6 Signs it’s Time to Upgrade and Modernize Your Overhead Crane
Overhead crane modernization can be as simple as replacing one component or replacing multiple component systems. A lot of business owners will take an “a-la-carte” approach and invest in the upgrade and replacement of multiple components of an aging crane system to improve efficiency, production, and help to improve safety.
The lifespan of an overhead crane system can span decades if it was properly engineered, installed, and maintained throughout its lifetime. However, it can be frustrating to feel like you’re stuck with an expensive piece of equipment that has become unreliable, unsafe, and outdated as your production needs have changed or your business has grown. An upgrade or modernization of your overhead crane equipment can change all of that.
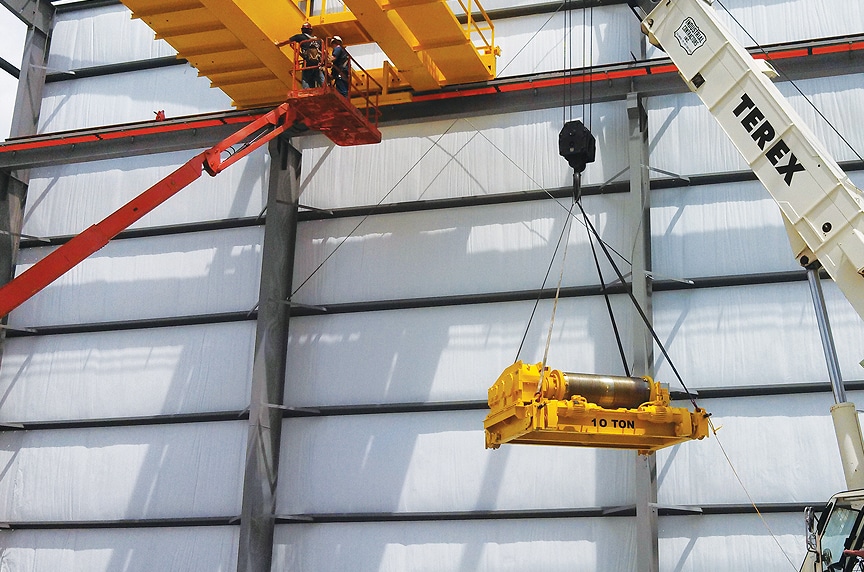
Fortunately, engineering advancements and modern technologies can extend the life of an overhead crane that no longer works efficiently or doesn’t meet the production requirements for which it is currently operating under.
At Mazzella, we specialize in servicing overhead cranes and hoists, including modernizing and upgrading overhead crane equipment. We can custom-engineer solutions to extend the life and improve the production of your crane equipment with more efficient hoists and drives, updates to electrification and drive control systems, and so much more.
Why Upgrade or Modernize Your Overhead Crane?
The major benefit of installing an overhead crane system is the lifespan that you can get once you’ve invested in the equipment. While the components of the crane can wear down over time and may need to be repaired or replaced, the structure of the crane itself typically has a longer lifespan than the other components.This allows you to upgrade or modernize the individual crane components as newer and more efficient technologies become available, all while continuing to utilize the main runway and girder structures in place.
So, why would you need to upgrade your overhead crane system? Let’s explore some reasons that would provide the opportunity to modernize your overhead crane’s components.
