The 6 Most Common Problems Found During a Rigging Gear Inspection
It’s not a stretch to say that some companies are more proactive in training their employees and inspecting their rigging gear than others. If you were to compare your most recent rigging inspection report to a similar company in your industry, how would you compare when it comes to failed equipment and compliance?
Do you hear the words “rigging inspection” and immediately begin breaking out in a cold sweat? Are you afraid a rigging inspection is going to disrupt your production and set you back when you have to replace all of the gear that fails inspection?
It’s not a stretch to say that some companies are more proactive in training their employees and inspecting their rigging gear than others. If you were to compare your most recent rigging inspection report to a similar company in your industry, how would you compare when it comes to failed equipment and compliance?
At Mazzella, our certified rigging inspectors inspect lifting slings, hooks, shackles, hoist rings, and below-the-hook devices in all kinds of operating environments for customers of all shapes and sizes. When our inspectors walk through the door, their goal isn’t to come in and see how much rigging equipment they can take away from your team. Instead, we want to come in and validate that the training and processes you’ve put in place are indeed working and help you identify opportunities for improvement.
In this article, we’ll walk you through some of the most common rigging inspection problems we see at any type of facility. No matter what the production process is, what’s being moved through the facility, or what type of rigging practices are being used, these are the most common problems we discover during the course of a rigging inspection.
Podcast: Common Problems Found During a Rigging Inspection
Mazzella Companies | The Rigging Professor
Common Problems Found During a Rigging Inspection
#1 – Missing or Illegible Identification/Tags on Rigging Equipment
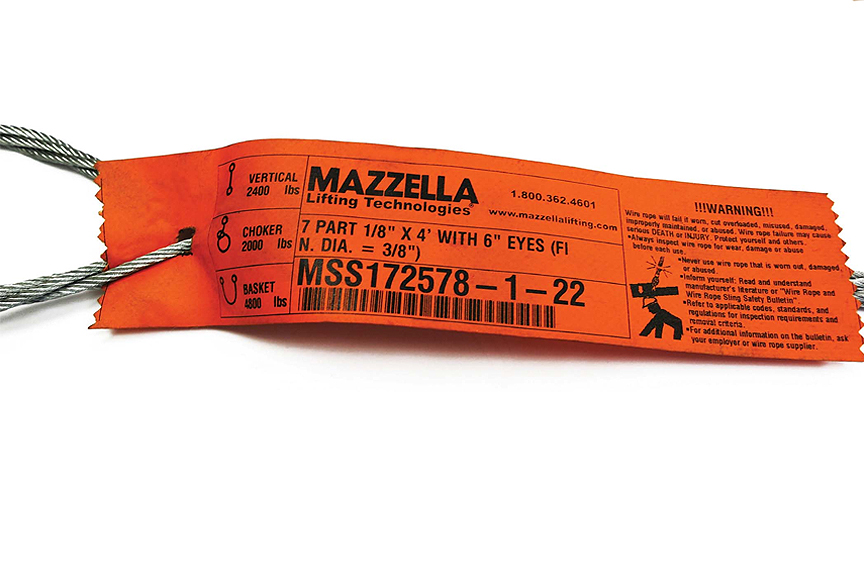
One thing that many people don’t understand is that just about every type of rigging or lifting device is required to have a tag or some form of identification information on it. Sling hooks, shackles, chain slings, synthetic slings, wire rope slings, below-the-hook devices—all of these items are required to have identification tags or markings that provide the end user with the capacity or Working Load Limit (WLL).
ASME has specific requirements for what identification or markings need to be on each type of device—but at the minimum, these tag requirements help the end-user understand the following:
- Manufacturer/serial number for traceability
- Product specifications—including material, diameter, weight, design category
- Working load limit
- Lifting capacities for different sling hitches and sling angles
The problem with rigging equipment is that its most commonly used in an environment that’s dirty, dusty, greasy, grimy, or just flat-out abusive. For slings, this usually means that they’re getting damaged, ripped off, covered in dirt or grease, or smudged to the point they’re no longer legible.
