What Are ASME’s Inspection Standards for Vacuum Lifting Devices?
What are the inspection requirements for vacuum lifting below-the-hook devices? The American Society of Mechanical Engineers (ASME) sets the standard for all inspections, including types and frequencies.
“Safety is everyone’s responsibility.”
Regardless of your job on a work site, your safety and that of your coworkers could be placed in jeopardy by making unsafe overhead lifts. Inspections of your below-the-hook lifting devices are a key part of keeping your equipment in compliance with industry standards, and also, safety at the forefront of every lift.
There are six types of below-the-hook lifting devices:
- Structural and Mechanical Lifting Devices
- Vacuum Lifting Devices
- Close Proximity Operated Lifting Magnets
- Remotely Operated Lifting Magnets
- Scrap and Material-Handling Grapples
- Clamps
Each device is used for different purposes, and as such, has its own inspection, testing and maintenance requirements. In this piece, we will look at vacuum lifting devices and provide the following information as listed in the ASME B30.20 Below-the-Hook Lifting Devices standard:
- Inspection classification for vacuum lifting devices
- Removal from service criteria
- Testing of repaired vacuum lifting devices
- Maintenance for vacuum lifting devices
Inspection Classification
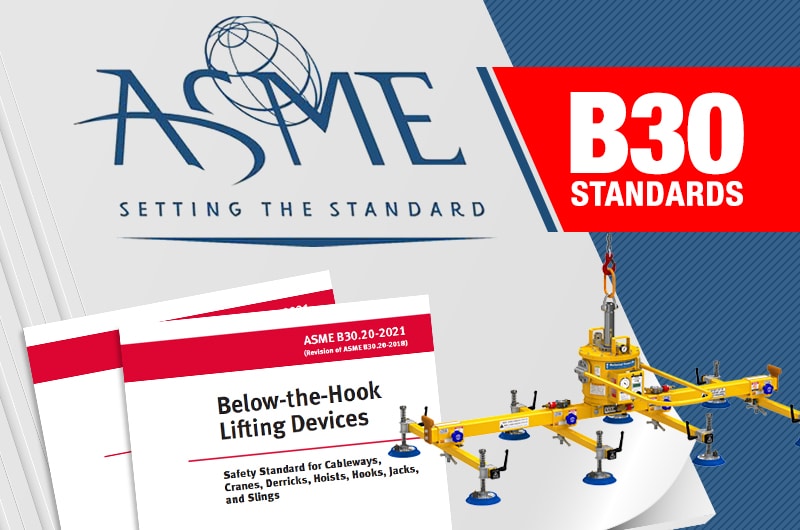
Not all below-the-hook lifting devices are made the same, as they are designed for very specific tasks. As such, each come with their own inspection and testing requirements. Also, there will be times when repairs need to be done, and that process is outlined in ASME B30.20.
In Chapter 2 of the ASME B30.20 Below-the-Hook Lifting Devices standard, the B30 Committee outlines the following:
- Inspection
- Testing
- Maintenance
General
All inspections shall be performed by a designated person. Any deficiencies identified shall be examined and a determination made by a qualified person as to whether they constitute a hazard, and, if so, what additional steps need to be taken to address the hazard.
Inspection of slings (ASME B30.9), hooks (ASME B30.10), rigging hardware (ASME B30.26), or other special devices shall comply with the inspection requirements in the applicable volume.
Initial Inspection
New and reinstalled vacuum lifters shall be inspected prior to initial use to verify compliance with applicable provisions of this Volume. Altered or repaired vacuum lifters shall be inspected. The inspection may be limited to the components affected by the alteration or repair, as determined by a qualified person.
Inspection Intervals. Inspection procedure for vacuum lifting devices in regular service is divided into three general classifications, based upon the intervals at which inspection should be performed. The intervals, in turn, are dependent upon the nature of the critical components of the vacuum lifting device and the degree of their exposure to wear, deterioration, or malfunction.
The three general classifications are designated as every lift, frequent, and periodic, with respective intervals between inspections as defined below.
Every Lift Inspection. Visual examination by the operator before and during each lift made by the vacuum lifting device.
