What New Lifting & Rigging Trends Can You Expect in Wind Energy?
Why has wind become an in-demand source of energy in recent years? There are many factors that have made harnessing the power of wind a viable option.
“A great wind is blowing, and that gives you either imagination or a headache.”
Like the words of European monarch Catherine the Great, engineers have used their imaginations over several decades to find better ways to harness the power of wind. And while their work has undoubtedly come with a headache or two, the engineers working on this technology have found better ways of converting wind into energy.
Renewable wind energy continues to be an emerging business. While wind farms are common across the world, the harnessing of offshore wind into energy has become increasingly popular in recent years.
What Factors Have Contributed to the Increase in Usage of Wind Energy?
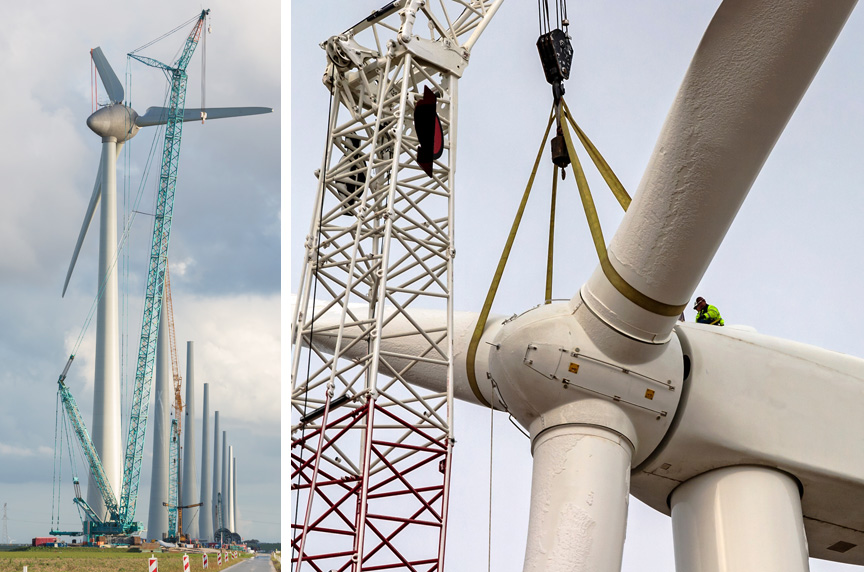
Since 2021, wind energy experts have seen the emergence of repower into the wind industry. That’s where governments decided to give credits to tear down old wind farms and replace them with newer turbines that generated more power. These older wind farms started using fewer turbines, which is a lot more cost effective.
Those in charge of wind farms have a need for regular maintenance and service, which have become more in-demand offerings. Additionally, there has been a change in the lifting equipment that is being used. That included moving away from traditional lifting slings, chains and fittings, and the adoption of using single-blade tools.
Service
On the mobile crane service side, the repower work is a lot more demanding on the wire rope itself because it’s a completely different application. The cranes themselves are getting larger and the winches work differently because they’re essentially going up without a load and coming down fully loaded—resulting in severe wear and rope issues.
On a traditional wind farm construction site, a crane’s hoist rope might last the entire job. However, on a repower job, they might go through two hoist ropes in the same timeframe. It’s resulted in a big transition for wire rope suppliers to provide ropes that can withstand the rigors of repower work.
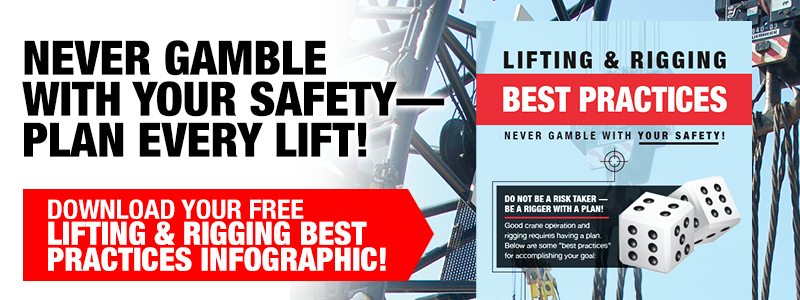
Did the 2021 Repower Credits Help Push Wind Energy Usage?
