Import vs. Domestic Rigging Products: How to Choose the Best
Ultimately, the decision to choose a domestic or an imported wire rope, shackle, hook, sling or any other type of rigging product will come down to what best suits your company’s needs. There are obviously advantages and disadvantages to choosing a domestically-made or imported hook, shackle, wire rope, chain sling, or synthetic roundslings.
One topic that’s sure to spark a lively discussion among those who work in the lifting or material handling industries is, “Are import rigging products just as good as domestic products?” There’s a certain stigma attached to rigging products like hooks, wire rope, chain slings, and synthetic roundslings that are brought in to the U.S. from overseas.
So, are import rigging products just as good as domestic? It’s a complex question and the answer is yes…and no.
A Change in Mindset
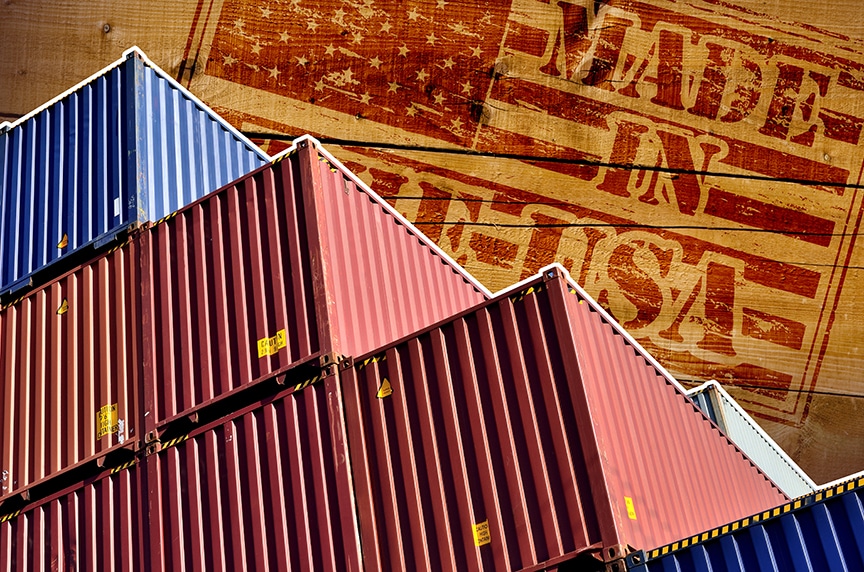
25 or 30 years ago, if you asked an industry veteran if they trusted import products on the job site, the answer was clearly, “No.” Import products were viewed as inferior across the board—from shackles, sling hooks, wire rope, blocks, and wire rope clips. When import rigging products started hitting the market, there were horror stories of failed hooks, broken cables and slings, mislabeled and unmarked shackles—resulting in injuries to workers and expensive damage to equipment and materials.
Import lifting products developed a reputation as being dangerous and of poor quality and were blacklisted at job sites all across the country. Employees at steel mills, assembly plants, and construction sites—who cared about keeping their equipment running and keeping their co-workers safe—proudly and rightfully declared, at that point in time, “No imports. Period.”
Since then, the world has changed. Our economy is now globalized and the perception of imported products has shifted as quality has improved. Across the board, industries have moved their manufacturing overseas and more products and goods are being brought in to the U.S. Major automotive companies are using imported parts in their assembly plants, some steel mills are owned by companies outside of the U.S., and construction companies have been increasingly open to using imported products on the job site.