6 Signs it’s Time to Upgrade and Modernize Your Overhead Crane Equipment
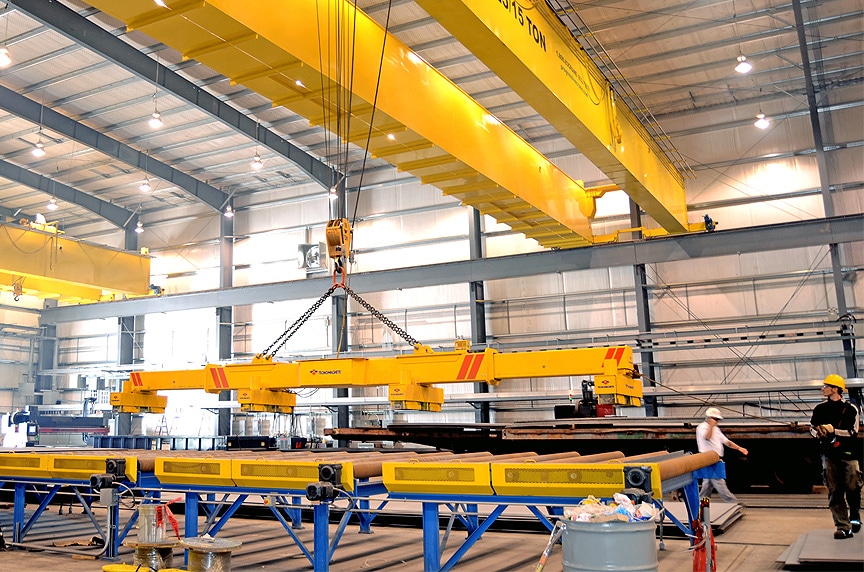
1. Your Production or Lifting Requirements Have Changed
You may have been reliably using your overhead crane system for years with no problems—but now your production needs have changed due to any of the following conditions:
- Another production shift has been added to the schedule
- You’re lifting different or heavier materials
- You require faster speeds to perform the lifts
- You need more precise controls
- You’re making more lifts per shift or using the crane more frequently
When you originally designed your overhead crane system, each individual component including the controls, hoist, end trucks, trolley, and drive systems were all specified to a specific duty cycle or crane service classification. If you now need the crane to make more frequent or heavier lifts, this can put a strain on your crane equipment if the new production demands exceed the duty cycle or service classification of the existing crane components. Over time, this will lead to premature wear or even failure of your crane components if they aren’t properly inspected, serviced, and maintained.
Consider your crane’s braking system. If over time, you have to keep replacing the brakes on your crane because the load it’s lifting is now heavier than what the brakes were originally specified for, this puts more strain on the brakes to slow down and stop the crane’s motion. This added strain will begin to prematurely wear the brakes—requiring more frequent service and an increase in maintenance costs. These increased costs add up over time and in the long-run, can end up costing more than it would to have simply upgraded and replaced the entire brake system with something more substantial.
2. You’re Experiencing Excessive Wear or Frequent Repair of Crane Components
Overhead crane components that receive a lot of use may be showing signs of excessive wear, or you may be experiencing more frequent shutdowns for service or repairs. The cost of frequent repairs can add up over time versus the cost of new replacement component (brake systems for example).
Not only do you need to consider the cost of the service call and replacement parts, but the true cost related to shutting down your production when your crane equipment goes down.
You have to factor in the cost of the equipment downtime, lost production costs, and lost production time for your workers. In certain manufacturing environments, the cost of downtime can be tens of thousands of dollars an hour!
Older cranes can require more maintenance and repairs. While you may find that your crane system is still structurally sound, you may want to consider modernizing or upgrading any specific components that need to be serviced or replaced frequently.
Think of it like this—if you had a work truck that constantly needed new shocks, at some point, you would decide it’s more cost-effective to install a heavier-duty set of shocks and springs that will hold up to the demands of your daily driving and hauling needs.
If you find that you’re replacing or repairing the same crane parts again and again, it may make sense to schedule a consultation with a professional crane technician to come in and inspect your crane equipment and make a recommendation on replacing or upgrading your equipment.
