What is Caldwell’s Dura-Lite™ Composite Lifting Beam?
Are you looking for a lightweight lifting beam that has a high capacity? Caldwell’s Dura-Lite™ Composite Lifting Beam is the answer you’ve been looking for.
“It’s not the size of the dog in the fight. It’s the size of the fight in the dog.” -Archie Griffin
The words of the two-time Heisman Trophy-winning running back and Ohio State football legend apply to many different fields. They describe a product Caldwell Lifting Solutions in Rockford, Illinois created: the Dura-Lite™ composite lifting beam.
Despite weighing a fraction of what its steel lifting beam or spreader bar counterparts do, the composite lifting beams could lift half-ton loads, or something as heavy as a:
- Grand piano
- Baby elephant
- Pile of more than 200 bricks
Dan Mongan, Caldwell’s senior sales engineer, explained the pros and cons, real-world applications, and why you might want to choose composite over a metal beam.
In this article, you will learn the answers to the following questions:
- What is the Dura-Lite™ Lifting Beam made from?
- What are the advantages of using a composite lifting beam?
- Is the Dura-Lite™ composite beam as strong as steel?
- What are the disadvantages of using a composite lifting beam?
- Are there real-world examples of companies using composite lifting beams?
- Are composite beams the future of lifting?
What Is the Dura-Lite™ Lifting Beam Made From?
The Dura-Lite™ Lifting Beam is innovative.
Nobody else in the industry has lifting equipment that is manufactured from composite materials. In fact, Caldwell has a patent on this technology. The technical word for the materials Caldwell is using is FRP, or Fiber-Reinforced Polymer. It’s essentially a high-strength fiberglass specially developed for use in the lifting and rigging industry.
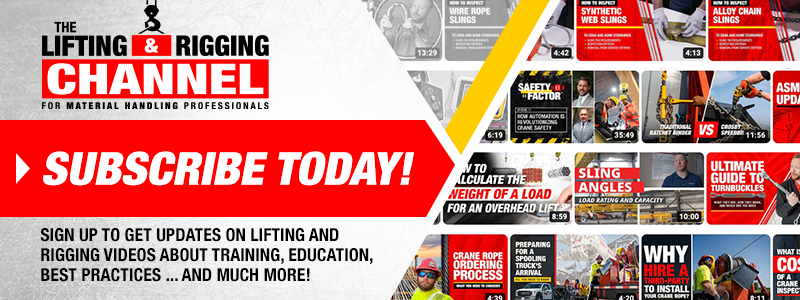
What Are the Advantages of Using a Composite Lifting Beam?
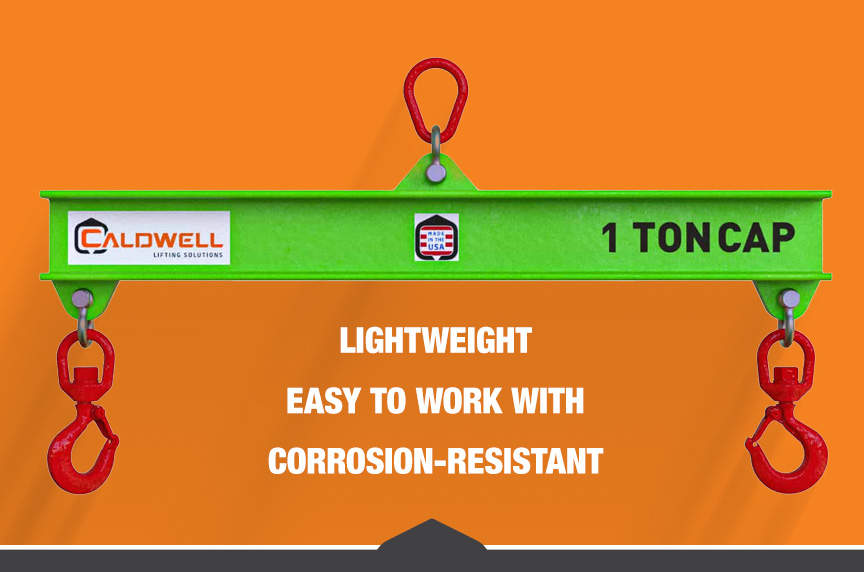
There are several significant advantages to using composite over a steel lifting beam.
