Which CMAA Crane Service Classification is Best for Your Business?
If you put a little bit of thought and consideration into how often you will be using an overhead crane, how hard your overhead crane will have to work, and the type of environment that your crane will be working in, you can get a pretty good sense of what type of crane duty cycle or service class will be best for your business or facility.
Selecting the right CMAA crane service classification, or duty cycle, for an overhead crane is critical for a customer who is trying to balance the initial investment of a crane system with the cost of future maintenance that will be required.
These four factors are the most important requirements that you should identify to make sure that your crane is specified for the correct duty cycle and classification:
- Rated load – Estimation of the loads lifted at or near capacity
- Service – Total hours in operation per day
- Number of lifts – Average lifts and trolley and bridge movements made each hour
- Distance – Average length of each movement
Other factors that may not directly affect the overhead crane classification, but should still be taken into consideration when designing and specifying an overhead crane, are:
- Speed – how quickly can the crane transfer materials or equipment? How many lifts per hour can the crane perform?
- Maintenance requirements – will the crane need to be serviced regularly and how will maintenance or repair affect production and downtime?
- Operating environment – In what type of environment or conditions will the crane be operating?
- Future needs – Any changes or increases in production requirements down the road? If you design a Class C crane, but know that down the road you be lifting heavier loads or using your crane more frequently, you may need to consider a Class D range crane.
Why Do You Need to Classify Cranes by Duty Cycle or Service Class?
Crane service classifications allow you to select and build an overhead crane that is the most economical and safest design for your lifting application. Selecting the right duty cycle or service classification of an overhead crane helps ensure that the components of the overhead crane are durable enough to withstand the load and usage requirements.
Two cranes with an equal capacity and span could vary in price as much as $100,000 because high duty cycle cranes (Class D, E, or F) require specialized components like the hoist, end trucks, motor, bearings, and controls. Low duty cycle cranes can get away with more standardized and economical components—resulting in significant cost savings.
When designing an overhead crane, you’ll also want to give special consideration to any future usage requirements. If you think that your production may expand down the road which may result in higher capacity lifts or an increase in the number of lifts per day, then you may want to spec out the crane and components so it can accommodate your future growth.
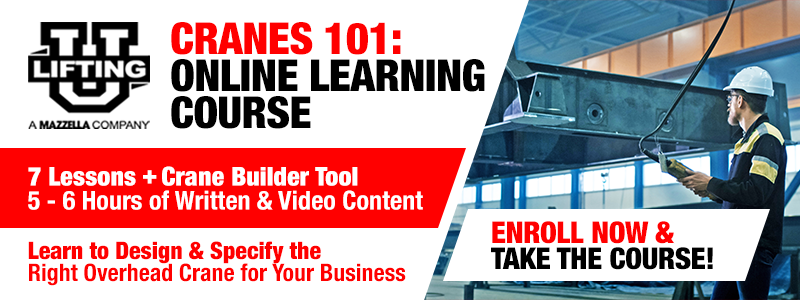
Different Types of Duty Cycles and Crane Service Classifications
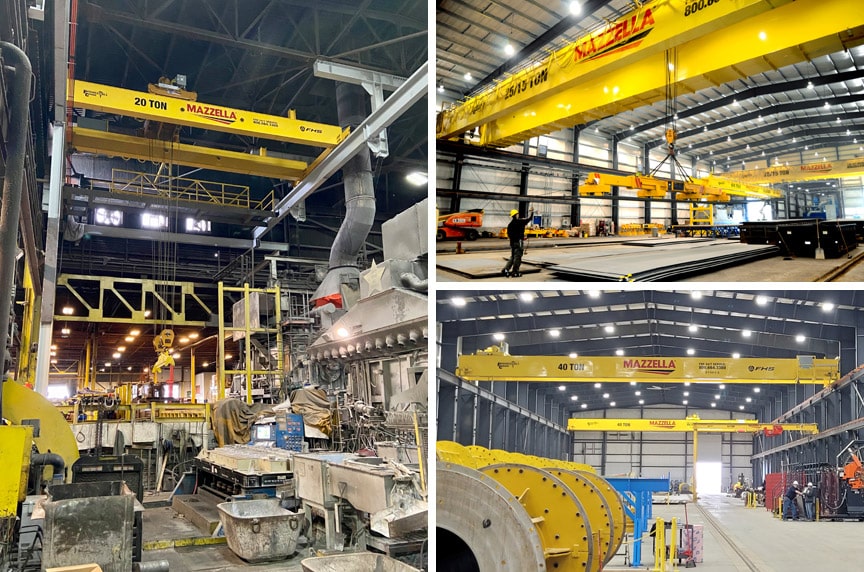
There are six (6) different classifications for overhead cranes, specified by the Crane Manufacturers Association of America (CMAA). Overhead crane service classifications were established so that the manufacturer and end-user could design the most economical crane for the application, based mostly on the average rated load that the crane will lift, and how often the crane will be performing lifts.
