Overhead Bridge Cranes: Single Girder vs. Double Girder Design
You’ll want to give careful consideration to the bridge design of your overhead crane system to make sure that you understand the requirements of the lifting task and the environment where the crane will be operating.
A bridge crane is a type of overhead crane that includes two or more overhead runways built into the building’s support structure. Bridge cranes have different configurations and can be comprised of one or two beams—more often referred to as a single girder or double girder design. Girders can be made of rolled steel or can be fabricated by welding the beams into a steel box design for added strength and rigidity.
The bridge is a load-bearing beam that runs the width of the crane bay and is the primary structural component that connects the runways and moves the hoist forward and backward using a trolley. The trolley and hoist can be designed to be top running or under running depending on the design of the building structure and the requirements needed to make the lift.
A single girder or double girder design will be one of the largest contributors to the complexity and overall cost of a new overhead crane system. In this article, we’ll discuss the advantages, disadvantages, and differences between single girder and double girder bridge crane systems. You’ll want to give careful consideration to the bridge design of your overhead crane system to make sure that you understand the requirements of the lifting task and the environment where the crane will be operating.
Single Girder Overhead Bridge Cranes
On a single girder crane, the bridge consists of one girder beam supported on each side by an end truck. The trolley and hoist are most commonly underhung—meaning they run on the bottom flange of the bridge. The bridge itself can either be top running or under running in design.
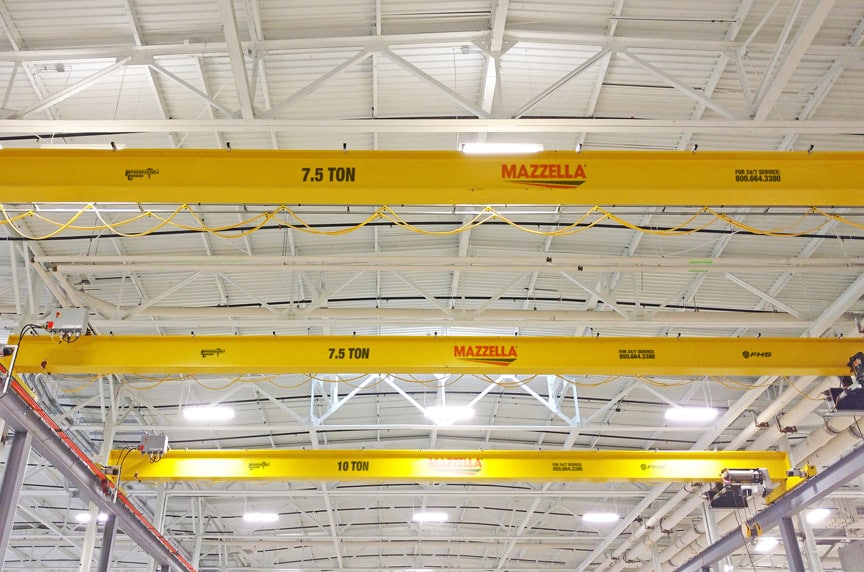
One of the most common misconceptions about single girder cranes is that they are not as durable or of the same high quality as double girder cranes. If properly designed, a single girder crane can be the perfect solution for a business that needs a light to medium duty crane, or for a facility where headroom and/or floor space is limited.
Single girder bridge cranes are often the most cost-effective lifting solution for various applications and industries. Single girder cranes use less material and are more compact and lightweight than a double girder crane, which results in a significant cost-savings in material, freight, and installation. Also, because they only require one bridge beam, these systems typically have less deadweight, meaning they can utilize lighter runway systems and tie into the existing building support structure.
Guidelines on Cost-Effective Designs for Single Girder Cranes
Max Capacity (Tons) | Maximum Span (Feet) |
---|---|
7.5 | 80 |
10 | 75 |
15 | 65 |
20 | 60 |
25 | 55 |
30 | 50 |
35 | 45 |
The major disadvantage of a single girder crane system is that they do have a limit in terms of capacity, span, and hook height. A double girder crane may be the better solution for overhead cranes that require capacities over 15 tons and spans over 65 feet.
Note: You will rarely see a single girder crane rated higher than 15-tons.
In addition, service walkways, enclosed or exposed operator cabs, magnet cable reels, or other specialized features can be difficult or expensive to incorporate into the crane’s design.
Advantages of a Single Girder Design:
- Less expensive due to a simpler trolley design, reduced freight costs, simplified and faster installation, and less material for the bridge and runway beams
- Most economical option for light to medium-duty cranes
- Lower loads on the building structure or foundations due to a reduced deadweight. In many cases, it can be supported by existing roof structure without the use of additional support columns.