Once a tag or identification is illegible or removed, the sling is no longer able to be used and must be removed from service.
If you’re having problems keeping tags on slings, or your gear is getting scuffed or marked to the point where the tag or rated load marking are no longer legible, you have to ask yourself a couple of questions:
Are you selecting the right type of gear for this type of lift?
If you’re using synthetic slings and your tags keep getting ripped off, maybe it’s time to switch to a more durable sling tag, or to a different style sling like wire rope slings, or alloy chain slings.
Are you using best practices when rigging the load?
If your tag keeps getting snagged on something and gets ripped off, are you rigging the load properly? Attach the end of the sling with the tag to the crane hook so it’s less likely to get scrubbed through something or pulled off during the course of a lift. Also, make sure your riggers and crane operators are properly trained and are using best practices when rigging a load.
#2 – Damage to Synthetic Slings (Cuts, Tears, UV Degradation, Chemical Exposure)
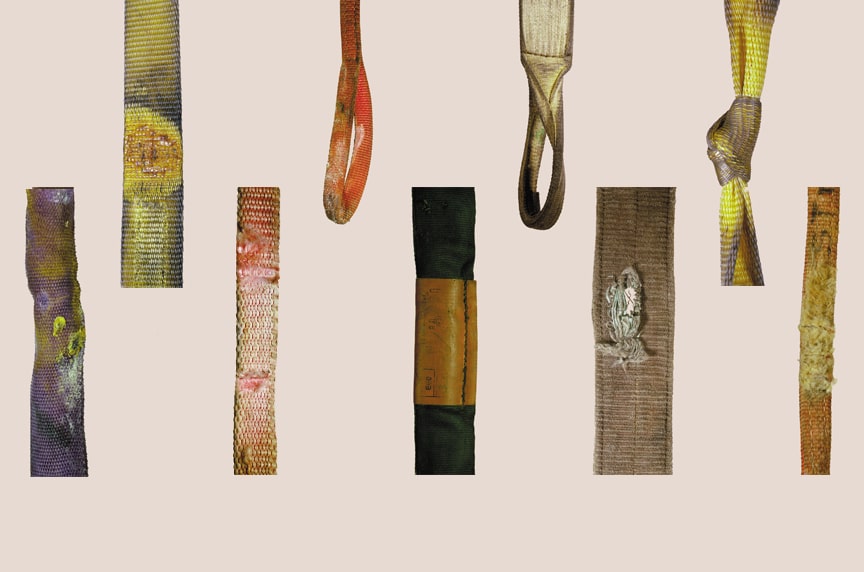
A synthetic lifting sling may be the best choice for your overhead lift and can provide the flexibility, strength, and support you need when moving material through your facility or across your job site. However, you’ll have to give special considerations to the operating environment, stretch under load, and the possibility of the load causing cuts or abrasion to the sling.
Synthetic web slings and roundslings—made from nylon or polyester—are more susceptible to damage from environmental factors like extreme temperatures, prolonged UV exposure, and chemically active environments. They’re also not as durable as steel wire rope slings or alloy chain slings when it comes to abrasion and cut resistance.
- Synthetic slings have a relatively low heat-resistance and are not recommended for use in high-heat applications. However, special high-heat resistant slings are available from certain manufacturers
- Special considerations must be made when selecting a synthetic sling to be used in chemical applications. Nylon and polyester slings have different resistance characteristics to acidic and alkaline environments
- Corner protectors or edge guards should be used to protect against cuts and tears
If there’s any evidence of heat damage, UV damage, rips, tears, punctures, abrasion, or worn or broken stitching, the sling should be removed from service and properly disposed of to discourage further use.
Another problem we see is that the end-user may have a solvent tank that they use to remove grease or grime from their equipment or machined parts. They’ll throw greasy web slings or roundslings into that solvent tank to clean them off and mistakenly think they’re taking care of their rigging gear. You can’t do this with a synthetic sling—these chemicals will degrade the nylon or polyester fibers in that sling and over time, this affects the integrity of that lifting sling.