Below we’ll identify and define the six types of overhead crane classes and provide types of businesses or industries that match up the best with each overhead crane classification.
Class A1 (Standby Service)
This service class covers cranes where precise handling of valuable machinery at slow speeds with long idle periods between lifts is required. Rated loads may be handled for initial installation of machinery and for infrequent maintenance.
Typical examples are cranes used in power houses, public utilities, turbine rooms, nuclear reactor buildings, motor rooms, nuclear fuel handling and transformer stations.
Bearing Life: 1,250 hours
Number of Lifts: Up to 2 per hour
Motor Starts/Stops: 75 per hour
Class A2 (Infrequent Use)
These cranes will be used in installations where the loads are relatively light, the speeds are slow, and a low degree of control accuracy is required. The loads may vary anywhere from no load to full rated load with a frequency of a few lifts per day or month.
Typical examples are small maintenance shops, pump rooms, testing laboratories, etc.
Bearing Life: 1,250 hours
Number of Lifts: Up to 2 per hour
Motor Starts/Stops: 75 per hour
Class B (Light Service)
This service class covers cranes where service requirements are light and the speed is slow and loads may vary from no load to occasional full rated loads.
- Average load is 50% of the rated capacity
- 2 to 5 lifts per hour
- Average lift distance of 15 feet
- No more than 50% of the lifts at rated capacity
Typical examples are cranes used in repair shops, light assembly operations, service buildings, light warehousing, etc.
Bearing Life: 2,500 hours
Number of Lifts: 2-5 per hour
Motor Starts/Stops: 75 per hour
Class C (Moderate Service)
This service covers cranes where service requirements are deemed moderate.
- Average load is 50% of the rated capacity
- 5 to 10 lifts per hour
- Average lift distance of 15 feet
- No more than 50% of the lifts at rated capacity.
Typical examples are cranes used in machine shops, paper mill machine rooms, etc.
Bearing Life: 5,000 hours
Number of Lifts: 5-10 per hour
Motor Starts/Stops: 150 per hour
Class D (Heavy Service)
In this type of service, heavy-duty production is required but with no specific cycle of operations.
- Average loads approaching 50% of the rated capacity will be handled constantly during the work period
- High speeds are desirable for this type of service with 10 to 20 lifts per hour
- Average lift distance of 15 feet
- No more than 65% of the lifts at rated capacity
Typical examples are cranes used in heavy machine shops, foundries, fabricating plants, steel warehouses, container yards, lumber mills, etc., and standard duty bucket and magnet operations where heavy-duty production is required.
Bearing Life: 10,000 hours
Number of Lifts: 10-20 per hour
Motor Starts/Stops: 300 per hour
Class E (Severe Service)
This type of service requires a crane capable of handling loads approaching the rated capacity continuously, in repetition throughout a stated period per day, in a predetermined cycle of operation.