Advantages and Disadvantages
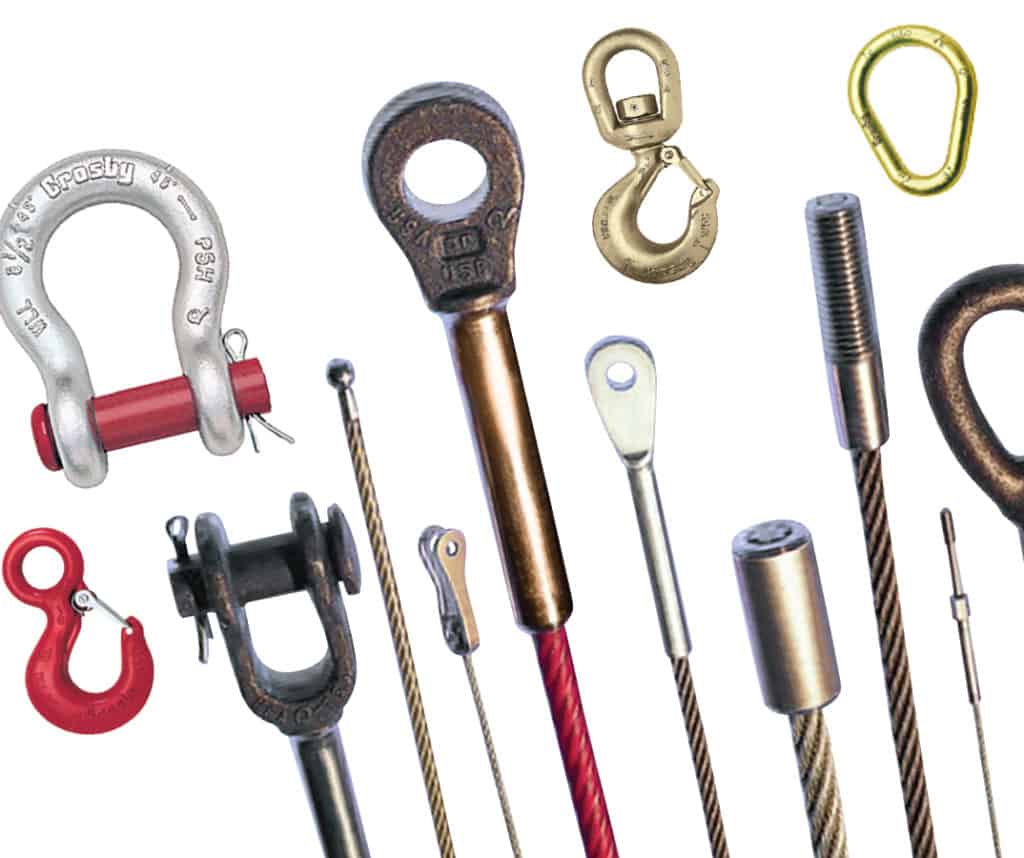
For many of us out there, there’s a sense of pride and sentiment in buying American-made goods. Many people have a deep-rooted connection to American manufacturing—maybe they feel loyal because a friend or relative put in a whole lifetime’s worth of work with a company who made their products in America. Or, maybe they’ve witnessed firsthand the impact that a large corporation had on their hometown when it moved its manufacturing processes overseas.
On the other hand, there are a lot of people out there who are forced to focus only on performance and the cost of rigging products because they’re under immense pressure to make their company profitable by reducing costs and expenses.
Ultimately, the decision to choose a domestic or an imported wire rope, shackle, hook, sling or any other type of rigging product will come down to what best suits your company’s needs. There are obviously advantages and disadvantages to choosing either.
For companies that import their rigging products, their business is built on offering their customers standard run-of-the-mill rigging products in the most popular sizes and configurations. Their manufacturing locations are built to churn out product in large batches and operate with little to no overhead. By doing so, an import supplier can offer their products at a discounted price. Unfortunately, they can’t offer their customers much in terms of variety or customized solutions.
Products like engineered below-the-hook devices, custom-sized hardware, and specialty products like aramid fiber roundslings are much better suited for domestic manufacturers. Companies who make their rigging products in the U.S. tend to have more of an infrastructure in place that is flexible, can make smaller-batch product runs, and can provide customized solutions for their customers. They may not be the cheapest option, but they can offer other value-added services like engineering, R&D, and custom innovations.
What to Look for When Considering an Import Supplier
A lot has changed over the past 30 or so years to improve the quality of imported rigging products, but there are still some products and parts of questionable quality coming into the U.S. When deciding on whether you want to use domestic or import rigging products for your company’s lifting program, consider the following:
- Make sure that imported rigging products, especially hardware items, have markings in accordance with federal standards and ask for a certificate of conformance from the supplier.