- Better hook approach for both trolley travel and bridge travel
- Easier to install, service, and maintain
- Ideal for workshops, warehouses, material yards, and manufacturing and production facilities
- Lighter load on runway rails or beams means less wear on the beams and end truck wheels over time
- Great for facilities with low headroom
Disadvantages of a Single Girder Design:
- The hoist is placed under the cross girder and cannot provide as much hook height as a double girder crane
- On a standard rolled steel bridge beam, the under running hoist trolley may cause premature wear to the bottom flange of the beam
- Special features like service walks, lights, and heavy service components can be expensive or difficult to incorporate
- Lower capacity rating
<!–[if lte IE 8]><![endif]–>
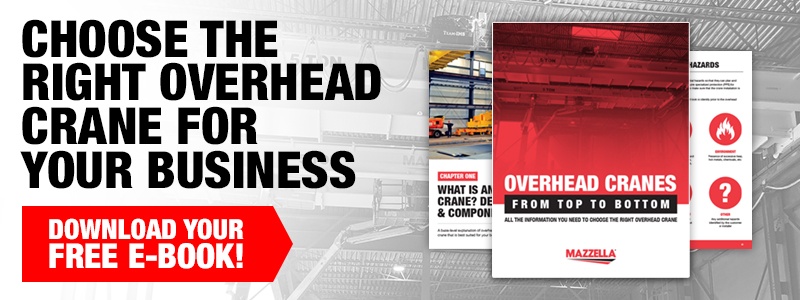
Double Girder Overhead Bridge Cranes
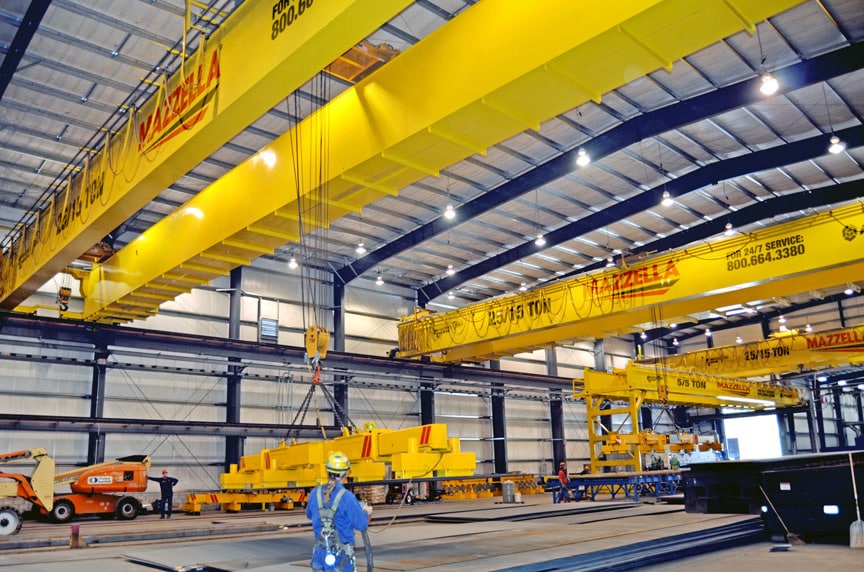
On a double girder crane, there are two girder beams that make up the bridge and they’re supported by an end truck on each side. In most instances, the trolley and hoist run on a rail installed on top of the bridge girders. With a double girder design, you gain the depth of the cross girder if the hoist is placed between or on top of the cross girders—providing an extra 18”-36” of hook height in most cases.
Double girder cranes can be either top running or under running in design. A top running double girder bridge crane will provide the most overhead room, as well as the greatest hook height.
Double girder cranes are recommended for heavy-duty applications where the crane has to handle heavier capacities and longer spans. Because of this, the components of the crane system, including the hoist and trolley, are more complex in design—making double girder cranes more expensive than a single girder crane.
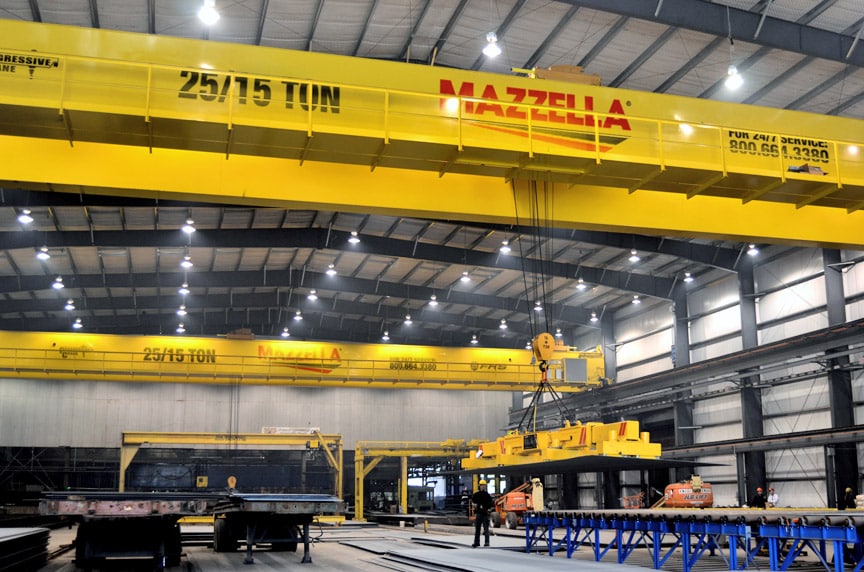
They also require more material for the bridge beams and the runway system, so extra consideration should be given to the building’s support structure. Additional tie-backs or support columns may need to be added to handle the additional deadweight on the supports or building foundation.