In 2021, the Federal tax credits incentivized wind farms to tear down old turbines and put up new ones. Over the last three years, there has been, and will continue to be, an increase in work on new wind farms. Wind energy experts have been seeing growth in more specialized lifting equipment being produced to accommodate the speed and scope of these repower projects.
Traditionally, the lifting industry used a lot more chain, or rounding material with protection, so tools or blades aren’t damaged during a lift. With these repower adjustments, it’s all about how quickly they can get the project done. This has forced manufacturers to develop blade tools that are specified to grip the turbine blade rather than the traditional method of wrapping around it and protecting it to stop damage being done to the tools.
With the repower and offshore industries, all of the equipment is getting so much heavier and bigger that manufacturers have had to produce wide-body round slings. Now, high-performance lifting slings are part of the industry, whereas before, the mentality was “just build the thing as easily as possible.”
However, construction companies have been purchasing their own equipment. They tend to rent the large tools, like the blade tools from the OEM (Original Equipment Manufacturers). The construction companies themselves still buy a lot of shackles and slings from third-party companies. Additionally, these companies are always looking for training on site.
What Are Some Challenges that Come with Using Wind Energy?
Getting workers properly trained on the equipment needed to execute safe lifts has been a problem.
The components are getting bigger, and the on-site workers are being trained on just general lifting equipment. From our perspective, these workers need more time being trained how to use our tools properly.
Unfortunately, in a lot of cases, the customized tools for building the turbines will arrive on site and need to be built. There’s not that many people in the field specifically trained on how to build these tools. From that perspective, third-party companies are spending more time training the end-user on how to use their products.
Although interactive training is possible, on-site work is preferred by the suppliers. It is important to train workers on how to build and maintain the tools. These tools aren’t “plug-and-play” devices.
There’s much work in the background that needs to be done with specialist lifting tools and transitioning to offshore applications. The offshore industry has added elements of danger. Along with the bigger components needed to move the turbines, components, and other equipment needed to install the turbines, from land-based to a barge system. You’re taking components out to a ship that’s going to build the wind turbine. You’ve got so many factors at play, including tidal movements, waves, and wind. There’s a lot of training needed to be done to perfect offshore construction and installation work.
Is Onshore Wind Energy Usage More Advanced than Offshore Usage?
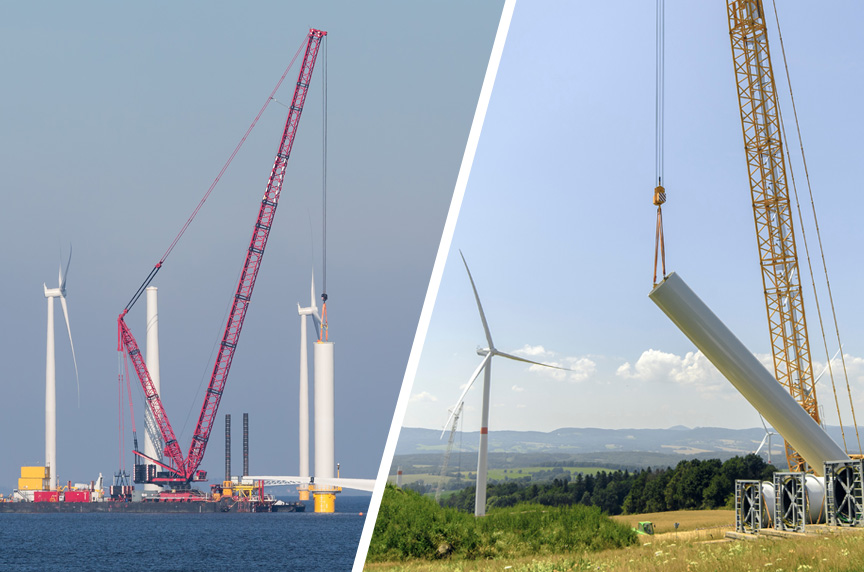
The short answer to this question is: Yes.
