How to Make Sure Your Lifting and Rigging Equipment Is OSHA Compliant
“Where do I start?” This is a question that is on the minds of safety and maintenance leaders in all types of industries when it comes to safety and compliance with OSHA and ASME standards. When you have that nagging feeling that you are not compliant with ASME standards regarding lifting, rigging and overhead cranes, the question “where do I start?” can keep conscientious safety and maintenance leaders up at night.
“Where do I start?” This is a question that is on the minds of safety and maintenance leaders in all types of industries when it comes to safety and compliance with OSHA and ASME standards. When you have that nagging feeling that you are not compliant with ASME standards regarding lifting, rigging, and overhead cranes, the question “where do I start?” can keep conscientious safety and maintenance leaders up at night. Mahatma Gandhi said, “Action expresses priorities.” So, if safety is your priority, then action must be taken. But the question, “where do I start?” still remains unanswered.
Here is one answer: a site assessment! Okay, it sounds as exciting as an income tax audit, but it is an action that expresses your priorities. A site assessment is a good old-fashioned clipboard and pencil assessment of your lifting and rigging equipment, and best practices, based on the applicable ASME standards. Yes, these are the same standards that OSHA compliance officers will hold you to if they should one day come knocking on your door. These site assessments can be performed in-house, or through a neutral third-party service provider.
At Mazzella, one of the services that we offer our customers is a site assessment of their job site or industrial facility. We work with our customers to help improve their lifting and rigging practices by focusing on the following items:
- Training – records, methods, content, and retention
- Equipment
- Maintenance
- Purchasing & Inventory
- Application & Facility Review
The results of these assessments are for your eyes only, and are not meant to provide a “gotcha” moment. Rather, your site assessment can be looked at as a learning experience and can spark a conversation on how to improve the safety, efficiency, and compliance of your rigging equipment and practices.
What Challenges Might You Face When Assessing Your Safety and Compliance Practices?
It seems so simple—why wouldn’t all companies want to do a safety and compliance assessment of their lifting and rigging equipment? One answer is that they are afraid of what they will find. Safety and maintenance leaders may feel that it is a reflection on the job that they are doing if opportunities for improvement are found. Well, it is a reflection on the job that they are doing, and a positive reflection at that. Education and transparency are key factors in any safe lifting and rigging practice, and a site assessment confirms that a willingness to improve, and a commitment to job site safety, are top priorities within that company or department.
Companies using crane and rigging equipment may not want to perform an OSHA compliance assessment because they believe that it is going to lead to more work, more time, and more money than they currently have available. Finding out where you stand in your lifting and rigging practices is just the first step. Your time and budget is just that—yours. The action that you take (or don’t take) has to fit within your schedule and your budget, but at the very least, if you go down the road of self-assessment for OSHA and ASME standards, you have initiated a plan for compliance—and that’s a start.
Another reason why a company may not want to perform a safety and compliance assessment is that they feel they already are compliant, rock solid, air tight. And you know what? Maybe they are…but, what better way is there to confirm this, than to perform a site assessment and make sure that you have all of your bases covered? Not only will you have documentation showing that you initiated an assessment, but you will also have evidence to show documented compliance with the lifting and rigging industry standards. Would you rather take the time to have yourself assessed, or would you rather take your chances and have OSHA perform that compliance assessment?
How to Get Started on an In-house Safety and Compliance Self-Assessment
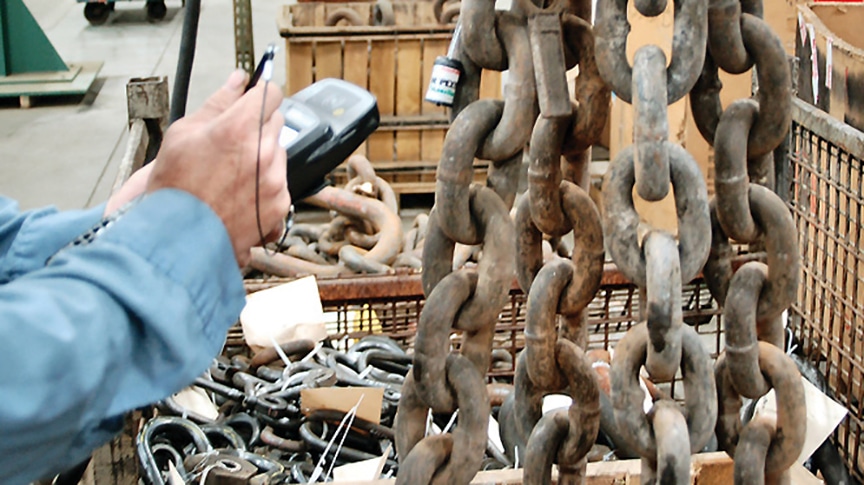
The purpose of doing an in-house safety and compliance assessment is to have your team systematically observe and record your lifting and rigging procedures, equipment, and documentation. This is not an inspection or an audit. But instead, is a general assessment by which opportunities for improvement may be identified. It all starts with the standards.
