How Does the No Touch® Electrode Handling System Make Steel Mills Safer?
Does your steel mill need help in creating a safer environment for your workers? The No-Touch® Electrode Handling System will help increase production while making your mill safer at the same time.
Steel mills can be hazardous places to work.
It’s a world full of the following hazardous conditions:
- Extreme heat
- Deafening noise
- Heavy machinery
- Toxic chemicals
- Crushing machines
Every step in the production process can put workers at risk. Electrodes can pose a severe hazard by exposing workers to electric shock burns, explosions and injuries resulting just from maneuvering these massive columns.
However, there is a way for you to improve safety and efficiency without ever going near the electrodes themselves. Mazzella produces the No-Touch® Electrode Handling System and component parts that will help make handling electrodes easier and much safer.
In this article, we’ll answer the following questions:
- What are the dangers of working in a steel mill?
- What are the hazards of handling electrodes?
- What is the No-Touch® Electrode Handling System?
- How does the No-Touch® System work?
- What are the benefits of using the No-Touch® System?
What Are the Dangers of Working in a Steel Mill?
Electrode handling, and the charging process for an electric arc furnace, can be very dangerous. The size of the electrodes themselves, the weight, the heat they give off, and the molten steel they produce are both impressive and intimidating.
If you look at the electrodes used in steel making, they are anywhere from 122” up to 140” in length. Typically, these 3,800-lb. pieces of graphite can be very dangerous in the steel mill environment. Handling electrodes is a huge obstacle in terms of safety, back injuries, hand injuries, arm injuries, and shoulder injuries.
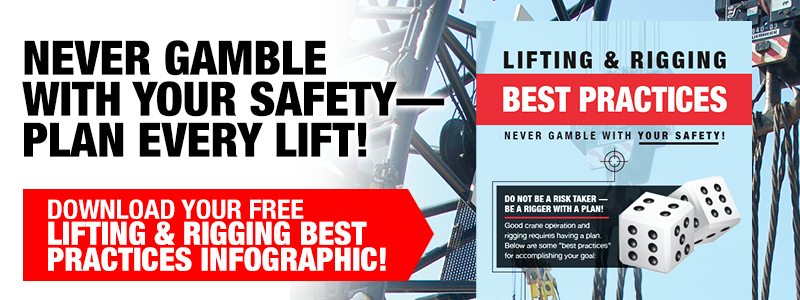
What Is the No Touch® Electrode Handling System?
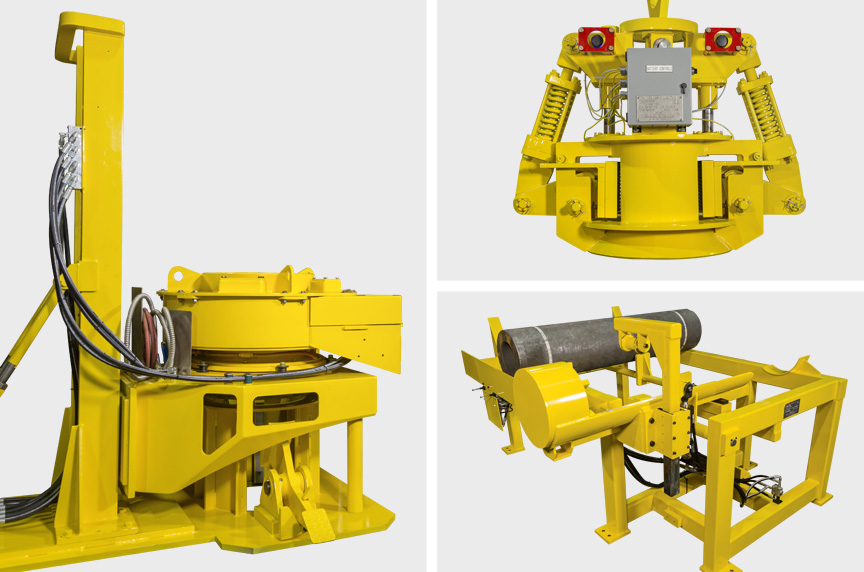
The No-Touch® Electrode Handling System has revolutionized safe and efficient electrode handling operations throughout the steel industry. Top industry professionals helped design this totally touchless system that removes operator risk from the electrode addition equation.