3. An Inspection Uncovered Issues with the Crane’s Equipment
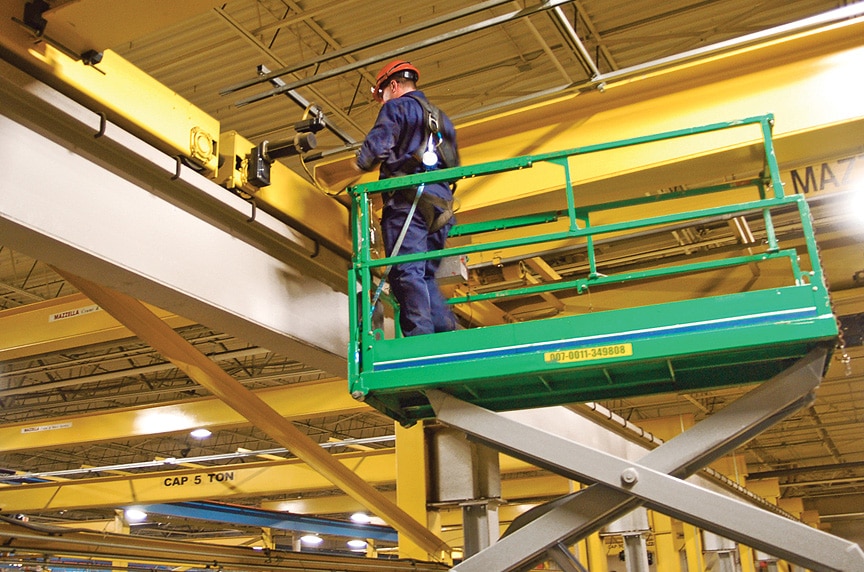
OSHA, ASME, and CMAA have specific guidelines for the frequency of inspections for overhead cranes. Establishing a regular inspection schedule can help to keep your crane and hoist equipment operating at top efficiency, help keep the operator and other personnel safe, and help reduce costly downtime and extend the life of the equipment.
Regular inspection also helps to identify signs of wear and irregularities with the whole crane system as well as with the individual components. If during the course of an inspection, you find that individual components are wearing faster than normal, you may be able to replace these with components that are stronger, have greater performance, and require less maintenance. That’s the benefit of replacing a 15-20-year-old part with a new and modern design.
You may also find that an industry sanctioning body like OSHA, ASME, HMI, or CMAA have released an updated version of one of their standards. When it comes to wear and fatigue tolerances for individual crane components—what may have been acceptable in the past may no longer be in compliance with current safety and design standards or best practices. Modernizing your overhead crane using components that meet or exceed the latest industry standards will help to ensure that you’re in compliance and help keep your employees safe.
4. Replacement Parts are Becoming Difficult to Find
As cranes age, it can become more and more difficult to find replacement parts for their individual components. The OE manufacturer may no longer be in business, may no longer have a distribution network, or the parts themselves may be obsolete. It can be difficult to source direct replacement parts for older cranes—and if you’re even able to find the parts, they may have extremely long lead times, and come at a steep price.
Some crane service companies are able to reverse engineer or rebuild parts for older crane systems, but this can also lead to high costs and long lead times as these are most often custom-designed and one-off builds.
Under certain circumstances, the easiest and most cost-effective solution can be to upgrade or modernize your crane’s broken or worn-down parts. Not only do you get the benefit of a brand new component and modern design, but you know that if it needs to be serviced or replaced down the road it will be easier and more economical to find replacement parts.
5. You Want to Improve the Safety and Efficiency of Your Overhead Lifts
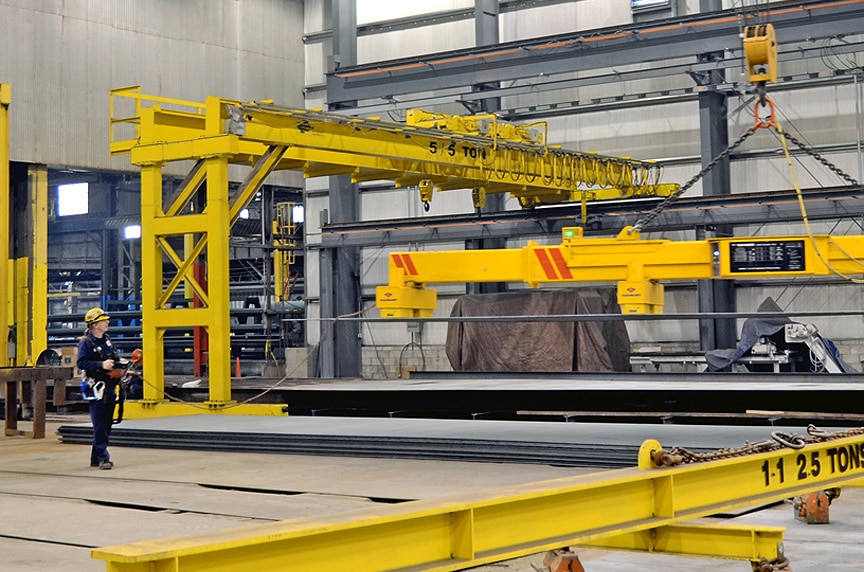
Today, most businesses with an older crane are replacing and modernizing their crane’s control systems and replacing the operator cab with push button pendant or remote radio controls.
