The Process of Ordering a Crane: Engineering, Fabrication, and Installation
Ordering a crane is no small task, and that's still true even after you sign the contract. In the finale to our series on ordering overhead cranes, we will cover what you can expect in the designing, installing, and manufacturing stages of ordering an overhead crane.
So, you’ve signed the contract to purchase an overhead crane for your facility. Congratulations! But, surprisingly, you’re only halfway there.
As we discussed in our previous article, the process of ordering a crane can be overwhelming, confusing, and frustrating. And this is no different in the engineering, designing, and installation stages of the project. There are many moving parts to account for, and collaboration between your team and the Project Manager will help keep the project on track.
At Mazzella, we have several decades of experience in designing, installing, and manufacturing overhead cranes for facilities in various industries. We also understand purchasing an overhead crane is a big financial decision, and we want you to be as informed as possible during this process.
In the finale to our series on ordering overhead cranes, we will be answering important questions during the latter half of the process, including:
- What Happens During the Approval Process of Ordering a Crane?
- What Goes Into the Engineering Phase of Ordering a Crane?
- What Happens During the Fabrication of a Crane?
- How Do Crane Companies Install Cranes?
- What Happens After You Install Your Crane?
- What Should You Know Before Purchasing a Crane?
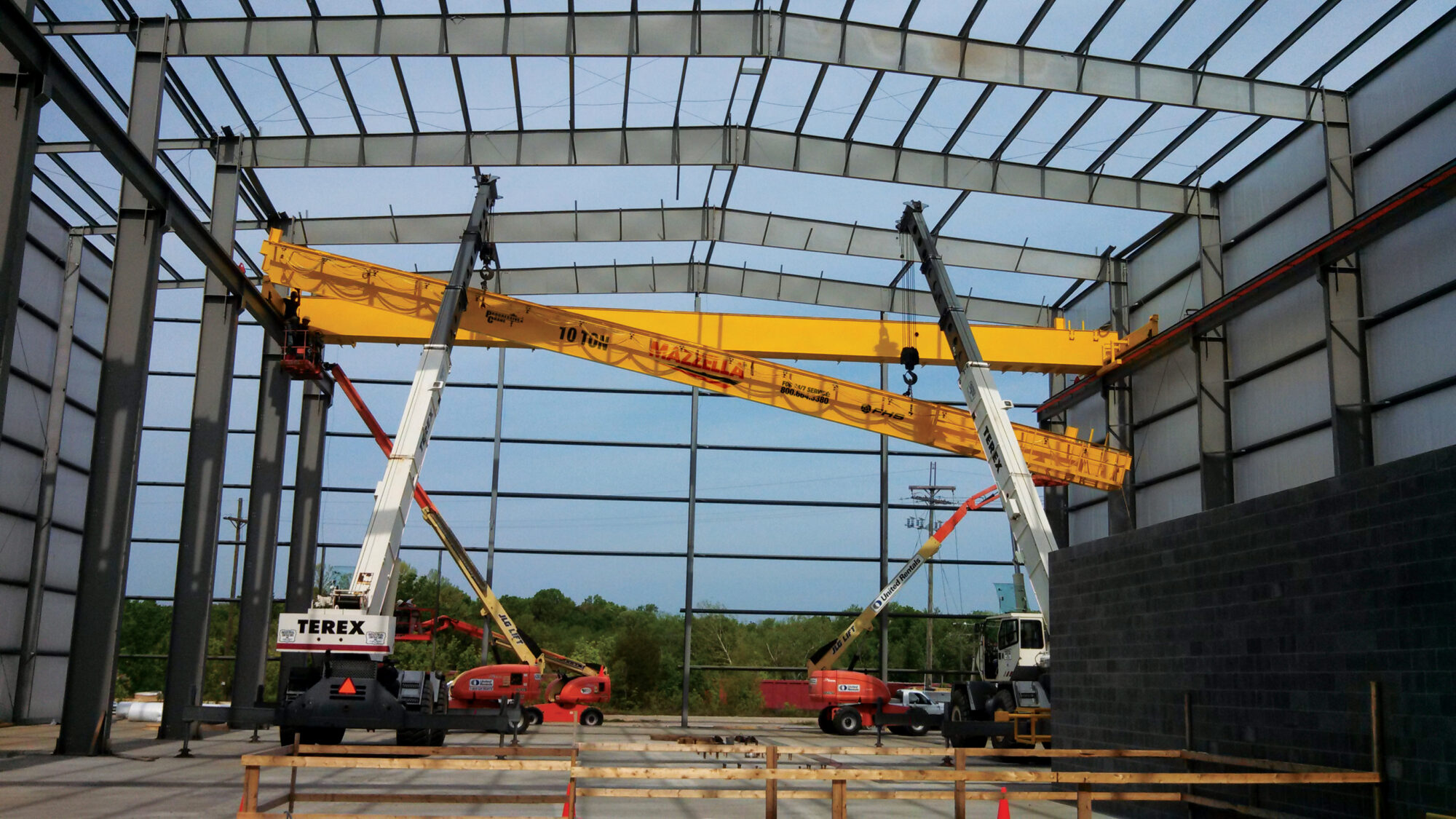
What Happens During the Approval Process of Ordering a Crane?