The offshore industry is completely new to the U.S. market, and thus, a whole new workforce must be trained. There will be a lot of unions involved in the offshore work. The unions are going to need to retrain all their staff to work onshore in the marshaling yards and ports. Additionally, they will look to train in offshore turbine construction and maintenance.
It will be a steep learning curve for suppliers and workers alike.
What Technological Advances Have Been Made That Could Help in Wind Energy Construction?
Verton Load-Control Devices
The Verton EVEREST SpinPod™ load-control device is one of the biggest technological advances lifting specialists have seen.
Often, the first question specialists get is: how do we transition this to wind? Verton already is working on blade systems to account for wind. It’s not all the way there yet, but Verton and the Crosby Group are working hard to further develop their technologies.
Currently, they’re working on The Windmaster, which they hope to have on the market soon. Like the SpinPod™, The Windmaster is a spreader beam designed for lifting turbine blades. It comes with gyroscopic controls, which removes the need for taglines. The Windmaster will hold a blade in position so it can be attached to the rotor. It gives the operator full control of the blade tool and holds it in position.
BlokCam
The BlokCam system is another innovation from Crosby.
BlokCam is a camera system that will be added to blade tools. When the crane operator is going to pick up a blade, he can actually get vision of picking up the blade.
The blades are marked, or they’re going to start to be marked again, where the lifting points are. Without these pick-point marks, there has been a lot of damage to blades in this industry. Unfortunately, blades have snapped when not picked up in the correct position.
Because of this, Crosby has started trials with some of the OEMs to put a BlokCam on the blade tools, and also, for tower lifting. When operators lift a tower section onshore, there’s always someone in the tower underneath the load. Now, with a BlokCam system, the crane operator actually can make sure there is nobody directly under the load before lowering sections of the tower.
Inspection Tools
Rental companies are being hired on construction and repower sites. That has led to a lot of requests for different tools for safety. It’s both safety-driven and money-driven. The cranes are getting extremely large, and with the cranes getting larger, the ropes are increasing in size.
Companies are trying to protect their investments, and not spend hundreds of thousands of dollars on downtime and rope changes in the field. They’re driving companies to develop new inspection:
- Tools
- Processes
- Programs
Typically, in the past, the main customer base has been crane rental companies. It’s starting to slowly, but surely, transition to the wind companies themselves and construction companies. They’re the ones requesting inspections.
How Can Europe’s Struggles Help North American Markets Avoid Pitfalls?
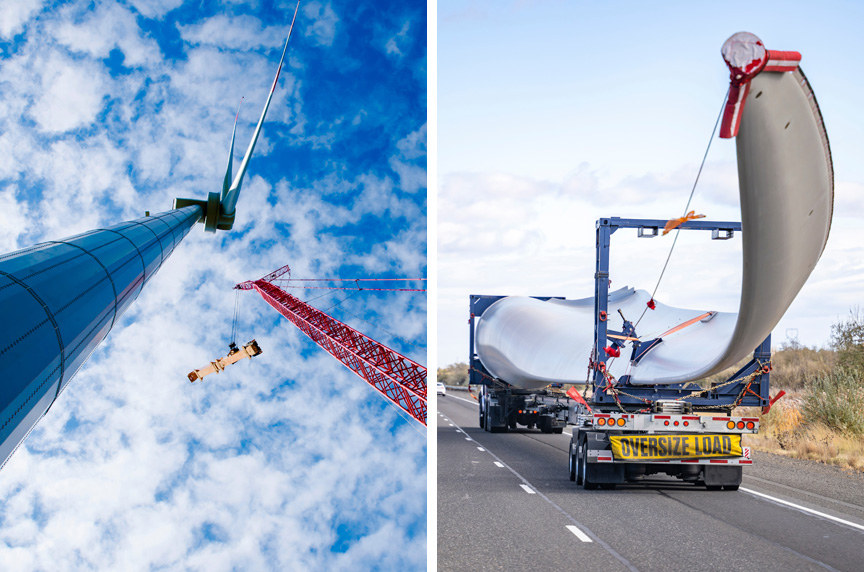
While much was learned from the struggles in Europe, North American companies are going to have similar short-term challenges.