The best way to help extend the life of a synthetic roundsling, and help to ensure that it stays in service, is to properly maintain it during and in-between each use. Take care of your gear and your gear will take care of you—it’s that simple.
Here are some best practices to keep your synthetic slings in great condition:
- Keep your slings off of the ground and store them in a cool, dry, and dark environment
- Avoid continued exposure to extreme hot or cold temperatures and store them away from direct sunlight and UV exposure to prevent loss of strength
- Keep your slings clean. Continual exposure to dust, dirt, and moisture can degrade the materials over time and shorten the life expectancy of the product.
- Do not store your synthetic slings in a chemically active environment. Chemically active environments can affect the strength of the sling material in varying degrees, ranging from little to total degradation. Consult your sling manufacturer before using your web slings or roundslings in a chemically active environment.
- Synthetic slings should not be used at temperatures in excess of 194° F / 90° C, or at temperatures below -40°F / -40° C
- Use edge protection or barriers to prevent cutting of the synthetic sling when lifting materials with edges
- Always contact the manufacturer with any questions or concerns about maintaining, storing, and protecting your synthetic slings
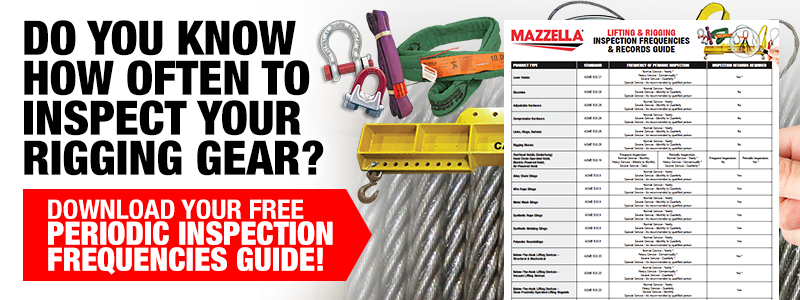
#3 – Stretched or Bent Links on Alloy Chain Slings
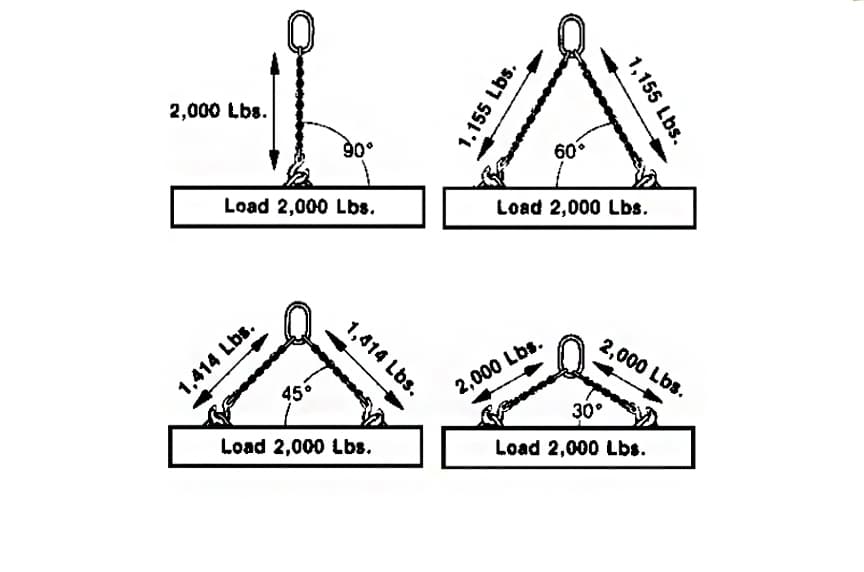
Alloy chain slings are some of the most over-used and abused pieces of rigging equipment in a facility. People tend to believe that because they’re made from alloy steel, they can lift the world with them and misuse and abuse them because they’re not as susceptible to damage as wire rope or synthetic slings.
A huge misconception is that alloy chain slings inherently have extra capacity. Terms like safety factor and design factor get thrown around, but just like any other lifting sling, a lift should never be made that exceeds the working load limit provided on the sling tag.