The built-to-order No-Touch® Electrode Handling System combines state-of-the-art technology and precision engineering to add and torque electrodes by remote control, protecting your most valuable resource, your employees, while improving efficiency.
The key is taking people out of harm’s way entirely, and that’s where the No-Touch® System comes in. You don’t have to touch the electrode because it’s added by the machine. It’s torqued by the machine, and it’s put together by the machine.
What Components Make Up the No Touch® Electrode Handling System?
The No-Touch® Electrode Handling System is made up of several components which add up to safer, more efficient work.
It features the following components:
- Up-ending Table
- Vertical Automatic Addition Tong (VAAT)
- Spinning Hydraulic Torque Device (SHTD)-When preloaded with an electrode column, the SHTD receives the new electrode that is lowered into place by the VAAT
How Does the No Touch® Electrode Handling System Work?
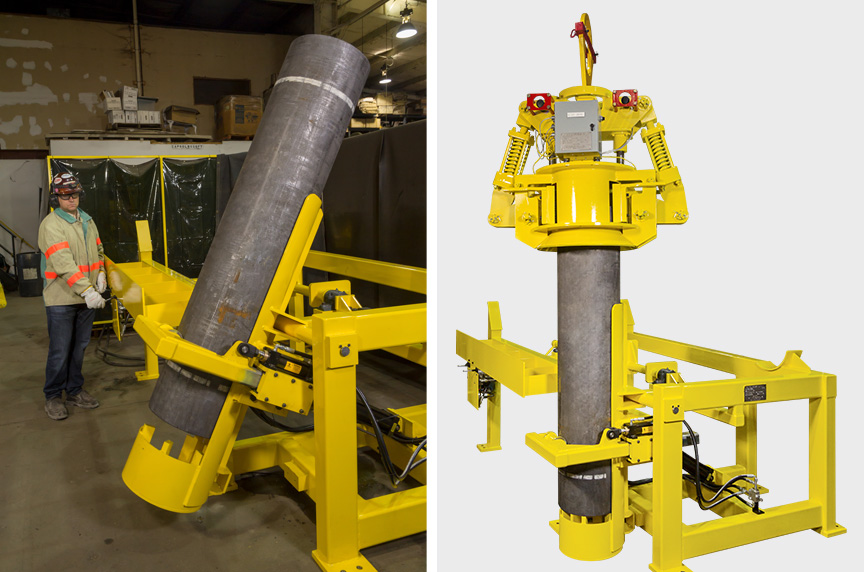
When the electrodes arrive on the handling floor, they’re loaded on an upending table by an overhead crane or fork truck. Once loaded, the electrodes are indexed as they roll toward the front of the machine and secured with an arm to ensure stability. Then, they are brought into a vertical position.
During this process, the Vertical Automatic Addition Tong is moved into position to remove the electrode from the upending table. The custom bale is designed so a crane hook can engage and lift the VAAT without furnace operator assistance. As the crane lowers the VAAT over the electrode, it locks down on the electrode and can be lifted in a true vertical formation. For the addition process, when the crane lifts the VAAT, the suspended electrode can be rotated a full 360°, providing a touch-free solution to the electrode addition process.
With the electrode in the air, the crane operator will maneuver the electrode above the Spinning Hydraulic Torque Device. Once in position, the operator lowers the new electrode section down toward the electrode column already inside the SHTD. With the correct space between the new electrode section and the electrode column, the SHTD clamps and starts rotating the new electrode.
The electrode column already inside the SHTD is clamped and held in place. The VAAT is equipped with a threaded system that matches the thread pitch of the electrode. The VAAT rotates independently and lowers with the electrode as it is threading onto the electrode column. Once torqued to the required specification set by the electrode manufacturer, the electrode column is lifted from the SHTD by the VAAT and returned to the electric arc furnace for operation.
What Are the Benefits of Using the No Touch® Electrode Handling System?
The No-Touch® Electrode Handling System makes a dangerous job significantly safer.
By keeping your workers away from heavy electrodes and extreme temperatures, this system relieves them of the burden of having to get these giant pieces of graphite into place. The system is fundamentally safer than on-furnace designs, as it removes the need for your workers to be on the furnace roof in harm’s way.