The obvious one is they weigh about half of what a steel version would weigh. If you’re on a construction site, you can just place the Dura-Lite™ Lifting Beam in the back of a pickup truck for transport. If you had a steel version, you’d have to get a forklift or you’d have to use a crane to move it.
Also, there’s certainly advantages to freight. These items can be shipped easily using UPS or FedEx. However, steel lifting beams would have to go LTL freight.
Aside from weight, the Dura-Lite™ Lifting Beam offers end-users corrosion resistance. If you think about the marine industry, it’s an ideal piece of equipment to use on a ship that may need a lifting beam or a rudder beam. The exposure to seawater will not corrode the lifting beam.
Additionally, the Dura-Lite™ Lifting Beam is chemical-resistant. If Caldwell understands what chemicals the beams will be exposed to, they can prove whether it would be a better solution than a steel version.
Caldwell has found these beams work really well in the utility industry. They are non-conductive, and specific electrical ratings are listed in the product manual. If a utility truck is in the field, and they’re working on high power lines, it’s a huge advantage to use a lifting beam that’s not conductive.
Is the Dura-Lite™ Composite Beam As Strong As Steel?
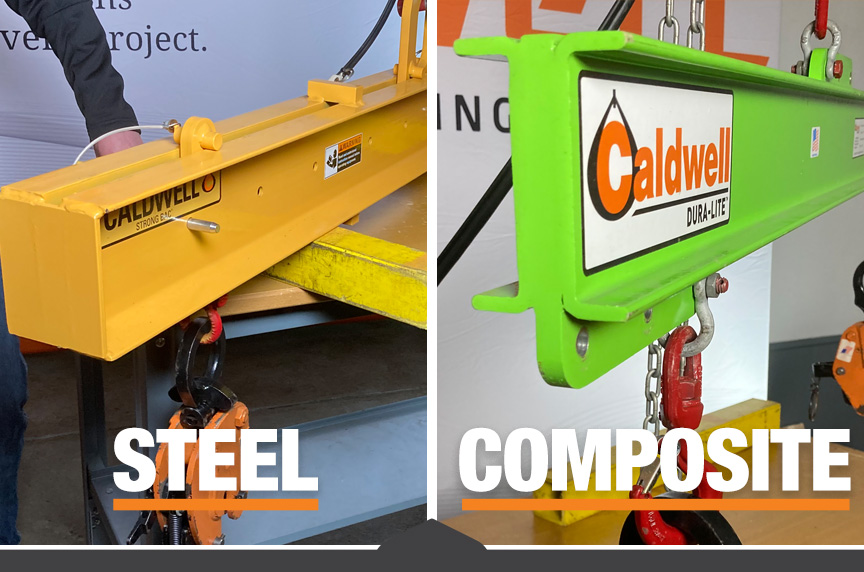
“Is it as strong as steel?” is hard to define.
According to Mongan, the testing performed exceeds testing they would do in steel versions. When developing composite lifting equipment, Caldwell employees weren’t sure how it would work. However, after going through the development process for two years, and then, environmental testing, Caldwell learned how “amazingly strong” the composite beams actually were.
As part of the testing, Caldwell took samples to a laboratory and froze them to -30°F. Then, they took other samples to 150°F. Doing so proved the adhesive used in the composite beams actually becomes stronger the colder it gets.
Then, Caldwell ordered the composite beams to go through 120 destructive tests before they launched the product line. Caldwell did so because it understood there would be some concern about going composite. However, these beams were developed to meet BTH Category 3 design requirements, which is over and above the typical steel versions. To prove that, Caldwell hired an outside contractor to do fatigue testing. Caldwell’s samples were put in a tester with the goal to go over 2 million cycles. Every sample exceeded that number. In fact, in two tests, the rigging failed and the beam did not.