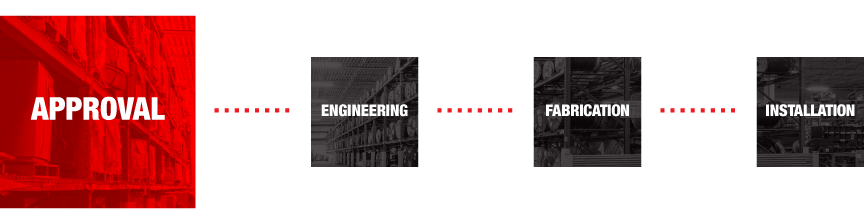
The approval process starts with meeting the Project Managers and they will gather dimensional and structural information at your facility. If it’s an existing building structure, the Project Managers will take measurements make sure the crane will fit. They will look for possible obstructions in your facility, like overhead lights, fans, water pipes, gas lines, and more.
Not only will they check the allotted space, but they will also confirm the equipment will meet your production, maintenance, and safety needs.
When visiting a site to gather measurements, it’s important that the engineers have full access to where the crane system will be installed. This could mean putting a break in production for a few hours and turning off the power to any existing cranes.
The approval process for a new building is different from adding to an existing facility. The Building Engineers and Project Managers will work with the architects or engineering company to get the new building blueprints. It is important to make sure the new building supplied is designed to support the crane loads.
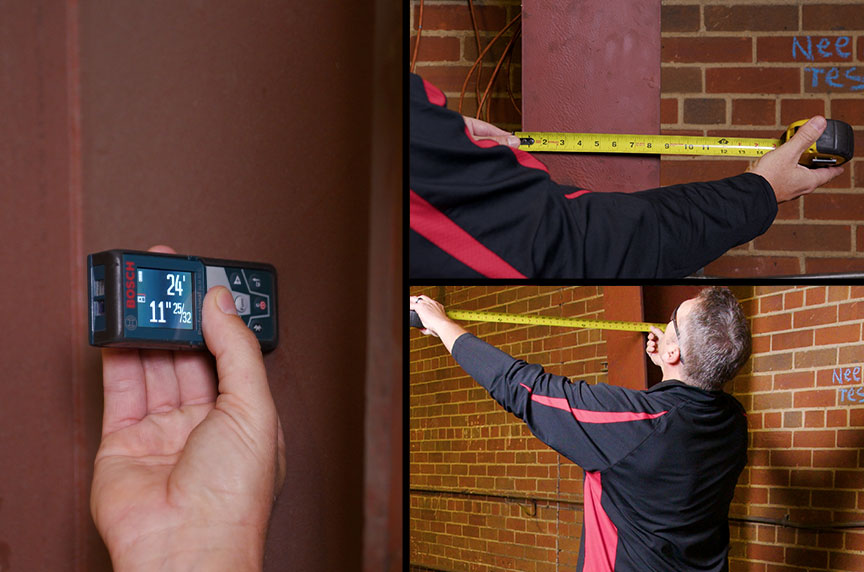
From there, the engineers can revise the approval drawings. As mentioned in our previous article, there will be multiple designs to your system. Changes will be made based on how your facility is laid out. You can expect a one-to-two-week turnaround on revisions.
