We Visited Kito Crosby’s Factory | How a Crosby Shackle is Made
We’re taking you behind the scenes at Kito Crosby’s flagship manufacturing plant in Longview, Texas, to show you the intricate Crosby shackle manufacturing process.
This video offers industry professionals a comprehensive overview of how Crosby shackles, essential components in lifting and rigging operations, are meticulously crafted from raw steel to finished products. Whether you work in construction, manufacturing, or the rigging industry, understanding how these critical pieces of rigging hardware are made can offer valuable insights into product quality and safety. Shackles play a vital role in lifting and rigging operations, and Crosby’s commitment to manufacturing excellence ensures that these tools meet the highest industry standards.
If you’re a Quality Control Manager maintaining industry standards focused on compliance and product reliability, a Procurement Officer or Purchasing Agent sourcing reliable high-quality rigging equipment, or a Safety Director prioritizing a safe and healthy workplace, this inside look at Crosby’s manufacturing process provides valuable insights into the quality and precision behind these critical rigging components.
The Crosby Shackle Manufacturing Process
The journey of a Crosby shackle starts with raw steel billets, sourced from domestic steel mills, and transformed into finished products through Kito Crosby’s detailed, multi-step shackle manufacturing process. Here’s a breakdown of the steps involved:
- Die Manufacturing: The Crosby shackle manufacturing process begins with creating precision dies using CNC machining. These dies define the shape of the shackle, ensuring accuracy and consistency along with clearly defined shackle markings. The dies, along with trim tools used to remove excess material, undergo regular maintenance to meet Crosby’s stringent standards.
- Forging: Once the dies are prepared, the billets are heated in an induction furnace to precise temperatures. The steel is then hammered in a closed-die forging process. This method ensures superior grain flow in the steel, which provides the shackles with enhanced strength and performance. The forged shackles are then trimmed to remove excess steel as part of the Crosby shackle manufacturing process.
- Heat Treatment: After forging, the shackles undergo a crucial heat treatment process. This involves quenching and tempering the steel to enhance its toughness, ductility, and strength. This step is key to ensuring that the shackles can withstand fatigue and impact without fracturing—an essential stage in the Crosby shackle manufacturing process.
- Drilling and Machining: After heat treatment, pinholes are drilled into the shackles using both automated and manual processes. These precision-machined holes ensure proper fit and functionality for the shackles, another important step in the Crosby shackle manufacturing process.
- Finishing and Testing: Before reaching the final stage, the shackles are subjected to rigorous testing. Some are individually proof-tested, while others undergo batch testing, depending on the type. Magnetic particle testing is also used to detect any potential defects for specific types of shackles. Finally, the shackles are powder-coated with the iconic Crosby red finish, providing protection against corrosion and wear. This stage completes the Crosby shackle manufacturing process.
Forging Knowledge
If you work in industries relying on lifting and rigging, like construction, industrial manufacturing, oil and gas, renewable energy, maritime operations, and more. Or if you enjoy taking a behind-the-scenes look at American manufacturing, this video will give you a deeper appreciation for the engineering, skill, and precision that goes into creating shackles and the vital safety components you use in your rigging processes. Understanding how these products are forged, tested, and finished can help ensure that you’re choosing the right equipment for your projects.
Shackles are used in a wide range of industries. Knowing the detailed Crosby shackle manufacturing process can help professionals make more informed decisions when selecting equipment for lifting and rigging tasks. For more information on Crosby shackles and other rigging hardware, explore our extensive inventory and expert resources. Have questions about shackle selection or application? Feel free to contact us and our team will be happy to assist you!
Transcript
Welcome to Kito Crosby’s Flagship Manufacturing Plant
– We are here in Longview, Texas, at one of Kito Crosby’s flagship manufacturing plants!
My name is Ben and this is The Lifting & Rigging Channel. We’re here in Longview, Texas, where Kito Crosby makes Crosby shackles. Next to a crane and a hook, a shackle is probably the most recognized piece of equipment within the lifting industry. It is a critical piece of equipment for rigging, and the Crosby name is synonymous with them. Here in Longview, Texas, Kito Crosby forges all different types of rigging equipment, and they’ve agreed to let us in and show us how a shackle is made. So let’s head on in and find out. Hi, Fernanda.
Who Is Kito Crosby?
– Hi, Ben.
– Nice to meet you.
– Nice to meet you too. Glad you’re here today.
– Thanks for having us. Can you tell me a little bit about Kito Crosby?
– Yes. Kito Crosby is the global leader of the lifting securement industry. We are the most vertically integrated manufacturer. We build what we sell.
– So what do you sell? What do you build?
– We build shackles, hooks, links, load binders, sockets, and many variation on those products.
– So we’re here to see how a shackle is made, right?