However, when improperly used, chain damage typically falls into one of the following categories and critical damage will be obvious to a properly trained inspector. These categories include:
- Cracks or breaks
- Excessive wear, nicks, or gouges
- Stretched links or fittings
- Heat damage or weld splatter
- Excessive pitting or corrosion
- Chain or fittings don’t move freely
For example, overload normally causes chain bending or stretch in the individual chain links on a sling. The overload can be the result of the load itself weighing more than the sling’s capacity.
Severe angles can also result in a sling being overloaded. Alloy chain sling charts have rated capacities at 30°, 45°, and 60° angles. The typical angle is 60°. Normally two, three, and four leg chains have three ratings for a specified number of pounds at 60°. The sling identification tag also states the rated capacity for the specified sling angle. Be aware that sling angles greatly affect the tension on each leg of the sling. The farther apart the legs of the sling are spread, the more tension there is on the sling legs.
In applications involving high heat, the user must pay attention to the amount of direct heat that the chain sees. Often, direct heat results in the chain turning a blueish color. The user should consult the chain manufacturer’s capacity reduction charts relating to heat. In addition, be aware of any damage caused by weld splatter or molten metal being splashed on the slings.
In applications that involve lifting loads with rough or sharp edges, wear pads should be used on unprotected corners—otherwise the chain is susceptible to nicks, gouges, and crushed or bent links.
#4 – Broken Wires, Corrosion, and Deformation to Wire Rope
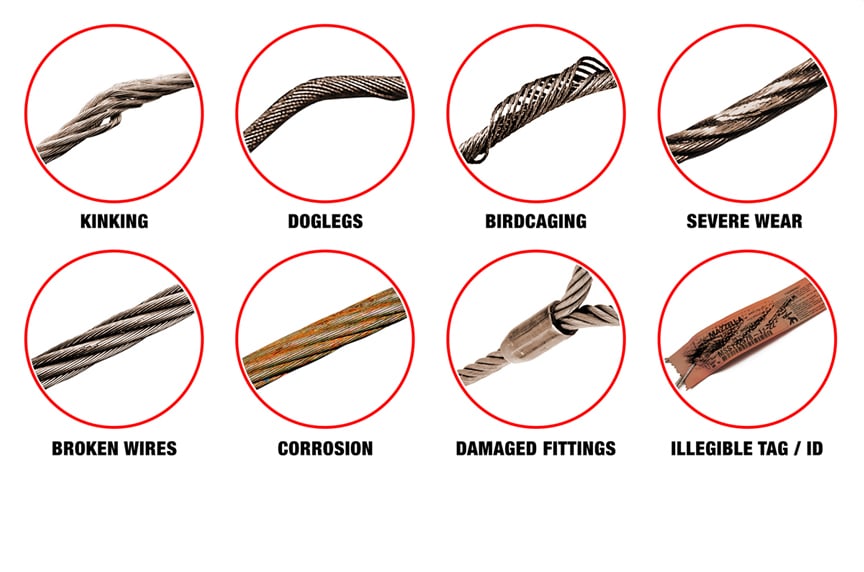
As a starting point, the same practices which apply to all “working” wire rope apply to wire rope which has been fabricated into a sling. Therefore, a good working knowledge of wire rope design and construction will not only be useful, but essential in conducting a wire rope sling inspection.
This being said, inspection of wire rope most often uncovers broken wires, corrosion, and distortion of the rope’s original structure (kinking, crushing, or birdcaging). Any type of distortion that doesn’t straighten itself out when the rope or sling is put under load is cause for removal from service.
This can also include wire rope sling eyes that have been narrowed or stretched because they were paired with a shackle pin or crane hook that has an insufficient D/d ratio. When these deformities don’t come out under load—an inspector is going to fail that sling and recommend it comes out of service.
OSHA does not provide clear guidelines on how to make proper and adequate inspections of wire rope slings. It is up to the designated inspection personnel to know the requirements of the sling inspection standards, and to develop a comprehensive inspection protocol. Wire rope inspection should follow a systematic procedure:
- First, it is necessary that all parts of the sling are readily visible. The sling should be laid out so every part is accessible.
