Understanding OSHA’s New Fall Protection Rule for Fixed Ladder Systems
OSHA is phasing out ladder cages from facilities across the country. Learn why vertical lifeline systems are a better alternative and how you can stay OSHA compliant.
For decades, ladder cages, sometimes called safety cages, were the standard fall protection method on fixed ladders at facilities. These metal enclosures, typically wrapped around the ladder’s upper sections, were intended to provide security and prevent falls for workers at height.
However, over time, safety experts and OSHA recognized that ladder cages often give a false sense of safety and are largely ineffective in stopping a worker from falling. In some cases, cages can even cause injury to workers, especially if the worker loses consciousness, slips, or becomes entangled.
Consequently, OSHA has updated its OSHA 1910.140 Personal Fall Protection Systems standards, effectively phasing out the use of ladder cages as acceptable fall protection on fixed ladders over 24′ in height, a decision that will impact general manufacturing facilities across the country.
This article will look at the key elements of the new rule, the reasons behind the change, and what it means for safety managers, facility operators, and business owners. We’ll also look at the costs, benefits, and practical steps for making the transition to a vertical lifeline system, including why you should partner with Mazzella.
- What Does OSHA’s New Fall Protection Rule Require?
- Why are Ladder Cages No Longer Considered Safe or Compliant
- Why are Vertical Lifeline Systems Better than Ladder Cages?
- How Much Do Vertical Lifeline Systems Cost?
- Why Should You Choose Mazzella as Your Fall Protection Provider?
- Final Thoughts
What Does OSHA’s New Fall Protection Rule Require?
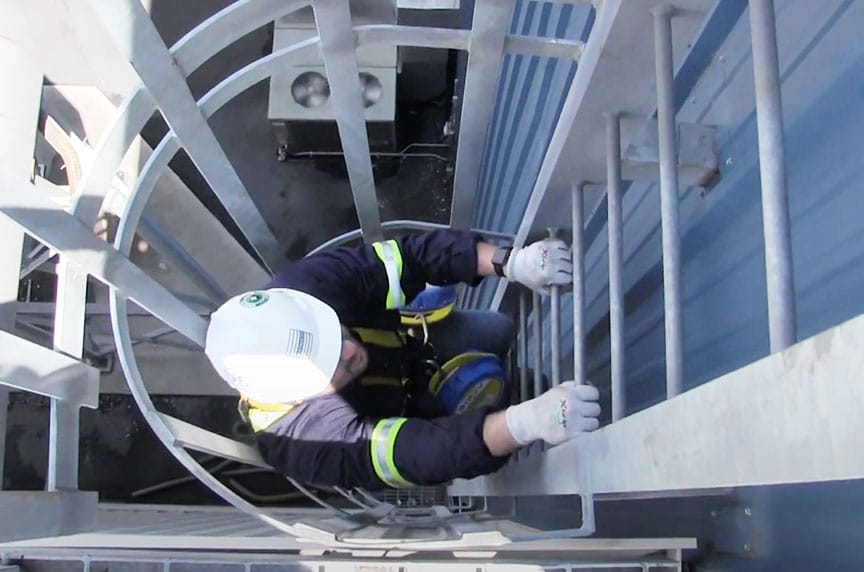
OSHA 1910.140 Personal Fall Protection Systems focuses on improving fall protection standards for fixed ladders over 24’. These ladders are commonplace in a variety of general industry facilities, including:
- Grain silos
- Warehouses and logistics centers
- Tanks
- Rooftops
- Mezzanines
- Cell towers and water towers
- Water towers
The most notable change is the removal of ladder cages from the list of acceptable fall protection methods. Moving forward, any new or existing fixed ladder over 24′ must have a personal fall arrest system.
While this rule originally applied only to the construction industry, it has expanded to cover general industry environments, too.
Why are Ladder Cages No Longer Considered Safe or Compliant?
