What is a Lifeline Fall Protection System? Different Types & OSHA Standards
Whether it’s vertical or horizontal, engineered or pre-engineered, or temporary or permanent, lifeline systems are an affordable and versatile fall protection system to have. Learn more about their best applications and key OSHA standards in this article.
Do you need a reliable fall protection system at your job site, but don’t know which one is best for your application?
Not having the proper fall protection on site not only leaves the door open for a heavy OSHA fine, but it can also delay your projects and cause serious injuries or death to your workers.
One of the more popular fall protection systems is a lifeline. The question is: is it right for your application? Also, is it good for my application, and would you be better purchasing an engineered or pre-engineered solution?
This comprehensive article will break down the basics of lifeline systems, helping you pick the right fall protection solution for your organization. We will go over:
What Is a Lifeline System?
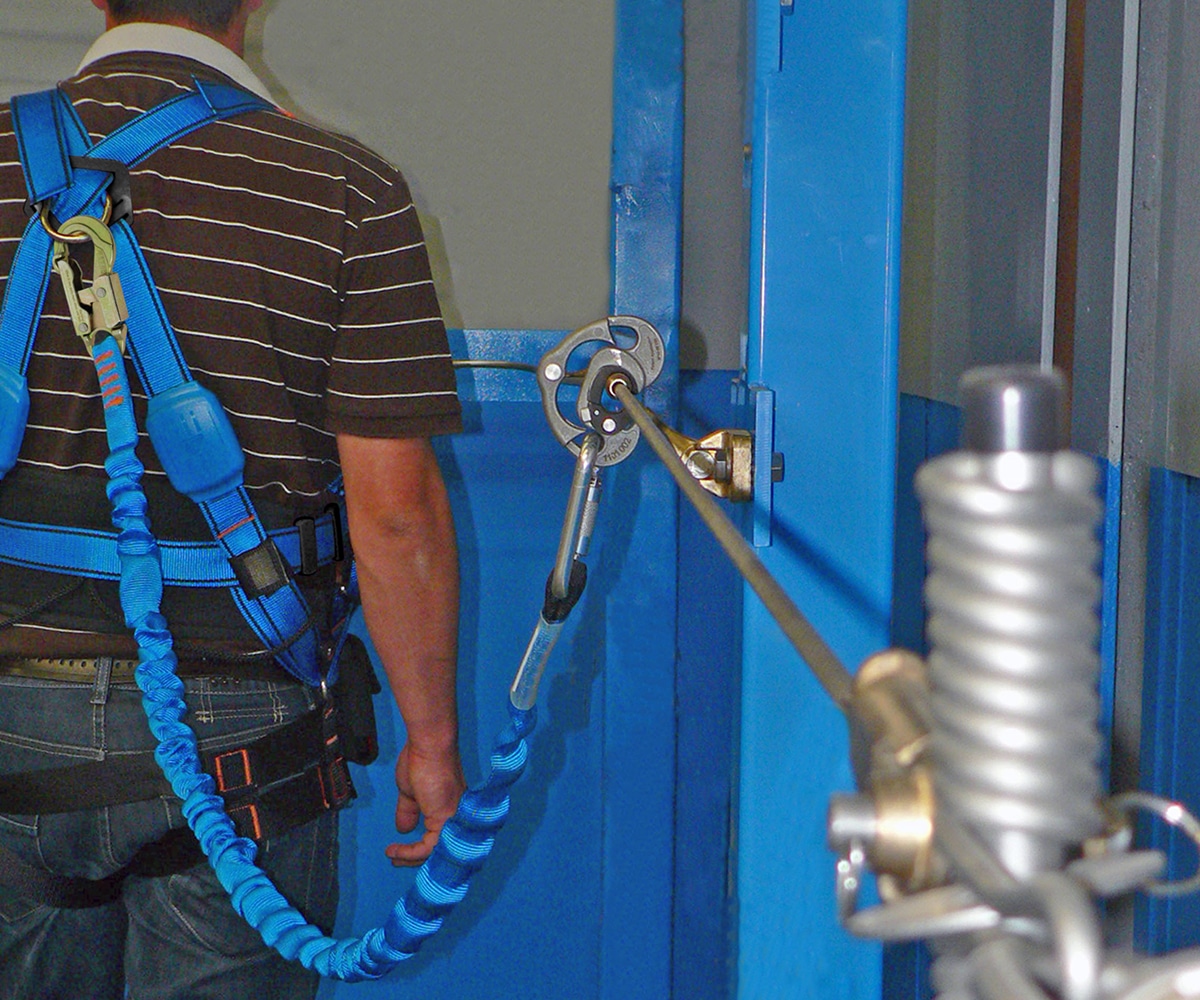
An engineered lifeline is a fall protection system which allows workers to safely move along rooftops, machinery, ladders, and other elevated working surfaces.