- Next, the sling should be sufficiently cleaned of dirt and grease so wires and fittings are easily seen. This can usually be accomplished with a wire brush or rags.
- The sling should then be given a thorough, systematic examination throughout its entire length, paying particular attention to sections showing the most wear.
- Special attention should also be paid to fittings and end attachments, and areas of the sling adjacent to these fittings.
- When the worst section of a sling has been located, this area should then be carefully checked against the OSHA and ASME criteria.
- Keep records of inspections that include dates and corresponding conditions of slings.
- Immediately dispose of slings that are rejected.
#5 – Broken or Damaged Rigging Hardware
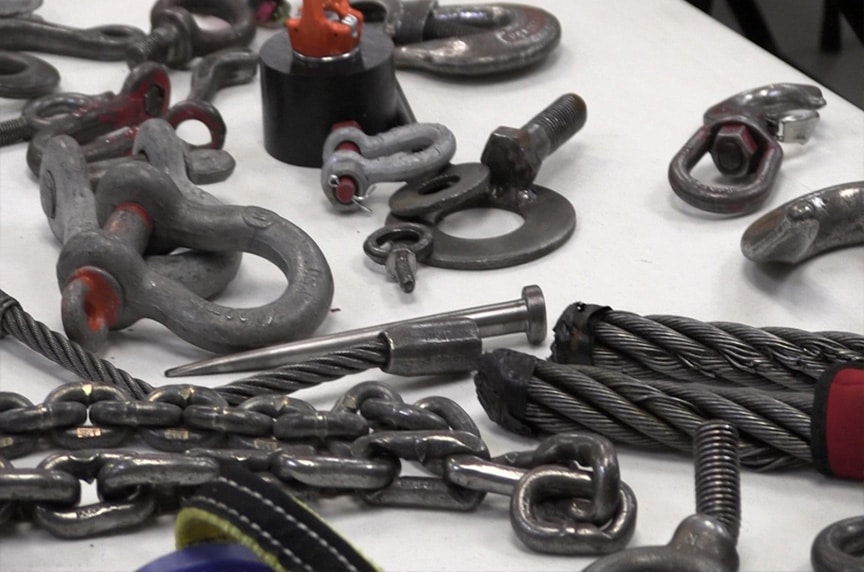
With rigging hardware, what we’re talking about is items like hooks, links, shackles, turnbuckles, eye bolts, and hoist rings. The most common problems tie back to misuse and abuse and lack of inspection. Some of the most common issues we see are:
- Hooks with missing or broken latches
- Rigging hardware that’s bent, stretched, broken, or chopped in half
- Items that have been “repaired” or modified through welding
- Shackles using the wrong size or improperly rated pins
- Hoist ring bolts that are locked up or “frozen” due to an overload
If you’re unfamiliar with best practices, inspection, and removal from service criteria for detachable rigging hardware, then you should purchase ASME B30.26 – Rigging Hardware. This standard covers:
- Shackles
- Adjustable Hardware (turnbuckles, eye nuts, swivel hoist rings)
- Compression Hardware (wire rope clips, wedge sockets)
- Links, Rings, and Swivels
- Rigging Blocks
#6 – Homemade or Unmarked Below-the-Hook Devices
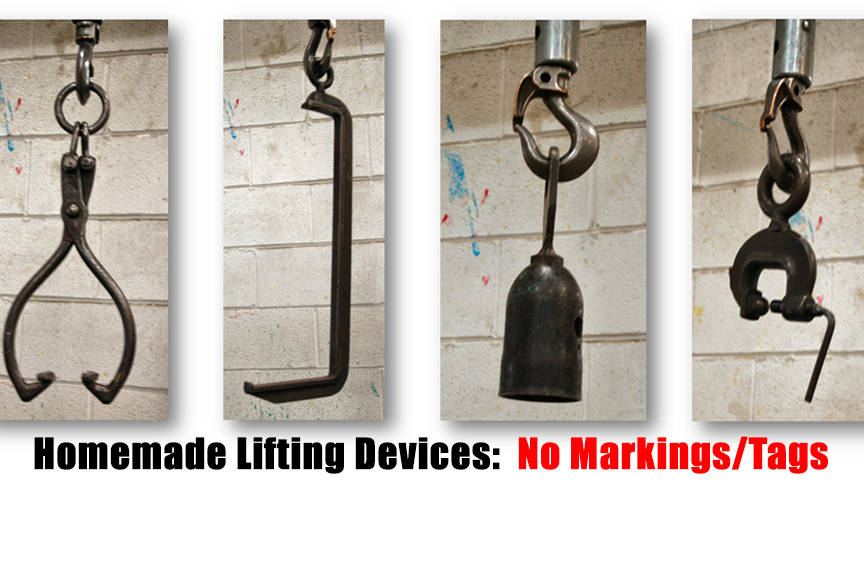
Does your homemade lifting device meet the design requirements of ASME B30.20 / ASME BTH-1? Was all welding performed in accordance with ANSI/AWS D14.1 welding specifications?