- Average load at or near the rated capacity
- High speeds are required with 20 or more lifts per hour
- The complete cycle of operation should be specified
Typical examples are magnet, bucket, magnet / bucket combination cranes for scrap yards, cement mills, lumber mills, fertilizer plants, container handling, etc.
Bearing Life: 20,000 hours
Number of Lifts: 20+ per hour
Motor Starts/Stops: 600 per hour
Class F (Continuous Severe Service / Steel Mill AISE Specification)
In this type of service, the crane must be capable of handling loads, approaching rated capacity continuously under severe service conditions throughout its life. Cranes in this class are covered by the current issue of The Association of Iron and Steel Engineers’ Standard No. 6-1969, Specification for Electric Overhead Traveling Cranes for Steel Mill Service.
Typical examples are custom-designed specialty cranes essential to performing the critical work tasks affecting the total production facility, providing the highest reliability, with special attention to ease of maintenance features.
How Load Class and Load Cycles Affect Crane Service Classifications
In both CMAA #70 and CMAA #74, there is a table that shows the relationship between the Load Classes and Load Cycles and how those affect the CMAA Crane Service Classification.
LOAD CLASS | LOAD CYCLES | |||
N1 | N2 | N3 | N4 | |
L1 | A | B | C | D |
L2 | B | C | D | E |
L3 | C | D | E | F |
L4 | D | E | F | F |
Irregular, occasional use followed by long periods of idle. | Regular use in intermittent operation | Regular use in continuous operation | Regular use in severe, continuous operation |
Load Classes
L1 = Cranes which hoist the rated load exceptionally and normally—very light loads.
L2 = Cranes which rarely hoist the rated load and normal loads of about 1/3 of the rated load.
L3 = Cranes which hoist the rated load fairly frequently and normally—loads between 1/3 and 2/3 of the rated load.
L4 = Cranes which are regularly loaded close to the rated load.
Load Cycles
N1 = 20,000 to 100,000 cycles
N2 = 100,000 to 500,000 cycles
N3 = 500,000 to 2,000,000 cycles
N4 = Over 2,000,000 cycles
CMAA Crane Classifications vs. European FEM Classifications
You should know that some overhead crane manufacturers use FEM Hoist Duty Classifications when specifying the service class and duty cycle of their crane systems. FEM is the European Federation of Materials Handling and they are responsible for publishing standards for the material handling industry. FEM standards use load spectrum and average daily operating time to determine their duty classifications.
It’s possible that you may even receive some quotes for a crane project with components specified to FEM standards. In the table below, we compare CMAA crane service classifications to the FEM hoist duty classifications and HMI hoist duty classifications.
Crane Classification |
Hoist Classification |
Use |
Typical Shift Operation |
Load Spectrum |
Approx. Lifts Per Hour |