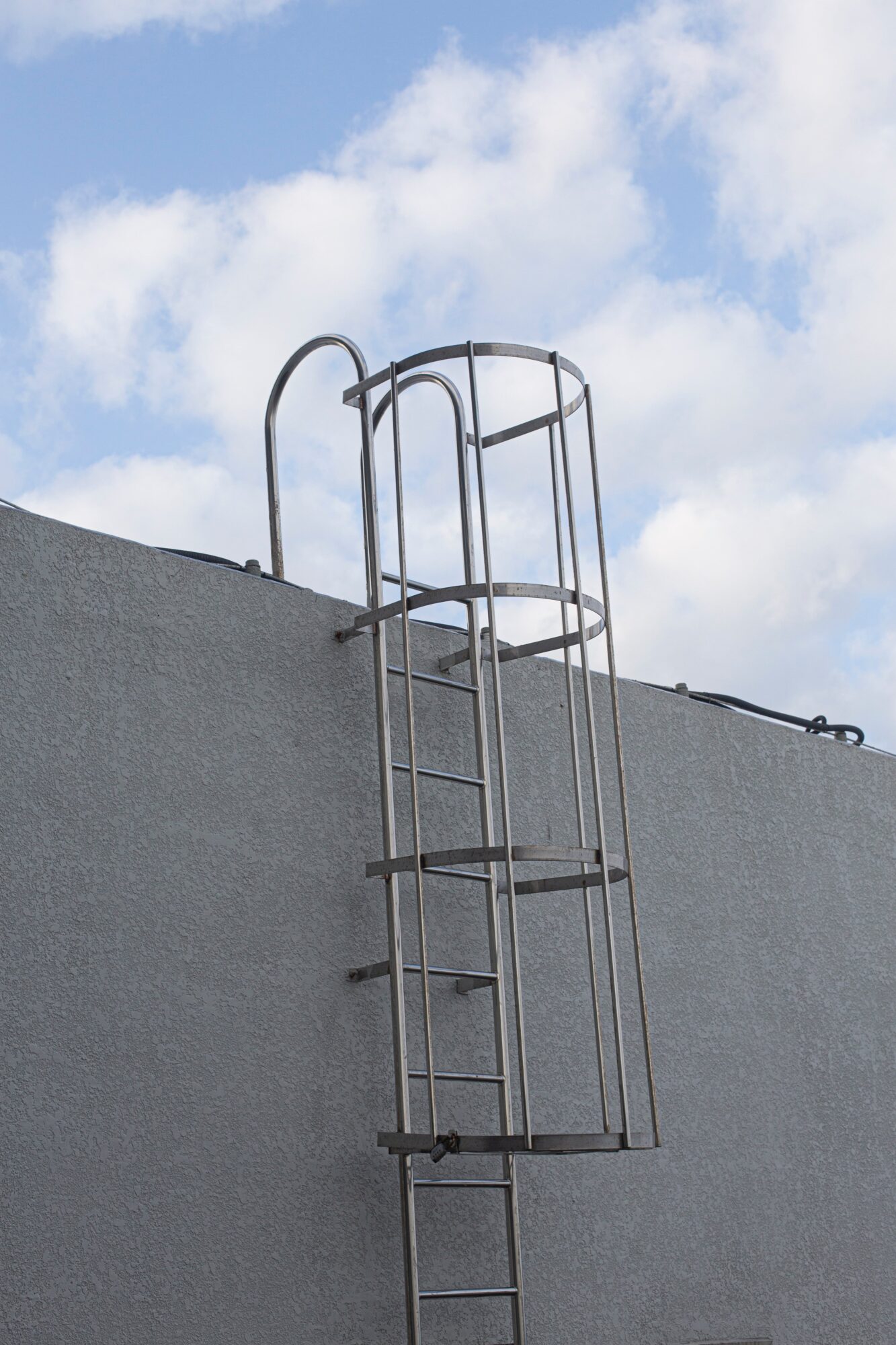
While ladder cages are common at facilities, their reputation as a legitimate safety system for workers at height has been questioned by OSHA and safety leaders over the years. In many cases, cage systems can actually lead to increased chances of injury.
Unlike personal fall arrest systems, ladder cages do not stop a fall in progress. Instead, cages can actually pose a serious threat to workers if they fall backwards. The cages are made from steel, and if a worker falls backward, their body can get tangled and make the rescue process even more challenging. Furthermore, cages offer no protection from sudden slips or missteps, particularly in wet, icy, or dirty industrial environments.