What Are the Disadvantages of Using a Composite Lifting Beam?
There was one interesting test that Caldwell performed before taking the Dura-Lite™ Lifting Beam to market.
Engineers literally drove over a steel beam with a forklift, and then, a composite beam with the same forklift. In that instance, the steel beam stood stronger under that pressure than the composite beam. In extremely abusive environments, you would want to use a steel beam.
Additionally, there are heat restrictions with composite beams, as there are with steel beams. However, Caldwell could engineer a steel lifting solution to handle thousands of degrees, where composite has a temperature limit of 150°F.
Are There Real-World Examples of Companies Using Composite Lifting Beams?
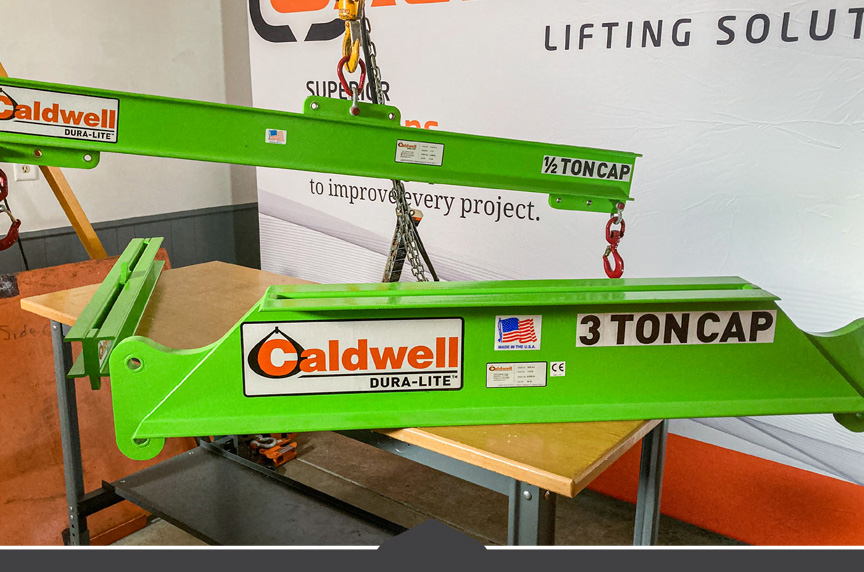
One of the more fun projects Caldwell has been involved in was the installation of a lifting system in a theme park in Florida in their aquarium to lift mammals.
Caldwell went to the aquarium and saw some of the dolphins that would be lifted. Engineers helped the park determine the right solution and how to safely lift the animals.
Because the lifts are uncommon, the theme park wanted the ability to disassemble this system. Caldwell built a three-beam system, which can be disassembled and stored away. The composite beam system was:
- Lightweight
- Easy to work with
- Corrosion-resistant to the saltwater environment
Are Composite Beams the Future of Lifting?
Based on previous industry trends, Caldwell believes the composite beams could become more prevalent in lifting and rigging. And they did not need to look back too far to find an example where an alternative lifting solution has become more commonplace.
Several years ago, wire rope and chain slings dominated the market. However, manufacturers started producing synthetic (nylon and polyester) slings. At first, there was a lot of skepticism in the industry, but today, they’re commonly used to make safe lifts.
As the Dura-Lite™ Lifting Beam progresses, Caldwell is optimistic that it will be further adopted and more common in the lifting and rigging industry.
How Can Mazzella Help You with Your Lifting and Rigging Needs?