Double girder bridge cranes are ideal for lifting heavy loads and can be used in more frequent operation than a single girder crane. They can also be used both indoors and outdoors, in a bridge or gantry setup, and are frequently used in mining, iron and steel production, railyards, and shipping ports.
Advantages of a Double Girder Design
- Greater hook height – how far above the floor the hoist will lift (typically 18-36” more than single girder)
- No limits to maximum span or capacity
- Ideal for production and transportation of heavy equipment
- Ideal for frequent lifting of heavy loads
- Added features like walkways and maintenance platforms, cabs, magnetic reels, and lights can be added and supported by a double girder design
- Can be used in indoor and outdoor applications, including mining, iron and steel, railyards, and ports
Disadvantages of a Double Girder Design
- More expensive because of added material costs, additional structural support, and more complex crane components
- Additional costs related to freight and the installation of the crane versus a single girder crane
- Hook approach is lessened for both trolley travel and bridge travel—especially on double girder top running cranes
Wrapping it Up
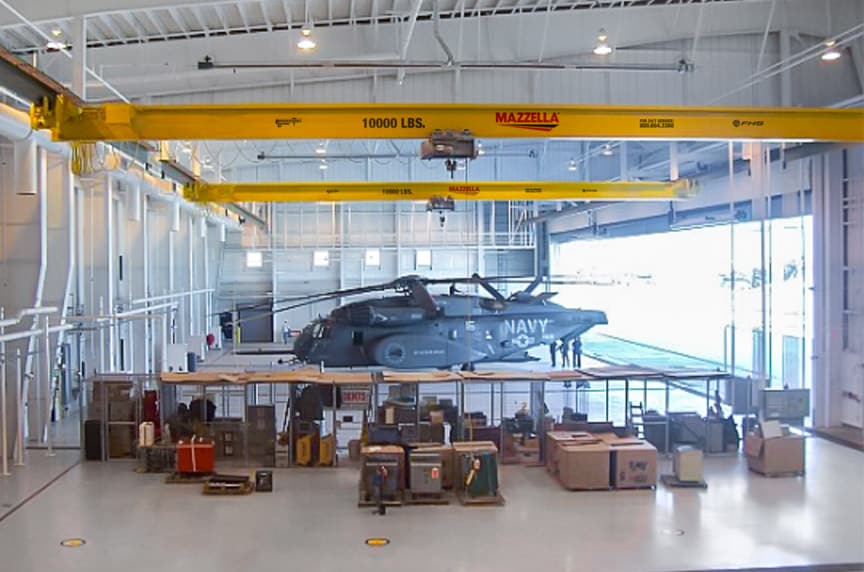
Careful consideration should be given to the design of your overhead crane system. A crane that requires a high capacity, wide span, or high lifting height will benefit from a double girder design, but may cost you more money upfront. Lighter duty cranes that don’t have hook height requirements or abnormal capacities or spans can be an inexpensive option that will help improve the efficiency and safety of your production or assembly facility.
At Mazzella, we are a leading manufacturer of world-class overhead cranes with more than 50 years of experience. We engineer and build custom solutions ranging from light-duty economical cranes to large-capacity, high-duty cycle cranes with welded plate-box girders. If you’re interested in receiving a quote on a new overhead crane system, or would like to schedule a consultation, contact one of our Crane Specialists today.
<!–[if lte IE 8]><![endif]–>
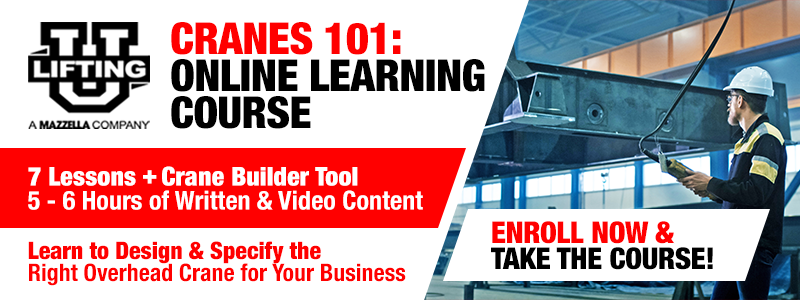
Copyright 2017. Mazzella Companies.