One of the most common issues found during a rigging inspection, are custom below-the-hook lifting devices that are either homemade or unmarked. In the below-the-hook lifting world there are two main standards that you should familiarize yourself with if you’re purchasing or designing an engineered below-the-hook lifting device:
- ASME B30.20 Below-the-Hook Lifting Devices – addresses structural and mechanical lifting devices, vacuum lifting devices, operated close proximity lifting magnets, remotely operated lifting magnets, and scrap and material handling grapples. It offers comprehensive solutions applying to the marking, construction, installation, inspection, testing, maintenance, and operation of equipment used for attaching loads to a hoist.
- ASME BTH-1 Design of Below-the-Hook Lifting Devices – provides minimum structural and mechanical design and electrical component selection criteria for ASME B30.20 below-the-hook lifting devices.
Make sure that the below-the-hook lifting device is properly marked and tagged in accordance with the industry guidelines, and you’ve gone a long way towards making sure your below-the-hook devices are OSHA and ASME compliant.
Too often we find that below-the-hook lifters have been made in-house and lack a tag or plate that provides the following information on the specific device:
- Manufacturer’s name and contact information
- Serial number (unique to that specific lifter)
- Lifter weight
- Rated load
- Cold current amps (when applicable)
- Rated voltage (when applicable)
- ASME BTH-1 Design Category
- ASME BTH-1 Service Class
This information can be critical for any rigger, as it provides the weight of the device itself—which must be considered when calculating if the load is within the capacity of the crane being used for the lift. It also provides the manufacturer’s name, contact information, and unique serial number. If you were to have issues with the device down the road, you would need that information for traceability purposes.
ASME tag requirements also provide the end-user with information regarding how and why the product was designed. Design Category tells whether the lifter was designed for a specific application or designed to be a general purpose lifter. Service Class provides a service classification for the device by factoring in load cycles per day, as well as the desired service life (in years) of the device.
Always make sure that your below-the-hook lifter has the capacity visible, as well as a plate or tag that is welded or stamped into the device. Lifting beams and other devices can get smashed and abused during the course of their lifetime and a rickety plate can get knocked loose, or a painted marking can get marred or scuffed and become illegible.
If an inspector finds a below-the-hook lifter that’s missing any or all of this information, they’ll have to fail the device for meeting compliance requirements—and you could be looking at an expensive and time-consuming process to get your device reverse engineered and re-tagged.
Wrapping it Up
You shouldn’t look at the inspection of your lifting and rigging gear as a nuisance that’s going to disrupt production or as an added expense when you have to replace discarded rigging gear. Our goal for this article is only to open your eyes to the most common problems our rigging inspectors find when they’re out in the field.
Share this article with your team and put a plan together to assess your lifting and rigging equipment and procedures. Education and transparency are key factors in any safe lifting and rigging environment. Your willingness to improve your processes confirms your commitment to job site safety and proves it’s a top priority within your company or department.