Typical Application |
||
CMAA |
FEM |
HMI |
ISO |
|||||
Class A |
1Cm |
H1 |
M2 |
Light-duty |
Single shift |
Very light |
Up to 2 per hour |
Standby
service or infrequent service cranes used in public utility facilities, small
maintenance or machine shops, testing
laboratories, etc. for initial installation or infrequent maintenance of
equipment. |
Class B |
1Bm |
H2 |
M3 |
Light-duty |
Single shift |
Maximum load lifted occasionally |
Up to 2 per hour |
Cranes
used in repair shops, light assembly operations, fabrication, service
buildings, light warehousing, etc. |
Class C |
1Am |
H3 |
M4 |
Light to medium-duty |
Single Shift |
Maximum load lifted occasionally |
2-5 per hour |
Cranes
used in machine shops, paper mill machine rooms, etc. |
Class D |
2m |
H4 |
M5 |
Medium to heavy-duty |
One or two shifts |
Medium to heavy loads |
5-10 lifts per hour |
Cranes
used in heavy machine shops, foundries, fabricating plants, steel warehouses,
container yards, lumber mills, etc. and standard duty bucket and magnet
operations where heavy-duty production is required. |
3m |
H4 |
M6 |
Heavy-duty |
Two shifts |
Heavy loads lifted regularly |
10-20 lifts per hour |
Cranes
used in heavy machine shops, foundries, fabricating plants, steel warehouses,
container yards, lumber mills, etc. and standard duty bucket and magnet
operations where heavy-duty production is required. |
|
Class E |
4m |
H4 or H5 |
M7 |
Extremely heavy-duty |
Two to three shifts |
Heavy loads lifted regularly |
20+ lifts per hour |
Typical
examples are magnet, bucket, magnet / bucket combination cranes for scrap
yards, cement mills, lumber mills, fertilizer plants, container handling,
etc. |
Class F |
6 |
N/A |
M8 |
Extremely heavy-duty continuous operation |
Two to three shifts |
Loads lifted continuously |
Continuous |
Custom-designed
for a specific function within a particular facility. Built for ultimate
performance and reliability. Example: Hot metal crane in a steel mill. |
Wrapping it Up
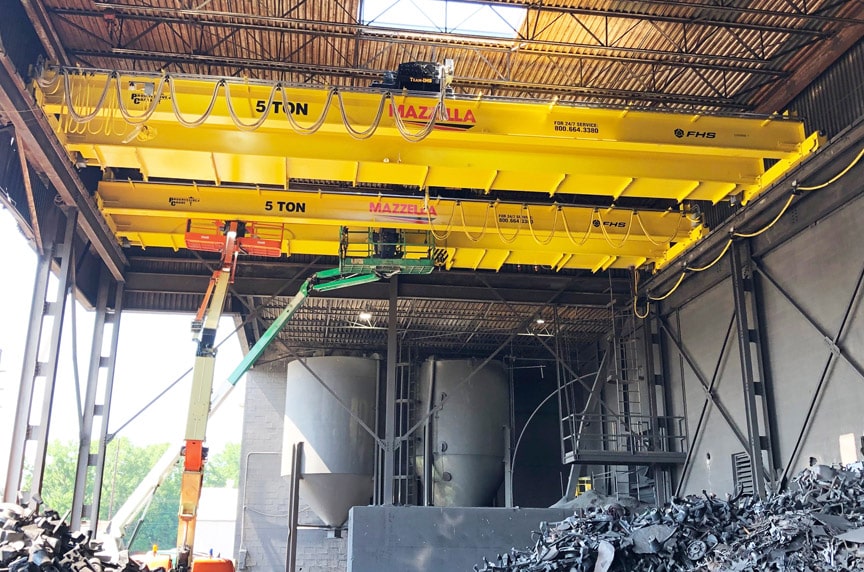
If you put a little bit of thought and consideration into how often you will be using an overhead crane, how hard your overhead crane will have to work, and the type of environment that your crane will be working in, you can get a pretty good sense of what type of crane class will be best for your business or facility and what type of crane will be the most economical design.
If you under-specify an overhead crane system, it will result in a lower initial investment, but will cost you more in maintenance and downtime in the long run. If you over-specify a crane, it will result in a higher initial cost for the crane and runway system, but will have less maintenance and down time in the long run.
Still have questions about overhead crane classifications, or need further input from an overhead crane expert? Please don’t hesitate to reach out to discuss with us further!
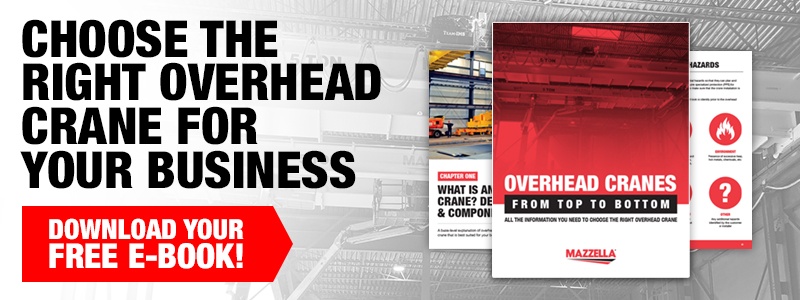
Copyright 2017. Mazzella Companies.