If torque equipment breaks down with state-of-the-art technology and precision engineering, the no-touch system improves efficiency, adding up to:
- A safer workplace
- Fewer lost-time injuries
- Better productivity on the floor
For example, the No-Touch® Electrode Handling System has proven especially useful to North Star BlueScope Steel. North Star’s workers no longer have to put their hands and arms in harm’s way. It is a totally touchless system. A steel mill’s employees are the most important part of this operation and keeping them safe is the most critical task.
What Accessories Help with Electrode Handling?
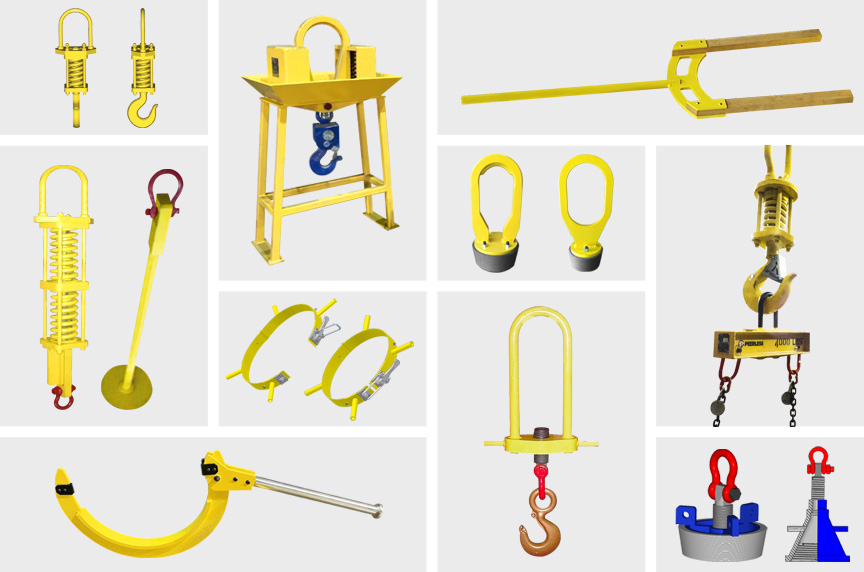
Along with the standard components that comprise the No-Touch® Electrode Handling System, there are several column assembly and transportation devices to help make the process safer and more efficient.
Those additional components include:
- Electrode Column Assembly and Transportation Devices
- Electrode Recovery Tools
- Specialty Equipment
- Hydraulic Torque Device and Assembly Station
Electrode Column Assembly and Transportation Devices
Graphite Lift Plugs
Graphite lift plugs are designed for vertical transportation of electrodes to and from the furnace. These devices enable the operator to leave the device on the column during furnace operation.
Metal Lift Plugs and Steel Lift Caps
Threaded-stem metal lift plugs and steel caps are used to take an electrode section from horizontal to vertical. Also, they help spin down at the same thread pitch as the electrode connecting pins during the jointing process.
Cushioned Lift Device
The Cushioned Lift Device is used for the addition and transfer of electrode columns for off-furnace assembly. Also, it can assist in negating the effects of shock loading that may occur when removing an electrode column from the electric arc furnace. An optional swivel or anti-rotational hook are available, too.
Cushioned Lift Device with Elebia® Auto-Hook – Low Headroom
The low-profile device gives you the benefits of a cushioned lift device and Elebia® Auto-Hook in one device.
Manual Clamping Collar
The manual clamping collar is used to spin an electrode section down into the adjoining electrode and help initiate the tightening process.
Wishbone Spacer
The lightweight, wooden wishbone spacer fits between electrode end faces during the jointing process to prevent damaging graphite threads. Also, it helps to “set the gap” between electrodes.
Rising Stem Lifting Device
The rising stem lifting device is used for the transportation of electrode sections, and also, to spin down at the same thread pitch as the electrode connecting pin. These devices are used in conjunction with graphite lift plugs.
Electrode Chain Wrench
This electrode chain wrench allows the operators to safely spin an electrode and tighten the electrode joint.
Torque Wrench
The torque wrench offers a positive torque indicator by means of an unmistakable signal. This ensures the graphite electrodes are torqued to the manufacturer’s recommended specification.