OSHA’s updated standard reflects a shift toward systems that physically intervene to prevent a fall, rather than passive systems, like cages, that merely enclose the user.
What Is the Compliance Standard for Replacing Ladder Cage Systems?
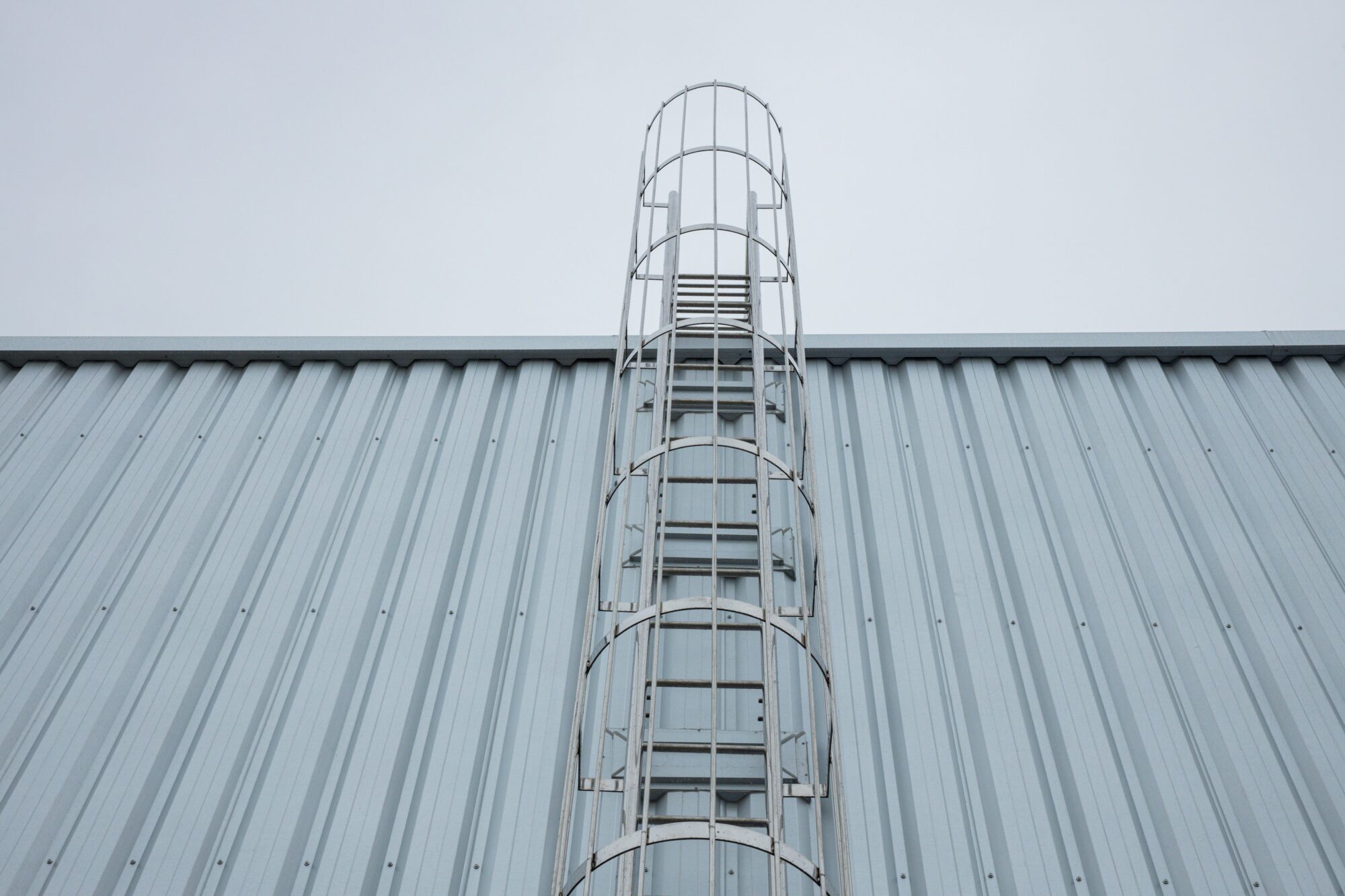
OSHA has set a compliance deadline of November 18, 2036, for retrofitting existing ladders. However, any new or replacement ladders installed after November 19, 2018, must already comply with the updated standard.