Frequent Inspection. Visual examinations by the operator or other designated persons with records not required.
- Normal service — monthly
- Heavy service — weekly to monthly
- Severe service — daily to weekly
- Special or infrequent service — as recommended by a qualified person
Periodic Inspection. Documented visual inspection of apparent external conditions to provide the basis for a continuing evaluation.
- Normal service for equipment in place — yearly
- Heavy service — semiannually
- Severe service — quarterly
- Special or infrequent service — as recommended by a qualified person before the first lift and as directed by the qualified person for any subsequent lifts
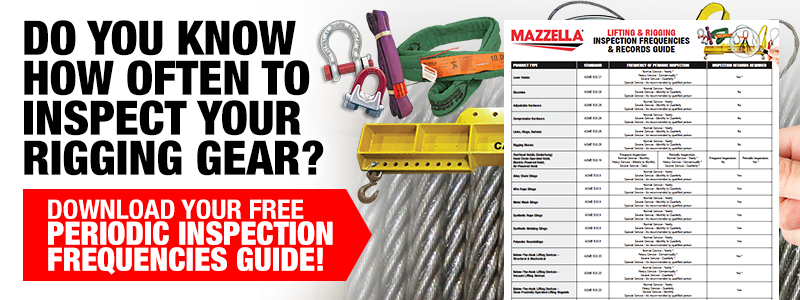
What Are Inspectors Looking for on Vacuum Lifters?
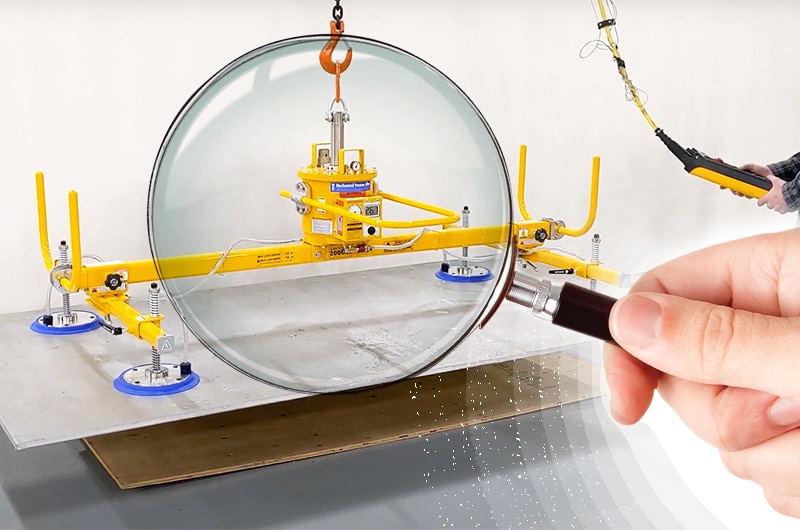
Along with the initial inspection, ASME B30.20 lists several other types of inspections for vacuum lifting devices to make sure they are in working order and safe for employees to use.
Every Lift Inspection
Vacuum lifters shall be inspected by the operator before and / or during every lift for any deficiencies as specifically indicated, including:
- Surface of the load for debris
- Seal of the vacuum pad for debris
- Condition and operation of the controls
- Condition and operation of the indicators, meters, and pumps when installed
Frequent Inspection
Vacuum lifters shall be inspected at intervals as defined in para. 20-2.3.1(b)(2). Conditions such as those listed in para. 20-2.3.7, or any other condition that may constitute a hazard, shall cause the vacuum lifter to be removed from service. A qualified person shall determine whether any deficiency constitutes a hazard, requires a repair, requires disassembly for further inspection, or will require more frequent inspection. The lifter shall not be returned to service until approved by a qualified person.
Periodic Inspection
Complete inspections of the vacuum lifting device shall be performed at intervals as defined in para. 20-2.3.1(b)(3). Conditions such as those listed in para. 20-2.3.7, or any other condition that may constitute a hazard, shall cause the vacuum lifter to be removed from service. A qualified person shall determine whether any deficiency constitutes a hazard, requires repair, requires disassembly for further inspection, or will require more frequent inspection. The vacuum lifter shall not be returned to service until approved by a qualified person. The inspection shall be based on the manufacturer’s instructions, para. 20-2.3.7, or the recommendation of a qualified person.
