What Is a Sling Angle, and How Can Knowing Them Make Our Lifts Better?
Are you having problems maximizing the lifespan of your slings? One of the root causes could be improper use leading to added stress. Knowing and understanding sling angles could help you extend the lifecycle of your slings by putting the proper tension on them during a lift.
If you’re not getting the most out of your rigging gear, using poor sling angles could be your problem.
Remember when you were daydreaming in high school geometry class believing you would never use those lessons in a real-world setting?
Well, if you’re entering the lifting and rigging industry, you’ll learn quickly how important those skills are. Knowing sling angles before making a lift is critical. Understanding how sling angles can affect the working load limit plays a key role in you doing your job efficiently and making lifts safer on the jobsites.
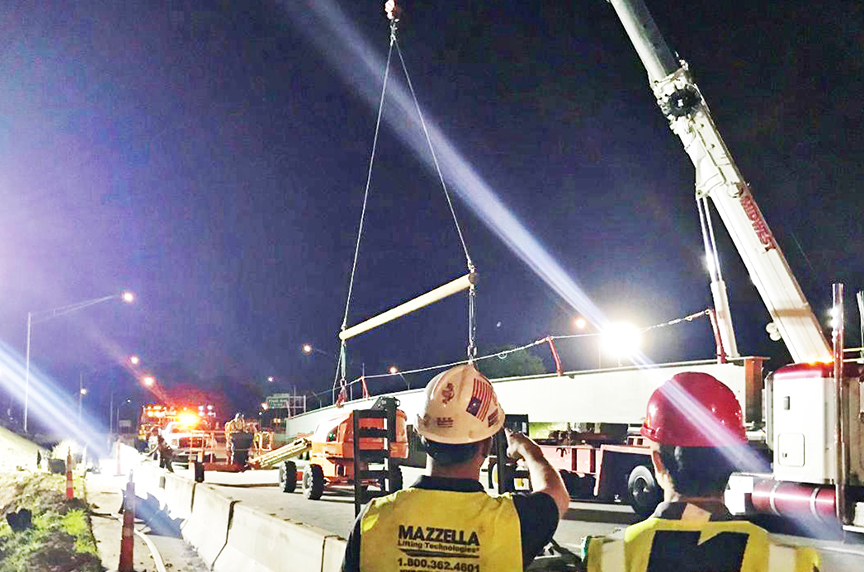
In our 65-plus years of experience, Mazzella’s Lifting Specialists have seen what happens when a sling fails to make a lift because of incorrect angles. They know the destruction that could follow a lift failure, including damage to the load being lifted and serious injuries for those on the jobsite.
According to OSHA (Occupational Safety and Health Administration) Publication 2056, there are nearly 6,000 workplace fatalities in the United States and 50,000 deaths due to workplace-related illnesses each year. Also, there are 5.7 million non-fatal workplace injuries, and those injuries alone cost U.S. businesses over $125 billion annually.
In this article, you’ll learn the answers to the following questions:
- What is a sling angle?
- How do you accurately measure a sling angle?
- Who is responsible for measuring sling angles?
- What should you do with a lift angle lower than 30°?
- Does a basket hitch affect the working load limit of a sling angle?
- How do I use the Mazzella Sling Working Load Limits Chart?
What Is a Sling Angle?
The sling angle, or horizontal angle, is the angle where the sling meets the load. You need to measure that to find out how you properly choose the piece of rigging you need for the applied force that’s going to be on them.
You want to check and make sure that sling angle is correct for the lift. In the lifting and rigging industry, you want to make sure the angle is at least 30° or more.
Lifting and rigging specialists tend to prefer 60° angles. When a multi-leg sling is tagged, it is tagged for 60°. Slings also can be used at 45° or 30°, but for most of the lifts, 60° is the baseline sling angle that riggers want to use.
That applies to all of the following fields:
- Industrial
- Manufacturing
- General construction
If you measure in-between your pick points, and you’ve got the same distance going back to the crane hook or common point, you have a 60° angle. If that’s the case, you can follow the limits listed on the tag and conduct your lift.