Paired with a proper harness and D-ring, engineered lifelines dramatically improve worker safety at heights. With a length ranging from 4’ all the way to 4,000’, lifeline systems can be a great fit for a variety of industries and applications.
Horizontal Lifeline System
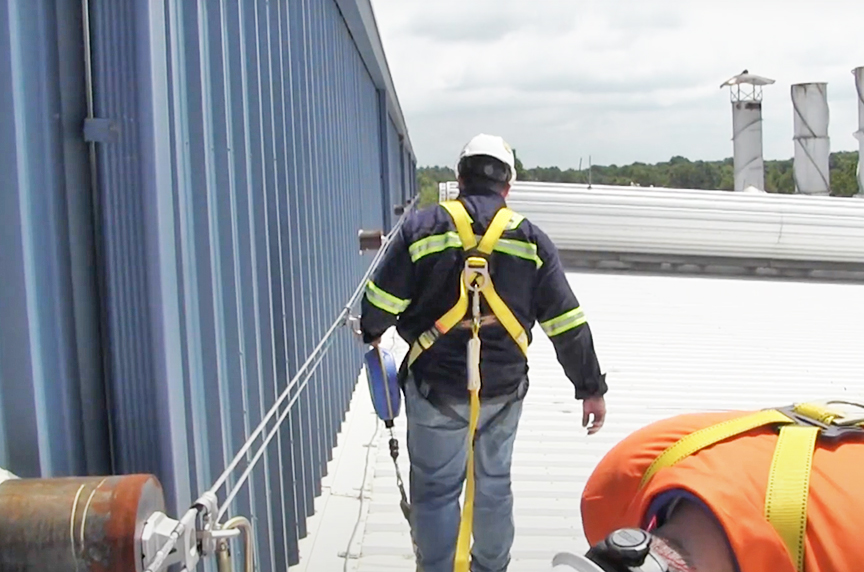
Horizontal lifelines can either be wire rope, synthetic rope, or an enclosed track system. Typically, they are mounted overhead as a permanent solution.
They are especially common in areas that lack existing anchor points for a personal tie-off. If you do fall, the system is designed to catch you in time before the next lowest obstruction.
Horizontal systems are great fits for long-spanning rooftops and facilities with low clearance conditions. Workers can be seen in horizontal lifeline systems on:
- Bridges
- Warehouses and shipping facilities
- Catwalks
- Loading docks and bays
- Runways
Vertical Lifeline System
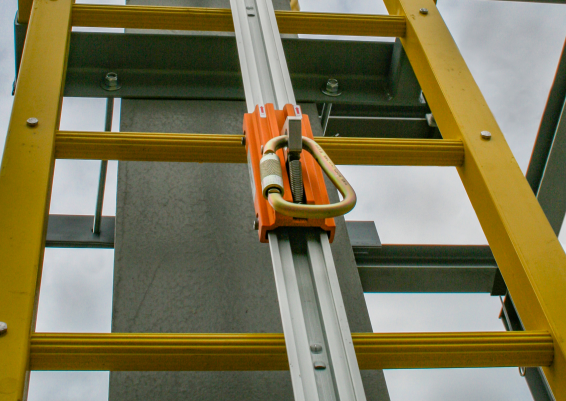
Vertical lifeline systems will be paired with permanent vertical ladders. According to OSHA standards, any ladder over 24’ in height shall have a personal fall arrest system or other ladder safety device. Vertical lifelines, like horizontal systems, limit the free fall distance for workers.
