How Are Turnbuckles Inspected and Repaired, per ASME Standards?
How are turnbuckles inspected, and how can they be repaired? There are very specific qualifications set forth by the American Society of Mechanical Engineers (ASME) that must be adhered to so your turnbuckles are in proper working order.
A turnbuckle is an adjustable device consisting of three primary components: a body, a right-hand threaded end fitting and a left-hand threaded end fitting.
Turnbuckles have three types of end fittings (hook, eye, or jaw) and can come in combinations with different fittings on the ends of the same piece of hardware.
To always ensure the turnbuckle you select meets or exceeds the working load limit (WLL) for the task at hand and is comparable to the working load limit of the slings and other rigging hardware being used, you must know the WLL.
Is the working load limit required to be durably marked on an turnbuckle for it to be compliant with the ASME B30.26 Rigging Hardware standard?
In this piece, we will examine the following:
- What needs to be marked on an turnbuckle
- Rigging best practices
- Inspections of turnbuckles
- Removal from service criteria for turnbuckles
What Needs to be Marked on a Turnbuckle?
According to ASME B30.26 Rigging Hardware, turnbuckles, like eyebolts and eye nuts, are required to be “durably marked by the manufacturer to show” the following:
- Name or trademark of manufacturer
- Size or rated load
- Grade for alloy eyebolts
Under the subsection ASME B30.26-2.5.3 Maintenance of Identification, “turnbuckle, eyebolt, eye nut, and swivel hoist ring identification should be maintained by the user so as to be legible throughout the life of the hardware.”
According to the standard, “Rated load” is defined as: “the maximum allowable working load established by the rigging hardware manufacturer. The terms ‘rated capacity’ and ‘working load limit’ are commonly used to describe rated load.” Also, a “rated load shall be in accordance with the recommendation of the hardware manufacturer.”
Factors to Consider When Using Turnbuckles
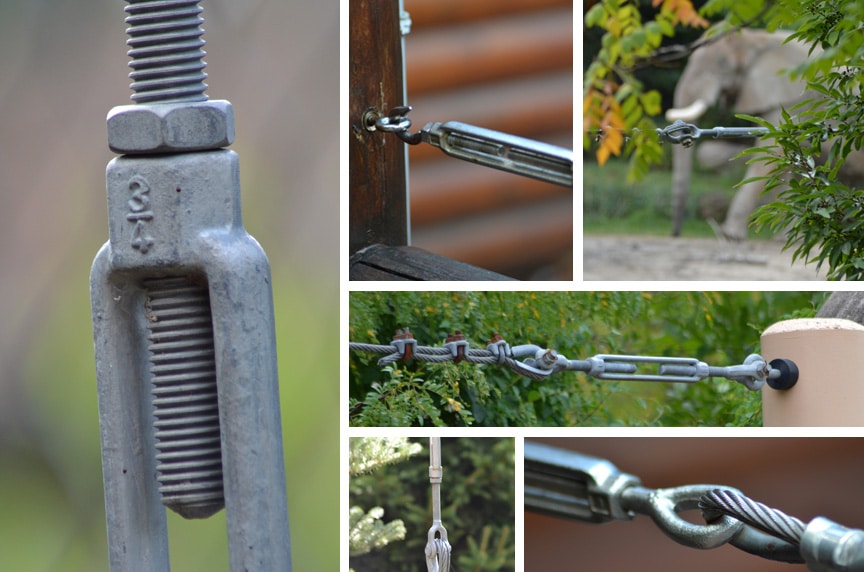
In order to prevent undue damage to the markings or the turnbuckles themselves, there are many steps to consider before using rigging hardware for overhead lifts.
As an end-user, you want to pay attention to the effects of the environment in which your rigging gear is used, including the following:
- Temperature
- Chemically Active Environments
- Training
- Storage and Work Environments
Temperature
When adjustable hardware, excluding swivel hoist rings and carbon steel eyebolts, is to be used at temperatures above 400°F (204°C) or below -40°F (-40°C), the hardware manufacturer or a qualified person should be consulted.
When carbon steel eyebolts are to be used at temperatures above 275°F (135°C) or below 30°F (-1°C), the hardware manufacturer or a qualified person should be consulted.
Chemically Active Environments
The strength of adjustable hardware can be affected by chemically active environments such as caustic or acidic substances or fumes. The adjustable hardware manufacturer or a qualified person should be consulted before use in chemically active environments.
Training
Adjustable hardware users shall be trained in the selection, inspection, cautions to personnel, effects of environment, and rigging practices as covered by Chapter B30.26-2.