Electrode Recovery Tools
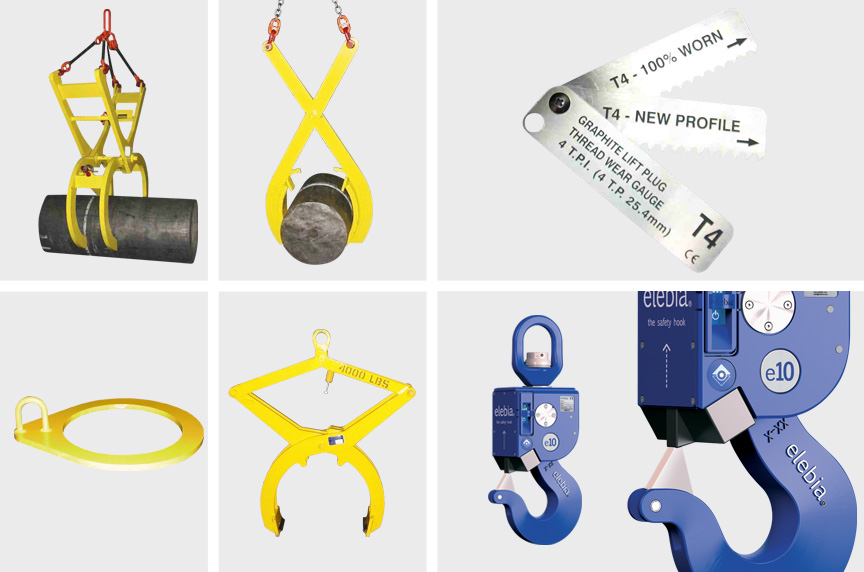
Electrode Recovery Ring
The electrode recovery ring is used for recovering broken or damaged electrode sections that are in vertical or semi-vertical positions.
LMF-Electrode Recovery Tong
Held open by a combustible extension, this LMF tong closes within close proximity of the molten steel bath, securing a broken electrode.
EAF-Electrode Recovery Tong
The EAF Electrode Recovery Tong is designed for the recovery of broken electrode sections or columns. This unit features a Heppenstall latch and will grip the electrode from true horizontal to semi-vertical.
Dual Arm Heavy-Duty EAF Electrode Recovery Tong
This heavy-duty tong is designed for the recovery of a broken electrode column. The unit is held open by a bump link and will grip the column from true horizontal to semi-vertical. The device comes complete with required rigging.
Specialty Equipment
Thread Wear Pocket Gages
This go / no-go gage identifies if the threads of a lift plug are considered worn out. There is a 3 threads-per-inch (T3) and 4 threads-per-inch (T4) device to fit your needs.
Tap Hole Lift Device Assembly
The tap hole lift device assembly is used to install stackable eccentric bottom tap-hole (EBT) refractory end blocks and tap hole sleeves into the base of the furnace. Also, the device assists in negating the effects of minor shock loads that may occur when installing the refractory. The springs of the device offer crane operators a visual indicator of the load that is being applied.
Slide Gate Lift System
This customized cushioned lift device is designed to safely remove slide gates from the bottom of ladles.
Mechanical Electrode Holder
Electrode column storage racks with eccentric locking devices allow jointing at each station. Mazzella can match existing holders, as well as engineer a custom-designed rack, to meet your specific needs.
Elebia® Auto-Hook
This professionally engineered and patented product is on the forefront of “hands free” safety. Offering a 5-ton, 10-ton, and 20-ton Auto-Hook, Mazzella is proud to be the exclusive distributor of Elebia® hooks to the steel industry in the United States.
Hydraulic Torque Device and Assembly Station
Spinning Hydraulic Torque Device – Off-Furnace Electrode Addition System
Complete with a mechanical electrode holder and eccentric locking device to ensure a positive torque reaction point, this device automatically spins down the electrode and applies the final recommended torque by using one lever.
Torque Flange Indicator
This indicator can be added to most Mazzella electrode addition stations to independently verify what torque is being applied.
What Is the Electrode Weigh Scale?