Most of the time, in dealing with construction, and even large manufacturing and industrial applications, headroom is not an issue. Just focus on getting the proper sling length you need, and you’ll be able to make your lift safely.
There are situations where that’s not possible, and you have to do some measuring and calculating. In that case, there are resources to help you find that angle quickly and easily.
How Do You Accurately Measure Sling Angles on a Jobsite?
The sling angle is going to affect the tension and stress put on each sling leg.
Example: If you have a 2,000 lb. load, and you’re picking it up with a two-legged sling, you have to divide the weight of the load across those two sling legs. When you’re lifting at a 60° angle, you have to use a multiplier to get that tension.
With the load distributed evenly, each sling leg would handle 1,000 lbs., but the angle affects that capacity.
The multiplier for a 60° angle is 1.155. That means the tension on each sling leg is 1,155 lbs.
For a 45° angle, you multiply the 1,000 lbs. on each sling leg by 1.414. That puts the tension at 1,414 lbs. on each of the sling legs.
With a 30° angle, you have to multiply the 1,000 lbs. by two, meaning each sling leg is under 2,000 lbs. of tension during the lift.
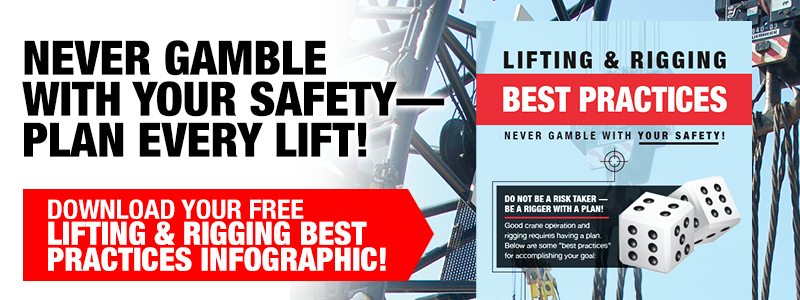
Who Is Responsible for Measuring Sling Angles?
There are instances where a designated person is overseeing a certain lift or pick.
In that case, the designated person needs to be the one to approve the lift and say it’s safe to make. That process starts with a “Critical Lift Plan,” and a meeting with the riggers and crane operator before anything is lifted.
Most times, in the construction industry or out on a shop floor, when a company deems someone competent and qualified, it’s that person’s responsibility to make sure the proper angles are achieved and the load is rigged safely for the lift.
Competent and qualified persons have to:
- Understand sling angles
- Know the sling angle of the load they’re lifting
- Be able to make the lift properly
Designated person
The OSHA 29 CFR 1910.179, Overhead and Gantry Cranes standard states:
“Only Designated Personnel shall be permitted to operate a crane in this section.”
Although OSHA doesn’t define “Designated Person,” the ASME B30.2 Overhead and Gantry Cranes standard defines a designated person as:
“A person selected or assigned by the employer or the employer’s representatives as being competent to perform specific duties.”
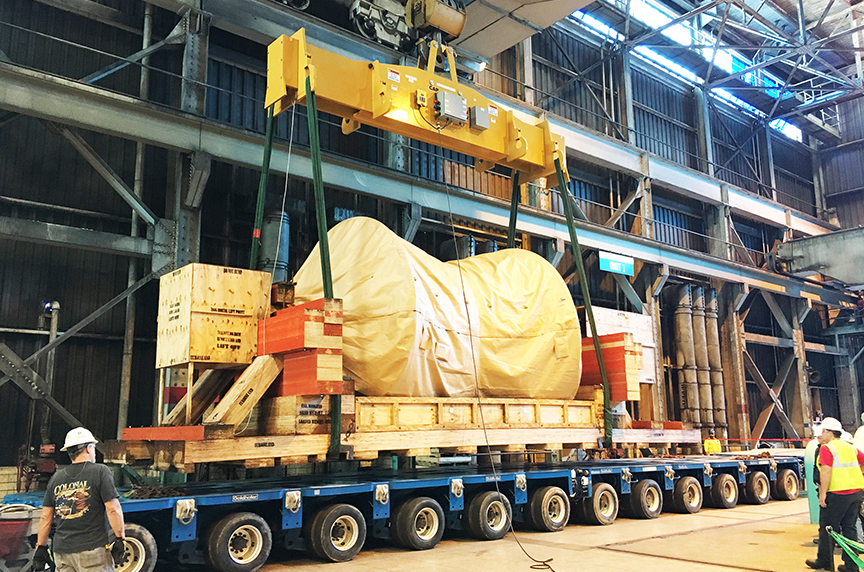
Qualified Person
OSHA defines a Qualified Person as:
“A person who, by possession of a recognized degree, certificate, or professional standing, or who by extensive knowledge or training and experience, successfully demonstrated the ability to solve/resolve problems related to the subject matter, the work, or the project.”