Whether inside or outside, you can find workers using vertical lifelines in a variety of fields, including:
- Cell towers
- Water towers
- Wind turbines
- Grain silos
- Amusement parks
- Oil platforms
Could You Use a Cage on a Vertical Ladder?
While cages are still common in facilities, they don’t have an attached lifeline. In the free fall process, your arm or leg could get stuck in the cage, causing severe injuries while coming down.
Furthermore, in 2018, OSHA published a new regulation saying that all new ladders must have some type of ladder safety system.
Vertical lifelines systems—that have a harness with a front D-ring—provide a much safer alternative. In fact, OSHA has announced that cage-only applications will be considered non-compliant by 2036.
What are the Training Requirements for Lifeline Systems?
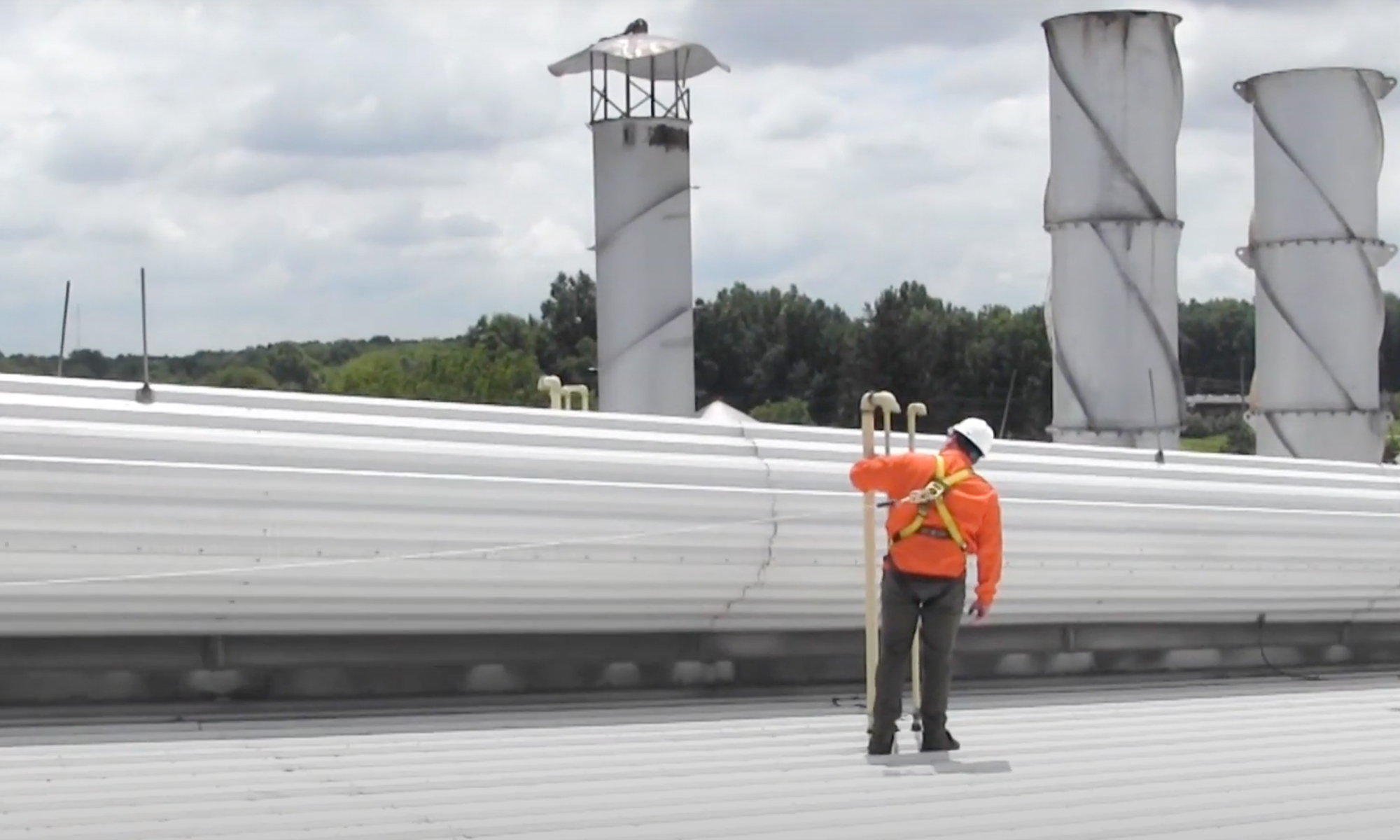
Anytime a worker is using fall protection, they shall be trained. Anybody that puts on a harness and lanyard at your facility needs to enroll, at the very least, in a basic training course.