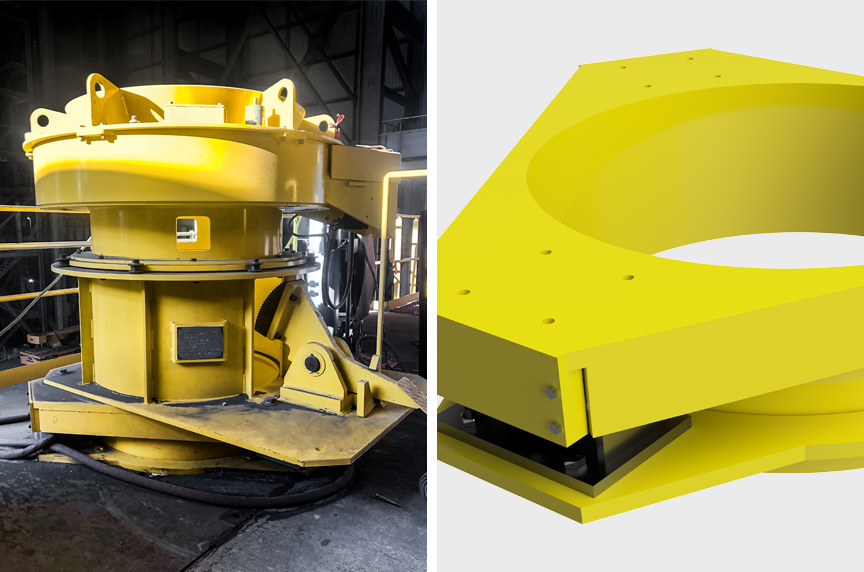
Graphite electrodes used in metal arc furnaces in the steelmaking industry are large and may weigh several tons.
As the electrode columns are consumed within the furnace, they eventually reach a length where they cannot be used independently. Partially consumed electrodes can be joined with other partially consumed electrodes, or new electrodes, in an end-to-end configuration, making them long enough again for use.
Until recently, there was no easy way for operators to gather useful information on the spent electrodes, either before or after they were consumed to an unusable length. However, with the patent-pending Mazzella electrode weigh scale, arc furnace operators now can measure and weigh electrodes to determine the mass of an electrode and how many heats remain in a partially consumed electrode.
This data will help operators:
- Understand electrode consumption
- Determine cost per ton of steel
- Calculate how many pounds of electrode material went into a specific output of steel
The Mazzella Electrode Weigh Scale includes:
- A mounting platform
- An electrode holder and clamping assembly
- An electrode weighing assembly with at least one load cell
Using this scale, multiple electrodes can be weighed before and after their use in the furnace to determine the difference in weight, providing valuable information on electrode consumption.
By using Mazzella’s electrode weigh scale, steelmakers can:
- Track electrode consumption
- Reduce inefficiencies in furnace operations
- Plan effectively for adequate electrode supplies for their arc furnaces
How Can Mazzella Help with Your Electrode Handling Needs?
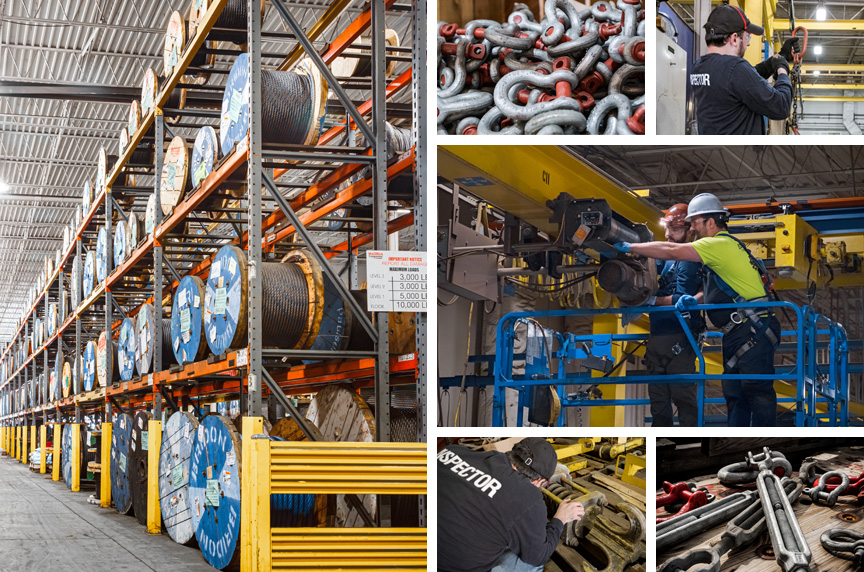
With close to 70 years of experience in steel mills, and the design and distribution of custom engineered products, below-the-hook lifting devices, and lifting attachments, Mazzella can help you get the correct devices for your specific needs.