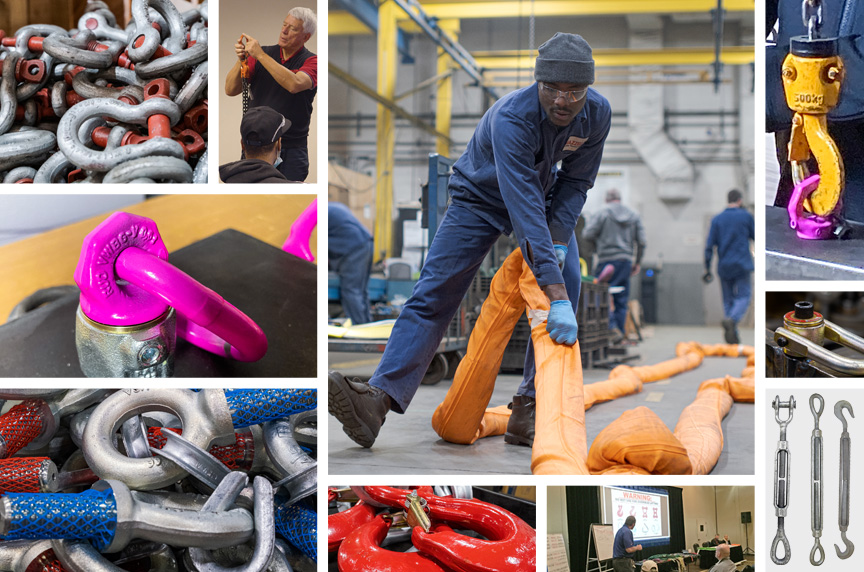
At Mazzella, we have you covered when it comes to all of your lifting and rigging needs. With our ready stock inventory, we offer all industries a variety of lifting and rigging devices.
Hardware
We offer one of the largest and most complete inventories of rigging and lifting products in the country from some of the largest manufacturers in the world. Some of the products we stock are:
- RUD lifting points
- Shackles—all types, sizes, and finishes from 1/4 ton to over 1,000 tons
- Hoist rings—standard and metric
- Eyebolts—forged, metric, and stainless steel
- Hooks—swivel, eye, choker, self-locking, and weld-on
- Master rings / links—all sizes, types and finishes
- Turnbuckles and swivels
Rigging Training
If you require a specific training course for OSHA compliance for slings, hoists and / or rigging hardware, Mazzella can assist you in creating a safe and reliable workplace.
Our rigging training focuses on:
- Overhead cranes
- Below-the-hook lifters
- Lifting slings
- Rigging hardware
- Wire rope
All Mazzella trainers have been accredited by our company through training with a third-party trainer (Industrial Training International, Inc.), Mazzella Companies’ internal Train-the-Trainer program, and are trained on OSHA and ASME standards.
Also, we provide site assessments. The purpose of an assessment is to systematically observe and record your lifting and rigging procedures, equipment, and records. This is not an inspection, but rather, a general assessment by which opportunities for improvement may be identified.
Rigging Inspection Services
OSHA 1910.184, ASME B30.9 Slings, ASME B30.20 Below-the-Hook Lifting Devices, ASME B30.26 Rigging Hardware & ANSI Z359 require…
Periodic, documented inspections on slings, rigging hardware, lifting devices, and fall protection every 12 months, at minimum, and monthly to quarterly in more severe service conditions.
Our rigging inspectors are certified to make sure your products meet OSHA and ASME requirements. Also, we provide personal fall protection inspections and basic level non-destructive testing (NDT) inspections to support our visual inspections.
Call us at 800.362.4601, or click here if you need inspections for rigging hardware, training, or any of our other services.