This training will last about four hours, and attendees will learn about:
- Differences between class one and class two, which is where they’re tying off.
- How to properly don a harness
- Identify hazards
- Personal fall arrest equipment
- Know the difference between arrest and restraint
- How to properly inspect harnesses
Regarding lifeline training, it depends on the complexity of the system, but every user that goes onto the system shall be trained in how to properly use it. The more customized your system is, it can involve more training.
Typically, it’s going to be a two-hour class that covers how to properly use the system, how to properly inspect it for pre-use, and how to identify any potential issues when using a lifeline.
Inspections
The inspection schedule for your lifeline system will depend on the manufacturer’s specifications. Most inspections are annual, but heavily used systems may require multiple inspections a year.
And under OSHA’s General Duty Clause, they can fine you for violating updated ASME standards, ANSI standards, and manufacturer recommendations, even if that standard isn’t in OSHA’s guidelines.
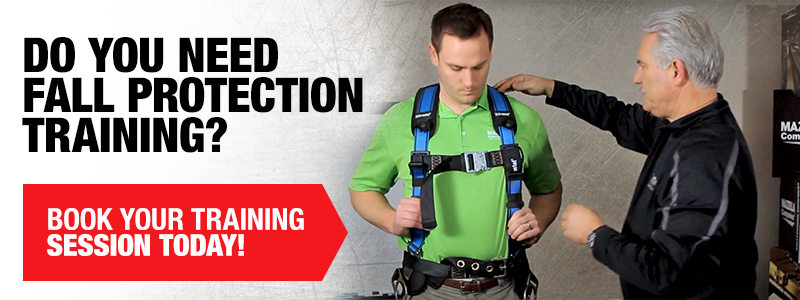
What are the OSHA Standards for Lifeline Systems?
Working at heights is inherently dangerous. As a result, OSHA has laid out rigid guidelines to keep workers safe. In general construction, workers shall be tied off anytime they are above six feet. For general industry, it is four feet.
In other cases, The Mining Safety and Health Administration (MSHA), a branch of OSHA that oversees America’s mining sector, requires fall protection or restraint anytime there’s a chance of a fall. This means they could require fall protection on a simple flight of steps.
Lifeline standards fall under OSHA 1926.502 authority. Some of the more important standards to follow include:
1926.502(d)(8):
“Horizontal lifelines shall be designed, installed, and used, under the supervision of a qualified person, as part of a complete personal fall arrest system, which maintains a safety factor of at least two.”
1926.502(d)(9):
“Lanyards and vertical lifelines shall have a minimum breaking strength of 5,000 pounds.”
1926.502(d)(11)
“Lifelines shall be protected against being cut or abraded.”
How Long Do Lifeline Systems Take to Install?
As mentioned earlier, the length of your lifeline system can vary immensely depending on the application / facility, which will directly affect your installation time.
For example, our team installed 3,300’ of lifelines on the rooftop of a military base. This mixed with seven wireless taglines and 39 SRLs in the facility’s interior took about two weeks to install.
In another example, our team installed 10,000’ of lifeline in a major manufacturing facility in four days. On the other hand, smaller lifeline systems can be installed in less than a day. According to our Fall Protection Specialists, the average installation takes about two to three days.
Not only does the amount of lifeline matter, but the complexity of your facility will also impact installation times. At Mazzella, we can schedule installation and upgrades on weekends to reduce interferences with your production schedule.