Employers are responsible for not only installing these systems but also ensuring they are used and maintained properly.
Training and Inspection Requirements
Employers are also responsible for training employees on how to use personal fall arrest systems correctly and performing both annual inspections by an authorized person and visual inspections before each use.
Failure to comply can result in citations, fines, and increased liability in the event of an accident.
Why are Vertical Lifeline Systems Better than Ladder Cages?
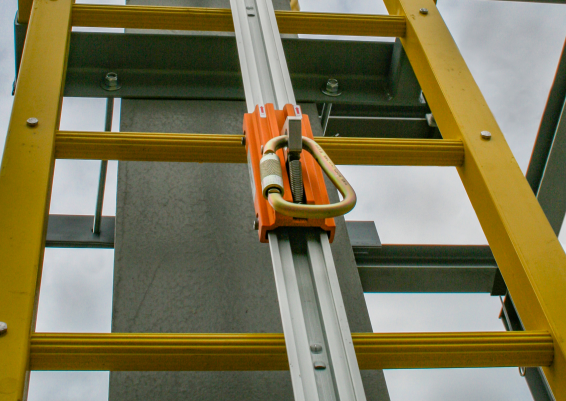
With ladder cages being phased out by OSHA, vertical lifeline systems are going to be the natural successor.
A typical vertical lifeline system setup includes a vertical cable or rail attached to the ladder structure, along with a fall arrest device that connects to the worker’s harness. As the worker ascends or descends, the device moves with them and locks instantly in the event of a fall. This feature, unlike a cage, significantly reduces the chance of a secondary injury occurring.
Benefits of a Vertical Lifeline System