***The references to para. 20-2.3.7 outline the removal from service criteria discussed below.
The references to para. 20-2.3.1(b)(2) and 20-2.3.1(b)(3) list the frequency for when inspections need to be performed. This was discussed in the above section.
Vacuum Lifters Not in Regular Use
What if your vacuum lifters are not used on a consistent basis? How often do they need to be inspected?
According to the ASME B30.20 standard, “a vacuum lifter that has been idle for a period of one month to one year shall be inspected in accordance with para. 20-2.3.3 before being placed in service. A vacuum lifter that has been idle for a period of one year or more shall be inspected in accordance with para. 20-2.3.4 before being returned to service.”
***The paras. 20-2.3.3 and 20-2.3.4 state that each inspection shall be conducted by a qualified person.
What Inspection Records Need to be Kept?
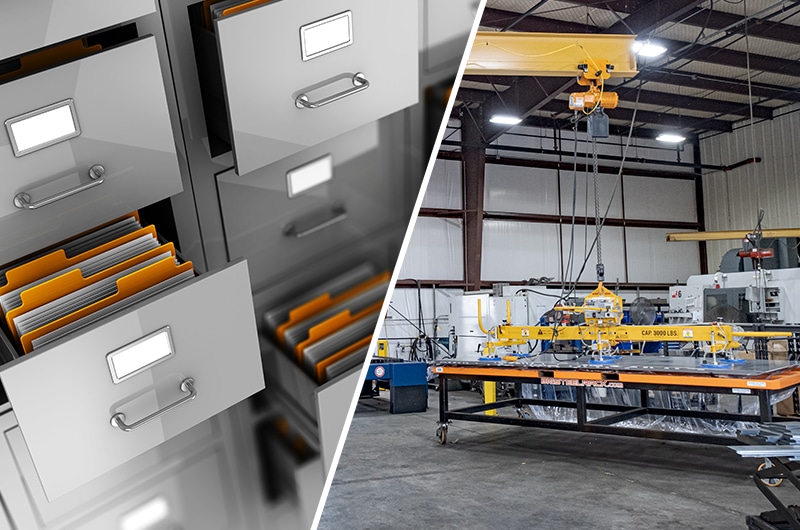
Once an inspection is complete, how long do the records need to be kept on file by the end-user?
According to the standard, dated inspection reports shall be made on critical items such as those listed in para. 20-2.3.4. Records should be available for each periodic inspection and when the vacuum lifter is either altered or repaired.
***The paras. 20-2.3.3 and 20-2.3.4 state that each inspection shall be conducted by a qualified person.
What Is the Removal Criteria for Vacuum Lifters?
A vacuum lifter shall be removed from service if conditions (if applicable) such as the following are present (limits established by the manufacturer or qualified person) and shall only be returned to service when approved by a qualified person:
- Deformation, cracks, or wear
- Loose or missing guards, fasteners, covers, stops, or nameplates
- Excessive pitting or corrosion
- Excessive nicks or gouges
- Indications of heat damage
- Unauthorized welds or modifications
- Unauthorized replacement components
- Improper assembly or function
- Impaired, seized, or bound moving parts
- Vacuum leaks greater than manufacturer specification [see para. 20-2.3.9.1(c)]
- Vacuum pads
- Contamination
- Excessive surface wear
- Lack of integrity of the seal material
- Reduced coefficient of friction
- Damaged or distorted pins
- Vacuum hoses and fittings
- Loose or disconnected hoses
- Kinked, collapsed, or damaged hoses
- Dirty or missing filters
- Deformed, broken, or missing components
- Missing or illegible operation control markings or product safety labels
- Other conditions, including visible damage, that cause doubt as to continued safe use
- Inability to achieve designated minimum vacuum level
- Incorrect operation or function of any controls, indicators, or warning devices
What Are the Repair Requirements for Vacuum Lifters?
Deficiencies disclosed by the inspection requirements of Section 20-2.3 shall be corrected according to the procedures outlined in para. 20-2.3.10 before operation of the vacuum lifter is resumed, unless a qualified person determines the deficiency does not constitute a hazard.