The price for a lifeline system is heavily solution-based. You have to account for many factors, like installation, engineering, soft goods, and fabrication, and your work environment.
What Is the Difference Between a Temporary and Permanent Lifeline?
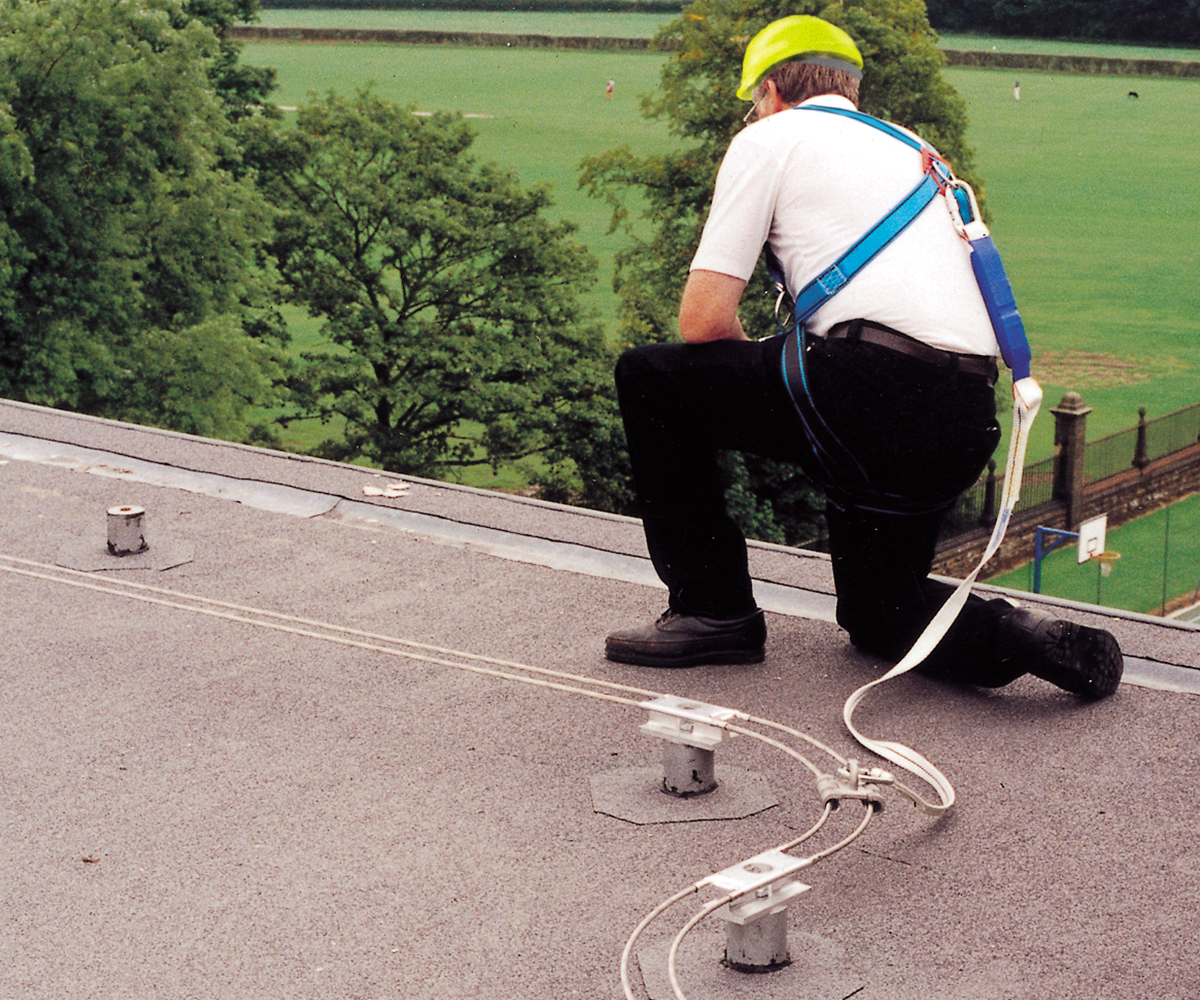
Temporary lifelines are (as the name implies) designed to be moved around a job site as projects progress.
