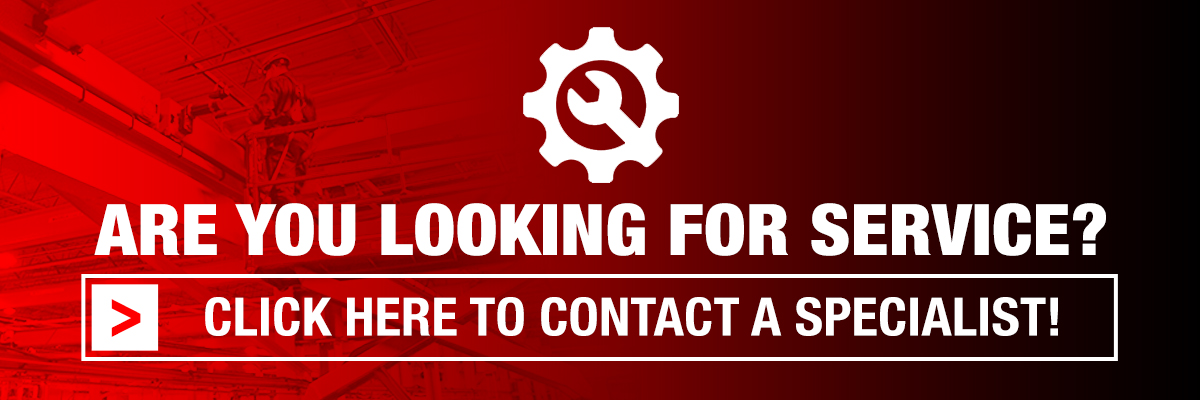

Rigging Inspection Services
OSHA 1910.184, ASME B30.9, B30.20, B30.26, and ANSI Z359 require periodic, documented inspections on slings, rigging hardware, lifting devices, and fall protection every 12 months, at minimum, and monthly to quarterly in more severe service conditions.
Our team of rigging inspectors are certified to make sure your products meet OSHA and ASME requirements.
Copyright 2021. Mazzella Companies.