What Signs Will Show if My Rigging Inspection was ASME-Compliant?
How do I know if the rigging inspection I just had done by a third-party company was a good one? There are several signs to look out for to see if the rigging inspection keeps you in compliance with ASME standards.
“If something is worth doing, it is worth doing right. I take that one step further. You shouldn’t do anything unless you do it right.”
Boxing legend George Foreman may not have been talking directly about the lifting and rigging industry. However, his thoughts apply to rigging inspections and the importance of getting the most out of your third-party inspectors.
Making sure your equipment is being properly inspected is key to keeping your workers safe.
When you hire someone to do your rigging inspections, you want to make sure they do a thorough job. Unfortunately, that’s not always the case. Things get missed, inspections seem too quick, and there’s a problem with communication.
In this article, we’ll answer the following questions:
- What does a bad inspection look like?
- How long should a good inspection take?
- How do I find an inspector?
- What kind of post-inspection support do good inspectors offer?
- How do I prepare for an inspection?
- What’s Mazzella’s inspection process like?
What Does a Bad Rigging Inspection Look Like?
We’ve had many customers reach out after they just had an inspection performed. They’ve got a gut feeling that something wasn’t right.
Maybe the inspection:
- Went too quickly
- Had too much gear marked damaged and needing repair/replacement
- Provided no documentation on needed repairs
- Wasn’t accompanied by an explanation of the damage to the rigging equipment
Example: We’ve heard from our customers, “We’ve got all of these chain slings that our inspector removed from service, but there are no danger tags or any real explanation as to what’s wrong with them.”
Your rigging inspection service provider should walk you through their process post-inspection. They should show you the damage to the slings. Also, they should validate their findings and removal from service criteria.
Our rigging inspectors have pre-inspection meetings, and would like you to accompany them throughout the facility during the inspection. This way, they can point out problems directly to you. If a consistent problem is found on your slings, we’ll recommend educating your employees on how to better take care of and monitor the use of your rigging gear.
How Long Should a Rigging Inspection Take?
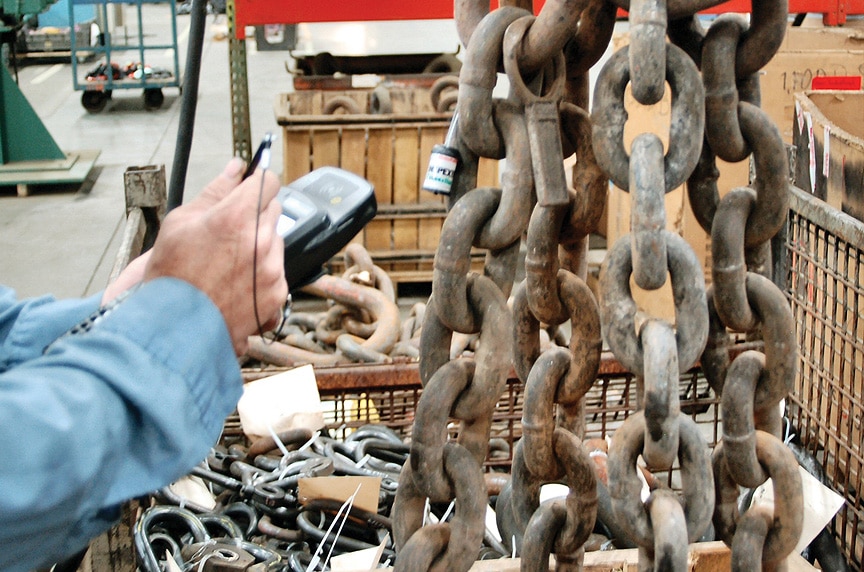
Simply put, a rigging inspection should last as long as necessary to inspect as many pieces of rigging gear as can be found in the facility.
Although it’s not required to examine every piece of rigging gear in your facility, you want a thorough inspection.
When talking about the post-inspection documentation, some of the worst evidence we see are reports not being provided to the customer. The inspection was performed. Somebody was there and did something. The customer has reached out to the vendor and can’t get the proper documentation returned from the inspection. We’ve also seen inspection “reports” written on a work order saying, “Hey, I looked at all your slings. Five of them were bad, and they’re by your office.”