The solution to any of these problems we listed above can be solved by:
- Providing more thorough training for riggers and crane operators
- Implementing a more thorough in-house inspection program
- Familiarizing yourself with the applicable ASME standards
The following standards are what our inspectors are trained to and what they use when inspecting, assessing, and documenting the condition of your rigging gear during the course of an inspection:
OSHA 1910.184 | Slings |
ASME B30.9 | Slings |
ASME B30.10 | Hooks |
ASME B30.16 | Overhead Hoists (Underhung) |
ASME B30.20 | Below-the-Hook Lifting Devices |
ASME B30.21 | Lever Hoists |
ASME B30.26 | Rigging Hardware |
If you haven’t familiarized yourself with these standards yet, then this is a great place to start. We recommend you do so immediately and also provide your employees training to give them exposure to these standards.
If you feel like this is a task that’s more than your team can handle, we can help! At Mazzella, we offer a variety of services including site assessments, rigging and crane operator training, sling inspection and repairs, overhead crane inspections and so much more. Our rigging inspection program is its own dedicated business unit with a team of inspectors that are certified through Industrial Training International to meet OSHA 1910.184 and ASME B30.9 requirements for sling inspection.
If you need help getting any part of your lifting and rigging program on track towards compliance, please don’t hesitate to contact us today.
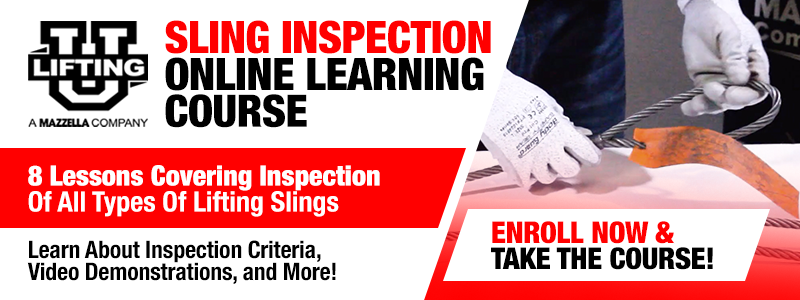
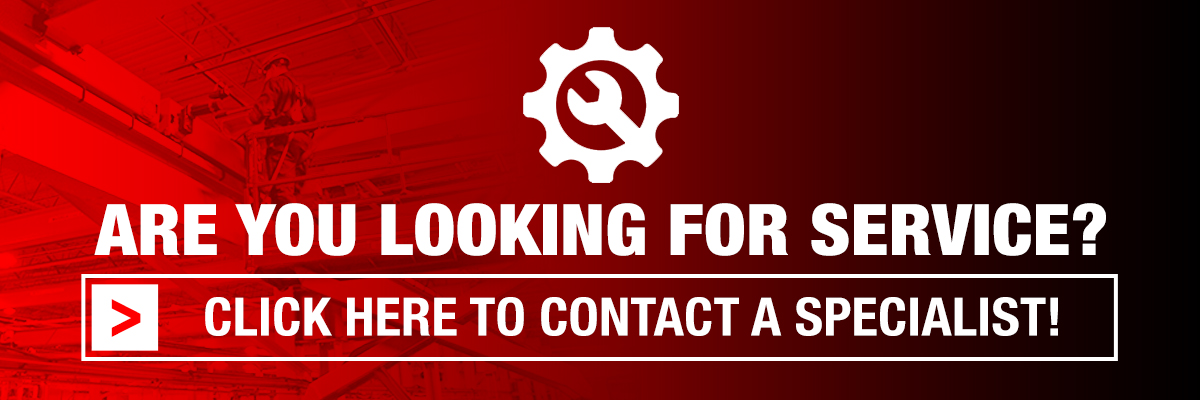
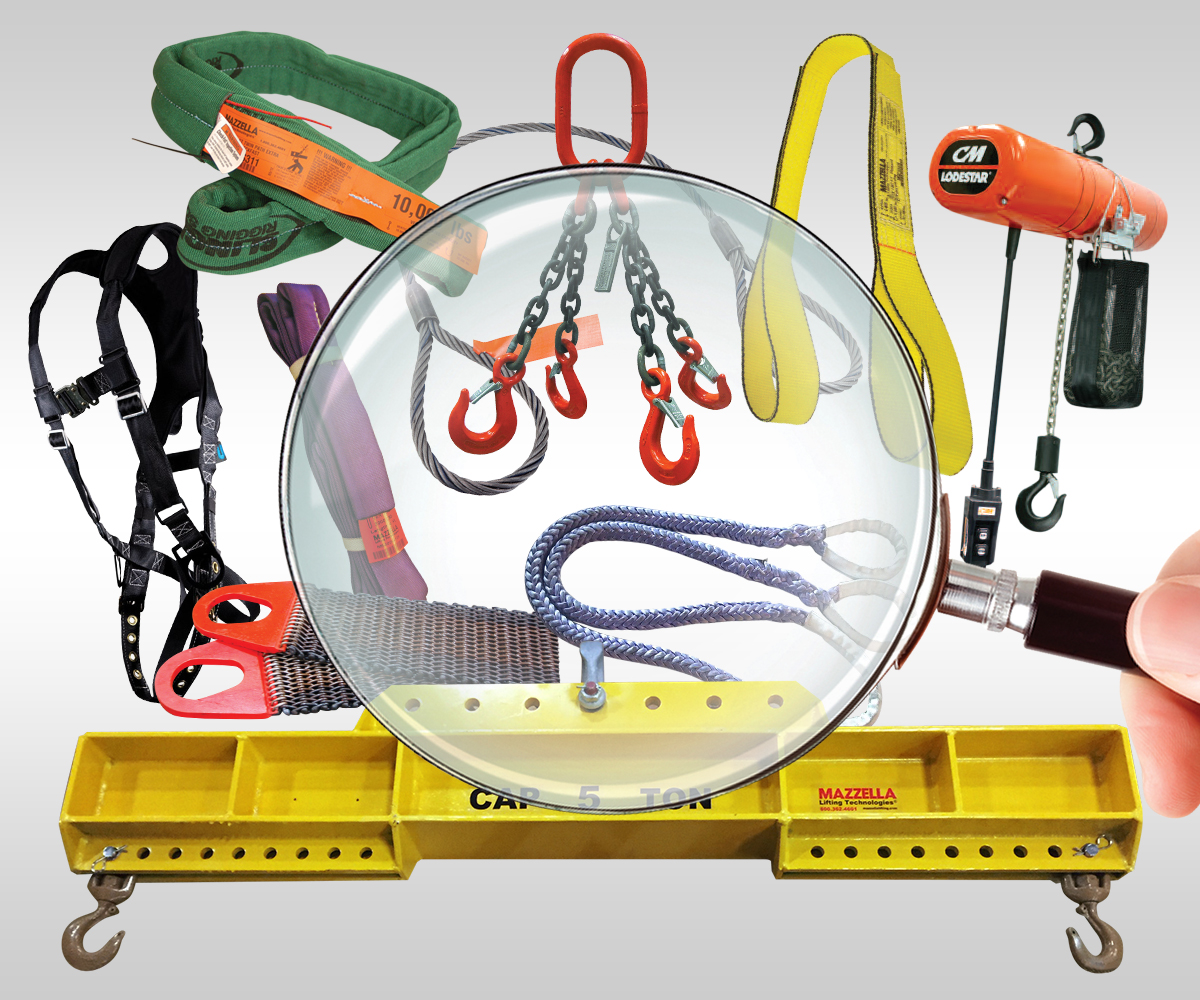
Rigging Inspection Services
OSHA 1910.184, ASME B30.9, B30.20, B30.26, & ANSI Z359 require periodic, documented inspections on slings, rigging hardware, lifting devices, and fall protection every 12 months, at minimum, and monthly to quarterly in more severe service conditions.
Call us at 800.362.4601 or click here if you need inspections for slings, rigging hardware, lifting devices, or fall protection!
Copyright 2018. Mazzella Companies.