The employer will have to determine if an employee is qualified and have answers to questions like:
- What do we consider a “recognized degree?”
- What does our company consider a “recognized certificate?”
- How do we define “extensive knowledge and training?”
- What behavior or actions demonstrate “the ability to solve/resolve problems related to the subject matter?”
Example: If a person has a certificate of training from a basic rigging course, that might not be enough to deem them a qualified person on the jobsite.
Most would say if they had an employee that had a certificate of training, or a degree in a related field, and paired either of those with applicable field experience, then they could be considered a qualified person.
Ultimately, the major takeaway is to understand that it’s the responsibility of the employer to determine if an employee is qualified to perform the job or task at hand, based on related training, degrees, certifications, and applicable experience.
Competent Person
OSHA defines a Competent Person as:
“One who is capable of identifying existing and predictable hazards in the surroundings, or working conditions which are unsanitary, hazardous, or dangerous to employees, and who has authorization to take prompt corrective measures to eliminate them.” [OSHA 29 CFR 1926.32(f)].
Of course, there are more questions, and some ambiguity when reading this definition of a competent person, but certainly, two words stand out – “capable” and “authorized.”
One of the questions you may ask is, “what makes someone capable, and how do you authorize them to take corrective actions?” Competency is demonstrated by a person’s knowledge, skills, experience, and training – not by successfully completing training programs or evaluations.
It is the employer’s responsibility to designate a competent person on a jobsite or in a facility. In the world of lifting and rigging, a competent person performs the inspections of lifting slings and rigging hardware prior to each shift or each lift. This person has demonstrated to their employer that they have the ability to recognize hazards, and have been deemed competent to take a questionable or damaged sling or piece of rigging hardware and remove it from service.
***Ultimately, it is the crane operator’s decision to perform or not conduct the lift.
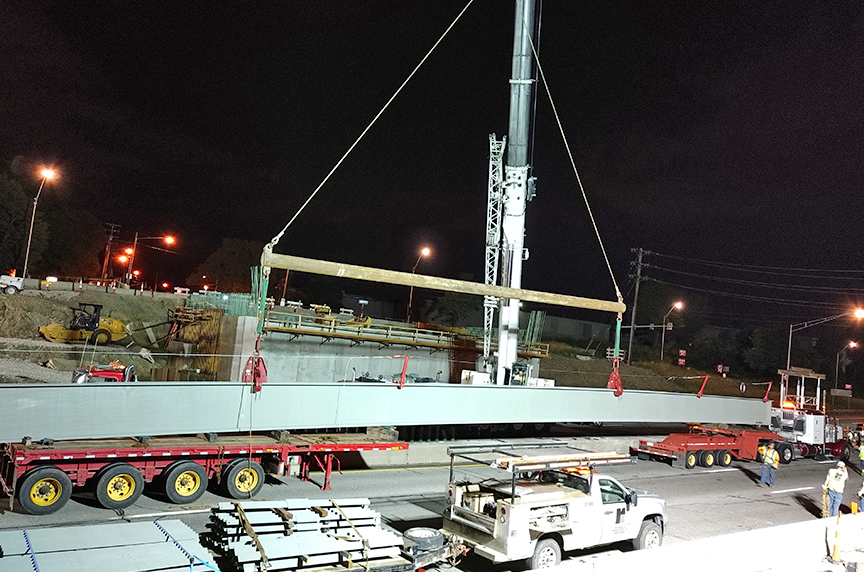
What Should You Do When Lifting with Angles Smaller than 30°?