Vertical lifeline systems are easy to use, especially for workers who routinely climb fixed ladders on tall structures. They also free up space and improve access to the ladder. Plus, many vertical lifeline systems can be retrofitted, which means you wouldn’t have to replace the entire ladder system.
You can also galvanize the cable on a vertical lifeline system to make it more durable for outdoor applications.
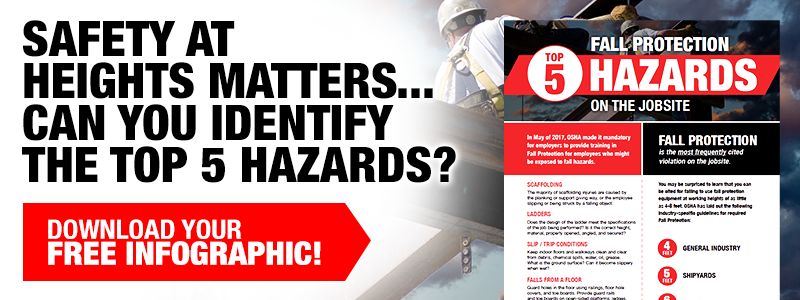
How Much Do Vertical Lifeline Systems Cost?
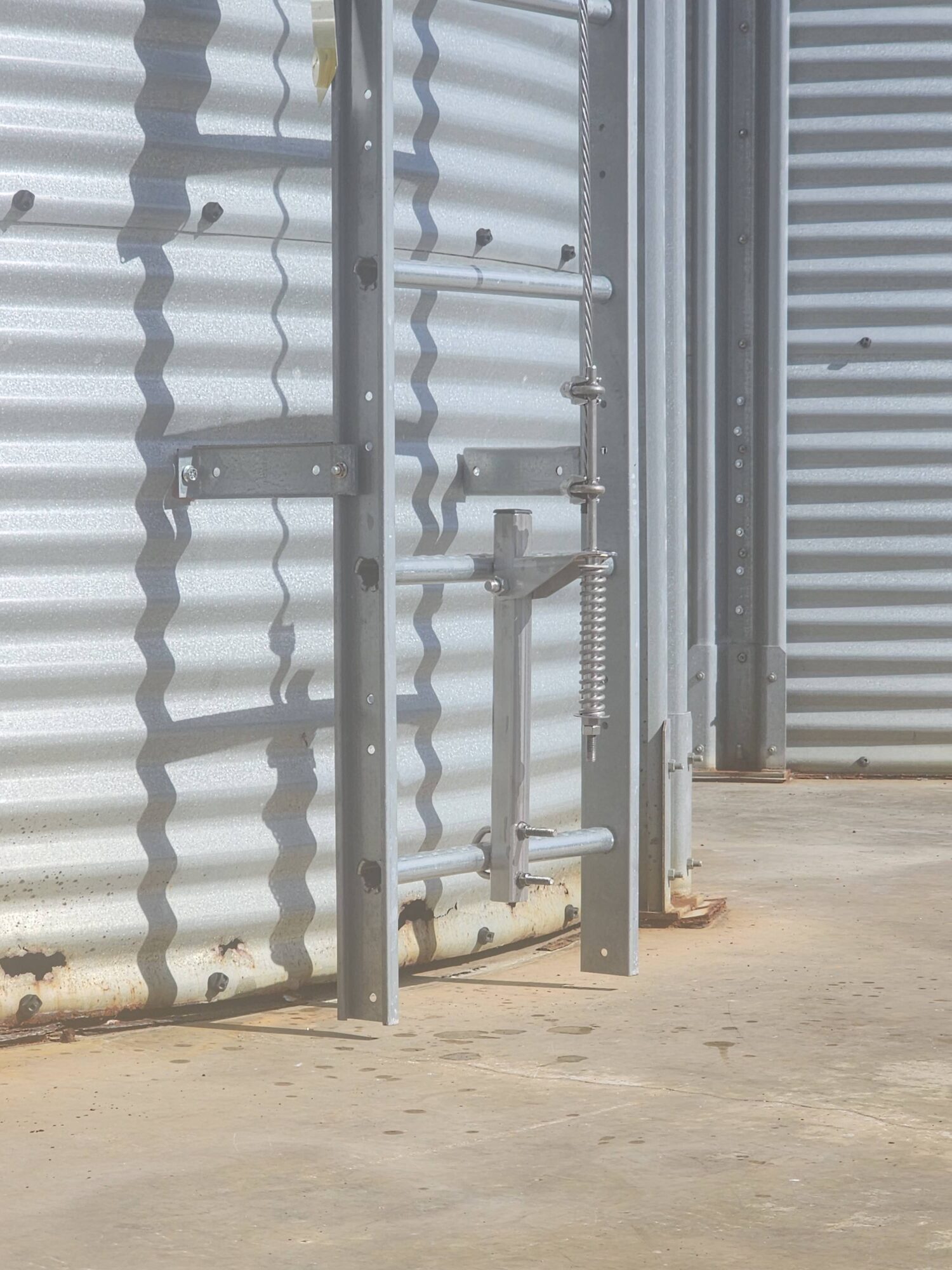
Installing a new vertical lifeline system typically runs around $2,000-$5,000 per ladder. However, prices can vary depending on factors like height, structural complexity, installation labor, and geographic location.
Employers should also factor in ongoing inspection and maintenance requirements, which include annual inspections by a competent person and visual checks before each use.
While the upfront investment may seem significant, it’s a small price compared to the potential costs of injuries, OSHA fines, or lost productivity.
How Can You Plan for OSHA Ladder Cage Compliance by 2036?
