5 Reasons Your Lifting & Rigging Program Isn’t OSHA/ASME Compliant
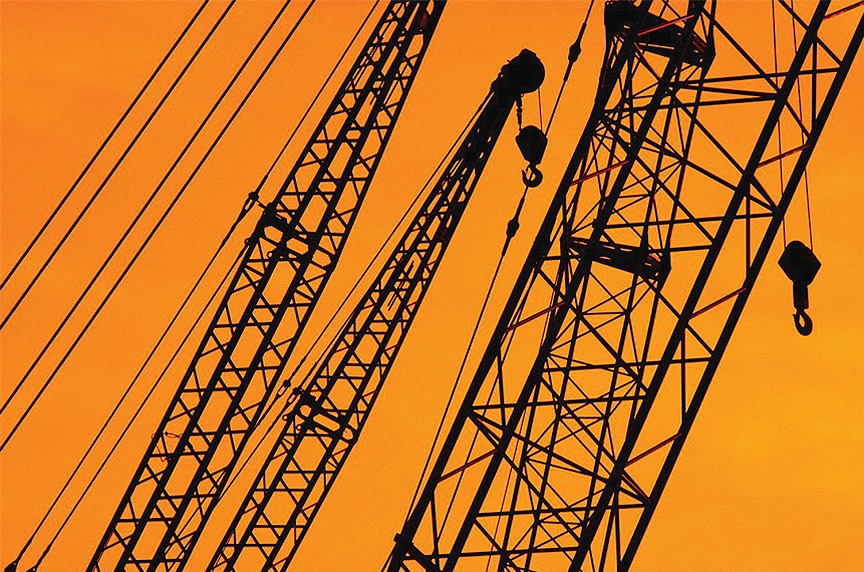
Those that have been in the lifting and rigging industries for a while will remember that years ago, sling and rigging inspections would frequently uncover mangled slings, homemade and unrated hooks and spreader beams, knotted chain slings, and off-the-shelf bolts used for shackle pins. At the time, OSHA wasn’t the ubiquitous entity that they are now and our society was less litigious. Working in dangerous environments seemed to be a risk that some workers and employers were willing to take to earn a living and operate profitably.
Now, fast forward to today’s working environment and it has vastly improved, particularly from a lifting and rigging standpoint. Whether lifting and rigging safety has improved because of insurance penalties, OSHA presence, education, or an overall appreciation for worker safety, it has improved over time.
Today, we rarely see the atrocities to the extent that we saw them in the past. What we see today are companies that make an effort to follow lifting and rigging standards and best practices, but instead are almost OSHA compliant.
Why would a company put effort into being 70-80% compliant and not reach full compliance? The reasons are numerous, but could be due to any of the following:
- Lack of knowledge or understanding of the standards
- Additional costs related to reaching compliance
- Business or operational processes that make it difficult to reach full compliance
Let’s face it, nobody wants to receive a grade of a B or C when it comes to safety—the only acceptable grade is an A. In this article, we’ll share some observations from the field that have kept our customers from reaching full compliance with industry standards and prevented them from offering a safe work environment for their employees.
As we go through these common observations, we hope that you look inward at your work environment and your company’s best practices, and determine if you’re in full compliance or falling just short of 100% safety and compliance.
Top 5 Reasons Your Lifting and Rigging Program Is Not OSHA or ASME Compliant
1. Failure to Inspect ALL Rigging Equipment
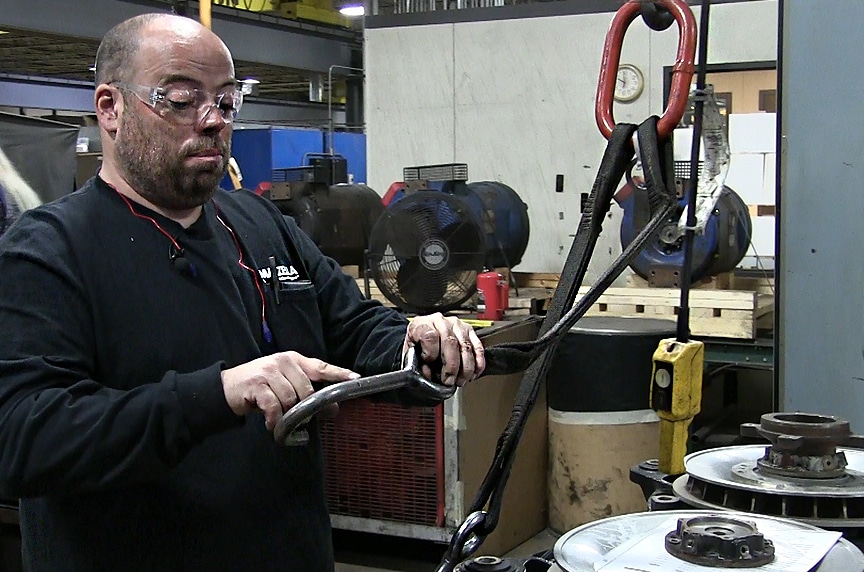
What we see:
Companies are compliant in inspecting their lifting slings, but ignore their rigging hardware including shackles, eye bolts, hoist rings, etc.