While not as popular today, open or enclosed operator cabs were standard on most crane systems. The operator sat in a cab that was attached to the bridge of the crane and relied on other personnel on the floor to provide signals and direction to help them lift, lower, and maneuver the crane’s hook to safely move a load through a facility. By moving the operator to the ground, you can reduce the number of personnel required to move and operate the crane—and in most instances, the operator can load, move, and unload the crane himself.
The most important reason that companies are converting to pendant or radio controls are for safety reasons. The operator has a much clearer vantage point from the ground to identify and react to obstacles, personnel, and hazards while the crane moves through the bay.
6. You’re Considering Purchasing a Replacement Overhead Crane System
If your overhead crane system has become a maintenance headache or is no longer a reliable piece of equipment, it can be easy to cave-in to the idea of buying a completely new crane system. While the idea of a brand new system can be attractive, it may not be a cost-effective solution. You can still modernize one or multiple component systems on an overhead crane at the fraction of the cost of a completely new overhead crane.
If your crane equipment is older, you should consider the return on your original investment. You’ve most likely paid off, or are close to paying off, the cost of the initial investment. Like we mentioned earlier—very rarely do you find that the actual structural components of the crane need to be replaced.
Also, an overhead crane upgrade or modernization can be scheduled in phases to spread out the cost of the upgrades, as well as cause less disruption and downtime that can affect your business’ production and manufacturing output. Consider how long your crane system could be down if you had to replace the entire structural, mechanical, and electrical pieces of your crane system.
Most crane upgrades consist of upgrades or modernization to the crane’s electrical or mechanical systems. Due to the cost and transportation of the material, the crane’s support structure (including the runways, supports, and girders) can be the single most expensive component of an overhead crane system.
We typically recommend that you price out the cost of modernizing or upgrading your overhead crane and weigh that versus the cost of an upgrade.
If the cost of your crane upgrade or modernization exceeds 65% of the cost of an overhead crane, then it may make more financial sense to go with a completely new replacement system.
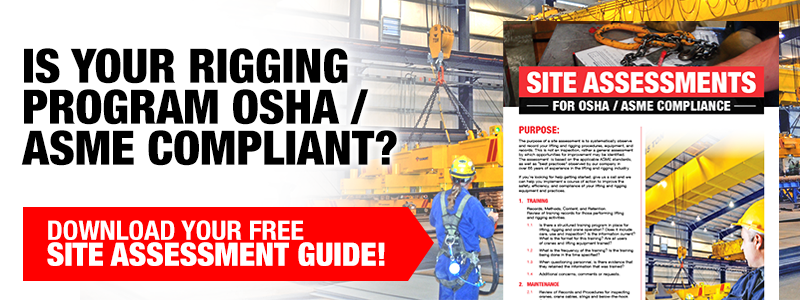
What Parts of an Overhead Crane System Can be Upgraded?
Overhead crane modernization can be as simple as replacing one component or replacing multiple component systems. A lot of crane owners will take an “a-la-carte” approach and invest in the upgrade and replacement of multiple components of an aging crane system. In this section, we’ll discuss the different components of an overhead crane that can be upgraded and also discuss their benefits to the efficiency and capabilities of the crane system.