That doesn’t meet the requirement of the American Society of Mechanical Engineers and their ASME B30.9 Slings standard.
We’ve seen other reports that are handwritten, where several notes were made, but no details were given about the inspection.
That leads you to another conversation where you’re trying to answer the following question:
“What did I get out of this inspection?”
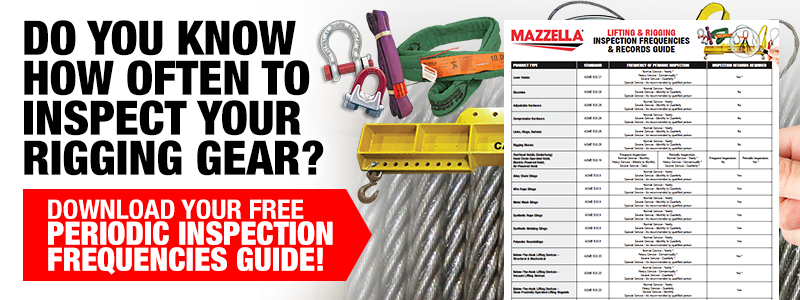
How Do I Find a Rigging Inspector?
Quality education is key.
First and foremost, customers should educate themselves on what to look for in a third-party rigging inspection company.
By your questions, rigging inspectors can tell if you’re familiar with this service or not. If you’re not, it’s the responsibility of a good rigging inspector to inform them of the process.
That conversation may go as follows:
“We know you need something. We’re here to inform you, not sell you anything. We’re going to put you in the best position. When you make your decision, you’re walking away from this meeting with the information you need.”
At Mazzella, we have a library of content that answers your inspection questions.
That’s where we’ve found there to be the customer’s biggest pain point. You’ve just had all your rigging gear inspected, and now, there’s one of the following problems to deal with:
- Are there a number of items in need of repair?
- Do several items need to be replaced?
- Can your provider repair them?
- Does your inspector have the ability to replace damaged rigging gear?
- Do they even know what needs to be replaced?
You want to choose somebody that can support you on the backend of an inspection because it could include better training of your employees on the proper use, care, and inspection of slings and rigging gear. If you had 100 items inspected and 60 failed for various reasons, your rigging inspection company should encourage you to retrain your employees.
Post-Inspection Support
Good inspection companies will outline what type of training program(s) you need to comply with the ASME B30.9 Slings standard. You should understand what ASME requires on a periodic basis regarding care, use, and inspection.
We’ll tell you that after training, we can perform more than one periodic inspection because that’s what’s required based on:
- Severity of service
- How many shifts you’re running
- How many lifts you’re making per day
That’s why you want to deal with a company who knows this business. They’re going to make sure after the inspection, you’re getting what you deserve/expect.
We might discover previous vendors just didn’t have the required experience to do a proper inspection.
We’re not saying crane technicians aren’t skillful enough to do the inspection. They just might not be as informed as a dedicated rigging inspector because it’s not their specialty. You need to take time to find proof that whoever does your rigging inspection is properly trained.
When you’re seeking out an inspector, make sure you spend the time checking their qualifications.
How to Prepare for a Rigging Inspection
No matter if it’s your first or 10th time managing your company’s rigging inspection program, you need to be ready to address any pain points found in the inspection.
You want to do this so your people buy into the program. If you don’t get that buy-in, you’re not likely to have a good inspection.
Always make sure you’re in a position to repair or replace something as quickly as possible. There’s few greater ways to lose support than not replacing or repairing a critical piece of rigging gear that’s been removed from service.
What we’ve found is when people see an inspector, or there’s notification put out about an upcoming inspection, rigging gear tends to go missing. This is done because workers don’t want to lose a piece of rigging gear that’s critical to the job or process they perform each day.
Example: If several of your chain slings are removed from service because of a damaged latch, you should ask your inspector if they distribute replacement latches. Also, if you have several types of synthetic slings, you might need help to standardize your rigging gear.