What we hear:
- “We have racks, buckets, and bins of hardware…it would take forever to go through it.”
- “We don’t use them.”
- “The hoist rings are always connected to the (die, fitting, machinery) so we forget to have it inspected.”
- “If they’re bad, we throw them out.”
What the standard says (ASME B30.26—Rigging Hardware):
“A visual inspection shall be performed by the user or designated person each day before the rigging hardware is used. A periodic inspection shall be performed by a designated person, at a minimum of once every 12 months. The rigging hardware shall be examined and a determination made as to whether they constitute a hazard. Written records are not required. Semi-permanent and inaccessible locations where frequent inspections are not feasible shall have periodic inspections performed…”
Just because you have a lot of hardware doesn’t exempt you from inspecting them. The OSHA and ASME standards specify that ALL rigging equipment shall be examined—regardless of quantity, usage, location, or application. All sling hooks, hoist rings, shackles, swivels, and eye bolts should be inspected.
2. Failure to Inspect Nylon Web Slings
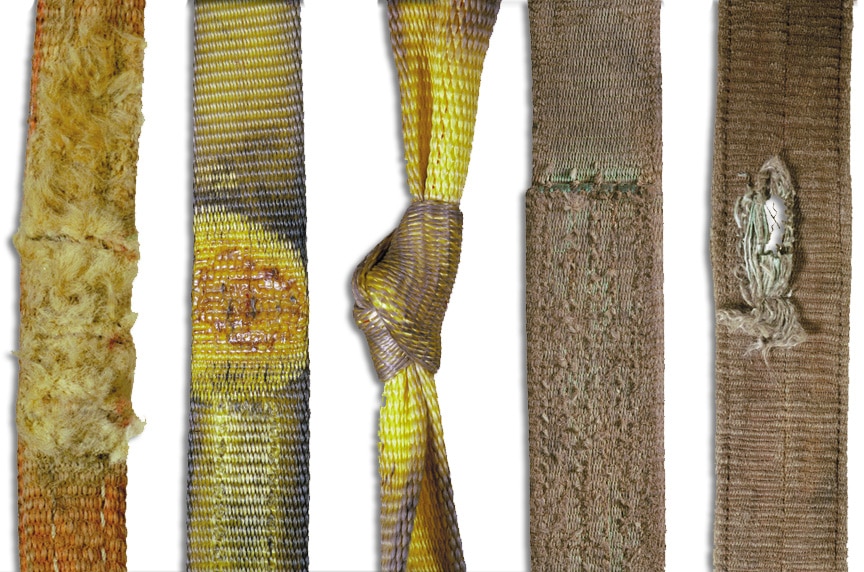
What we see:
Companies follow protocol and industry standards for the inspection of wire rope slings, chain slings, and synthetic roundslings, but don’t have their web slings inspected regularly, or don’t maintain records of these inspections.
What we hear:
- “We go through those like water, they don’t last long enough to inspect.”
- “We don’t get them repaired, so we don’t inspect them.”
- “When we see one is damaged, we just go get a new one.”
What the standard says (ASME B30.9—Slings):
“A visual inspection for damage shall be performed by the user or designated person each day or shift the sling is used. A complete inspection for damage shall be performed periodically by a designated person, at least a minimum of at least every 12 months. Written records of most recent periodic inspection shall be maintained.”
With one of our customers who normally did not inspect web slings because they felt they “never last long enough for a periodic inspection,” we did a sample inspection of some of their web slings. We traced the serial numbers with our inspection records and found that some of the web slings had been in regular use for 3 years without any inspection documentation—a clear non-conformance of the B30.9 standard.
To make matters worse, some of the slings were in terrible condition and were removed from service and disposed of. Needless to say, the customer had us include the nylon web slings in their periodic inspections going forward. They went from “almost compliant” to fully compliant to the B30.9 standard.