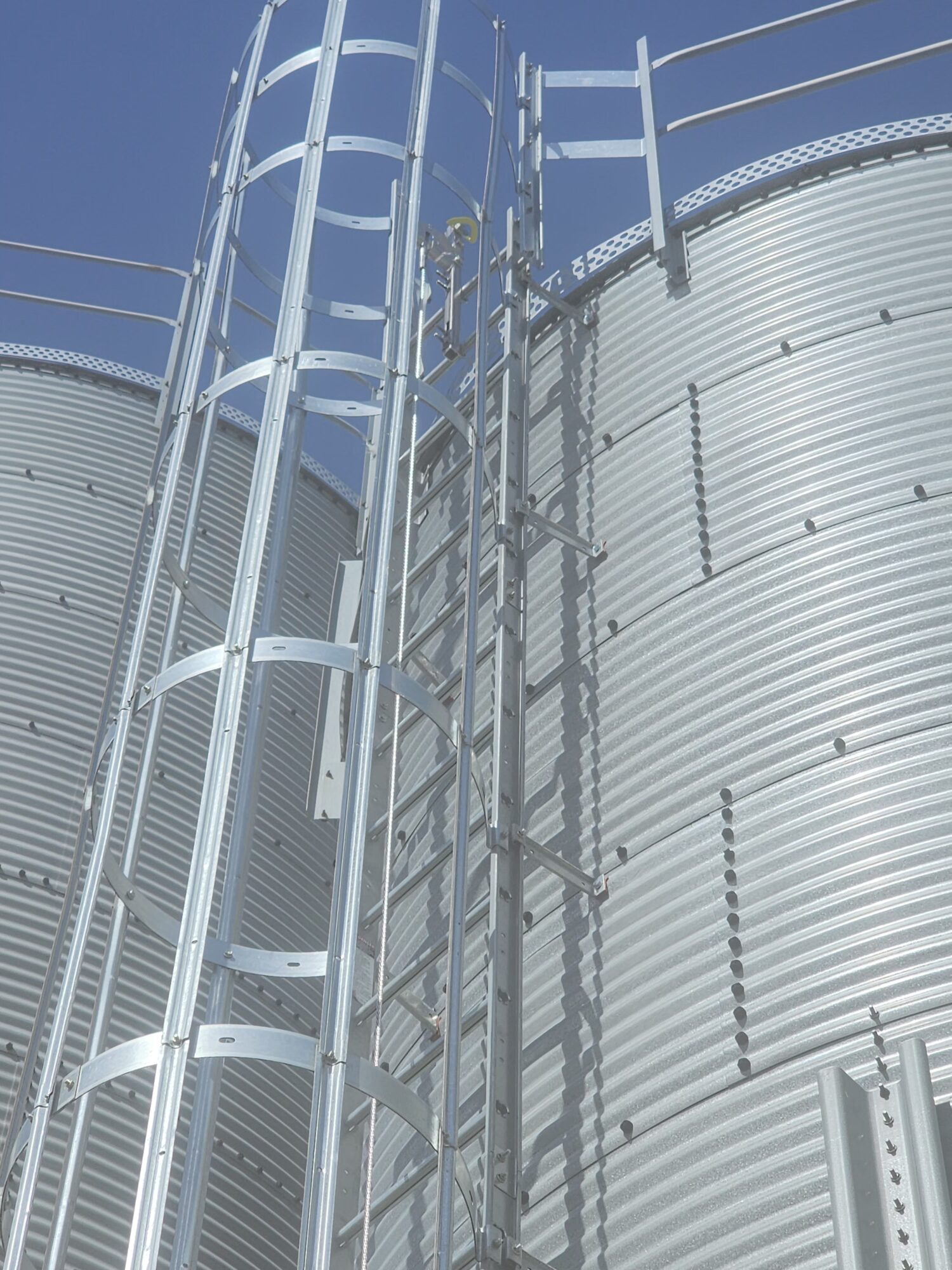
While the OSHA-mandated deadline of 2036 seems far away, procrastinating the replacement of your ladder cages could create unnecessary risks and logistical headaches, especially if your facility has multiple ladders that need to be upgraded.
General industry companies have to constantly deal with supply chain issues, labor shortages, and scheduling backlogs. It’s easy for deadlines like this to slip through the cracks, which is why the best time to start planning is now. Here’s how to get started:
Audit Existing Ladders
Work with your Safety Managers, Plant Managers, and other relevant parties to determine which ladders exceed the 24′ threshold and determine whether they already have compliant fall protection systems installed.
For those still using cages or lack fall protection, flag them for immediate action. A site inspection by a fall protection expert can help assess your current risks and compliance status.
Focus on a Phased Implementation Plan
A phased implantation plan allows you to manage costs more effectively, schedule installations during downtime, and train employees gradually. Integrating fall protection upgrades into planned maintenance cycles can also help minimize disruption.
Plan to Update Your Training and System Maintenance Protocols
Even the best fall protection systems can fail if not used properly or regularly inspected. Create a plan for training workers on how to use personal fall arrest systems. You should also establish a routine inspection schedule to ensure continued compliance and safety.
Anytime a worker uses fall protection, they shall be trained. Anybody that puts on a harness and lanyard at your facility needs to enroll, at the very least, in a basic fall protection training course.