Anytime a competent or qualified person working in the field is lifting loads, 30° will be the minimum they should allow to conduct a lift. There should be a “Critical Lift Plan” involved or even some kind of engineered backing or designated person understanding, “Okay, we’re about to make a lift under 30°. Let’s make sure, 100%, that we’ve got the proper slings in place to make this lift safely.”
The ASME B30.9 Slings standard states that anybody lifting loads below 30° needs to have a qualified person approve a “Critical Lift Plan” before it’s done.
Our lifting and rigging specialists recommend finding another option if you’re lifting a load with an angle lower than 30°.
One of those options includes using a spreader bar, which disperses the load more effectively than a small angle. A spreader bar will allow the slings to come down at the correct angle and make the lift a lot better.
How Do I Use the Mazzella Sling Working Load Limits Chart?
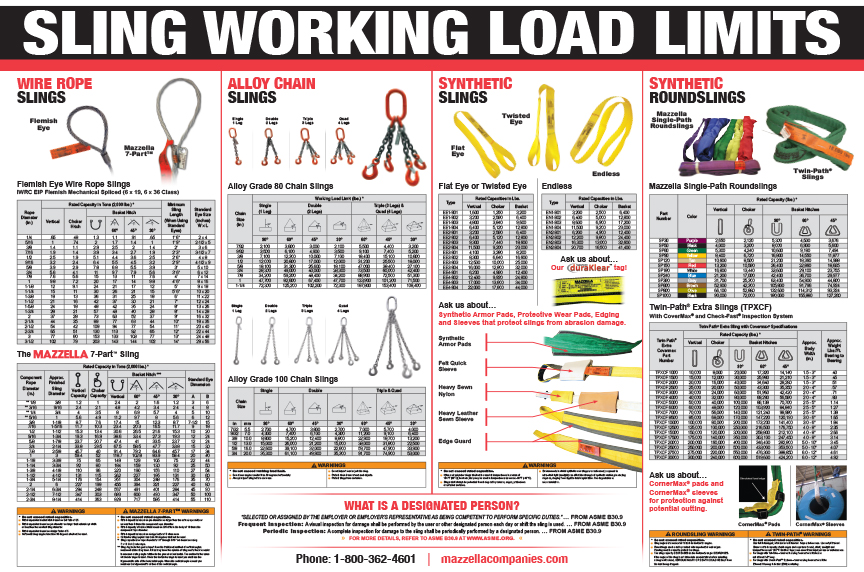
The Mazzella Sling Working Load Limits chart is separated into different types of slings with each table showing different:
- Sling diameters
- Part numbers
- Sling types
- Chain sizes
Also, the chart shows the sling angle and how much the sling can lift from that angle.
Example: Although looking at this chart is pretty straightforward, when looking at a basket hitch, you want to understand the working load limit for a true vertical basket hitch say for a 1/4” wire rope sling is 1.3 tons. If you take one sling and put it over a crane hook with an inverted basket hitch at a 60° angle, it’ll have a working load limit of 1.1 tons.
“But what if I take two slings up to a common point? Would that mean it’s a true vertical basket hitch?”
The answer is no. With two slings or one sling in an inverted basket, the working load limit still is going to be at 1.1 tons at a 60° angle.
Why Is Knowing Sling Angles so Important?