Transport
The biggest challenges for U.S. companies include not having the infrastructure to handle these large components. In the initial phase of offshore wind turbine construction, all components will come from overseas. They’ll be shipped over to the U.S. and put into a marshaling yard or port. Then, they’ll be shipped back out to the installation vessel.
When this happens, they have to use Jones Act, which requires an American-flagged ship to make the transport. We’ll have to develop a barging system or transfer vessel system to take components out to these sites.
Facility Upgrades
The ports themselves will need upgrades to handle the weight of the components. There will be a big demand for new cranes, as well as new warehouses. Then, additions to the staff will be necessary, and they must be trained how to handle these components.
Guidelines
The lifting regulations and specifications are interesting. There are no real offshore regulations in the U.S. Everything that’s going to be done will be handled by the Global Wind Organization (GWO), or IMCA (the International Marine Contractors Group). They set guidelines for lifting and rigging equipment.
How Have Safety Improvements on Wind Energy Sites Changed the Lifting Industry?
The most noticeable difference is the increase in sheer size of the wind turbine’s components.
The first towers were maybe 50-60 meters in height with blades of 30-40 meters. While driving the main highways in Oklahoma and Texas, our lifting specialists have gotten up-close views of the newer components. They are significantly larger than the towers and components being replaced.
Improved Communication
The good part about the lifting industry, like high-performance lifting slings and wide-body shackles, they’ve made it so much lighter and safer. The lifting industry has probably got better because of the renewable energy construction industry. It had to evolve to lift such awkward products safely.
Today, crane operators and supervisors will meet at the actual turbine site with the rigging crew. The supervisor will run through everything that’s going to happen that day, and tell them all the different components they’re going to use. Then, they’ll inspect the components. Everybody on that team has to sign a sheet saying they took part in the meeting and inspection.
The industry has come a long way, and for the better, compared to even 15 years ago when things were more relaxed. The offshore wind market is going to make the industry even tougher on lifting regulations.
How Can Mazzella Help You with Your Lifting and Rigging Needs?
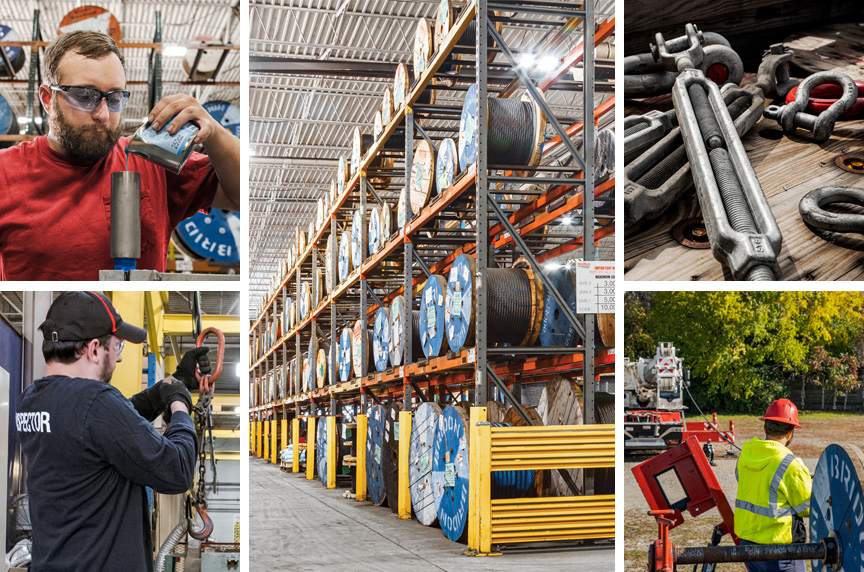
At Mazzella, we have you covered when it comes to all of your lifting and rigging needs. With our ready stock inventory, we offer all industries a variety of lifting and rigging devices.