3. Failure to Inspect Below-the-Hook Devices
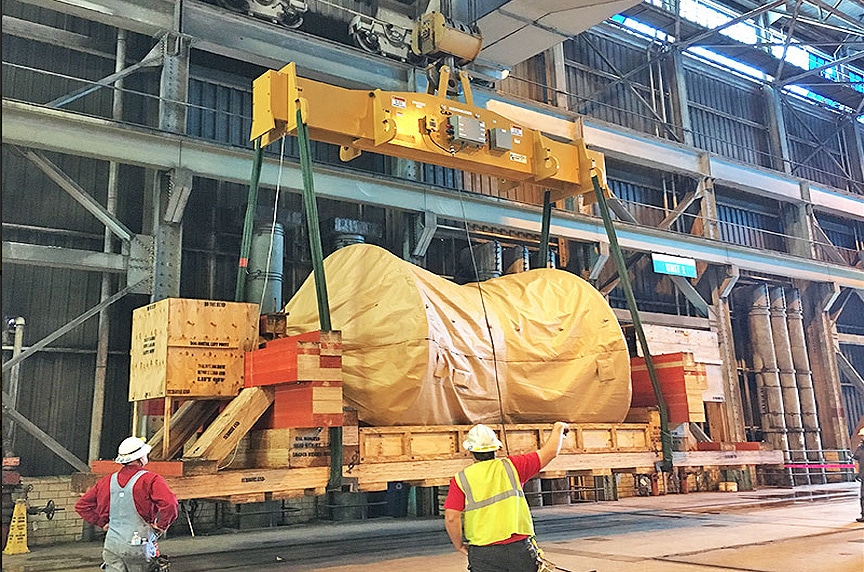
What we see:
End users conduct periodic sling inspections but don’t inspect their spreader beams, lifting beams, coil hooks, or other below-the-hook lifting devices.
What we hear:
- “We didn’t realize you had to inspect lifting beams…”
- “We only use them on large picks.”
- “We have had those (C- hooks, spreader beams, lifting tongs, etc) for twenty years and never had any problems.”
What the standard says (ASME B30.20—Below-the-Hook Lifting Devices):
“Inspection by the operator before and during each lift made by the lifter. (2) Frequent Inspection. Visual examinations by the operator or other designated persons with records not required. (a) Normal service — monthly (b) Heavy service — weekly to monthly (c) Severe service — daily to weekly (d) Special or infrequent service — as recommended by a qualified person before and after each occurrence (3) Periodic Inspection. Visual inspection by a qualified person making records of apparent external conditions to provide the basis for a continuing evaluation. An external code mark on the lifter is an acceptable identification in lieu of records. (a) Normal service for equipment in place — yearly (b) Heavy service [as in (a) above, unless external conditions indicate that disassembly should be done to permit detailed inspection] — semiannually (c) Severe service [as in (b) above] — quarterly (d) Special or infrequent service — as recommended by a qualified person before the first such occurrence and as directed by the qualified person for any subsequent occurrences.”
B30.20 also states in paragraph 20-1.3.6:
“Dated inspection reports shall be made on critical items such as those listed in para. 20-1.3.4. Records should be available to appointed personnel for each periodic inspection and when the lifter is either modified or repaired.”
As you can see, the standard is no easy read—which may be another contributing factor for not inspecting below-the-hook devices. However, a simple interpretation of the standard could be, “inspect and document the inspection for all below-the-hook lifting devices.”
It is interesting to note that we regularly observe end users in OSHA an ASME compliance for overhead crane inspection, mobile crane inspection, and rigging inspections, but not for their below-the hook-lifting devices—used directly in between the crane and the slings.