Crane Control Systems
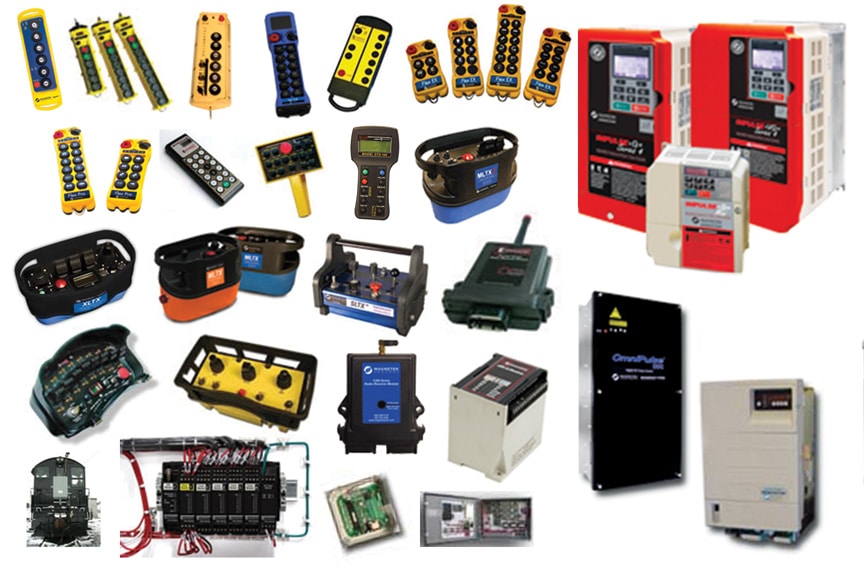
For newer style cranes, there is an added safety bonus when converting from pendant to radio controls. Radio controls operate wirelessly using a transmitter and receiver and don’t require the operator to be tethered to the crane like a pendant system does. This allows the operator to work away from the load, and also away from other obstacles or trip hazards as the crane moves down the bay.
Modern-style radio controls also offer diagnostics and monitoring (off-site or on-site). Crane operators and production personnel can now use mobile devices, tablets, workstation computers, or an operator’s “belly box” to view real-time diagnostic data, including:
- Fault codes
- Number of lifts and cycles that the drives have made
- Capacity of lifts
- Maintenance requirements for certain components
- Amp draw and voltage
For many years, the drive controls on overhead cranes were commonly single-speed, two-speed, or fixed-speed designs. These types of drives can be pretty rough on the brakes, gearboxes, couplers, and girders on the crane because the starting and stopping of the crane can be fairly abrupt.
With the introduction of variable frequency drives, microprocessors now control all the components of the drive system, and provide smoother acceleration and deceleration curves. This allows for smooth starts, smooth transitions, and smooth stopping which greatly reduces the strain on the gear boxes, couplers, girders, and other crane components. This also greatly prolongs the life of the brake system as the computer controls and slows down the motor, while the brakes mostly act as a control to keep the crane from moving. Also, by eliminating the abrupt starting and stopping of the crane, you get far less load swing because the crane movies in a controlled manner—making it safer for everyone on the floor.
Brake Systems
Like many other components of an overhead crane, it can be difficult to source replacement parts for a crane’s brake system.
Overhead cranes with older brake systems also miss out on the benefits of newer technologies like wear sensors and auto-adjust features. Auto-adjust features make sure the brake is always in proper adjustment, and doesn’t require maintenance or service personnel to manually and repeatedly adjust the brakes. This results in equal wear on the brake pads and less wear and tear on the moving components.
If you choose to upgrade your crane’s brake system at the same time that you add variable frequency drive controls, you can greatly reduce the wear and tear and maintenance on your brake system. Having a microprocessor control the motor and slow the crane’s motion versus using the brakes to slow down the crane, can prolong the life of the brake system.
Hoist, Trolley, and Gear Box
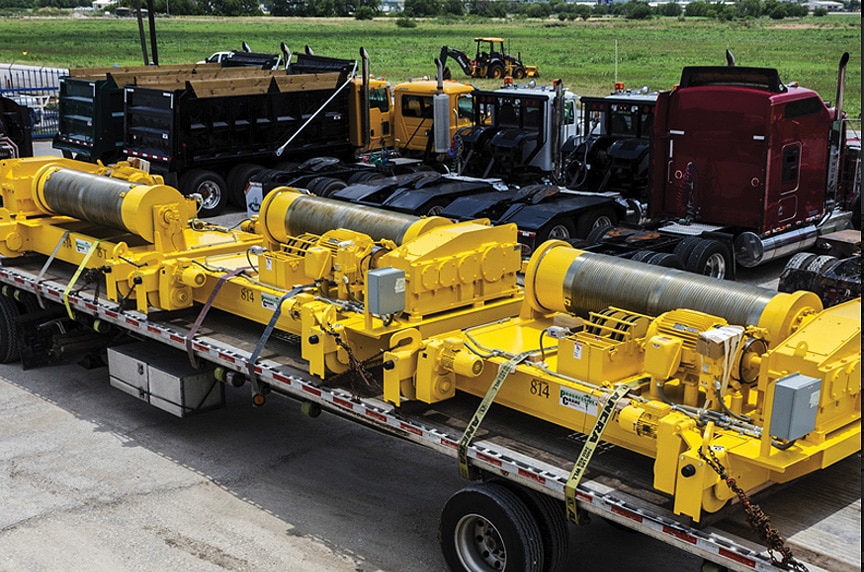
Most often, an overhead crane’s hoist is considered an age-related replacement. If you’ve been using the same hoist for a while and the gear box has become worn, it may be time to swap out to a newer model.