Repairs of slings (ASME B30.9), hooks (ASME B30.10), rigging hardware (ASME B30.26), or other special devices shall comply with repair requirements in the applicable volumes or standards.
***Para. 20-2.3.10 outlines the maintenance program and procedures that need to take place before a vacuum lifter is returned to service.
What Tests Do Vacuum Lifters Need before being Used in a Lift?
Whether your vacuum lifter is new or has been repaired, there are multiple tests that have to be performed on the device to ensure it is in compliance with the standard and ready to be put into service.
Vacuum lifters must undergo the following types of tests:
- Operational tests
- Load tests
Operational Tests
New and reinstalled lifting devices shall be tested by, or under the direction of the manufacturer or a qualified person prior to initial use to verify compliance with applicable provisions of this Volume, including, but not limited to, the following:
- Moving parts
- Latches
- Stops
- Limit switches
- Control devices
- Vacuum pad seals
- Vacuum lines
Altered or repaired lifting devices shall be tested by a qualified person, or a designated person under the direction of the manufacturer or a qualified person. This test may be limited to the components affected by the alteration or repair, as determined by a qualified person with guidance from the manufacturer.
The seals and connections shall be tested for leaks by attaching a smooth, nonporous, clean material to the vacuum pad or pads, and then, stopping the vacuum source. Vacuum level in the system shall not decrease by more than the manufacturer’s specified rate.
All indicator lights, gauges, horns, bells, pointers, and other warning devices and vacuum level indicators shall be tested by the same method as in para. 20-2.3.9.2, which outlines the procedures for load testing.
Dated reports of all operational tests shall be filed.
Load Tests
Prior to initial use, all new, altered, or repaired vacuum lifting devices shall be load tested and inspected by a qualified person, or a designated person under the direction of the manufacturer or a qualified person. A written report shall be prepared by the qualified person and placed on file, confirming the load rating of the vacuum lifting device. Test loads shall not be more than 125% +5%/−0% of the rated load of the system, unless otherwise recommended by the manufacturer or a qualified person.
Altered or repaired vacuum lifting devices shall be tested by, or under the direction of, a qualified person. This test may be limited to the components affected by the alteration or repair, as determined by a qualified person with guidance from the manufacturer.
The load test shall consist of one of the following procedures:
- Actual Load Test
- Attach pads to the designated test load
- Raise the test load a minimum distance to ensure the load is supported by the vacuum lifting device
- Hold the load for 2 minutes
- Lower the load for release
- Simulated Load Test
- Using a test fixture, apply forces to all load-bearing components, either individually or in assemblies, equivalent to the force encountered by the components if they were supporting a load that was 125% of the rated load.
After the test, the vacuum lifting device shall be visually inspected. Any condition that constitutes a hazard shall be corrected before the lifting device is placed in service. If the correction affects the structure, then the lifter shall be retested.
What Maintenance Programs Are Required for Vacuum Lifters?
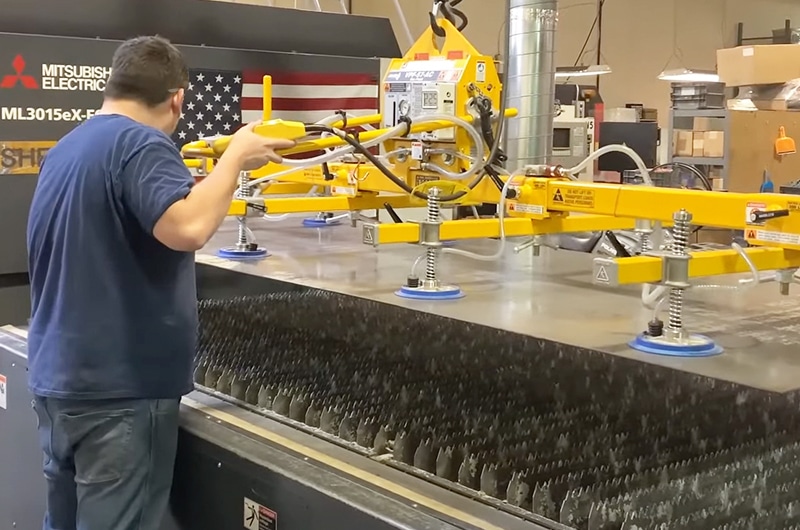
No matter how much care one takes with their equipment, eventually parts do wear out and need to be replaced. To avoid undo wear and tear on your vacuum lifters and their components, there are regular maintenance steps that can be taken to extend service life.