If you have those conversations and ask good questions of the inspector, but don’t get proper answers, you might not have gotten the service you deserved.
It’s the responsibility of the provider on the front end to make sure you’re going to receive what you’re paying for. If you’re receiving a “free” service, it still needs to be done to the same ASME standards as paid inspections.
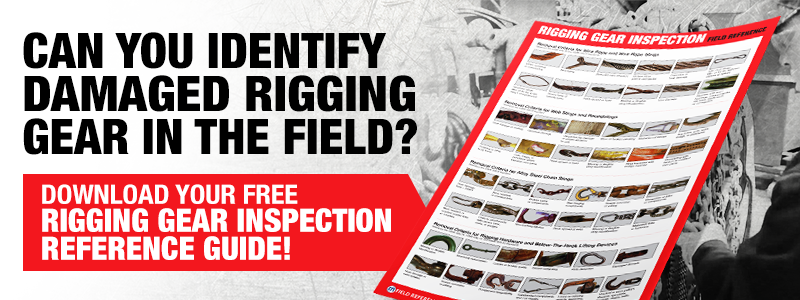
What’s Mazzella’s Rigging Inspection Process Like?
Prior to performing an inspection, we’ll want to walk around your facility and learn what the job entails:
- Quantity-wise
- Size-wise
- What’s happening during each shift
- Downtimes
- Anything else that can hold up an inspection
When a customer hires us for an inspection, we want to make sure there’s no conflict of interest. We’re only there for the inspection itself, and we’re not there to sell you:
- Replacements
- Repairs
- Any other service
We want the inspection performed to your satisfaction and make sure you’re in compliance with OSHA (Occupational Safety and Health Administration) and ASME standards.
With a conflict of interest, sometimes that’s why you see poor inspections. There might’ve been an agreement with the service provider before the inspection that says, “I’m going to purchase my repairs and my replacements from you.”
Our path is different because we value our service. There’s a fee for it, but you’re going to get what you paid for. You’re not going to be pushed into anything you don’t need.
What We’re Looking for in a Rigging Inspection
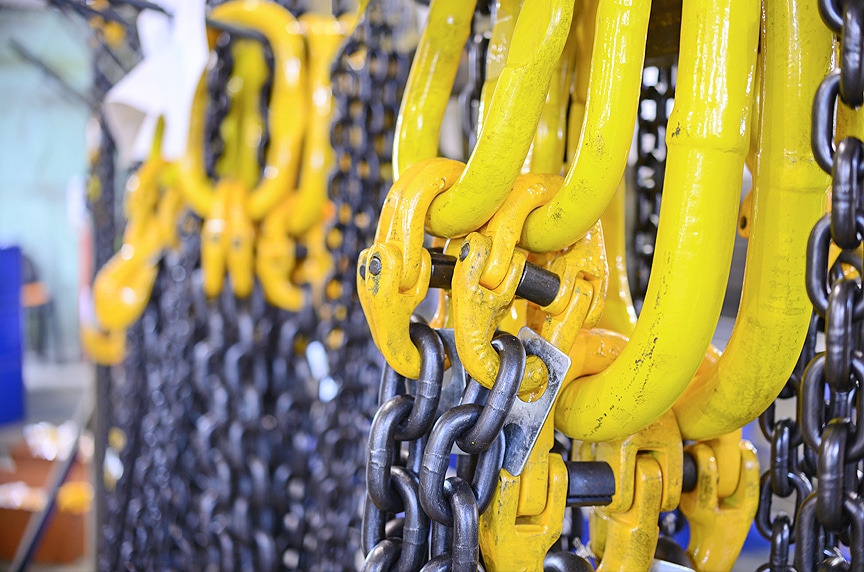
As we’re walking through your facility, we’ll notice pieces of equipment that are out of compliance. That could include anything like:
- Alloy chain slings without tags
- Homemade below-the-hook devices
Often, homemade below-the-hook devices don’t have proper markings. Also, good rigging inspectors can tell when it’s been repaired and rebuilt numerous times.
When we review your previous inspection reports, we might find another vendor has marked these devices as compliant. Should such an instance occur, we’ll refer to the ASME B30.20 Below-The-Hook Devices standard to show you may have received a “pencil-whipped report.”