Over time, it can become harder and harder to get replacement parts for the hoists and gear boxes. Even a model that’s 10-15 years old may have parts that are now obsolete or hard to track down. Sourcing these hoist components can become expensive as the price may jump up if the parts are hard to come by. It can also lead to costly production downtime if there are long lead times on getting the parts you need replaced or reverse-engineered.
A change in production needs can also require you to replace the hoist on your overhead crane. If you’re adding a new production shift, or starting to make heavier or more frequent lifts during the course of a day, you may need to upgrade to a hoist that meets the proper service specifications. This will ensure that your new hoist is designed and built to withstand the rigors of the job you’ll be performing.
HMI/ASME has five duty cycle classifications for electric hoists that take the following into consideration:
- Average operating time per day
- Load spectrum
- Starts per hour
- Operating periods
- Equipment life
Gear boxes also have the longest lead time for replacement gears and internal components. Most styles of overhead crane gear boxes aren’t commercially available, so individual components are repaired or replaced. There also aren’t a lot of repair or rebuild kits readily available–especially for the heavy-duty and higher end boxes. Manufacturing or reverse-engineering of these gears and components can take a long time due to machining and heat-treating of the components for strength and durability.
End Trucks and Wheels
One of the most common problems with overhead cranes is uneven and excessive wear to the end truck wheels. The wheels on an overhead crane will naturally wear down due to normal use and may require more frequent maintenance, replacement, and adjustment than other components. However, a crane that is out of alignment or is moving loads outside of the capacities and service classes that it was designed for, will put extra stresses on the end truck and wheels as it moves down the runway.
You can upgrade to wheels made of a harder material that is best suited for the application and for the hardness of the rail itself. A wheel that is harder than the hardness of the rail will begin to cause excessive wear to the rail or beam itself, so make sure that the wheels were made specifically for the rail they’re running on.
The majority of crane wheels are made from high-carbon steel, but can also be made of polyurethane, alloys, cast steel, and or medium-carbon steel. Carbon steels will increase the hardness of the wheel, and heat-treating can also be used to increase the hardness as well.
As wheels and end trucks age, it can become more difficult to get older style bearings or cast wheel replacements—your best bet may be to upgrade the entire end truck itself. You can also choose to modernize your crane’s end trucks or wheels when you upgrade the drives, couplings, controls, or electrification. Often times you can immediately increase the efficiency and performance of your crane by upgrading and combining multiple systems—especially as it relates to the drives and controls.