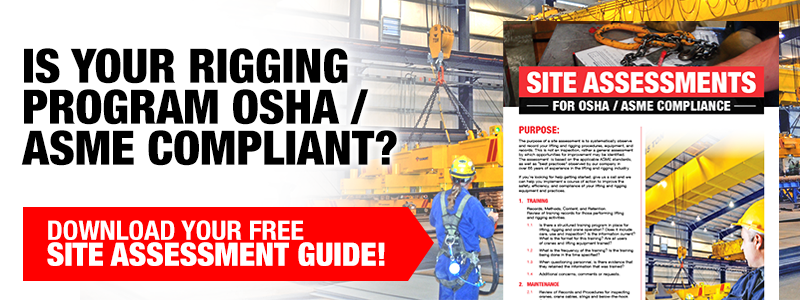
4. Failure to Inspect Fall Protection Equipment
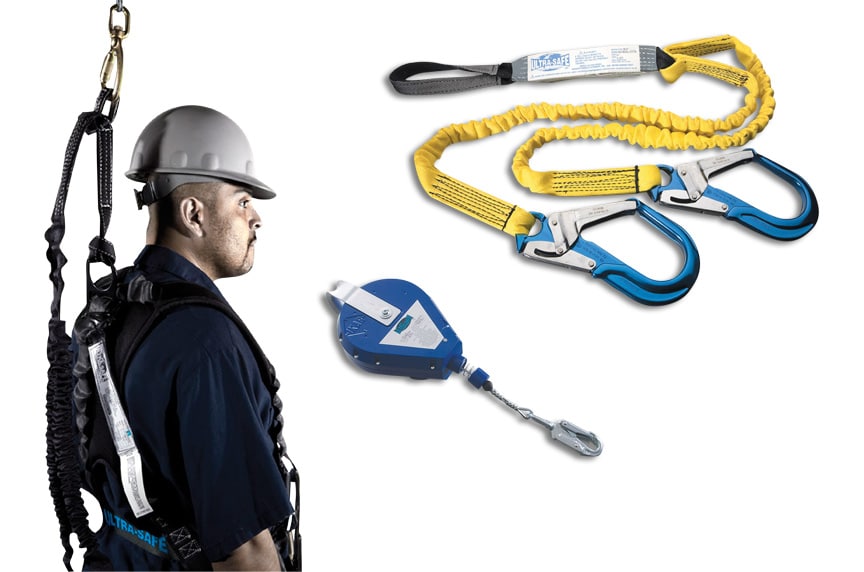
What we see:
Lanyards, harnesses, and retractables are not being inspected.
What we hear:
- “This is my own personal harness, the company didn’t buy it for me.”
- “I only use my PPE a few times a year.”
- “I only use it when I’m in the scissor lift.”
- “I thought you only had to inspect it if you fall.”
What the standard says (ANSI/ASSE Z359.2-2017—Minimum Requirements for a Comprehensive Managed Fall Protection Program):
“Fall protection equipment shall be inspected by the authorized person at least once at the beginning of each 8-hour shift in which it is used to verify that it has not sustained any wear or damage that would require its removal from service. Fall protection and fall rescue equipment shall be inspection on a regular basis not to exceed one year (or more frequently if required by the manufacturer’s instructions) by a competent person or a competent rescuer, as appropriate, to verify that the equipment is safe for use.”
You would hope that you or your co-workers never have to use fall protection for what it was designed to do. But if you did, wouldn’t you want to make sure that it’s in good working condition prior to each shift?
5. Failure to Maintain Inspection Records on Lifting Equipment
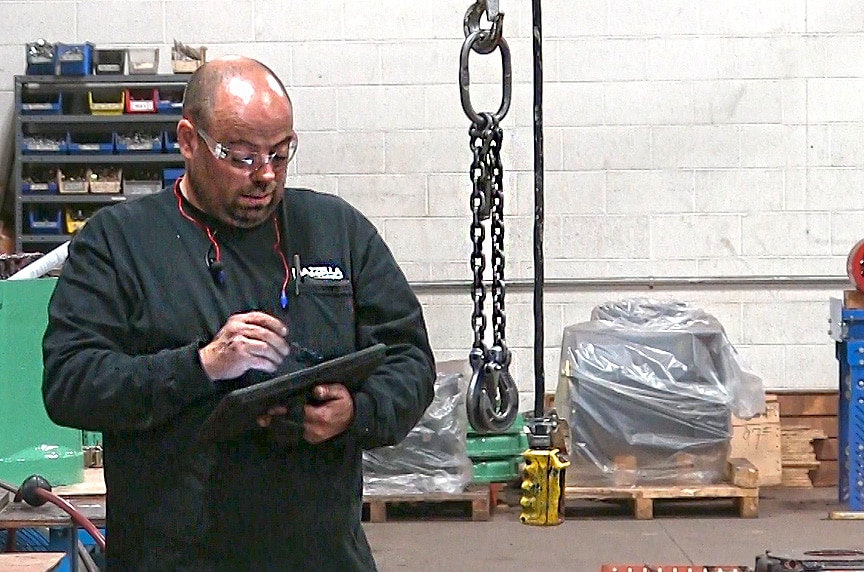
What we see:
Job sites and mobile crews have no inspection documentation or records to show for their lifting equipment.