Depending on what crane manufacturer you select, there are varying degrees of cooperation during the approval process. While most manufacturers will simply provide an approval drawing to you and make you responsible for checking yhe dimensions, Mazzella has more of a hands-on approach.
The parties involved in the approval process on the customer side range depending on the crane’s need. Generally, it’s maintenance, production, or safety personnel. Sometimes it’s all three.
The customer’s main contact after they submit a PO or provide a contract for the crane system will be a Project Manager. But this doesn’t mean the Account Managers and Crane Specialists are not involved.
When working with the Project Manager, establish a preferred contact method (email, text, phone calls, video calls) and a cadence that you see fit.
What Goes Into the Engineering Phase of Ordering a Crane?
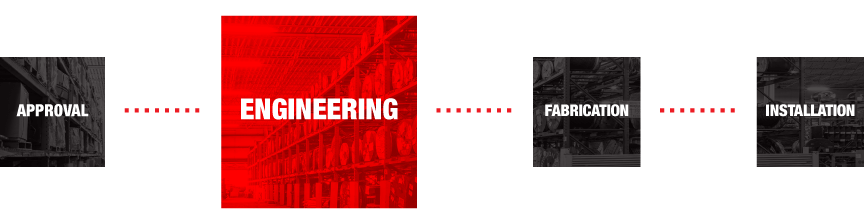
During the engineering phase, while you and your Project Manager stay in contact, it’s minimal compared to the approval process—mostly periodic schedule updates.
If anything changes during the engineering phase, they will reach out and let you know. If there are changes, they’re usually minor, and they will also provide an updated system drawing.
The engineering phase varies because the items can be off-the-shelf items, or they could be long lead items. If it’s a crane system with an off-the-shelf hoist, that could be a five to six week turnaround.
The sales team and the account managers will still be in the loop on how things are progressing leading to the fabrication phase.
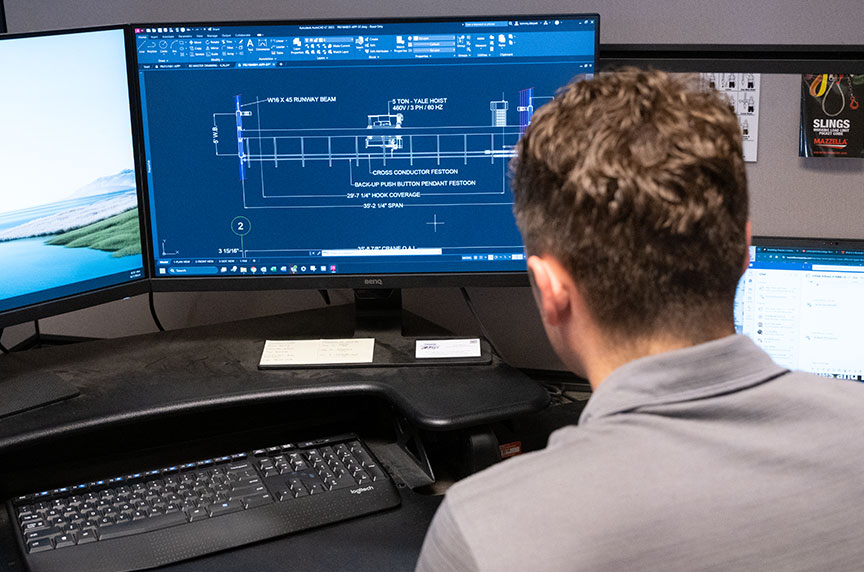
What Happens During the Fabrication of a Crane?