First, obtain the applicable ASME standards, which you can purchase from the ASME.org website. Some of the standards that you should familiarize yourself with are:
- ASME B30.9 for slings
- ASME B30.26 for hardware (such as shackles, sling hooks, and turnbuckles)
- ASME B30.2 for overhead and gantry cranes
Once you have the standards, take the requirements and turn them into questions. For example, the ASME standards state that “periodic inspection” of rigging gear and overhead cranes is required. From this, you can formulate assessment questions such as:
- Do we perform periodic inspections of our slings?
- Are the inspections documented?
- Are our users trained to use the equipment properly?
- Do we have documentation of this training taking place?
Other standards in regards to storage, retirement criteria, and usage can all be turned into additional questions that become the basis for your site assessment. When you go through this process of turning the standards requirements into questions, you’re doing the majority of the legwork upfront, and then you can get to the heart of the matter—which is compliance and identifying safe lifting and rigging practices. Once you have all of your questions identified, these can be used in all of your future site assessments as well.
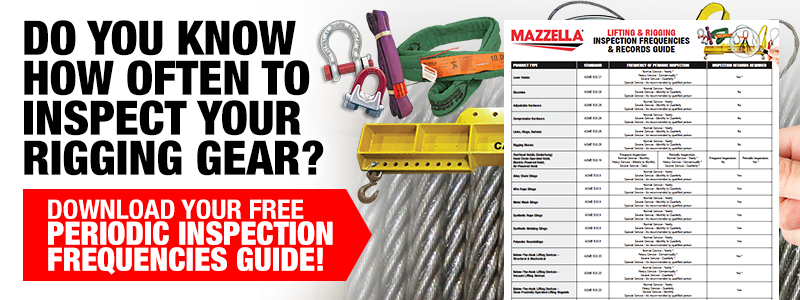
What to Expect from a Third-party Safety and Compliance Assessment
If you truly feel like you don’t have the time or resources to perform an OSHA safety and compliance self-assessment, a good option is to hire a neutral third-party to perform the assessment for you. The assessment itself is rather simple and painless—most consist of a short list of questions concerning the care, use, inspection, training, and documentation of your lifting and rigging equipment and those who use it.
The first thing that a third-party safety and compliance assessor will want to do is to review your documentation, including:
- Training records for those that use and inspect your lifting, rigging, and overhead cranes
- Training materials and frequency of training
- Frequency and thoroughness of your inspection records and any subsequent repairs or actions taken from those inspections.
From there, they will then assess the actual use, care, and storage of your rigging equipment. Although it is not an inspection, assessors will look to make sure that your lifting and rigging equipment is properly tagged, stored, and maintained and then document the general overall condition of the equipment.
During a safety and compliance assessment, a third-party assessor may also perform the following actions:
- Observe the company’s lifting and rigging practices as they happen, and ask to speak with those who perform these practices on the methods that they use to move and lift loads.
- Look for ASME standards compliance and look to identify any opportunities for improvement for lifting and rigging efficiency.
- Make recommendations and identify opportunities for improvement regarding slings, rigging hardware, and below-the-hook devices that may increase efficiency or save money.
- Check to see that the practices of the users operating the cranes and lifting equipment matches the training that was received and documented. Often times, training and actual practices are divergent.
- Identify any critical safety issues observed and notify the customer immediately of its urgency.
- Schedule a follow-up meeting to review findings and opportunities for improvement.