Storage and Work Environments
Adjustable hardware should be stored in an area where it will not be subjected to damage, corrosive action, or extreme heat.
If extreme temperatures or chemically active environments are involved, the guidance provided in the above sections discussing temperature and chemically active environments shall be followed.
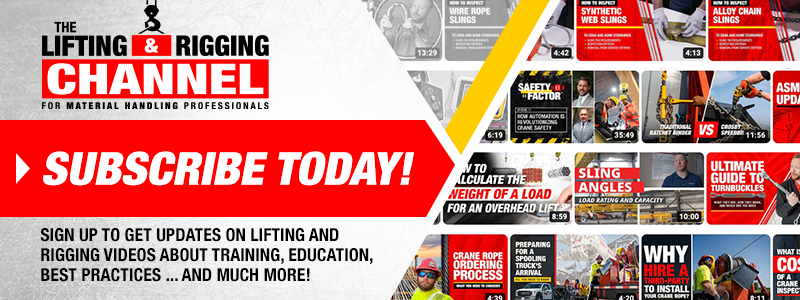
Best Practices for Using Turnbuckles
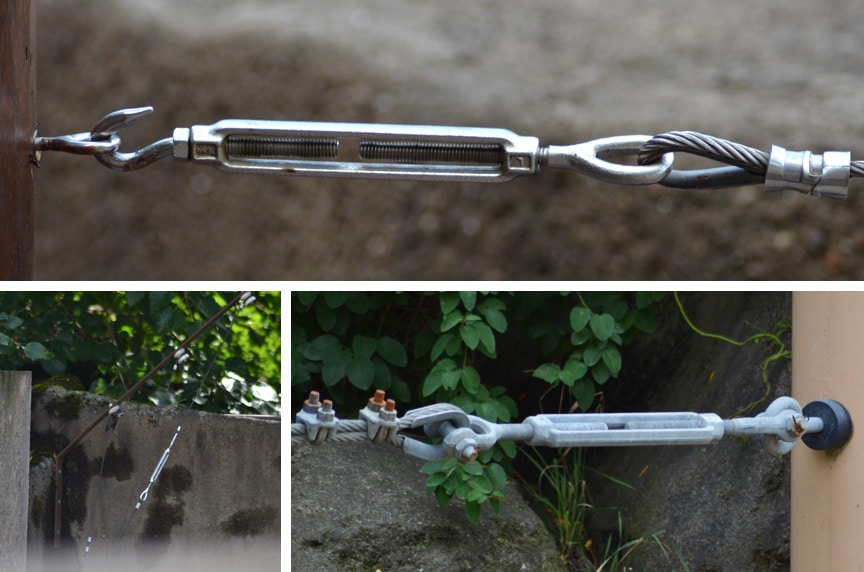
In Chapter 2.9.4.1, the ASME B30 Committee outlines the following 11 points of emphasis for rigging best practices with turnbuckles:
- Turnbuckle end-fitting threads shall be fully engaged in the body threads.
- NOTE: Pipe bodies conceal the length of thread engagement. Verify full engagement before loading.
- Components, including pins, bolts, nuts, or cotter pins used with jaw ends, shall be in good working condition prior to use.
- If locking nuts are used, they shall be compatible with the threads of the turnbuckle end.
- Contact with obstructions that could damage or bend the turnbuckle should be avoided.
- Shock loading should be avoided.
- The load applied to the turnbuckle should be in line and in tension.
- Turnbuckles should not be side loaded.
- Turnbuckles should be rigged or secured to prevent unscrewing during lifting or load-handling activities.
- For long-term installations, turnbuckles shall be secured to prevent unscrewing.
- Turnbuckles should not be dragged on an abrasive surface.
- Turnbuckles should be adjusted with a properly sized wrench, used on the wrench flats of the turnbuckle body
Inspections of Turnbuckles
Like other types of rigging hardware, turnbuckles are required to have three types of inspections, where identification markings will be closely examined for legibility. Examining the identification markings is one of the many steps that must be taken during the following types of inspections:
- Initial inspections
- Frequent inspections
- Periodic inspections
26-2.8.1 General
All inspections shall be performed by a designated person. Any deficiencies identified shall be examined and a determination made by a qualified person as to whether they constitute a hazard.
26-2.8.2 Initial Inspection
Prior to use, all new, altered, modified, or repaired adjustable hardware shall be inspected to verify compliance with the applicable provisions of this Chapter. Written records are not required.
26-2.8.3 Frequent Inspection
A visual inspection shall be performed each shift before the adjustable hardware is used. Rigging hardware in semi-permanent and inaccessible locations where frequent inspections are not feasible shall have periodic inspections performed.