Why Should You Choose Mazzella as Your Fall Protection Provider?
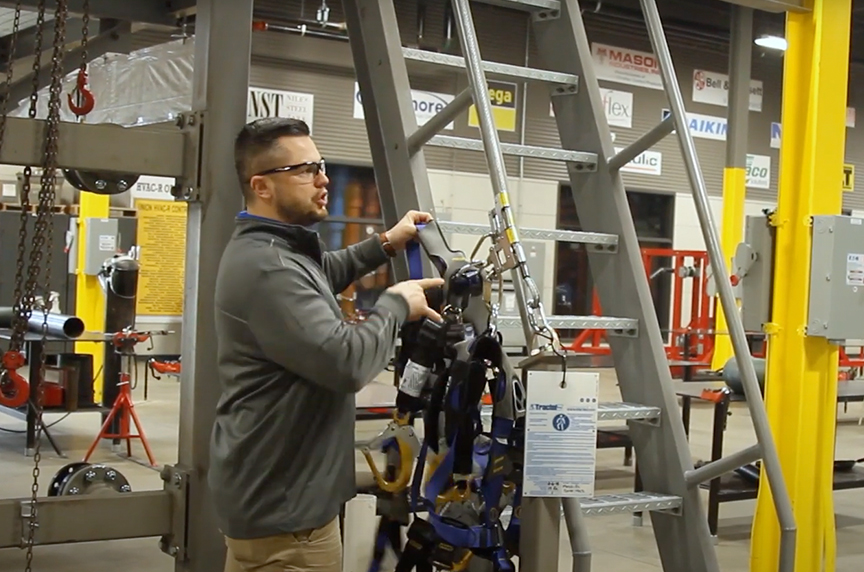
Staying OSHA compliant, especially with fall protection, is not easy. It’s why partnering with a trusted fall protection partner is crucial for long-term success and safety for your workers. Some of the biggest benefits of partnering with Mazzella to upgrade your vertical fall protection systems include:
Great Pricing from Trusted Brands
Mazzella partners with some of the most reliable vendors in the fall protection industry, including 3M and SafeWaze, who are leaders in manufacturing vertical lifeline systems. Our partnerships allow for short lead times and better pricing.
Quick Installation Times
We have a proven track record of installing these systems quickly. According to our Fall Protection team, the typical turnaround time on a vertical lifeline system from purchase to installation is 20 days maximum.
Flexible Scheduling
If needed, our team can work after hours or weekends to install systems. However, since most fixed ladders are on the outside of a building, you can expect little to no disruption to your daily operations.
Beyond installation, Mazzella supports ongoing compliance by offering inspection services, training programs, and guidance on proper equipment use. This full-service approach ensures not only that companies meet OSHA’s requirements and function safely and effectively for years.