– Yes, exactly. Let’s go.
– Alright.
How Is a Shackle Engineered?
– [Narration] Our first stop was to learn what goes into engineering a shackle. Justin broke it down for us.
– Developing shackles has been done for a long time, so we have a lot of historical information to go off of. We do a lot of supporting the manufacturing team to make sure that we make quality products. Sometimes if there’s a creative loading scenario that maybe brings questions to our standard guidance, I’ll run finite element analysis to make sure that customers won’t have any issues.
Most of the design is us making sure that we comply with third party specifications, so that’s the things that customers have come to expect out of shackles. That’s fatigue life, that’s the standard dimensions, so they fit with any product out in the field, and other mechanical properties, like corrosion resistance and hydrogen embrittlement protection.
What Are the Steps of Shackle Manufacturing?
– [Narration] After getting outfitted with our PPE and receiving a thorough safety briefing, we went down to the factory floor.
– Hey, welcome to Longview, Texas. I’m Jim Zupancic. We’re standing here today at one of Kito Crosby’s flagship plants where we manufacture from cradle to grave our Crosby shackles, from raw billet to finished good. Now come on back and let me show you how they’re made.
So today, we’re going to walk through the entire manufacturing process that takes this raw billet to this finished Crosby shackle, and every step along the way. In those steps, we go from our die manufacturing and to drop hammer forging, to our heat treat process, and then to secondary operations, drill tap and assembly, to proof testing, and then all of our quality checks through to powder coating and finishing to final assembly, and then finally, onto our shipping trucks and off to the distribution center to fulfill one of our many customer orders. But it all starts right here with our die manufacturing, which we do one hundred percent in-house from raw steel. And combined in-house between our design engineers and our expert operators, we have over 160 years of die manufacturing experience.
Crosby Die Manufacturing
– [Narration] Crosby die blocks are machined in a programmed CNC machine according to the specific shackle being made. Engineers create the detailed designs of the shackles to be forged. These dies are also created for all different types of Crosby rigging products.
Just as important as the dies which forge the shackles are the trim toolsets. These are used to cut away the excess steel from the edges of the shackles after they are hammered. Each undergoes regular maintenance to prolong their lifespan and keep the quality consistent with Crosby standards.
These dies are then sent to the drop forge hammers, where the hot steel billets are forged into their shackle shape. Product Identification Codes, or PICs, are formed in the dies, so each shackle and its materials are fully traceable.
Analyzing the Steel Billets
The billets are made from the highest quality fine grain special bar forging steel, all from domestic steel mills. Every heat or batch of steel receives a certified material analysis for quality and metallurgic properties in Kito Crosby’s laboratory before being sent to the forge.
Induction Heating of Steel Billets for Shackle Forging
The billets are dropped into a hopper, which allows a continuous supply of billets to feed the induction heater. The hopper vibrates, causing the billets to inch along, moving in line towards the induction furnace.
Once in the furnace, each billet is heated to an exact temperature before heading down the conveyor to the hammer forge. If, at any time, heat sensors read a temperature that is not within tolerance, the billets drop into a side hopper and are not allowed to pass through to the forging process. Temperatures must be perfectly controlled to maintain Crosby quality standards.
Crosby Shackle Forging Process
The hot billets travel on a conveyor to the hammers, where they are placed on the die. The hammers are all closed die forging hammers. This is an important part of Kito Crosby’s process. While many other shackles are forged in an open die, all Crosby shackles 300 tons and smaller are forged in a closed die, giving Crosby shackles superior performance characteristics. Closed die forging is essential for superior grain flow in the steel, consistency and accuracy within the dimensions of the shackle, as well as clear lettering.
Some of the shackles are hammered through manual manipulation, where each billet is moved by hand to the different stages of the die: preform, forge, and finishing. The shackles are then moved by hand to the trim tool, where the excess steel is removed. The hot shackles drop onto a conveyor belt, taking them to a hopper, where they are collected for the next stage.
Crosby’s Automated Shackle Forging Process
Other hammers are fully automated, with Kuka robots performing each of the manipulations. The robots move the shackles through each stage of the forging process, from preforming, to forging, finishing, trimming, and onto the conveyor belt.
The real work here is done by the robot techs, who program each of these moves, operate the machines, and keep the robots performing at the highest level.
Giant Crosby Shackle Forging Process
The largest shackles, with a Working Load Limit of 30 tons all the way up to 300 tons, are forged using a powerful steam hammer. Each shackle of this size is manipulated by hand and large equipment. Different products and sizes require a different number of blows to forge it. Each blow of this massive hammer shakes the entire building. A crane is used to move the product from hammer to trim.
No matter what hammer is used, the shackles all pass through stringent quality control checks at each stage.