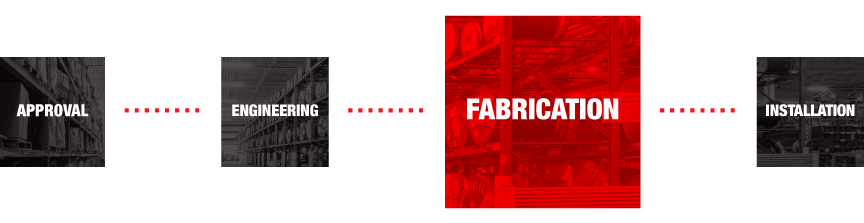
After the engineering phase, we head to the fabrication phase. During the fabrication phase, Mazzella will receive the components and materials that were ordered for the crane.
From there, the fabrications shop will assemble the crane and test it in a controlled environment. In some cases, they can build a runway if necessary.
The time required for the fabrication phase depends on size of the system and the lead time of the components. At Mazzella, once we receive the components, the turnaround time for a standard crane is about two weeks.
But, if it’s a more complicated crane, it could be three to four weeks, or even longer. There typically aren’t additional costs that a customer might see. When there are additional costs to a project, it’s usually handled during the approval process.
During the fabrication process, you can send emails, phone calls, or texts to get updates on production and ship dates. If you want weekly updates, you can arrange that with your Project Manager.
While the crane is being fabricated, there’s usually correspondence between you and the Project Manager. Here, they will:
- Confirm that you will have power ready for the crane system when it gets shipped and installed
- Confirm obstructions identified during the approval process have been or will be removed prior to delivery of the crane
- Make sure the area is safe for the installation crew to work in
- Bring the crane and runway into the building and designate staging areas so the material is close to the installation site.
While your main contact remains the Project Manager, Account Managers and Crane Specialists remain in contact with the Project Manager with any relevant updates.
How Do Crane Companies Install Cranes?
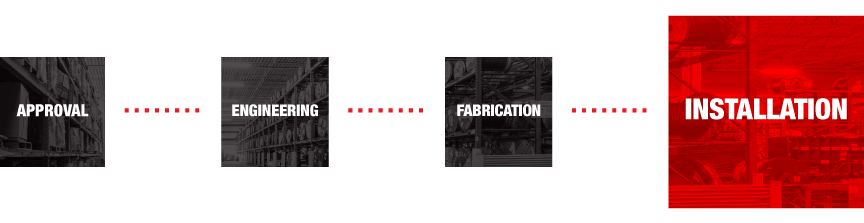
After the fabrication stage, we move on to the installation phase of the project. Prior to the installation, there’s going to be a site visit and conversation with the Project Manager, regarding what will be needed for the installation to go smoothly.
These conversations typically discuss potential access areas to the building and staging areas. For installation projects, you will not have a lot of responsibility regarding the logistics of the crane systems. Most crane manufacturers, including Mazzella, will arrange freight and schedule the crane’s arrival.
The installation crew will also be responsible for handling the new equipment. They’re used to rigging and lifting these pieces, so they can help prevent potential equipment damage.
Prior to the installation, the crane manufacturers will ask you to clear the area as much as possible to allow installers free access.
Mazzella handles most of the crane systems’ logistics—arranging the trucks and scheduling deliveries based on when our installation crews will be onsite.
If a customer would like us to ship a crane for them to stage on-site for any reason, we can arrange that, but the customer would likely be responsible for offloading the equipment. Typically, we try to schedule fabrications so they can be installed immediately after. This lowers the chance of equipment getting damaged and parts going missing.