Wrapping it Up
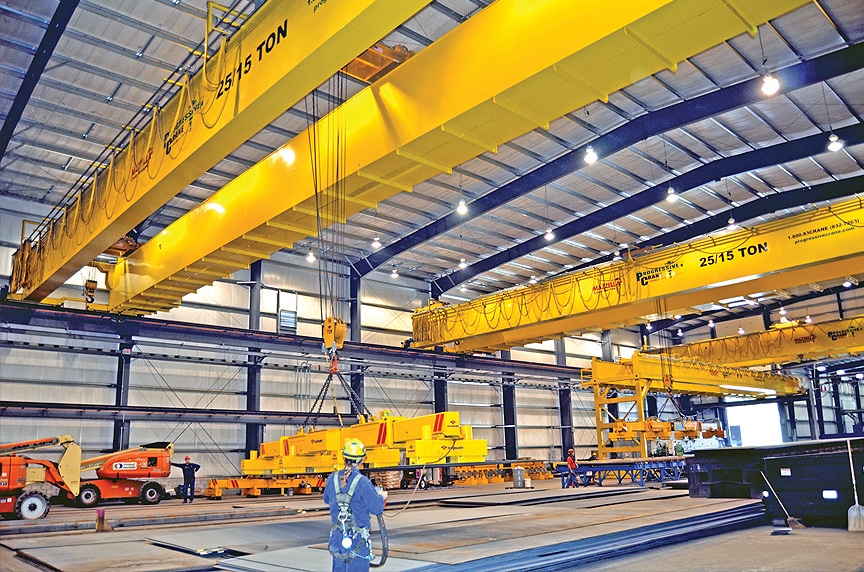
So, to bring everything full circle—Gandhi once said, “The difference between what we do, and what we are capable of, would suffice to solve most problems.” We are all capable of providing a safe lifting and rigging work place, but will we do it? A thorough site assessment of your lifting and rigging equipment, and best practices, is the best place to start.
A site assessment can spark conversations on how to improve the safety and efficiency of your lifting equipment and practices. Often, you and your team or a third-party assessor, will come up with suggestions for improvement based on experience and knowledge learned from other assessments and audits that they have gone through in the past.
At Mazzella, we offer site assessment services where our trained and certified personnel will come on-site and observe your lifting practices, review your documentation and training records, and look at the equipment that you use to make lifts. The assessment that we provide is based on adherence to ASME standards, as well as best practices that we’ve observed in over 60 years of experience in the lifting and rigging industry.