Conditions such as those listed in para. 26-2.8.5 or any other condition that may result in a hazard shall cause the adjustable hardware to be removed from service. Adjustable hardware shall not be returned to service until approved by a qualified person.
Written records are not required.
***Paragraph 26-2.8.5 outlines the removal from service criteria for turnbuckles listed below!
26-2.8.4 Periodic Inspection
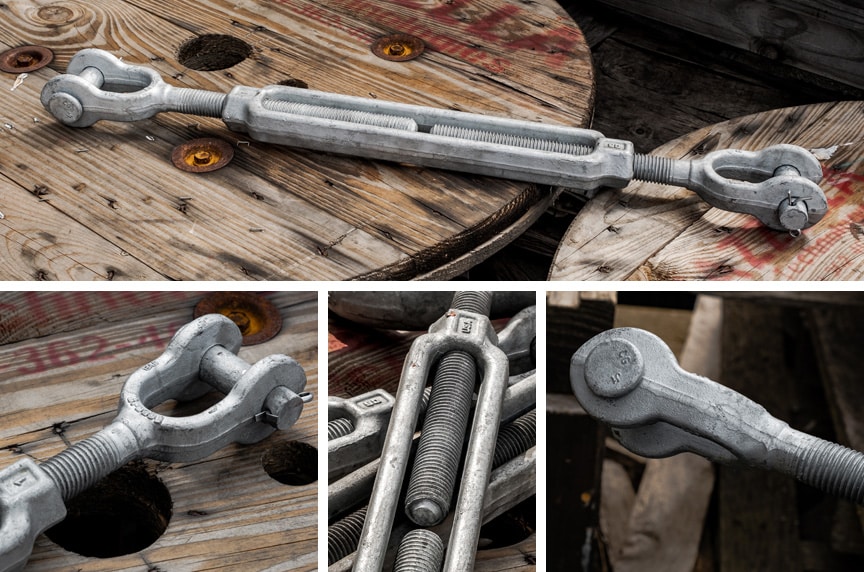
A complete inspection of the adjustable hardware shall be performed. The adjustable hardware shall be examined for conditions such as those listed in para. 26-2.8.5 and a determination made as to whether they constitute a hazard.
Periodic Inspection Frequency
- Periodic inspection intervals shall not exceed one year. The frequency of periodic inspections should be based on:
- Frequency of use
- Severity of service conditions
- Nature of lifting or load-handling activities
- Experience gained on the service life of adjustable hardware used in similar circumstances
- Guidelines for the time intervals are
- Normal service — yearly
- Severe service — monthly to quarterly
- Special service—as recommended by a qualified person
Written records are not required.
Removal From Service Criteria for Turnbuckles
Adjustable hardware shall be removed from service if conditions such as the following are present and shall only be returned to service when approved by a qualified person:
- Missing or illegible identification
- Indications of heat damage, including weld splatter or arc strikes
- Excessive pitting or corrosion
- Bent, twisted, distorted, stretched, elongated, cracked, or broken load-bearing components
- Excessive nicks or gouges
- A 10% reduction of the original or catalog dimension at any point
- Excessive thread damage or wear
- Evidence of unauthorized welding or modification
- Other conditions, including visible damage, that cause doubt as to continued use
How Can Mazzella Help with Your Turnbuckles?
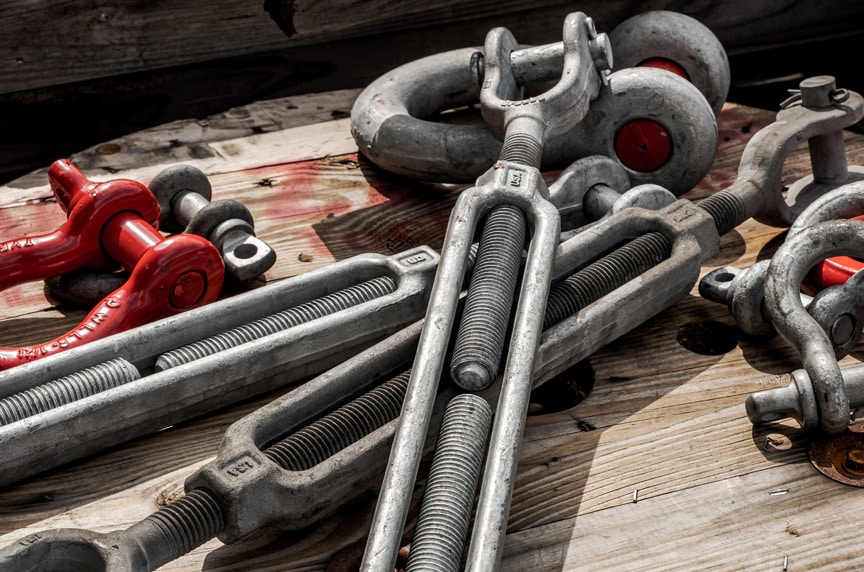
As a one-stop shop for your lifting and rigging needs, Mazzella has a diverse range of products and services that can help you execute safe overhead lifts.