Electrification Systems
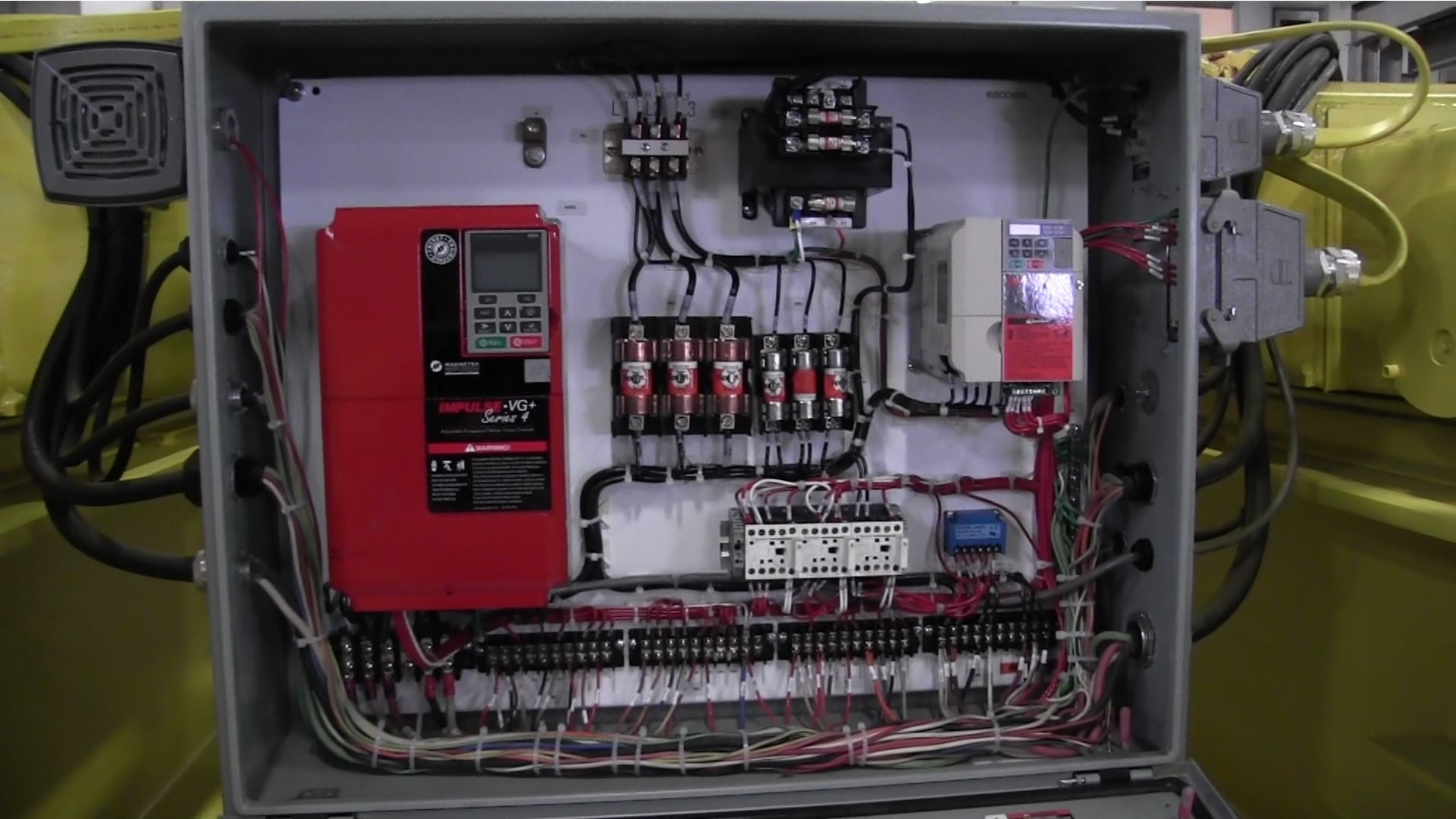
An overhead crane’s electrical system can cause more downtime than anything else. Loose or broken wires, shorts in the electrical connections, and blown fuses can all require service calls that will result in equipment and production downtime.
The original electrical systems on older cranes weren’t really engineered or designed at all. In a lot of instances, uninsulated and bare copper wiring was run loose with the only goal being to provide power to the crane. In some instances, your main control panel could look like a rats’ nest of tangled and unmarked wires as a result of different service technicians digging through and trying to patch together a fix over time.
When you upgrade an older crane’s electrification system, you get the added benefit of a higher efficiency system, which can translate into energy cost-savings. You may also save some money when it comes time to file your taxes, as a new electrical system in your crane equipment could translate into an energy credit.
Upgrading to a newer electrical system comes with inherent safety features. All new wiring is insulated or shielded and it should be routed cleanly with clear markings or indicators during the installation process.
With the addition of a modernized electrical system, you also prolong the life and increase the efficiency and reliability of your other electrical components—including the control systems, drives, and other structural and mechanical devices of your overhead crane.