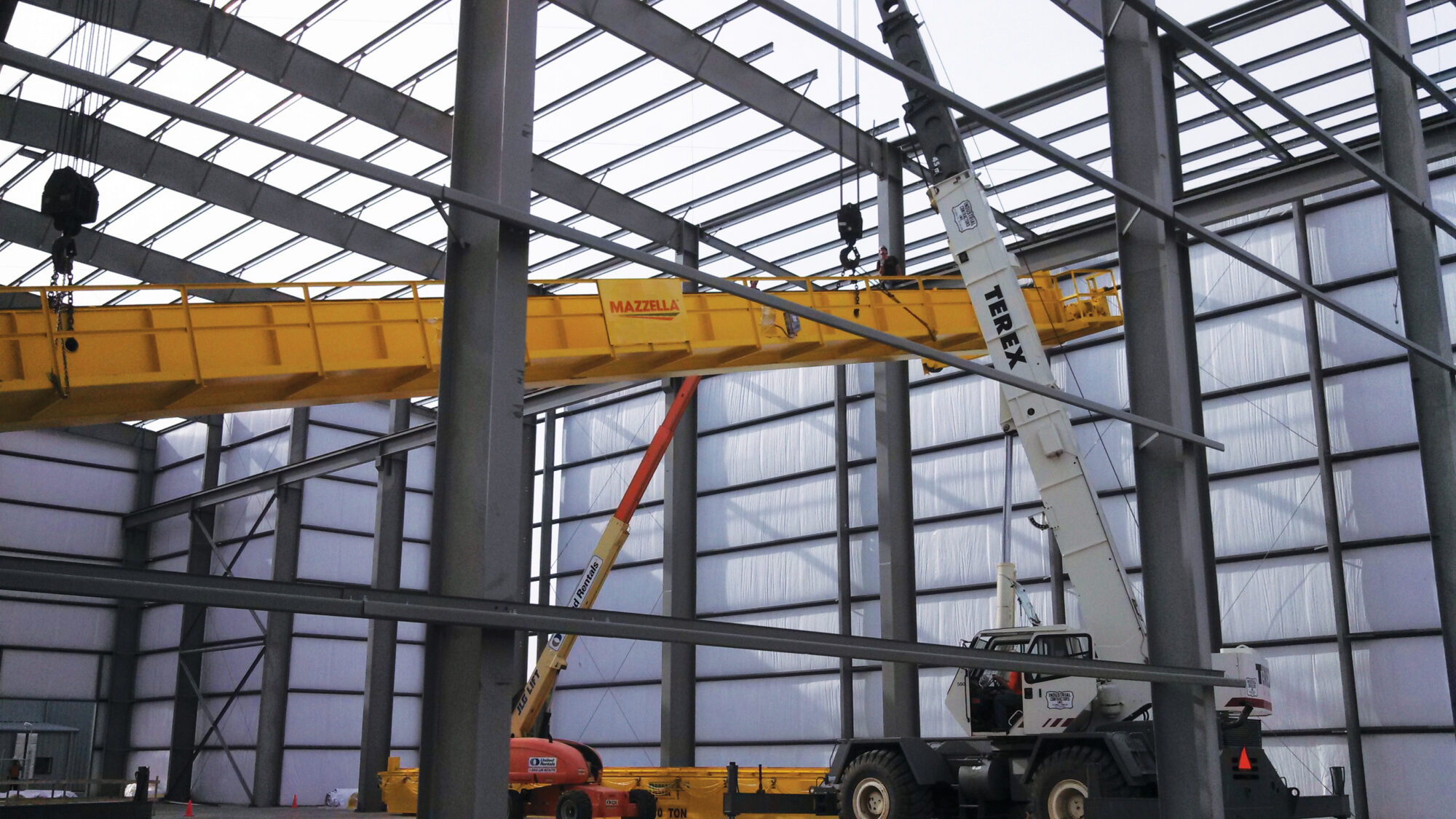
Are There Any Additional Cost?
During the installation phase of the project, it’s possible to have some additional costs if unexpected delays occur. To avoid this scenario, have pre-installation meetings with your team to discuss and establish installation plans.
Is Load Testing Required for a Crane?
The load tests of the new crane systems are ultimately a requirement to be completed by the end user. Mazzella typically includes that as part of their scope in the original proposal. So just in case a customer might not realize that that’s a requirement of theirs, Mazzella offer that as a standard in our proposals.
If a load test is conducted, the load shall be not less than 100% nor more than 125% of the rated load of the crane.
There are several methods to install an overhead crane. Mazzella has in-house service technicians who are experts at installing cranes. But like other crane manufacturers, we will also use subcontractor companies that specialize in installing crane systems.