Maintenance Program
A maintenance program shall be established and be based on recommendations made by the vacuum lifting device manufacturer. If a qualified person determines it is appropriate, the program should also include that individual’s additional recommendations based on a review of the vacuum lifting device application and operations.
Maintenance Procedure
Before adjustments and repairs are started on a vacuum lifting device, the following precautions shall be taken:
- Locate the vacuum lifting device where it will cause the least interference with other operations in the area.
- All sources of power shall be disconnected, locked out, and tagged “Out of Service.”
- Relieve fluid pressure from all circuits before loosening or removing fluid power components.
Only designated personnel shall perform adjustments, repairs, and tests when required.
- Provisions should be made for designated persons to work on energized equipment when adjustments and tests are required.
- All moving parts of the vacuum lifting device for which lubrication is specified should be regularly lubricated. The manufacturer’s recommendations as to points and frequency of lubrication, maintenance of lubrication levels, and types of lubricant should be used.
- Adjustments shall be maintained to assure correct functioning of components.
- Repairs or replacements shall be made as needed.
Replacement parts shall be at least equal to the original manufacturer’s specifications.
After adjustments and repairs have been made, the vacuum lifting device shall not be returned to service until it has been inspected according to para. 20-2.3.4.
Dated records of repairs and replacements should be made.
How Can Mazzella Help You with Vacuum Lifters?
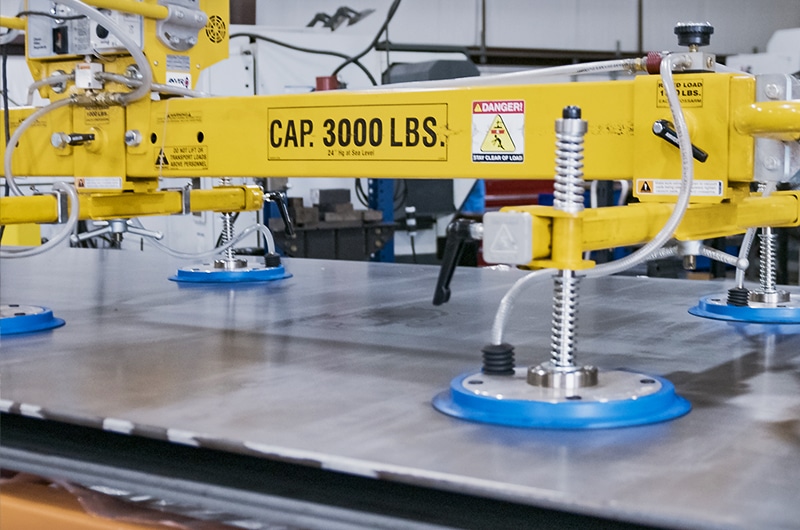
We provide vacuum lifters, vacuum lifting systems, and custom vacuum lifting equipment of all types!
These vacuum tube lifting systems are ergonomic lift assist devices that can help increase your productivity while offering an economic solution to your material handling needs.
These vacuum tube lifting systems grab the load (via vacuum suction), support, lift and lower the load without the use of a hoist, all by means of a single operator control.
The use of vacuum suction pads for attachment allows objects to be lifted without fear of damage to the surface or edges of the product, often caused by manual lifts or grabs. A remotely connected high-efficiency vacuum pump supplies vacuum power to the vacuum lift tube to lift and lower the attached load.
Call us at 800.362.4601 or click here if you need a vacuum lifting solution!