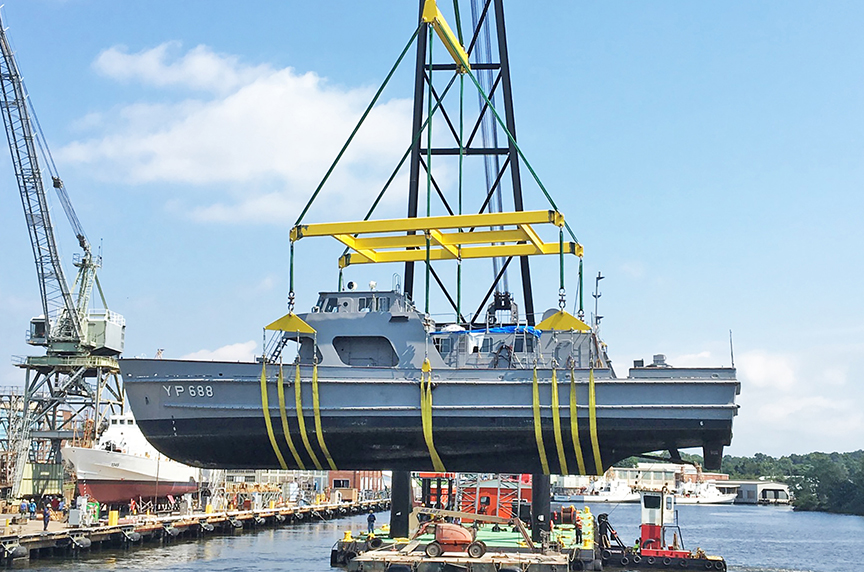
Safety is the most important thing to keep in mind when making a lift.
The goal is to pick up the load and deliver it where needed on a jobsite efficiently, and without putting your employees at risk.
By reading this article, we hope you understand the importance of:
- Measuring the sling angles correctly
- Keeping up with the latest safety standards
- Getting the most out of your lifts and lifting equipment
If you have more questions about sling angles or need new slings, call us at 800.362.4601 and speak with a Mazzella Lifting Specialist today!
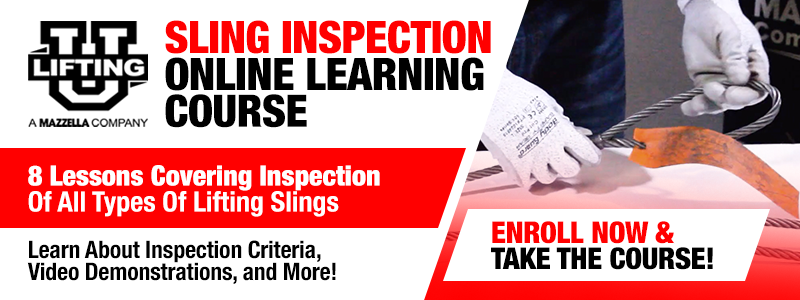