- Make sure the distributor has visited the facilities that produce their import rigging products and has properly vetted them.
- Make sure the wholesaler/distributor has adequate Product Liability Insurance. Even if the specific overseas manufacturer has liability insurance and an incident were to occur, it is nearly impossible to collect on any claim.
- Make certain that your distributor has products made to their specifications, not the manufacturer’s. This promotes consistent quality and lessens the liability.
- Make certain that your wholesaler / distributor does not buy through a Broker. Buying through a Broker can oftentimes lead to mixed product of varying quality from multiple manufacturing facilities.
- If your application must meet specific Conflict Mineral Compliance, such as RoHS or REACH, Asian manufacturers cannot supply you a solution at this point in time.
- Make sure the import product supplier has a product traceability program in place.
- Make sure the distributor conducts their own inspection and testing in-house.
Federal Standards
One thing to consider prior to purchasing an imported rigging product is to make sure that it meets federal specifications. For instance, if you’re considering using an imported wire rope, request a “certificate of conformance” from the distributor—this will at least give you documentation that the rope meets the RR-W-410 federal specifications required for domestic-made wire rope. It can also make certain that import rigging hardware items have the proper markings in accordance with federal standards.
While this is a good first step, the federal standard does not guarantee a high-quality product. Instead, it will at least guarantee that the part meets the same federally-required specifications as domestically-made products.
Identifying the Source and Vetting Supplies
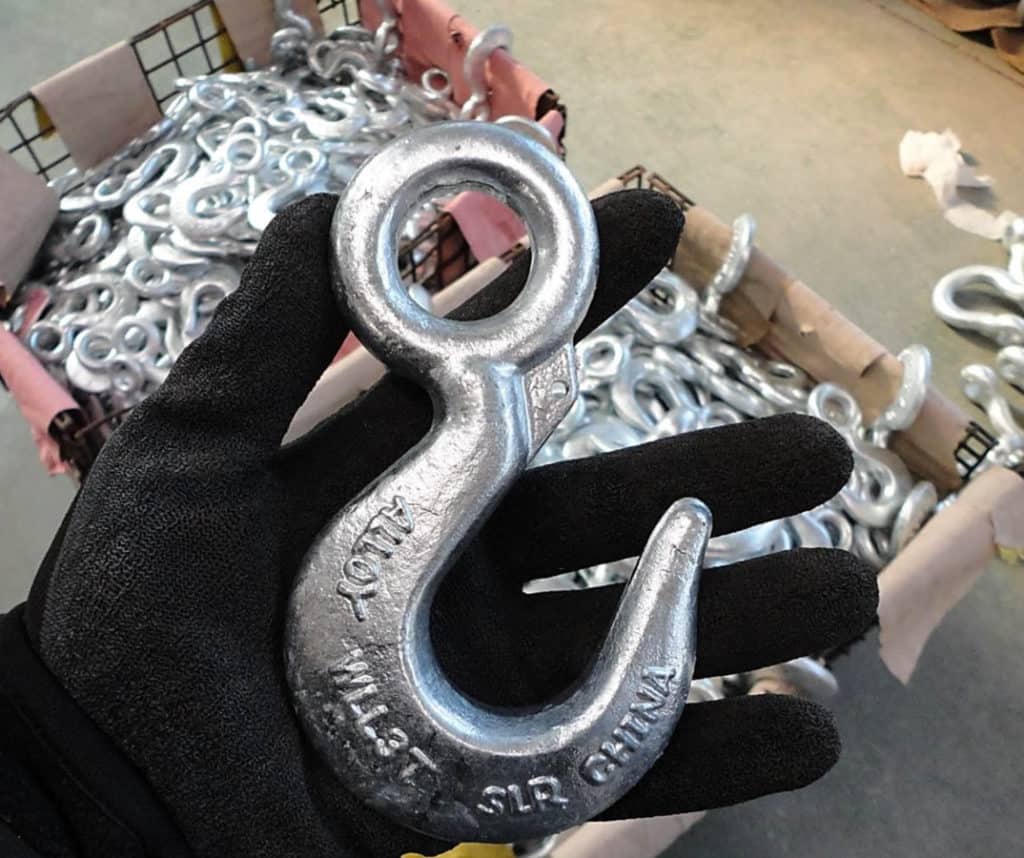
You should consider the source of the imported rigging products that you’re looking to purchase. Many in the lifting industry who have aversions to using “import products” have different ideas of what imports are. Most consider import products as those coming from emerging industrial markets such as China, Korea, India and Malaysia. However, some of the same customers who do not want “import products” are perfectly fine with products from Canada, Germany, France, and Sweden—and may even pay a premium to buy them!