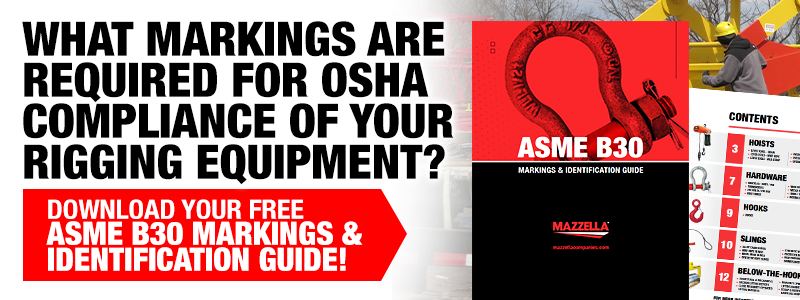
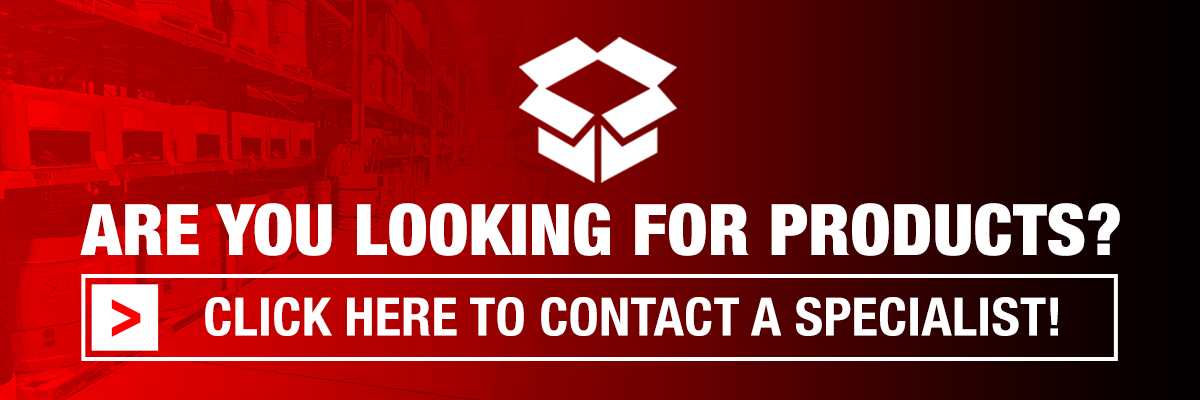
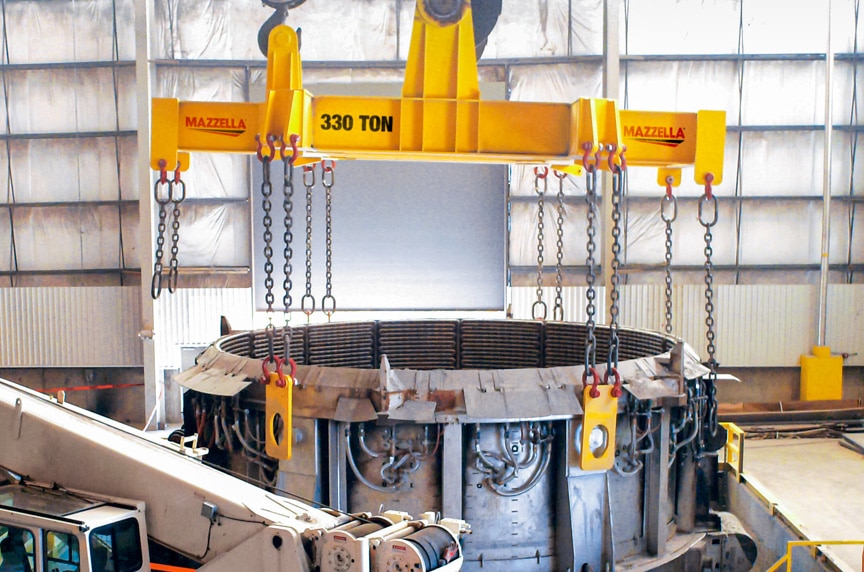
Below-the-Hook Lifting Devices
We have more than 65 years of experience in designing and developing custom engineered products, below-the-hook lifting devices, and lifting attachments for use with all types of cranes.
On-staff engineering and our commitment to ISO 9001: 2015 guides us to continued success in quality products and processes.
Copyright 2022. Mazzella Companies.