That implies your previous inspector just walked through your facility and checked off boxes on a checklist. Conversely, we’ll inform you on:
- What the standards say
- What you should expect
- Why our proposal’s going to look different from inspections you’ve received in the past
When we do inspections, we like the customer to be with us, if they can. We want you to learn from us as we inspect the rigging gear. That’s really the best way to go through an inspection.
We understand some customers just don’t have that luxury of time and manpower to dedicate to an inspection. If that’s the case for you, we’ll inform you before the inspection that if we find anything out of compliance, we’ll want to meet during the day. At the end of the inspection, we’ll meet with you again and:
- Share the findings
- Walk you through next steps
- Address anything that needs immediate attention
- Discuss something that might take time to quote for repair/replacement
Wrapping it Up
No matter who you choose to conduct your next rigging gear inspection, we want to prepare you with the knowledge to find the right inspector by following these steps:
- Ask the right questions
- Look out for warning signs if the inspection isn’t going the way it should
- Know the steps to take if you’ve had a bad inspection
At Mazzella, we understand the importance of an inspection. We’re not there to upsell or get in and out and as fast we can. We’re here to do a comprehensive, detailed inspection to ensure safety and instill confidence and comfort.
Call us at 800.362.4601 or click here if you need inspections for slings, rigging hardware, lifting devices, or fall protection!
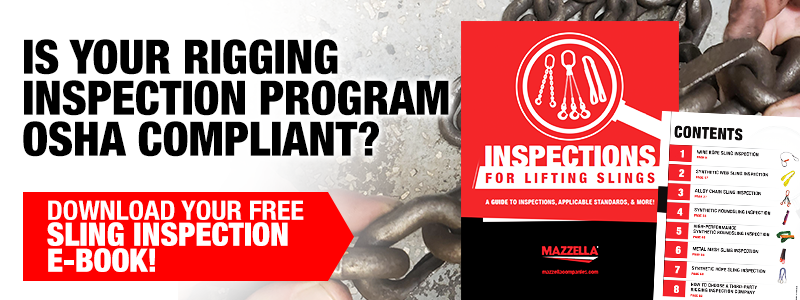
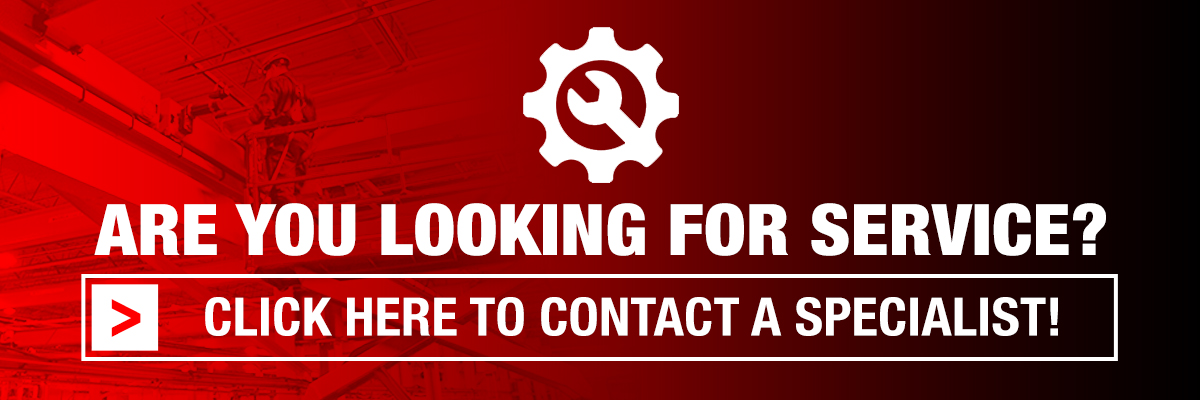
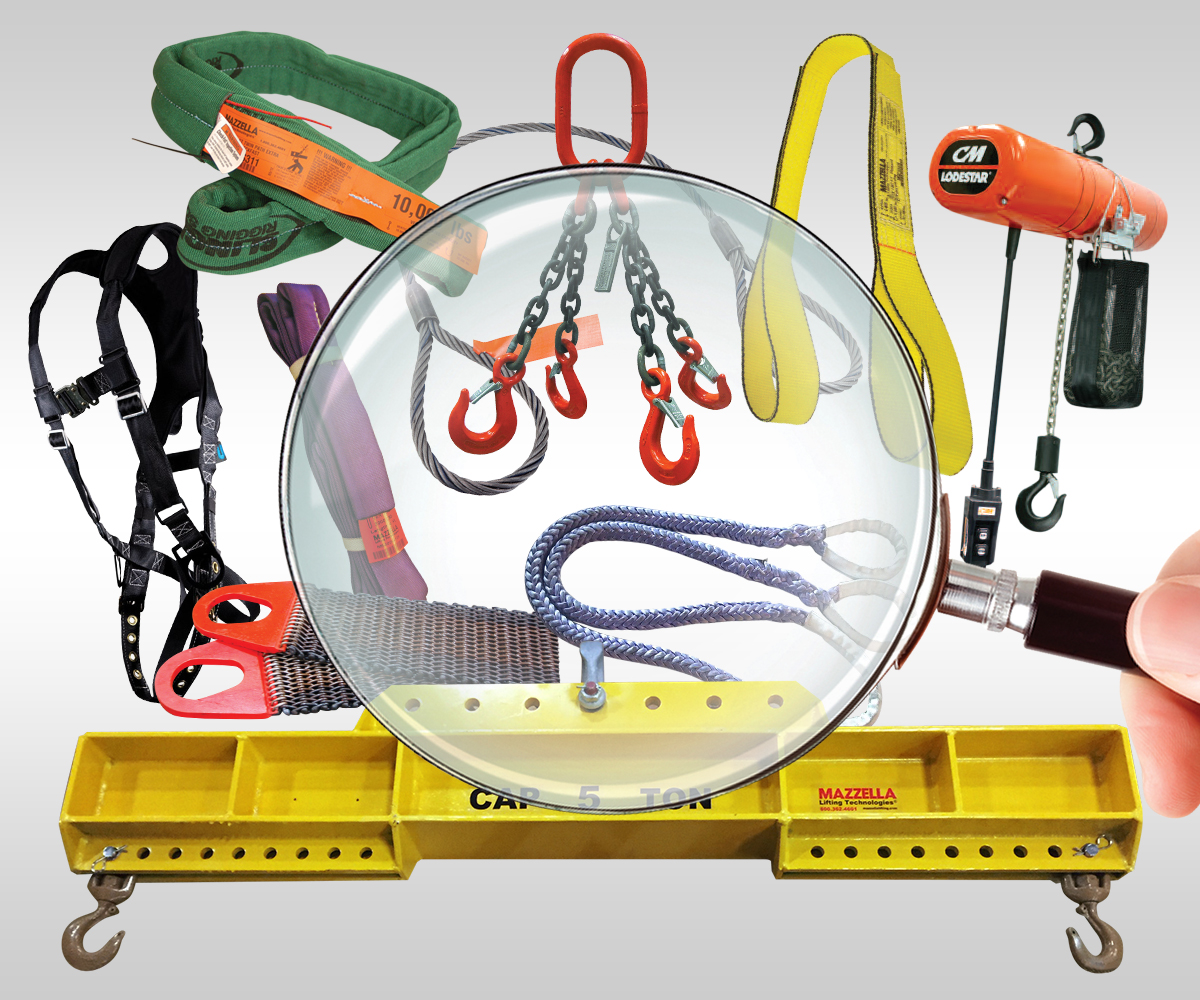
Rigging Inspection Services
OSHA 1910.184, ASME B30.9, B30.20, B30.26, and ANSI Z359 require periodic, documented inspections on slings, rigging hardware, lifting devices, and fall protection every 12 months, at minimum, and monthly to quarterly in more severe service conditions.
Our team of rigging inspectors are certified to make sure your products meet OSHA and ASME requirements.
Copyright 2021. Mazzella Companies.