We train on every fall protection system we install to ensure the system is being used properly. We also document this inspection so you can have it on file when an inspector arrives at your facility.
Final Thoughts
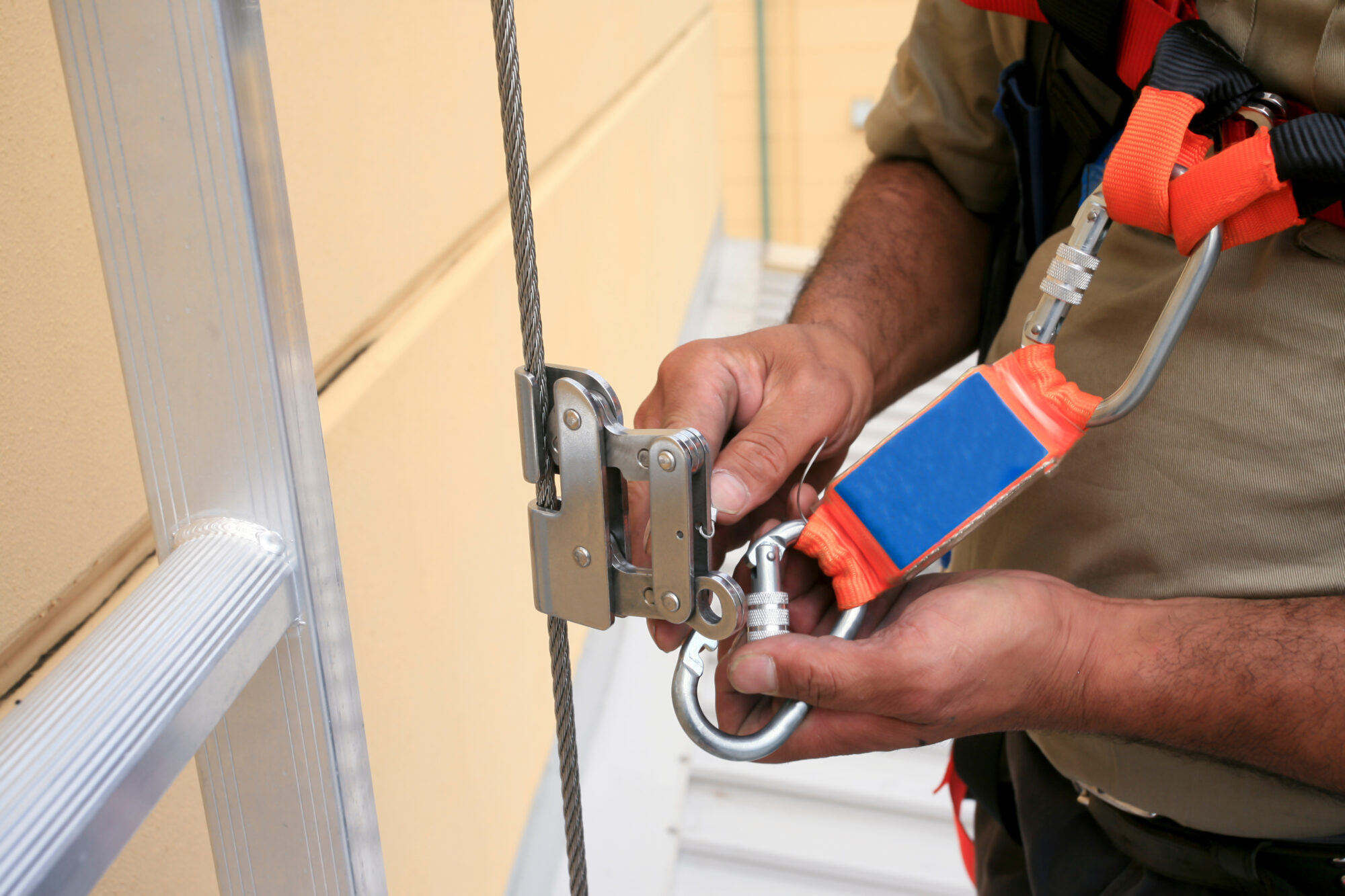
With ladder cages no longer considered compliant, and the deadline to implement personal fall arrest systems approaching in 2036, upgrading to a vertical lifeline system will help your company improve worker safety and productivity compared to outdated cage setups.
You shouldn’t have to wait until the 2036 deadline to improve worker safety. Start assessing your ladder safety strategy today to ensure your workforce is protected and your business is fully aligned with OSHA’s evolving standards.
Partnering with a trusted provider, like Mazzella, can help streamline the transition process, reduce administrative burdens, and ensure your investment in fall protection truly safeguards your workforce. Read our article to learn more about the different types of lifeline fall protection systems. Furthermore, contact a member of our Fall Protection team if you have any questions.
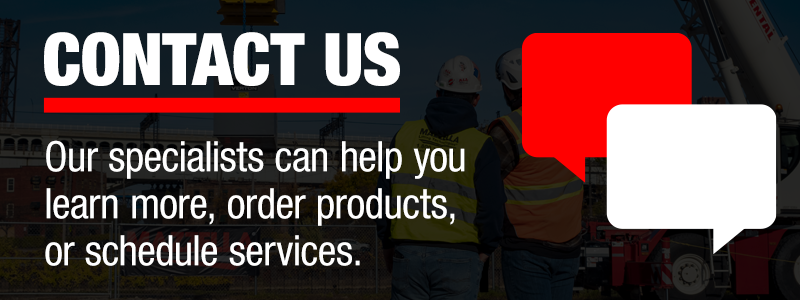
Copyright 2025. Mazzella Companies.