Hardware
We offer one of the largest and most complete inventories of rigging and lifting products in the country from some of the largest manufacturers in the world. Some of the products we stock are:
- Shackles—all types, sizes, and finishes from ¼ ton to over 1,000 tons
- Hoist rings—standard and metric
- Eyebolts—forged, metric, and stainless steel
- Hooks—swivel, eye, choker, self-locking, and weld-on
- Master rings / links—all sizes, types and finishes
- Turnbuckles and swivels
Also, we stock many other rigging hardware items.
If you can’t find a standard item to meet your specific needs, inquire about custom rigging and lifting hardware. All hardware products meet the ASME B30.26 Rigging Hardware specification.
Rigging Training
If you require a specific training course for OSHA (Occupational Safety and Health Administration) compliance for slings, hoists and / or rigging hardware, Mazzella can assist you in creating a safe and reliable workplace.
Our rigging training focuses on:
- Overhead cranes
- Below-the-Hook lifters
- Lifting slings
- Rigging hardware
- Wire rope
Also, we provide site assessments. The purpose of an assessment is to systematically observe and record your lifting and rigging procedures, equipment, and records. This is not an inspection, rather a general assessment by which opportunities for improvement may be identified.
All Mazzella trainers have been accredited by our company through training by a third-party company (Industrial Training International, Inc.), Mazzella Companies’ internal Train-the-Trainer program, and are educated on OSHA and ASME standards.
Rigging Inspection Services
OSHA 1910.184, ASME B30.9, B30.20, B30.26 & ANSI Z359 require…
Periodic, documented inspections on slings, rigging hardware, lifting devices, and fall protection every 12 months, at minimum, and monthly to quarterly in more severe service conditions.
Our rigging inspectors are certified to make sure your products meet OSHA and ASME requirements. Also, we provide personal fall protection inspections and basic level non-destructive testing (NDT) inspections to support our visual inspections.
Call us at 800.362.4601 or click here if you need rigging hardware, training, or inspections!
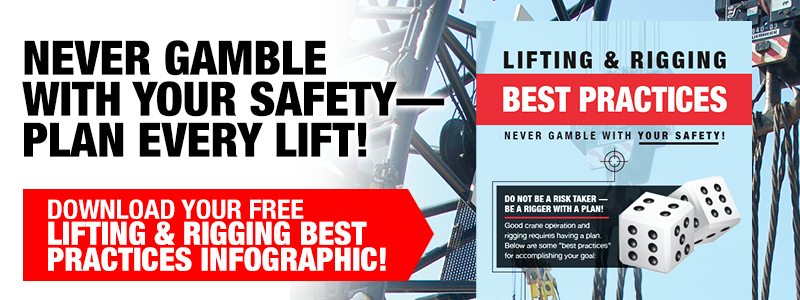
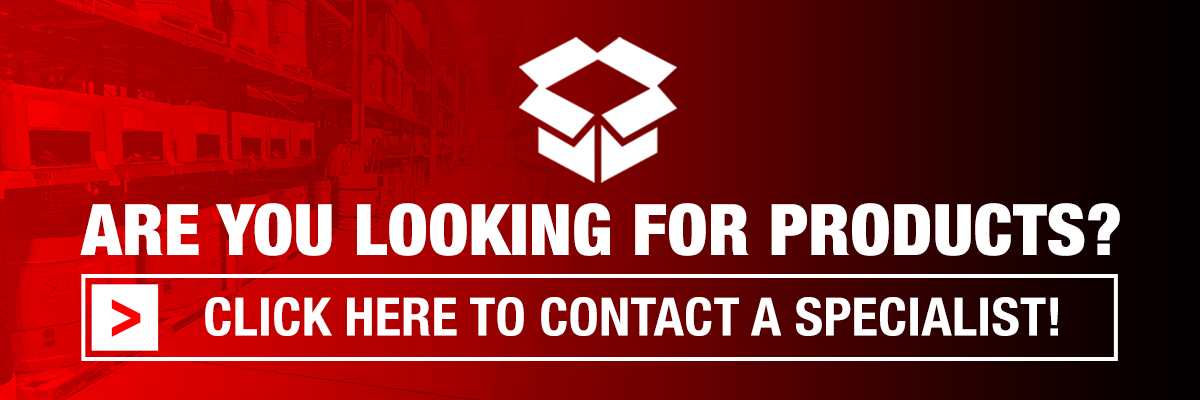
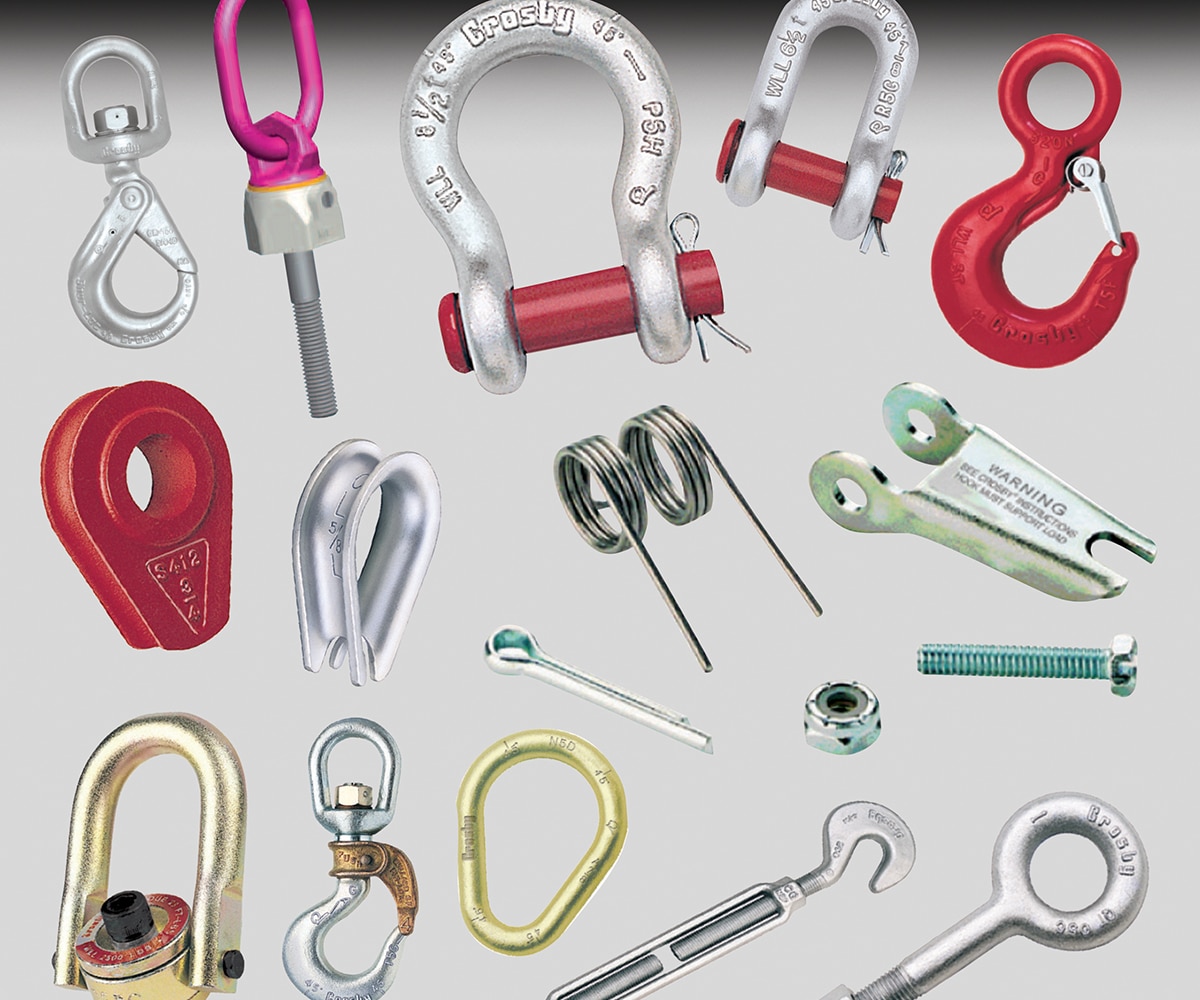
Rigging Hardware
We offer one of the largest and most complete inventories of rigging and lifting products in the country from some of the largest manufactures in the world.
If you can’t find a standard item to meet your specific needs, inquire about custom rigging and lifting hardware. All hardware products meet the ASME B30.26 specification.
Copyright 2022. Mazzella Companies.