But, even in emerging industrial countries there can be a huge quality gap between manufacturers of rigging products. For instance, some facilities in China may have modern automated factories that have excellent quality control programs and equipment that rivals any factory in the U.S. Others may be using antiquated technologies and the same processes that turned out inferior quality products thirty years ago.
Most importantly, before you buy an import rigging product, ask the distributor if they or someone from their company has been to the facility making their equipment. If they say no, simply don’t buy it. Unfortunately, some countries outside of the U.S. don’t require manufacturers to adhere to quality standards, workplace regulations, or basic employee rights and this can lead to deplorable working conditions in their factories. If a distributor has visited the facility that is producing their rigging products, it should tell you that they are vetting their import suppliers and care about the people that are using their products, as well as the people making them.
Product Tradeability
Responsible and forward-thinking manufacturers should maintain records of how and when their products were made and where the raw material(s) originated from. Some raw materials, such as high alloy steels are not available in other countries and can greatly affect the performance of the resulting manufactured products.
Maintaining traceability records will ensure that they are able to trace each part back to an individual manufacturer and batch number. This will allow them to be proactive in identifying a quality issue and take appropriate action before it becomes a disruption or liability.
Testing Protocols
Before you buy an imported rigging product, ask the question, “Have you tested the product?” Importers that vet foreign manufacturers should not rely solely on their supplier, and should always conduct their own set of in-house tests and inspection. Something as simple as providing documentation that a batch break test was performed stateside will tell you that the importer prioritizes safety and providing their customers with quality products. If they don’t test, don’t buy.
Wrapping it Up
There are plenty of import rigging products on the market that are quality pieces, safe to use, and meet the same federal specifications as domestic rigging products. If you’ve taken the steps to vet your supplier, and your supplier is vetting their manufacturer, then you’ve covered your bases.
At Mazzella, we sell the highest-quality import and domestic rigging products because product quality and operating safety go hand-in-hand. We have one of the largest and most complete inventories of both domestic and imported rigging and lifting products to suit your lifting needs.
We work hand-in-hand with our domestic and international suppliers to make sure their parts meet federal specifications, we’re allowed access to their facilities, they have traceability programs in place, and that each shipment of parts is inspected and batch-tested once we receive them.
If you have any other questions about our vetting or testing processes for our rigging products, or need a recommendation on lifting solutions or rigging products for your facility, give us a call and we’ll put you in touch with one of our Lifting Specialists at a location near you.
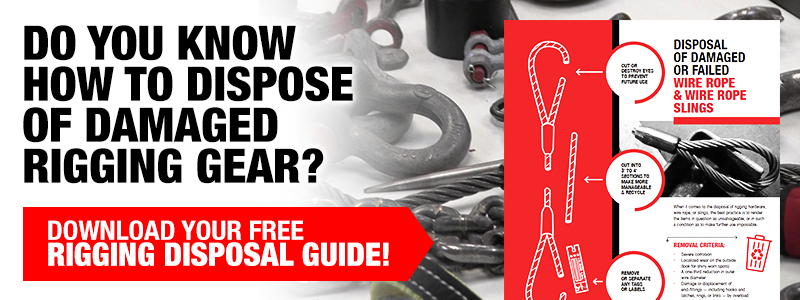
Copyright 2017. Mazzella Companies.