What we hear:
- “Once we send lifting equipment out to a job site, it never comes back…we send it straight to the next job.”
- “Our service crews are always on the road and never in the yard when we do our inspections.”
What the standards say:
There are multiple standards that relate to the documentation of lifting and rigging equipment inspection, as well as standards for how long those records should be retained. If you have questions about what lifting equipment you need documented inspections for, and how long the inspection records should be retained for, refer to the applicable ASME, OSHA, or CMAA standards for:
- Overhead Cranes
- Slings (chain, wire rope, synthetic, etc.)
- Below-the-Hook Lifting Devices
- Rigging Hardware
- Fall Protection
The applicable standards still apply, whether the lifting equipment is in your shop, your yard, in a truck, or on a job site. We’ve also seen companies who have their slings and rigging equipment inspected at their yard or facility, but are unable to pry loose the rigging equipment that’s squirreled away in personal lockers, cabinets, and job boxes.
Apparently, the logic is that users would rather use potentially dangerous lifting equipment that has never been inspected, rather than getting it inspected, having it fail the inspection, and having to replace it.
Often, end users emotionally attach themselves to their rigging gear like their favorite flannel shirt and never want to give them up. Another type of product that has this same type of “hands off” personal attachment is fall protection equipment.
Wrapping it Up
Craig D. Lounsbrough said, “We know enough to know that all of this is not quite right. And we know enough to know that settling for what’s not quite right is quite wrong.”
Don’t settle with being almost ASME and OSHA compliant when it comes to rigging and lifting safety. At Mazzella, one of the services that we offer our customers is a Site Assessment of their job site or industrial facility.
We work with our customers to help improve their lifting and rigging practices by focusing on the following items:
- Training – records, methods, content, and retention
- Equipment
- Maintenance
- Purchasing and Inventory
- Application and Facility Review
The results of these assessments are for your eyes only, and are not meant to provide a “gotcha” moment. Rather, your site assessment can be looked at as a learning experience and can spark a conversation on how to improve the safety, efficiency, and OSHA and ASME compliance of your rigging equipment and practices.
If you think your program is “not quite right,” contact a Lifting Specialist and we can perform a site assessment to get you on your way to 100% compliance and a safer work place.
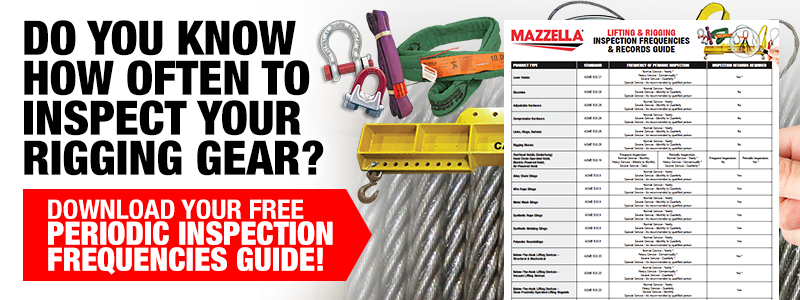
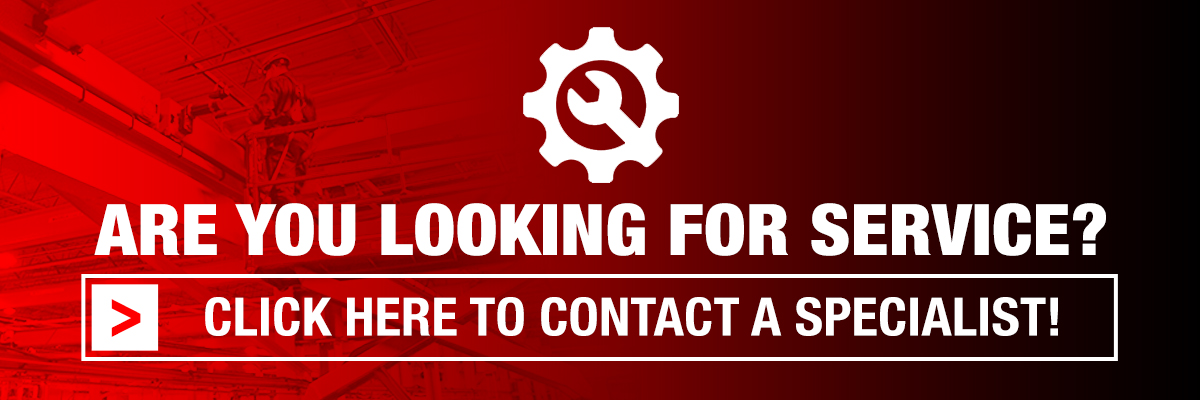
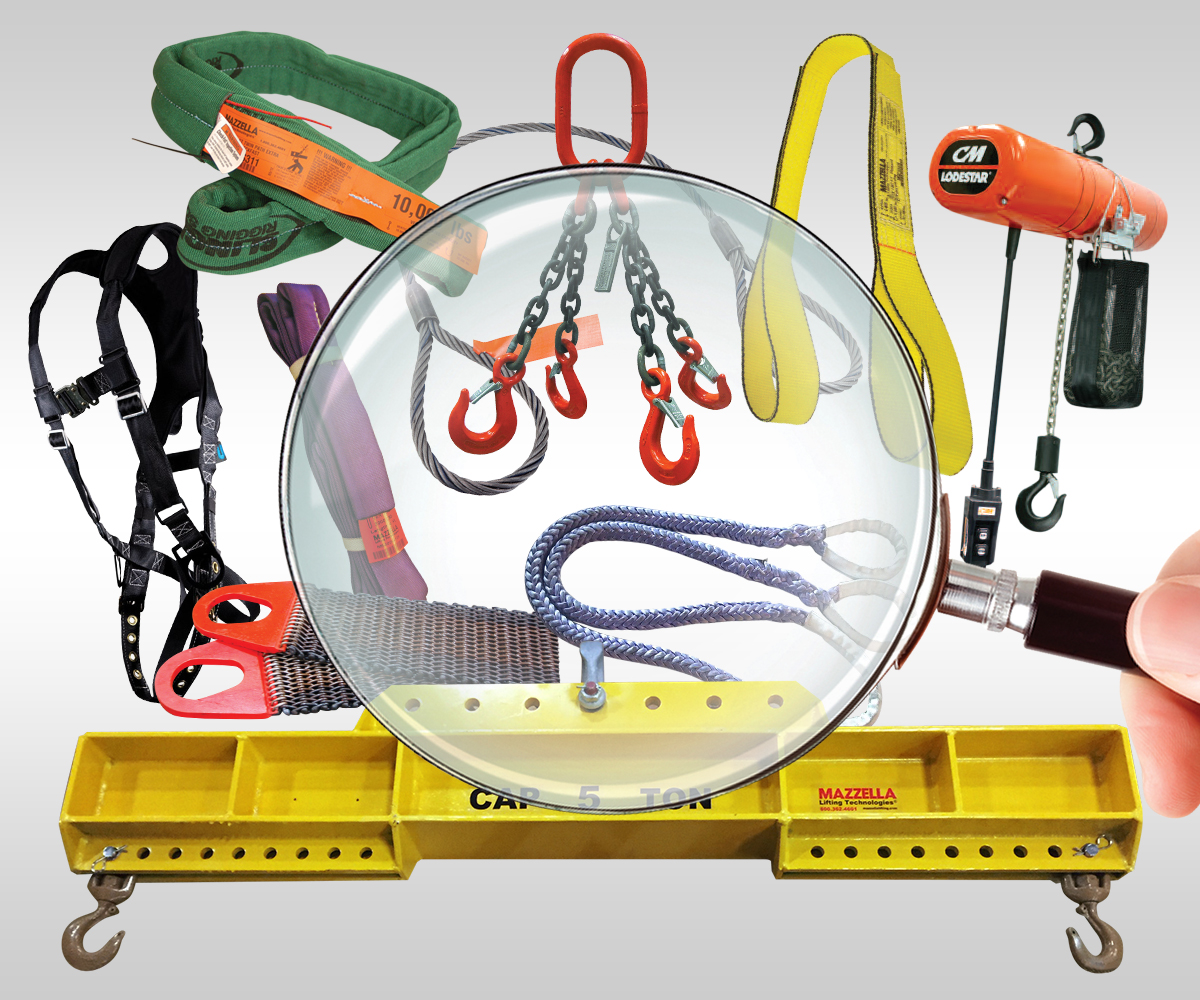
Rigging Inspection Services
OSHA 1910.184, ASME B30.9, B30.20, B30.26, & ANSI Z359 require periodic, documented inspections on slings, rigging hardware, lifting devices, and fall protection every 12 months, at minimum, and monthly to quarterly in more severe service conditions.
Call us at 800.362.4601 or click here if you need inspections for slings, rigging hardware, lifting devices, or fall protection!
Copyright 2017. Mazzella Companies.