You will see temporary lifelines at all kinds of construction sites, including bridges, dams, rooftops, and skyscrapers. You can also find them in the mining sector and in aircraft hangars.
For example, when steel erectors are building a skyscraper, they put stanchions up and then attach the wire rope on it. As the project progresses, they can move the lifeline system up with them, allowing for temporary tie-offs.
However, permanent lifelines will be great for consistent and high-use applications with lots of space. You can find permanent lifeline systems on rooftops, catwalks, and balconies. Due to these applications, permanent lifelines are made to withstand corrosion and exposure to the elements.
The two systems will also have different components. In one example, permanent lifelines will have intermediate support, while temporary lifelines do not.
What are the Benefits of a Permanent Lifeline System?
Permanent lifelines will come with swaged fittings on it as well, which helps decrease your fall clearance more than a temporary system. Permanent lifelines can also be on a wall or above the worker—it just depends on the application.
And while a permanent lifeline will cost about twice as much as a temporary system, the added safety features may be worth the investment.
Should You Use Wire Rope or Synthetic Rope?
For temporary systems, you can use either wire rope or a synthetic rope, but according to our Fall Protection experts, there are several factors to consider.
While synthetic ropes are lighter and easier to package, they will require greater clearance because it’s going to stretch way more than a wire rope.
What Is the Difference Between Engineered and Pre-Engineered Lifelines?
At Mazzella, we offer our engineered systems in a kit that specifies the distance and strength requirements needed (minimum 5,000 lbs. per person) when you install the system. Pre-engineered systems will also come with items such as a carabiner and a shock absorber.
Unlike pre-engineered systems, an engineered lifeline must be done by a manufacturer-approved installer. And while you may think you can go straight to the manufacturer and get trained, the chances are very low due to the time and cost associated with it.
Mazzella does not allow our customers to install engineered lifelines. We will do it for you. Even if you have been certified recently, the manufacturer will still send someone out to supervise you to ensure proper procedures are followed.
In short, the biggest difference between engineered and pre-engineered systems is your ability to install them.
What are the Negatives of a Lifeline System?
Compared to a rigid fall protection system, a lifeline has a much larger free fall distance and sag. This combination raises the chance of injuries occurring during secondary falls.
Because of the lower fall clearance, a rigid rail system would also be a better fit for low-headroom applications than a lifeline. Additionally, rigid systems are going to be better for organizations that need multiple users working at the same time.
Why Should You Invest in a Lifeline System?
Whether it’s vertical or horizontal, engineered or pre-engineered, or temporary or permanent, lifeline systems are an affordable and versatile fall protection system to have. And although there are applications where a rigid track system would be better, lifeline systems are a great tool to improve employee safety.
As you go through your decision-making process, consider your application, your budget, and if it’s a permanent or temporary solution.
Mazzella’s Fall Protection Specialists have inspected and installed lifeline systems in every corner of the country. Download our Fall Protection Risk Assessment Bundle to help you identify how your workers at height perform their job now and how they may need to perform it in the future. Furthermore, jump into Fall Protection Brochure to learn more about best practices.
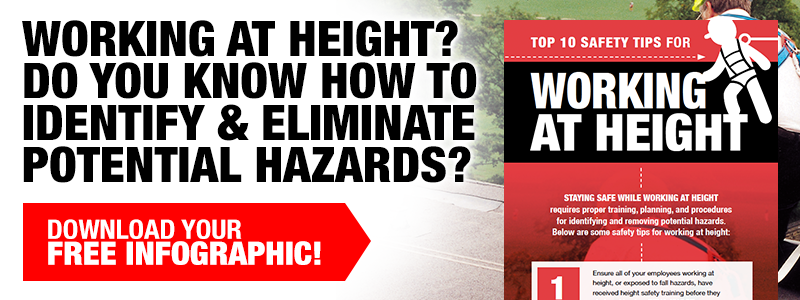
Copyright 2024. Mazzella Companies.