You should also be aware that if you’re currently running 3-bar conductors to power your crane system, you are not in compliance with industry standards.
Current design standards for overhead cranes require the use of 4-bar conductors with a ground—there are no exceptions or grandfather clauses. If you’re still running 3-bar conductors, you need to upgrade your electrification system immediately.
Structural and Runway Components
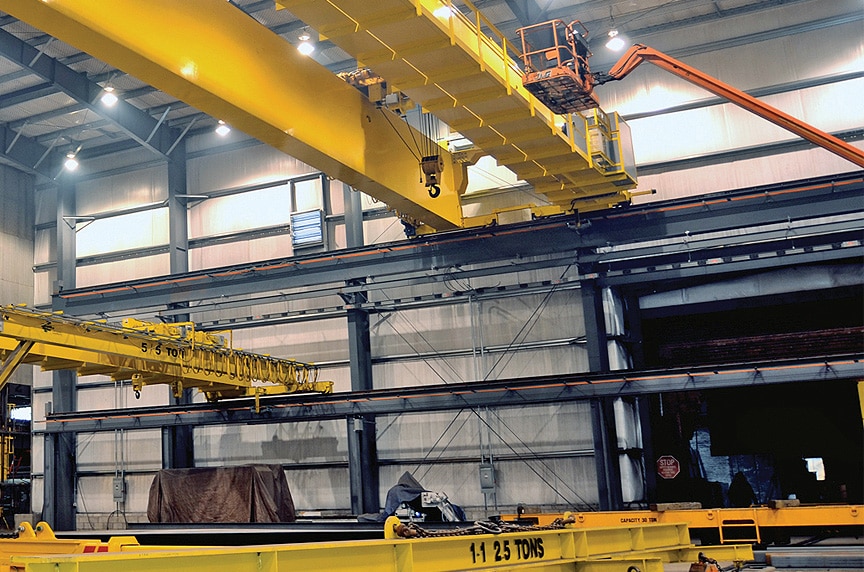
Structural components on an overhead crane can be replaced if necessary, but when designed and installed properly, can far exceed the life span of other crane and electrical components.
Replacing or upgrading the runways, girders, or tie-back supports can be one of the most expensive projects you may go through. During a process like this, you’ve probably already had an engineering team come in to provide a structural survey and foundation assessment of your building and flooring. You may have also had a reliability survey conducted on your overhead crane to see how much life is left in the components of the crane and of the structural support.
At this point, you’ll have to do a thorough cost-benefit analysis of what it will cost to replace cracked, bent, warped, or corroded runway or bridge beams (plus any other components that have reached the end of their effective productiveness) vs. the cost of a new overhead crane system.
Wrapping it Up
At Mazzella, we understand how important a functioning and reliable crane can be to your business. An overhead crane upgrade or modernization can take an unreliable crane system and extend the life of the crane equipment and make it more productive, efficient, and safer.
We can service any make or model of overhead equipment and pride ourselves on fast, quality service 24 hours a day. We also perform all of our work in compliance with OSHA and CMAA standards.
If you’re interested in speaking with a crane service specialist, please contact us for a quote today. We can work with you to develop a specialized crane upgrade or modernization program for the fraction of the cost of a new system!
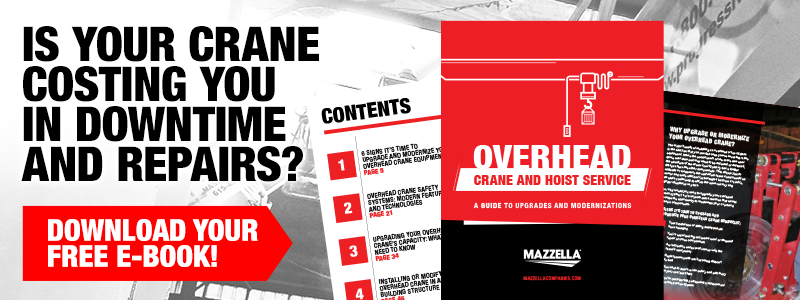
Copyright 2017. Mazzella Companies.