If you’re interested in partnering with us, give us a call to speak with a local Mazzella location and we’ll connect you with the right team to get an in-house site assessment scheduled. Once uncovered, our assessment team can always find ways to address and help solve safety and compliance issues regarding cranes and lifting equipment.
Having the proper lifting sling for your application is also crucial for OSHA compliance. Download our Lifting Slings Types and Terms E-book for the best and worst applications for the four major lifting slings: wire rope slings, synthetic web slings, synthetic roundslings, and alloy chain slings.
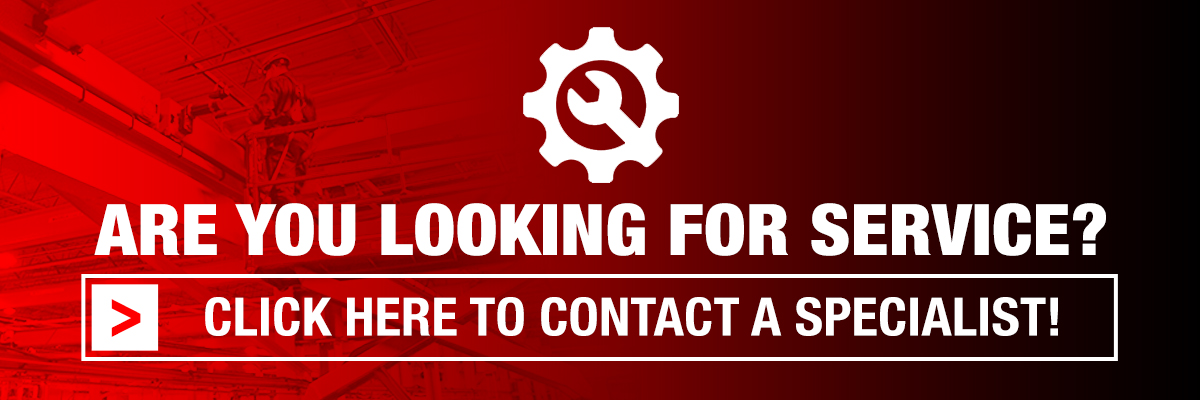
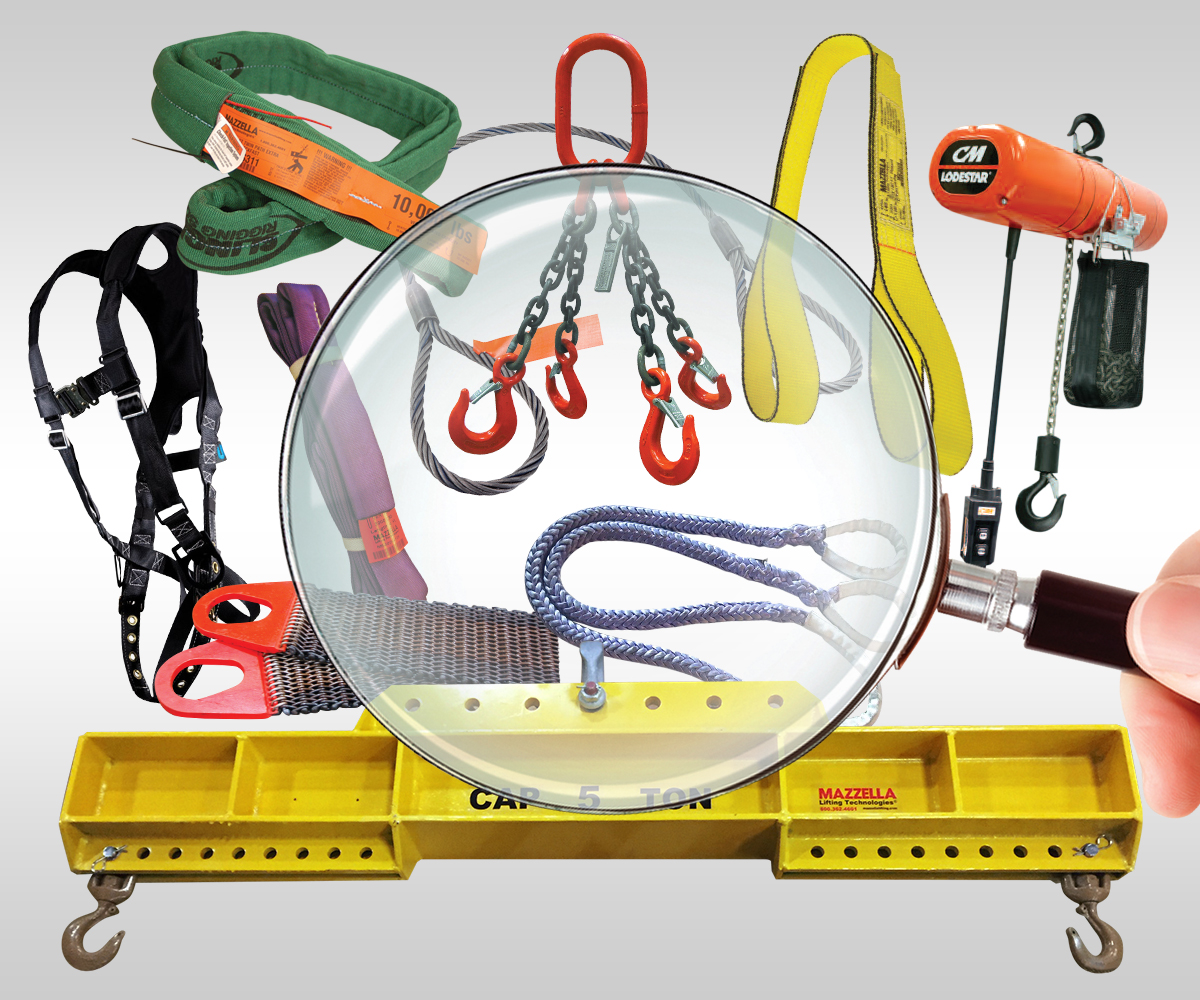
Rigging Inspection Services
OSHA 1910.184, ASME B30.9, B30.20, B30.26, & ANSI Z359 require periodic, documented inspections on slings, rigging hardware, lifting devices, and fall protection every 12 months, at minimum, and monthly to quarterly in more severe service conditions.
Call us at 800.362.4601 or click here if you need inspections for slings, rigging hardware, lifting devices, or fall protection!
Copyright 2017. Mazzella Companies.