Crosby Bolt Type Pin Manufacturing Process
Large bolt-type shackle pins are created using a bolt header. Robots move induction heated pins to a press, where the head of the bolt-type pin is formed. Each bolt head is clearly marked with a Product Identification Code for complete traceability. They then head off for the machining of their threads.
Manual Shackle Ear Drilling Process
Here, some shackles are drilled. If the shackle needs to be manually drilled, it is done at this stage. Shackles are held in place while their ears are drilled to create the pinholes. Once the holes are drilled, they are sent off for heat treatment.
Crosby Shackle Heat Treatment Process
After the shackles leave the forging hammers or manual drills, they are transported to a belt furnace to begin the quench and temper heat treatment process. This process is arguably the most important part of making a Crosby shackle, as it develops a tough material that reduces the risk of brittle catastrophic failure.
Kito Crosby heats the shackle to the perfect temperature. The microstructure of the steel is formed into tempered martensite, refining grain boundaries and giving the shackle the toughness to best resist fracture. Out of the furnace, the shackles are then quenched in liquid. Quenching freezes the steel’s grain structure within the shackle.
The shackles then move into a second furnace to be tempered. This time, they are heated to a lower temperature to relax the steel and give the shackle their ductility.
Each of these temperatures has been perfected, tweaking the temperature over many decades to give the shackles superior ductility ratings, toughness, fatigue, and impact properties. After the heat treatment, hardness checks are performed to make sure the shackle is within the required tolerances.
Automated Shackle Ear Hole Drilling Process
Next, if the shackles have yet to be drilled, they head to the robo drills. Automated drills are used to drill through the ears and quickly create precise pinholes. These workstations allow for an extremely efficient process as workers move between the different automated stations, drilling some shackles and tapping and assembling a different batch of shackles.
Crosby Shackle Tumbling Process
Once heat-treated and drilled, the shackles are cleaned by running them through a tumbler. The shackles are loaded into the tumbler and the steel is tumbled until shiny. Now the shackles are ready to head to the finishing stages of their manufacturing.
Crosby Shackle Assembly Process
Depending on if the shackle is a screw pin, round pin, or bolt-type shackle will determine the next stages. Most screw pin shackles are tapped, adding the threads in the ear, and assembled in an automated process. Some screw pin shackles, including the larger ones, are tapped and assembled by hand.
Bolt-type shackles require hand assembly, screwing on the bolt, and adding the cotter pin.
How Crosby Shackles Are Tested
Once assembled, the shackles head off for testing, and then to powder coating or galvanizing. It is important for the shackles to be tested for quality and performance. Creating a consistently safe product is of the utmost importance to Kito Crosby and its customers.
The shackle type and size will determine if the shackles are individually proof-tested and magnetic particle tested, or if they are batch tested.
Shackles are put in a pull tester, pulled to their proof load, and held for a set amount of time. Specific shackles undergo magnetic particle testing, where fluorescent magnetic particles are applied and then inspected under ultraviolet light to determine if there are any defects in the shackle. Only once their quality is assured can they move on to the next stage of the process.
Crosby Powder Coating Process
Now the shackles are ready to receive their color. Powder coating of Crosby shackles is all done in-house. Powder coating is the painting process. The shackles are hung on hooks that are electrically grounded. The line then runs the shackles to clean them and remove any contaminants. They are then run through a drying oven before spraying them with the powder coating.
The powder is electrostatically charged, attracting it to the electrically grounded shackles and adhering to the surface, ensuring a uniform coating. From here, the line moves the shackles into the curing oven, where the powder is melted, forming a film that adheres to the surface and is baked on. Once out of the oven, the dull powder now shines with that signature Crosby red.
Once the shackles are powder coated and assembled, they are ready to be shipped.
Crosby Shackles Heading to Your Jobsite
Millions of Crosby shackles are shipped each year. In one year, Kito Crosby manufactured enough shackles to lift 22 million tons. From here, Crosby shackles are shipped all over the world and used on construction sites, ships, factories, and mills.
They are used in just about every industry that you can imagine, from construction, industrial manufacturing, utility and power generation, oil and gas, renewable energy, transportation, aerospace, forestry and agriculture, fishing and aquaculture, mining, military and defense, maritime, entertainment, and more.
How Mazzella Can Help With Your Lifting Operations
– So that’s how Crosby shackles are made. I hope that the next time you drive past a construction site, or you look up and see one of these suspending something in the air, you have a bit more appreciation for the technique, skill, and hard work it takes to make these and keep everybody safe. The men and women who make these are proud of the job that they do.
At Mazzella, we have a massive inventory of Crosby shackles. We also have one of the largest inventories of wire rope, hoists, hoist parts, slings, rigging hardware, pullers, and more. And we have the experts who can make sure that you get the right piece of equipment to make sure you get the job done safely. Feel free to contact us by clicking the link in the description if you want to learn more.