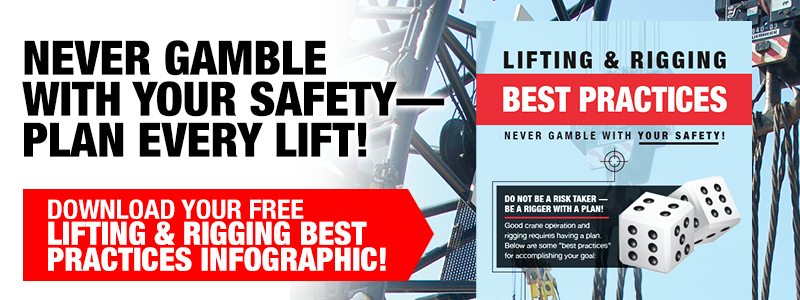
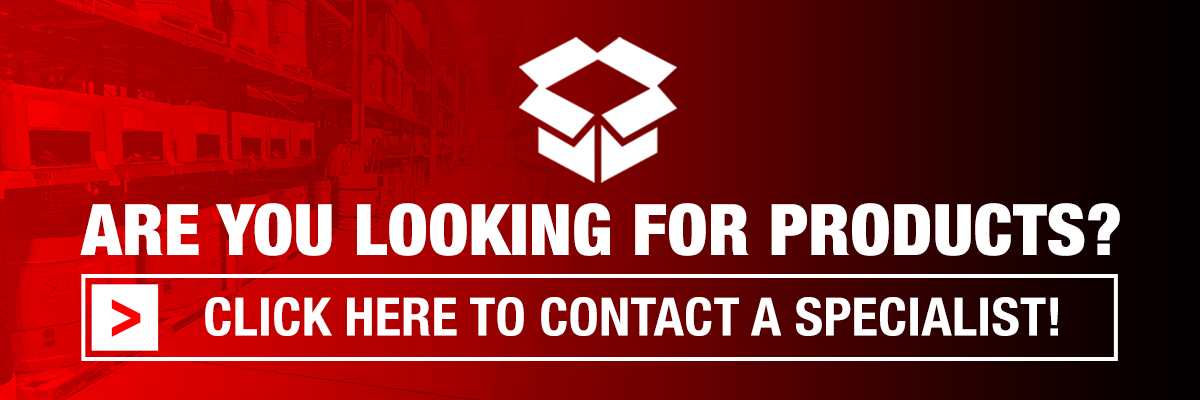
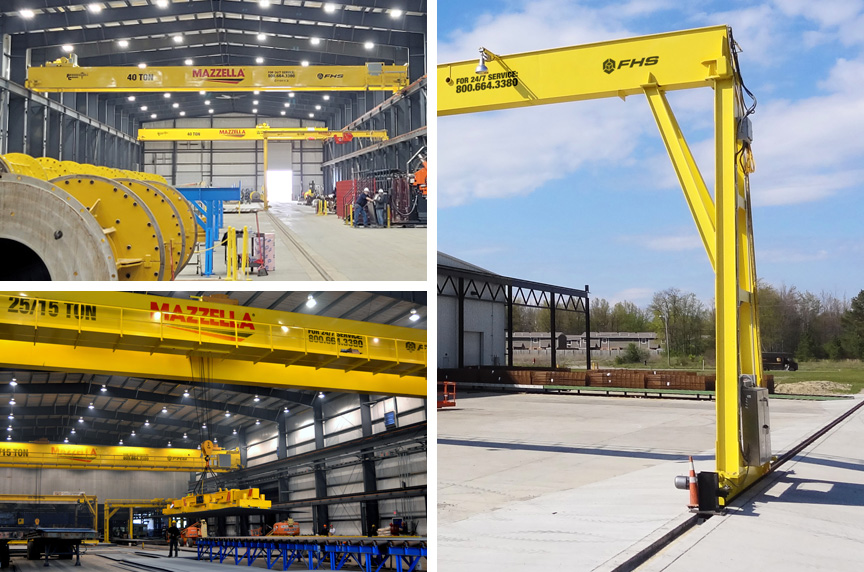
Overhead Cranes & Material Handling
Mazzella is a leading manufacturer of world-class overhead cranes with over 65 years of experience. We engineer and build custom solutions ranging from light-duty, economical cranes up to large capacity, high-duty cycle cranes with welded plate-box girders.
Copyright 2023. Mazzella Companies.