Crane Ropes
Mazzella is a one-stop-shop for high-performance crane ropes, or any kind of specialty ropes. Also, we have fittings and sockets that we can install in the field, and a large inventory of ropes in stock that allows us to help get you back up and running as quickly as possible.
We offer a new rope replacement off the same spooling truck and trailer used for inspections. If it’s a rope replacement, that’s something we can typically get on a truck and on the way the same day if the order is placed by 2 p.m. ET. If that happens, we can get the rope on the road and conduct the installation the next day.
Mazzella has one of the largest specialty rope inventories in the United States…ready for immediate delivery! We provide wire rope assemblies, and manufacture bridge cables, crane cables, steel mill cables, and thousands of OEM assemblies:
- In sizes from ¼” to 3” diameter and 9mm to 52mm diameter
- Domestic and Non-Domestic
- In stock and ready for same or next-day shipment from one of our many service centers
In addition to crane ropes installations and inspections, Mazzella has the capabilities to do button and OEM socket installations. We have technicians around the country who have been trained to do:
- Socket installs
- Run the spooling trucks
- Perform crane rope inspections
- Conduct slip and cuts repairs
Hardware
We offer one of the largest and most complete inventories of rigging and lifting products in the country from some of the largest manufacturers in the world. Some of the products we stock are:
- Shackles—all types, sizes, and finishes from 1/4 ton to over 1,000 tons
- Hoist rings—standard and metric
- Eyebolts—forged, metric, and stainless steel
- Hooks—swivel, eye, choker, self-locking, and weld-on
- Master rings / links—all sizes, types and finishes
- Turnbuckles and swivels
Rigging Training
If you require a specific training course for OSHA compliance for slings, hoists and / or rigging hardware, Mazzella can assist you in creating a safe and reliable workplace.
Our rigging training focuses on:
- Overhead cranes
- Below-the-hook lifters
- Lifting slings
- Rigging hardware
- Wire rope
All Mazzella trainers have been accredited by our company through training by a third-party company (Industrial Training International, Inc.), Mazzella Companies’ internal Train-the-Trainer program, and are trained on OSHA and ASME standards.
Also, we provide site assessments. The purpose of an assessment is to systematically observe and record your lifting and rigging procedures, equipment, and records. This is not an inspection, but rather, a general assessment by which opportunities for improvement may be identified.
Rigging Inspection Services
OSHA 1910.184, ASME B30.9 Slings, ASME B30.20 Below-the-Hook Lifting Devices, ASME B30.26 Rigging Hardware & ANSI Z359 require…
Periodic, documented inspections on slings, rigging hardware, lifting devices, and fall protection every 12 months, at minimum, and monthly to quarterly in more severe service conditions.
Our rigging inspectors are certified to ensure your products meet OSHA and ASME requirements. Also, we provide personal fall protection inspections and basic level non-destructive testing (NDT) inspections to support our visual inspections.
Call us at 800.362.4601 or click here if you need inspections for rigging hardware, training, or any of our other services.