If you found this video useful, informative, entertaining, or you just feel like being friendly, then hit that like button so we can get this information out to everyone who needs it. Subscribe and hit the bell so you never miss a video. If you have a question, drop it in the comments so we can get you an answer. Remember, safe rigging is smart rigging. My name is Ben. Stay safe out there.
FREE Downloads
- Shackle Markings Identification Guide
- Rigging Gear Inspection Field Reference
- Lifting and Rigging Best Practices Infographic
- Shackles At A Glance
- Construction Products & Services Catalog
- Calculating Load Weight Pocket Guide
- Lifting Slings Types and Terms E-book
- Lifting and Rigging Inspection Frequencies and Records Guide
- Lifting and Rigging Site Assessment Guide
- Mazzella Capabilities Brochure
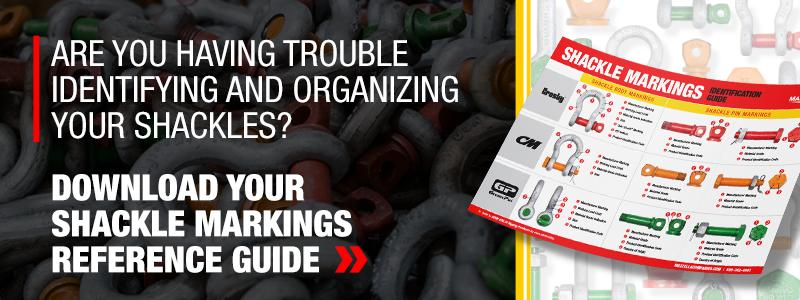
Learn More! Articles, Videos, and Podcasts!
- What Are the Different Types of Shackles for Lifting and Rigging?
- ASME B30.26 Shackle Inspection Requirements & Best Practices for Use
- Shackle Ratings in Short or Metric Tons, Inspection Requirements
- What’s Crosby’s Wireless Load Shackle, & How Does It Monitor Lifts?
- Toolbox Talks: Hand Signal vs. Walkies, Pin Up/Down, Dynamic Loads, & Old Slings
- A Brief Rigging Glossary: Basic Industry Terms You Should Know
- Basic Rigging Questions and Terms Answered and Defined
- How to Calculate the Weight of a Load Before an Overhead Lift
- What Is the Crosby | Straightpoint Radiolink Plus Load Cell?
- Which Crosby | Straightpoint Load Cell Is Right For You?
- What Is the BlokCam, and How Does It Make Lifts Safer?
- How an Easement Machine Manufacturer Solved Their Lifting and Rigging Challenges Using a Single-Source Provider
- OSHA Inspection Series: How Important Are Rigging Inspections?
- How Much Does an OSHA/ASME Compliant Rigging Inspection Cost?
- OSHA Inspection Series: How Can Lifting & Rigging Training Help with OSHA Compliance?
- How Do You Safely Lift Off-Center Loads?
- What Is a Sling Angle, and How Can Knowing Them Make Our Lifts Better?
- How Can You Ensure Your Overhead Lifts Are Safe?
Contact Mazzella
- Schedule Remote or In-Person Rigging Training
- Contact Mazzella’s Lifting and Rigging Division
In this video
0:00 – Welcome to Kito Crosby’s Flagship Manufacturing Plant
0:49 – Who Is Kito Crosby?
1:21 – How Is a Shackle Engineered?
2:14 – What Are the Steps of Shackle Manufacturing?
3:36 – Crosby Die Manufacturing
4:26 – Analyzing the Steel Billets
4:43 – Induction Heating of Steel Billets for Shackle Forging
5:20 – Crosby Shackle Forging Process
6:34 – Crosby’s Automated Shackle Forging Process
7:21 – Giant Crosby Shackle Forging Process
8:17 – Crosby Bolt Type Pin Manufacturing Process
8:59 – Manual Shackle Ear Drilling Process
9:26 – Crosby Shackle Heat Treatment Process
10:39 – Automated Shackle Ear Hole Drilling
11:31 – Crosby Shackle Tumbling Process
12:16 – Crosby Shackle Assembly Process
13:19 – How Crosby Shackles Are Tested
14:08 – Crosby Powder Coating Process
15:12 – Crosby Shackles Heading to Your Jobsite
15:56 – How Mazzella Can Help With Your Lifting Operations
Disclaimer:
Any advice, graphics, images, and/or information contained herein are presented for general educational and information purposes and to increase overall safety awareness. It is not intended to be legal, medical, or other expert advice or services, and should not be used in place of consultation with appropriate industry professionals. The information herein should not be considered exhaustive and the user should seek the advice of appropriate professionals.