Our decades of steel mill experience and expertise has taught us that delivery of the right product, to the right specs, at the right time…saves our customers a lot of time and money.
With a significant amount of customer-specific inventory on hand, when critical equipment goes down, we offer 24/7 emergency responsiveness for critical crane cables.
Also, we offer the following value-added services to our steel customers:
- Exact & Matched Crane Cables – a documented ISO procedure allows us to provide exact and matched crane cables to our steel customers with guaranteed accuracy for ease of installation.
- Mazzella Ready Stock™ Program – our Ready Stock™ program eliminates the need for our customers to purchase replacement wire rope inventory prior to a specific need. This process improves cash flow, eliminates damage to ropes during storage, and reduces overall and inventory carrying costs.
- Wire Rope Surveys – our team will come on-site and work with your team to assess the critical ropes and cables you’re using on your cranes and machinery. We’ll help identify opportunities to:
- Improve wire rope service life
- Reduce labor time during installation
- Reduce on-site inventory of backup wire rope
- Assure proper inventory levels
- Inspection Services – OSHA overhead crane inspections, OSHA sling inspections, and inspections of fall protection equipment and below-the-hook lifting devices
- One-Stop Shop – traditional rigging products, engineered lifting devices, overhead cranes, overhead crane service, parts, training and more!
Contact us if you need help with electrode handling, crane upgrades or modernizations, training, rigging inspections, wire rope or rigging!
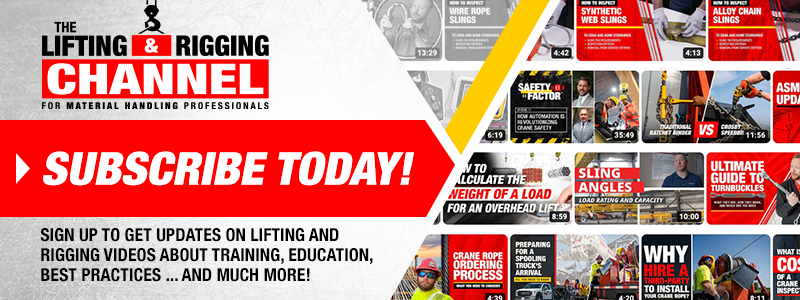
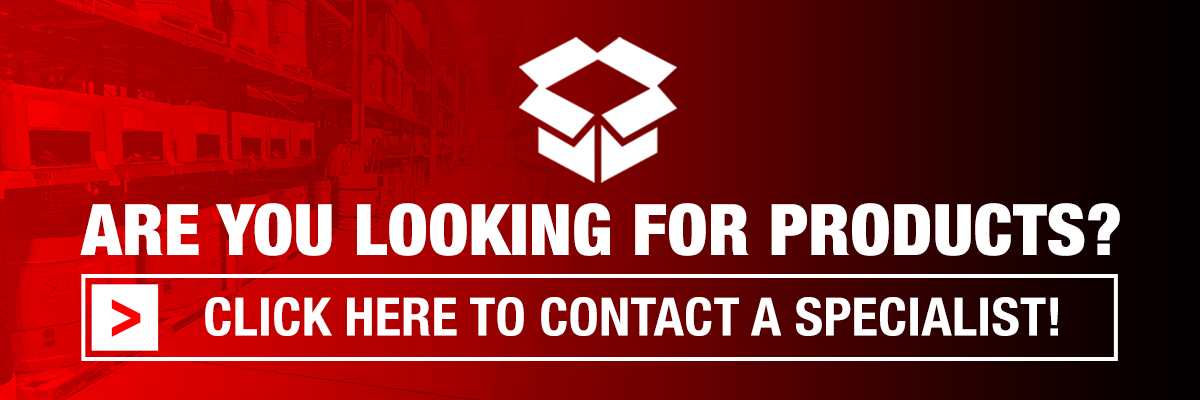
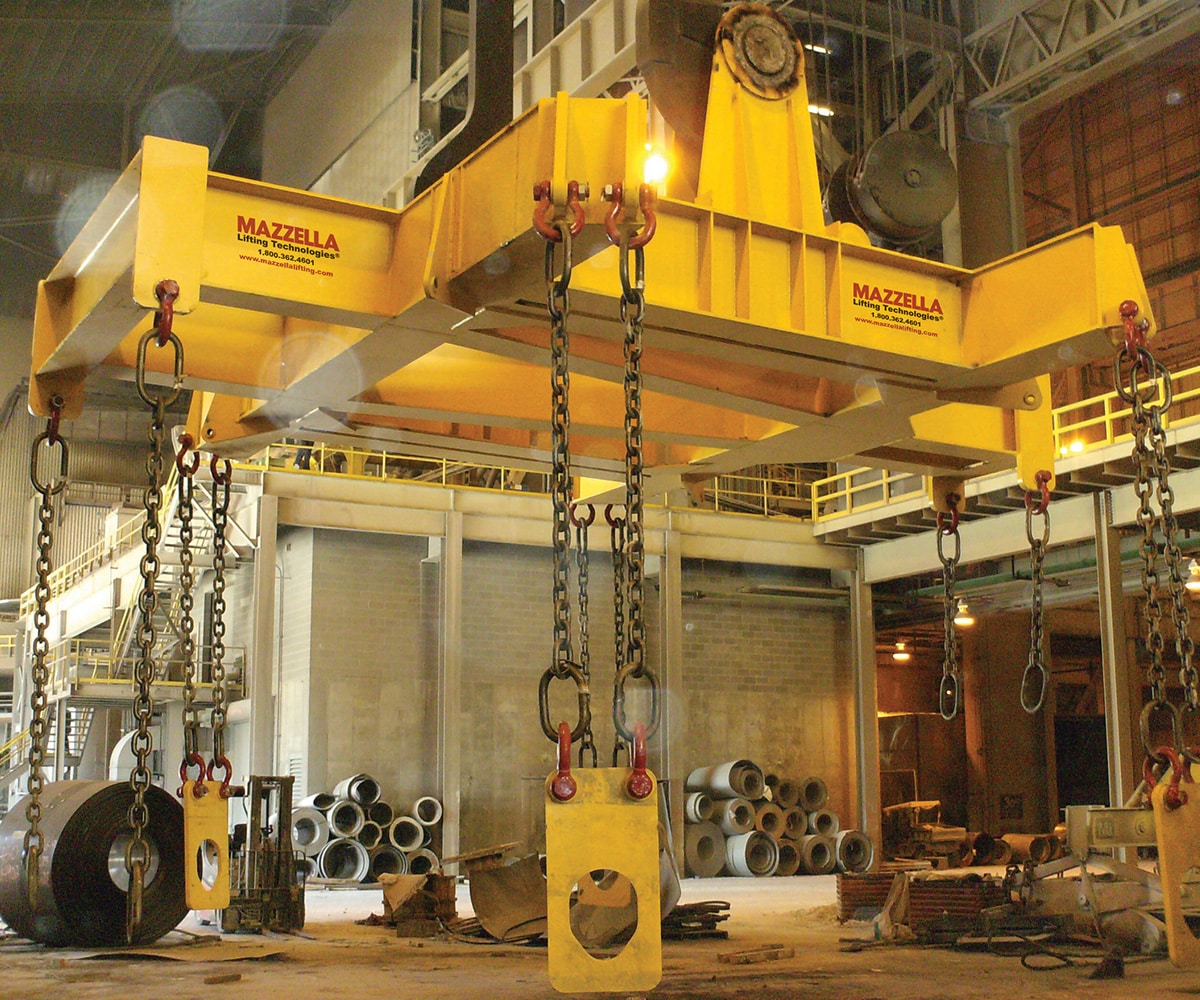
Below-the-Hook Lifting Devices
We have more than 65 years of experience in designing and developing custom engineered products, below-the-hook lifting devices, and lifting attachments for use with all types of cranes.
On-staff engineering and our commitment to ISO 9001: 2015 guides us to continued success in quality products and processes.
Copyright 2023. Mazzella Companies.