During the installation phase, your main point of contact is still the Project Manager. Once the startup and load test are complete, we provide a load test certificate and the Project Manager’s job is done. They will follow up with you to ensure the crane is performing as expected.
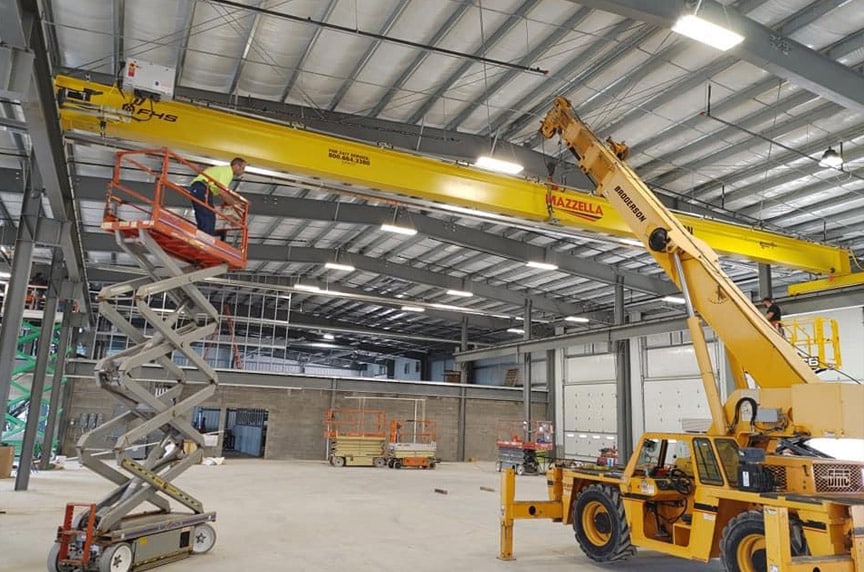
What Happens After You Install Your Crane?
To most, a crane is just a crane. However, each one operates differently and has unique features that a new operator needs to know.
Your Account Manager or Crane Specialist can walk you through the new crane and talk about safe rigging and operating practices. These discussions will ensure your operators are well informed about the new system.
Training for overhead crane operation is a requirement. However, certification is not required for overhead crane operations. If you need training for your crane operators, Mazzella can provide that.
After the crane’s installation, the account managers, crane specialists, and Project Managers are still available if you have any questions.
Is Warranty Provided?
Overhead cranes are typically provided with a standard one-year warranty. If you have issues with the system in that first year, you should reach out to your crane specialist or your account manager.
Typically, we will send out a crane technician to review the problem, and from there we can determine if it is a warranty issue.
Whether you have a new crane or an old crane, Mazzella has trained technicians that are qualified to work on your system. Any crane that you have requires at least an annual inspection. If it’s a highly used crane, you may want to look at semiannual or even monthly inspections.
What Should You Know Before Purchasing a Crane?
Hopefully, you better understand the process you may go through when purchasing an overhead crane.
If you are considering making that investment, we have a ton of information to help you become a more informed buyer. From our overhead crane buyers course to our overhead cranes e-book to numerous articles and videos, we have plenty of resources to keep you informed.
If you’d like to speak to an expert, contact one of our Crane Specialist to learn about our processes and offerings.
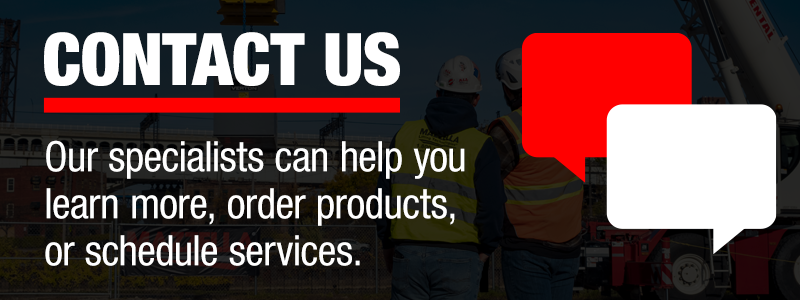
Copyright 2024. Mazzella Companies.