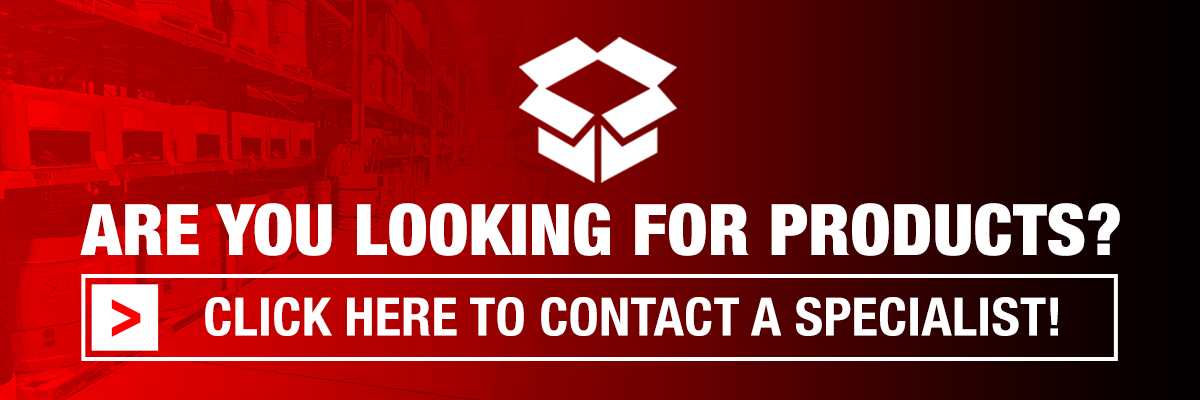
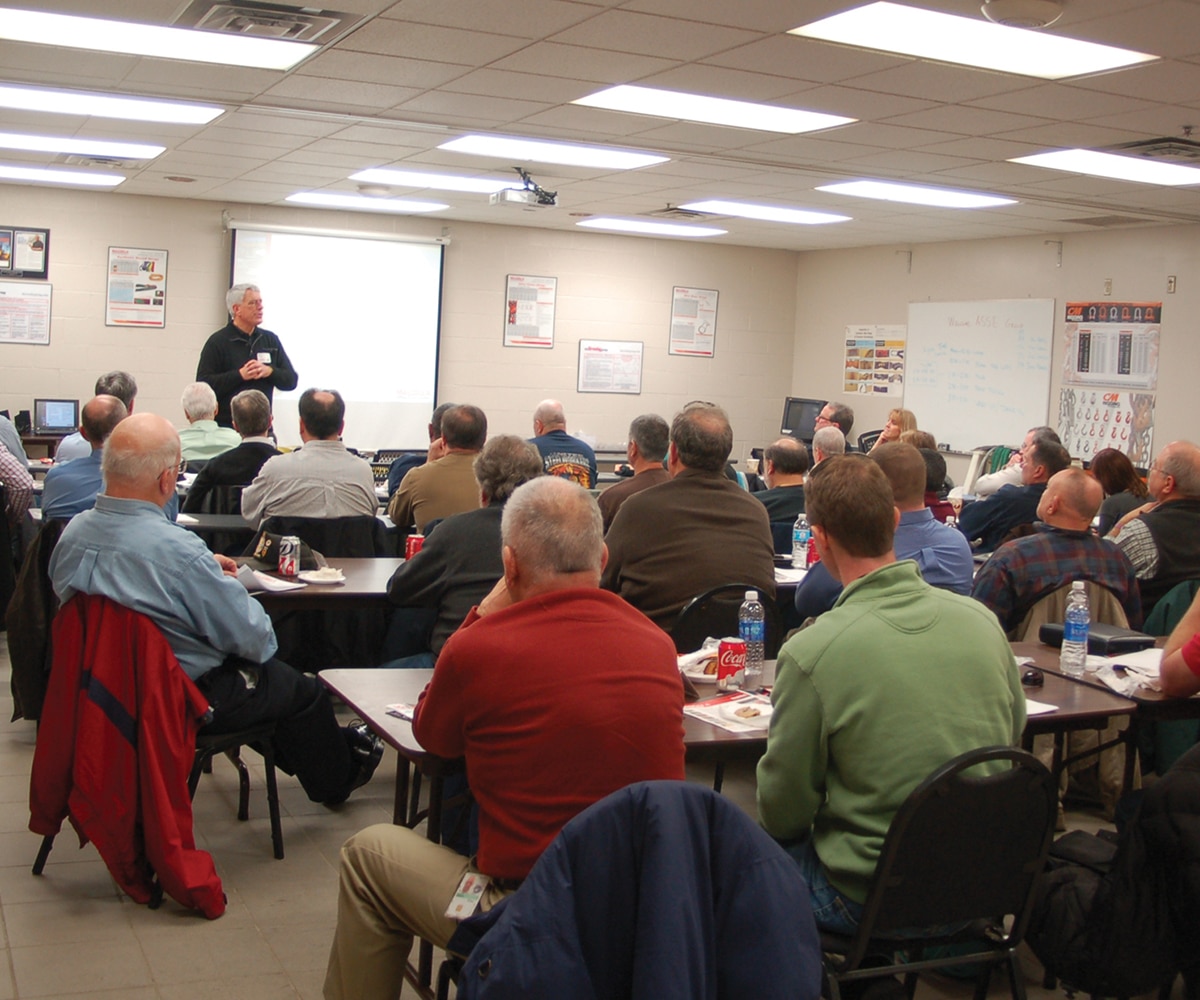
Lifting & Rigging Training
If you require a specific training course for OSHA compliance, Mazzella can assist you in creating a safe and reliable workplace. We qualify our trainers by requiring them to complete an internal train the trainer program (which trains to applicable OSHA and ASME standards and training technique), extensive field experience, and additional training from third-party entities, such as Crosby, CM, Harrington, Gorbel, and Industrial Training International (ITI).
Copyright 2021. Mazzella Companies.