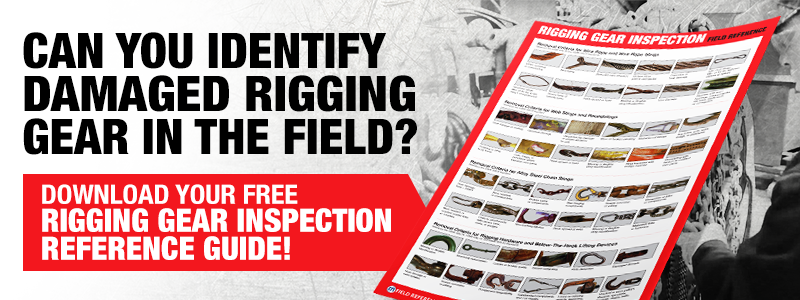
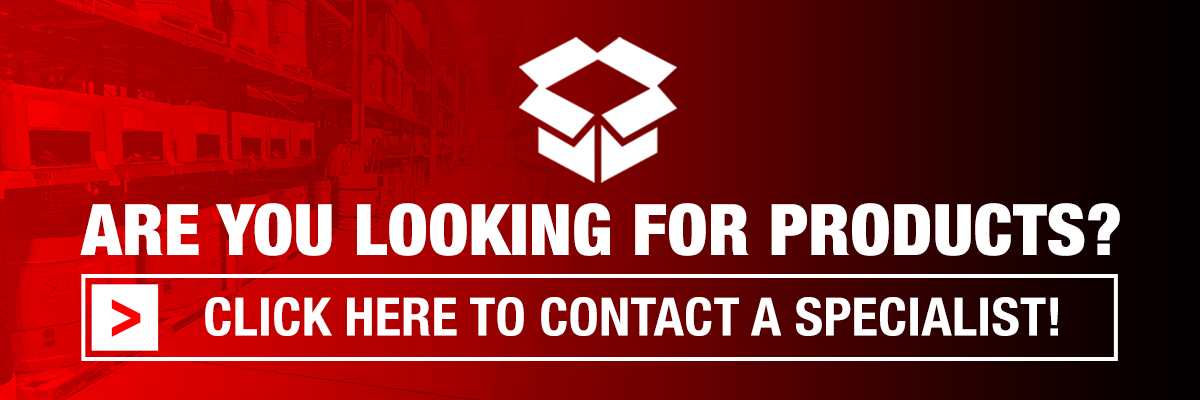
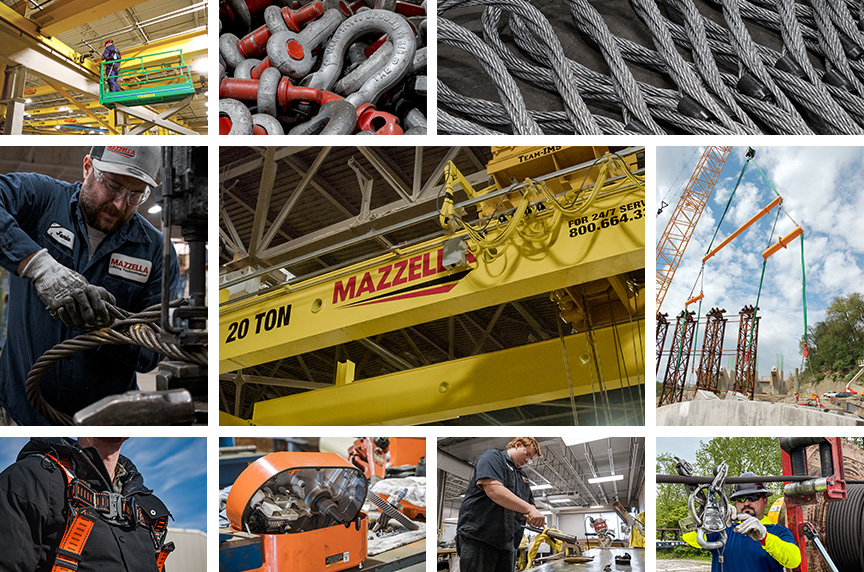
Lifting and Rigging
The Mazzella name is synonymous with quality slings. Mazzella’s quality slings include chain, wire rope, nylon, polyester, cordage, and high-performance synthetic slings.
We also provide wire rope assemblies—both large and small. We manufacture bridge cables, crane cables, steel mill cables and thousands of OEM assemblies.
Copyright 2023. Mazzella Companies.